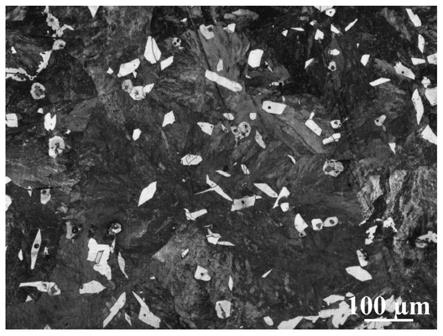
1.本发明涉及钢铁冶金领域,特别是涉及一种非调质钢及其冶炼方法。
背景技术:2.非调质钢标准gb/t 15712
‑
2008对非调质钢的定义为:通过微合金化、控制轧制和控制冷却等强韧化方法,取消了调质热处理,达到调质钢力学性能的一类优质结构钢。非调质钢在生产过程中无需对产品进行热处理、矫直,简化了工艺操作,提高了产品成材率,降低能耗的同时减少了对环境的污染,故有“绿色钢材”之称。
3.国内对于非调质钢的研究和开发相比于国外先进国家起步较晚。目前,共开发出非调质钢20余种,生产的主要是棒材产品,规格主要集中在φ10mm~φ115mm范围内。主要用于汽车发动机连杆、曲轴等零部件中,还成功应用到了n80石油套管、无缝钢管等制品,应用范围涉及汽车。虽然微合金非调质钢的研究和发展已经达到了一定的水平,但对于生产高品质非调质,在钢晶粒度控制、夹杂物控制等方面仍与国外先进水平有较大差距,难以满足高端用户的要求。
技术实现要素:4.发明目的:本发明的目的之一是提供一种细晶粒曲轴用非调质钢,其具有细晶粒和高品质的优点;本发明的目的之二是提供一种细晶粒曲轴用非调质钢的冶炼方法。
5.技术方案:本发明的细晶粒曲轴用非调质钢,包括按重量百分比计的如下成分:c:0.65~0.75%,si:0.15~0.25%,mn:0.5~2.5%,p:≤0.02%,s:0.06~0.07%,al:≤0.01%,v:0.03~0.04%,[n]≤0.01%,mg:0.001~0.003%,余量为fe和不可避免的杂质。
[0006]
为开发高品质细晶粒非调质钢,本发明采用加入的mg元素形成mgo
·
al2o3,促进铁素体的形核,同时钉扎晶界,细化晶粒。mgo
·
al2o3夹杂物在高温钢液中尺寸细小、成分稳定、分布弥散,为铁素体转变提供了异质形核点。这是因为mgo
·
al2o3中存在mg空位,可以吸收mn元素,使得其周围出现贫mn,促进了针状铁素体的形核,提高,起到细化晶粒的作用。
[0007]
优选地,上述重量百分比计的成分中,mg含量为0.001~0.003%;以进一步细化晶粒度和提高钢种品质。
[0008]
优选地,所述非调质钢的金相组织为珠光体和晶内铁素体。
[0009]
本发明还提供了上述细晶粒曲轴用非调质钢的冶炼方法,冶炼工序为:转炉(电炉)
→
lf
→
vd(rh)
→
cc,在vd工序,其他成分调整结束后,加入一定含量mg元素,利用mg元素对mns夹杂物改质,形成细小弥散分布的硫化锰与镁铝氧化物复合夹杂物,作为铁素体形核核心,诱导形成等轴铁素体,细化晶粒。本发明所述细晶粒非调质钢性能优良,且成本低,易于实现工业生产,提升国内非调质钢晶粒度控制水平。
[0010]
具体的,其包括以下步骤:
[0011]
(1)转炉或电炉冶炼,控制转炉终点:c≥0.06%、p≤0.015%,控制出钢温度为1625+20℃,出钢1/4开始依次往钢包中加入合金及渣料;
[0012]
(2)lf炉全程吹氮,lf精炼过程用碳化硅进行渣面脱氧,依次调整元素成分;进vd前控制al<0.015wt%,其他元素除n、s外努力按要求控制;
[0013]
(3)rh或vd,控制真空度小于2mba,其中高真空(即前述真空度小于2mba)处理时间≥12min,rh或vd全程使用氮气作为提升气;在rh或vd处理结束后按目标喂加mnn线,然后喂入硅钙线,软吹后根据钢水硫含量使用硫铁线调整硫;s含量调整结束后,利用喂丝机喂入si
‑
mg包芯线,喂入镁元素后静搅,使钢液的镁含量为0.001%~0.005%;
[0014]
在vd或rh工序,其他成分调整结束后,向钢液中喂入硅镁包芯线,使钢液的镁含量为0.001%~0.003%。
[0015]
(4)喂入镁元素后静搅时间为10~15分钟;
[0016]
(5)连铸浇注,对铸坯进行缓冷,得到钢坯;
[0017]
(6)轧钢,轧制过程采用高温扩散加热工艺,并执行控轧控冷工艺。
[0018]
作为优选地,在vd或rh工序,喂入si
‑
mg包芯线前,需控制钢种氧含量[o]为5
‑
15ppm,以保证镁元素发挥作用。在vd或rh工序,要求控制mg元素含量为0.001~0.003%。
[0019]
