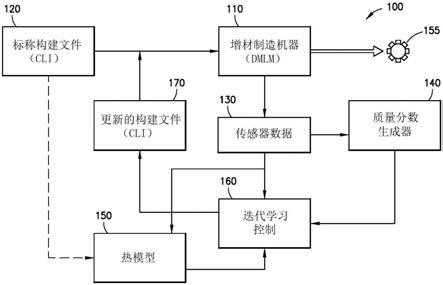
1.所公开的实施例针对基于热模型和传感器数据在增材制造过程中校正构建参数。
背景技术:2.术语“增材制造”是指用于合成三维物体的过程,其中连续的材料层由增材制造机器(amm)在计算机控制下形成,以使用来自3d模型的数字模型数据来创建物体。基于粉末床熔合的增材制造的一个例子是直接金属激光烧结(dmls),其使用激光射进到粉末金属床中,激光自动瞄准由3d模型限定的空间中的点处,从而使材料熔化在一起,以创建固体结构。术语“直接金属激光熔化”(dmlm)可以更准确地反映该过程的性质,因为它通常会在凝固时实现完全成熟的均质的熔池和完全致密的块体。在应用任何必要的热处理之后,熔化材料的快速的局部加热和冷却的性质能够实现近锻造的材料特性。
3.dmlm过程使用要制造的物体的3d计算机辅助设计(cad)模型,由此创建cad模型数据文件并将其发送到制造设施。技术人员可以使用3d模型来正确地定位用于零件构建的几何结构,并可以根据需要向设计添加支撑结构。一旦这个“构建文件”完成,它就会被“切片”成用于特定dmlm制造机器的适当厚度的层,并下载到机器以允许开始构建。dmlm机器使用例如400w yb光纤激光器。在构建室区域内,有粉末分配平台和构建平台,以及用于在构建平台上移动新粉末的重涂器刀片。通过使用聚焦激光束局部熔化金属粉末,金属粉末被熔合成固体零件。通过这种方式,零件被逐层叠加性构建——通常使用20到100微米厚的层。此过程允许直接从3d cad数据自动创建高度复杂的几何结构,无需任何工具。dmlm生产的零件具有高精度和细节分辨率、良好的表面质量和优异的机械特性。
4.在dmlm过程中,可能因为各种机器、编程、环境和过程参数以及因为所用材料的化学性质而出现异常,例如表面下孔隙率、裂纹、未熔合等。例如,镜面位置和激光聚焦的机器校准中的缺陷可能导致大量填充(bulk
‑
fill)激光通道与边缘轮廓通道不相交。此类缺陷可能导致部件表面附近出现未熔合的粉末,这可能会冲破表面而导致异常,这些异常无法通过包括热等静压(hip)的后处理热处理步骤来修复。激光和光学器件退化、过滤和其他典型的激光焊接效果也会显著地影响处理质量,尤其是在每次构建操作数十或数百小时的时候。
5.在常规的增材制造实践中,零件构建计划(pbp)针对特定的零件设计而生成,并由增材制造机器(amm)执行。基于pbp,amm控制在构建期间应用的多个构建参数,包括材料添加区域的行进路径以及管理添加到区域中的零件的材料的施加和处理的参数。通常,这些参数与构建零件的质量之间存在复杂关系。
6.pbp的设计是迭代过程,其包括基于试验pbp构建零件,之后评价由此产生的试验零件质量,然后修改试验pbp以调整期望的零件质量。为满足整体制造要求(例如零件质量和生产率)的这种试验pbp的迭代可能需要多次迭代才能达到所需的制造要求。常规上,通过使用破坏性或非破坏性技术对零件进行实验测试来完成对试验零件质量的评价。特别
是,dmlm零件可以被剖切,从处理过的剖面产生光学显微照片,并处理显微照片以量化异常。试验零件质量的评价基于此类测试。这种测试费力、昂贵且耗时,并且显著增加了开发可接受pbp以发布到最终产品的时间和成本。
7.在常规方法中,使用固定参数组来构建零件,然后进行各种物理测量,例如切割/显微分析、相干断层显像(ct)扫描和其他检查技术,以评估零件的不同区域的质量。然后进行随后的构建,其中几何结构可以被分段并且被分配不同的参数组。构建的零件经过物理测试并且进行进一步的迭代,直到零件质量收敛到可接受的范围内。每次这样的迭代可能需要,例如,3
‑
4周,因为零件可能需要被送到专门的设施来进行鉴定,即物理测量,然后设计专家必须解释鉴定结果并做出关于分段和参数变化的决定。此类方法可能需要10到12次迭代,这意味着可能需要一年或更长时间才能生产出可接受的零件。手动分段/参数修正方法的另一个缺点是功率级段的边界往往是可能的故障点。
技术实现要素:8.公开的实施例提供了一种使用模型和传感器数据的组合来校正dmlm过程中的可预测干扰的方法。基于干扰预测的时间尺度,该技术可用于从构建到构建(例如,对于几何干扰)或者甚至层到层(例如,对于烟雾遮挡)提高零件质量。目标是减少用于零件参数优化的周期时间,零件参数优化常规上是通过试错法来完成的,因此可能需要数周时间来收敛到可接受的参数组。此外,常规方法更多的是艺术而不是科学,因为最终结果取决于个人的专业知识。
9.在公开的实施例中,基于可以快速执行的模型来估计扫描参数的初始猜测。迭代的结果记录在传感器中,并与先前生成的参考(例如,先前迭代的结果或模型的输出)进行比较。然后通过跟踪滤波器反馈估计误差以改进模型,并且更新后的模型用于生成新的扫描参数组。然后可以根据需要使用跟踪误差来进一步调谐扫描参数。由于算法方法,期望该过程在一次构建内仅经过几次迭代后就能收敛到最佳参数组。此外,在常规方法中,迭代和调整是手动的,因此结果取决于工程师的专业知识。算法方法无需直接人工干预就可提供更好的结果。在一些常规方法中,每个周期的迭代时间为几周,因为迭代结果是通过构建后的切割和材料鉴定来评估的。相比之下,使用本文描述的算法,可以在构建后立即从传感器数据评估结果。由于参数是以算法调整的,而不是通过试错,因此收敛所需的迭代次数更少。常规的手动参数优化需要借用材料,因为它们无法以足够精细的分辨率对零件进行分段,从而沿走向(strike)具有不同的扫描参数。
10.较低的新产品引入(npi)周期时间导致复杂零件的成本节省以及更大的生产量(即,在同一时间内优化更多的零件)。本文描述的技术还具有通过实现原本不可能实现的几何结构来扩展设计空间的潜力。与常规方法相比,将传感器数据与模型数据相结合并使用跟踪滤波器来更新模型可以获得更高的保真度结果。
11.所公开的实施例提供了无需在每次试构建迭代中的物理测试步骤的情况下预测零件质量。零件质量模型基于零件构建期间进行的传感器测量和构建时已知的其他信息而被开发。基于零件质量的决定,例如对pbp的修改,或者零件接受/拒绝,是基于质量模型结果。分析构建期间生成并在分析时已知的数据,而不是进行构建后测试,降低了pbp开发的成本和经过时间,以及用于生产零件质量评价的成本和时间。所公开的方法可以完全或部
