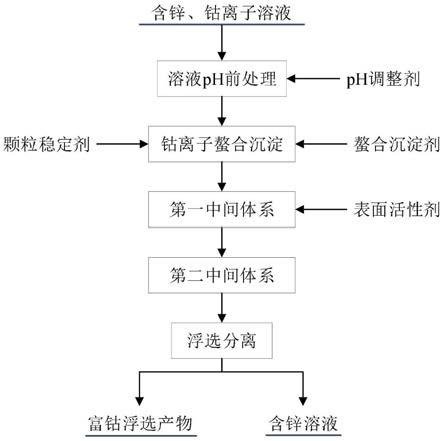
1.本发明属于钴回收技术领域,特别涉及一种溶液中锌、钴离子的分离方法。
背景技术:2.钴是一种支撑高科技领域发展的战略金属资源。随着电子产品的普及和新能源汽车的推广,钴在电池材料中的应用越来越广泛,钴的需求量也与日俱增。然而,全球钴储量仅700万吨左右,分布相对集中。我国储量仅占全球储量的1.1%,且大多以锌、铜、镍等金属的硫化矿伴生,对含钴矿物直接冶炼提取不仅工艺难度大、成本高,而且难以满足我国迅速增长的钴消费需求。所以,各类含钴资源(含钴固体废弃物、工业废水等)的分离提取技术开发是保障钴原料供应的必要任务。
3.含锌钴的冶炼渣、工业固废、废旧电池材料是重要的含钴二次资源,通过酸浸工艺可使金属组分进入到浸出液中;另外,还有一部分工业废水中存在一定浓度的锌钴离子。无论是含锌钴二次资源中钴的分离提取还是溶液中钴的净化除杂,都需要面临溶液中锌、钴离子的高效分离问题,即需要对溶液中钴离子具有高选择性的分离试剂和方法。
4.目前,溶液中锌钴的分离方法主要有锌粉置换法、萃取法、沉淀法等。锌粉置换法需要大量锌粉,利用锌钴电位差,实现溶液中钴的还原并形成沉淀;但该方法需要加入超过理论量数十倍的锌粉,形成的除钴渣中含有大量未反应的锌粉,因此,除钴渣中钴的提取将再次面临锌钴分离的问题。采用溶剂萃取法分离溶液中锌钴时,由于上述溶液中钴离子含量普遍较低,萃取效果不佳;同时,采用沉淀法分离溶液中锌钴时,可用沉淀剂包括硫化物、黄药等,但同样受到钴离子含量低的影响,难以形成较大的沉淀颗粒,沉降过程缓慢,难以彻底分离。
5.以上溶液中锌钴离子分离的方法均受限于溶液中钴离子浓度较低而造成的选择性差、分离效率低且不彻底等问题。因此,如何能够高效分离溶液中锌钴离子成为亟待解决的问题。
技术实现要素:6.鉴于以上分析,本发明旨在提供一种溶液中锌、钴离子的分离方法,用以解决现有技术中由于溶液中钴离子浓度低而造成的选择性差、分离效率低且不彻底的问题,能实现溶液中锌、钴离子的高效分离。
7.本发明的目的主要是通过以下技术方案实现的:
8.本发明提供了一种溶液中锌、钴离子的分离方法,包括:
9.步骤1、通过ph调整剂将含锌、钴离子的溶液的ph调整至酸性;
10.步骤2、在一定温度下,向上述溶液中同时加入钴离子螯合沉淀剂和颗粒稳定剂,搅拌混合,获得第一中间体系;所述第一中间体系为含有钴离子螯合沉淀颗粒的溶液;
11.步骤3、向第一中间体系中加入表面活性剂,并搅拌混合均匀,获得第二中间体系;所述第二中间体系为含有钴沉淀悬浮颗粒的悬浮液;
12.步骤4、采用浮选分离装置对上述第二中间体系进行充气浮选,收集得到含有钴沉淀的颗粒。
13.进一步的,所述步骤1中,含锌、钴离子的溶液中,锌离子的浓度为0.5~185g/l,钴离子的浓度为1mg/l~5g/l。
14.进一步的,所述步骤1中,调整后的溶液的ph为4.5~6.0。
15.进一步的,所述步骤2中,温度为20~50℃。
16.进一步的,所述步骤2中,钴离子螯合沉淀剂为乙基黄原酸钠和乙基黄原酸钾中的一种或二者混合物。
17.进一步的,所述步骤2中,钴离子螯合沉淀剂的加入量与溶液中钴离子的摩尔比为4:1~10:1。
