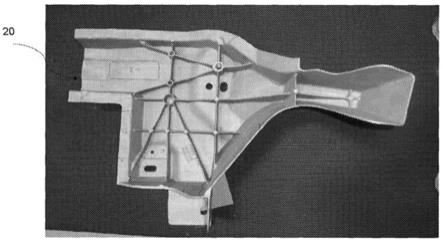
用于结构高压真空压铸应用的铝合金
1.相关申请的交叉引用
2.本pct国际专利申请要求于2019年2月8日提交的题为“aluminum alloys for structural high pressure vacuum die casting applications”的美国临时专利申请序列号62/803,000的权益和优先权,其全部公开内容通过引用并入本文。
3.发明背景
1.技术领域
4.本发明涉及铝合金、至少部分地由再利用材料和铝合金生产的部件、和制造其的方法。
2.
背景技术:5.本部分提供了与本公开相关的背景信息,其不一定是现有技术。
6.铸造、挤出和锻造是流行的生产工艺,其中材料被熔化、成形、并且使其冷却并凝固成制品。在这样的工艺中使用的一种材料为铝,并且更特别地为已表明表现出优异的机械特性、良好的可铸性(流动性)和通过热处理而硬化的能力(析出硬化)的aural系列铝合金。由aural系列合金生产的制品通常通过高压压铸过程形成。虽然表现出这些品质,但是aural系列合金是昂贵的,并且通常以比其他更常见的铝合金更低的量生产。此外,在某些过程例如熔炼期间aural系列合金的可加工性可能是困难的。
7.已经尝试消除aural系列合金的上述缺点。一些努力包括对更容易且更廉价去生产但仍复现了aural系列合金的材料品质的不同合金进行开发。另一些努力包括对生产aural系列合金的过程的改进以使生产过程更廉价且更有效。例如,一种尝试包括使用再利用材料作为原材料。再利用材料或再利用材料也称为废料或“脏材料”,并且可以大大降低生产的成本,特别是对于更昂贵的材料例如铝来说。铝是可无限再利用的,并且再利用过程仅使用原生铝生产中所需能量的5%。因此,再利用铝的碳足迹仅为原生铝的碳足迹的5%。在一些常规生产过程期间,将再利用材料添加至炉中的熔融aural系列合金材料中并混合。基于化学组成的差异,以特定比例将再利用材料添加至总熔融材料中。除了再利用材料之外,还添加中间合金(master alloy)添加剂例如硅、锰、镁和锶以补偿再利用材料与aural系列合金材料的组成之间的差异。
8.虽然该再利用过程可以以较低的成本生产与aural系列合金相当的合金,但是存在某些缺点。例如,中间合金是昂贵的,并且其旨在用于小的调节。中间合金在引入炉期间也倾向于至少部分地燃烧。此外,在对材料进行再利用的过程期间,例如使用化学光谱盘和/或其他光学发射光谱仪准确测量炉中的组成需要时间。还存在所生产的合金可能在特定aural系列合金化学组成的期望规格之外的风险。在这种情况下,用该合金制成的所有铸件将不满足材料特性要求,并且将不得不报废。
9.因此,持续期望开发并进一步改进能够使用再利用材料生产在aural系列合金规格内的合金的方法。
技术实现要素:10.本部分提供了与本公开相关的发明构思的一般概述,并且不旨在解释为其所有方面、目的、特征和优点的完整且全面的列举。
11.本发明的一个方面提供了制造混合材料的方法。所述方法包括将再利用铝合金与改善铝合金混合以形成混合材料。基于再利用铝合金的总重量,再利用铝合金以重量百分比(重量%)计包含6.5重量%至7.5重量%的硅、最高达0.25重量%的铁、最高达0.2重量%的铜、最高达0.1重量%的锰、0.25重量%至0.45重量%的镁、最高达0.1重量%的锌、最高达0.2重量%的钛、最高达0.15重量%的量的另外的元素、和余量的铝。基于混合材料的总重量,混合材料以重量百分比(重量%)计包含6.0重量%至8.0重量%的硅、最高达0.25重量%的铁、0.40重量%至0.60重量%的锰、0.1重量%至0.60重量%的镁、0.01重量%至0.03重量%的锶、和最高达0.15重量%的钛、最高达0.15重量%的量的另外的元素、以及余量的铝;或者基于混合材料的总重量,混合材料以重量百分比(重量%)计包含9.5重量%至11.5重量%的硅、最高达0.25重量%的铁、0.40重量%至0.60重量%的锰、0.1重量%至0.60重量%的镁、0.01重量%至0.025重量%的锶、和最高达0.12重量%的钛、最高达0.15重量%的量的另外的元素、以及余量的铝。