分地替代物理测试,或者可以替代整个测试过程的某些部分(例如,长构建时间和昂贵部分)。这些方法可以应用于选定的迭代,而在迭代的选定中使用物理测试。这些方法可用于筛选构建零件并减少进行物理测试的零件的数量。在公开的实施例中,质量分数生成器的输出可以附加到整个零件、零件的区段、整个构建或构建的区段。质量分数生成器的输出可以基于复杂性或几何结构附加到零件的部分,例如附加于轮廓、薄壁和突出部分,而不是大块区域。质量分数生成器的输出可以是二进制的,例如通过/失败,或者可以具有多个级别,例如高、中和低,在这种情况下,具有高质量分数的零件可以被视为优质零件,具有中等质量分数的零件可以被视为可接受的零件(即用于在不太关键的应用中使用的零件),而低质量的零件可以被拒绝。质量分数生成器的输出可以是指示零件所需的特定类型的后处理(例如后处理a、后处理b和拒绝)的一组值。例如,某些零件可能需要轻度的热等静压(hip)处理,其他零件可能需要强烈的hip,其他零件可能会切掉有用的区段,以及其他零件可能会被拒绝。
12.在公开的实施例中,可以考虑由过程变量导致的对完工条件下的异常和微观结构变化的光电二极管响应,包括质量分数与后处理零件(例如,经受热处理和/或hip的零件)的微观结构之间的相关性。可以通过直接(例如,光学、sem成像)或间接方法(例如,衍射、光谱)来测量/映射增材制造零件或零件的代表性区域/区段的材料微观结构和化学,其中输出可以是每个测量类型(例如,平均值、中值、标准偏差等)的单个值或一组单个值或测量区域的全场空间分布图。用于映射/测量完工和后处理增材制造零件的微观结构和元素化学分布的方法可以包括例如光学成像、扫描电子成像、背散射电子成像、电子背散射衍射、能量或波长色散光谱、原子力显微术、x射线衍射、透射电子显微术(成像和衍射两者)等。
13.在公开的实施例中,对不同的异常,例如孔密度、裂纹密度和未熔合缺陷密度,可以确定质量分数。单个总分数可以从多个子分数的组合中导出,例如总和、加权总和、最大值、平均数、加权平均数。可以生成由多个表面图像形成的响应图,其中质量分数被映射到输入过程参数(例如,激光功率、扫描速度、束斑尺寸/焦点偏移和影线间距(hatch spacing))。可以生成响应图,其中完工异常(例如,孔隙、裂纹、未熔合缺陷)和微观结构测量参数(例如,晶粒尺寸和伽马/伽马主要尺寸分布)被映射为输入参数(例如,激光功率、扫描速度、束斑尺寸/焦点偏移、影线间距)、导出值(例如,线性热输入、能量密度和束强度)、过程变量(例如,熔池宽度和深度)以及生成的质量分数的函数。
14.在一个方面,所公开的实施例提供了一种用于向增材制造机器提供更新的构建参数的方法(以及相应的系统和软件)。该方法包括在使用第一组构建参数制造零件期间,经由包括处理器的设备的通信接口,从增材制造机器接收传感器数据。该方法进一步包括接收第一组构建参数。该方法进一步包括使用设备的处理器,基于第一组构建参数和接收到的传感器数据,确定评估参数。该方法进一步包括使用设备的处理器,基于从第一组构建参数中导出的零件的热模型,生成热数据。该方法进一步包括使用设备的处理器,对接收到的传感器数据、确定的评估参数和生成的热数据应用第一算法,以产生第二组构建参数,第一算法被训练以改进评估参数。该方法进一步包括将第二组构建参数输出到增材制造机器以生产第二零件。
15.实施例可以包括以下特征中的一个或多个。
16.评估参数可以包括通过将第二算法应用于第一组构建参数和接收到的传感器数
据而确定的质量分数。可以通过接收从对至少一个参考零件进行的物理测量中导出的参考来训练第二算法,使用一组参考构建参数来构建至少一个参考零件。热数据的生成可以包括基于标称热模型和第一组构建参数来计算第一组热数据值。热数据的生成可以包括基于计算出的第一组热数据值与接收到的传感器数据的比较来确定更新的热模型;并且基于更新的热模型计算第二组热数据值。标称热模型可以通过以下方式导出:将零件的体积划分为体素;确定在每个体素的中心的限定半径内的周围材料的相对量;以及基于周围材料的相对量计算每个体素的热数据值。可以从激光功率传感器、致动器传感器、熔池传感器和环境传感器中的至少一个接收传感器数据。
附图说明
17.图1是用于在增材制造过程中校正用于生产零件的构建参数的系统的框图;
18.图2是用于使用质量分数生成器来确定所生产的零件的质量分数的系统的图,质量分数生成器从增材制造机器接收传感器数据;
19.图3是质量分数生成器的示意图;
20.图4描绘了用于更新在增材制造过程中生产的零件的热模型的系统;
21.图5a描绘了被体素化以产生标称热模型的零件的一部分;
22.图5b以俯视图描绘了确定特定体素的中心的限定半径内的周围材料的相对量;
23.图5c以侧视图描绘了确定特定体素的中心的限定半径内的周围材料的相对量;和
24.图6是根据一些实施例的系统的框图。
具体实施方式
25.使用对于零件的几何结构中的所有位置被固定的参数组进行增材制造构建可能不会产生令人满意的结果。例如,假设使用了固定参数组的设计,该固定参数组基于零件制造中使用的材料的特性而被开发。这样的参数组可以在零件的大块区域(即具有相对均匀的几何结构的部分)中很好地工作。然而,在其导热率远低于大块区域的零件的薄壁部分中,熔池尺寸将会更大,并且熔池将会更热,因此薄壁区域中的材料特性可能会比大块区域中的材料特性有显著差异,当使用固定参数组时,这可能导致不令人满意的零件质量。作为进一步的例子,如果零件有突出的表面,例如,拱形,那么有很小的热导率。因此,熔池将相对大得多,这导致构建的零件具有非常差的表面光洁度。因此,使用标称参数组进行的构建可能会导致材料特性的缺陷。可以调整标称参数组以尝试改进材料的表面的特性。例如,可以遍及整个构建或在分段的区域中降低激光功率。然而,这种调整会引入或增加材料的孔隙率。
