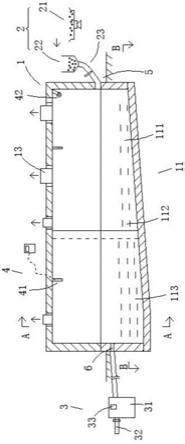
1.本实用新型属于瓦斯灰冶炼设备技术领域,更具体地说,是涉及一种含锌高炉瓦斯灰冶炼装置。
背景技术:2.目前,高炉冶炼过程中随高炉煤气一起排出的粉尘颗粒物,经过重力除尘和布袋除尘器收集,形成布袋灰,布袋灰又常称为瓦斯灰,瓦斯灰含碳量高达30%~50%,铁含量低,在15%~30%,锌、钠等含量较高,锌、钠等元素对高炉危害大,一般不能直接用于烧结配料。
3.钢厂系统还有其它一些除尘灰,比如:焦化煤场除尘灰,煤、焦炭的皮带通廊的除尘灰,干熄焦系统除尘灰,这些除尘灰的特点是碳含量很高;炼钢的煤气干法除尘,这种除尘灰铁含量较高,达到50%以上,钠、锌等含量高,直接用于烧结配料,锌、钠对高炉冶炼也危害较大。
4.锌、钠等含量高的固体废物是各钢厂面临的共同难题,而且对于瓦斯灰等固废也不允许直接外排,因为高炉不适合冶炼含锌等固体废料的特点,因此就采用了各种处理方法处理这些固废,如磁选法、焙烧法、转底炉法等,以上各处理方法各有利弊,然而对于瓦斯灰的处理还是存在不理想之处,而且通过常规高炉也不适合冶炼含锌高炉瓦斯灰,因此急需提出一种能够适合冶炼含锌高炉瓦斯灰的冶炼装置。
技术实现要素:5.本实用新型的目的在于提供一种含锌高炉瓦斯灰冶炼装置,旨在解决现有的高炉不适合冶炼含锌瓦斯灰的技术问题。
6.为实现上述目的,本实用新型采用的技术方案是:提供一种含锌高炉瓦斯灰冶炼装置,包括冶炼炉、送料机构、出料机构和监控机构,冶炼炉呈长条形,下部埋设于地面下,所述冶炼炉底面与水平面之间呈夹角设置,所述冶炼炉的两端分别设有进料口和出料口,所述冶炼炉用于冶炼含锌瓦斯灰并产出铁水和氧化锌粗品;送料机构设于所述进料口处,用于向所述冶炼炉内输送高炉瓦斯灰干球;出料机构设于所述出料口处,用于承接从所述冶炼炉内输出的铁水和液体炉渣;监控机构设于所述冶炼炉内侧顶部,用于监控所述冶炼炉内温度和物料反应过程。
7.作为本技术另一实施例,所述送料机构包括称重台、料仓和给料管路,称重台用于称重待进入所述冶炼炉内的瓦斯灰的重量;料仓用于盛放瓦斯灰干球,称重后瓦斯灰干球放置在所述料仓内暂存;给料管路呈倾斜设置,一端连通所述料仓、另一端连接所述进料口,所述料仓内的瓦斯灰干球经所述给料管路输送至所述冶炼炉内。
8.作为本技术另一实施例,所述出料机构包括避渣器、铁水沟和渣沟,避渣器与所述出料口连通管并承接输出的铁水和液体炉渣,所述避渣器用于分离铁水和液体炉渣;铁水沟连通所述避渣器的输出端,所述避渣器将铁水分离后,铁水流向所述铁水沟;渣沟连通所
述避渣器的输出端,所述避渣器将液体炉渣分离后,液体炉渣流向所述渣沟。
9.作为本技术另一实施例,所述监控机构包括温度监控器和成像仪,温度监控器设于所述冶炼炉内侧顶部,用于监控所述冶炼炉内的温度;成像仪设于所述冶炼炉内侧顶部,用于采集所述冶炼炉内反应过程中的图像。
10.作为本技术另一实施例,所述冶炼炉包括炉体、高温空气管和废气出管,所述炉体下部埋设于地面下、上部位于地面上;高温空气管为多个,均设于所述冶炼炉两侧并连通至所述冶炼炉内,用于与高温空气源连通,高温空气源通过所述高温空气管向所述冶炼炉内输送高温空气;废气出管为多个,均设于所述冶炼炉上端并连通至所述冶炼炉内,所述冶炼炉内产生的废气通过所述废气出管进入废气余热回收系统,经过降温、除尘后达标排放。
11.作为本技术另一实施例,沿所述进料口至所述出料口的方向所述冶炼炉依次分为反应区、过渡区和渣铁分离区,反应区的底部置于地面下并呈长条槽型结构,进入至所述冶炼炉内的物料在所述反应区进行反应,所述进料口位于所述反应区的进料端;过渡区的底部置于地面下并呈弯弧槽型结构,所述反应区内的物料流入至所述过渡区;渣铁分离区的底部置于地面下并呈长条槽型结构,反应中产生的铁水和渣通过所述过渡区流动至所述渣铁分离区,在所述渣铁分离区内渣与铁分离,所述出料口位于所述渣铁分离区的出料端,所述过渡区两端分别圆弧过渡承接所述反应区和所述渣铁分离区。
