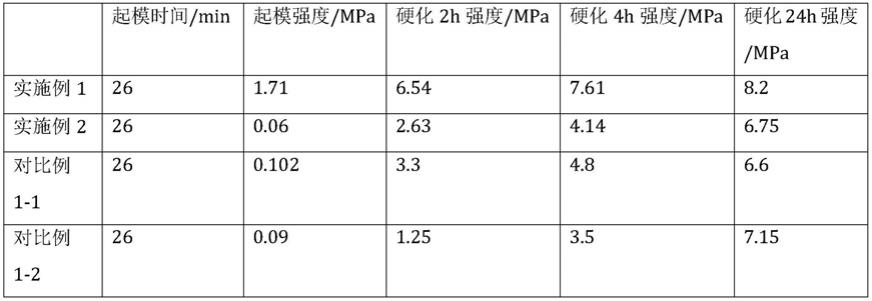
1.本发明涉及的是一种砂型铸造领域的技术,具体是一种铸造用自硬呋喃树脂快速造型方法。
背景技术:2.我国上世纪70年代开始对自硬呋喃树脂进行研制,并逐步应用于铸造生产,是目前树脂砂中应用最广泛、积累经验最多的一种造型制芯工艺。用此工艺生产的铸铁件尺寸精度可达ct8~ct10级,比粘土砂高2级;铸件表面粗糙度达ral2.5~50μm,比粘土砂高l~2级;铸件废品率可稳定在5%以下;车间单位面积的铸件产量比原粘土砂增长了1倍;铸件清砂的效率提高3倍,是目前铸造生产不可或缺的主流工艺之一。呋喃树脂砂造型既可用于机械化生产线批量生产,也可以单件小批量生产,既可生产大件,也可生产小件,是一种生产灵活的造型制芯工艺。
3.在生产中,作为粘结剂的呋喃树脂,必须配套合适的固化剂,固化剂在固化过程中起到催化作用,固化剂性能强弱对型砂可使用时间、固化速率等具有显著影响。另外,造型时气温和环境湿度在固化过程中也是关键两个影响因素,对此,应首先根据气温确定合适型号的固化剂,再根据环境湿度情况调整固化剂加入量,这样才能充分发挥呋喃树脂的粘结性能,使呋喃树脂砂型达到预期的固化效果,获得较高的型砂强度(终强度),砂型达到终强度后才能浇注。
4.砂型强度分为抗压、抗拉强度二种,其中,抗压强度检测参照jb/t 7526
‑
2008《铸造用自硬呋喃树脂》附录d(规范性附录)树脂砂常温抗拉强度的测定方法中规定的试验条件检测,试验条件:砂温20
±
2℃,室温20
±
2℃,相对湿度60
±
5%,配套固化剂为质量浓度70%的对甲苯磺酸水溶液,对应《铸造自硬呋喃树脂用磺酸固化剂》gb/t 21872
‑
2008标准中固化剂型号为gh05。标准中规范了试验条件及固化剂型号,改变任一条件,结果差异很大。但是用户使用时,通常无法控制生产车间砂温、室温、相对湿度,往往出现可使用时间长,固化速度慢,起模时间长,经常遇到24h后强度还是达不到终强度,特别是在严冬及高湿梅雨季节,出现砂型强度低、效力低、次品率高等问题。
5.面对这些问题,用户常以改用高浓度固化剂或增加固化剂加入量的方式应对,由此导致旧砂中残留硫含量增加。硫元素与mn、mg等其它元素亲和力强,产生阻碍石墨化的稳定碳化物,消耗铁液中的球化元素,形成mgs、mns等残渣,使有效的球化元素含量过低,而降低球化,形成夹渣及皮下气孔等缺陷。
6.进一步地,为了控制硫含量,防止砂型中出现硫铸件,有的厂家在低温季节选用低硫型固化剂。所谓低硫固化剂在常规固化剂中添加磷酸、乳酸等,不但价格高,磷酸中的磷会影响铸件力学性能,降低铸件的韧性和致性,使铸件开裂,增加铸件脆性等缺陷;也有企业采用电热丝烘烤,电热功率大,耗能高,烘烤时产生废气,污染环境,影响操作人员身体健康。
7.为了解决现有技术存在的上述问题,本发明由此而来。
技术实现要素:8.本发明针对现有技术存在的上述不足,提出了一种铸造用自硬呋喃树脂快速造型方法,对环境湿度进行控制,实现砂型快速硬化,并使制得的砂型具有最佳终强度。
9.本发明涉及一种铸造用自硬呋喃树脂快速造型方法,包括以下过程:
10.将铸造用砂与固化剂混合均匀,之后加入呋喃树脂,继续混合,制得混合料;根据铸件的设计,采用混合料进行造型,造型后在抽真空条件下硬化,得到成品。
11.优选地,抽真空条件下真空度不小于
‑
0.08mpa。
12.优选地,铸造用砂为1重量份,呋喃树脂为铸造用砂重量的0.8%~1.0%、固化剂为呋喃树脂重量的35%~60%。技术效果
13.与现有技术相比,本发明具有如下技术效果:
14.1)通过抽真空对硬化环境的湿度进行控制,去除了环境水分和硬化反应生成的水分,避免了水分的存在干扰砂型硬化,实现了砂型快速硬化,有利于低温季节、高湿环境等条件下的生产;
15.2)在去除水分实现砂型快速硬化的基础上,无需选用高浓度固化剂、低硫型固化剂等,亦无需增加固化剂加入量,从而保证制得的砂型具有最佳终强度;同时还能减少铸造用砂的添加量,降本增效。
具体实施方式
16.下面结合具体实施方式对本发明进行详细描述。实施例中未注明具体条件的实验方法,按照常规方法和条件进行。实施例1
17.本实施例涉及一种铸造用自硬呋喃树脂快速造型方法,包括以下步骤:
