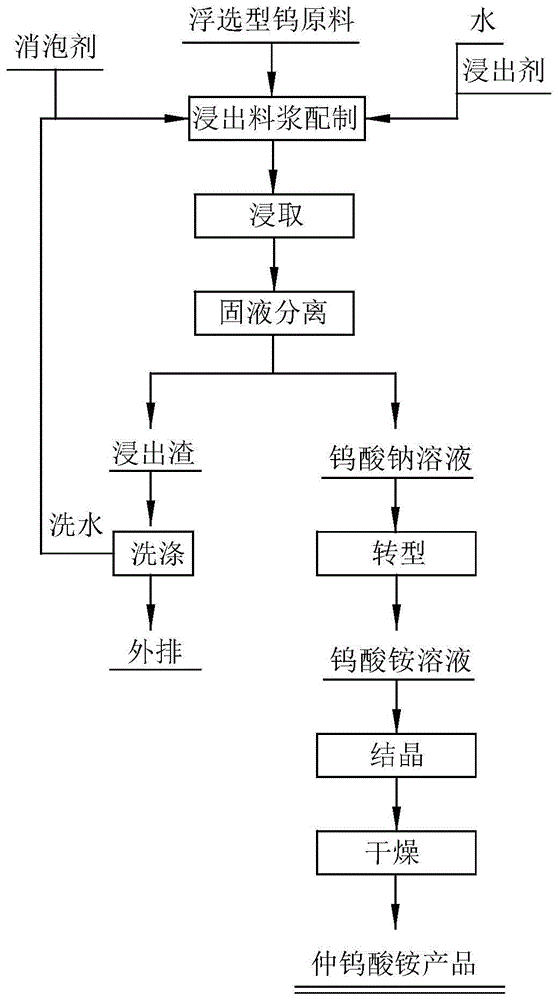
本发明涉及冶金化工
技术领域:
,尤其涉及一种浮选型钨原料的分解工艺。本文中,“浮选型钨原料”是指通过浮选法获得的适合冶炼的浮选型钨原料。浮选法是一种选矿方法,是指据矿物表面物理、化学性质的差异从水的悬浮体(矿浆)中浮出固体矿物的选矿过程。浮选型钨原料包括白钨矿、钨细泥等。术语“c4~c16”是指碳链碳原子为4至16个的有机物,其他类同。术语“高沸点”是指沸程180~350℃。术语“叔胺分子式:r1r2r3n”中的r1、r2、r3的碳链碳原子数、支链数、支链形式可相同,也可不相同。
背景技术:
:钨是一种难熔的有色金属,因其具有熔点高、硬度大、延性强、耐磨和耐腐蚀等特点而得到广泛应用。我国钨资源总量中2/3为白钨矿,随着黑钨资源的不断消耗,白钨矿等浮选型钨原料已成为钨工业的主要原料。浮选型钨原料中含有表面活性剂,采用浮选型钨原料配制浸出料浆时,料浆表面形成泡沫,大量钨原料粘在泡沫上而未与浸出剂接触并发生反应,导致浸出渣中钨含量高,造成钨损失。现有技术中,为去除浮选型钨原料中的表面活性剂,均采用氧化焙烧的方法对浮选型钨原料进行处理,即在氧化性气氛下将浮选型钨原料升温至600~700℃氧化一定时间,从而将浮选型钨原料中的表面活性剂氧化去除,以保证钨酸钠溶液中不含表面活性剂。现有技术的缺点在于焙烧过程温度高导致能耗高,劳动强度大和作业环境差,产生大量难以治理的焙烧烟气从而造成巨大的环境风险,尤其是焙烧过程多批次浮选型钨原料随机混合(钨由于产量小价格高,浮选型钨原料通常十吨成一批次,批次与批次之间钨含量差别较大),造成浸取时浮选型钨原料入冶品位不清楚,从而严重影响后续的配料、浸取等作业过程,为保证浮选型钨原料的浸出率,生产上通常过量配入浸取剂又造成浸取剂浪费,更有甚者焙烧过程导致大量的浮选型钨原料损失,造成极大的资源浪费,经济性差。根据生产经验,即使经过焙烧,仍然有可能因为焙烧不完全,钨原料中仍然有表面活性剂的残留,而且现有技术中浮选型钨原料焙烧过程造成的钨损失率约为2.5%。技术实现要素:因此,本发明的目的在于开发一种浮选型钨原料的分解工艺,其可不需要对浮选型钨原料进行焙烧,便可以获得较好的分解率。本发明提供了一种浮选型钨原料的分解工艺,包括以下步骤:s1、浸出料浆配制:将浮选型钨原料、浸出剂、水和/或洗水、一种或多种消泡剂按一定比例在浸出反应器混合,获得浸出料浆;s2、浸出:将所述浸出料浆置于100~250℃的反应温度下反应一段时间,获得钨酸钠溶液和浸出渣的混合料浆;s3、固液分离:将浸取反应获得的混合料浆进行固液分离,获得钨酸钠溶液和浸出渣。优选地,所述消泡剂包括矿物油类、醇类、羧酸、酯类、酰胺和胺中的一种或多种。优选地,所述矿物油类为c10~c18高沸点烃类;和/或所述醇类为c4~c16醇类;和/或所述羧酸为脂肪酸;和/或所述酯类为蓖麻油;和/或所述酰胺为c4~c16酰胺类;和/或所述胺为叔胺,分子式为r1r2r3n,其中r1、r2、r3为碳原子数为4~12的碳链。