12.作为本技术另一实施例,埋设于地面下的所述反应区、所述过渡区和所述渣铁分离区均为槽型结构,漏出于地面上的所述反应区、所述过渡区和所述渣铁分离区为与槽型结构相适配的拱形结构,所述拱形结构与所述槽型结构相互对接扣合形成一体且内部为中空。
13.作为本技术另一实施例,所述进料口处设有用于向所述冶炼炉内泵送氧气的氧气泵送组件。
14.作为本技术另一实施例,所述进料口位于所述冶炼炉上埋深较浅的一端,所述出料口位于所述冶炼炉上埋深较深的一端。
15.作为本技术另一实施例,所述冶炼炉包括厚钢板制成的外壳和铺设于所述外壳内壁上的耐火砖,所述外壳内部为中空。
16.本实用新型提供的含锌高炉瓦斯灰冶炼装置的有益效果在于:与现有技术相比,本实用新型含锌高炉瓦斯灰冶炼装置,冶炼炉埋设在地面上并与水平面呈一夹角,物料从进料口进入冶炼炉后,由于倾斜设置冶炼炉,物料在冶炼炉内反应后能从出料口处输出,通过高温空气管向炉体内输送高温空气,用于燃烧反应过程中产生的煤气,并放出热量,维持炉内高温环境,反应中产生的废气能够经过入余热回收、除尘系统后达标排放,含锌瓦斯灰通过送料机构送入冶炼炉内,反应后通过出料机构输出,通过监控机构可看出冶炼炉内温度和反应过程,该长条形冶炼炉呈卧式设置,能处理含锌瓦斯灰,解决了现有的高炉不适合冶炼高炉瓦斯灰的技术问题,具有长条形冶炼炉可用于含锌瓦斯灰的冶炼,冶炼过程中反应稳定和快速的技术效果。
附图说明
17.为了更清楚地说明本实用新型实施例中的技术方案,下面将对实施例或现有技术描述中所需要使用的附图作简单地介绍,显而易见地,下面描述中的附图仅仅是本实用新
型的一些实施例,对于本领域普通技术人员来讲,在不付出创造性劳动的前提下,还可以根据这些附图获得其他的附图。
18.图1为本实用新型实施例提供的含锌高炉瓦斯灰冶炼装置的结构示意图;
19.图2为图1中的a
‑
a处截面图(炉体上部和下部结构侧视图);
20.图3为图1中的b
‑
b处截面图(炉体下部结构俯视图);
21.图4为本实用新型实施例提供的含锌高炉瓦斯灰冶炼装置的冶炼炉结构俯视图。
22.图中:1、冶炼炉;11、炉体;111、反应区;112、过渡区;113、渣铁分离区;12、高温空气管;13、废气出管;2、送料机构;21、称重台;22、料仓;23、给料管路;3、出料机构;31、避渣器;32、铁水沟;33、渣沟;4、监控机构;41、温度监控器;42、成像仪;5、进料口;6、出料口;7、氧气泵送组件。
具体实施方式
23.为了使本实用新型所要解决的技术问题、技术方案及有益效果更加清楚明白,以下结合附图及实施例,对本实用新型进行进一步详细说明。应当理解,此处所描述的具体实施例仅仅用以解释本实用新型,并不用于限定本实用新型。
24.请一并参阅图1至图4,现对本实用新型提供的含锌高炉瓦斯灰冶炼装置进行说明。所述含锌高炉瓦斯灰冶炼装置,包括冶炼炉1、送料机构2、出料机构3和监控机构4,冶炼炉1呈长条形,下部埋设于地面下,冶炼炉1底面与水平面之间呈夹角设置,冶炼炉1的两端分别设有进料口5和出料口6,冶炼炉1用于冶炼含锌瓦斯灰并产出铁水和氧化锌粗品;送料机构2设于进料口5处,用于向冶炼炉1内输送高炉瓦斯灰干球;出料机构3设于出料口6处,用于承接从冶炼炉1内输出的铁水和液体炉渣;监控机构4设于冶炼炉1内侧顶部,用于监控冶炼炉1内温度和物料反应过程。
