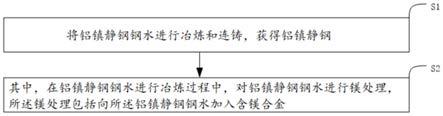
1.本发明属于钢铁冶炼技术领域,特别涉及一种低夹杂物的铝镇静钢的制备方法。
背景技术:2.铝镇静钢顾名思义炼钢过程采用al脱氧钢,目前工业生产中95%以上低合金钢为铝镇静钢。铝镇静钢生产过程中因采用铝脱氧会产生大量al2o3夹杂,al2o3夹杂极易聚集成簇长大,部分不能去除会严重危害钢的力学、腐蚀、疲劳性能。因此工业生产中普遍采用夹杂物改性处理技术对al2o3夹杂改性处理,降低大尺寸al2o3夹杂物尺寸和类型,从而改善钢的综合性能。
3.以国内外管线钢的生产冶炼为例,普遍采用铁水预处理
→
转炉冶炼
→
炉外精炼
→
板坯连铸工艺流程冶炼高洁净管线钢。该钢的具体生产方法包括以下步骤:冶炼
→
lf
→
rh(vd)精炼
→
连铸
→
加热
→
轧制
→
轧后水冷
→
成品。在炼钢过程工艺质量控制上,采用lf+rh(vd)真空处理,钢水夹杂物变性处理几乎100%采用ca处理工艺,钙处理可以有效改善钢铁生产中水口结瘤和al2o3变性处理大型夹杂物脱除问题,因此ca处理在管线钢冶炼生产中得到广泛工业应用。
4.研究发现只有直径大于25μm以上的液相夹杂物才能通过漂浮而去除,而这些残留于钢液中的15
‑
25μm夹杂物对钢质的影响是非常不利的,即使钙处理后仍然存在少部分15
‑
25μm夹杂物存在于钢液中,甚至在ca处理的铝镇静钢中发现更大的铝酸钙夹杂,这种夹杂物会造成严重的钢的质量问题。这对于管线钢特别是腐蚀环境下的抗酸管线和海底管线钢尤其不利,另外,15μm以上的夹杂物易引起钢板氢致裂纹和氢鼓泡现象,严重威胁了管线钢的服役质量安全。
5.而mg氧化物冶金在管线钢中,用于大线能量焊接和改善热影响区韧性。目前钢液mg处理主要集中在船板钢、管线钢,处于试验研究阶段,工业批量mg处理少有报道;中国发明专利申请cn 106399633 a一种船板钢钢液镁处理工艺,采用mg
‑
al包芯合金线在lf(rh)后mg处理,喂入位置为钢包二透气砖对侧,距钢包中心1/3~1/2半径处,喂线速度2.5~4.0m
·
s
‑
1,喂线后软吹≥12min;中国发明专利申请cn102181802a一种镁处理的易焊接高强韧性x80g管线钢的制备方法,实验室真空感应炉采用镁处理获得了高强韧性x80管线钢但是对工艺过程未报导。
技术实现要素:6.申请人在发明过程中发现:mg在对钢中夹杂物变性处理方面,可以减少大颗粒尺寸夹杂物尺寸,故在制备率镇静钢时对钢液进行镁处理,克服了技术偏见。mg处理后,钢中多半形成小的、硬的和尖晶石型的氧化物,这种氧化物在轧制过程中不变形。这种氧化物比通常用ca处理的钢的氧化物小得多。在用mg处理的钢中,会形成固体的mgo
·
al2o3尖晶石,它不呈簇状,而是随机分布在钢中。虽然在mg处理的钢中,会析出大量的小的(<3μm)氧化物,但这种小的氧化物夹杂对钢的力学性能几乎没有任何不利影响。在用mg处理的钢由小
的尖晶石氧化物的边缘几乎都是圆滑的,这与有尖锐棱角的al2o3夹杂不同。这类尖晶石氧化物既不能引发形成空穴,也下能像一般al2o3夹杂物那样成为应力源。所以mg处理后钢中存在的夹杂物对h2s的hic和sscc性能相比ca处理都要更好。
