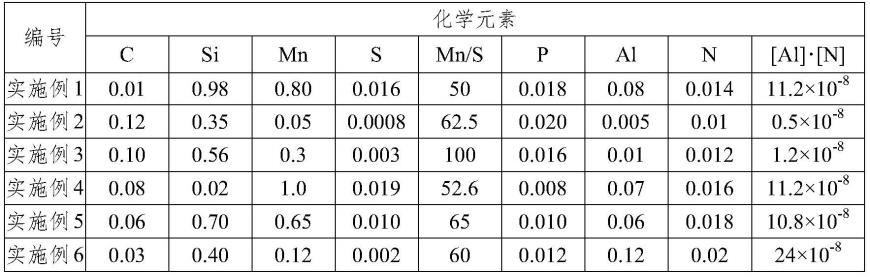
1.本发明涉及一种低碳高氮的镀锡基板、且板坯连铸不产生纵裂与角横裂纹的制造方法,属冶金技术领域。
背景技术:2.镀锡板是指两面镀有纯锡的冷轧低碳薄钢板或薄钢带,经碱洗、酸洗、电镀锡、软熔、钝化、静电涂油等处理步骤后成为表面组成及结构较为复杂的镀锡板。镀锡板将钢的强度和机械性与锡的耐蚀性、可焊性与美观性结合于一体,目前被广泛应用于罐装食品和饮料等的包装领域。随着人民生活水平的改变和出口贸易的不断增长,我国食品工业快速发展,各种罐头、果汁、八宝粥等食品的市场需求与产量也不断增长,对包装原材料镀锡板的需求也随之大幅上升,用于对于镀锡基板的轧制和烘烤需求越来越高,低碳高氮镀锡板品种也是镀锡板产品的主要发展方向
3.含碳含氮的钢种连铸过程中,从结晶器开始,直至二冷区后裂纹均有可能发生。当连铸坯在结晶器内时,在钢液凝固的过程中存在枝晶间的元素偏析,另一方面由于振痕处冷却较弱,使得生成的奥氏体晶粒粗大,并且整个坯壳凝固厚度不均匀,在坯壳薄的地方容易产生裂纹,而铁锰的氧硫化物在奥氏体晶界的析出会弱化晶界引发裂纹。当进入二冷区后,在高温区由于aln、mns等析出物在奥氏体晶界的生成,以及随着温度的降低发生的奥氏体向铁素体转变生成沿晶铁素体,均会大幅度降低连铸坯的热塑性。在此基础之上,若二次冷却存在冷却不均匀、强度不适中等不合理条件,当连铸坯受到弯曲、矫直及热应力等外应力作用后,裂纹会大量生成并扩展,形成宏观角部横裂纹。随着温度的进一步降低,在晶界生成的渗碳体也会弱化晶界,增强裂纹敏感性。
技术实现要素:4.本发明所要解决的技术问题在于提供一种可提高连铸坯质量的低碳高氮镀锡基板。
5.其所要解决的技术问题可以通过以下技术方案来实施。
6.一种低碳高氮镀锡基板,其特点为,该基板的钢种由以下质量百分比的元素组成:
7.c:0.01~0.12%,0《si≤1.0%,0《mn≤1.0%,s≤0.020%,p≤0.040%,al:0.005~0.12%,n:0.010~0.020%,且mn/s≥50,0.5
×
10-8
≤[al]
·
[n]积≤24
×
10-8
,余量为fe和不可避免的杂质。
[0008]
作为本技术方案的优选实施例,该基板的钢种由以下质量百分比的元素组成:
[0009]
c:0.03~0.10%(碳在镀锡基板中作为固溶强化元素,转炉出钢c含量0.03~0.04%,从满足产品特性和成本角度,本发明优选c≥0.03%;但碳含量超过0.10%时,钢种塑性低,最容易产生连铸角横裂纹,降低使用寿命,本发明优选c≤0.10%);
[0010]
0《si≤0.7%(本发明发现si同样能增加镀锡基板的固溶强化性能,当si≥0.7%时,固溶强化能力增加速率缓慢,如果超过1.0%则会增加材料脆性和降低耐蚀性,本发明
优选si≤0.7%);
[0011]
0《mn≤0.8%(且mn/s≥50,可同时增加钢的韧性和固溶强度,随着mn含量增加可有效提高mn/s,提高材料的临界应变、即抵抗裂纹能力增强;同时,mn加入也要考虑s含量,从成本角度和性能综合考虑,满足一定的mn/s比即可。故本发明优选0《mn≤0.8%,且mn/s≥50);
[0012]
s≤0.016%(硫为有害元素,含量越低越好,但需要精炼过程使用大量的石灰和低温控制,消耗大且冶炼周期长,通过mn/s比配合,本发明优选s≤0.016%即可满足要求);
[0013]
p≤0.020%(硫为有害元素,含量越低越好,同样需要转炉过程高温脱p,消耗大且冶炼周期长,从满足产品性能角度,本发明优选p≤0.020%即可满足要求);
