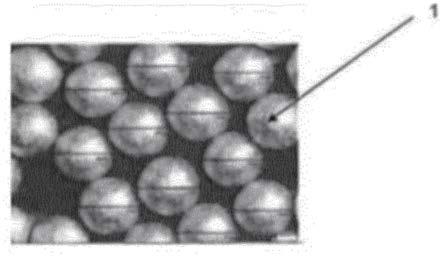
用于电路板组装的表面金属化并整粒的复合焊料球
1.本发明总体上涉及复合焊料球的制造以及这些焊料球作为电路板组装的互连方案的用途。
2.对于日益小型化且不使用铅的电路板组装技术的探索越来越多地鼓励该技术领域的工业从业者寻求创新方案,以实现机械应力敏感型组件之间的互连,例如cbga(陶瓷球栅阵列“ceramic bail grid array”的英文缩写)型球栅阵列,微机电系统(常用英文缩写mems“micro electro mechanical system”来表示)。
3.柔性球(如[图1]所示)是一项用于实现系统级封装的技术,通常用英文缩写sip“system in package”)来表示。它们具有焊接触点,使得它们可以轻松地组装在封装件中。
[0004]
然而,目前,该领域中现在使用的柔性球存在由聚合物材料构成致密内芯的缺陷,这会对初始球粒的制粒和整粒过程的产率以及球粒最终密度的相关制造成本产生负面影响。另一方面,在后续钎焊操作过程中,颗粒的内芯和金属外壳之间可能会遇到热膨胀不同的问题。
[0005]
为了克服这个缺陷,申请人开发了一种表面金属化并整粒的复合焊料球的制造方法,所述焊料球包括内芯和外壳,所述内芯由直径为d0的发泡聚苯乙烯(eps)球形载体颗粒构成,并且粒内孔隙率至少为50%,所述外壳包覆所述载体颗粒并且由多层金属表面层构成,尤其包括厚度为e
cu
的铜涂层、至少一层厚度为e
ni
的镍层、厚度为e
au
的金表面层,使得成品颗粒具有直径df。
[0006]
根据本发明,该方法的特征在于其包括以下步骤:
[0007]
a)提供载体颗粒的第一步骤,然后是
[0008]
b)对所述载体颗粒进行粒度分选的第一步骤,包括物理和/或机械分离载体颗粒的步骤,载体颗粒的直径为d0,公差为+/-5%,例如d0=d
f-2*(e
ni
+e
cu
+e
au
),d0可以选定为200μm到1000μm之间;
[0009]
c)活化如此选定的载体颗粒的处理步骤,以获得活化载体颗粒;
[0010]
d)通过一层或多层铜的自催化化学沉积,对所述活化载体颗粒进行金属化的第一步骤,重复该步骤直至铜层的厚度达到15μm到35μm,从而获得铜包覆的载体颗粒;
[0011]
e)通过至少一层与磷合金化的镍层nip的自催化化学沉积,对铜包覆的载体颗粒进行金属化的第二步骤,其中磷与所述nip层总重量的质量百分比为7到10%,进行该步骤直至化学镍层的厚度e
ni
达到4μm到7μm,从而获得化学镍包覆的载体颗粒;
[0012]
f)对化学镍包覆的载体颗粒进行金属化的第三步骤(包括金沉积步骤,该金沉积步骤采取电置换工艺,所述电置换工艺是通过在含有金离子(通常根据现有技术来实现)的水溶液中浸渍来实现的),从而获得金属化复合焊料球,并且表面包覆有厚度e
au
在0.05μm到0.12μm之间的金表面层;
[0013]
g)对如此金属化的颗粒进行粒度分选的第二步骤,以分选和选出表面金属化复合焊料球(1),其直径为df,公差为+/-5%。
[0014]
发泡聚苯乙烯(eps)球粒具有加热时能够减小粒度的优点,因此提供了通过热处理进行整粒的可能性。
[0015]
本发明中,粒内孔隙率是指载体颗粒的内部孔隙率,在其表面和/或内部可以观察到不同类型的孔隙:孔道、网格、“袋状孔”、盲孔和表面凸凹。它可以例如通过氦比重计来测量。
[0016]
根据本发明的方法的第一步骤是提供载体颗粒(步骤a)。
[0017]
有利地,可以使用粒内孔隙率大于90%的发泡聚苯乙烯(eps)球粒。
[0018]
在根据本发明的方法中,首先进行对这些载体颗粒进行粒度分选的第一步骤(步骤b),包括物理和/或机械分离出选定直径d0在200μm到1000μm之间的载体颗粒(10)。根据本发明方法的一种有利实施方式,载体颗粒的粒度分选步骤b)可以包括机械筛分以分选和选出选定直径d0在200μm到1000μm之间的载体颗粒。在实际操作中,将选择粒度对应于目标值d0+/-5%的载体颗粒。