26.在公开的实施例中,迭代学习控制(ilc)在设计阶段被使用,以将可变校正应用于构建参数,用于可预测的干扰,从而例如根据激光位置校正激光功率水平。ilc特别适用于热导率在几何结构的不同部分中显著变化的零件几何结构。利用ilc,对构建参数有更精细的控制,因此可以单独控制细粒度区域。这种构造有助于使孔隙率的引入最小化,因为对激光功率有更精细的控制。
27.图1是用于在增材制造过程中校正用于生产零件的构建参数的系统100的框图。该系统使用从构建参数和传感器数据中导出的热模型和评估参数(例如,质量分数)。一组标
称构建参数被输入到增材制造机器(amm)110,例如,直接金属激光熔化(dmlm)打印机(即,机器)。标称构建文件120可以是公共层接口(cli)文件的形式,其可以包括一组扫描参数,即构建参数。当dmlm打印机110基于标称构建文件120进行构建时,从与打印机相关联的各种传感器中收集传感器数据130。传感器数据130被输入到质量分数生成器140,质量分数生成器140在没有对零件进行大量物理测试的情况下,计算指示构建零件的质量的分数。
28.标称构建文件120也被输入到热模型150,热模型150对构建零件对应用的激光功率的热响应进行建模。如下文进一步详细描述的,热模型150使用标称构建文件120和从dmlm打印机110接收到的传感器数据130来预测构建零件155的体积内的热密度,热密度将由在扫描期间从激光器应用特定水平的热量输入而引起。实际上,热模型150在扫描路径中的每个位置处在构建文件中指定的热输入参数(例如,激光功率和扫描速度)与在构建期间该位置的期望传感器读数(例如,光电二极管读数)之间创建相关性。
29.传感器数据130、由质量分数生成器140计算出的质量分数、以及热模型的输出被输入到迭代学习控制(ilc)160。如下文进一步详细描述的,ilc 160基于这些输入,使用机器学习算法来产生更新的构建文件170。因此,ilc 160创建构建文件的扫描参数与使用构建文件产生的零件的结果质量分数之间的映射,这允许使用迭代机器学习过程来优化构建文件。该过程导致构建零件具有更高的质量,而无需像常规方法那样进行多轮实验测试。
30.迭代学习控制160是涵盖各种学习和控制算法的术语,这些学习和控制算法被构造为从先前的构建中学习并提高后续构建的质量。公开的实施例通过使用迭代学习过程在需要参考来跟踪的控制应用中提供质量分数的应用。如本文所讨论的,质量分数的生成和使用允许对物理特性的阵列进行建模,例如,孔隙率、表面光洁度等,其传统上使用切割来确定。在公开的实施例中,可以检查传感器数据和其他输入数据,以确定构建零件的物理特性,例如,孔隙率和表面光洁度,并且可以在模型中使用这些传感器空间以实现所需质量的零件。
31.在公开的实施例中,给定各种输入,例如,传感器输入和过程参数,模型可以预测质量分数,而质量分数又可以用于确定构建零件是否将可接受。如果预测的零件质量不可接受,则可以采取各种措施来改进制造过程。换句话说,给定模型、给定与传感器的响应图、给定构建数据和扫描文件(例如,cli构建文件),质量分数生成器可用于预测构建是否可接受。如果质量分数表明构建将不可接受,则ilc尝试了解什么是不可接受的(例如,经由机器学习算法)并对正在构建的零件的扫描文件进行校正以使未来的构建更容易接受。
32.一般来说,可能有许多不同的干扰作用于制造过程。如果没有干扰,人们可以设计理想的扫描参数组,例如激光功率、速度等,并且人们将期望每次执行该参数组(即“配方”)时,结果将是具有所需特征的零件。然而,这不会发生,因为有干扰作用于整个系统,使过程偏离其标称值。其中一些可以是可预测的干扰,例如,如果有人试图构建相同的几何结构,那么热导率是对于每个实例(即,每个构建)都相同的干扰。类似地,如果正在使用相同的机器并且光学系统中存在问题,则问题是已知的,并且可以为此进行校准。另一方面,将会有一些随机的并且因此会因构建而异的干扰。这种干扰无法以可预测的方式被补偿。迭代学习控制(ilc)用于从历史构建中学习并在后续构建中校正,这可以被认为是“前馈”控制过程。这仅对于可预测的干扰是可能的——算法学习什么是可以被预测的并对其进行补偿。另一方面,对于随机干扰,可以使用反馈控制过程。
33.ilc具有控制算法,该控制算法在第一回路中接收跟踪误差,跟踪误差基于与基于构建期间测量的传感器数据所预测的质量分数相比较的一组参考(即,期望)质量分数被确定。基于跟踪误差,算法更新构建文件(即,扫描文件或参数组)以在下一次构建迭代中使用。替代地,如上所述,一组参考传感器数据值可用作跟踪误差回路中的比较基础。在这种情况下,将测量到的传感器数据与跟踪回路中的参考传感器数据值进行比较,而不是将测量到的传感器数据转换为质量分数(使用参考表面)并将质量分数与所需的质量分数目标进行比较。
34.在公开的实施例中,ilc在第二回路中接收估计误差,该估计误差是预测到的传感器数据值与测量到的传感器数据的比较。传感器数据使用热模型被预测,热模型开始时为标称热模型,但随后通过算法基于估计误差而被更新。热模型接收构建参数,例如扫描文件,并基于该输入,预测一组传感器数据值。在完美热模型的情况下,预测到的传感器数据值将与测量到的传感器数据准确对应。由于标称热模型并不完美,所以实际的传感器响应与预测到的传感器响应不同——这种差异就是估计误差。估计误差可以被馈送到跟踪滤波器,跟踪滤波器将预测到的传感器数据值(即,通过热模型而被预测)和测量到的传感器数据进行比较,并以适合于使估计误差最小化的方式更新热模型。
35.上述ilc的两个回路,可以分别称为迭代学习控制回路和跟踪滤波器回路,可独立运行(例如,一次一个)或可以组合操作。注意,本文使用的术语将跟踪误差描述为被馈送到ilc,并将估计误差描述为被馈送到跟踪滤波器。
36.在公开的实施例中,ilc回路和跟踪滤波器回路被组合使用,以使两种类型的误差,即跟踪误差和估计误差,迭代最小化。跟踪误差的最小化意味着构建零件的预测到的质量分数应该从不可接受的范围移动到可接受/期望的范围。估计误差的最小化意味着热模型接近高准确度。因此,预测到的传感器值将与测量到的传感器数据紧密匹配,这将允许ilc回路(其依赖热模型)更快地收敛。如上所述,可以在没有跟踪滤波器回路的公开的实施例中使用跟踪滤波器回路,因为标称热模型在实践中可能足够准确。如上所述,在常规方法中,不系统地对整个零件或零件区域应用功率校正以优化例如表面光洁度,会导致对其他材料特性(例如孔隙率)的影响。另一方面,使用ilc允许构建参数(例如功率)以可以导致改进的材料特性的方式收敛,而无需对任何一种材料特性进行重大权衡。
