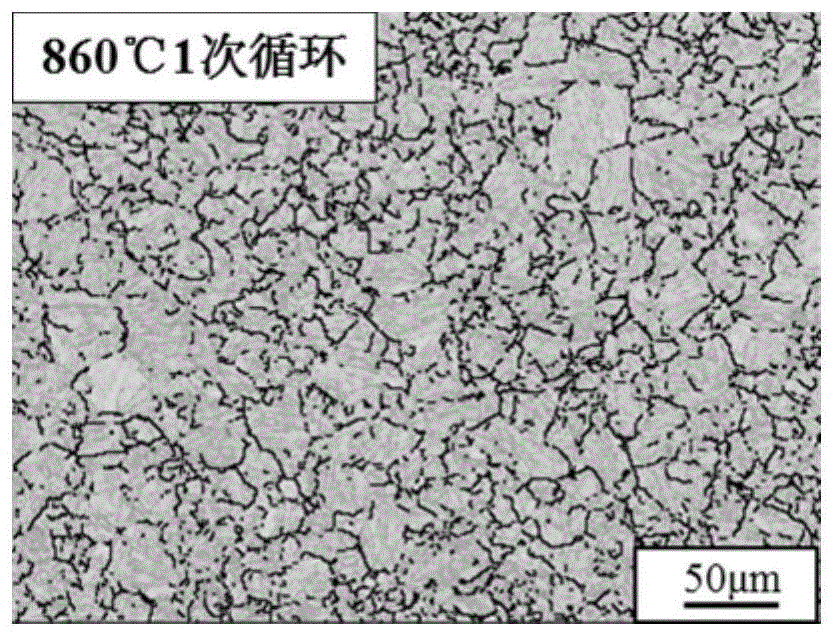
本发明属于冶金生产工艺
技术领域:
,具体为一种提升2.3gpa级纳米析出强化型18ni(350)马氏体时效钢室温冲击韧性的热处理方法,满足用户对不同规格锻造材料力学性能的技术需求。
背景技术:
:18ni(350)钢是国际镍公司(inco)于60年代初研制的马氏体时效钢。它是以无碳(或超低碳)铁镍马氏体为基体,适当温度时效时能产生金属间化合物沉淀硬化的超高强度钢。该钢通常在时效状态下使用,其微观组织特征是在时效马氏体基体中弥散析出棒状ni3ti强化相,与基体呈半共格关系的ni3ti保证了析出强化效果。而超高强钢韧化一直是一个难以解决的问题,细晶强化既可以保证材料强度,同时也可以显著提高材料韧性,获得良好的强韧性匹配。该材料的热处理方式通常为固溶热处理和时效热处理,而晶粒细化可以有效阻碍裂纹扩展,改善应力集中,在保证强度的同时尽可能提升材料的冲击韧性。因此,对材料的固溶热处理和时效热处理之间引入循环相变细晶处理显得尤为重要。技术实现要素:本发明的目的在于提供一种提升2.3gpa级纳米析出强化型18ni(350)马氏体时效钢室温冲击韧性的热处理方法,以提升这种材料的综合力学性能。本发明的技术方案是:一种提升纳米析出强化型18ni(350)马氏体时效钢室温冲击韧性的热处理方法,热处理方法包括按顺序设置的固溶热处理、循环相变热处理和时效热处理,其中:循环相变热处理包括快速升温、短时保温和水淬处理工序三个步骤,并重复循环两次以上,使得合金元素完全固溶于铁基体中,并增加基体中的残余奥氏体含量。所述的提升纳米析出强化型18ni(350)马氏体时效钢室温冲击韧性的热处理方法,按重量百分计比,马氏体时效钢为包含有下述组分的固溶时效处理棒材:c≤0.001%,ni18.1~18.2%,co11.1~11.5%,mo4.94~4.98%,ti0.94~0.98%,o≤0.0013%,n≤0.0008%,余量为fe和不可避免的杂质。所述的提升纳米析出强化型18ni(350)马氏体时效钢室温冲击韧性的热处理方法,按重量百分比计,不可避免的杂质包括p和s,p≤0.0009%,s≤0.0009%。所述的提升纳米析出强化型18ni(350)马氏体时效钢室温冲击韧性的热处理方法,固溶处理工序是按以下步骤进行的:将棒材放入真空热处理炉中按5~15℃/min的加热速率加热至860℃±10℃,保温0.5~1.5小时后,出炉水冷至室温完成。所述的提升纳米析出强化型18ni(350)马氏体时效钢室温冲击韧性的热处理方法,循环相变热处理工序是按以下步骤进行:将固溶处理后的棒材放入真空热处理炉中按5~15℃/min的加热速率加热至860℃±10℃,保温10~20分钟,出炉水冷至室温,循环相变热处理重复循环3~5次完成。所述的提升纳米析出强化型18ni(350)马氏体时效钢室温冲击韧性的热处理方法,时效热处理为人工时效处理,其具体过程为:待棒材完成循环相变热处理后,将其放入真空热处理炉中,并按4~6℃/min加热速率加热至510℃±10℃,保温4h~16h,出炉空冷至室温完成。