25.本实用新型提供的含锌高炉瓦斯灰冶炼装置,与现有技术相比,本实用新型含锌高炉瓦斯灰冶炼装置,冶炼炉1埋设在地面上并与水平面呈一夹角,物料从进料口5进入冶炼炉1后,由于倾斜设置冶炼炉1,物料在冶炼炉内反应后能从出料口6处输出,通过高温空气管12向冶炼炉1内输送高温空气,用于燃烧反应过程中产生的煤气,并放出热量,维持炉内高温环境,反应中产生的废气能够经过入余热回收、除尘系统后达标排放,含锌瓦斯灰通过送料机构2送入冶炼炉1内,反应后通过出料机构3输出,通过监控机构4可看出冶炼炉1内温度和反应过程,该长条形冶炼炉1呈卧式设置,能处理含锌瓦斯灰,解决了现有的高炉不适合冶炼高炉瓦斯灰的技术问题,具有长条形冶炼炉1可用于含锌瓦斯灰的冶炼,冶炼过程中反应稳定和快速的技术效果。
26.上述冶炼炉1的结构可选用现有技术中的冶炼炉1的炉体结构,其具备冶炼等的功能。在瓦斯灰投放入冶炼炉1之前,要把瓦斯灰制作成干球,再将干球投放入冶炼炉1内部,冶炼炉1平卧后,可使冶炼炉1内部的物料在反应中从进料口5侧不断向出料口6侧移动,这样当冶炼炉1内物料反应完成后,则铁水和炉渣就会汇集到出料口6侧,打开出料口6,铁水和炉渣连续排出。通过设计本实用新型的冶炼炉1,不用其他工具和操作工序,送料机构2和出料机构3使物料能够自动进入冶炼炉1,且反应后的物料能够自动排出,相比于高炉冶炼瓦斯灰,操作较方便。
27.作为本实用新型提供的含锌高炉瓦斯灰冶炼装置的一种具体实施方式,请参阅图
1至图4,送料机构2包括称重台21、料仓22和给料管路23,称重台21用于称重待进入冶炼炉1内的瓦斯灰的重量;料仓22用于盛放瓦斯灰干球,称重后瓦斯灰滚球放置在料仓22内暂存;给料管路23呈倾斜设置,一端连通料仓22、另一端连接进料口5,料仓22内的瓦斯灰干球经给料管路23输送至冶炼炉1内。要使瓦斯灰干球进入冶炼炉1中进行冶炼反应,必须是在一定重量的条件下进行的,或可理解为,进入冶炼炉1中的瓦斯灰干球是按照一定的重量事先要称重的,投入多少重量的瓦斯灰干球,则会产生多少重量的铁水、氧化锌粗品等,是有一定要求的,因此通过称重台21可以对瓦斯灰干球进行称重,称重后才能进入到冶炼炉1内。
28.瓦斯灰干球称重后进入到料仓22内,该过程可以用机械工具或其他输送机械来实现,位于料仓22内的瓦斯灰干球通过给料管路23自动下降并输送至进料口5,进而进入到冶炼炉1内部,料仓22呈广口型,给料管路23与进料口5之间为密封连接,给料管路23与水平面之间夹角约为45
°
。
29.作为本实用新型提供的含锌高炉瓦斯灰冶炼装置的一种具体实施方式,请参阅图1至图4,出料机构3包括避渣器31、铁水沟32和渣沟33,避渣器31与出料口6连通管并承接输出的铁水和液体炉渣,避渣器31用于分离铁水和液体炉渣;铁水沟32连通避渣器31的输出端,避渣器31将铁水分离后,铁水流向铁水沟32;渣沟33连通避渣器31的输出端,避渣器31将液体炉渣分离后,液体炉渣流向渣沟33。
30.避渣器31能够将铁水和液体炉渣分离,铁水流向铁水沟32,液体炉渣流向渣沟33,便于后期进行分类处理。具体的,避渣器31与出料口6之间通过沟渠连通。
31.本实用新型的出铁方式与高炉除铁方式不同,本实用新型的长条形冶炼炉正常生产时出铁口或出料口6处于常开状态,连续出铁、出渣,铁水和渣从长条形冶炼炉出料口6连续流出,进入避渣器31,再进入铁水沟32,通过避渣器31实现渣铁分离,铁水进入铁水沟32,液体炉渣进入渣沟33,液体炉渣经过水淬处理后,流入水渣池。
32.以上对炉体11输出的物料进行出料操作方式已属于现有技术,其具体的操作方式见现有技术操作,在此不再赘述,出料口6的设置位置位于紧邻地面以下且紧邻地面。