[0019]
如果使用发泡聚苯乙烯(eps)球粒作为载体颗粒,则载体颗粒的粒度分选步骤b)可以包括载体颗粒的机械筛分。然后可以有利地最后在100℃到120℃之间,优选110℃到120℃之间的温度下对如此分选的上层颗粒(也就是说粒度大于d0+5%的颗粒)进行热处理,从而提高初始球粒群的整粒产率。实际上,由于发泡聚苯乙烯(eps)球粒的直径会在加热时减小,因此如果将机械筛分与加热相结合,则先前分选的上层球粒在筛分时的截留物直径会减小,从而使这些最初被报废的球粒达到目标直径d0+/-5%。这样尤其可以通过提高具有直径d0的球粒数量的产率来显着降低生产成本。该热处理步骤可以有利地在流化床中通过气体途径或液体途径来完成,从而保持球粒的初始球度。
[0020]
在粒度分选步骤b)结束时,对先前选定的载体颗粒进行活化处理(步骤c),以获得活化载体颗粒。
[0021]
在本发明中,活化处理是指活化载体颗粒表面的处理,从而可以很好地控制后续的金属化处理。
[0022]
这种活化处理的第一有利实施方式可以包括例如通过还原溶液中的银离子,使银晶核沉积到在先前选定的载体颗粒表面上,其中银沉积物是通过萌发-生长形成的。该操作可以通过例如还原乙二醇基溶液中的氨性硝酸银来实现。
[0023]
这种活化处理的另一种有利实施方式也可以包括通过气相物理沉积(pvd),使小于或等于1μm的薄层铜沉积到先前选定的载体颗粒表面上。
[0024]
一旦载体颗粒被活化,进行所述的颗粒金属化(步骤d至f)。
[0025]
对活化载体颗粒进行金属化的第一步骤(步骤d),是一层或多层铜的自催化化学沉积步骤,重复该步骤直至铜层的厚度达到15μm到35μm,从而获得铜包覆的载体颗粒。可能需要多次连续金属化才能获得预期的铜厚度。
[0026]
如果希望焊料球是空心的或近似空心球的,可以在金属化步骤d和e之间部分或完全溶解,或者部分或全部热分解构成载体颗粒的发泡聚苯乙烯(eps)。为此,在步骤e中形成的铜层应该足够薄或足够多孔,以使eps消失。
[0027]
金属化的第二步骤(步骤e)包括通过至少一层与磷合金化的镍层nip的自催化化学沉积,对步骤d)中获得的铜包覆载体颗粒(可能转化成空心或近似空心的球粒)进行金属化,其中磷与nip层(或化学镍)总重量的质量百分比为7%到10%。进行该步骤e)直至化学镍层(111)的厚度eni达到4μm到7μm,从而获得化学镍包覆的载体颗粒。
[0028]
金属化的第三步骤(步骤f)包括通过在含有金离子的溶液中浸渍,以对化学镍包
覆的载体颗粒金属化,从而获得金属化复合焊料球,并且表面包覆有厚度e
au
在0.05μm到0.12μm之间的金表面层。
[0029]
最后,根据本发明的方法的最后步骤(步骤g)是对如此金属化的颗粒进行粒度分选的第二步骤,以分选和选出表面金属化的复合焊料球,其直径为df,公差为+/-5%。
[0030]
本发明的目的还在于可以通过根据本发明的制造方法获得的焊料球粒。
[0031]
根据本发明的第一特别有利的实施方式,焊料球粒可以具有以下特征:
[0032]-直径d0约为630μm+/-5%,
[0033]-铜层的厚度约为30μm,
[0034]-nip层的厚度e
ni
约为5μm,
[0035]-金层的厚度e
au
在0.05μm到0.12μm之间,
[0036]-直径df约为700μm+/-5%。
[0037]
根据本发明的第二特别有利的实施方式,焊料球粒可以具有以下特征:
[0038]-直径d0约为350μm+/-5%μm,
[0039]-铜层的厚度ecu约为20μm,
[0040]-nip层的厚度e
ni
约为5μm,
[0041]-金层的厚度e
au
约为0.1μm,
[0042]-直径df约为400μm+/-5%。
[0043]
