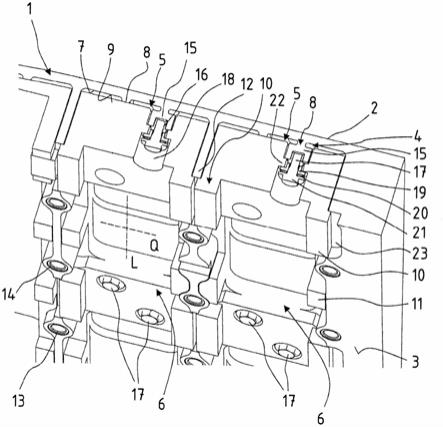
1.本发明涉及一种具有权利要求1前序部分的特征的金属型板。
背景技术:2.在连铸过程中铜铸型上的热应力会导致铜合金内部产生相当大的材料应力,尤其是在薄板坯连铸设备(d
ü
nnbrammen
‑
stranggieβanlagen)中。金属型板在其朝向熔体的热侧、即铸造侧承受极大的热应力,而朝向冷却水的后侧则基本上保持冷态。在只有几毫米厚的金属型板内,热侧和水冷后侧之间存在数百开尔文的温度梯度。这导致从铸造侧到后侧的厚度分布中的不同热膨胀。铸造侧试图膨胀,但同时被朝向冷却水的后侧阻止膨胀。由此产生高的内部材料应力。当内部材料应力超过铜合金的弹性极限时,这导致铸造侧的塑性变形,即所谓的鼓胀(bulging)。除了材料疲劳之外,塑性变形还引起在金属型宽边和窄边之间的间隙形成。液态钢可渗入金属型窄边和宽边之间产生的间隙中。这会导致在宽度调整期间金属型板上的损伤。在不利的情况下,金属型下面的坯壳(strangschale)会在板坯的外角区域中裂开。
3.已知通过及时对铸造表面进行再加工来通过预防性维护防止间隙形成。基于再加工减小的壁厚减少了金属型的剩余使用寿命。这又导致维护间隔缩短和连铸设备的可用性降低。
4.为了防止金属型板在铸造侧上的变形(鼓胀),金属型板与后侧支撑板或所谓的水箱的紧固点彼此之间的距离较小并且数量较多。彼此之间距离较小的紧固点预定特定的冷却通道走向。根据冷却通道的布置,在整个热侧上看,散热可能具有不希望的不均匀性。不均匀的散热在铸造期间又引起材料应力,尤其是在金属型板的弯月形区域(meniskusbereich)中。材料应力可如此之高,以至于发生塑性变形。在极端情况下,铜合金甚至会软化。此外,存在由金属型板的热侧和冷侧之间的温度梯度引起的金属型板弹性变形的基本风险。
5.从de 10 2016 124 801 b3已知,通过冷却通道中的嵌件提高冷却水的流速。由此形成冷却间隙,水可在高压和高流速下通过这些冷却间隙。这些减少冷却通道局部横截面的嵌件部分桥接相对宽的冷却通道。由此需要更少的单个嵌件。一方面,尽可能大的嵌件是适宜的,因为由此简化了冷却板的后侧,另一方面,通过非常宽的冷却通道和相应宽的嵌件增加了鼓胀的风险。
6.建议通过夹具或紧固螺栓将嵌件与冷却面中的紧固点连接。还建议避免在金属型板通过紧固螺栓与支撑板或水箱连接的那些区域中出现热点。为此,至少一个冷却通道从紧固点朝向金属型板的与后侧的支撑板或水箱相对置的铸造侧看应延伸直到紧固点下方。由此可改善紧固点底座区域中的冷却。
7.jp 2006 320 925 a公开了紧固点下方的附加冷却通道。紧固点用于容纳用于将金属型板与支撑板连接的紧固螺栓。与de 10 2016 124801 b3不同,没有加宽外部邻接的冷却通道以使其延伸到紧固点下方,而是在紧固点下方形成另一冷却通道。但制造相对复
杂。
8.de 10 2004 001 928 a1公开了一种用于连铸金属的液冷金属型,其中金属型板借助紧固螺栓与支撑结构连接。金属型板或金属型管与支撑结构彼此无夹紧地连接,在支撑结构和金属型板或金属型管之间存在工作间隙。工作间隙位于紧固点侧向并且尤其是位于设置在那里的螺纹嵌件侧向,所述螺纹嵌件是紧固点的一部分或形成紧固点。