37.如上所述,如果正在构建的零件具有困难的几何结构,例如突出区域,则由于讨论中的区域中的降低的热导率而将存在相对较大的熔池,即,较少的热量通过零件的大块材料而从该区域被传导出去,导致零件质量下降。在这种情况下,可能需要相对较大的功率降低来进行补偿。换句话说,熔池越大,需要的功率“增量(delta)”就越大。在某些情况下,激光速度和焦点也可能会应用增量以帮助补偿较大的熔池。
38.在公开的实施例中,可以根据以下公式迭代地确定校正的激光功率水平,其中i是表示迭代数(第i次迭代)的整数,k1和k2是分别用于传感器误差和热误差的实验确定的增益系数:
39.corrected_power
i
=power
i
+k1*tracking_error
i
+k2*estimation_error
i
40.基于一组参考(即,期望)质量分数来确定以上等式中的跟踪误差(tracking_error),一组参考质量分数与基于构建期间测量到的传感器数据所预测的质量分数进行比较。替代地,如上所述,一组参考传感器数据值可以用作跟踪误差回路中的比较基础。随着
迭代收敛,跟踪误差接近于零。
41.基于预测到的传感器数据值(即,通过热模型被预测)和测量到的传感器数据的比较来确定以上等式中的估计误差(estimation_error)。随着迭代收敛,估计误差接近于零。
42.在公开的实施例中,可以基于参考强度和光电二极管传感器强度(即,测量到的传感器数据)之间的差异来确定传感器误差图。如果光电二极管传感器强度表示为“intensity
i”。通过将所有扫描路径(即影线)上的中值功率设置(即构建文件中设置的标称激光功率)除以影线上的中值测量强度(即,测量到的传感器数据)来给出功率的转换(例如,以瓦特为单位)。那么,(逐点的)传感器误差是:
43.sensor_error
i
=(ref
i
‑
intensity
i
)*intensity_to_power_scaling
44.这个计算出的传感器误差将对应于替代实施例中的跟踪误差,在替代实施例中,一组参考传感器数据值用作跟踪误差回路中的比较基础(即,其中将测量到的传感器数据与跟踪回路中的参考传感器数据值进行比较,而不是使用参考表面将测量到的传感器数据转换为质量分数并将质量分数与期望的质量分数目标进行比较的实施例)。以这种方式获得的传感器误差与光电二极管强度有关。校正功率然后由下式给出:
45.sensor_corrected_power
i
=power
i
+sensor_error
i
46.在不可能或不希望对激光功率进行连续小调整的实施例中,以这种方式确定的传感器校正功率可以作为统一功率设置被应用于扫描路径的子分段。如上所述,ilc回路适用于调整corrected_power
i
,以便零件的大块材料中的余热在整个构建过程中更均匀地分布。在某些情况下,可以以非常精细的时间标度连续调整输入功率。然而,对激光的许多小调整可能代价高昂。因此,代替逐点校正功率,规定分段(即子分段)常数模型有时更实用。为此,采用子分段程序,其中确定校正功率中的相对稳定性的子分段。然后,将沿子分段的校正功率的中值设定为分段中的校正功率。
47.在某些情况下,传感器误差以及因此的校正功率在接近分段的开始处往往很大。在这种情况下,为了算法的更好的稳定性,可以使用校正功率的移动平均值。例如,对于从(x0,y0)开始的每个影线,当|y
‑
y0|>0.1y时,只要例如|x
‑
x0|>100μm,可以在(x,y)处开始新的子分段。一旦校正功率信号稳定,x阈值增加到例如300μm。这个子分段过程的示例如下。对于每个传感器读数,为其所在的区域(例如,体素)确定相关联的热输入q
in
。
48.对于基于热模型的校正,可以在以下等式中引入热模型,用于通过传感器(例如雪崩光电二极管(apd))测量的强度:
49.intensity=c1*laser power+c2*vf+c3。
50.这个等式可以被重写,以如下解出功率:
51.thermal_power
i
=(intensity
i
‑
c2*vf
i
‑
c3)/c152.在这些等式中,c1、c2和c3是实验确定的系数,并且vf是在计算标称(即,初始)热模型期间为特定体素所确定的体积分率(变量thermal_power用于代替laser power)。
53.可以基于热输入q
in
与测量到的传感器强度之间的差异来确定热误差图。那么热误差为:
54.thermal_error
i
=ref
i
*intensity_to_power_scaling
‑
thermal_power
i
55.其中ref
i
是用于计算传感器误差的相同参考强度。
56.热模型的校正功率可以被计算为
57.thermal_corrected_power
i
=power
i
+thermal_error
i
58.使用与本文针对基于跟踪误差和估计误差的校正功率所呈现的等式相类似的等式,可以组合基于传感器和基于热模型的功率校正,以形成用于获得用于下一构建的总校正功率的模型:
59.corrected_power=power+k1*sensor_error+k2*thermal_error
60.其中k1和k2是增益参数。
61.在新的构建文件(例如,cli文件)中使用校正功率来构建下一迭代。在公开的实施例中,对于后续构建(即,在第一次功率校正构建之后),使用额外步骤。取代将上面讨论的子分段应用于已经被子分段的先前构建,子分段过程被应用于一组原始影线(即,扫描路径)。因此,新的传感器数据与先前构建一起被首先登记,以便可以在每个点处获得相关的输入功率。然后,用一组原始影线(从第一次未校正构建中获得)来标识这些分段。在此之后,可以应用以上呈现的步骤来获得新的功率校正构建。