7.同时,申请人在对钢水进行镁处理时发现,无论是rh还是vd工艺,直接加mg会造成爆炸的安全性问题,另外,mg密度较低,加入时会在钢液表面;mg的沸点低,加入前已气化,很难溶入钢液。
8.鉴于上述问题,提出了本发明以便提供一种克服上述问题或者至少部分地解决上述问题的低夹杂物的铝镇静钢的制备方法。
9.本发明实施例提供了一种低夹杂物的铝镇静钢的制备方法,所述方法包括:
10.将铝镇静钢钢水进行冶炼和连铸,获得铝镇静钢;
11.其中,在铝镇静钢钢水进行冶炼过程中,对铝镇静钢钢水进行镁处理,所述镁处理包括向所述铝镇静钢钢水加入含镁合金。
12.可选的,所述含镁合金包括ni
‑
mg合金和mg
‑
al合金中的至少一种。
13.可选的,以重量计,所述ni
‑
mg合金的成分包括:ni70%
‑
90%和mg10
‑
30%。
14.可选的,以重量计,所述mg
‑
al合金的成分包括:al40
‑
50%和mg10
‑
15%,余量为fe。
15.可选的,所述铝镇静钢钢水加入含镁合金的方式包括投入法,所述投入法具体包括:在保护气体氛围下,将含所述镁合金投入所述铝镇静钢钢水,所述保护气体氛围的气压为:40
‑
100kpa,所述含镁合金的粒度≤30mm。
16.可选的,所述铝镇静钢钢水加入含镁合金的方式包括喂线法,所述喂线法具体包括:将含镁合金包芯线喂入所述铝镇静钢钢水,所述含镁合金的粒度为1mm
‑
3mm。
17.可选的,以重量计,所述含镁合金包芯线的喂线量为所述铝镇静钢钢水的0.0002%
‑
0.0018%。
18.可选的,所述含镁合金包芯线的喂线深度为钢水深度的0.6
‑
0.8倍。
19.可选的,所述含镁合金包芯线的喂线速度为3m/s
‑
6m/s。
20.可选的,喂线完成后,将铝镇静钢钢水进行软吹氩气,所述软吹氩气的时间为3min
‑
8min。
21.可选的,所述镁处理的时机为:在铝镇静钢钢水经熔渣脱氧、钢水脱氧、钢水降硫、钢水合金化微调操作后。
22.本发明实施例中的一个或多个技术方案,至少具有如下技术效果或优点:
23.本发明实施例提供的低夹杂物的铝镇静钢的制备方法,所述方法包括:将铝镇静钢钢水进行冶炼和连铸,获得铝镇静钢;其中,在铝镇静钢钢水进行冶炼过程中,对铝镇静钢钢水进行镁处理,所述镁处理包括向所述铝镇静钢钢水加入含镁合金;通过改变mg的加入形态,克服mg元素熔点低、密度小、蒸气压高和化学性质活泼等特点,采取升高熔点和密度、降低蒸气压和化学活性的方法来解决安全加mg问题,采用以ni
‑
mg、mg
‑
al等中间合金形式,实现安全加mg。
24.上述说明仅是本发明技术方案的概述,为了能够更清楚了解本发明的技术手段,而可依照说明书的内容予以实施,并且为了让本发明的上述和其它目的、特征和优点能够更明显易懂,以下特举本发明的具体实施方式。
附图说明
25.为了更清楚地说明本发明实施例中的技术方案,下面将对实施例描述中所需要使用的附图作一简单地介绍,显而易见地,下面描述中的附图是本发明的一些实施例,对于本领域普通技术人员来讲,在不付出创造性劳动的前提下,还可以根据这些附图获得其它的附图。
26.图1是本发明实施例提供的方法的流程图;
27.图2是本发明实施例提供的喂线法的正视图;
28.图3是本发明实施例提供的喂线法的俯视图;
29.图4是本发明实施例提供的钢水内部示意图;