技术实现要素:9.本发明所基于的任务是提供一种金属型板,其中鼓胀的风险被降低。应尽量减少连铸过程中金属型板的变形。
10.所述任务在具有权利要求1的特征的金属型板中解决。
11.从属权利要求涉及本发明的有利扩展方案。
12.根据本发明的金属型板具有铸造侧和背离铸造侧的后侧。金属型板由铜合金制成。它可与其它具体的板组装成金属型,如在熔融金属的连铸中所使用的。在后侧中设置有至少一个朝向后侧敞开的冷却通道。该冷却通道具有与铸造侧相对置的冷却面。在冷却通道中设置有嵌件,以便在嵌件的内表面和冷却面之间形成冷却间隙。在铸造操作期间,冷却水流过该冷却间隙,以便通过冷却面冷却金属型板并且由此也冷却铸造侧。嵌件通过紧固螺栓与冷却面中的紧固点连接。冷却面区域也可称为冷却的槽底。本发明不排除在嵌件和金属型板之间存在其它连接点。优选嵌件仅通过冷却面中、即冷却通道中的紧固点与金属型板连接。
13.通常,嵌件并不在冷却面区域内与金属型板连接,而是在冷却面区域之外。但通过将紧固点直接设置在冷却面上或中,在冷却通道的相邻壁之间的区域被桥接。在冷却管道壁的区域中设有固定点,通过这些固定点金属型板可与由钢制成的承载的支撑板或水箱螺接。为了更好地区分,在本发明中,将用于连接金属型板与支撑板的点称为固定点,而将用于连接嵌件与金属型板的点称为紧固点。在两种情况下,连接以相同的方式进行,即,通过紧固螺栓或固定螺栓,也就是通过螺栓连接进行。在本发明中,紧固螺栓可作为定位螺栓(stehbolzen)设置在金属型板上,从而必须将螺母拧到紧固螺栓上。然而,反过来也可以是具有螺栓头并在紧固点或固定点处拧入螺纹容纳部中的紧固螺栓。定位螺栓和螺栓的混合方案是可能的。
14.紧固点的根据本发明的布置的主要优点在于,本就向后支撑在支撑板上的嵌件不仅用于确定冷却间隙的横截面并提高流速,而是更多地有助于防止通过冷却间隙区域中的鼓胀而产生塑性变形。冷却面区域中的紧固点或紧固相当显著地提高了整个金属型板在铸造使用期间的尺寸稳定性,尤其是在设置多个紧固点的情况下。优选至少设置与固定点一样多的紧固点。连接点(包括固定点在内的紧固点)数量的加倍使得金属型板被极大地加固,而金属型板的壁厚不必朝向铸造侧增加。由此,大量热量仍然可在很短的时间内散去,降低了塑料变形的风险以及在连铸金属型的宽边和窄边之间形成间隙的风险。如果很少或没有形成间隙,则不需要或不再需要该范围中的预防性维护。可根据需要以更长的时间间隔对铸造表面进行再加工。金属型的使用寿命由此总体上更长,从而提高了连铸设备的可用性。
15.在实际的实施方式中,紧固点尤其是相对于冷却面的岛状凸起。冷却面优选是基
本上平坦的面。在冷却面内可设置各个肋条,其指向嵌件内表面。在这些肋条或冷却面与内表面之间形成各个冷却间隙,冷却水流过这些冷却间隙。紧固点优选位于肋条区域中,从而相应冷却间隙始终可基本上笔直地延伸。冷却面中的各个肋条优选也笔直地并且彼此平行地、即沿相应冷却通道的纵向方向延伸。在一个冷却通道内优选设置两个或三个肋条。相应于肋条的数量,在冷却通道内紧固点位于每个肋条的区域中。因此,紧固点沿通道横向方向的间距相应于肋条的间距。所述间距分别涉及中心距。优选存在两个沿横向方向彼此间隔开的紧固点。
