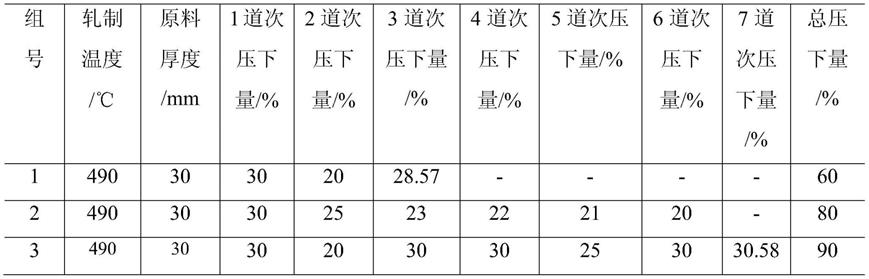
一种超高强al
‑
zn
‑
mg
‑
cu
‑
sc
‑
zr合金板材及其制备工艺
技术领域:
1.本发明属于合金板材制备技术领域,具体涉及一种超高强al
‑
zn
‑
mg
‑
cu
‑
sc
‑
zr合金板材及其制备工艺。
背景技术:2.7xxx系合金是在al
‑
zn
‑
mg合金基础上通过添加cu发展起来的,其强度高于2xxx系铝合金,一般称为超高强铝合金。超高强铝合金具有密度低、比强度高、热加工性能好等优点,其研究和应用一直倍受关注。
3.最初的7xxx系合金是由韦伯于1932年提出的,在al
‑
zn
‑
mg合金中添加cu的同时加入了少量mn,开发出世界上第一种以al
‑
zn
‑
mg
‑
cu为基的高强铝合金。但由于合金具有较高的应力腐蚀敏感性(scc)而未得到实际应用。1936年,日本学者五十岚第一次将cr加入到 al
‑
zn
‑
mg
‑
cu合金中,开发出著名的esd超硬合金 (al
‑
7.5%zn
‑
l.5%mg
‑
2%cu
‑
0.6%mn
‑
0.25%cr),这种合金具有600mpa以上的强度和较好的抗应力腐蚀性能,该合金最先在飞机制造业中获得实际应用。在esd合金研究的基础上,各国相继开发了一批含有少量cr、mn的7xxx系铝合金。1943年美国开发出了7075合金,并第一次应用于b
‑
29型轰炸机上,给飞机结构和性能带来革命性变化,为超高强铝合金的飞速发展奠定了基础。1954年,在7075合金的基础上提高zn、mg和cu的含量,开发出了强度高于7075
‑
t651合金的7178
‑
t651合金。该合金强度虽高,但断裂韧性太差,在波音747飞机上被7075
‑
t651合金替代。1960年,开发出二级时效工艺t73,并应用于7075合金,解决了厚截面的scc问题。60年代中期开发了t76时效工艺,使合金强度较t73有所提高,且抗应力腐蚀和抗剥蚀性能满足使用要求。1968年,美国铝业公司在7001合金的基础上,增加 mg、zn含量,降低cu、cr含量,开发出7049合金。1969年在7075合金基础上,通过降低fe、si含量,控制cr含量,调整mn、cu含量以提高断裂韧性,研制出7xxx系断裂韧性最高的7475合金,该合金除了成分差别外,加工工艺也有所改变,通过调整晶粒度、均匀性、 e相(al
12
mg2cr)的尺寸和质点间距,使其韧性得到改善。1971年,美国以7075为基础,增加了zn、cu含量和cu/mg比值来提高强度,用添加zr代替cr来克服淬火敏感性问题和调整晶粒尺寸,开发出了强度、断裂韧性和抗应力腐蚀性能较高的7050合金,并于同年在美国铝业协会登记注册。80年代,alcoa公司进行了大量研究,在7050和7150合金的基础上,进一步降低si、mn杂质元素的含量,提高zn/mg比值,研制成功7055合金,并于1993年申请到专利。在50年代末至80年代末期间开发出一系列高水平的al
‑
zn
‑
mg
‑
cu系超高强铝合金。在俄罗斯的铝合金牌号中,ц为含zr合金,цч为高纯合金,0ч为最高纯合金。1948 年开发出b95合金,与美国的7075合金相近。1956年,在深入研究al
‑
zn
‑
mg
‑
cu基础上,世界上首次在al
‑
zn
‑
mg
‑
cu系合金中添加zr来代替cr,研制出合金化程度和强度最高的b96 合金;1968年通过降低杂质fe含量和添加mn元素,开发出b96
ц