33.作为本实用新型提供的含锌高炉瓦斯灰冶炼装置的一种具体实施方式,请参阅图1至图4,监控机构4包括温度监控器41和成像仪42,温度监控器41设于冶炼炉1内侧顶部,用于监控冶炼炉1内的温度;成像仪42设于冶炼炉1内侧顶部,用于采集冶炼炉1内反应过程中的图像。通过红外成像仪42,可以定时或定期的拍摄冶炼炉1内部反应过程中的图像,通过图像的连续性,以便于工作人员进行观察反应过程等,具体的,红外成像仪42与冶炼炉1之间为可拆卸连接。
34.作为本实用新型提供的含锌高炉瓦斯灰冶炼装置的一种具体实施方式,请参阅图1至图4,冶炼炉1包括炉体11、高温空气管12和废气出管13,炉体11下部埋设于地面下、上部位于地面上;高温空气管12为多个,均设于冶炼炉1两侧并连通至冶炼炉1内,用于与高温空气源连通,高温空气源通过高温空气管12向冶炼炉1内输送高温空气;废气出管13为多个,均设于冶炼炉1上端并连通至冶炼炉1内,冶炼炉1内产生的废气通过废气出管13进入废气余热回收系统,经过降温、除尘后达标排放。由于炉体11的倾斜设置,则能使物料在炉体11内自由流动,便于反应后生产出预想的产品,且相比于高炉作业,能够对瓦斯灰进行充分的冶炼。
35.在本实施例中,通过高温空气管12向炉体11内部吹高温空气,空气中有氧气,能够
加速物料的反应,高温空气有一定的压力,通过高温空气管12输入炉体11,可起到对炉体11内部空气助燃预热的功能,炉体11内反应中产生的气体就会从废气出管13排出。
36.作为本实用新型提供的含锌高炉瓦斯灰冶炼装置的一种具体实施方式,请参阅图1至图4,沿进料口5至出料口6的方向冶炼炉1依次分为反应区111、过渡区112和渣铁分离区113,反应区111的底部置于地面下并呈长条槽型结构,进入至冶炼炉1内的物料在反应区111进行反应,进料口5位于反应区111的进料端;过渡区112的底部置于地面下并呈弯弧槽型结构,反应区111内的物料流入至过渡区112;渣铁分离区113的底部置于地面下并呈长条槽型结构,反应中产生的铁水和渣通过过渡区112流动至渣铁分离区113,在渣铁分离区113内渣与铁分离,出料口6位于渣铁分离区113的出料端,过渡区112两端分别圆弧过渡承接反应区111和渣铁分离区113。
37.反应区111、过渡区112和渣铁分离区113的底部设有槽型结构,便于物料的反应和流动,炉体11属于现有技术中的冶炼炉1,具备现有技术冶炼炉1的各种功能,故在此不再赘述。
38.具体的,其中80%的冶炼反应进度在反应器完成,有20%的冶炼反应进度及部分渣铁分离功能在过渡区112完成,炉渣与铁等金属分离是在渣铁分离区113完成的。
39.反应区111的宽度为3米,总长度为7
‑
8米,干球从进料口5进入炉体11内部,干球一边反应一边向过渡区112、渣铁分离区113流动,80%的冶炼反应进度在反应区111内完成;渣铁分离区113的宽度为1米,总长度为5
‑
6米,用于冶炼出的铁等高沸点金属与渣依靠重力分离,冶炼出的锌等低沸点金属从渣中蒸发分离;过渡区112为反应区111和渣铁分离区113的连接区域,为弯弧型的槽型结构,实现了一种“过渡”的功能,过渡区112的宽度由宽变窄,过渡区112承担20%的冶炼反应进度及部分渣铁分离功能。反应区111与过渡区112、过渡区112与渣铁分离区113之间都没有明显的界限,界限受操作条件、处理能力、干球冶金性能等因素有关。
40.冶炼炉1的处理能力:含碳25%
‑
40%,含铁35%
‑
45%(扣除碳以后,纯铁的含量)的干球15
‑
25t/h。
41.作为本实用新型提供的含锌高炉瓦斯灰冶炼装置的一种具体实施方式,请参阅图1至图4,埋设于地面下的反应区111、过渡区112和渣铁分离区113均为槽型结构,漏出于地面上的反应区111、过渡区112和渣铁分离区113为与槽型结构相适配的拱形结构,拱形结构与槽型结构相互对接扣合形成一体且内部为中空。
42.为安全起见,将炉体11分为上部和下部,即地上部分和地下部分,炉体11内部为中空,在正常操作下,渣的最高液面在地平面以下的200