有利地,根据本发明的焊料球可以是空心(或气近似空心)球粒,在采用发泡聚苯乙烯(eps)的情况下,包括由体积最高50%的聚合物材料构成的内芯。这类焊料球是通过根据本发明的方法获得的,在该方法的过程中,在步骤d)和e)之间包括部分或完全溶解的步骤,部分或全部热分解构成起始载体颗粒的发泡聚苯乙烯(eps)的步骤。
[0044]
本发明的目的还在于根据本发明的球粒在电路板组装方面的用途。实际上,根据本发明的球粒的结构可以实现机械应力敏感型部件(cbga、mems等)之间的互连。它们还具有一个优点是一方面保持受控定位,另一方面限制基材和部件之间互连时的机械应力。
[0045]
通过下文中作为非限制性示例给出的描述,并参照附图,将能够理解本发明的其他优势和特点,其中:
[0046]
[图1]是现有技术中已知的柔性球示例的示意图,其中包括焊接触点,用于使它们组装到集成电路封装件中,
[0047]
[图2]是根据本发明的柔性球示例的示意图,
[0048]
[图3]也是根据本发明的柔性球示例的示意图,但是为了清楚起见,金表面层未示出,
[0049]
[图4]是根据本发明方法的活化步骤c)结束时获得的活化eps球粒(包覆有银薄层)的照片,
[0050]
[图5]是根据本发明方法的利用铜金属化步骤d)结束时获得的活化且包覆有铜层的eps球粒的照片,
[0051]
[图6]是根据本发明方法的利用化学镍金属化步骤e)结束时获得的活化且连续包覆有铜层和化学镍层(nip)的eps球粒的照片,
[0052]
[图7]是根据本发明的焊料球的照片,其包括根据本发明方法的利用化学镍金属化步骤f)结束时获得的活化且连续包覆有铜层、化学镍层(nip)和金层的eps球粒,
[0053]
[图8]是根据本发明的球粒截面的光学显微镜图像,其中示出了在根据本发明方法的第一实施方式结束时获得的载体eps球粒和连续的铜层、化学镍层和金层(eps球粒直径约为655μm,铜层厚度为17μm),
[0054]
[图9]示出了根据本发明方法的第二实施方式的步骤d)结束时获得的eps球粒截面的光学显微镜下拍摄的图像(a)(eps球粒直径约为660μm,铜层厚度为15μm),以及根据本发明方法的第三实施方式的步骤d)结束时获得的铜包覆eps球粒截面的光学显微镜下拍摄的图像(b)(eps球粒直径约为630μm,铜层厚度为31μm),
[0055]
[图10]示出了在光学显微镜下拍摄的第一图像a,其中示出了eps载体球粒10,其粒度d0的分布在0.5到1mm之间,以及在光学显微镜下拍摄的第二图像b,其中示出了选定直径在0.63到0.66mm之间的粒度分选后获得的eps载体球粒10。
[0056]
[图11]示出了根据本发明的金属化球粒1,其直径约为400μm+/-5%,
[0057]
[图12]为示出了在360℃下热处理之前的根据本发明的金属化球粒1的sem图像(a),以及在360℃下经过了20分钟后续热处理以确认球粒耐热性的根据本发明的金属化球粒1的sem图像(b)。
[0058]
[图13]为带有致密聚苯乙烯内芯的球粒的sem图像,所述球粒按照根据本发明方法的步骤a至g进行了金属化处理,并在360℃下经过了20分钟后续热处理以确认球粒的耐热性(b)。
[0059]
[图1]在现有技术背景介绍中进行了描述。它具体示出了具有焊接触点1、2以便于组装的柔性球。在以下实施例中对图2至图12进行了更详细地描述,这些实施例解释了本发明而不限制其范围。
实施例
[0060]
装置和仪器
[0061]-自催化化学沉积装置(用于铜和化学镍沉积);
[0062]-机械筛分装置
[0063]
起始物
[0064]-直径在595μm到665μm之间的发泡聚苯乙烯球粒(eps);
[0065]-直径约为400μm的发泡聚苯乙烯球粒(eps),
[0066]-化学镍(含重量比7到10%的p),
[0067]-铜,
[0068]-硝酸银,
[0069]-金离子。
[0070]
表征:形态分析
[0071]
光学显微镜观察是利用光学显微镜在表面([图4]至[图7])和横截面([图8]和[图9])上完成的。