优选地,所述消泡剂为c4~c16醇类,c4~c16醇类和c10~c18高沸点烃类的混合物,c4~c16醇类和叔胺的混合物,c4~c16醇类与c10~c18高沸点烃类和叔胺的混合物中的一种。优选地,所述消泡剂与浮选型钨原料的质量比为1:1×109~1:2×102,优选为1:1×108~1:2×102。优选地,本发明的一种浮选型钨原料的分解工艺,还包括以下附加技术特征至少其中之一:所述浮选型钨原料是指通过浮选法获得的原料中三氧化钨质量百分数为5~75%的钨原料;所述浸出剂包括碳酸钠、氢氧化钠、氟化钠、磷酸钠、磷酸一氢钠、磷酸二氢钠中的一种或多种;所述浸出工序在密闭耐压反应容器中进行;所述固液分离方法包括压滤分离、真空抽滤分离和离心分离中的一种或多种。优选地,所述固液分离工序之后还包括浸出渣洗涤工序,所述浸出渣洗涤工序具体包括:采用洗涤剂将固液分离获得的浸出渣进行洗涤,将所述浸出渣中的可溶于水的钨与所述浸出渣分离,并获得洗水,所述洗水前返用于浸出料浆配制。优选地,还包括对步骤s3中获得的钨酸钠溶液中的过量的浸出剂进行回收的工艺。优选地,步骤s1中浸出料浆配制时,还添加有杂质浸出抑制剂和/或浸出助剂,其中:所述杂质浸出抑制剂为氧化镁、硫酸铝钾、氧化铝、硫酸铝的一种或多种;所述浸出助剂包括硝酸钠。优选地,本发明的一种浮选型钨原料的分解工艺,还包括焙烧工序和/或磨矿工序,其中:所述焙烧工序具体包括:将浮选型钨原料在400~800℃的条件下,焙烧0.1~5小时,优选为在500~700℃的条件下,焙烧0.5~2小时;所述磨矿工序具体包括:采用机械破碎的方法将浮选型钨原料磨矿破碎至矿物粒度≤45μm部分质量百分比≥95%;所述磨矿工序设置在步骤s1浸出料浆配制工序之前,所述焙烧工序设置在所述磨矿工序之前。优选地,步骤s2浸出还包括向浸出反应器通入富氧气体,至浸出反应器中的压力>0.1mpa,其中,富氧气体为氧气体积百分比含量>20.9%的气体。本发明可取得如下有益效果至少其中之一:1、本发明通过在浸取工序中添加消泡剂,能够有效抑制浮选型钨原料中的表面活性剂对生产过程的影响,有效缩短料液输送的时间,获得较好的溶液净化效果并获得高品质的仲钨酸铵产品,并可减少生产事故的发生。2、本发明通过在浸取工序中加入富氧气体,能够有效将原料中的表面活性剂在浸出工序予以去除,以克服其对生产过程的影响,生产工艺节能环保,经济效益好,极易实现产业化,并可提高仲钨酸铵品质。3、本发明可处理高杂钨酸钠溶液,改善和优化生产工艺过程,减少了钨原料的损失,生产出低杂质含量、高质量的仲钨酸铵产品,能耗低、劳动强度低、生产成本低,作业环境良好。4、本发明以湿法冶金的方式替代现有技术中采用火法高温焙烧去除钨矿物原料中表面活性剂的方法及系统,从而解决现有技术生产过程中表面活性剂去除时造成的能耗高,劳动强度大和作业环境差,产生大量难以治理的焙烧尾气从而造成巨大的环境风险,以及由焙烧导致的钨矿物原料浸取时入冶品位不清,从而导致的钨矿物原料浸取率低,浸出渣中钨含量高和浸取剂浪费等问题,以及焙烧过程导致大量的钨矿物原料损失,造成资源极大浪费和经济性差等问题。