‑1合金;1970年通过进一步降低fe、si杂质含量,同时降低主合金元素,又开发出塑性较好而强度略有降低的b96
ц
‑3。全苏轻合金研究所和全苏航空材料研究所继1948年研制出b95合金后,通过降低fe、si杂质含量,于1971年开发出b95
цч
,和b95
oч
,这两种合金不仅用来制造伊尔96
‑
300型和图 204型飞
机,而且现今还用来制造苏
‑
27和苏
‑
30飞机的结构件。
4.我国超高强铝合金的研究开发起步较晚。20世纪80年代初,东北轻合金加工厂和北京航空材料研究所开始研制al
‑
zn
‑
mg
‑
cu系铝合金。目前,我国在普通7xxx系铝合金的生产和应用方面己进入实际应用阶段,主要包括7075、7050、7175等,用于航天航空器的某些结构件的制造。90年代中期,北京航空材料研究所釆用连续铸造法成功制成了7a55超高强铝合金,近年来又开发了强度更高的7a60铝合金。北京有色金属研究总院和东北轻合金加工厂,开展了采用喷射成形工艺研发含zn量更高的超高强铝合金。北京有色金属研究总院、东北大学、中南大学、北京航空航天大学、北京科技大学和东北轻合金加工厂等单位联合研究新型超高强度高强合金。合金名义成分为a1
‑
10%zn
‑
2.5%mg
‑
2.3%cu
‑
0.15%zr。北京有色金属研究总院釆用喷射成形技术制备铸锭,铸锭无裂纹、组织细小,经过变形和热处理后强度达到810mpa
[19
‑
20]
。综上所述,超高强铝合金的研究基本是沿着高强度、低韧性
‑
高强度、高韧性
‑
高强度、高韧性、耐腐蚀方向发展;热处理状态研究方向沿着t6
‑
t73
‑
t76
‑
t736(t74)
‑
t77 发展;合金设计方向的发展特点是合金化程度越来越高,fe、si等杂质含量越来越低,微量过渡族元素添加越来越合理,最终结果是在大幅度提髙强度的同时保持合金具有优良的韧性和抗腐蚀性能。
[0005]
目前各国民用飞机上铝合金用量已占结构重量的70%
‑
80%,其中大部分为超高强铝合金。为此,各国的材料工作者多年来一直致力于研究开发集高强、高韧、高抗腐蚀性为一体的超高强铝合金。本发明对7xxx系铝合金成分设计进行优化并添加稀土元素sc和zr元素,设计了新型的al
‑
zn
‑
mg
‑
cu
‑
sc
‑
zr合金成分,并提出了该合金板材轧制及热处理的方法。
技术实现要素:[0006]
本发明的目的是克服上述现有技术存在的不足,提供一种超高强al
‑
zn
‑
mg
‑
cu
‑
sc
‑
zr合金板材及其制备工艺。
[0007]
为实现上述目的,本发明采用以下技术方案:
[0008]
一种超高强al
‑
zn
‑
mg
‑
cu
‑
sc
‑
zr合金板材包括组分及质量百分含量为:zn 6.5%~7%、mg 1.8%~2.3%、cu 1.9%~2.4%、sc 0.18%~0.22%、zr 0.08%~0.12%,si≤0.1%、fe≤0.15%、 mn≤0.05%、cr≤0.04%、ti≤0.06%,余量为al。
[0009]
所述的zn以纯zn形式加入,mg以纯mg形式加入,cu以纯cu形式加入,sc以al
‑
2%sc 中间合金形式加入,zr以al
‑
5%zr中间合金形式加入。
[0010]
所述的超高强al
‑
zn
‑
mg
‑
cu
‑
sc
‑
zr合金板材抗拉强度为705mpa~725mpa,屈服强度为608 mpa~632mpa,断裂伸长率为9.2%~11.5%。
[0011]
所述的超高强al
‑
zn
‑
mg
‑
cu
‑
sc
‑
