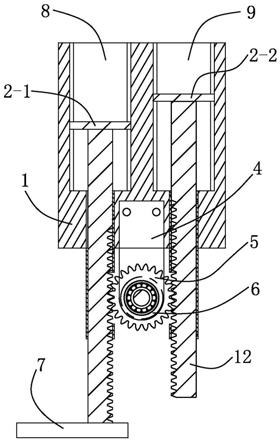
一种用于缩小大尺寸3d打印装备成型体积的装置
技术领域
1.本发明涉及3d打印装备。属于装备制造技术领域。特别涉及一种用于缩小大尺寸3d打印装备成型体积的装置。
背景技术:2.现有大型3d打印装备的尺寸相对来说是比较大的,需要比较大体积的成形区域,这势必也会要求成形缸和粉料缸的尺寸同步,耗费了大量的粉末。3d装备本身就比较昂贵,打印的材料如钛合金这类金属也非常昂贵,装满粉料缸的钛合金粉料也需要几万元,所以成本是非常巨大的,这样经济效益就会被急剧拉低。
技术实现要素:3.本发明是为克服现有技术不足,提供一种用于缩小大尺寸3d打印装备成型体积的装置。可满足在原有3d打印装备的基础上减小成型体积,减少一次打印需要的粉料。
4.一种用于缩小大尺寸3d打印装备成型体积的装置,包含成形缸、粉料缸、外框和传动系统;成形缸和粉料缸被外框分割包裹,所述传动系统包含直齿轮、驱动板、两个柱套和两个齿柱;成形缸和粉料缸的底部分别连接有一个柱套,两个柱套上相邻两侧面上分别开有一豁口,两个柱套内分别可滑动地设置有齿柱,齿柱的齿外漏于豁口处,直齿轮可转动地设置在外框底部的两个柱套之间,且直齿轮的齿伸入两个豁口并同时与两个齿柱的齿啮合,成形缸内设置有与其内壁相滑动配合的成形缸台板,粉料缸内设置有与其内部相滑动配合的粉料缸台板,两个齿柱的上端分别与成形缸台板和粉料缸台板连接,成形缸内的齿柱的下端与驱动板连接。
5.本发明相比现有技术的有益效果是:
6.本发明传动系统采用齿轮齿柱传动,实现台板的升降效果,进而实现了送粉和铺粉。相比于改进前的结构,减小了成型体积,减少了粉料的使用,有效的减少了生产制造成本。在需要打印较小尺寸的零件时只需要较小的成型区域,可满足在原有3d打印装备的基础上减小成型体积(reduced building volume,简称rbv),减少一次打印需要的粉料,具有在现有3d打印装备基础上做到较小的成型缸和粉料缸可降低成本的优点。
7.下面结合附图和实施例对本发明的技术方案作进一步地说明:
附图说明
8.图1为本发明用于缩小大尺寸3d打印装备成型体积的装置的主剖视图;
9.图2为本发明用于缩小大尺寸3d打印装备成型体积的装置的主视图;
10.图3为图2的侧视图;
11.图4为去掉外框后的本发明结构示意图;
12.图5为本发明安装于现有的3d打印装备的成形缸内的示意图;
13.图6为图5的主剖视图;
14.图7为本发明安装于现有3d打印装备的成型缸中,粉料缸台板处于最低位置,成型缸台板处于最高位置的状态图;
15.图8为本发明安装于现有3d打印装备的成型缸中,粉料缸台板处于最高位置,成型缸台板处于最低位置的状态图。
具体实施方式
16.如图1
‑
图4所示,本实施方式的一种用于缩小大尺寸3d打印装备成型体积的装置,包含成形缸8、粉料缸9、外框1和传动系统;成形缸8和粉料缸9被外框1分割包裹;
17.所述传动系统包含直齿轮5、驱动板7、两个柱套11和两个齿柱12;成形缸8和粉料缸9的底部分别连接有一个柱套11,两个柱套11上相邻两侧面上分别开有一豁口,两个柱套11内分别可滑动地设置有齿柱12,齿柱12的齿外漏于豁口处,直齿轮5可转动地设置在外框1底部的两个柱套11之间,且直齿轮5的齿伸入两个豁口并同时与两个齿柱12的齿啮合,成形缸8内设置有与其内壁相滑动配合的成形缸台板2
‑
1,粉料缸9内设置有与其内部相滑动配合的粉料缸台板2
‑
2,两个齿柱12的上端分别与成形缸台板2
‑
1和粉料缸台板2
‑
2连接,成形缸8内的齿柱12的下端与驱动板7连接。