62.在公开的实施例中,质量分数被限定并在概率意义上用于指出在构建零件中已经发生(或将要发生)哪种缺陷。例如,对于特定过程,为了可接受的零件质量,可能需要确定的熔池温度和尺寸。其他技术考虑感兴趣的变量,例如激光功率和速度,并尝试检测这些变量中的变化。然而,此类技术并未提供所确定的偏差是否会导致例如构建零件中的未熔合、孔隙率和裂纹以及此类缺陷的可能性的指示。另一方面,质量分数分析获取输入数据,并基于到质量分数的映射来预测构建零件中的缺陷及其可能性。常规地,通过对零件进行破坏性分析(例如,切割)来获得此类评估输出。一旦获得参数组,就用该参数组进行构建,从机器中取出样品(即,零件),并进行零件的切割。缺陷分数可以从显微镜下的自动分析中获得。当对一组点、对一组特定输入参数完成这个过程时,就会产生响应表面。基于从切割层的分析所确定的分数,每层可能存在良好的部分、不良的部分以及介于两者之间的灰色区域的部分。这些点可以在视觉上描绘为具有例如红色、蓝色和绿色区域的响应表面。响应表面是经由实验导出的数学函数,其中有一组输入参数,例如,激光功率、焦点、扫描速度、影线间距和层厚度。响应表面(即,函数)的输出可以是例如孔隙率分数、裂纹(即缺陷)分数和未熔合分数。
63.响应表面可以表示为n维向量函数。例如,如果函数具有输入x和y以及输出a和b,那么这个从{x,y}到{a,b}的函数将被称为2x2向量函数。在公开的实施例中,响应表面是n
×
m向量函数。输入可以是构建参数,例如,功率、速度、焦点、影线间距、层厚度以及测量到的参考传感器数据。参考表面的输出是从参考零件的材料特性的物理评价中导出的质量分数,例如,映射在零件的表面和/或体积上的孔隙率、未熔合、微裂纹等。
64.可以使用查找表来表示参考表面,在这种情况下,在表中查找的一组输入将提供一组预测输出值,例如质量分数。计算参考表面可能需要大量数据,但诸如使用机器学习技术进行外推的技术可以增强测量数据。在公开的实施例中,可以使用将孔隙率质量分数映射到激光功率水平的相对简单的参考表面。基于这个简单的参考表面,收集到的传感器数据可以输入到参考表面查找表中,这将输出表明构建零件的质量是否可接受的质量分数。如果以这种方式确定的质量分数是可以接受的,则设计,即构建文件,可以被冻结并宣布为生产做好准备。如果质量分数是不可接受的,则可以使用迭代学习控制(ilc)调整构建文件中的参数,如下文进一步详细讨论的。替代地,可以使用参考表面导出一组参考(即,目标)
传感器数据值并用作比较的基础。
65.公开的实施例提供了记录足够的传感器数据以扩展输入空间,使得传感器数据协同输入参数组一起提供足够的信息以允许缺陷分数的预测。进行破坏性测试以生成x
‑
mat表面,然后将这些结果推广到应用于任何构建零件。换句话说,将实验获得的x
‑
mat表面与输入参数对准以获得系统模型。
66.图2是用于使用质量分数生成器140确定生产零件的质量分数的系统200的图,该质量分数生成器140从增材制造机器110接收传感器数据。传感器数据可以包括来自与amm110中的致动器220相关联的致动器传感器210(例如,振镜位置传感器)的数据。传感器数据还可以包括来自环境传感器230的数据,例如,大气压力、氧气水平、气流、烟雾等。传感器数据还可以包括来自监测熔池特征的传感器240(例如,光电二极管、高温计、声发射等)的数据。此外,如下文进一步详细解释的,质量分数生成器140接收训练数据,例如从构建零件的实验测试中导出的响应表面/图250。
67.当增材制造机器110(例如dmlm机器)进行构建时,机器从熔池传感器240产生输出数据,例如以技术数据管理流(tdms)格式的数据文件的形式。数据也由机器的其他传感器产生,例如,测量定位激光点的振镜位置的致动器传感器210,以及各种环境传感器。其他数据源包括对增材机器的命令、材料特性数据和响应表面/图250。基于这些各种过程参数来确定构建零件特性。如上所述,来自dmlm机器的数据可以用作质量分数生成器的输入,质量分数生成器输出质量分数。在简单的情况下,这种质量分数可以是“通过/不通过”分数。在公开的实施例中,数字分数用于表示构建零件的质量。在公开的实施例中,在零件被构建之后(或在构建期间)使用质量分数来评价零件是否具有可接受的质量。这是代替或协同其他更耗时的评估过程(例如零件的切割和分析)完成的。
68.常规地,通过对零件进行破坏性分析来获得这样的评估输出,例如,当针对一组特定输入参数完成该过程时,可以生成响应图。基于从切割层的分析所确定的分数,可能存在产生良好结果的输入参数的组合、产生不良结果的组合以及介于两者之间的灰色区域。输入参数的这些组合可以在响应图中可视化地被描绘为2d或3d图的轴,而输出(例如,异常的密度或质量分数)可以用颜色编码的(例如,红色的、蓝色的、和绿色的)区域表示。
69.在公开的实施例中,响应图(例如,“响应表面”)可以是例如具有颜色编码图的2d、3d或3d上的实验数据的直接图示,或者通过实验导出的数学函数,其中有通过以下给出的输入:(i)一组参数,例如激光功率、聚焦偏移或束斑大小、扫描速度、影线间距和层厚度,和/或(ii)测量到或导出的过程变量,例如熔池深度、熔池宽度、熔池温度和/或热梯度。从响应图中获得的输出可以是例如异常或缺陷的密度的颜色编码图,例如孔隙、裂纹和未熔合缺陷的面积或体积百分比。应该注意的是,术语“响应表面”用于描述例如如上所述的各种过程输入与异常的密度之间的数学关系,而不是与正在构建的零件的物理表面相关的事物。
70.公开的实施例提供了记录足够的传感器数据以扩展输入空间,使得传感器数据协同输入参数组(例如,构建文件)一起提供足够的信息,以允许预测缺陷分数(例如,质量分数),而无需进行切割(即,剖切)和/或进行其他直接零件测试,例如光学相干断层扫描(oct)成像。在公开的实施例中,进行实验(例如,物理测试),以生成响应表面,然后例如通过创建模型将这些结果进行推广以应用于任何构建零件。