本发明的关键技术环节是材料的配比设计及工艺条件的控制,两者相辅相成。通过元素调配,结合冶炼控制工艺,协同作用下得到了高品质曲轴用非调质钢,其具有细晶粒、夹杂物含量少且均匀分布,疲劳性能好
[0020]
有益效果:
[0021]
本发明选用非调质钢,创新性地添加mg元素来细化非调质钢晶粒度,能够以较低的成本进一步提升钢晶粒度,得到细晶粒高品质非调质钢,钢种的晶粒度细小,夹杂物少且形貌好,无聚集现象,金相组织符合高品质钢的苛刻要求,全面提升综合性能。
[0022]
本发明采取在vd或rh工序喂线方式加入mg元素,工艺简单,易于实现工业生产,进一步提升国内非调质钢控制水平。
附图说明
[0023]
图1是对比例1的金相图片;
[0024]
图2是实施例1的金相图片;
[0025]
图3是实施例2的金相图片;
[0026]
图4是实施例3的金相图片;
[0027]
图5是实施例4的金相图片;
[0028]
图6是样品晶粒度及铁素体含量变化曲线;
[0029]
图7是对比例1的典型夹杂物形貌图;
[0030]
图8是典型镁与mns复合夹杂物的图片和成分测试;(a)为形貌图片,(b)为成分测试结果;
[0031]
图9是实施例1的典型夹杂物形貌图;
[0032]
图10是实施例2的典型夹杂物形貌图;
[0033]
图11是实施例3的典型夹杂物形貌图;
[0034]
图12是实施例4的典型夹杂物形貌图。
具体实施方式
[0035]
下面结合实施例对本发明进一步地详细描述。
[0036]
实施例1:
[0037]
本实施例的非调质钢冶炼采用100吨电炉,冶炼过程具体为:
[0038]
(1)控制电炉终点:c:0.10%、p:0.0053%,出钢温度1639℃;出钢1分钟30秒开始依次往钢包中加入硅锰类合金692kg,硅铁103kg,石灰550kg,精炼渣252kg。
[0039]
(2)lf炉全程吹氮,流量为75.0l/min;lf精炼过程用碳化硅130kg进行渣面脱氧,调整元素含量成分,出lf时取样检测,钢水中碳元素含量为0.705%,硅元素含量为0.156%,锰含量为0.565%,铝含量为0.004%,硫含量0.0586%。
[0040]
(3)vd工序,真空度1.1mbar,高真空处理时间12min,rh或vd全程使用氮气作为提升气,真空保持时气体流量82.9l/min。
[0041]
(4)在rh或vd处理结束软吹后喂入硫铁线30米,调整硫含量为0.066%;
[0042]
(5)s含量调整结束后,利用喂丝机喂入100米si
‑
mg包芯线,喂线速度180m/min。
[0043]
(5)喂入镁元素后静搅时间为10分钟取样检测,上连铸。
[0044]
冶炼终点成分含量为:c:0.70%,si:0.157%,mn:0.574%,p:0.0117%,s:0.065%,al:0.0038%,v:0.0389%,mg:0.0011%,余量为fe,以及不可避免的杂质。
[0045]
(6)连铸采用传统工艺浇注。
[0046]
连铸采用320*420mm断面浇注,提高材料压缩比,减少材料的低倍缺陷,其中结晶器电磁搅拌电流450a*5,轻压下采用12mm大压下量的模式来降低铸坯的低倍缺陷级别。
[0047]
实施例2:
[0048]
本实施例的非调质钢冶炼采用100吨电炉,冶炼过程具体为:
[0049]
(1)控制电炉终点:c:0.083%、p:0.0049%,出钢温度1642℃;出钢1分钟30秒开始依次往钢包中加入硅锰类合金694kg,硅铁87kg,石灰550kg,精炼渣254kg。
[0050]
(2)lf炉全程吹氮,流量为75.0l/min;lf精炼过程用碳化硅70kg进行渣面脱氧,调整元素含量成分,出lf时取样检测,钢水中c:0.689%,si:0.178%,mn:0.567%,alt:0.005%,s:0.0494%。
[0051]
(3)vd工序,真空度1.1mbar,高真空处理时间12min,rh或vd全程使用氮气作为提升气,真空保持时气体流量71.2l/min。
[0052]
(4)在rh或vd处理结束软吹后喂入硫铁线100米,调整硫含量为0.0622%;s含量调整结束后,利用喂丝机喂入150米si
‑
mg包芯线,喂线速度180m/min。
[0053]
