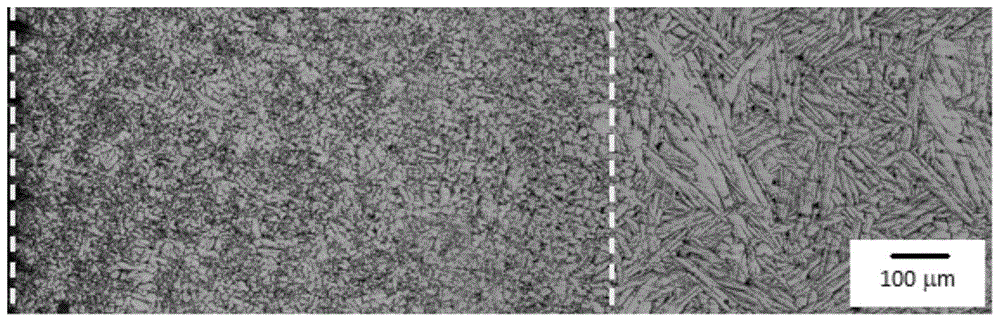
本发明涉及粉末冶金
技术领域:
,具体涉及一种具有碳化钛增强钛基复合材料硬化层的钛制品及制备方法。
背景技术:
:钛及钛合金因其轻质、高强、耐蚀、耐热、无磁无毒等一系列优势而广泛应用于航空航天、国防军工以及生物医疗等领域。然而,钛较差的硬度和耐磨性影响其在高摩擦环境下的应用。因此钛制品的表面硬化技术成为提高其硬度并降低摩擦系数的有效方式。目前普遍使用的技术包括化学气相沉积法(cvd)、物理气相沉积法(pvd)、激光表面处理法、热氧化法、离子氮化法和固态扩散法等几种表面改性技术,其目的是在钛的表面形成坚硬的耐磨损层。应用以上技术能形成含有氮化物、碳化物、硼化物和氧化物的坚硬的表面层和/或富含氮、碳、硼、氧的次表面层,但这些表面层和次表面层都有一些自身的不足之处。例如,用cvd和pvd技术得到的涂层厚度较薄(<250μm);用热氧化法和离子氮化以及注入氧原子和氮原子后得到的表面层的最大硬度较低;激光表面处理基础上的方法工艺复杂,成本高等。因此,寻求新的表面硬化技术对拓展钛合金在高摩擦环境下的应用极具意义。技术实现要素:本发明的主要目的在于提供一种具有碳化钛增强钛基复合材料硬化层的钛制品及制备方法,该制备方法将近终成形的粉末压坯浸泡于碳质粉末的分散液中,通过毛细作用使得碳质粉末渗入粉末压坯中一定厚度,可达到厘米尺度,随后通过高温烧结制备具有碳化钛增强钛基复合材料涂层的钛制品,以突破传统的钛表面硬化技术硬质涂层厚度薄的技术问题。为了实现上述目的,根据本发明的第一方面,提供了一种具有碳化钛增强钛基复合材料硬化层的钛制品的制备方法。该制备方法包括以下步骤:s1:压坯制备,选取钛原料并采用近终成形技术制得粉末压坯;s2:渗碳处理,将所述粉末压坯浸泡于含碳质粉末的分散液中一定时间后取出并静置;或者将含碳质粉末的分散液涂抹于所述粉末压坯表面,随后静置;s3:将步骤s2得到的渗碳后的粉末压坯进行高温烧结,得到钛制品。进一步的,所述钛原料的粒度为10~60mm。在本发明中,钛原料可以为预合金粉末、混合元素钛或钛合金粉末,其中混合元素钛或钛合金粉末可以为ta、tb、tc系列的各种钛合金牌号。进一步的,步骤s1中,所述近终成形技术为模压、冷等静压和注射成形工艺中的任一种。进一步的,步骤s1中,所述粉末压坯的相对密度为50~80%。过低的压坯密度强度过低,不利于后续操作,也可能造成烧结过程出现开裂;过高的压坯密度会产生迷宫密封效应,阻碍含碳分散液的向坯体的渗入,使得硬质涂层厚度过薄。进一步的,步骤s2中,所述含碳质粉末为微细碳质粉末;所述微细碳质粉末包括炭黑粉、石墨粉、石墨烯和碳纳米管。进一步的,步骤s2中,所述分散液的液体介质为有机溶剂;所述有机溶剂为水、酒精和丙酮中的至少一种。进一步的,所述分散液中所述含碳质粉末的重量为0.5~20%。碳质粉末过低时,硬质涂层中的硬质相比例过低,表面硬化作用较弱;当碳质粉末含量过高时,分散液分散效果急剧下降,会造成局部硬质相的团聚,影响硬质涂层的均匀性。进一步的,步骤s2中,浸泡时间为1~5min;静置时间为2~3h。浸泡时间是控制硬质涂层厚度的重要因素,时间短则硬质涂层较薄,时间长则涂层厚度较厚。进一步的,所述高温烧结采用气氛烧结或真空烧结工艺;烧结温度为1200~1350℃,烧结时间为2~5h。为了实现上述目的,根据本发明的第二方面,提供了一种具有碳化钛增强钛基复合材料硬化层的钛制品。该钛制品采用上述的制备方法制备得到,其中:所述钛制品的硬质层与异性钛制品一体制造,并且所述硬质层的厚度为30~1000μm。本发明中将粉末冶金技术与硬质涂层制造技术相结合,实现了短流程制备具有碳化钛(tic)增强钛基复合材料硬化层的钛制品。同时,实现了将硬质涂层与基体合金的短流程一体化成形制备,显著降低了制造成本。利用粉末压坯的多孔特点,通过液体的毛细渗透作用,将微细碳质粉末运送入钛粉颗粒间,在后续的高温烧结过程中获得致密钛合金产品同时原位生成tic增强颗粒,实现了厚度可控,且可达30~1000μm的硬质涂层。附图说明通过阅读下文优选实施方式的详细描述,各种其他的优点和益处对于本领域普通技术人员将变得清楚明了。附图仅用于示出优选实施方式的目的,而并不认为是对本发明的限制。而且在整个附图中,用相同的参考符号表示相同的部件。