18.进一步的,所述步骤2中,颗粒稳定剂包括无水硫酸铜和/或含水硫酸铜。
19.进一步的,所述步骤2中,颗粒稳定剂的加入量与溶液中钴离子的摩尔比为1:1~3:1。
20.进一步的,所述步骤2中,搅拌速率小于或等于100rpm,搅拌时间为10~60min。
21.进一步的,所述步骤3中,悬浮颗粒的颗粒直径为20~50μm。
22.与现有技术相比,本发明至少能实现以下技术效果之一:
23.1)本发明首次将螯合沉淀-浮选方法应用于溶液中锌钴离子的分离,利用钴离子螯合沉淀剂的选择性络合作用,钴离子螯合沉淀剂与溶液中的钴离子选择性螯合,并通过同时加入的颗粒稳定剂,使钴离子与药剂的螯合物形成悬浮颗粒,再借助微泡浮选技术,最终实现溶液中钴离子的选择性提取,从而达到高效分离溶液中锌、钴离子的目的。本发明的方法可用于各种含有低浓度钴离子的溶液中锌钴离子分离及钴离子去除,锌钴分离效果好,钴离子回收率高,成本低,流程短。
24.2)现有锌钴分离技术包括锌粉置换法、黄药除钴法、α-亚硝基-β-萘酚除钴法。锌粉置换法:锌粉消耗量大,一般是理论量的20倍以上,作业时间长,需要在80℃左右进行,且常会产生ash3和sbh3有毒气体。黄药除钴法:由于溶液中钴离子浓度较低,要使反应迅速进行且除钴彻底,必须加入过量的黄药,用量一般为理论用量的10~15倍。α-亚硝基-β-萘酚除钴法:与黄药除钴法具有同样的缺点,药剂用量大,为保证净化后液电解的品质,需要采用活性炭吸附浸出液中过量的有机药剂。本发明的方法与现有方法相比,本发明对溶液中金属离子浓度适用范围广,尤其在低浓度离子去除方面具有更强的适用性,试剂用量低;可连续进行,溶液处理量大,且固液分离速率快、金属离子分离更为彻底。
25.本发明的其他特征和优点将在随后的说明书中阐述,并且,部分可从说明书中变得显而易见,或者通过实施本发明而了解。本发明的目的和其他优点可通过在所写的说明书以及附图中所特别指出的内容来实现和获得。
附图说明
26.附图仅用于示出具体实施例的目的,而并不认为是对本发明的限制,在整个附图中,相同的附图标记表示相同的部件。
27.图1为本发明的分离方法的工艺流程图。
具体实施方式
28.以下结合具体实施例对一种溶液中锌、钴离子的分离方法作进一步的详细描述,这些实施例只用于比较和解释的目的,本发明不限定于这些实施例中。
29.一种溶液中锌、钴离子的分离方法,包括以下步骤:
30.步骤1、通过ph调整剂将含锌、钴离子的溶液的ph调整至酸性;
31.步骤2、在一定温度下,向上述溶液中同时加入钴离子螯合沉淀剂和颗粒稳定剂,搅拌混合,获得第一中间体系;第一中间体系为含有钴离子螯合沉淀颗粒的溶液;
32.步骤3、向第一中间体系中加入表面活性剂,并搅拌混合均匀,获得第二中间体系;第二中间体系为含有钴沉淀悬浮颗粒的悬浮液;
33.步骤4、采用浮选分离装置对上述第二中间体系进行充气浮选,收集得到含有钴沉淀的颗粒,实现溶液中钴离子的选择性螯合沉淀-浮选去除,实现锌钴高效分离。