12.本发明的另一个方面提供了混合材料,基于混合材料的总重量,混合材料以重量百分比(重量%)计包含6.0重量%至8.0重量%的硅、最高达0.25重量%的铁、0.40重量%至0.60重量%的锰、0.1重量%至0.60重量%的镁、0.01重量%至0.03重量%的锶、和最高达0.15重量%的钛、最高达0.15重量%的量的另外的元素、以及余量的铝;或者基于混合材料的总重量,混合材料以重量百分比(重量%)计包含9.5重量%至11.5重量%的硅、最高达0.25重量%的铁、0.40重量%至0.60重量%的锰、0.1重量%至0.60重量%的镁、0.01重量%至0.025重量%的锶、和最高达0.12重量%的钛、最高达0.15重量%的量的另外的元素、以及余量的铝。混合材料通过将再利用铝合金与改善铝合金混合来形成。基于再利用铝合金的总重量,再利用铝合金以重量百分比(重量%)计包含6.5重量%至7.5重量%的硅、最高达0.25重量%的铁、最高达0.2重量%的铜、最高达0.1重量%的锰、0.25重量%至0.45重量%的镁、最高达0.1重量%的锌、最高达0.2重量%的钛、最高达0.15重量%的量的另外的元素、和余量的铝。
13.本发明的另一个方面提供了制造用于车辆的部件的方法。所述部件由混合材料形成,基于混合材料的总重量,所述混合材料以重量百分比(重量%)计包含6.0重量%至8.0重量%的硅、最高达0.25重量%的铁、0.40重量%至0.60重量%的锰、0.1重量%至0.60重量%的镁、0.01重量%至0.03重量%的锶、和最高达0.15重量%的钛、最高达0.15重量%的量的另外的元素、以及余量的铝;或者基于混合材料的总重量,混合材料以重量百分比(重量%)计包含9.5重量%至11.5重量%的硅、最高达0.25重量%的铁、0.40重量%至0.60重量%的锰、0.1重量%至0.60重量%的镁、0.01重量%至0.025重量%的锶、和最高达0.12重量%的钛、最高达0.15重量%的量的另外的元素、以及余量的铝。混合材料通过将再利用铝合金与改善铝合金混合来形成。基于再利用铝合金的总重量,再利用铝合金以重量百分比(重量%)计包含6.5重量%至7.5重量%的硅、最高达0.25重量%的铁、最高达0.2重量%的铜、最高达0.1重量%的锰、0.25重量%至0.45重量%的镁、最高达0.1重量%的锌、最高达0.2重量%的钛、最高达0.15重量%的量的另外的元素、和余量的铝。所述方法还包括对混
合材料进行铸造以形成部件。
14.根据本文所提供的描述,其他适用领域将变得明显。本发明内容中的描述和特定示例仅旨在用于说明的目的,而不旨在限制本公开的范围。
附图说明
15.本文中所描述的附图仅用于所选实施方案的说明性目的,并且不旨在限制本公开的范围。通过参照结合附图的以下描述,将更容易理解与本公开相关的发明构思,其中:
16.图1示出了至少部分地由包含再利用合金和改善铝合金并且满足aural系列合金规格的混合材料形成的一个示例性部件;
17.图2示出了根据一个示例性实施方案的再利用铝合金的碎片;
18.图3a和3b提供了示出根据一个示例性实施方案的再利用铝合金的孔隙率的显微视图;
19.图4a至4d示出了根据一个示例性实施方案的混合材料在各种过程加工之后的枝晶臂间距(das);
20.图5a至5i示出了根据一个示例性实施方案的高压真空压铸过程的步骤;
21.图6是示出常规高压压铸hpdc、真空辅助高压压铸和高真空高压真空压铸之间的差异的图表;
22.图7a至7h为可以由混合材料形成的示例性部件;以及
23.图8提供了铝合金的残渣因子的描述。
具体实施方式
24.现在将参照附图更全面地描述示例性实施方案。通常,主题实施方案涉及至少部分地由再利用材料和改善合金生产的部件、改善合金、以及将改善合金与再利用材料混合的方法。然而,仅提供示例性实施方案使得本公开将是透彻的,并且将向本领域技术人员充分地传达范围。阐述了许多具体细节,例如特定部件、装置和方法的实例,以提供对本公开的实施方案的透彻理解。对于本领域技术人员而言将明显的是,不需要采用具体细节,示例性实施方案可以以许多不同的形式体现,并且两者均不应被解释为限制本公开的范围。在一些示例性实施方案中,没有详细地描述公知的过程、公知的装置结构和公知的技术。