16.冷却面中的岛状凸起还具有以下优点:紧固并非通过嵌入冷却面中进行,而是通过冷却面上的紧固点进行。由此,在铸造侧和冷却面之间金属型板在紧固点区域中的厚度至少不小于该冷却通道的其它区域中的厚度。因此,在紧固点区域中不发生材料削弱。这又在力传递方面具有优势并且在热传递的均匀化方面也具有优势。保留了用于再加工铸造侧的材料储备。
17.为了最佳的冷却功率,希望冷却面下方的金属型板的厚度变化不要太大。尤其是应尽可能不产生热点,即散热减少的点。从理论上讲,这种热点可能会出现在非常大面积的岛状凸起中,因为冷却水不会到达岛状凸起的核心区域。因此,这种紧固点下方的散热可能减少。但根据本发明规定,从紧固点朝向铸造侧看,至少一个冷却间隙延伸直到紧固点下方。紧固点在一定程度上具有侧凹。侧凹可以在一侧或两侧。如果紧固点设置在肋条的中央,则可这样设计侧凹,使得肋条也在紧固点下方以恒定的宽度和/或高度延伸,而紧固点本身仅在肋条上方开始。由此,紧固点下方的肋条以与紧固点之外相同的方式被冷却。不产生热点。散热在肋条的整个长度上保持均匀和一致。
18.所述多个紧固点优选不仅沿冷却通道的纵向方向而且也沿冷却通道的横向方向彼此偏移地设置。如上所述,它们尤其是相对于相应的肋条对齐设置。两个相邻肋条的紧固点不必强制位于相同的长度区段中,即沿横向方向直接并排设置。它们尤其是可沿纵向方向彼此偏移地设置。因此,在两个肋条的基础上产生一种紧固点的布置,其不仅增加了横向方向上而且也增加了纵向方向上的紧固点数量。相应紧固点尤其是沿纵向方向看与固定点间隔开,金属型板通过所述固定点固定在支撑板上。紧固点例如可以锯齿形图案或梯形图案设置。目的是在冷却通道区域中实现薄壁金属型板的尽可能均匀的支撑。在需要时,各个紧固点可位于相同高度上,即设置在相同的长度区段中。
19.嵌件在安装位置中支撑在支撑板上是现有技术。它们因此在其边缘区域中的支撑突出部上至少区段地具有在冷却通道的从金属型板的后侧到冷却面的整个深度上延伸的高度或厚度。
20.在本发明中规定,延伸直到金属型板后侧的后部的支撑突出部优选设置在紧固点所在的冷却通道的长度区段中。由此,金属型板可直接通过肋条或紧固点支撑在设置在后侧的支撑板上。如果嵌件搭接限定冷却通道的肋条或概括地说搭接冷却通道的壁,则嵌件可吸收由铸造侧的热膨胀产生的拉力。金属型通过冷却通道中的紧固点不能从嵌件上抬起并且嵌件不能向铸造侧方向移动,因为它支撑在肋条或壁上。支撑突出部可搭接肋条或壁。它们可搭接肋条的较低高度的区域或嵌入金属型板后侧的凹窝中,使得它们不突出于后侧。支撑突出部在此情况下具有双重功能,即它们吸收拉力和压力并且可根据邻接面(支撑板的前侧/肋条的后侧)的位置将所述力传递到相邻的构件(金属型板、支撑板)。
21.彼此直接相对置的支撑突出部尤其是位于嵌件的两个纵向侧上,即在紧固点的高度处。当紧固点彼此非常靠近时,即当紧固点沿纵向方向具有小的间距时,支撑突出部可彼此合并或者可设置一个唯一的、相应更宽的支撑突出部。