5、采用本发明的工艺,料液运输效率能提高50%以上,消除了表面活性剂带来的不利影响,萃取无三相异物、出水口可以长期不清理,浸出设备备件更加耐用,大大降低了生产成本,提高了产品质量。附图说明图1为本发明优选实施例的一种浮选型钨原料的分解工艺流程图。具体实施方式下面将结合本发明的实施例中的附图,对本发明的实施例中的技术方案进行清楚、完整地描述,显然,所描述的实施例仅仅是本发明一部分实施例,而不是全部的实施例。基于本发明中的实施例,本领域普通技术人员在没有做出创造性劳动前提下所获得的所有其他实施例,都属于本发明保护的范围。如图1所示,本发明的优选实施例,提供了一种浮选型钨原料的分解工艺,包括以下步骤:s1、浸出料浆配制:将浮选型钨原料、浸出剂、水和/或洗水、一种或多种消泡剂按一定比例在浸出反应器混合,获得浸出料浆;s2、浸出:将所述浸出料浆置于100~250℃的温度下浸出一段时间,获得钨酸钠溶液和浸出渣的混合料浆;s3、固液分离:将浸出反应获得的混合料浆进行固液分离,获得钨酸钠溶液和浸出渣。其中,消泡剂包括矿物油类、醇类、羧酸、酯类、酰胺和胺中的一种或多种。其中,矿物油类为c10~c18高沸点烃类;和/或醇类为c4~c16醇类;和/或羧酸为脂肪酸;和/或酯类为蓖麻油;和/或酰胺为c4~c16酰胺类;和/或胺为叔胺,分子式为r1r2r3n,其中r1、r2、r3为碳原子数为4~12的碳链。其中,消泡剂优选为c4~c16醇类,c4~c16醇类和c10~c18高沸点烃类的混合物,c4~c16醇类和叔胺的混合物,c4~c16醇类与c10~c18高沸点烃类和叔胺的混合物中的一种。其中,消泡剂与浮选型钨原料的质量比为1:1×109~1:2×102,优选为1:1×108~1:2×102。其中,浮选型钨原料是指通过浮选法获得的原料中三氧化钨质量百分数为5~75%的钨原料。其中,浸出剂包括碳酸钠、氢氧化钠、氟化钠、磷酸钠、磷酸一氢钠、磷酸二氢钠中的一种或多种。其中,浸出工序在密闭耐压反应容器中进行。其中,固液分离方法包括压滤分离、真空抽滤分离和离心分离中的一种或多种。其中,固液分离工序之后还包括浸出渣洗涤工序,浸出渣洗涤工序具体包括:采用洗涤剂将固液分离获得的浸出渣进行洗涤,将浸出渣中的可溶于水的钨与浸出渣分离,并获得洗水,洗水前返用于浸出料浆配制。其中,还包括对步骤s3中获得的钨酸钠溶液中的过量的浸出剂进行回收的工艺。其中,步骤s1中浸出料浆配制时,还添加有杂质浸出抑制剂和/或浸出助剂,其中:所述杂质浸出抑制剂为氧化镁、硫酸铝钾、氧化铝、硫酸铝的一种或多种;所述浸出助剂包括硝酸钠。其中,本发明的一种浮选型钨原料的分解工艺,还包括焙烧工序和/或磨矿工序,其中:焙烧工序具体包括:将浮选型钨原料在400~800℃的条件下,焙烧0.1~5小时,优选为在500~700℃的条件下,焙烧0.5~2小时;磨矿工序具体包括:采用机械破碎的方法将浮选型钨原料磨矿破碎至矿物粒度≤45μm部分质量百分比≥95%;磨矿工序设置在步骤s1浸出料浆配制工序之前,焙烧工序设置在磨矿工序之前。