25.本公开提供了由再利用铝合金和改善铝合金形成的混合材料、由再利用铝合金和改善铝合金生产混合材料的方法、由混合材料形成的部件、以及由混合材料生产部件的方法。该方法允许相对廉价且有效地生产表现出优异的材料特性优选与由aural系列合金形成的部件相似或相同的部件。
26.图1示出了由由再利用铝合金和改善铝合金形成的混合材料制成的部件20。在该实例中,部件为用于车辆的车身的结构部件,具体地为前车身铰链柱。混合材料可以用于形成用于车辆应用的各种其他部件。所述部件至少部分地由混合材料形成,但优选完全地由混合材料形成。
27.再利用铝合金的化学组成可以例如通过光学发射光谱仪测量,并且可以设定改善铝合金的组成以实现具有期望组成的混合材料。所得混合材料通常且优选满足aural 2、aural 5s或另外aural系列合金的规格。
28.用于形成部件的再利用铝合金优选在引入炉中之前被清洁并切碎。在一个优选实施方案中,再利用铝合金包括再利用356铝合金,优选从使用过的车轮和/或轮辋获得的a356.2铝,如图2中所示。将使用过的车轮或轮辋压碎、切碎(或碎裂),并清洁,而不需要熔化并铸造成锭,进一步减少了碳足迹。在碎裂之后,将再利用铝合金放入炉中,使其熔化,并与改善铝合金混合。
29.由铝合金形成的铸件可能极大地受熔融混合合金中氧化物膜和杂质的存在的影响。在某些实施方案中,随着经破碎和经压碎的车轮的表面积的增加,可能出现略微高的氧化物和其他夹杂物的潜在风险。为了满足拉伸测试的astm要求,该方法可以包括在对再利用铝合金进行铸造或混合之前的对熔体的适当清洁、晶粒细化添加和改性。
30.以下段落提供了再利用合金二者的示例性实施方案。然而,这些示例性实施方案是出于说明的目的而提供的,并且不旨在穷举或限制本公开。这些组成可以例如通过使用光学发射光谱法现场测量。
31.再利用铝合金通常为再利用356.2铝合金,并且具有与原生且未使用的a356.2的组成非常类似的组成。唯一的典型例外是fe含量,基于合金的总重量,所述fe含量以重量百分比(重量%)计通常在平均为0.11%至0.14%的范围内(与a356.2的0.12%极限相比)。当车轮由a356.2制成时,其通常包括甚至比0.12%极限更高的关于fe的纯度规格。再利用356.2合金目前可以适合于改善的处理和物流的袋的形式获得。如有必要,该方法可以包括将再利用356.2合金与原生铝混合/稀释以精确地遵守a356.2化学成分,尽管对于大多数实施方案来说这不是必需的。
32.根据该实施方案,其中再利用铝合金为356.2铝,并且基于合金的总重量,再利用356.2铝以重量百分比(重量%)计大约或精确地包含:硅(6.81重量%);铁(0.156重量%);铜(0.0467重量%);锰(0.0213重量%);镁(0.353重量%);锌(0.0072重量%);钛(0.1015重量%);以及剩余部分为铝和另外的微量元素。
33.根据另一个实施方案,基于合金的总重量,再利用356.2铝以重量百分比(重量%)计大约或精确地包含:硅(7.0重量%);铁(0.11重量%);铜(0.004重量%);锰(0.006重量%);镁(0.334重量%);锌(0.005重量%);钛(0.12重量%);另外的元素(0.03重量%);以及剩余部分为铝。
34.在包括再利用356.2铝合金的实施方案中,优选的是炉足够热使得在熔化之后,基于合金的总重量,再利用356.2铝合金以重量百分比(重量%)计大约或精确地包含:硅(7.0重量%);铁(0.15重量%);铜(0.011重量%);锰(0.006重量%);镁(0.348重量%);锌(0.005重量%);钛(0.10重量%);另外的元素(0.03重量%);以及剩余部分为铝。