71.在公开的实施例中,在所有输入变量与质量分数的某种形式的量化概念之间创建关联,其可以是离散的或连续的(例如,低/中/高或实数)。模型的初始版本(例如,回归模型)可用于建立从输入变量到输出质量分数的直接关联。这种模型可以使用以输入变量与系数表示的等式,即,回归模型。输入变量与输出之间的关系可能是高度非线性和复杂的,因为可能存在大量输入(例如,256x256像素图像的每个像素的强度)并且可能只有一个输出,即,质量分数。可以创建输入变量的转换,即,可以使用明确地将输入变量转换为“特征空间”或神经网络、决策树等,即机器学习。这提供了使映射问题更容易的空间。换句话说,人们可以从直接变量开始,构造潜变量空间来简化问题。特别是,机器学习可用于获取高维多变量空间并将其映射到输出,其中已知潜在关系是复杂的、非线性的和非平凡的。
72.图3是质量分数生成器140的图。如上所述,质量分数生成器140接收来自amm的传感器数据130、正在生产的零件的标称构建文件120和从构建零件的测试中导出的参考数据250。传感器数据130和标称构建文件120被输入到机器学习算法310,机器学习算法310被训练以产生构建零件的质量分数。机器学习算法310使用响应表面/图250被训练,如上所述,响应表面/图250从零件的物理测试中导出。这种测试可以涉及对构建零件进行切片并且例如使用光学相干断层扫描(oct)来分析每个切片,以确定各种类型异常的存在和密度。可以进行质量分数计算330,例如对不同类型的异常的质量分数进行组合,并且结果由质量分数生成器140输出。替代地,机器学习算法310可以确定由质量分数生成器140直接输出的质量分数。
73.在公开的实施例中,可以考虑三种类型的异常:孔隙、裂纹和未熔合缺陷。可以针对此类特征中的每个特征预测此类异常的总体面积或体积百分比和/或密度的指示,例如质量分数,或者取决于这些特征相对于所需物理和机械性能的相对重要性,可以组合这些质量分数以获得总和、最大值、加权平均值等。例如,在某些情形下,裂纹可能是最重要的特征,而在其他情形下,孔隙密度和未熔合异常可能更为重要。
74.为了训练机器学习算法310,可以进行构建零件的切割以产生响应表面/图250。在公开的实施例中,切割的图像可以被划分为更小的子区域,例如3x3像素空间的区域(k x k,一般来说,其中k可以视为参数),从而将图像转化为向量,即使图像扁平化。可以生成具有多个输入的数值矩阵,例如,用于每个3x3像素空间的九个变量,以及一个输出变量。确定切割后的检查是否显示该3x3像素空间中的任何异常,这意味着人们正在局部查看图像并询问是否存在未熔合或任何孔隙率问题或其他异常。然后将标签分配给正在被检查的3x3像素。换句话说,在二进制标度上,这个3x3像素区域是否有异常。这相当于作为机器学习模型使用输入的典型数据格式的二进制分类问题,尽管这个问题的多类版本(由此不同的类将是不同的缺陷类型)也可以使用机器学习方法解决多类分类问题。无论哪种情况,多元潜变量模型,即机器学习模型,可以进行九元素向量(通常,n元素向量)到单个值之间的映射。使用这样的模型,可以创建强度的任何3x3(通常,k x k)像素组合并将其馈送到模型中,它将指示构建零件的相应子区域中存在缺陷(或缺陷类型)的可能性。
75.在替代实施例中,代替将测量到的零件数据扁平化成矩阵,图像可以作为一个整体被机器学习算法310使用,机器学习算法310可以例如是深度学习模型,例如全卷积网络或“u
‑
nets”。这种模型可用于直接从传感器数据构造预测的显微图像。在替代实施例中,可以使用一组三维切片,而不使用二维图像。换句话说,人们可以检查3x3x3像素立方,而不是
3x3像素组。此外,虽然已经描述了金属横截面,但也可以从2d计算机断层扫描(ct)切片生成三维重建体积,并将3d空间中的传感器数据与3d ct图像相关联。
76.在公开的实施例中,开发了统计质量传递函数以预测构建零件中的特定异常的密度。可以考虑各种类型的异常,例如孔隙、未熔合缺陷和裂纹。用于正在构建的零件的重要参数可以包括光电二极管信号的平均值和特定过程参数,例如,除以激光扫描速度的激光功率设置和功率。可以使用线性或非线性模型来提供传递函数,在公开的实施例中,传递函数具有相对高的r平方因子,例如高于约0.8的r平方因子。
77.在公开的实施例中,可以有至少两种类型的响应表面/图250。第一种类型可以基于受控实验产生,该受控实验试图基于输入参数(例如,激光功率、焦点和速度)来描述零件的材料的特性。在这种情况下,零件可以被生产并受到分析,例如切割和成像。算法,例如机器学习,可以结合相对少量的迭代而被使用。此类实验的结果提供了在激光参数空间中的区域的指示,其为零件给出了足够低的异常密度。这又可用于设置增材制造机器(amm)的初始设置。
78.第二种类型的响应表面/图250可以包括激光参数,例如上面提到的与传感器输出数据相结合的那些参数。例如,当制造过程正在运行时,可以使用诸如光电二极管和照相机之类的传感器来测量熔池的特征,例如,大小和温度。例如,传感器数据可以显示激光参数不必转化为稳定的熔池特征。例如,测量到的光电二极管信号可以不是恒定的,即,它可以具有变化并且可以不是关于零件的空间位置的干净信号。因此,传感器输出的特征,例如,光电二极管输出信号,可以提供另一种预测零件质量的方式。因此,由第一种类型的响应表面提供的可用于设置激光参数的材料特性的信息可通过传感器读数被补充,以提供更准确的零件质量的模型。
79.在公开的实施例中,质量分数生成器140接收传感器数据130,并应用多维数学公式或算法,例如机器学习算法310,以产生质量分数,质量分数可以是一个数字或一组数字。算法310可以通过进行零件的若干构建和进行物理测试(例如,切割和/或体积ct等)来被训练,以测量异常/缺陷。这可以包括构建相对简单的参考零件和使用不同的激光参数组来构建零件。此类实验可以作为上述实验的辅助,用于产生响应表面。质量分数生成器可适用于使用公式,该公式采用各种类型的异常,例如孔隙率、未熔合、裂纹,并结合相应的个体质量分数以产生总体质量分数(例如,通过使用加权平均)。组合质量分数可适用于向特定类型的异常给出更大权重。因此,可以通过实验,例如,通过生产和物理分析零件的多次迭代,来训练质量分数算法。