34.具体的,上述步骤1中,含锌、钴离子的溶液可以为湿法炼锌浸出液,或含锌钴固体废弃物的酸性浸出液,或含锌钴电子垃圾浸出液,或含锌钴的工业废水。其中,锌离子的浓度为0.5~185g/l,示例性地,如1g/l、10g/l、30g/l、40g/l、50g/l、70g/l、90g/l、100g/l、110g/l、130g/l、140g/l、150g/l、170g/l、180g/l;钴离子的浓度为1mg/l~5g/l,示例性地,如1mg/l、10mg/l、100mg/l、200mg/l、300mg/l、400mg/l、500mg/l、600mg/l、700mg/l、800mg/l、900mg/l、1g/l、2g/l、3g/l、4g/l、5g/l。
35.具体的,上述步骤1中,考虑到溶液ph过高会造成后续步骤中锌离子水解沉淀,从而影响锌钴离子的分离效率;溶液ph过低,将影响后续步骤中沉淀剂与钴离子的络合沉淀效率。因此,控制步骤1中调整后的溶液的ph为4.5~6.0。
36.需要说明的是,上述步骤1中,ph调整剂为无机酸或碱,例如硫酸、盐酸或氢氧化钠等。
37.具体的,上述步骤2中,温度过高将使沉淀剂分解,造成沉淀剂的不必要损耗;温度过低,则加重处理过程中温度控制的难度;因此,控制温度为20~50℃,示例性地,如20℃、25℃、30℃、35℃、40℃、45℃、50℃。
38.具体的,上述步骤2中,钴离子螯合沉淀剂为乙基黄原酸钠和乙基黄原酸钾中的一种或二者混合物。
39.考虑到钴离子螯合沉淀剂的加入量过低,则会造成溶液中钴离子的去除率偏低;沉淀剂加入量过高,则会造成试剂的浪费以及对溶液造成污染。因此,上述步骤2中,控制钴离子螯合沉淀剂的加入量与溶液中钴离子的摩尔比为4:1~10:1,示例性地,如4:1、5:1、6:1、7:1、8:1、9:1、10:1。
40.具体的,上述步骤2中,颗粒稳定剂包括无水硫酸铜和/或含水硫酸铜。
41.具体的,上述步骤2中,硫酸铜稳定钴离子螯合沉淀产物的原理是:硫酸铜在除钴过程中可以作为一种氧化剂,将溶液中co
2+
氧化成co
3+
,在co
3+
与钴离子螯合沉淀剂结合形成絮状沉淀的同时,cu
+
也与钴离子螯合沉淀剂结合形成絮状沉淀,促使含钴絮状沉淀物颗粒增大并稳定存在。以乙基黄原酸钠为例:
42.8c2h5ocs2na+2cuso4+2coso4=cu2(c2h5ocs2)
↓
+2co(c2h5ocs2)3↓
+4na2so443.考虑到颗粒稳定剂的加入量过低,则会造成溶液中钴离子的去除率偏低;颗粒稳定剂的加入量过高,则会造成试剂的浪费以及对溶液造成铜离子污染。因此,控制颗粒稳定
剂的加入量与溶液中钴离子的摩尔比为1:1~3:1,示例性地,如1:1、1.5:1、2:1、2.5:1、3:1。
44.具体的,上述步骤2中,搅拌速度过快会造成颗粒难以聚集长大,对后续浮选造成不利影响;搅拌时间过短会造成螯合沉淀不充分;时间过长则影响处理效率。因此,控制搅拌速率小于或等于100rpm,搅拌时间为10~60min,示例性地,如10min、15min、20min、25min、30min、35min、40min、45min、50min、55min、60min。
45.具体的,上述步骤3中,表面活性剂为十六烷基三甲基溴化铵(ctab)、十二烷基硫酸钠(sds)和甲基异丁基甲醇(mibc)中的一种或多种。