22.通过彼此相对置的支撑突出部可将作用在紧固点上的力均匀地在嵌件的左侧和右侧从金属型板经由嵌件传导到后支撑板中。优选两个直接相对置的支撑突出部之间的区域构造为加厚的轭(joch),在其中设置有一个或两个紧固螺栓。因此,优选嵌件在在纵向侧相对置的支撑突出部之间比在沿纵向方向设置在支撑突出部旁边的区域中具有更大的厚度。通过更大的厚度在紧固螺栓区域中或在紧固点区域中实现嵌件的更高的弯曲刚度。
23.在有利的扩展方案中,这样设计金属型板和嵌件之间的连接,使得在铸造条件下不会阻碍金属型板基于高热影响而膨胀。在本发明的一种扩展方案中,这可通过在紧固点区域中在金属型板和嵌件之间设置工作间隙来实现。工作间隙非常小。它应确保金属型板在紧固点处相对于嵌件浮动地支承。在此,紧固点、即金属型板应可横向于冷却通道、即侧向地在冷却通道的纵向方向和横向方向上无夹紧地移动。浮动支承不应理解为金属型板通过附加的自由度而趋于鼓胀并且因此发生塑性变形。这只是为了防止在金属型板内产生额外的应力。因此,紧固螺栓位于足够大的通孔中,该通孔如此之大,使得金属型板连同设置在其上的紧固螺栓可横向于嵌件,但只能有限地垂直于嵌件移动。嵌件相对于金属型板的位置通过支撑板在后侧上的贴靠预先确定。
24.在本发明的一种扩展方案中,紧固螺栓在插入螺栓防松元件的情况下与紧固点螺接。尤其是螺栓防松元件支撑在位于螺栓头和紧固点之间的套筒上。在此情况下,具有套筒和螺栓防松元件的紧固螺栓以及金属型板形成一个单元,该单元可相对于嵌件横向移动。
25.紧固螺栓设置在其中的通孔优选在直径中具有阶梯,从而形成用于螺栓头或套筒的突出凸缘的贴靠面,螺栓头支撑在该凸缘上。贴靠面与工作间隙相结合定义金属型板垂直于冷却面的自由度。在此,即使是最小的间隙也足以允许金属型板相对于嵌件横向移动,而不会增加鼓胀的风险。工作间隙的宽度优选小于0.2mm。
26.尽管冷却剂可渗入工作间隙,但本发明意义上的工作间隙并非构造为冷却剂通道,而是具有明显更小的宽度。原则上,在本发明范围中,可不同地设置工作间隙,并且紧固点的布置和数量也可变化,以实现金属型板的尽可能均匀的冷却和恒定的刚度。
27.在本发明范围中,表述“金属型板和嵌件之间的无夹紧连接”应理解为,当金属型板基于热影响在纵向方向或横向方向上相对于嵌件移动时,金属型板的铜材料中只产生轻微的材料应力。嵌件和紧固点的接触在具有小的摩擦系数的同时并不关键。仅应优选避免在该区域中通过嵌件和金属型板之间的高预应力而引起的夹紧和锁住。
28.最后,如果紧固螺栓的螺栓头完全沉入嵌件中的阶梯通孔中,则被认为是特别有利的。嵌件在通孔区域中稍大的厚度是因为支撑突出部设置在嵌件的纵向侧上并且应在紧固点和支撑突出部之间得到嵌件的高抗扭刚度。在该区域中嵌件用作轭。但这并不意味着必须使用特别长的螺栓。为了节省材料,螺栓头可完全沉入通孔中。
29.通孔优选在两侧具有阶梯。一方面,螺栓头可沉入通孔中。在中间区域中通孔具有向内指向的凸缘形式的贴靠面。在通孔或凸缘的相对置侧上设置有岛状凸起的紧固点。紧固点优选完全嵌入嵌件中。在紧固点的圆周侧具有足够宽的间隙,使得金属型板可横向于通孔移动。
附图说明
30.图1示出现有技术并且用于解释技术背景。它不是要求保护的实施方式。下面借助图2中纯粹示意性示出的实施例详细阐述本发明。