[0072]
图12和13中的观察是利用扫描电子显微镜(sem)获得的。
[0073]
实施例1:
[0074]
按照根据本发明方法的第一实施方式,制造根据本发明的焊料球。
[0075]
根据本发明的焊料球是按照根据本发明方法的第一实施方式,利用发泡聚苯乙烯
(eps)球粒制造的。制造分为以下几个步骤:
[0076]-1)对粒度分布在0.5到1mm之间的eps球粒10进行第一次机械筛分,以便仅保留直径约为630μm的球粒([图10]);
[0077]-2)然后,对eps颗粒进行表面活化,以便可以在后续的金属化处理中具有良好的附着力。活化球粒10'是通过在球表面沉积银晶核获得的。该操作是在硝酸银还原浴中进行的。该处理结束后,获得如[图4]所示的球粒10';
[0078]-3)第三步骤包括利用铜进行金属化处理。通过自催化化学沉积获得厚度ecu为30μm的铜层110(参见[图2]、[图3])。该处理结束后,获得如[图5](表面示图)或[图9]所示部分b(剖视图)的球粒10";
[0079]-第四步骤包括在铜层110上沉积一层厚度为5μm的化学镍层(nip)111(参见[图2]、([图3])。该涂层也是通过自催化化学沉积产生的。该处理结束后,获得如[图6]所示的球粒10'";
[0080]-金属化的最后一层是金表面层112(参见[图2])。沉积是通过电置换来实现的,该电置换是通过在含有金离子的水溶液中浸渍化学镍包覆的球粒10'"。因此沉积了厚度e
au
在0.05μm到0.12μm之间的金层(参见[图2])。该处理结束后,获得如[图7]所示的焊料球1;
[0081]-最后一个步骤是球粒的粒度分选,从而仅保留根据本发明的直径df为700μm+/-5%的球粒1。
[0082]
实施例2:
[0083]
按照根据本发明方法的第二实施方式,制造根据本发明的焊料球
[0084]
采用与实施例1相同的材料制备了根据本发明的焊料球,其中载体球粒的直径为660μm并且铜沉积厚度约为15至17μm(参见图8和图9a)。
[0085]
实施例3:
[0086]
按照根据本发明方法的第三实施方式,制造根据本发明的焊料球
[0087]
采用与实施例1和2相同的材料制备了根据本发明的焊料球,从而获得直径df大约为400μm+/-5%的球粒(参见[图12])。
[0088]
实施例4:
[0089]
筛分步骤后热处理的作用
[0090]
sem分析([图12])呈现了在360℃热处理之前(12a)和之后(12b)的根据本发明的金属化并整粒的球粒。观察到球粒在热处理后没有发生降解/改性,这证明其具有温度稳定性。
[0091]
实施例5(对照)
[0092]
为了建立球粒重量的对照分析,根据本发明方法的步骤a至g(cu/nip/au金属化)制备了3批球粒(直径d0为700μm+/-5%),然后在360℃下经过了20分钟后续热处理(b)以确认球粒的耐热性。为此,使用了3种不同类型的载体球粒:
[0093]-第一批由发泡聚苯乙烯球粒制成(孔隙率约为95%),
[0094]-第二批由交联聚苯乙烯球粒制成(致密),
[0095]-第三批由铜金属球粒制成(致密)。
[0096]
对每批取样1000粒并称重。所得结果汇总如下表1所示:
[0097]
表1
[0098]
载体球粒1000个金属化球粒的重量(g)发泡聚苯乙烯0.225致密聚苯乙烯0.390致密铜2.100
[0099]
根据本发明由发泡聚苯乙烯(第一批)制备的球粒,其相比现有方案(有机或金属材料制成的致密内芯)的质量减少因子为1.7到9.4之间。
[0100]
另一方面,已经注意到,相比由致密内芯获得的球粒(第二批和第三批球粒),球粒的热稳定性由于使用了eps内芯(第一批根据本发明的球粒)而得到了改善。实际上发现,从360℃开始,由致密聚苯乙烯制成的球粒(第二批和第三批球粒)表现出行为缺陷,球粒表面出现有机物“液滴”(图1)。根据本发明的由发泡聚苯乙烯制成的球粒(第一批球粒)未观察到这种现象。