(5)喂入镁元素后静搅时间为10分钟。
[0054]
冶炼终点成分含量为:c:0.7059%,si:0.165%,mn:0.571%,p:0.0108%,s:0.0623%,al:0.0035%,v:0.0378%,mg:0.0015%,余量为fe,以及不可避免的杂质。
[0055]
(6)连铸采用传统工艺浇注。
[0056]
连铸采用320*420mm断面浇注,提高材料压缩比,减少材料的低倍缺陷,其中结晶器电磁搅拌电流450a*5,轻压下采用12mm大压下量的模式来降低铸坯的低倍缺陷级别。
[0057]
实施例3:
[0058]
本实施例的非调质钢冶炼采用100吨电炉,冶炼过程具体为:
[0059]
(1)控制电炉终点:c:0.071%、p:0.0056%,出钢温度1635℃;出钢1分钟30秒开始
依次往钢包中加入硅锰类合金693kg,硅铁91kg,石灰550kg,精炼渣252kg。
[0060]
(2)lf炉全程吹氮,流量为75.0l/min;lf精炼过程用碳化硅120kg进行渣面脱氧,调整元素含量成分,出lf时取样检测,钢水中c:0.685%,si:0.182%,mn:0.546%,al:0.0092%,s:0.0611%。
[0061]
(3)vd工序,真空度1.3mbar,高真空处理时间12min,rh或vd全程使用氮气作为提升气,真空保持时气体流量71.2l/min。
[0062]
(4)在rh或vd处理结束软吹后喂入硫铁线120米,调整硫含量为0.069%;s含量调整结束后,利用喂丝机喂入200米si
‑
mg包芯线,喂线速度180m/min。
[0063]
(5)喂入镁元素后静搅时间为10分钟。
[0064]
冶炼终点成分含量为:c:0.7206%,si:0.171%,mn:0.555%,p:0.0075%,s:0.069%,al:0.0036%,v:0.0399%,mg:0.0021%,余量为fe,以及不可避免的杂质。
[0065]
(6)连铸采用传统工艺浇注。
[0066]
实施例4:
[0067]
本实施例的非调质钢冶炼采用100吨电炉,冶炼过程具体为:
[0068]
(1)控制电炉终点:c:0.069%、p:0.0044%,出钢温度1644℃;出钢1分钟30秒开始依次往钢包中加入硅锰类合金696kg,硅铁91kg,石灰550kg,精炼渣250kg。
[0069]
(2)lf炉全程吹氮,流量为75.0l/min;lf精炼过程用碳化硅90kg进行渣面脱氧,调整元素含量成分,出lf时取样检测,钢水中c:0.704%,si:0.229%,mn:0.551%,al:0.0045%,s:0.0084%。
[0070]
(3)vd工序,真空度0.89mbar,高真空处理时间15min,rh或vd全程使用氮气作为提升气,真空保持时气体流量76.1l/min。
[0071]
(4)在rh或vd处理结束软吹后喂入硫铁线150米,调整硫含量为0.0657%;s含量调整结束后,利用喂丝机喂入300米si
‑
mg包芯线,喂线速度180m/min。
[0072]
(5)喂入镁元素后静搅时间为10分钟。
[0073]
冶炼终点成分含量为:c:0.70%,si:0.19%,mn:0.52%,p:0.0046%,s:0.062%,al:0.0023%,v:0.0355%,mg:0.0036%,余量为fe,以及不可避免的杂质。
[0074]
(6)连铸采用传统工艺浇注。
[0075]
对比例1:
[0076]
本实施例的非调质钢冶炼采用100吨电炉,冶炼过程具体为:
[0077]
(1)控制电炉终点:c:0.096%、p:0.0044%,出钢温度1640℃;出钢1分钟30秒开始依次往钢包中加入硅锰类合金613kg,硅铁91kg,石灰550kg,精炼渣249kg。
[0078]
(2)lf炉全程吹氮,流量为75.2l/min;lf精炼过程用碳化硅120kg进行渣面脱氧,调整元素含量成分,出lf时取样检测,钢水中c:0.691%,si:0.151%,mn:0.555%,alt:0.0072%,s:0.0657%。
[0079]
(3)vd工序,真空度0.89mbar,高真空处理时间12min,rh或vd全程使用氮气作为提升气,真空保持时气体流量71.2l/min。