31.图1以透视图且部分以剖视图示出金属型板1的局部区域。用于解释图1的金属型板1的附图标记在根据图2的根据本发明的金属型板1中继续用于基本上内容相同的部件。
具体实施方式
32.图1的金属型板1具有背离观察者的铸造侧和朝向观察者的后侧2。在安装位置中,后侧2支撑在未详细示出的支撑板上。在铸造操作期间,铸造侧2上的热熔体应这样冷却,即,热量被金属型板1吸收并经由通过位于冷却通道5内的冷却间隙4的冷却水导走。该金属型板1的铸造方向相应于竖直方向。冷却通道5因此平行于铸造方向从上向下延伸。它们彼此平行延伸。
33.在冷却通道5内分别设有嵌件6,这些嵌件向后侧3限定冷却间隙4。嵌件6在横截面中构造为u形。它们朝向冷却间隙4的内表面7贴靠在肋条8上,所述肋条从冷却通道5的冷却面9指向金属型板1的后侧3方向。肋条8决定冷却间隙4的高度。肋条8彼此的间距决定冷却间隙4的宽度并且因此总体上决定冷却间隙4的横截面积。在铸造操作期间,在冷却间隙4中存在高压。因此,嵌件6在所述操作期间支撑在未详细示出的支撑板上。为此它们具有多个彼此间隔开设置的支撑突出部10,这些支撑突出部延伸直至金属型板1的后侧3。嵌件6在其纵向侧上是轮廓化的并且具有支撑突出部11,这些支撑突出部朝向纵向侧这样成型,使得它们适配于冷却通道5的壁的轮廓,从而嵌件6既在纵向方向l上也在横向方向q上在冷却通道5内定位定向(lageorientiert)。嵌件6只能朝向后侧3从冷却通道5被取出。
34.两个相邻的冷却通道5通过肋条12彼此分开。在肋条12内设有彼此间隔开的固定点13。它们具有螺纹嵌件14,通过螺纹嵌件可将金属型板1与嵌件6一起拧紧到待设置在后侧上的支撑板上。由此,相应嵌件6也在冷却通道内被精确地定位定向和保持。
35.根据本发明的金属型板1的主要区别在于,在冷却通道5的相应冷却面9上设置有具有螺纹嵌件16的紧固点15。紧固点15朝向金属型板1的后侧3。紧固螺栓17设置在相应嵌件6中的通孔18中并且拧入紧固点15的螺纹嵌件16中。紧固螺栓17的螺栓头21通过套筒19和螺栓防松元件20贴靠在紧固点15上。通孔18中的凸缘22具有间隙地保持在紧固点15和套筒19之间。以一种未详细示出的方式,在紧固点和套筒19之间存在宽度小于2/10mm的狭窄工作间隙。此外,通孔18的直径在其整个长度区域上确定为如此大,使得紧固点15可相对于嵌件6进行轻微侧向移动。以该方式避免了嵌件6和金属型板1之间的热致应力。
36.紧固点15分别位于肋条8区域中。由于存在彼此平行间隔开的两个肋条8,因此存在两排紧固点15。相邻排的紧固点15沿冷却通道5的纵向方向l彼此偏移地设置。由于限定冷却间隙4的肋条8彼此以大约相同的间隔设置,因此相应紧固点15与相应通道5的左壁和右壁的距离大约相同并且因此与设置在那里的固定点13的距离也大约相同。由此得到紧固点15或固定点13的高的密度,通过这些紧固点或固定点金属型板1可与嵌件6或支撑板连接。
37.紧固点15是岛状凸起。它们开始于距冷却面17一定距离处,即肋条8结束的地方。由于紧固点15具有比肋条8更大的宽度,因此在从后侧向铸造侧的垂直视向上紧固点15具