80.一旦算法310被充分训练,人们就可以输入测量到的传感器数据130和用于非实验情况的标称构建文件110,并且算法310可以输出响应表面(例如,表示例如激光参数和传感器数据的输入与例如异常密度的输出之间的多维关系的图),就像已经进行了物理测试和分析一样。然后可以根据质量分数对生成的响应表面进行量化。例如,质量分数可以经由进一步的计算(例如,异常密度的平均)而被获得。替代地,算法310可以直接输出一个或多个质量分数,其可被单独使用或被数学组合。确定的质量分数可以被反馈320到算法310。
81.图4描绘了用于更新在增材制造过程中生产的零件155的热模型150的系统400。如上所述,热模型150使用从amm 110(例如,dmlm打印机)接收到的标称构建文件120和传感器数据130来预测构建零件155的体积中的热输入(即,能量密度),其将由在扫描期间应用特
定水平的激光功率而产生。热模型150将预测到的能量密度转换成对应的预测到的传感器读数,例如,光电二极管传感器数据410。跟踪滤波器420将预测到的传感器读数410与从amm 110接收到的实际测量到的传感器数据430进行比较。差异用于生成更新的热模型440,更新的热模型440由跟踪滤波器420输出以替换现有的热模型150。
82.图5a描绘了零件500的一部分,其被体素化以产生标称热模型。例如,零件500可以被分成例如尺寸大约为0.3到1.0mm的立方体。其他大小也是可能的并且可以基于零件500的几何结构而被选择。当激光在构建过程期间扫描每个体素时,体素中产生的一部分热量消散到相邻的体素520。如图5b所示,对于特定体素510,可以通过确定在确定的半径(r)内的相邻体素的数量来估计散热。例如,如果体素510(如从顶部观察)在所有侧面都被相邻的体素520包围,则可以期望体素510耗散由扫描产生的相对大部分的热量。另一方面,如图5c所示,如果体素510(从侧面观察)位于构建零件500的顶部,则散热半径仅适用于顶表面处或顶表面下方的相邻体素520,这使得整个(即,上部)半球没有相邻体素来提供散热。
83.在公开的实施例中,提供了以标称热模型(即,用于正在构建的零件的散热模型)开始的跟踪回路。在这种情况下,ilc的输入包括零件的热模型和扫描文件(例如,cli构建文件)。基于此,ilc基于热特征来预测传感器响应将是什么样子,例如,零件中的哪些点将比可允许的更热、比可允许的更冷等。例如,如果应用相同量的能量,角部具有较少的热流/导热性将因此变得比零件的其他部分更热。另一方面,在零件的中间区域,有很多导热性(即,更多的路径用于散热),因此如果应用相同量的能量,则有问题的区域将会更冷,因为热量可能更容易流走。
84.如果完美的热模型可用,则将不需要迭代学习回路。在这种情况下,人们将拥有模型和参考,例如基于传感器数据的响应表面/图,因此可以生成理想的构建文件以实现特定的限定的质量结果。在实践中,近似模型可用,近似模型足以用于控制目的,但会导致实际传感器数据与预测值不同。这些差异(即估计误差)可以通过跟踪滤波器被反馈以更新模型。因此,对于每个构建,标称热模型基于估计误差被更新。经过几次迭代后,具有更新参数组的标称热模型将具有非常高的保真度,这将有助于ilc更快地收敛。
85.如上所述,标称(即,初始)热模型的确定可以包括通过创建处于不同分辨率的体素并且对每个体素计算在其下面连接多少金属,来分析零件几何结构,例如在三维中具有梯形几何结构的零件。例如,在体素在零件中间的情况下,那么所有体素体积在其下面将会有固体金属,所以体积分率(vf)将是1。另一方面,在角部附近,体积分率可以约为1/4。在拱形几何特征的情况下,中间点处的体素几乎没有金属,因此体积分率将接近于零。通过这种方式,分析几何结构,并为每个体素分配体积分率,并且例如以文件格式hdf5存储模型。可以进行一组实验,设置激光功率、速度和关注体积分率,并使用测量到的强度传感器数据来创建回归分析,该回归分析可以基于模型的输入和体积分率来预测传感器数据。这是预测传感器数据的标称热模型。如果热模型与测量到的强度传感器数据不匹配,则基于跟踪滤波器算法调整模型的系数(例如,本文所讨论的c0、c1和c2)以使其更好地匹配。
86.图6是根据一些实施例的装置600的框图。装置600可以包括通用或专用计算装置并且可以执行程序代码以进行本文所述的任何功能。装置600可以包括系统100的一个或多个元件的实现。根据一些实施例,装置600可以包括未示出的附加元件。
87.装置600包括可操作地联接到通信设备620、数据存储设备/存储器630、一个或多
个输入设备(未示出)和一个或多个输出设备630的处理器610。网络接口620可以促进与例如应用服务器的外部设备的通信。输入设备可以在装置600中或在经由网络接口620连接的客户端设备中实现。输入设备可以包括例如键盘、按键、鼠标或其他指点设备、麦克风、旋钮或开关、红外线(ir)端口、扩展坞和/或触摸屏。输入设备可用于例如操纵图形用户界面并将信息输入到装置600中。输出设备630可以包括例如显示器(例如,显示屏)、扬声器和/或打印机。
88.数据存储设备/存储器640可以包括任何设备,包括磁存储设备(例如,磁带、硬盘驱动器和闪存)、光存储设备、只读存储器(rom)设备、随机存取存储器(内存)等的组合。
89.存储设备640存储用于控制处理器610的程序和/或平台逻辑。处理器610执行程序的指令,从而根据本文描述的任何实施例进行操作,包括但不限于过程。
90.程序可以以压缩的、未编译的和/或加密的格式存储。程序还可以包括其他程序元素,例如由处理器610使用的与外围设备接口的操作系统、数据库管理系统和/或设备驱动器。
91.前述图表示根据一些实施例的用于描述过程的逻辑架构,并且实际实现可以包括以其他方式布置的更多或不同的部件。可以结合其他实施例使用其他拓扑。此外,本文描述的每个系统可以由经由任意数量的其他公共和/或专用网络彼此通信的任意数量的计算设备来实现。两个或更多个这样的计算设备可以彼此远离并且可以经由任何已知的网络方式和/或专用连接彼此通信。每个计算设备可以包括任何数量的适合提供这里描述的功能以及任何其他功能的硬件和/或软件元件。例如,在系统100的实现中使用的任何计算设备可以包括用于执行程序代码的处理器,使得计算设备如本文所述那样操作。