其中,步骤s2浸出还包括向浸出反应器通入富氧气体,至浸出反应器中的压力>0.1mpa,其中,富氧气体为氧气体积百分比含量>20.9%的气体。其中,步骤s3中获得的钨酸钠溶液采用离子交换法和/或酸性萃取法和/或碱性萃取法生产仲钨酸铵产品。其中,离子交换法生产工艺是指钨酸钠溶液采用离子交换法转型获得钨酸铵溶液,钨酸铵溶液采用蒸发结晶法、冷却结晶法、中和结晶法中的一种,将钨酸铵溶液中的钨从溶液中沉淀出来,获得仲钨酸铵晶体和结晶母液,仲钨酸铵晶体经干燥后获得仲钨酸铵产品。其中,酸性萃取法生产工艺是指钨酸钠溶液经净化去除溶液中的硅、磷、砷、氟、钼等杂质后获得精钨酸钠溶液,精钨酸钠溶液在ph为1~4的条件下,采用叔胺萃取法转型获得钨酸铵溶液,钨酸铵溶液采用蒸发结晶法、冷却结晶法、中和结晶法中的一种,将钨酸铵溶液中的钨从溶液中沉淀出来,获得仲钨酸铵晶体和结晶母液,仲钨酸铵晶体经干燥后获得仲钨酸铵产品。其中,碱性萃取法生产工艺是指在ph>7的条件下采用季铵盐萃取法净化钨酸钠溶液并转型获得钨酸铵溶液,钨酸铵溶液采用蒸发结晶法、冷却结晶法、中和结晶法中的一种,将钨酸铵溶液中的钨从溶液中沉淀出来,获得仲钨酸铵晶体和结晶母液,仲钨酸铵晶体经干燥后获得仲钨酸铵产品。以下是具体实施例:实施例1:一种浮选型钨原料的分解工艺,包括以下步骤:s1、浸出料浆配制:将浮选型钨原料、浸出剂、水、消泡剂混合,获得浸出料浆;其中,浸出剂为碳酸钠,消泡剂为由石油经分馏或裂化而得的c10~c18烷烃产物(消泡剂与浮选型钨原料的质量比为1:1×109);s2、浸出:于100℃下浸出8小时,获得钨酸钠溶液和浸出渣的混合料浆;s3、固液分离:将混合料浆进行压滤分离,获得钨酸钠溶液和浸出渣。实施例2:一种浮选型钨原料的分解工艺,包括以下步骤:s1、浮选型钨原料磨矿破碎工序:采用机械破碎的方法将浮选型钨原料磨矿破碎至矿物粒度≤45微米部分质量百分比≥95%。s2、浸出料浆配制:将浮选型钨原料、浸出剂、水、消泡剂混合,获得浸出料浆;其中,浸出剂为碳酸钠,消泡剂为蓖麻油(消泡剂与浮选型钨原料的质量比为1:1×108)。s3、浸出:于120℃下浸出7小时,获得钨酸钠溶液和浸出渣的混合料浆。s4、固液分离:将混合料浆进行真空抽滤分离,获得钨酸钠溶液和浸出渣。实施例3:一种浮选型钨原料的分解工艺,包括以下步骤:s1、浮选型钨原料磨矿破碎工序:采用机械破碎的方法将浮选型钨原料磨矿破碎至矿物粒度≤45微米部分质量百分比≥95%。s2、浸出料浆配制:将浮选型钨原料、浸出剂、水、消泡剂混合,获得浸出料浆;其中,浸出剂为碳酸钠,消泡剂为油酸(消泡剂与浮选型钨原料的质量比为1:1×107);s3、浸出:于150℃浸出6小时,获得钨酸钠溶液和浸出渣的混合料浆;s4、固液分离:将混合料浆进行离心分离,获得钨酸钠溶液和浸出渣。s5、浸出渣洗涤:采用洗涤剂将固液分离获得的浸出渣进行洗涤,将所述浸出渣中的可溶于水的钨与所述浸出渣分离,并获得洗水,所述洗水前返用于浸出料浆配制。