有侧凹。分别相邻的冷却间隙4延伸直到相应紧固点15下方,但仅达到肋条18的宽度预定的范围。在图2的剖视图中,紧固点15看起来是在侧向收窄的。因此,紧固点15下方的这些收窄部具有彼此径向相对置并且通过肋条彼此分开的弓形(segmenten)形状。肋条8在某种程度上是紧固点15和冷却面9之间的连接元件。
38.通孔18位于两个径向相对设置的支撑突出部10之间,所述支撑突出部分别设置在嵌件6的一个纵向侧上。与前述支撑突出部10间隔开地还存在另外的支撑突出部11。如在现有技术的实施方式中那样,支撑突出部10、11用于将嵌件6向后支撑在未详细示出的支撑板上。较宽的支撑突出部11位于相应嵌件6比沿纵向方向l相邻的嵌件6区域具有更大的厚度之处。其它区域是指其中没有紧固点15或通孔18的那些长度区段。在相对置的、较宽的支撑突出部10之间的较厚区域用作轭并且设置用于吸收由金属型板1在冷却面9区域中并且通过紧固点15施加在嵌件6上的力。所提到的支撑突出部10之间的区域是特别抗弯并且坚实的。在嵌件6的仅具有限定冷却间隙4的功能但不通过附加紧固点15吸收力的其余区域中,不需要这样坚实的支撑。与此相应,那里的支撑突出部11的横截面尺寸较小。
39.嵌件6不仅可吸收从冷却面9上的肋条8作用在嵌件6方向上的力并将该力传递到支撑板,而且也可吸收指向相反方向的力。为此,支撑突出部10搭接两个冷却通道5之间的肋条12。在该区域中,嵌件6比冷却通道5更宽。肋条12在该区域中具有稍低的高度。由此支撑突出部10不突出于后侧3,而是在与固定点13和肋条12的其余区域相同的平面中结束。如果没有肋条,如在边缘侧冷却通道5的情况下,支撑突出部10可嵌入后侧的凹窝23中,该凹窝是后侧3中的凹部。因此,支撑突出部10不突出于后侧3。
40.还可以看出,紧固螺栓17的螺栓头21设置为完全沉入嵌件6的阶梯状的通孔18中。
41.根据本发明的金属型板1基于嵌件6之间的多个紧固点15而具有更高的弯曲刚度,以避免因热影响引起的塑性变形。与现有技术相比,散热的均匀性得以保持。
42.附图标记列表
[0043]1ꢀꢀꢀꢀꢀ
金属型板
[0044]2ꢀꢀꢀꢀꢀ
金属型板的铸造侧
[0045]3ꢀꢀꢀꢀꢀ
金属型板的后侧
[0046]4ꢀꢀꢀꢀꢀ
冷却通道中的冷却间隙
[0047]5ꢀꢀꢀꢀꢀ
金属型板中的冷却通道
[0048]6ꢀꢀꢀꢀꢀ
冷却通道中的嵌件
[0049]7ꢀꢀꢀꢀꢀ
嵌件的内表面
[0050]8ꢀꢀꢀꢀꢀ
内表面上的肋条
[0051]9ꢀꢀꢀꢀꢀ
冷却通道的冷却面
[0052]
10
ꢀꢀꢀꢀ
支撑突出部
[0053]
11
ꢀꢀꢀꢀ
支撑突出部
[0054]
12
ꢀꢀꢀꢀ
金属型板的肋条
[0055]
13
ꢀꢀꢀꢀ
固定点
[0056]
14
ꢀꢀꢀꢀ
固定点中的螺纹嵌件
[0057]
15
ꢀꢀꢀꢀ
紧固点
[0058]
16
ꢀꢀꢀꢀ
紧固点中的螺纹嵌件
[0059]
17
ꢀꢀꢀꢀ
紧固点中的紧固螺栓
[0060]
18
ꢀꢀꢀꢀ
通孔
[0061]
19
ꢀꢀꢀꢀ
套筒
[0062]
20
ꢀꢀꢀꢀ
螺栓防松元件
[0063]
21
ꢀꢀꢀꢀ
紧固螺栓的螺栓头
[0064]
22
ꢀꢀꢀꢀ
通孔中的凸缘
[0065]
23
ꢀꢀꢀꢀ
金属型板的后侧中的凹窝
[0066]
l
ꢀꢀꢀꢀꢀ
冷却通道的纵向方向
[0067]
q
ꢀꢀꢀꢀꢀ
冷却通道的横向方向