35.然而,更优选的是,在包括再利用356.2铝合金的实施方案中,将再利用356.2铝合金脱气。例如,可以用帕尔默(palmer)旋转脱气机对再利用356.2铝合金进行氩脱气约20分钟。在脱气之后,基于合金的总重量,再利用356.2铝合金以重量百分比(重量%)计大约或精确地包含:硅(7.0重量%);铁(0.15重量%);铜(0.006重量%);锰(0.006重量%);镁(0.338重量%);锌(0.005重量%);钛(0.13重量%);另外的元素(0.03重量%);以及剩余部分为铝。
36.总之,基于再利用铝合金的总重量,再利用356.2铝合金以重量百分比(重量%)计通常包含以下优选范围和近似值的以下元素(它们在再利用车轮中是典型的,并且可以代
表优选实施方案中的标称组成):硅(最少6.5重量%,最多7.5重量%);铁(最少0.13重量%,最多0.25重量%);铜(最多0.2重量%或最多0.10重量%);锰(最多0.1重量%或最多0.05重量%);镁(0.25重量%至0.45重量%或0.3重量%至0.45重量%);锌(最多0.05重量%或最多0.1重量%);钛(最多0.1重量%或最多0.2重量%);以及剩余部分为铝和另外的微量元素。
37.下表1至3提供了再利用铝合金的具体示例性组成。再利用铝合金可以包括在a356.0 astm b108、a356.1 astm b179或a356.2 astm b179规格范围内的任何组成。
38.表1
[0039][0040]
表2
[0041]
元素sifecumnmgnizntipbsnsr重量%6.810.1560.04670.02130.3520.00330.00720.1015
‑
00
[0042]
表3
[0043]
元素sifecumnmgzn重量%6.5至7.50.13至0.250.100.050.3至0.450.05
[0044]
以下段落提供了改善铝合金二者的示例性实施方案。然而,这些示例性实施方案是出于说明的目的而提供的,并且不旨在穷举或限制本公开。这些组成可以例如通过使用光学发射光谱法现场测量。
[0045]
改善铝合金优选由这样的化学组成组成:当在炉中与再利用铝合金混合时,不需要任何另外的元素或材料来形成期望的混合材料。更具体地,在混合期间不需要向炉中添加另外的中间合金例如硅、锰、镁和锶。改善铝合金通常在引入炉中之前形成铸锭。
[0046]
改善铝合金的第一个示例性实施方案,称为e5.50,基于合金的总重量,所述改善铝合金以重量百分比(重量%)计包含:硅(最少7.4重量%,最多7.9重量%);铜(最多0.01重量%或最多0.25重量%);铁(最少0.16重量%,最多0.2重量%);镁(无最少量,最多0.1重量%);锌(无最少量,最多0.03重量%);锰(最少0.92重量%,最多1.0重量%);钛(无最少量,最多0.06重量%);锶(最少0.03重量%,最多0.04重量%);镍(微量);铬(微量);锡(微量);另外的元素(总计最多0.1重量%,单独最多0.03重量%);以及剩余部分为铝。该示例性改善铝合金优选具有约1.8的残渣因子。当在炉中与再利用356.2铝组合时,这种改善铝合金为亚共晶的。
[0047]
改善铝合金的第二个示例性实施方案,称为e2.50,基于改善铝合金的总重量,所
述改善铝合金以重量百分比(重量%)计包含:硅(最少12.5重量%,最多13重量%);铜(最多0.01重量%或最多0.25重量%);铁(最少0.16重量%,最多0.2重量%);镁(最少0.27重量%,最多0.33重量%);锌(无最少量,最多0.03重量%);锰(最少0.92重量%,最多1.0重量%);钛(无最少量,最多0.06重量%);锶(最少0.03重量%,最多0.04重量%);镍(微量);铬(微量);锡(微量);另外的元素(总计最多0.1重量%,单独最多0.03重量%);以及剩余部分为铝。这种改善铝合金优选具有约1.8的残渣因子。当在炉中与再利用356.2铝合金组合时,这种改善铝合金为共晶的。
[0048]