实施例4:一种浮选型钨原料的分解工艺,包括以下步骤:s1、浮选型钨原料磨矿破碎工序:采用机械破碎的方法将浮选型钨原料磨矿破碎至矿物粒度≤45微米部分质量百分比≥95%。s2、浸出料浆配制:将浮选型钨原料、浸出剂、浸出助剂、杂质浸出抑制剂、水、消泡剂混合,获得浸出料浆;其中,浸出剂为碳酸钠、磷酸一氢钠,浸出助剂为硝酸钠,杂质浸出抑制剂为氧化铝,消泡剂为2-苯基丙二酰胺(消泡剂与浮选型钨原料的质量比为1:1×106)。s3、浸出:于160℃浸出5小时,获得钨酸钠溶液和浸出渣的混合料浆。s4、固液分离:将混合料浆进行压滤分离,获得钨酸钠溶液和浸出渣。s5、浸出渣洗涤:采用洗涤剂将固液分离获得的浸出渣进行洗涤,将所述浸出渣中的可溶于水的钨与所述浸出渣分离,并获得洗水,所述洗水前返用于浸出料浆配制。实施例5:一种浮选型钨原料的分解工艺,包括以下步骤:s1、焙烧:将浮选型钨原料在400℃的条件下,焙烧5小时;s2、浮选型钨原料磨矿破碎:采用机械破碎的方法将浮选型钨原料磨矿破碎至矿物粒度≤45微米部分质量百分比≥95%。s3、浸出料浆配制:将浮选型钨原料、浸出剂、浸出助剂、杂质浸出抑制剂、水、消泡剂混合,获得浸出料浆;其中,浸出剂为磷酸一氢钠,浸出助剂为硝酸钠,杂质浸出抑制剂为氧化镁,消泡剂为质量比1:1:1的c10伯醇、仲辛醇、叔胺(n235)(消泡剂与浮选型钨原料的质量比为1:1×105);s4、浸出:于180℃浸出4小时,获得钨酸钠溶液和浸出渣的混合料浆;s5、固液分离:将混合料浆进行真空抽滤分离,获得钨酸钠溶液和浸出渣。s6、浸出渣洗涤:采用洗涤剂将固液分离获得的浸出渣进行洗涤,将所述浸出渣中的可溶于水的钨与所述浸出渣分离,并获得洗水,所述洗水前返用于浸出料浆配制。实施例6:一种浮选型钨原料的分解工艺,包括以下步骤:s1、焙烧:将浮选型钨原料在800℃的条件下,焙烧0.1小时;s2、浮选型钨原料磨矿破碎:采用机械破碎的方法将浮选型钨原料磨矿破碎至矿物粒度≤45微米部分质量百分比≥95%。s3、浸出料浆配制:将浮选型钨原料、浸出剂、浸出助剂、杂质浸出抑制剂、水、消泡剂混合,获得浸出料浆;其中,浸出剂为磷酸二氢钠,浸出助剂为硝酸钠,杂质浸出抑制剂为硫酸铝钾,消泡剂为质量比1:1的由石油经分馏或裂化而得的c10~c18烷烃产物、c10伯醇(消泡剂与浮选型钨原料的质量比为1:1×104);s4、浸出:于200℃浸出3小时,获得钨酸钠溶液和浸出渣的混合料浆;s5、固液分离:将混合料浆进行离心分离,获得钨酸钠溶液和浸出渣。s6、浸出渣洗涤:采用洗涤剂将固液分离获得的浸出渣进行洗涤,将所述浸出渣中的可溶于水的钨与所述浸出渣分离,并获得洗水,所述洗水前返用于浸出料浆配制。实施例7:一种浮选型钨原料的分解工艺,包括以下步骤:s1、焙烧:将浮选型钨原料在500℃的条件下,焙烧2小时;s2、浮选型钨原料磨矿破碎:采用机械破碎的方法将浮选型钨原料磨矿破碎至矿物粒度≤45微米部分质量百分比≥95%。