zr合金板材的晶粒呈等轴状,晶粒尺寸为60~80μm,晶粒内存在可强化合金的析出相,包括gp区、η'相和al3(sc,zr)相,晶界处存在利于塑性的晶界无析出带,所述的al3(sc,zr)相为细小弥散的豆瓣状粒子,粒子尺寸为5
‑
12nm。
[0012]
所述的超高强al
‑
zn
‑
mg
‑
cu
‑
sc
‑
zr合金板材制备工艺,包括以下步骤:
[0013]
(1)按照超高强al
‑
zn
‑
mg
‑
cu
‑
sc
‑
zr合金组分熔炼后浇注,获得合金铸坯;
[0014]
(2)对合金铸坯在490
‑
510℃下保温1
‑
3h后进行热轧,所述的初轧温度为480℃~490℃,终轧温度为440℃~450℃,获得合金板材;其中,所述的轧制道次为5~6道次,总压
下量为 73.33%~80%,单道次压下量为20%~30%;
[0015]
(3)对合金板材进行热处理,包括固溶处理和回归再时效处理,制得超高强 al
‑
zn
‑
mg
‑
cu
‑
sc
‑
zr合金板材,其中,所述的固溶处理工艺参数为(480
‑
490℃)
×
(0.5
‑
1.5h),回归再时效处理工艺参数为:
[0016]
(140
‑
160℃)
×
(17
‑
19h)+(190
‑
210℃)
×
(0.5
‑
1.5h)+(150
‑
170℃)
×
(17
‑
19h)。
[0017]
所述的步骤(1)中,合金熔炼温度为730℃~740℃;炉料加入顺序为:纯al、al
‑
5%zr中间合金、al
‑
2%sc中间合金、纯cu、纯zn和纯mg;在加入纯zn时搅拌熔体;在加入纯 mg时搅拌熔体。
[0018]
所述的步骤(1)中,待所有炉料加入后扒去熔体表面浮渣后进行取样分析,确保成分合格。
[0019]
所述的步骤(1)中,浇注温度为720℃~730℃,使用玻璃丝布及陶瓷过滤器进行铝液转注过程的过滤除渣,其中过滤器由2层玻璃网和ppi40泡沫陶瓷过滤芯组成。
[0020]
所述的步骤(1)中,合金铸坯厚度为30mm、宽度为200mm、长度为500mm。
[0021]
所述的步骤(2)中,轧制速度为0.5
‑
2.5m/s。
[0022]
所述的步骤(2)中,初轧温度优选为490℃。
[0023]
所述的步骤(2)中,第1道次压下量优选为30%,当轧制道次为5道次时,所述的单道次压下量值顺序为第1道次≥第2道次≥第3道次≥第4道次≥第5道次≥;当轧制道次为6道次时,所述的单道次压下量值顺序为第1道次≥第2道次≥第3道次≥第4道次≥第5道次≥第6 道次,也即保证大部分压下任务在前面道次完成,向后单道次压下量逐渐减小。
[0024]
所述的步骤(2)中,合金板材厚度为6mm~8mm。
[0025]
本发明的有益效果:
[0026]
本发明的超高强al
‑
zn
‑
mg
‑
cu
‑
sc
‑
zr合金板材及其制备工艺,在al
‑
zn
‑
mg
‑
cu系合金基础上添加适量的sc和zr元素,并通过热轧和热处理,在双级时效中间加入了特定的高温回归过程,可以使大尺寸的析出相回溶,使析出相整体细小弥散,通过控制合金组织,来获得高强度高塑性的合金板材,该发明可推广至超高强铝合金板材生产中,扩大超高强铝合金的使用范围。
附图说明:
[0027]
图1为本发明对比例3
‑
6制备的al
‑
zn
‑
mg
‑
cu
‑
sc
‑
zr合金板材拉伸断口的扫描电子显微镜图像;
[0028]
图2为本发明实施例3制备的al
‑
zn
‑
mg
‑
cu
‑
sc
‑
zr合金板材拉伸断口的扫描电子显微镜图像;
[0029]
图3为本发明对比例3