46.具体的,上述步骤3中,表面活性剂用于进一步调控颗粒尺寸及稳定性。考虑到表面活性剂的加入量过多,会造成溶液中表面活性剂的残留;加入量过少,则起不到调控颗粒尺寸的作用。因此,控制表面活性剂的添加量为10~100mg/l,示例性地,如10mg/l、15mg/l、20mg/l、25mg/l、30mg/l、40mg/l、45mg/l、50mg/l、55mg/l、60mg/l、65mg/l、70mg/l、75mg/l、80mg/l、85mg/l、90mg/l、95mg/l、100mg/l。
47.具体的,上述步骤3中,搅拌混合的时间为5~60min,示例性地,如5min、10min、15min、20min、25min、30min、35min、40min、45min、50min、55min、60min。
48.具体的,上述步骤3中,影响悬浮颗粒的颗粒大小的因素主要包括颗粒稳定剂的加入量、搅拌混合时间、搅拌速度、离子浓度等;考虑到悬浮颗粒的颗粒尺寸过小,则浮选过程中难以被气泡黏附后浮选分离;颗粒尺寸过大,质量大、动量高难以被气泡带出。因此,严格控制上述参数,保证悬浮颗粒的颗粒直径为20~50μm。
49.需要说明的是,发明人经过深入研究发现,由于溶液中钴离子浓度很低,形成的颗粒较小,如果采用沉淀过滤的方法则容易堵塞滤布,如果采用沉淀过滤的方法则需要形成大颗粒沉淀,生产时间长、并且需要更多的过量反应试剂来增大颗粒;生产效率低,反应试剂用量大,经济性差;因此,上述步骤4中,采用浮选分离装置对上述第二中间体系进行充气浮选。
50.具体的,上述步骤4中,浮选分离装置包括浮选机或浮选柱。
51.具体的,上述步骤4中,充气浮选的步骤包括:将第二中间体系通入浮选分离装置中,充气浮选;含有钴沉淀的颗粒随气泡上浮并富集在上部泡沫层中,随泡沫排出而被收集。
52.或者,上述步骤1-4中,将含锌、钴离子的溶液通入浮选分离装置中,然后将含锌、钴离子的溶液的ph调整至酸性;然后继续进行步骤2-4。
53.与现有技术相比,现有的溶液中锌钴分离普遍采用沉淀法,然而由于有些情况下,钴离子浓度较低,难以形成较大沉淀颗粒,必须加大沉淀剂用量以保证形成的沉淀颗粒满足过滤分离对颗粒尺寸的要求。生产时间长、并且需要更多的过量反应试剂来增大颗粒;生产效率低,反应试剂用量大,经济性差。本发明的技术方案中利用钴离子螯合沉淀剂与溶液中的钴离子选择性螯合,通过同时加入的颗粒稳定剂,使钴离子与钴离子螯合沉淀剂形成悬浮沉淀颗粒,进而采用微泡浮选技术实现溶液中钴离子螯合沉淀小颗粒的浮选分离,最终实现溶液中低浓度钴离子的选择性提取,从而达到高效分离溶液中锌、钴离子的目的;本发明的方法反应试剂用量少,反应时间短,生产效率高,经济效益显著,且锌钴分离效果良好。
54.实施例1
55.本实施例提供了一种溶液中锌、钴离子的分离方法,包括如下步骤:
56.向含有0.5g/l锌离子和1mg/l钴离子的溶液中加入ph调整剂,调节溶液的ph值为4.5;控制溶液温度为20℃,向溶液中加入钴离子螯合沉淀剂(100%乙基黄原酸钠),其加入量与溶液中钴离子的摩尔比为4:1,同时加入颗粒稳定剂(无水硫酸铜),其加入量与溶液中钴离子的摩尔比为1:1;在搅拌速度为50rpm条件下,搅拌10min,获得含有钴离子螯合沉淀颗粒的溶液(第一中间体系);然后向第一中间体系中加入10mg/l的十六烷基三甲基溴化铵(ctab)作为表面活性剂,进一步搅拌均匀得到钴沉淀的悬浮液(第二中间体系),搅拌时间为5min;鼓入气泡进行浮选,浮选的泡沫产品经干燥后获得富钴物质。经螯合沉淀-浮选过程,可将溶液中95.7%的钴离子浮选回收,锌离子浮选回收率为1.1%,获得的富钴物质中锌离子含量为3.5%,锌钴分离效果良好。