s3、浸出料浆配制:将浮选型钨原料、浸出剂、浸出助剂、杂质浸出抑制剂、水、消泡剂混合,获得浸出料浆;其中,浸出剂为磷酸钠、磷酸二氢钠,浸出助剂为硝酸钠,杂质浸出抑制剂为氧化铝,消泡剂为质量比1:1:1的由石油经分馏或裂化而得的c10~c18烷烃产物、三(辛-癸)烷基叔胺(消泡剂与浮选型钨原料的质量比为1:1×103),浸出料浆的体积与浸出反应器的有效容积之比0.5;s4、浸出:将富氧气体通入浸出反应器中,至浸出反应器中的压力为0.3mpa,富氧气体为氧气体积百分比含量为98%的空气,210℃浸出2.5小时,获得钨酸钠溶液和浸出渣的混合料浆;s5、固液分离:将混合料浆进行压滤分离,获得钨酸钠溶液和浸出渣。s6、浸出渣洗涤:采用洗涤剂将固液分离获得的浸出渣进行洗涤,将所述浸出渣中的可溶于水的钨与所述浸出渣分离,并获得洗水,所述洗水前返用于浸出料浆配制。实施例8:一种浮选型钨原料的分解工艺,包括以下步骤:s1、焙烧:将浮选型钨原料在600℃的条件下,焙烧1小时;s2、浮选型钨原料磨矿破碎:采用机械破碎的方法将浮选型钨原料磨矿破碎至矿物粒度≤45微米部分质量百分比≥95%。s3、浸出料浆配制:将浮选型钨原料、浸出剂、浸出助剂、杂质浸出抑制剂、水、消泡剂混合,获得浸出料浆;其中,浸出剂为碳酸钠、氢氧化钠,浸出助剂为硝酸钠,杂质浸出抑制剂为硫酸铝,消泡剂为质量比1:1:1的由石油经分馏或裂化而得的c10~c18烷烃产物、c12伯醇、三(辛-癸)烷基叔胺(消泡剂与浮选型钨原料的质量比为1:1×102);s4、浸出:浸出料浆的体积与浸出反应器的有效容积之比0.5;然后将富氧气体通入浸出反应器中,至浸出反应器中的压力为0.8mpa,富氧气体为氧气体积百分比含量为90%的空气,于230℃浸出2小时,获得钨酸钠溶液和浸出渣的混合料浆;s5、固液分离:将混合料浆进行离心分离,获得钨酸钠溶液和浸出渣。s6、浸出渣洗涤:采用洗涤剂将固液分离获得的浸出渣进行洗涤,将所述浸出渣中的可溶于水的钨与所述浸出渣分离,并获得洗水,所述洗水前返用于浸出料浆配制。实施例9:一种浮选型钨原料的分解工艺,包括以下步骤:s1、焙烧:将浮选型钨原料在700℃的条件下,焙烧0.5小时;s2、浮选型钨原料磨矿破碎:采用机械破碎的方法将浮选型钨原料磨矿破碎至矿物粒度≤45微米部分质量百分比≥95%。s3、浸出料浆配制:将浮选型钨原料、浸出剂、浸出助剂、杂质浸出抑制剂、水、消泡剂混合,获得浸出料浆;其中,浸出剂为氢氧化钠、氟化钠,浸出助剂为硝酸钠,杂质浸出抑制剂为氧化镁、硫酸铝钾,消泡剂为质量比1:1:1:1的由石油经分馏或裂化而得的c10~c18烷烃产物、c12伯醇、仲辛醇、叔胺n235(消泡剂与浮选型钨原料的质量比为1:1×105);s4、浸出:浸出料浆的体积与浸出反应器的有效容积之比0.5;然后将富氧气体通入浸出反应器中,至浸出反应器中的压力为1.3mpa,富氧气体为氧气体积百分比含量为80%的空气,于250℃浸出1小时,获得钨酸钠溶液和浸出渣的混合料浆;s5、固液分离:将混合料浆进行真空抽滤分离,获得钨酸钠溶液和浸出渣。s6、浸出渣洗涤:采用洗涤剂将固液分离获得的浸出渣进行洗涤,将所述浸出渣中的可溶于水的钨与所述浸出渣分离,并获得洗水,所述洗水前返用于浸出料浆配制。