‑
7制备的al
‑
zn
‑
mg
‑
cu
‑
sc
‑
zr合金板材拉伸断口的扫描电子显微镜图像;
[0030]
图4为本发明对比例3
‑
8制备的al
‑
zn
‑
mg
‑
cu
‑
sc
‑
zr合金板材开裂情况图;
[0031]
图5为本发明对比例3
‑
9制备的al
‑
zn
‑
mg
‑
cu
‑
sc
‑
zr合金板材开裂情况图。
具体实施方式:
[0032]
下面结合实施例对本发明作进一步的详细说明。
[0033]
以下实施例1
‑
4中,制备的超高强al
‑
zn
‑
mg
‑
cu
‑
sc
‑
zr合金板材的晶粒尺寸,以及al3(sc, zr)相粒子尺寸限于检测手段未做进一步细分,但实际各有不同,平均晶粒尺寸与al3(sc,zr) 相粒子平均尺寸:实施例1>实施例4>实施例2>实施例3。
[0034]
实施例1
[0035]
一种超高强al
‑
zn
‑
mg
‑
cu
‑
sc
‑
zr合金板材包括组分及质量百分含量为:zn 6.5%、mg1.8%、cu 1.9%、sc 0.18%、zr 0.08%,si≤0.1%、fe≤0.15%、mn≤0.05%、cr≤0.04%、ti≤0.06%,余量为al。
[0036]
所述的zn以纯zn形式加入,mg以纯mg形式加入,cu以纯cu形式加入,sc以al
‑
2%sc 中间合金形式加入,zr以al
‑
5%zr中间合金形式加入。
[0037]
所述的超高强al
‑
zn
‑
mg
‑
cu
‑
sc
‑
zr合金板材制备工艺,包括以下步骤:
[0038]
(1)按照超高强al
‑
zn
‑
mg
‑
cu
‑
sc
‑
zr合金组分熔炼后浇注,获得合金铸坯,合金铸坯厚度为30mm、宽度为200mm、长度为500mm,其中:
[0039]
合金熔炼温度为730℃;炉料加入顺序为:纯al、al
‑
5%zr中间合金、al
‑
2%sc中间合金、纯cu、纯zn和纯mg;在加入纯zn时搅拌熔体;在加入纯mg时搅拌熔体;
[0040]
浇注温度为720℃,使用玻璃丝布及陶瓷过滤器进行铝液转注过程的过滤除渣,其中过滤器由2层玻璃网和ppi40泡沫陶瓷过滤芯组成;
[0041]
待所有炉料加入后扒去熔体表面浮渣后进行取样分析,确保成分合格;
[0042]
(2)对合金铸坯在490℃下保温3h后进行热轧,所述的初轧温度为480℃,终轧温度为440℃,轧制道次为5道次,总压下量为73.33%,第1道次压下量为30%,第2道次压下量为22%,第3道次压下量为21.98%,第4道次压下量为21.75%,第5道次压下量为20%,轧制速度为0.5m/s,获得合金板材,厚度为8mm;
[0043]
(3)对合金板材进行热处理,包括固溶处理和回归再时效处理,固溶处理工艺参数为 480℃
×
1.5h,回归再时效处理工艺参数为:140℃
×
19h+190℃
×
1.5h+150℃
×
19h;制得超高强 al
‑
zn
‑
mg
‑
cu
‑
sc
‑
zr合金板材,所述的超高强al
‑
zn
‑
mg
‑
cu
‑
sc
‑
zr合金板材的晶粒呈等轴状,晶粒尺寸为60~80μm,晶粒内存在可强化合金的析出相,包括gp区、η'相和al3(sc,zr)相,晶界处存在利于塑性的晶界无析出带,所述的al3(sc,zr)相为细小弥散的豆瓣状粒子,粒子尺寸为5
‑
12nm。抗拉强度为705mpa,屈服强度为608mpa,断裂伸长率为10.3%。
[0044]
实施例2
[0045]
一种超高强al
‑
zn
‑
mg
‑
cu
‑
sc