18.上述实施方式的用于缩小大尺寸3d打印装备成型体积的装置是安装于大型3d打印装备的成形缸中,打印装备的粉料缸就暂时空置。
19.如图5和图6所示,使用时,所述成形缸8、粉料缸9、外框1和传动系统置于现有的3d打印装备成形缸a内,外框1与现有的3d打印装备成形缸a连接,驱动板7用于连接现有的3d打印装备成形缸升降板14。驱动板7通过塑料螺栓与原成型缸升降板14相连接.从而在原3d打印装置成型缸升降板14下降时通过驱动板7带动减小成型体积的成型缸8的齿柱12下移,为减小成型体积机械装置提供动力。采用塑料螺栓是因为预防紧急事故,可快速将驱动板7与原3d打印装备升降板14脱开。
20.进一步地,如图5所示,外框1的顶部还设有用于连接外框1和现有的3d打印装备成形缸a的外框托板13。
21.如图4所示,优选地,所述柱套11和齿柱12均为圆柱形。直齿轮5为直齿圆柱齿轮。
22.进一步地,如图3和图4所示,直齿轮5利用直齿轮固定系统实现传动;所述直齿轮固定系统包含芯轴10、两个固定板4和两个球轴承6;两个齿套11之间布置有两个固定板4,两个固定板4固接在外框1上,每个固定板4上安装有球轴承6,齿直轮5固装在芯轴10的中部,芯轴10两端与两个球轴承6配合。两个球轴承6起到固定芯轴10的作用,优先选用s7204 gb 292
‑
94的球轴承。驱动板7用于连接现有的3d打印装备成形缸升降板14,打印过程中3d打印装备成形缸升降板14每下移时就会通过驱动板7带动减小成型体积装置的成形缸台板2
‑
1及齿柱12运动,从而给整个减小成型体积的本装置提供动力。
23.如图7和图8所示,当每一次激光扫描工作完成后成形缸升降板14下降,带动与之相连接的驱动板7上的减小成型体积的成形缸8的齿柱12下降,实现减小体积的成形缸台板2
‑
1下降,给铺粉刷推过来的粉料让出空间。齿柱12又可带动直齿圆柱齿轮转动,从而粉料缸上齿柱12上升并带动粉料台板2
‑
2升高,将金属粉料推出后铺粉刷将粉料推到成形缸8去。成形缸8作为成型区域,可以每激光扫描一次后向下位移一段距离,给新来的粉料腾出空间,粉料缸9是存放打印原料的地方,粉料缸9在每次激光扫描后上升一段位移,将粉料推
到粉料缸台板2
‑
2上,铺粉刷将粉料推到成型区域,以此循环。优选地,如图1
‑
6所示,所述成形缸8和粉料缸9均为矩形缸。
24.工作过程:本实施结构是安装于大型3d打印装备成形缸中,打印装备的粉料缸就暂时空置。3d打印工作正常进行,只需要在设计打印程序时缩小构建的尺寸,确保激光选区融化在减小成型体积装置的成形缸8中完成。首先将三维cad模型进行切片离散及扫描路径规划,得到可控制激光束扫描的切片轮廓信息;其次,计算机逐层调入切片轮廓信息,通过激光束选择性的逐线搭接扫描粉层上选定区域,形成面轮廓,未被激光照射区域粉末依旧呈松散状。一层加工完成后,原3d打印装备成形缸升降板14向下运动造成与其用驱动板7连接的成形缸内齿柱12向下运动,同时与粉料缸内齿柱12啮合的直齿轮5带动该齿柱12上升微米,从而实现了成形缸台板2
‑
1下降,降低切片层厚的高度,粉料缸台板2
‑
2上升。铺粉刷将粉末从粉料缸刮到成形缸台板2
‑
1上,激光束将新铺上的粉末融化,与上一层融为一体。重复上述过程,直至成型过程完成,得到与三维实体模型相同的三维金属零件。
25.本发明已以较佳实施案例揭示如上,然而并非用以限定本发明,任何熟悉本专业的技术人员,在不脱离本发明技术方案范围内,当可以利用上述揭示的结构及技术内容做出些许的更动或修饰为等同变化的等效实施案例,均仍属本发明技术方案范围。