[0014]
al:0.01~0.08%(aln既做脱氧剂,又起到细化晶粒作用;钢中大量细小的aln沿晶界析出,降低了奥氏体晶界强度,易在应力作用下沿晶界开裂,导致镀锡基板塑性下降,因此必须将al含量控制在0.01~0.08%范围内效果最佳);
[0015]
n:0.010~0.018%(n的主要作用是提高镀锡板连续退火和表面光轧等加工性能;本发明成分体系下,发现n含量低于0.01%时,细化晶粒和冷加工性能效果不明显;但钢中[n]含量增加,会引起连铸坯的第三脆性区变宽,尤其是n含量高于0.018%后角横裂纹敏感性增强;故本发明的n含量优选控制在0.010~0.018%的范围);
[0016]
且mn/s≥50,2
×
10-8
≤[al]
·
[n]积≤20
×
10-8
,余量为fe和不可避免的杂质。
[0017]
在镀锡板中,aln既做脱氧剂,又起到细化晶粒作用,n含量还能起到提高镀锡板连续退火和表面光轧等加工作用,通过控制[al]
·
[n]积含量,实现上述作用。本发明成分体系下,当[al]
·
[n]积大于2
×
10-8
后,细化晶粒作用效果和提高冷加工性能效果明显提升;但当[al]
·
[n]积大于20
×
10-8
后,细化晶粒作用效果和提高冷加工性能效果接近于饱和,继续增加[al]
·
[n]积含量,随着连铸过程二冷区表面温度升温和降温热振荡,aln析出相在铸坯晶界聚集,引发晶间裂纹风险。故本发明优选2
×
10-8
≤[al]
·
[n]积≤20
×
10-8
。
[0018]
本发明所要解决的另一技术问题在于提供一种可以实现板坯连铸时不产生纵裂与角横裂纹的低碳高氮镀锡基板的钢材板坯连铸制造方法。
[0019]
该方法采用如下技术方案。
[0020]
一种上述低碳高氮镀锡基板的钢材板坯连铸生产方法,其特点在于,连铸工序中,
[0021]
将连铸二冷区沿铸机长度方向,划分为0~8段,总计9个段。
[0022]
二冷区0和1号段基于拉速控制,平均拉速控制在1.0~1.8m/min,二冷水总比水量控制在1.2~1.6l/kg;
[0023]
二冷区2~8号段采用目标温度控制,目标温度650~750℃;
[0024]
二冷电磁搅拌电流为1200~2200a、搅拌频率2.0~4.0hz;中间包内钢液过热度控制在10~50℃;结晶器宽面水量2000~2800l/min;连铸结晶器水口插入深度控制在100~160mm;结晶器窄面锥度1.05~1.25。
[0025]
作为该生产方法的进一步改进,板坯连铸工序中,控制板坯断面的厚度
×
板坯宽度为(200~300)mm
×
(800~1650)mm。
[0026]
作为优选方案,二冷区0和1号段基于拉速控制,平均拉速控制在1.2~1.70m/min,比水量控制在1.3~1.5l/kg。提高拉速,水口射流的速度也会增加,结晶器的表面流速就会增加,本发明发现如果平均拉速高于1.70m/min,连铸通钢量大、铸坯卷入结晶器保护渣的
风险加剧,轧后易发生白斑缺陷,并且随着拉速提升结晶器内初生坯壳较薄,铸坯冷却不均匀,容易产生纵向裂纹、乃至漏钢。铸坯从结晶器内出来后铸坯表面温度约1000℃,直接进入二冷区0号和1号段,结晶器内纯水冷却速率大、二冷区气雾冷却速率小,因此铸坯表面温度会回升至1100℃,而aln的析出峰值温度对应于800~1100℃,为了使得铸坯表面温度快速aln析出峰值温度区间,基于拉速的水表控制能够保证铸坯表面以一定的冷却速率降温,经研究发现平均拉速控制在1.2~1.70m/min,效果最佳。进一步,如果拉速低于1.2m/min,铸坯在结晶器内停留时间过程,温降快易引发大量的mns和aln提前析出,增强了铸坯裂纹敏感性;同时考虑到炼钢连铸生产节奏控制,连铸拉速不宜过低,故本发明平均拉速优选控制在1.2~1.70m/min。二冷区0和1号段基于拉速水表控制,平均拉速控制在1.2~1.70m/min,比水量优选方案为1.3~1.5l/kg。