30.图5是本发明对比例1提供的铝镇静钢常规al2o3夹杂的示意图;
31.图6是本发明实施例1提供的铝镇静钢镁处理后夹杂物的示意图;
32.图7是本发明实施例3提供的镁加入量为0.0002%处理后钢中夹杂物三元相图;
33.图8是本发明实施例3提供的镁加入量为0.0004%处理后钢中夹杂物三元相图;
34.图9是本发明实施例3提供的镁加入量为0.0018%处理后钢中夹杂物三元相图;
35.图10是本发明实施例3提供的镁加入量为0.0022%处理后钢中夹杂物三元相图。
具体实施方式
36.下文将结合具体实施方式和实施例,具体阐述本发明,本发明的优点和各种效果将由此更加清楚地呈现。本领域技术人员应理解,这些具体实施方式和实施例是用于说明本发明,而非限制本发明。
37.在整个说明书中,除非另有特别说明,本文使用的术语应理解为如本领域中通常所使用的含义。因此,除非另有定义,本文使用的所有技术和科学术语具有与本发明所属领域技术人员的一般理解相同的含义。若存在矛盾,本说明书优先。
38.除非另有特别说明,本发明中用到的各种原材料、试剂、仪器和设备等,均可通过市场购买得到或者可通过现有方法制备得到。
39.本申请实施例的技术方案为解决上述技术问题,总体思路如下:
40.在国内,对于钢液mg处理技术研究多用于实验和基础理论研究阶段,工业化技术推广应用还未见公开报导。本发明以铝镇静钢生产工艺为基础,提出一种铝镇静钢mg处理工艺技术。包括了mg处理工业应用的原料制备、加入工位、方法和相应的工艺处理等一套工艺技术。该技术可以实现不同工况下,大气、或真空负压下mg处理工艺在生产中工批量安全、高效应用。满足系列高品质铝镇静钢对夹杂物精细化控制的目标。
41.根据本发明一种典型的实施方式,提供了一种低夹杂物的铝镇静钢的制备方法,所述方法包括:
42.将铝镇静钢钢水进行冶炼和连铸,获得铝镇静钢;
43.其中,在铝镇静钢钢水进行冶炼过程中,对铝镇静钢钢水进行镁处理,所述镁处理包括向所述铝镇静钢钢水加入含镁合金。
44.作为一种可选择的实施方式,所述含镁合金包括ni
‑
mg合金和mg
‑
al合金中的至少一种。在其他的实施例中,含镁合金还可以选自si
‑
mg合金、稀土si
‑
mg合金、mg
‑
fe合金等等本领域技术人员能够想到的含镁合金,在此不一一列举。
45.申请人在发明过程中发现:工业生产中冶炼管线钢等高品质洁净钢时通常采用真空处理,无论是rh还是vd工艺,直接加mg会造成爆炸的安全性问题,且mg密度较低,加入时会在钢液表面,同时,mg的沸点低,加入前已气化,很难溶入钢液,另外,镁的化学活性很强,能同氧、硫氮结合而失去合金化的效果,在炼钢温度下,mg接触钢液之前即汽化并形成高压mg蒸汽,mg气化形成的蒸汽压高达1.86mpa,遇到氧会产生剧烈氧化产生爆炸,因此直接把mg加入钢液是很危险的,如何将mg安全地加入钢液中就成为加mg工艺中需首要解决的技术问题。
46.采用以上设计,通过改变mg的加入形态,克服mg元素熔点低、密度小、蒸气压高和化学性质活泼等特点,采取升高熔点和密度、降低蒸气压和化学活性的方法来解决安全加mg问题,采用以ni
‑
mg、mg
‑
al等中间合金形式,实现安全加mg。在实际操作中,以重量计,通常选用的ni
‑
mg合金的成分包括:ni70%