92.在此讨论的所有系统和过程可以体现在存储在一个或多个计算机可读非暂时性介质上的程序代码中。这种介质非暂时性介质可以包括例如固定盘、软盘、cd
‑
rom、dvd
‑
rom、闪存驱动器、磁带和固态ram或rom存储单元。因此,实施例不限于硬件和软件的任何特定组合。
93.本发明的进一步方面由以下条款的主题提供:
94.1.一种用于向增材制造机器提供更新的构建参数的方法,所述方法包括:在使用第一组构建参数制造零件期间,经由包括处理器的设备的通信接口,从所述增材制造机器接收传感器数据;接收所述第一组构建参数;使用所述设备的所述处理器,基于所述第一组构建参数和接收到的传感器数据,确定评估参数;使用所述设备的所述处理器,基于从所述第一组构建参数导出的所述零件的热模型,生成热数据;使用所述设备的所述处理器,将第一算法应用于接收到的传感器数据、确定的评估参数和生成的热数据,以产生第二组构建参数,所述第一算法被训练以改进所述评估参数;和将所述第二组构建参数输出到所述增材制造机器以生产第二零件。
95.2.根据前述条款中任一项所述的方法,其中所述评估参数包括质量分数,所述质量分数通过将第二算法应用于所述第一组构建参数和所述接收到的传感器数据而被确定。
96.3.根据前述条款中任一项所述的方法,其中通过接收从对至少一个参考零件进行的物理测量中导出的参考来训练所述第二算法,使用一组参考构建参数构建所述至少一个参考零件。
97.4.根据前述条款中任一项所述的方法,其中所述热数据的生成包括基于标称热模
型和所述第一组构建参数计算第一组热数据值。
98.5.根据前述条款中任一项所述的方法,其中所述热数据的生成进一步包括:基于计算出的第一组热数据值与所述接收到的传感器数据的比较来确定更新的热模型;和基于所述更新的热模型来计算第二组热数据值。
99.6.根据前述条款中任一项所述的方法,其中所述标称热模型通过以下方式导出:将所述零件的体积划分为体素;确定每个所述体素的中心的限定半径内的周围材料的相对量;和基于周围材料的所述相对量计算每个体素的热数据值。
100.7.根据前述条款中任一项所述的方法,其中从激光功率传感器、致动器传感器、熔池传感器和环境传感器中的至少一个接收所述传感器数据。
101.8.一种用于向增材制造机器提供更新的构建参数的系统,所述系统包括:包括通信接口的设备,所述设备被构造为在使用第一组构建参数制造零件期间,从所述增材制造机器接收传感器数据,所述设备进一步包括处理器,所述处理器被构造为进行:接收所述第一组构建参数;基于所述第一组构建参数和接收到的传感器数据,确定评估参数;基于从所述第一组构建参数导出的所述零件的热模型,生成热数据;将第一算法应用于接收到的传感器数据、确定的评估参数和生成的热数据,以产生第二组构建参数,所述第一算法被训练以改进所述评估参数;和将所述第二组构建参数输出到所述增材制造机器以生产第二零件。
102.9.根据前述条款中任一项所述的系统,其中所述评估参数包括质量分数,所述质量分数通过将第二算法应用于所述第一组构建参数和所述接收到的传感器数据而被确定。
103.10.根据前述条款中任一项所述的系统,其中通过接收从对至少一个参考零件进行的物理测量中导出的参考来训练所述第二算法,使用一组参考构建参数构建所述至少一个参考零件。
104.11.根据前述条款中任一项所述的系统,其中所述热数据的生成包括基于标称热模型和所述第一组构建参数计算第一组热数据值。
105.12.根据前述条款中任一项所述的系统,其中所述热数据的生成进一步包括:基于计算出的第一组热数据值与所述接收到的传感器数据的比较来确定更新的热模型;和基于所述更新的热模型来计算第二组热数据值。
106.13.根据前述条款中任一项所述的系统,其中所述标称热模型通过以下方式导出:将所述零件的体积划分为体素;确定每个所述体素的中心的限定半径内的周围材料的相对量;和基于周围材料的所述相对量计算每个体素的热数据值。
107.14.一种存储程序指令的非暂时性计算机可读存储介质,所述程序指令在被执行时使处理器进行用于向增材制造机器提供更新的构建参数的方法,所述方法包括:在使用第一组构建参数制造零件期间,经由包括所述处理器的设备的通信接口,从所述增材制造机器接收传感器数据;接收所述第一组构建参数;使用所述设备的所述处理器,基于所述第一组构建参数和接收到的传感器数据,确定评估参数;使用所述设备的所述处理器,基于从所述第一组构建参数导出的所述零件的热模型,生成热数据;使用所述设备的所述处理器,将第一算法应用于接收到的传感器数据、确定的评估参数和生成的热数据,以产生第二组构建参数,所述第一算法被训练以改进所述评估参数;和将所述第二组构建参数输出到所述增材制造机器以生产第二零件。
108.15.根据前述条款中任一项所述的计算机可读存储介质,其中所述评估参数包括质量分数,所述质量分数通过将第二算法应用于所述第一组构建参数和所述接收到的传感器数据而被确定。
109.16.根据前述条款中任一项所述的计算机可读存储介质,其中通过接收从对至少一个参考零件进行的物理测量中导出的参考来训练所述第二算法,使用一组参考构建参数构建所述至少一个参考零件。
110.17.根据前述条款中任一项所述的计算机可读存储介质,其中所述热数据的生成包括基于标称热模型和所述第一组构建参数计算第一组热数据值。
111.18.根据前述条款中任一项所述的计算机可读存储介质,其中所述热数据的生成进一步包括:基于计算出的第一组热数据值与所述接收到的传感器数据的比较来确定更新的热模型;和基于所述更新的热模型来计算第二组热数据值。
112.19.根据前述条款中任一项所述的计算机可读存储介质,其中所述标称热模型通过以下方式导出:将所述零件的体积划分为体素;确定每个所述体素的中心的限定半径内的周围材料的相对量;和基于周围材料的所述相对量计算每个体素的热数据值。
113.20.根据前述条款中任一项所述的计算机可读存储介质,其中从激光功率传感器、致动器传感器、熔池传感器和环境传感器中的至少一个接收所述传感器数据。
114.本文描述的实施例仅用于说明的目的。本领域技术人员将认识到,可以通过对上述实施例的修改和变更来实践其他实施例。