[0027]
作为优选方案,二冷区2~8号段采用目标温度控制,目标温度675~750℃。基于上面的表述,二冷区0和1段通过拉速水表控制,将铸坯表面温度降至800℃以下。随后进入二冷区2~8号段采用目标温度控制,优点是基于数学模型和目标温度方法,对二冷水量精确控制,保证铸坯表面温度控制在650~750℃,本发明合金体系该温度区间内铸坯塑性相对较高,最高的塑性温度区间为675~750℃,在该温度区间内铸坯矫直,铸坯不易产生裂纹,表面质量良好。
[0028]
作为优选方案,所述二冷电磁搅拌电流为1400~2000a、搅拌频率2.5~3.5hz。本发明发现电磁搅拌电流强度高于1400a后,对于改善铸坯中心质量和柱状晶枝晶效果开始显著;电磁搅拌电流强度高于2000a,结晶器液面波动开始变大、且铸坯负偏析评级增加;本发明优取二冷区电磁搅拌电流为1400~2000a、搅拌频率2.5~3.5hz。
[0029]
作为优选方案,中间包内钢液过热度控制在20~40℃。提高钢液过热度有利于防止低碳高氮镀锡板结晶器卷渣,当钢液过热度高于20℃,发现保护渣熔化效果变好、液态保护渣逐步增加,固态保护渣卷入几率降低。但当过热度高于40℃后,发现铸坯凝固凝固时间长、选分结晶充分,加剧铸坯内部质量问题;故本发明中间包内钢液的过热度优选控制在20~40℃。
[0030]
作为优选方案,结晶器宽面水量2200~2500l/min。根据低碳含氮镀锡板凝固特点,采用结晶器缓冷换方式,有利于抑制纵裂,降低坯壳凝固初始位置及其凝固速率,减弱不均匀性,抑制裂纹倾向。当结晶器宽面水量超过2500l/min,结晶器宽面两侧铜板水温差差异增加,说明传热变得不均匀。当结晶器宽面水量低于2200l/min后,结晶器出口坯壳减薄明显,前面提到的拉速1.7~1.8m/min时结晶器出口的坯壳厚度要求,结晶器漏钢风险增加。故本发明优选的结晶器宽面水量2200~2500l/min。
[0031]
作为优选方案,连铸结晶器水口插入深度控制在120~150mm。对于低碳高氮镀锡板来说,结晶器水口插入深度决定了结晶器流场和化渣条件,当结晶器水口插入深度变浅,有利于保护渣熔化、增加液态保护渣;但插入深度变得太浅的话,结晶器液位波动过大,增加保护渣卷渣几率。同时,如果结晶器水口插入太深,固态保护渣还未来得及熔化,也不利于钢液中夹杂物上浮,夹杂物和保护渣都有被卷入铸坯的风险。故本发明水口插入深度优选控制在120~150mm。
[0032]
作为优选方案,结晶器窄面锥度1.10~1.20。结晶器锥度用来补偿凝固坯壳收缩,减少结晶器/铸坯间产生气隙,增强传热均匀性。本发明应用于生产过程中发现结晶器锥度
太小,锥度低于1.1时凝固坯壳容易鼓胀,铸坯容易发生凹陷;反之若锥度大于1.20时,坯壳与结晶器铜板摩擦力开始增加,导致铸坯纵裂风险,同时铸坯与结晶器铜板接触,导致结晶器铜板磨损严重、寿命降低。故本发明结晶器窄面锥度优选控制在1.10~1.20。
[0033]
本发明的技术方案机理及其限定原因如下:
[0034]