‑
90%和mg10
‑
30%,选用的mg
‑
al合金的成分包括:al40
‑
50%和mg10
‑
15%,余量为fe。
47.铝镇静钢钢水加入含镁合金的方式有两种,分别是投入法和喂线法。
48.作为一种可选的实施方式,铝镇静钢钢水加入含镁合金的方式为投入法,所述投入法具体包括:在保护气体氛围下,将含所述镁合金投入所述铝镇静钢钢水,所述保护气体氛围的气压为:40
‑
100kpa,所述含镁合金的粒度≤30mm。具体而言,保护气体氛围可以选择氩气、氮气、co2等;需要说明的是,大气常压下不需要保护气氛、密闭容器熔炼如真空时才保护气氛。
49.保护气体氛围的作用抑制镁的蒸发,真空下,mg直接加入钢液过程中特别活泼,严重时发生喷发,充入熔炼空间一定压力的保护气体,mg的蒸发受到抑制,压力越高mg收得率越高,控制保护气体氛围的气压为:40
‑
100kpa的原因是气压取值过大时成本过高,过小的不利影响是压力不足,不足以抑制mg挥发。
50.控制含镁合金的粒度≤30mm的原因是mg合金粒度太大,加入钢水时钢水局部mg蒸汽压较大、容易喷发,对合金收得率不利。以合金包芯线加入时,合金线包裹的mg合金粒度更小,尺寸普遍在5mm以下。
51.作为一种可选的实施方式,铝镇静钢钢水加入含镁合金的方式包括喂线法,所述喂线法具体包括:将含镁合金包芯线喂入所述铝镇静钢钢水,所述含镁合金的粒度为1mm
‑
3mm。
52.控制含镁合金的粒度为1mm
‑
3mm的原因是考虑综合合金收得率较高,该粒度取值过大的不利影响是合金局部蒸气压力大,mg元素快速蒸发,过小的不利影响是比重太低被高温蒸气带走,两者都会造成合金收得率降低。
53.申请人在发明过程中发现:现有ca处理的铝镇静钢中仍发现存在的夹杂物尺寸偏大,在ca处理后没有完全去除,在真空前提前mg处理,存在mg收得率低,真空后mg处理,钢中mg含量极低或过高都会造成产品质量不稳定从而影响夹杂物改性工艺效果,如何界定合适的mg含量确保夹杂物改性效果成为了难题。
54.本实施例中,以重量计,所述含镁合金包芯线的喂线量为所述铝镇静钢钢水的0.0002%
‑
0.0018%;含镁合金包芯线的喂线深度为钢水深度的0.6
‑
0.8倍;含镁合金包芯线的喂线速度为3m/s
‑
6m/s。
55.根据钢液中存在的al2o3夹杂和al含量确定al2o3夹杂改质需要的最少mg含量喂线
量,该喂线量取值过大的不利影响是喂线成本较高,mg较高时会产生单颗粒mgo等夹杂,此外加入钢水中mg含量较难达到0.0018%以上,过小的不利影响是无法对钢中大量的有害al2o3夹杂改质。
56.控制含镁合金包芯线的喂线深度为钢水深度的0.6
‑
0.8倍的原因是为了在安全不发生钢水剧烈沸腾状态下保证有效含量的mg合金进入钢液,该深度取值过大的不利影响受mg合金活性影响存在钢水剧烈沸腾,过小的不利影响是mg合金线在无法达到钢水内部,镁蒸气快速上浮至钢液上层,无法均匀化,同时收得率较低。
57.控制含镁合金包芯线的喂线速度为3m/s
‑
6m/s的原因是为了安全高效的控制喂线过程安全性和稳定mg的收得率,该速度取值过大的不利影响是因为钢水内部大量的mg蒸气造成钢水剧烈沸腾,影响安全性,同时造成局部mg含量浓度较高,部分mg直接生成mgo,减少改质有用mg含量,过小的不利影响是造成冶炼周期延长、降低生产效率。