改善铝合金的第三个示例性实施方案,称为e2.70,基于改善铝合金的总重量,所述改善铝合金以重量百分比(重量%)计包含:硅(最少17重量%,最多17.5重量%);铜(最多0.01重量%);铁(最少0.16重量%,最多0.2重量%);镁(最少0.27重量%,最多0.33重量%);锌(无最少量,最多0.03重量%);锰(最少1.65重量%,最多1.70重量%);钛(无最少量,最多0.06重量%);锶(最少0.06重量%,最多0.07重量%);镍(微量);铬(微量);锡(微量);另外的元素(总计最多0.1重量%,单独最多0.03重量%);以及剩余部分为铝。这种改善铝合金优选具有约1.8的残渣因子。当在炉中与再利用356.2铝合金组合时,这种改善铝合金为过共晶的。
[0049]
表4提供了改善铝合金e5.50、e2.50、和e2.70的具体示例性组成。以上公开并在以下列出的改善铝合金的镍、铬和锡的“微量”为最高达0.05重量%。改善铝合金可以包含微量的镍、铬和锡。这些微量元素的总量优选不大于0.15重量%。图8提供了“残渣因子”和如何计算其的描述。
[0050]
表4
[0051]
合金e5.50重量%合金e2.50重量%合金e2.70重量%si7.4至7.9si12.5至13si17至17.5cu最多0.01cu最多0.01cu最多0.01fe0.16至0.2fe0.16至0.2fe0.16至0.2mg0至0.1mg0.27至0.33mg0.27至0.33zn最多0.03zn最多0.03zn最多0.03mn0.92至1.0mn0.92至1.0mn1.65至1.7ni微量ni微量ni微量cr微量cr微量cr微量sn微量sn微量sn微量ti0至0.06ti0至0.06ti0至0.06sr0.03至0.04sr0.03至0.04sr0.06至0.07残渣因子1.8残渣因子1.8残渣因子1.8其他每一者最多0.03其他每一者最多0.03其他每一者最多0.03其他总计0.1其他总计0.1其他总计0.1al剩余部分al剩余部分al剩余部分
[0052]
在包括改善合金e5.50或合金e2.50的实施方案中,优选的是,方法包括向炉中添加同等部分的改善铝合金和再利用356.2铝合金,并将所得熔融材料混合。在包括改善合金e2.70合金的实施方案中,优选的是,方法包括除了向炉中添加比再利用356.2铝合金更多
的e2.70合金之外还有更长的熔化期间,并将所得熔融材料混合。在一些实施方案中,方法包括在熔化之后略微调节炉中混合材料的组成。
[0053]
在一个优选实施方案中,再利用铝合金包括再利用356铝合金,优选从使用过的车轮和/或轮辋获得的a356.2铝;并且改善合金为以重量百分比(重量%)计包含至少7%的硅的铝合金。在另一个实施方案中,基于改善铝合金的总重量,再利用铝合金包含6.81重量%的量的硅、0.156重量%的量的铁、0.021重量%的量的锰、0.325重量%的量的镁、0.102重量%的量的钛、和0.047重量%的量的铜;并且将再利用铝合金与改善铝合金e5.50混合以获得混合材料,基于混合材料的总重量,所述混合材料包含7.31重量%的量的硅、0.16重量%的量的铁、0.544重量%的量的锰、0.164重量%的量的镁、0.011重量%的量的锶、0.064重量%的量的钛,以及在一些实施方案中,0.01重量%的量的铜。
[0054]
根据一些优选实施方案,混合材料包括aural 5s规格内的任何组成。在这种情况下,基于混合材料的总重量,混合材料以重量百分比(重量%)计包含6.0重量%至8.0重量%的硅、最高达0.25重量%的铁、0.40重量%至0.60重量%的锰、0.1重量%至0.60重量%的镁、0.01重量%至0.03重量%的锶、和最高达0.15重量%的钛、各自的量最高达0.05重量%的另外的元素、总量最高达0.15重量%的另外的元素、以及余量的铝。
[0055]
根据另一些优选实施方案,混合材料包括aural 2规格内的任何组成。在这种情况下,基于混合材料的总重量,混合材料以重量百分比(重量%)计包含9.5重量%至11.5重量%的硅、最高达0.25重量%的铁、0.40重量%至0.60重量%的锰、0.1重量%至0.60重量%的镁、0.01重量%至0.025重量%的锶、和最高达0.12重量%的钛、各自的量最高达0.05重量%的另外的元素、总量最高达0.15重量%的另外的元素、以及余量的铝。