57.实施例2
58.本实施例提供了一种溶液中锌、钴离子的分离方法,包括如下步骤:
59.向含有75g/l锌离子和1g/l钴离子的溶液中加入ph调整剂,调节溶液的ph值为5.5;控制溶液温度为40℃,向溶液中加入钴离子螯合沉淀剂(100%乙基黄原酸钾),其加入量与溶液中钴离子的摩尔比为7:1,同时加入颗粒稳定剂(无水硫酸铜),其加入量与溶液中钴离子的摩尔比为2:1;在搅拌速度为75rpm条件下,搅拌30min,获得含有钴离子螯合沉淀颗粒的溶液(第一中间体系);然后向混合溶液中加入50mg/l的十六烷基三甲基溴化铵(ctab)作为表面活性剂,进一步搅拌均匀得到钴沉淀的悬浮液(第二中间体),搅拌时间为30min;鼓入气泡进行浮选,浮选的泡沫产品经干燥后获得富钴物质。经螯合沉淀-浮选过程,可将溶液中97.8%的钴离子浮选回收,锌离子浮选回收率为1.5%,获得的富钴物质中锌离子含量为4.7%,锌钴分离效果良好。
60.实施例3
61.本实施例提供了一种溶液中锌、钴离子的分离方法,包括如下步骤:
62.向含有185g/l锌离子和5g/l钴离子的溶液中加入ph调整剂,调节溶液的ph值为6.0;控制溶液温度为50℃,向溶液中加入钴离子螯合沉淀剂(50%乙基黄原酸钠,50%乙基黄原酸钾),其加入量与溶液中钴离子的摩尔比为10:1,同时加入颗粒稳定剂(五水硫酸铜),其加入量与溶液中钴离子的摩尔比为3:1;在搅拌速度为100rpm条件下,搅拌60min,获得含有钴离子螯合沉淀颗粒的溶液(第一中间体系);然后向混合溶液中加入100mg/l的十六烷基三甲基溴化铵(ctab)作为表面活性剂,进一步搅拌均匀得到钴沉淀的悬浮液(第二中间体),搅拌时间为60min;鼓入气泡进行浮选,浮选的泡沫产品经干燥后获得富钴物质。经螯合沉淀-浮选过程,可将溶液中94.2%的钴离子浮选回收,锌离子浮选回收率为1.4%,获得的富钴物质中锌离子含量为4.8%,锌钴分离效果良好。
63.对比例1
64.本对比例提供了一种溶液中锌、钴离子的分离方法,采用黄药直接沉淀法,处理与实施例1相同的含有锌、钴离子的溶液。采用的化学试剂的加入量与溶液中钴离子的摩尔比为13:1;沉淀处理的时间为3-5h;可将溶液中87.5%的钴离子沉淀回收,锌离子沉淀率为8.5%,获得的富钴物质中锌离子含量为10.8%。该对比例的反应时间长,效率低,且钴回收率低,锌钴分离效果较差。
65.本发明的技术方案中利用钴离子螯合沉淀剂与溶液中的钴离子选择性螯合,通过同时加入的颗粒稳定剂,使钴离子与钴离子螯合沉淀剂形成悬浮沉淀颗粒,进而采用浮选技术实现溶液中钴离子螯合沉淀小颗粒的浮选分离,最终实现溶液中低浓度钴离子的选择性提取,从而达到高效分离溶液中锌、钴离子的目的。本发明的方法反应试剂用量少,反应时间短,生产效率高,经济效益显著,且锌钴分离效果良好。
66.以上所述,仅为本发明较佳的具体实施方式,但本发明的保护范围并不局限于此,任何熟悉本技术领域的技术人员在本发明揭露的技术范围内,可轻易想到的变化或替换,都应涵盖在本发明的保护范围之内。