58.本实施例中,喂线完成后,将铝镇静钢钢水进行软吹氩气,所述软吹氩气的时间为3min
‑
8min。
59.软吹氩气的作用是促进合金均匀化和改性效果,控制软吹氩气的时间为3min
‑
8min的原因是在保证合金均匀化和改性效果的前提下尽可能的节约时间。
60.作为一种可选择的实施方式,镁处理的时机为:在铝镇静钢钢水经熔渣脱氧、钢水脱氧、钢水降硫、钢水合金化微调操作后。
61.从钢水状态对mg影响来分析,钢水mg处理应该确保有效的mg对钢中al2o3变形处理,而炉渣和钢水中的氧会损耗mg,为减少炉渣、钢水氧化对mg消耗的损失,需要在加mg前确保炉渣氧势较低,最好在熔渣改质(造白渣)、脱氧完毕、所有合金化微调结束后进行mg处理;同时,在实际操作时,还应注意:mg处理钢水不应该长时间停留,减少炉衬对mg处理后低氧洁净钢水的污染和二次氧化。此外,mg处理前钢水中s含量过高也会影响mg对氧化物改性效果,在较低氧含量钢液中mg会与钢中s结合形成mgs夹杂,从而影响mg直接对al2o3变形处理。并且,较高的钢水温度对mg处理收得率也不利。综上,mg处理前钢水状态应该确保所有合金化微调结束、较低氧、硫含量、合适的温度,具体而言,钢水中氧含量最好低于0.003%,硫含量最好低于0.003%,温度最好控制在钢水过热度的80℃以下、以低温钢水温度为宜。
62.综上所述,结合炼钢工业生产,在喂mg线前需要对一定要顶渣改质和钢水脱氧,降低熔渣的氧势造白渣和钢水中氧含量,从工艺顺序上也要求放在lf精炼完毕或真空精炼结束后。以管线钢为例,管线钢工艺下:冶炼
→
lf
→
rh(vd)精炼
→
连铸,需要在真空处理后开盖大气压下进行,加mg线过程为了确保喷溅较少,在实际操作时,在初始喂mg合金线时,可以降低速度,待加入mg合金线钢液面沸腾平稳后逐渐升速,从而通过实践找到一个平衡速度。在喂mg线后进行底吹ar3
‑
8分钟,促进合金元素均匀和mg处理效果。为确保mg处理效果,利用含mg标样采用电火花直读光谱分析仪对炼钢钢水取样快速分析。
63.下面将结合实施例、对照例及实验数据对本申请的低夹杂物的铝镇静钢的制备方法进行详细说明。
64.实施例1
65.管线钢钢液镁处理生产时采用的工艺流程为:高炉铁水
→
铁水脱硫
→
转炉顶底复合吹炼
→
lf炉
→
rh(mg)处理
→
连铸。管线钢在炼钢lf炉完成了脱氧、脱硫任务,并对钢包顶部炉渣进行了熔渣改质,大幅降低了炉渣的氧化性,经真空rh处理钢中气体危害元素n、h、o
进一步降低,从而为钢液镁处理提供了良好的热力学条件。
66.在rh喂线工位开展喂mg线操作的流程为:
67.(1)mg处理合金线,针对含ni管线钢可以选择ni
‑
mg合金线或al
‑
mg合金线,无ni管线钢仅使用al
‑
mg合金线,al
‑
mg合金线为mg10
‑
15%、al40
‑
50%余fe,包芯线外径13mm,钢带厚度0.4mm。
68.(1)钢包喂线方式详见附图2
‑
4,钢包中钢水重量278吨,喂线操作在真空处理结束后进行,打开钢包炉盖,通过喂丝机喂mg
‑
al线300~450米。喂线前开始软吹,使钢水循环流动起来,喂线时吹氩强度应增至钢包中心渣面被吹开已利镁线喂入钢液,喂线深度约为0.60~0.80h(钢水深度),喂线速度3~6m/秒,喂线后软吹氩气3
