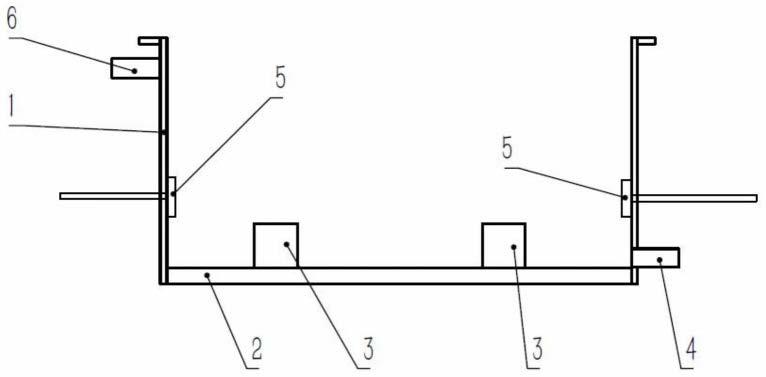
1.本发明涉及液压缸筒增材修复加工工艺技术领域,具体涉及一种促动器油缸缸筒的修复方法。
背景技术:2.促动器是fast望远镜主动反射面变形的驱动装置,共计2225台,是世界罕见的野外局地大规模设备群。促动器在野外工作,经受气温反复变化、雨水侵蚀等作用,促动器油缸缸筒易出现锈蚀、裂纹等缺陷。由于缸筒长径比较大,离两端位置较远的缺陷维修不便,通常需要返厂后做报废处理,造成一定程度的浪费。为此提出一种修复方法,作为fast望远镜促动器群维修维护的关键技术,用于在fast维护车间展开对促动器油缸的维修。目前尚无任何公开资料介绍该种修复方法。
技术实现要素:3.本发明的目的在于提供一种促动器油缸缸筒的修复方法,该方法使用高能量激光熔化金属粉末与金属母材,使缺陷处融合。
4.为实现上述目的,本发明所采用的技术方案如下:
5.一种促动器油缸缸筒的修复方法,该方法采用金属粉末熔融技术修补油缸体管壁,具体包括如下步骤:
6.(1)将待修复缸筒的缺陷处填满修复用金属粉末,并将缸筒平放并固定在修复箱内的定位工装上,使待修复的缺陷处水平朝上;
7.(2)向修复箱内填充金属粉末,直到待修复缸体最上沿刚好没入金属粉末中;
8.(3)采用覆盖耐温塑料膜等方式对修复箱进行封闭处理后,在修复箱内通入惰性气体以降低箱体内的氧含量,同时对金属粉体和油缸缸体进行预热处理;
9.(4)修复处理:将激光熔覆头伸入修复箱对准待修复部位;开启激光,对于薄壁缸筒,激光功率不宜过大,控制在2kw~4kw范围内,熔覆头的进给速度控制在10mm~20mm/min。过低的激光功率和过快的进给速度会导致粉末未熔化,缺陷处未熔合的情况,而过高的激光功率和过慢的进给速度会导致熔池过深、加工热影响区过大,变形量过大等后果。本发明的工艺方法在使用激光熔覆头对缸体表面进行熔融修复时,所需的供粉量远低于传统的激光熔融增材制造方法,实际送粉速率控制在1g~3g/min之间。送粉量不宜过大,过大的送粉量并不能有效提高修复效果,同时要避免修复区域的粉末被送粉气流吹散。
10.(5)修复后处理:停止对金属粉体的加热,使缸体在惰性气体的保护氛围下缓慢冷却。
11.步骤(1)之前,先进行修复前准备,即在油缸缸筒缺陷处采用铣削或气刨等方式将缺陷处清理干净,包括缸体待修复位置的表面漆。
12.步骤(1)中,修复用金属粉末采用与促动器油缸缸筒同材质的低碳钢气雾化球形粉末。粉末在使用前在密封容器内保存,避免氧化。
13.步骤(3)中,控制修复箱中的氧气含量降低至5000ppm以下,加热到的预热温度为200~300℃。修复时对粉末和缸筒进行预热以减小热变形和开裂现象。
14.步骤(3)之后,通过用位于油缸缸筒两端的活塞加压,逐渐由小到大调节压力使油缸缸筒内的金属粉末刚好不至于从缸筒缺陷处流出,稳定压力并使粉末保持一定的致密度;活塞的加压力能使缸筒内的粉末达到较好的致密度,此避免修复时零件管壁熔穿,同时提高修复成形质量。
15.步骤(4)中,熔覆头的运动可由手工操作,也可由多轴运动机构或关节机器人来控制。
16.步骤(5)中待缸筒冷却接近室温时取出,对缸筒进行清理,并对修复处进行打磨、镗孔等后处理,使缸筒最终尺寸和表面状态达到规定要求。
17.本发明的促动器缸筒修复工艺方法借鉴了现有的金属粉末激光熔融增材制造技术与埋弧焊接技术,但是在实施方法和技术细节上明显区别于上述方法,具体区别如下:
18.(1)采用金属粉末激光熔融增材制造方法对零件进行修复时,熔化的金属粉末来源主要是靠从激光熔覆头上配置的送粉管路提供,要求的送粉量高,为了保证粉末输送到指定位置,采用较高的送粉气压和流速,送粉量通常要控制在10g/min左右;而本发明的方法将缸筒内充入粉末并加压,主要靠激光能量将修复位置原有粉末熔化,熔覆头只提供少量的额外粉末,即约1g~3g/min的粉末,以增加修复部位的致密度,因此采用低压低流量送粉方式,也可采用从上方只依靠重力供粉的方式。