[0056]
再利用铝合金和/或改善铝合金可以在混合之前、期间或之后经历另外的加工。例如,可以在生产过程期间对合金进行脱气、熔剂处理(fluxed)、过滤和晶界强化。在一个实施方案中,脱气步骤包括用帕尔默(palmer)旋转脱气机进行氩脱气20分钟。
[0057]
混合材料也可以经历前述另外的加工步骤中的一者或更多者。此外,所得混合材料可以在铸造之后经历热处理。例如,可以根据美国材料与试验协会(american society for testing and materials,astm)astm b917将混合材料热处理至t6,并对astm b917稍作修改将混合材料热处理至t61以增加延伸率。对于t6处理,可以对混合材料进行砂型铸造并退火至540℃持续9小时,在25℃下的水中淬火,并在次日老化至155℃持续4小时。对于t61处理,可以将混合材料永久铸造成棒材,固溶退火至540℃持续9小时,在25℃下的水中淬火,然后在162℃下老化9小时。可以在535℃、15000psi下通过热等静压2小时来进一步处理混合材料。此外,可以将混合材料加热至730℃的温度并熔化,然后可以进一步在860
°
f下经历t7处理75分钟,并在215℃(419
°
f)下以14℃/秒强制空气冷却淬火两小时。这些加工步骤可以实现图4a至4d中所示出的显微组织,其为表现出细α铝晶粒和球化共晶硅的截面的中心。此外,在一些实施方案中,用0.05%ti(al%5ti1b)对熔融混合材料进行晶粒细化。
[0058]
根据替代实施方案,对再利用铝合金进行改性,并且在某些情况下,再利用合金的改性导致对混合材料的改善。虽然以下段落中所描述的特定材料特性与再利用铝合金有关,但是应理解,对材料特性进行改性的方法中的任一者也可以在部件20的混合或铸造之前、之后或期间应用于改善铝合金和/或混合材料。还应理解,这些方法步骤可以以不同的变型组合。
[0059]
上表1对再利用356.2铝合金的三种变型的组成与astm b108下的a356.0、astm b179下的a356.1、和astm b179下的a356.2的astm要求的规格进行了比较。进行实验以评估合金和混合材料。使再利用356.2铝合金在具有碳化硅坩埚的dynarad mg260 75kw电阻炉中熔化。在于275℃下预热之后,在约3小时25分钟内完成熔化。通常,由于增加的表面积,使较小的压碎车轮片熔化比使较大的铸锭、砂床铸铁(砂床铸造金属,sow)或t型梁熔化更快。在熔化结束时,再利用356.2铝合金的最后一些片的一些漂浮表皮在熔体表面上可见。在对未经处理的熔体取样之前,将那些氧化物撇去;移除的总撇渣为0.66磅或装料的0.5%,这对于大多数类型的装载材料来说都在正常的范围内。
[0060]
特别地由于车轮/轮辋的清洁步骤和组成,就纯度而言,接收的356.2再利用铝合金的化学分析完全在a356.2规格内(与0.12%极限相比,可能具有甚至更高的关于fe的纯度规格)。表2中提供了所测量的356.2铝合金的组成。在熔化期间,再利用铝合金被坩埚中的一些fe略微污染(因此熔化时的再利用合金中含有0.15%的fe),但是除了将其基本上置于a356.1规格内之外,这不具有任何显著影响。由于在脱气之前测量到熔体中88ppm的锶残留水平并且在脱气之后测量到79ppm,因此未对熔体进行锶改性。
[0061]
混合材料实现了大于180的极限抗拉强度、大于120的屈服强度和大于5%的延伸率。下表5包括包含e.250和由热处理之后的车轮获得的再利用a356.2铝合金的混合材料的材料特性。
[0062]
表5
[0063]
位置utsys延伸率119612418.7219812417.6220113016.0l19512418.8219412315.1119512315.9219512115.9119612516.4219912714.6119612317.5118912117.1219812617.5119512518.7219512515.9119712918.8219812917.1119512914.9平均196125.1816.85标准偏差2.572.791.40