所述的提升纳米析出强化型18ni(350)马氏体时效钢室温冲击韧性的热处理方法,时效热处理后马氏体时效钢棒材力学性能如下:σb:2235~2250mpa,σs:2180~2195mpa,a:9.5~10.0%,z:60.0~65.0%,akv:(25℃)20~25j。本发明的设计思想是:本发明旨在保证材料强度的同时,提升材料韧性,改善材料的强韧性匹配。在常规固溶处理和时效处理之间引入循环相变处理。(1)固溶处理使合金中各种相充分溶解,强化固溶体,并提高韧性及抗蚀性能,消除应力与软化,为后续的时效强化做好准备。(2)循环相变利用快速升温、短时保温、快速淬火冷却的方法对晶粒进行细化。循环相变细化晶粒过程中,材料经历的反复转变,而马氏体相变为切变型相变,切变过程中在马氏体组织中产生大量微观缺陷,在逆转变时会被继承,微观缺陷增加了材料的储存能,促进再结晶。经过再结晶处理的样品板条碎化,位错密度明显升高,保证了材料的强度等级。同时,晶粒细化有效阻碍了裂纹扩展,改善了应力集中,有效地提升了材料的韧性。(3)时效处理使得颗粒细小、分布均匀的析出强化相大量析出,保证材料的强度等级。经过固溶处理、循环相变处理、时效处理后材料固溶充分、保证了强化相的充分且均匀析出,同时经过循环细晶后材料位错密度明显升高,晶粒明显细化,得到了较好的强韧性匹配。本发明的优点及有益效果是:(1)本发明提供一种提升2.3gpa级18ni(350)超高强度马氏体时效钢室温冲击韧性的热处理方法,经860℃循环相变热处理后晶粒得到明显细化,有效阻碍了裂纹扩展,改善了应力集中,在保证强度等级的前提下,显著提升钢的冲击韧性。(2)本发明提供一种提升2.3gpa级18ni(350)超高强度马氏体时效钢室温冲击韧性的热处理方法,可用于实际铸锻件的性能热处理,综合提升强韧性。附图说明图1(a)-图1(d)为实施例1中不同循环相变热处理后所得的微观组织图片。图1(a)860℃1次循环,图1(b)860℃2次循环,图1(c)860℃3次循环,图1(d)860℃4次循环。具体实施方式在具体实施过程中,本发明提升2.3gpa级18ni(350)超高强度马氏体时效钢冲击韧性的热处理方法,包括按顺序设置的固溶热处理、循环相变热处理和时效热处理,其中循环相变热处理包括快速升温、短时保温和水淬处理工序三个步骤,并多次循环,使得合金元素完全固溶于铁基体中,并增加基体中的残余奥氏体含量。采用本发明热处理方法能够在保证强度等级的前提下,显著提升材料的冲击韧性,从而获得良好的综合力学性能。按重量百分比计,马氏体时效钢为包含有下述组分的固溶时效处理棒材:c≤0.001%,ni18.1~18.2%,co11.1~11.5%,mo4.94~4.98%,ti0.94~0.98%,o≤0.0013%,n≤0.0008%,余量为fe和不可避免的杂质。上述实施方式中,为了更好控制本发明所述马氏体时效钢的组分,尽可能通过本发明的热处理方法提升冲击韧性,所述不可避免的杂质包括p、s,其中按重量百分比计的p≤0.0009%,s≤0.0009%。