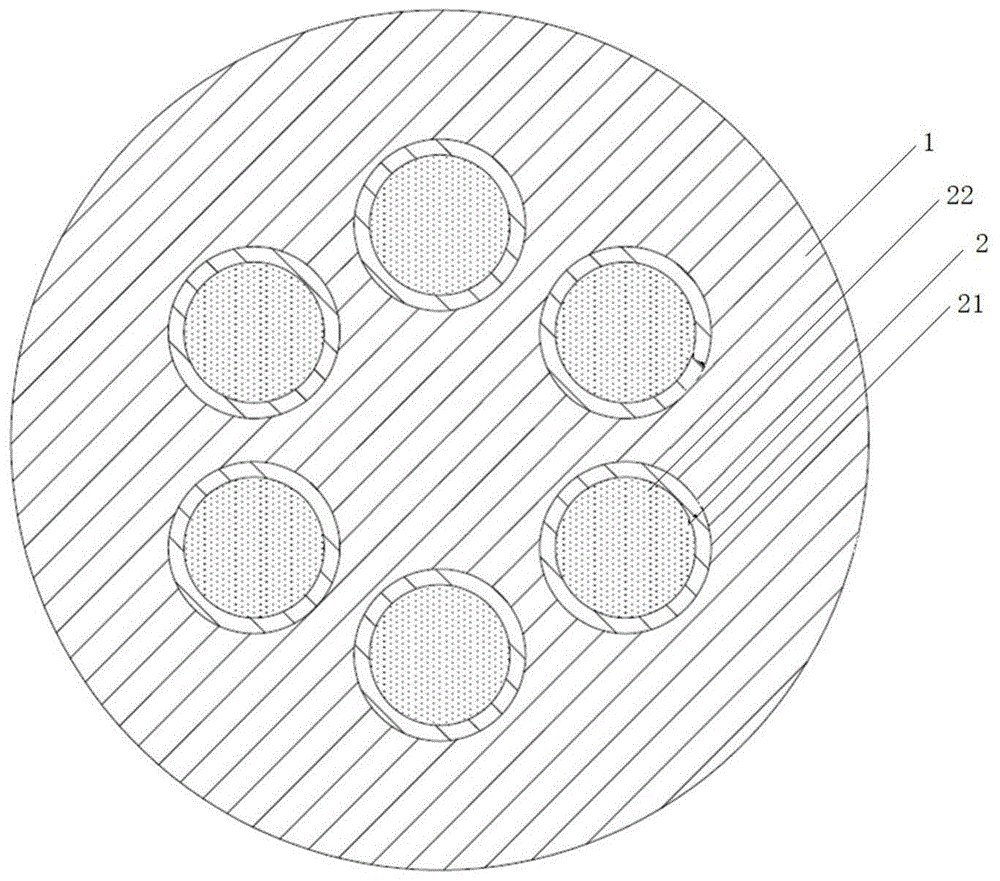
本发明涉及高氮钢的冶炼
技术领域:
,尤其涉及一种加压电渣重熔用高氮钢自耗电极及其制备方法。
背景技术:
:高氮钢是指材料中的实际氮含量超过了常压下制备材料所能达到极限值的钢。氮作为钢中的间隙原子元素,通过与其它合金元素(锰、铬、钼、钒、铌和钛等)的协同作用,能改善钢的多种性能,例如氮可以有效提高钢的强度、硬度和耐腐蚀性能,尤其是提高钢的耐晶界腐蚀性。由于高氮钢具有优异的性能和可观的应用前景,目前,实现高氮钢生产过程中氮含量分布均匀,实现高氮钢中氮含量的精准控制,研究低成本大批量稳定地制备高氮钢的设备和工艺技术已成为该领域最前沿的研究方向之一。加压电渣重熔工艺能够有效避免高氮钢生产过程中因氮含量较高引起的疏松、缩孔等问题,同时能有效的提高氮在钢中的均匀度,减少氮偏析程度。该工艺不仅仅能实现快速凝固,同时可以显著降低钢中的夹杂物,改善其在组织中的分布,从而实现提高材料的强度、韧性和耐腐蚀性。加压电渣重熔工艺通过控制自耗电极的熔化速率等手段来改善重熔钢锭的凝固组织和偏析分布,这一优点是其他特种冶金技术所无法实现的,因此加压电渣重熔工艺是目前商业上生产高氮钢的有效方法。氮合金化技术是加压电渣重熔的核心技术之一。传统工艺中,添加剂多在重熔过程中分多个批次依次人工加入,例如德国研制的加压电渣炉上设有合金添加装置,可以在保持炉内压力条件下,向渣中添加氮化合金颗粒,如si3n4(25-30%n)、fecrn(8-10%n)和crn(4-12%n)等以实现高氮钢的生产,而自耗电极采用常规方法制备。其中采用si3n4进行氮合金化,容易使钢中si含量超标,在高压下熔炼,在渣中添加氮化物时也会因形成氮气而使渣沸腾,扰乱了熔炼过程,使重熔钢锭中氮含量分布不均匀,为此就需要再次重熔改善氮的均匀性。另一种添加剂加入方法是在自耗电极母材周围焊接多个合金管,合金管内装入合金添加剂和脱氧剂,这种方法易造成重熔钢锭心部到边部成分不均匀,并且焊接部位造成钢液增氧,及焊接造成的其他成分污染;同时,自耗电极制备过程复杂且工作量大,电极直径增加也使电极与结晶器之间的间隙减小影响安全操作,难以实现工业化生产。因此,亟需一种加压电渣重熔用高氮钢自耗电极及其制备方法。技术实现要素:(一)要解决的技术问题鉴于上述技术中存在的问题,本发明至少从一定程度上进行解决。为此,本发明的一个目的在于提出了一种加压电渣重熔高氮钢用自耗电极,避免了电渣重熔过程中氮化合金的渗漏,改善了重熔钢锭心部到边部的成分分布。