[0080]
(4)在rh或vd处理结束软吹后喂入硫铁线150米,调整硫含量为0.068%;s含量调整结束后,静搅时间为10分钟。
[0081]
(5)冶炼终点成分含量为:c:0.7185%,si:0.203%,mn:0.559%,p:0.0053%,s:
0.069%,al:0.0038%,v:0.0385%,余量为fe,以及不可避免的杂质。
[0082]
(6)连铸采用传统工艺浇注。
[0083]
上述实施例1~5与对比例1得到的非调质钢中的元素含量如下表1所示。
[0084]
表1、本发明实施例及对比例1的化学成分对比(wt%)
[0085]
元素csimnpsalvmg对比例10.71850.2030.5590.00530.0690.00380.0385/实施例10.700.1570.5740.01170.0650.0038%0.03890.0011实施例20.70590.1650.5710.01080.06230.00350.03780.0015实施例30.72060.1710.5550.00750.0690.00360.03990.0021实施例40.700.190.520.00460.0620.00230.03550.0036
[0086]
图1是对比例1的金相图片,图2~5依次是实施例1~4的金相图片,可以看出,对比例1与实施例组织均为珠光体+沿晶析出的网状铁素体+部分晶内析出铁素体,但是晶粒度显著大于实施例1~4。实施例1~4的金相组织为珠光体+沿晶析出的网状铁素体+部分晶内析出铁素体,且随着镁元素含量的增加,珠光体和铁素体的比例增多,晶粒度不断细化。
[0087]
利用image pro plus 6.0软件对样品晶粒度进行测量,得到数据如表2所示,经过测量计算得出实施例不同镁含量,和对比例1样品的平均晶粒度及单位面积铁素体数量,如图6所示。可以看出,添加镁元素后,单位面积铁素体数量明显增加,镁对晶粒度细化明显,表明均匀分散的细小含镁夹杂物有助于针状铁素体的非均匀形核,使钢的显微组织更加细化。
[0088]
当镁元素达到0.0036%后,细化晶粒效果达到饱和,因此,本发明将0.001
‑
0.003%作为优选方案。
[0089]
利用金相显微镜及扫描电子显微镜对钢中mns夹杂物进行观察,如图7所示,对比例1中mns夹杂物为长条状或树枝状,且易于聚集,对钢疲劳性能危害较大;图8是典型镁与mns复合夹杂物的图片和成分测试;(a)为形貌图片,(b)为成分测试结果。如图9
‑
12所示,实施例1
‑
4中夹杂物分布均匀,且尺寸变小,与对比例相比,夹杂物形貌明显改善,夹杂物的数量明显减小,无聚集现象。其中,晶粒尺寸结果如下表2所示。
[0090]
表2、样品晶粒尺寸测定(μm)
[0091] 12345678910平均值对比例175.43298.56205.89203.44118.8199.28101.36137.1751.8484.34147.61实施例172.1344.0865.1942.4985.1570.2570.3159.6560.17100.6767.01实施例252.8375.8461.0958.8132.7351.9142.2335.1153.7545.4550.98实施例339.7226.6441.8543.6438.9622.2924.5822.9946.2825.0133.20实施例447.5253.2431.2927.2337.1734.8517.8650.3636.7120.6835.691
[0092]
对比例2:
[0093]
本对比例与实施例1基本相同,不同之处在于冶炼终点镁元素的成分含量,mg元素含量为0.004%,
[0094]
测试结果发现,控制冶炼工艺,使得mg元素含量超出0.0036wt%时,以0.004wt%为例,试验结果发现晶粒度显著变大,夹杂物聚集现象明显。
[0095]
对比例3:
[0096]
本对比例与实施例1基本相同,不同之处在于在vd或rh工序,喂入si
‑
mg包芯线前需控制钢种活度氧为18~20ppm。
[0097]
测试结果发现,在vd或rh工序,喂入si
‑
mg包芯线前需控制钢种活度氧略超出5
‑
15ppm范围时,夹杂物数量明显增多,呈大块聚集状,力学性能显著降低。