‑
8分钟,促进合金均匀化和改性效果,喂mg线合金增量见下表;
[0069][0070]
管线钢mg处理后钢水进行连铸和并经过加热轧制为成品厚度12.7mm。
[0071]
对轧态下钢中夹杂物进行分析,见图6,钢中主要夹杂物未见大尺寸≥15μm夹杂物,夹杂物主要为颗粒状mgo
·
al2o3和表面富集硫化物的颗粒状mgo
·
al2o3。
[0072]
实施例2
[0073]
车轮钢钢液镁处理生产时采用的工艺流程为:高炉铁水
→
铁水脱硫
→
转炉冶炼
→
吹氩
→
lf炉(mg处理)
→
连续铸钢。车轮钢在炼钢lf炉完成了脱氧、脱硫任务,并对钢包顶部炉渣进行了熔渣改质,大幅降低了炉渣的氧化性,从而为lf炉后钢液镁处理提供了良好的热力学条件。
[0074]
在lf喂线工位开展喂mg线操作的流程为:
[0075]
(1)mg处理使用al
‑
mg合金线,al
‑
mg合金线为mg10
‑
15%、al40
‑
50%余fe,包芯线外径13mm,钢带厚度0.4mm。
[0076]
(2)钢包喂线流程见附图1,钢包中钢水重量278吨,喂线操作在lf处理结束后进行,打开钢包炉盖,通过喂丝机喂mg
‑
al线200~600米。喂线前开始软吹,使钢水循环流动起来,喂线时吹氩强度应增至钢包中心渣面被吹开已利镁线喂入钢液,喂线深度约为0.60~0.80h(钢水深度),喂线速度3~6m/秒,喂线后软吹氩气3
‑
8分钟,促进合金均匀化和改性效果,喂mg线合金增量见下表;
[0077][0078]
车轮钢mg处理后钢水进行连铸和并经过加热轧制为成品厚度1.8~16.0mmmm。
[0079]
对轧态下钢中夹杂物进行面扫描夹杂物统计分析,钢中主要夹杂物未见大尺寸≥15μm夹杂物,夹杂物主要为颗粒状mgo
·
al2o3和表面富集硫化物的颗粒状mgo
·
al2o3。
[0080]
实施例3
[0081]
电炉生产铝脱氧镇静钢时采用的工艺流程为:电炉
→
vim(真空感应炉)/vd(真空脱气)(mg处理)
→
连铸/模铸。铝脱氧镇静钢在电炉完成了脱氧、脱硫任务,在真空进行真空处理使钢中气体危害元素n、h、o进一步降低。后续开展了真空mg处理。具体工艺为:
[0082]
(1)mg处理使用了ni
‑
mg合金,其中ni
‑
mg合金ni90%、mg10%,粒度2
‑
20mm,采用从顶部投入法加入到钢液表面。
[0083]
(2)在真空炉真空精炼,钢水重量500kg,钢水成分到了目标要求,钢中全氧≤0.003%,然后在真空室内开展mg处理工艺。mg处理前填充保护气体ar气(40
‑
100)kpa,然后加入ni
‑
mg合金,合金加入后进行提升功率进行电磁搅拌1
‑
3分钟促进合金均匀化,然后浇铸成锭。钢中成品含量见下表。
[0084][0085][0086]
电炉mg处理后钢锭经热轧轧制为成品厚度12~25.4mmm。
[0087]
对轧态下钢中夹杂物进行面扫描夹杂物统计分析,钢中主要夹杂物均未见大尺寸≥15μm夹杂物,说明钢中仅有0.0002%的mg也已经对夹杂物有效改性,夹杂物主要为颗粒状mgo
·
al2o3和表面富集硫化物的颗粒状mgo
·
al2o3。
[0088]
对比例1