[0064]
图3a和3b是示出再利用铝合金的孔隙率的显微视图。孔隙率通过表面的图像分析
来评估。如图3a中所示(从左至右),未经处理的熔体的永久模制棒材中的孔隙率为0.67%,经脱气的熔体为0.36%,以及在热等静压(hipping)之后为0.02%。热等静压封闭了孔隙并且显著改善了机械特性,因此对于某些实施方案(例如,来自低压/反压铸造或挤压铸造)表现出改善的结果。砂型铸造测试棒材中的孔隙率示于3b中,并且包括在0.53%处的拉伸特性的平均值。当与图3a中所呈现的永久模制体结果相比时,较低的凝固速度或位于树脂砂型中是较高孔隙率含量的原因。
[0065]
图4a至4d是示出枝晶臂间距的混合材料的显微视图。枝晶臂间距与凝固速度和效率相关。金属模具中的快速冷却产生比砂型中更细的组织。通过添加锶的步骤进行改性以使针状共晶硅转变成圆形形状,这改善了延伸率。
[0066]
图4a中示出了由包含e.250和经t7处理的再利用铝合金的混合材料铸造的测试棒材。图4b中示出了由包含e.5.50和t5热处理之后的再利用合金的混合材料铸造的测试棒材。图4c和4d中示出了由包含e.2.50和t5热处理之后的再利用合金的混合合金铸造的测试棒材。
[0067]
对再利用铝合金进行清洁的步骤可以包括洁净度的评价。在测试期间可以用kmold开始金属清洁。在经脱气的熔体中用热多孔板过滤设备(porous disk filtration apparatus,podfa)理想地评价再利用合金洁净度。podfa可以用于熔融洁净度评价,其中熔融金属在真空下强制流动通过陶瓷过滤器。每kg滤出的夹杂物的量和夹杂物类型通过金相学测量并以mm2/kg表示。包括再利用356.2铝合金的方法的podfa结果已显示出优异的结果。
[0068]
如上所述,在脱气步骤之后,再利用铝合金可以经历熔剂处理的步骤。用0.8g/kg的promag si熔剂来进行熔剂处理步骤,然后用帕尔默(palmer)脱气机进行氩脱气20分钟。可以产生1.7磅的量的熔渣。在熔化处理(包括用于浇注和测试经脱气的合金的4小时操作)之后,熔体中的镁几乎没有变化,为0.32%。锶在熔剂处理和脱气之后降至20ppm。
[0069]
对所有在永久模具中铸造的经熔剂处理且经脱气的棒材进行测试,对这些棒材以及经脱气和未经处理的系列进行热处理,并且对50%进行热等静压。表5中所示的抗拉结果与经脱气的熔体结果没有特别不同。然而,结果表明熔体已经足够清洁,并且在某些实施方案中脱气是充分的并且熔剂处理是不必要的。在铸造和压铸操作中,还可以实施对任何再利用合金或混合材料进行过滤。
[0070]
包括再利用356.2铝合金的各种再利用合金是可大量获得的。根据以上教导用改善铝合金混合提供了较低价格点的益处,并且省去了一个或更多个生产步骤(例如添加中间合金),从而导致对物流、处理等的改善。对于某些部件和产品,与较轻重量的铝铸件替代品的原材料相关的成本节约对于oem来说具有经济意义,从而使他们能够用较轻的铸件替代较重的替代品,并有助于整体车辆轻量化。此外,重量的减轻对车辆的排放物产生和燃料消耗产生有益影响。虽然示例性再利用合金为a356,但是其也可以包括多种压铸过程和材料。例如,某些压铸件由原始合金(例如365或a365)制成,其也可以被使用并经历以上方法并表现出类似的积极的经济影响和环境影响。此外,目前通过压铸(以二次合金)制造的多种部件可以从与改善合金混合的再利用356.2合金提供的更高品质和有竞争力的输入材料中受益。由于改善的机械特性,这些压铸部件可以以减少车辆的整体重量的方式重新设计。此外,由具有改善的特性的混合材料形成的压铸部件可以用于替代较重的铝(例如,在由较
厚壁制成的永久模具铸件、或其他较重的金属铸件中)。可以实现车辆重量显著更多地减轻,并因此可以实现燃料消耗和排放物产生的减少。与任何装载材料一样,再利用356.2合金的装载时间和熔化时间将取决于炉类型和布置以及其装载方式。在大多数情况下,如果以适当的方式完成装载,则在小铸锭、t型梁或砂床铸铁之间在装载时间方面几乎不存在差异(例如用整包(sacks)(替代t型梁或砂床铸铁))。熔化时间还可以取决于表面积与质量之比,其与铸锭尤其是t型梁或砂床铸铁相比大得多,因此通常切碎的再利用材料将熔化更快,尤其是如果将装料浸入熔融金属中。可以计算所有这些特征来改进各种方法步骤。