在附图中:图1为本发明实施例中制备得到的具有tic硬质层的钛合金制件的光学显微镜形貌。图中:图片的左侧区域表示为硬质层;图片的右侧区域表示为制件基体。具体实施方式下面将参照附图更详细地描述本公开的示例性实施方式。虽然附图中显示了本公开的示例性实施方式,然而应当理解,可以以各种形式实现本公开而不应被这里阐述的实施方式所限制。相反,提供这些实施方式是为了能够更透彻地理解本公开,并且能够将本公开的范围完整的传达给本领域的技术人员。本发明中的制备方法将粉末近终成形技术与硬质涂层制备技术相结合,利用粉末压坯的多孔特点,通过液体的毛细渗透作用,将微细碳质粉末运送入钛粉颗粒间,在后续的高温烧结过程中获得致密钛合金产品同时原位生成tic增强颗粒,实现了一定厚度的硬质涂层。而且,采用上述的的制备方法制得的具有tic增强钛基复合材料硬化层的钛制品,实现了硬质层与异性钛制品实现一体制造,且硬质层的厚度可控,可达30~1000μm。以下将通过具体实施例对本发明中具有tic增强钛基复合材料硬化层的钛制品的制备方法进行详细说明。实施例1:具有tic增强的硬质涂层的冷压纯钛齿轮的制备s1:原料准备,选取-325目的氢化脱氢钛粉,与3%硬质酸润滑剂混合均匀。s2:冷压成形,将上述原料在钢制模具中冷压成形齿轮产品。压制压力为500mpa。s3:渗碳处理,将上述齿轮压坯浸泡于石墨粉悬浊液中1min后取出静置2h。其中,石墨固相含量为3wt.%。s4:真空烧结,将上述压坯真空烧结致密化,最高温度为1200℃,保温时间为2h。实施例2:具有tic增强的硬质涂层的tc4微型注射成形产品的制备s1:原料准备,采用tc4球形预合金粉末,粉末粒度小于20μm。s2:压坯制备,将上述粉末与粘结剂进行混炼,经过注射成形、脱脂后获得近终成形粉末坯。s3:渗碳处理,将石墨烯分散液涂抹于粉末压坯表面,静置2h。其中,分散液中石墨烯固相含量为1wt.%。s4:真空烧结,将注射成形坯料进行真空烧结致密化,温度为1250℃,烧结时间为2h。实施例3:具有tic增强的硬质涂层的tc4无缝管的制备s1:原料准备,采用tc4混合元素氢化脱氢粉末,粉末粒度小于50μm。s2:压坯制备,将上述粉末装入带芯棒的橡胶模具中冷等静压成形,压力200mpa。s3:渗碳处理,将管件压坯浸泡于炭黑粉悬浊液中5min,静置2h。其中,分散液中石墨固相含量为5wt.%。s4:真空烧结,将冷等静压坯料进行真空烧结致密化,温度为1250℃,烧结时间为2h。以下将通过对比实验对本发明中制备方法的优势进行详细说明。一、实验对象对比实施例1:在1000℃温度下,将致密ti-6al-4v合金在氮气或氨气气氛下进行氮化得到硬质涂层。对比实施例2:在1000℃对致密ti-6al-4v合金进行固体渗硼处理得到硬质涂层。二、实验方法采用现有技术中常规的检测方法对实施例1-3以及对比实施例1-2中制备得到的钛合金产品中硬质涂层的厚度进行测定。三、实验结果对实施例1-3以及对比实施例1-2的实验结果进行汇总,详见表1。表1组别涂层厚度/μm涂层硬度/hv实施例1180±20550±30实施例230±10450±20实施例31000±50780±20对比实施例1150±20950±30对比实施例280±20850±30由表1可知,本发明中采用粉末压坯进行硬质相的复合,能够显著增加涂层厚度,实验结果表明最大涂层厚度可达1000μm,最小涂层厚度可达30μm。传统的化学气相沉积法(cvd)、物理气相沉积法(pvd)、激光表面处理等工艺最大涂层厚度为100~200μm,该工艺能够能够显著增加最大涂层厚度约4~5倍。同时,通过调整碳质悬浮液浓度、浸泡时间等工艺参数能够实现涂层厚度和涂层中硬质相比例(即涂层硬度)可控。虽然涂层硬度范围为450~780hv,略低于传统涂层硬度值或基本相当,完全达到使用需求。本发明更具优势的是将粉末冶金技术和硬质涂层合成进行一体化集成,不仅降低了硬质涂层涂覆难度和生产加工成本。同时该发明能够解决一些具有硬质层的复杂形状异形件的整体制造,结合粉末注射成形、粉末冷压烧结等粉末冶金工艺能够产生极大的应用和市场价值。以上所述,仅为本发明较佳的具体实施方式,但本发明的保护范围并不局限于此,任何熟悉本
技术领域:
的技术人员在本发明揭露的技术范围内,可轻易想到的变化或替换,都应涵盖在本发明的保护范围之内。因此,本发明的保护范围应以所述权利要求的保护范围为准。当前第1页12