所述的时效热处理是按以下步骤进行的,待淬火处理的棒材冷却至室温后,将其继续放入真空热处理炉中,并按5℃/min加热速率加热至510℃,保温,出炉空冷至室温完成所述的人工时效处理,其中在真空热处理炉中保温时长为4h~16h。而所述的固溶处理工序是按以下步骤进行的,将棒材放入真空热处理炉中按10℃/min的加热速率加热至860℃,保温1小时后,出炉水冷至室温完成所述固溶处理工序。所述的循环相变热处理工序是按以下步骤进行的,将固溶处理后的棒材放入真空热处理炉中按10℃/min的加热速率加热至860℃,保温15分钟,出炉水冷至室温,重复循环四次完成。综上所述,采用本发明所述18ni(350)马氏体时效钢,并对其进行上述的双固溶热处理和时效热处理,可显著提升冲击韧性,其综合强韧性满足关键结构件的使用条件。时效处理后的棒材性能指标,抗拉强度σb:2235~2250mpa,屈服强度σs:2180~2195mpa,延伸率a:9.5~10.0%,断面收缩率z:60.0~65.0%,冲击功akv:(25℃)20~25j,综合力学性能良好。下面,实施例和附图对本发明进一步详细阐述。实施例1本实施例中,按重量百分比计,18ni(350)超高强度马氏体时效钢为包含有下述组分的固溶时效处理棒材:c0.0008%,ni18.1%,co11.3%,mo4.95%,ti0.96%,o0.0007%,n0.0006%,p0.0004%,s0.0005%,余量为fe。产品技术要求如表1所示:表1产品技术要求牌号直径/mm屈服强度σs/mpa抗拉强度σb/mpa冲击功akv/j18ni(350)80±5≥2100≥2200≥20本实施例中,以规格为直径80mm、长度200mm的棒料为例,提升2.3gpa级18ni(350)超高强度马氏体时效钢冲击韧性的热处理方法,包括如下步骤:(1)固溶热处理。将棒料放置于真空热处理炉的平台中心处,将棒料按10℃/min加热至860±10℃保温1小时,后出炉进行水冷至室温。(2)循环相变热处理。将步骤(1)处理后的棒料放入真空热处理炉中进行循环相变热处理,将棒料按10℃/min加热至860±10℃并保温15min后出炉进行水淬至室温,重复循环四次。(3)时效热处理。将步骤(2)处理后的棒料放入真空热处理炉中进行时效热处理,将棒料按5℃/min加热至510±10℃并保温16h,随后出炉空冷至室温。根据本实施例所获得的产品力学性能数据如表2所示:表2产品力学性能如图1(a)-图1(d)所示,18ni(350)马氏体时效钢按照本发明申报的工艺方案不同循环相变热处理后的晶粒尺寸微观组织照片,黑色为原奥氏体晶界,其余为马氏体基体。从中可见,经过多次循环相变后材料晶粒得到明显细化,晶粒度明显提高,晶粒尺寸为8.0~9.5微米,晶粒度等级为10.5~11.0。实施例结果表明,本发明通过固溶处理、循环相变热处理以及时效热处理能显著细化材料晶粒尺寸,并且能保证纳米级析出相的稳定存在,这种细小且均匀的晶粒使得产品的力学性能能够满足产品的技术要求,且显著提升了冲击韧性。以上所述仅为本发明的较佳实施例,并不用以限制本发明,凡在本发明的精神和原则之内所作的任何修改、等同替换、改进等,均应包含在本发明的保护范围之内。当前第1页12