‑
zr合金板材包括组分及质量百分含量为:zn 6.6%、mg2.0%、cu 2.0%、sc 0.19%、zr 0.09%,si≤0.1%、fe≤0.15%、mn≤0.05%、cr≤0.04%、ti≤0.06%,余量为al。
[0046]
所述的zn以纯zn形式加入,mg以纯mg形式加入,cu以纯cu形式加入,sc以al
‑
2%sc 中间合金形式加入,zr以al
‑
5%zr中间合金形式加入。
[0047]
所述的超高强al
‑
zn
‑
mg
‑
cu
‑
sc
‑
zr合金板材制备工艺,包括以下步骤:
[0048]
(1)按照超高强al
‑
zn
‑
mg
‑
cu
‑
sc
‑
zr合金组分熔炼后浇注,获得合金铸坯,合金铸坯厚度为30mm、宽度为200mm、长度为500mm,其中:
[0049]
合金熔炼温度为730℃;炉料加入顺序为:纯al、al
‑
5%zr中间合金、al
‑
2%sc中间合金、纯cu、纯zn和纯mg;在加入纯zn时搅拌熔体;在加入纯mg时搅拌熔体;
[0050]
浇注温度为720℃,使用玻璃丝布及陶瓷过滤器进行铝液转注过程的过滤除渣,其
中过滤器由2层玻璃网和ppi40泡沫陶瓷过滤芯组成;
[0051]
待所有炉料加入后扒去熔体表面浮渣后进行取样分析,确保成分合格;
[0052]
(2)对合金铸坯在490℃下保温3h后进行热轧,所述的初轧温度为485℃,终轧温度为 445℃,轧制道次为5道次,总压下量为75%,第1道次压下量为30%,第2道次压下量为21.9%,第3道次压下量为20.73%,第4道次压下量为20%,第5道次压下量为27.88%,轧制速度为1.5m/s,获得合金板材,厚度为7.5mm;
[0053]
(3)对合金板材进行热处理,包括固溶处理和回归再时效处理,固溶处理工艺参数为 485℃
×
1h,回归再时效处理工艺参数为:150℃
×
18h+200℃
×
1h+160℃
×
18h;制得超高强 al
‑
zn
‑
mg
‑
cu
‑
sc
‑
zr合金板材,所述的超高强al
‑
zn
‑
mg
‑
cu
‑
sc
‑
zr合金板材的晶粒呈等轴状,晶粒尺寸为60~80μm,晶粒内存在可强化合金的析出相,包括gp区、η'相和al3(sc,zr)相,晶界处存在利于塑性的晶界无析出带,所述的al3(sc,zr)相为细小弥散的豆瓣状粒子,粒子尺寸为5
‑
12nm。抗拉强度为718mpa,屈服强度为626mpa,断裂伸长率为10.6%。
[0054]
实施例3
[0055]
一种超高强al
‑
zn
‑
mg
‑
cu
‑
sc
‑
zr合金板材包括组分及质量百分含量为:zn 6.8%、mg 2.2%、cu 2.2%、sc 0.20%、zr 0.10%,si≤0.1%、fe≤0.15%、mn≤0.05%、cr≤0.04%、ti≤0.06%,余量为al。
[0056]
所述的zn以纯zn形式加入,mg以纯mg形式加入,cu以纯cu形式加入,sc以al
‑
2%sc 中间合金形式加入,zr以al
‑
5%zr中间合金形式加入。
[0057]
所述的超高强al
‑
zn
‑
mg
‑
cu
‑
sc
‑
zr合金板材制备工艺,包括以下步骤:
[0058]
(1)按照超高强al
‑
zn
‑
mg
‑
cu
‑
sc
‑
zr合金组分熔炼后浇注,获得合金铸坯,合金铸坯厚度为30mm、宽度为200mm、长度为500mm,其中:
[0059]
合金熔炼温度为730℃~740℃;炉料加入顺序为:纯al、al
‑
5%zr中间合金、al
‑