[0071]
然而,对于增加的表面积与质量之比(即,较快熔化)而言,一种考虑还涉及产生更多的氧化表面,并因此产生更多的熔渣。测试表明,对于再利用356.2铝合金,熔体损失低且与铸锭相当。在包括275磅熔体的一系列示例性方法步骤中,步骤和结果包括:首先,将0.66磅或0.5%的装料撇去;其次,在脱气之后将5.97磅或2.17%的装料撇去,熔渣中总计2.67%的装料损失。对于清洁且干燥的装载材料如铸锭或t型梁,这种损失可以在1%至2%的范围内。通常,使用切碎的再利用356.2合金将导致比铸锭多约1%的熔渣,这被其更低的价格点和高熔化速率的节能而抵消。例如在将e2.50与熔剂处理操作之前的再利用铝合金混合之后,由混合材料形成的部件的氧化物测试可以通过kmold氧化物测量(kmold oxide measurement)包括在该方法中。
[0072]
通常,熔体损失/熔渣产生取决于设备和金属的加工、装载材料的表面积与质量之比、和装载材料的表面状况。在切碎的再利用356.2合金的情况下,其表面状况优异且极其清洁,因此其不会另外地导致熔体损失/熔渣产生。再利用356.2铝合金为可以使铸造和压铸机实现非常良好品质的铸件——接近于450mpa(在永久型铸中)的材料。
[0073]
如上所述,各种部件可以由包含再利用铝合金和改善铝合金的混合材料形成。根据一个优选实施方案,部件通过高压真空压铸形成。在此过程期间,将熔融金属在高速度和高压力下注入钢模(模具)腔中。金属通常在5ksi至15ksi的压力下以90英尺/秒至200英尺/秒的速度注入。腔(模具)填充时间在几毫秒至长达半秒的范围内。压铸机的额定夹紧吨数通常等于其可以施加在模具上的压力的量。机器尺寸在400吨至4000+吨的范围内。金属模具在热处理条件(硬化条件)下由合金工具钢(通常为h13)制成。将模腔温度保持在约450
°
f至500
°
f,并严格控制熔融合金的温度以确保足够的流动性和模腔填充。
[0074]
图5a至5i示出了根据一个示例性实施方案的高压真空压铸过程的步骤。图5a示出了模具的起始位置。在图5b的步骤中,关闭模具并将熔融铝合金倒入冷室中。在图5c的步骤中,施加真空以移除模腔和压射室内的气氛。在图5d的步骤中,液压活塞将金属缓慢推向模腔。在图5e的步骤中,模腔在几分之一秒内被填充。在图5f的步骤中,金属在压力下凝固以形成铸件。在图5g的步骤中,打开模具并移出铸件。在图5h的步骤中,将脱模剂施加至模具。在步骤5i中,铸造设备准备进行下一个循环。
[0075]
图6是示出常规高压压铸hpdc、真空辅助高压压铸和高压真空压铸之间的差异的图表。
[0076]
图7a至7h为可以由混合材料形成的示例性部件。图7a为底盘部件,特别地为前副车架。图7b为结构车身部件,具体地为前减震塔。图7c为结构车身部件,具体地为后纵梁。图7d为结构车身部件,具体地为前降档纵梁(front kick
‑
down rail)。图7e为结构车身部件,具体地为前车身铰链柱。图7f为结构车身部件,具体地为通道(tunnel)。图7g为结构车身部
件,具体地为前车身铰链柱。图7h为结构车身部件,具体地为后减震架。
[0077]
虽然本公开旨在以最少的处理步骤生产部件,但是根据所需的化学和铸造特性,在某些情况下可能需要少量添加mg和sr或用原始a356.2(或更高纯度)铸锭进行可能的稀释。在一些情况下,对熔体进行熔剂处理不改变抗拉结果,这表明再利用铝合金非常清洁。
[0078]
应理解,前述实施方案的描述是出于说明的目的而提供的。换言之,本公开主题并不旨在穷举或限制本公开。特定实施方案的各个要素或特征通常不限于该特定实施方案,而是在适用的情况下可互换并且可以在选定的实施方案中使用,即使没有具体地示出或描述亦是如此。本公开也可以以许多方式变化。这样的变化不被视为偏离本公开,并且所有这样的修改均旨在包括在本公开的范围内。