c:0.01~0.12%,0《si≤1.0%,0《mn≤1.0%,s≤0.020%,且mn/s≥50,p≤0.040%,al:0.005~0.12%,n:0.010~0.020%,0.5
×
10-8
≤[al]
·
[n]积≤24
×
10-8
,余量为fe和不可避免的杂质。
[0035]
c:碳在镀锡基板中作为固溶强化元素,从满足产品特性和成本角度,c≥0.01%;但碳含量超过0.12%时,容易产生连铸角横裂纹,降低使用寿命。故本发明的c控制在0.01~0.12%。
[0036]
si:硅一般由原材料和合金料带入;硅含量高,能增加镀锡基板的固溶强化性能,但如果大量添加会增加材料脆性和降低耐蚀性,因此硅含量不宜过高。故本发明控制在0《si≤1.0%。
[0037]
p和s:磷和硫均为有害元素,都能生成低熔点的脆性物、导致发生裂纹倾向性大,故本发明控制在p≤0.040%,s≤0.020%。
[0038]
mn:锰一般可增加钢的韧性,通过固溶强化增加钢的强度;但由于mn与s结合形成mns,加剧铸坯角横裂纹产生,研究表明mn/s≥50能够提高材料的临界应变,有利于改善角横裂纹。故本发明控制在0《mn≤1.0%,且mn/s≥50。
[0039]
al:al作为脱氧剂,同时适量的aln可起到细化晶粒作用;钢中大量细小的aln沿晶界析出,降低了奥氏体晶界强度,易在应力作用下沿晶界开裂,导致镀锡基板塑性下降,因此必须将al含量控制在合理范围内。故本发明的al控制在0.005~0.12%的范围。
[0040]
n:n的加入有利于后续连续退火和表面光轧等加工;但钢中[n]含量增加,会引起连铸坯的第三脆性区变宽,角横裂纹敏感性增强。故本发明的n控制在0.010~0.020%的范围。
[0041]
[al]
·
[n]积直接影响铸坯角横裂的发生,根据研究和实践结果,控制为0.5
×
10-8
≤[al]
·
[n]积≤24
×
10-8
时,有利于降低角横裂的发生率。
[0042]
连铸工序中,当进入二冷区后,在高温区由于aln、mns等析出物在奥氏体晶界的生成,以及随着温度的降低发生的奥氏体向铁素体转变生成沿晶铁素体均会大幅度降低连铸坯的热塑性。总结得出该钢种在二冷区宜采用强冷工艺制度;故在所述低碳高氮镀锡基板的钢材板坯连铸工序中,二冷区0和1号段基于拉速控制,平均拉速控制在1.0~1.80m/min,比水量控制在1.2~1.6l/kg;二冷区2~8号段采用目标温度控制,目标温度650~750℃。
[0043]
对于所述板坯连铸工序中,在断面的板坯厚度
×
板坯宽度为(200~300)mm
×
(800~1650)mm时,如果平均拉速高于1.80m/min,初生坯壳较薄,铸坯冷却不均匀,容易产生纵向裂纹、乃至漏钢;考虑到炼钢连铸节奏和高拉速目标,如果平均拉速不低于1.0m/min,且不影响连铸机总体生产能力;故本发明平均拉速控制在1.0~1.80m/min。
[0044]
为了改善在连铸过程可能引起的偏析问题,本发明增加二冷区电磁搅拌工艺。如果电磁搅拌电流强度低于1200a,对于改善铸坯中心质量起不到效果;电磁搅拌电流强度高于2200a,结晶器液面波动较大、且铸坯易发生负偏析;经过大量实验表明,本发明控制电磁搅拌电流强度1200~2200a、搅拌频率2~4hz。
[0045]
如果连铸过程钢水的过热度低于10℃,钢液流动性差,容易导致结晶器水口冻钢、迫使浇注中断,且保护渣熔化效果不好;如果钢水过热度高于50℃,极易发生偏析,导致凝固时间长、选分结晶充分,加剧铸坯质量问题;故本发明中间包内钢液的过热度控制在10~50℃。