2%sc 中间合金、纯cu、纯zn和纯mg;在加入纯zn时搅拌熔体;在加入纯mg时搅拌熔体;
[0060]
浇注温度为720℃~730℃,使用玻璃丝布及陶瓷过滤器进行铝液转注过程的过滤除渣,其中过滤器由2层玻璃网和ppi40泡沫陶瓷过滤芯组成;
[0061]
待所有炉料加入后扒去熔体表面浮渣后进行取样分析,确保成分合格;
[0062]
(2)对合金铸坯在500℃下保温2h后进行热轧,所述的初轧温度为490℃,终轧温度为 450℃,轧制道次为6道次,总压下量为80%,第1道次压下量为30%,第2道次压下量为 25%,第3道次压下量为23%,第4道次压下量为22%,第5道次压下量为21%,第6道次压下量为20%,轧制速度为1.5m/s,获得合金板材,厚度为6mm;
[0063]
(3)对合金板材进行热处理,包括固溶处理和回归再时效处理,固溶处理工艺参数为 485℃
×
1h,回归再时效处理工艺参数为:150℃
×
18h+200℃
×
1h+160℃
×
18h;制得超高强 al
‑
zn
‑
mg
‑
cu
‑
sc
‑
zr合金板材,所述的超高强al
‑
zn
‑
mg
‑
cu
‑
sc
‑
zr合金板材的拉伸断口的扫描电子显微镜图像如图2所示。合金板材的晶粒尺寸为60~80μm,晶粒内存在可强化合金的析出相,包括gp区、η'相和al3(sc,zr)相,晶界处存在利于塑性的晶界无析出带,所述的al3(sc, zr)相为细小弥散的豆瓣状粒子,粒子尺寸为5
‑
12nm。晶粒呈等轴状,未见沿轧制方向拉长的情况。由此可见,通过轧制且压下量满足一定临界条件时,发生了较为充分的动态再结晶,使得原始粗大的铸态组织被细化。根据hall
‑
petch原理,晶粒细化可实现强度和塑性的良好匹配,因此在总压下量为80%时合金强度大幅度提高的同时塑性并未见明
显降低。抗拉强度为725mpa,屈服强度为632mpa,断裂伸长率为9.2%。
[0064]
实施例4
[0065]
一种超高强al
‑
zn
‑
mg
‑
cu
‑
sc
‑
zr合金板材包括组分及质量百分含量为:zn 7%、mg 2.3%、 cu 2.4%、sc 0.22%、zr 0.12%,si≤0.1%、fe≤0.15%、mn≤0.05%、cr≤0.04%、ti≤0.06%,余量为al。
[0066]
所述的zn以纯zn形式加入,mg以纯mg形式加入,cu以纯cu形式加入,sc以al
‑
2%sc 中间合金形式加入,zr以al
‑
5%zr中间合金形式加入。
[0067]
所述的超高强al
‑
zn
‑
mg
‑
cu
‑
sc
‑
zr合金板材制备工艺,包括以下步骤:
[0068]
(1)按照超高强al
‑
zn
‑
mg
‑
cu
‑
sc
‑
zr合金组分熔炼后浇注,获得合金铸坯,合金铸坯厚度为30mm、宽度为200mm、长度为500mm,其中:
[0069]
合金熔炼温度为730℃~740℃;炉料加入顺序为:纯al、al
‑
5%zr中间合金、al
‑
2%sc 中间合金、纯cu、纯zn和纯mg;在加入纯zn时搅拌熔体;在加入纯mg时搅拌熔体;
[0070]
浇注温度为720℃~730℃,使用玻璃丝布及陶瓷过滤器进行铝液转注过程的过滤除渣,其中过滤器由2层玻璃网和ppi40泡沫陶瓷过滤芯组成;
[0071]
待所有炉料加入后扒去熔体表面浮渣后进行取样分析,确保成分合格;
[0072]