[0089]
管线钢钢液生产时采用的工艺流程为:高炉铁水
→
铁水脱硫
→
转炉顶底复合吹炼
→
lf炉
→
rh(mg)处理
→
连铸。
[0090]
对轧态下钢中夹杂物进行面扫描夹杂物统计分析,夹杂物分布见图5中al2o3,钢中存在簇状夹杂物经过热轧变形后延轧向分布,尺寸较大。
[0091]
对比例2
[0092]
管线钢钢液钙处理生产时采用的工艺流程为:高炉铁水
→
铁水脱硫
→
转炉顶底复合吹炼
→
lf炉
→
rh(ca)处理
→
连铸。
[0093]
附图7
‑
8的详细说明:
[0094]
如图2
‑
8所示,分别为镁加入量为0.0002%、0.0004%、0.0018%和0.0022%处理后钢中夹杂物三元相图,由图可得,随着钢中mg含量依次从0.0002%、0.0004%、0.0018%、0.0022%的增加,钢中mgo
·
al2o3尖晶石中mg含量逐渐增加,未改性的al2o3逐渐减少。但当钢中mg含量达到0.0022%后,钢中10
‑
15μm有增加趋势,因此理想的mg含量为0.0002
‑
0.0018%。
[0095]
本发明实施例中的一个或多个技术方案,至少还具有如下技术效果或优点:
[0096]
(1)本发明实施例提供的方法,通过将纯镁进行钝化处理,制成al
‑
mg(al40~50%、mg10~15%)、ni
‑
mg(ni70%~90%、mg10~30%)等合金形式,克服了直接加镁易发生爆炸等问题,不但在常压下可以实现钢液镁处理,亦可以在负压下实现安全加镁;
[0097]
(2)本发明实施例提供的方法,提供了mg处理工业应用的原料制备、加入工位、方法和加入量等一整套工艺技术,突破了目前的实验和基础理论研究阶段,实现了工业化技术推广应用;
[0098]
(3)本发明实施例提供的方法,通过喂线机在lf或rh真空处理后常压下进行,mg处理前必须对熔渣脱氧和钢水脱氧、降硫操作,喂线量约0.0002~0.0018%,深度约为0.60~0.80h(钢水深度),喂线速度3~6m/秒,喂线后软吹氩气3
‑
8分钟,mg处理均能达到良好改性效果,钢中未见大尺寸≥15μm夹杂物;
[0099]
(4)本发明实施例提供的方法,真空负压熔炼气氛下,亦可以采用投入法实现钢液镁处理,mg处理前必须对完成钢水脱氧、降硫操作,填充保护气氛(40
‑
100)kpa后,投入镁合金,细化钢中夹杂物尺寸,实现钢液中改性为小尺寸颗粒状mgo
·
al2o3和mgo
·
al2o3‑
s。
[0100]
最后,还需要说明的是,术语“包括”、“包含”或者其任何其他变体意在涵盖非排他性的包含,从而使得包括一系列要素的过程、方法、物品或者设备不仅包括那些要素,而且还包括没有明确列出的其他要素,或者是还包括为这种过程、方法、物品或者设备所固有的要素。
[0101]
尽管已描述了本发明的优选实施例,但本领域内的技术人员一旦得知了基本创造性概念,则可对这些实施例作出另外的变更和修改。所以,所附权利要求意欲解释为包括优选实施例以及落入本发明范围的所有变更和修改。
[0102]
显然,本领域的技术人员可以对本发明进行各种改动和变型而不脱离本发明的精神和范围。这样,倘若本发明的这些修改和变型属于本发明权利要求及其等同技术的范围之内,则本发明也意图包含这些改动和变型在内。