实施例1~9中浮选型钨原料为通过浮选法获得的原料中三氧化钨质量百分数为40.3%的钨原料。对比例1:浸出料浆配制中不加入消泡剂,其余同实施例1。实施例1~9和对比例1得到的钨酸钠溶液经过两级逆流萃取、两级逆流反萃取和两级逆流洗涤后,采用冷却结晶法将钨酸铵溶液中的钨从溶液中沉淀析出,获得仲钨酸铵晶体和结晶母液,仲钨酸铵晶体经干燥后获得仲钨酸铵产品。实施例1~9和对比例1所得仲钨酸铵产品的结果如表1所示。表1钨酸钠溶液中总杂质含量产品中wo3含量总杂质含量实施例161.86g/l88.85%67ppm实施例261.86g/l88.87%67ppm实施例361.86g/l89.22%63ppm实施例461.86g/l89.34%62ppm实施例561.86g/l88.95%66ppm实施例661.86g/l89.16%65ppm实施例761.86g/l89.38%62ppm实施例861.86g/l89.62%61ppm实施例961.86g/l89.92%60ppm对比例161.86g/l88.52%96ppm由表1数据可知,本发明得到的仲钨酸铵产品中杂质含量少,能够得到高质量的仲钨酸铵产品,均符合仲钨酸铵产品国家标准(gbt10116-2007)中apt-0级品要求,杂质少,纯度高;同时减少了钨矿物原料的损失、萃取效果优异,并且具有能耗低、劳动强度低、作业环境良好、生产成本低等优点。其他性能测试:1、通过加入消泡剂,可以加快料液运输。实施例1中,通过泵输送料液时,有利于溶液输送,效率能提高50%以上,目前通过添加消泡剂,运输只需要28分钟。对比例1中,通过泵运输9m3的溶液需要60分钟。实施例1~9运输分别需要28、29、26、27、27、26、25、25、23分钟。2、实施例1~9,通过加入消泡剂,表面活性剂的活性被抑制,溶液在下一步处理过程中,比如净化,在加热和搅拌的条件下不会冒槽(不容易造成跑冒滴漏)。而不添加消泡剂的对比例1,则容易造成上述生产事故。3、实施例1~9,萃取无三相异物,出水口可以长期不清理。对比例1中不添加消泡剂,萃取槽出水口容易三相异物被堵住,需要1天清理一次。实施例1~9添加消泡剂后,出水口只需隔半年清理一次。4、浸出设备备件更加耐用。对比例1浸出过程中,不添加消泡剂,设备使用2-3天,设备不保压,需要更换盘根。实施例1~9添加消泡剂,1-2月才更换一次盘根。综上,本发明的冶炼工艺,在生产过程中料液运输效率能提高50%以上,消除了表面活性剂带来的不利影响,萃取无三相异物、出水口可以长期不清理,浸出设备备件更加耐用,最终得到的仲钨酸铵产品中杂质含量少,产品质量高。最后应说明的是:以上仅为本发明的优选实施例而已,并不用于限制本发明,尽管参照前述实施例对本发明进行了详细的说明,对于本领域的技术人员来说,其依然可以对前述各实施例所记载的技术方案进行修改,或者对其中部分技术特征进行等同替换,凡在本发明的精神和原则之内,所作的任何修改、等同替换、改进等,均应包含在本发明的保护范围之内。当前第1页12