(2)对合金铸坯在510℃下保温1h后进行热轧,所述的初轧温度为490℃,终轧温度为 450℃,轧制道次为5道次,总压下量为75%,第1道次压下量为30%,第2道次压下量为 21.9%,第3道次压下量为20.73%,第4道次压下量为20%,第5道次压下量为27.88%,轧制速度为2.5m/s,获得合金板材,厚度为7.5mm;
[0073]
(3)对合金板材进行热处理,包括固溶处理和回归再时效处理,固溶处理工艺参数为 490℃
×
0.5h,回归再时效处理工艺参数为:160℃
×
17h+210℃
×
0.5h+170℃
×
17h;制得超高强 al
‑
zn
‑
mg
‑
cu
‑
sc
‑
zr合金板材,所述的超高强al
‑
zn
‑
mg
‑
cu
‑
sc
‑
zr合金板材的晶粒呈等轴状,晶粒尺寸为60~80μm,晶粒内存在可强化合金的析出相,包括gp区、η'相和al3(sc,zr)相,晶界处存在利于塑性的晶界无析出带,所述的al3(sc,zr)相为细小弥散的豆瓣状粒子,粒子尺寸为5
‑
12nm。抗拉强度为707mpa,屈服强度为610mpa,断裂伸长率为11.0%。
[0074]
对比例3
‑1[0075]
同实施例3,区别在于,超高强al
‑
zn
‑
mg
‑
cu
‑
sc
‑
zr合金板材中sc为0.4%~0.5%、zr为0.3%~0.4%。采用后续相同热处理工艺。经检测,制备的超高强al
‑
zn
‑
mg
‑
cu
‑
sc
‑
zr合金板材晶粒内gp区和η'相因析出受抑制而减少,al3(sc,zr)相尺寸增大至30~45nm,且相数量减少,相应获得的抗拉强度为675mpa,屈服强度为580mpa,断裂伸长率为8.5%。
[0076]
对比例3
‑2[0077]
同实施例3,区别在于,超高强al
‑
zn
‑
mg
‑
cu
‑
sc
‑
zr合金板材中sc为0.05%~0.1%、zr 为0.02%~0.05%。采用后续相同热处理工艺。因二者加入量过少,不利于在热处理过程中抑制晶粒的长大,经检测,制备的超高强al
‑
zn
‑
mg
‑
cu
‑
sc
‑
zr合金板材中的al3(sc,zr)相数量极少,且晶粒尺寸增大为110μm~130μm,抗拉强度为610mpa,屈服强度为525mpa,断裂伸长率为8.0%。
[0078]
对比例3
‑3[0079]
同实施例3,区别在于,步骤(3)获得的合金板材采用常规的时效,具体时效参数为160℃
×
36h,制得al
‑
zn
‑
mg
‑
cu
‑
sc
‑
zr合金板材,经组织观察,由于时效时间长,保留不住gp
区,使得析出相中gp区都转化为η'相,晶内析出相主要为η'相与al3(sc,zr)相,且al3(sc,zr)相粒子尺寸较实施例3明显增大。制备的al
‑
zn
‑
mg
‑
cu
‑
sc
‑
zr合金板材抗拉强度590mpa,屈服强度508mpa,断后伸长率为8.8%。
[0080]
对比例3
‑4[0081]
同实施例3,区别在于,步骤(3)获得的合金板材采用双级时效,具体为 150℃
×
18h+160℃
×
18h,1级用低温、2级用高温,缩短了高温时效时间,制备的 al
‑
zn
‑
mg
‑
cu
‑
sc
‑
zr合金板材组织为晶内析出相,虽然也包括gp区、η'相和al3(sc,zr)相,但各析出相尺寸都相对更大,特别是al3(sc,zr)相尺寸较大,大于20nm,性能数据为抗拉强度650mpa,屈服强度578mpa,断后伸长率为7.9%。
[0082]
对比例3
‑5[0083]
同实施例3,区别在于,步骤(3)获得的合金板材采用的回归再时效工艺参数为: 150℃
×
18h+180℃
×
1h+160℃
×
18h,制备的al