‑
400mm处,炉体11的拱形结构和槽型结构(上部和下部)罩扣在一起形成整体,供瓦斯灰在炉体11内部反应。
43.反应区111的宽度为渣铁分离区113的宽度的2
‑
3倍。在本实施例中,反应区111的宽度与渣铁分离区113的宽度之比在2倍以上,都可以满足炉体11对瓦斯灰的冶炼要求,因此都在本实用新型的保护范围内。
44.作为本实用新型提供的含锌高炉瓦斯灰冶炼装置的一种具体实施方式,请参阅图1至图4,进料口5处设有用于向冶炼炉1内泵送氧气的氧气泵送组件7,泵送氧气后炉体11空气得到助燃预热,使炉体11内部温度维持平衡。通过高温空气管12向炉体11内部输送氧气,帮助炉体11内部空气助燃预热,维持炉体11内部空气温度恒定。氧气泵送组件7包括用于与
氧气源和进料口5连通的输氧管路、设置在输氧管路上的气泵以及设置在输氧管路上位于气泵和进料口5之间的气阀。通过输送管路向炉体11内部输送氧气,帮助炉体11内部空气助燃预热,维持炉体11内部空气恒定。
45.高温空气管12的数量为3
‑
10个,从热量衡算上分析,在反应区111需要补充的热量最多,尤其是在干球进口区域,因此,在干球的进料口5侧,高温空气管12的数量最多,并与氧气泵送组件7的配合运行,能够向炉体11内补充氧气和高温热空气,使炉体11内的温度维持稳定,用于保证干球的进料口5侧就具有1400℃
‑
1700℃的温度;另外,废气出管13的数量为2
‑
5个,均布于炉体11的顶部。
46.作为本实用新型提供的含锌高炉瓦斯灰冶炼装置的一种具体实施方式,请参阅图1至图4,进料口5位于冶炼炉1上埋深较浅的一端,出料口6位于冶炼炉1上埋深较深的一端。通过地面呈倾斜状设置的炉体11,使得炉体11内的物料能够在反应过程中从进料口5侧向出料口6侧移动,当物料移动到出料口6侧时,能够变成渣和铁水,以便于进行渣铁的分离。
47.作为本实用新型提供的含锌高炉瓦斯灰冶炼装置的一种具体实施方式,请参阅图1至图4,冶炼炉1包括厚钢板制成的外壳和铺设于外壳内壁上的耐火砖,外壳内部为中空并可用于冶炼作业。冶炼炉1外壳为耐高温锰钢板制成,并内衬耐火材料。
48.瓦斯灰在炉体11内反应,是需要一定的理论支撑,才能实现的,或可理解为该冶炼炉1的工作原理:
49.反应区111的槽型结构是为了保证粒径为30mm
‑
80mm的干球在炉体11内有7
‑
14分钟的停留时间,干球在渣层下面隔绝空气的条件下发生氧化还原反应,在高温下干球优先从表面反应,随着球内部温度的升高并升高的一定温度,干球内部也开始反应,反应过程中,碳逐渐损耗,球的表面和内部出现孔洞,反应产生的大量co和co2气体,加速干球的破裂,这样可对渣层产生剧烈的搅拌作用,使渣呈沸腾状,氧化铁逐步还原成氧化亚铁、铁,随着碳的损耗,氧化铁的还原,破碎的小球比重越来越大,反应速度很快,几分钟内就可能实现干球绝大部分被还原。
50.冶炼出的铁水等高沸点金属比重远远大于渣的比重,依靠重力与渣分离,也需要一定分离时间,按2
‑
4分钟的停留时间控制,其实在反应区111、过渡区112就已经开始了渣铁分离,因此,渣铁分离区113设计时间较短;裹在渣里的铁给一定的轻微扰动,有利于渣铁分离,因此,将渣铁分离区113的宽度适当缩小,可提高渣的适当的扰动度。
51.冶炼出的锌等低沸点金属,在渣中蒸发成气体,从渣中出来得以分离。
52.本实用新型适用于冶炼含锌等低沸点金属的含铁固体废料,弥补了高炉不适合冶炼含锌等固体含铁废料的缺陷,属于高炉冶炼技术的一个补充技术。
53.以上所述仅为本实用新型的较佳实施例而已,并不用以限制本实用新型,凡在本实用新型的精神和原则之内所作的任何修改、等同替换和改进等,均应包含在本实用新型的保护范围之内。