18.混合料配制步骤:取200重量份铸造用砂放入shy型树脂砂混砂机里,开动后立即加入1重量份固化剂gh07,搅拌1min,加入2重量份呋喃树脂xy86
‑
a,继续搅拌1min,得到混合料;每重量份设置为12.5g;
19.制样步骤:根据铸件的设计,采用混合料进行造型;混合料共制成五块试样;在制样过程中,将混合料倒入的芯盒中,一组五块试样,人工压实,确保用力均匀一致,然后刮平,刮平操作需要在混合料开始配制的5min内完成;制样完成后一段时间内起模,测定起模强度。
20.放置硬化步骤:将已成型的试样放置在真空干燥器中,10~15℃下,抽真空至真空度达到
‑
0.08mpa,自然硬化,得到成品。
21.对采用本实施例方法制得的成品与现有技术进行对比,对比方案如下:
22.通过swy液压强度试验机分别测定五块试样的抗压强度值,即将试样放在swy液压强度试验机的夹具中,并使夹具两端面贴紧试样,转动手轮逐渐加载测试压力,直至试样破裂,抗压强度值直接从压力表中读出;去掉最大值和最小值后,对剩下的三个强度值取平均值,作为试样平均强度值。三个强度值中任何一个强度值与试样平均强度值相差不得超过10%,如果超过,重新制作试样。实施例2
23.实施例2试样制造:相对于实施例1,本实施例将呋喃树脂含量调整为实施例1的80%,固化剂含量调整为实施例1的80%。
24.对比例1
‑
1试样制造:混合料配制步骤与制样步骤同实施例1,放置硬化步骤在10~15℃、常湿、室内进行。
25.对比例1
‑
2试样制造:混合料配制步骤与制样步骤同实施例1,放置硬化步骤在10~15℃、密闭、干燥容器中进行。
26.对比结果如下表1所示。
27.表1抗压强度变化对比表
28.根据表1可知,在原料及其配比相同的情况下,实施例1具有较好的起模强度,更重要的是4h抗压强度达到对比例1
‑
1的24h抗压强度(已满足现有产品生产的需要);故采用本发明实施例的制备方法可加快生产节凑,提高生产效率;
29.另一方面,实施例2将呋喃树脂含量调整为现有技术(对比例1
‑
1)的80%,以及将固化剂含量调整为现有技术(对比例1
‑
1)的80%,在抽真空条件下,其硬化24h强度也略高于对比例1
‑
1硬化24h强度,因此,在保持现有生产效率的条件下,能够减少20%左右呋喃树脂及固化剂的使用成本,从而减少有机废气的排放,降低固化剂引入的硫元素的残留量,增加旧砂循环利用率,节约用砂使用成本,减少旧砂废弃率10%左右,符合绿色铸造、节能减排发展的要求。实施例3
30.实施例3试样制造:相对于实施例1,本实施例将固化剂含量调整为实施例1的35%。
31.对比例3
‑
1试样制造:相对于实施例1,固化剂用量减少50%,放置硬化步骤在10~15℃、常湿室内进行。
32.对比例3
‑
2试样制造:相对于实施例1,固化剂用量减少50%,放置硬化步骤在10~15℃、密闭、干燥容器中进行。
33.对比结果如下表2所示。
34.表2抗压强度变化对比表
35.根据表2可知,在显著降低实施例3的固化剂加入量后,实施例3的4h抗压强度仍能够达到对比3
‑
1的24h抗压强度,故按照本发明实施例的制备方法能够减少固化剂加入量,降低成本,减少旧砂中硫残留,加快硬化速度,提高生产效率。实施例4
36.实施例4试样制造:相对于实施例1,将固化剂型号调整为gh06,固化剂用量减少50%。
37.对比例4
‑
1试样制造:相对于实施例1,固化剂用量减少50%,放置硬化步骤在10~15℃、常湿室内进行。
38.对比例4
‑
2试样制造:相对于实施例1,固化剂用量减少50%,放置硬化步骤在10~15℃、密闭、干燥容器中进行。
39.对比结果如下表3所示。
40.表3抗压强度变化对比表表3抗压强度变化对比表
41.根据表3可知,在10~15℃条件下,实施例4固化剂的型号调整为15~20℃时使用的gh06(相对于10~15℃时使用的固化剂gh07浓度要低),4h抗压强度达到对比例4
‑
1的24h抗压强度;故本发明实施例在气温较低的季节,即使不采用高浓度固化剂,亦能快速硬化。
42.需要强调的是:以上仅是本发明的较佳实施例而已,并非对本发明作任何形式上的限制,凡是依据本发明的技术实质对以上实施例所作的任何简单修改、等同变化与修饰,均仍属于本发明技术方案的范围内。