‑
zn
‑
mg
‑
cu
‑
sc
‑
zr合金板材由于回归温度太低,大尺寸析出相回溶效果不好。组织中晶内析出相gp区、η'相和al3(sc,zr)相的尺寸略有减小,但仍然较大,存在少量晶界无析出带,性能数据为抗拉强度660mpa,屈服强度582mpa,断后伸长率为8.2%。
[0084]
对比例3
‑6[0085]
同实施例3,区别在于,步骤(2)中的初轧温度为460℃,制备的al
‑
zn
‑
mg
‑
cu
‑
sc
‑
zr合金板材抗拉强度672mpa,屈服强度594mpa,断后伸长率为7.5%,合金拉伸断口的扫描电子显微镜图像如图1所示。
[0086]
对比例3
‑7[0087]
同实施例3,区别在于,步骤(2)中的初轧温度为520℃,制备的al
‑
zn
‑
mg
‑
cu
‑
sc
‑
zr合金板材抗拉强度660mpa,屈服强度587mpa,断后伸长率为8.6%,合金拉伸断口的扫描电子显微镜图像如图3所示。
[0088]
对比图1
‑
3的三张合金拉伸断口的扫描电子显微镜图像可见,初轧温度为460℃时,合金的拉伸断口以冰糖状断口为主,沿晶断裂特征明显,同时具有少量小而浅的韧窝,合金塑性相对最低,初轧温度在490℃时,合金的拉伸断口以较深的韧窝为主,表现为韧性断裂特征合金塑性相对最佳,初轧温度升高至520℃时,合金的拉伸断口上韧窝数量减少,冰糖状断口增多,为韧脆混合型断裂,合金的塑性下降。由此可见,490℃的初轧温度选择下,对合金塑性的提高最为明显。
[0089]
对比例3
‑8[0090]
同实施例3,区别在于,步骤(2)中,第一道次压下量为35%,制备的al
‑
zn
‑
mg
‑
cu
‑
sc
‑
zr 合金板材发生了不同程度开裂,板材开裂情况如图4所示,板材发生边裂,且裂纹沿宽度方向贯穿整个板材。
[0091]
对比例3
‑9[0092]
同实施例3,区别在于,步骤(2)中,第一道次压下量为40%,制备的al
‑
zn
‑
mg
‑
cu
‑
sc
‑
zr 合金板材开裂情况如图5所示,板材头尾发生了严重开裂。
[0093]
对比例3
‑
10
[0094]
同实施例3,区别在于,步骤(2)中的总压下量分别进行60%、80%和90%总压下量的3 组轧制实验。每组具体轧制成形工艺参数如下表1所示,总压下量为60%和80%时合金
的性能对比数据如表2所示,其中,2组即为实施例3。
[0095]
表1
[0096][0097]
表2
[0098][0099]
第一组总压下量为60%的合金的强度和塑性明显低于第二组总压下量为80%的合金,第三组总压下量为90%的al
‑
zn
‑
mg
‑
cu
‑
sc
‑
zr合金板材,发现板材发生了明显的边裂。
[0100]
对比例3
‑
11
[0101]
同实施例3,区别在于,步骤(2)中的道次压下量分配方式采用以下表3中的三组方式,第1组的轧制工艺策略在前面道次尽量采用较大单道次压下量;第2组的轧制工艺策略在首道次和末道次采用较大单道次压下量;第3组的轧制工艺策略在后面道次用较大单道次压下量。通过轧制实验结果发现,第2组和第3组板材都发生了不同程度的边裂现象,在后面道次采用较大单道次压下量的轧制工艺策略将降低成材率,因此不予采用。
[0102]
因此,总压下量为80%时板材将获得最佳的强度和塑性匹配,且在分配道次压下量时需尽量在前面道次采用较大单道次压下量,同时需注意单道次压下量不超过30%,使大部分压下任务在前面道次完成,后面道次适当使用稍小的单道次压下量以调控板形。
[0103]
表3
[0104]