19.(2)激光能量密度大,采用金属粉末激光熔融增材制造方法对仅有几个毫米壁厚的薄壁零件进行单面成形修复时,容易出现烧穿使熔池塌陷或者造成背面成形质量低的现象,为了解决这个问题,传统的做法主要有在背面加垫板,或者采用双面成形熔融这两种方法。在背面加垫板的方法存在两个问题,一是对于不同直径的缸筒,需要制作不同曲率的垫板,造成浪费,而且垫板也要在后续的机械加工中去除。另一个问题是对于大长径比的缸筒,安装和去除垫板都是十分困难的事。倘若双面成形,需要制作专门的工具将熔覆头送入缸筒,操作不便,另外缸筒的长径比和熔覆头的尺寸也限制了双面成形熔融方法的应用。本发明的修复工艺方法可克服以上缺点:本发明的修复工艺属于单面成形修复工艺,不需要在缸筒内壁一侧进行焊接操作,通过将粉末充满缸筒并施加一定压力,位于修复位置内侧的粉末代替垫板,起到了防止烧穿提高熔体质量的作用。修复位置内侧和外侧的缸筒表面可采用机械加工进行修整。
20.(3)传统的埋弧焊将带有脱氧、造渣等成分的颗粒状焊剂铺满焊接位置,接着将电弧埋入焊剂下进行焊接。这种焊接方法由于焊剂遮挡了焊接位置,因此无法直接观察焊接位置与熔池,手工操作不便。另外,在焊接薄壁零件时,这种方法仍然存在烧穿、对侧成形质量差的问题。本发明的工艺方法由于未遮挡修复位置,因此更易于手工作业。同时,采用机器人等自动执行机构操作熔覆头运动,也可进行自动化修复作业。
21.(4)整个修复作业在封闭箱体内进行,不会造成金属粉末的浪费。另外粉床与油缸缸筒一同预热,修复作业在均匀的温度场中进行,相比激光熔融、电弧焊等工艺,本发明的零件变形量小。
22.(5)粉末和油缸筒体可在封闭箱体中一同保温、缓慢冷却,修复后的零件残余应力小。
23.(6)本发明修复工艺适用于促动器液压缸缸筒的修复,也可以用于其他普通液压缸缸筒的修复,尤其适合大长径比的管类零件修复。
附图说明
24.图1为修复所用的箱体容器示意图。
25.图2为待修复的缸筒安装示意图。
26.图3为修复过程示意图。
27.图4为缸筒修复完成后的示意图。
28.图5为检测修复部位的致密度。
具体实施方式
29.为了进一步理解本发明,以下结合实例对本发明进行描述,但实例仅为对本发明的特点和优点做进一步阐述,而不是对本发明权利要求的限制。
30.本发明提供一种促动器油缸缸筒的修复方法,该方法采用金属粉末熔融技术修补油缸体管壁。修复时采用的修复箱结构如图1所示。该修复箱包括箱体壁板1、可进行加热的底板2、安装缸筒的定位工装3、惰性气体入口4、加压活塞5和惰性气体出口6;加压活塞5共2个,相对设置安装在箱体壁板1上并能沿垂直于箱体壁板的方向移动;待修复油缸筒体安装到定位工装上后,两个加压活塞5分别位于待修复油缸筒体的两侧。
31.图2是本发明修复工艺中的准备阶段:将待修复的油缸筒体安装到定位工装上,使待修复的缺陷处朝上。在箱体内逐渐倒入金属粉末,使缸筒刚好没入粉末中。使用塑料薄膜将箱体密封。从惰性气体入口4向修复箱体中通入惰性气体(如ar),箱体中的气体经由惰性气体出口6排出,逐渐置换出箱体中原有的空气,使箱体中的氧含量逐渐降低。加热粉末,并利用加压活塞5对缸筒中的粉末施加一定压力,使之致密化。控制修复箱中的氧气含量降低至5000ppm以下,加热到的预热温度为260℃。
32.图3是本发明修复工艺中的进行阶段:移动激光熔覆头,使激光焦距接近修复位置,开启激光对修复处母材与粉末进行熔融加工。此时缸筒两端的活塞持续加压,使缸筒内的粉末保持致密度。致密化的粉末起到了垫板的作用可防止熔池塌陷。熔覆头在输送激光能量的同时也为熔池提供少量的粉末,用以提高熔接的质量。该修复过程中激光功率为2.5kw,熔覆头的进给速度为16mm/min。送粉速率2.2g/min。
33.图4是本发明修复后的缸筒缺陷示意图。缺陷处位于缸筒内侧的位置的粉末也被激光能量熔化,将缸筒缺陷修复,未熔化的致密粉末起到了垫板的作用,使熔池达到了类似双面成形工艺的效果。使工艺箱体缓慢冷却后取出促动器缸筒,后续经过机械加工处理修复好的缺陷位置,使缸筒恢复至设计尺寸。即完成本发明的促动器油缸所有修复工艺。
34.对于修复的部位主要要求致密度,致密度较高的情况下修复部位的材料实际静强度一般不低于基材强度。图5为经该工艺处理后修复部位的试样经打磨抛光后在光学显微镜下的表征图,经图像处理软件imagej分析,修复部位的致密度可达99.9%以上,无明显缺陷及穿透性孔洞,满足促动器油缸的实际使用要求。