[0046]
不同于现有技术将结晶器宽面水量控制在3000~3500l/min以上,在一些优选的实施方式中,为了防止在结晶器内产生裂纹和凹陷,采用弱冷方式,可以将结晶器宽面水量控制在2000~2800l/min。
[0047]
结晶器水口插入深度过浅的话,水口流股对钢渣界面的冲击较强,增加钢液与结晶器保护渣反应几率,同时增加弯月面卷渣概率;结晶器水口插入过深的话,铸坯易产生裂纹;故本发明设计的连铸结晶器水口插入深度控制在100~160mm。
[0048]
在凝固过程中,结晶器/铸坯间产生气隙,这会使传热不均匀,导致坯壳生长厚度不均,容易形成表面凹陷或裂纹,故设置一个倒锥度以补偿凝固坯壳的收缩。若结晶器锥度太小,坯壳容易鼓胀;若锥度太大,坯壳与结晶器铜板摩擦力增加。一般应根据钢种、铸坯宽度和拉速来选择结晶器锥度。本发明设计的结晶器窄面锥度1.05~1.25。
[0049]
与现有技术相比,本发明开发的低碳高氮镀锡基板及其板坯连铸生产方法,具有连铸坯表面和中心质量好等特点,对提高连铸坯质量也有利。本技术是实现低碳高氮镀锡基板板坯连铸生产和质量保证的关键技术。
[0050]
进一步,与现有技术相比,本发明开发的低碳高氮镀锡基板板坯连铸生产方法,具有连铸坯表面和中心质量好等特点,可以充分发挥连铸生产的优势,能抑制铸坯的凹陷和裂纹产生,显著提高铸坯表面和中心质量,且能实现多炉连浇。本技术是实现低碳高氮镀锡基板板坯连铸生产和质量保证的关键技术。对采用连铸工艺流程实现生产和试验的企业开发含氮品种以及优化工艺很有推广应用价值,提高了产能,降低了生产成本,增强了企业的综合竞争力。
具体实施方式
[0051]
下面将结合具体的实施例对本发明所述的低碳高氮镀锡基板及其板坯连铸工艺做进一步的解释和说明,然而该解释和说明并不对本发明的技术方案构成不当限定。
[0052]
实施例1-6
[0053]
下表1列出了实施例1-6的低碳高氮镀锡基板中各化学元素质量百分比。
[0054]
表1.(wt%,余量为fe和其他除了p、s、n以外的不可避免的杂质)
[0055][0056]
本发明所述实施例1-6的低碳高氮镀锡基板均采用以下连铸生产工艺制得:
[0057]
在连铸工序中,二冷区0和1号段基于拉速控制、平均拉速控制在1.0~1.80m/min,比水量控制在1.2~1.6l/kg;二冷区2~8号段采用目标温度控制,目标温度650~750℃;二冷电磁搅拌电流为1200~2200a、搅拌频率2~4hz;中间包内钢液过热度控制在10~50℃;结晶器宽面水量2000~2800l/min、窄面水量450~550l/min;连铸结晶器水口插入深度控制在100~160mm;结晶器窄面锥度1.05~1.25。
[0058]
下表2列出了实施例1-6的低碳高氮镀锡基板的制造方法的具体工艺参数。
[0059]
表2.
[0060][0061]
采用低碳高氮镀锡基板及其板坯连铸方法生产的连铸板坯,经热轧和冷轧连续退后,调质度t-5ca的hr30t硬度可达67~73,高于传统的62~68;二次冷轧后,轧制方向的抗拉强度约65~75kg/mm2,高于传统的60~65kg/mm2。
[0062]
最后应说明的是:以上实施例仅用以说明本发明而并非限制本发明所描述的技术方案;因此,尽管本说明书参照上述的各个实施例对本发明已进行了详细的说明,但是,本领域的普通技术人员应当理解,仍然可以对本发明进行修改或等同替换;而一切不脱离本发明的精神和范围的技术方案及其改进,其均应涵盖在本发明的权利要求范围中。