本发明的第二个目的在于提出了一种加压电渣重熔高氮钢用自耗电极的制备方法,避免了焊接带来钢液增氧的发生,并且制备工艺简单、成本低。(二)技术方案为了达到上述目的,本发明一方面提供一种加压电渣重熔高氮钢用自耗电极,包括自耗电极母材和至少两个嵌入自耗电极母材内部的包芯管;包芯管包括铁管和填充于铁管内的氮化合金,包芯管的第一端位于自耗电极母材插入渣池的一端,包芯管的第二端位于自耗电极母材远离渣池的一端。进一步地,自耗电极母材为圆柱状,铁管为圆筒状;铁管的轴向平行于自耗电极母材的轴向进行设置,铁管在距离自耗电极母材中心轴预定距离的圆周上均匀分布。进一步地,预定距离为自耗电极母材直径的1/5~1/3,铁管的直径为自耗电极母材直径的1/6~1/5。此外,本发明还提供一种加压电渣重熔高氮钢用自耗电极的制备方法,包括:s1、根据设计钢种的化学成分,确定自耗电极母材的氮含量,根据设计钢种的目标重量、设计钢种的氮含量和自耗电极母材的氮含量,确定包芯管中氮化合金的用量并准备氮化合金;s2、将氮化合金填充进预定数量的铁管内形成包芯管,每一根包芯管的直径和质量均相同,之后将包芯管竖直固定在铸锭模内,包芯管的下端与铸锭模的底部接触,包芯管的上端与铸锭模的顶部齐平;s3、根据设计钢种的化学成分、设计钢种的目标重量、氮化合金的重量以及铁管的重量,确定冶炼自耗电极母材所需工业纯铁、金属铬、金属锰、金属镍、金属钼和工业硅的用量并进行准备;s4、将工业纯铁、金属铬、金属锰、金属镍、金属钼和工业硅置于炉内进行冶炼,待炉内炉料澄清后保持熔炼温度,并向炉内充入氮气进行氮合金化,冶炼出自耗电极母材钢液;s5、将钢液从铸锭模顶部进行浇铸,浇铸结束后经冷却泄压获得铸锭,对铸锭的表面进行修整,获得自耗电极。可选地,氮化合金为fecrn和crn中的一种或两种。可选地,s2中,将氮化合金填充进预定数量的铁管内形成包芯管,包括:将粒径为3~5mm的氮化合金颗粒填充进预定数量的铁管内并压实,形成包芯管。可选地,s2中,将包芯管竖直固定在铸锭模内,包括:在铸锭模的顶端开口处安装有包芯管固定盘,包芯管固定盘上开设有包芯管安装孔和钢液浇注孔,包芯管通过包芯管安装孔竖直固定在铸锭模内。可选地,s4中,将工业纯铁、金属铬、金属锰、金属镍、金属钼和工业硅置于氮气保护的真空感应炉内进行冶炼。可选地,s5中,控制感应炉内氮气压力小于0.1mpa,出钢温度为1510℃~1530℃,将钢液从铸锭模顶部进行浇铸。可选地,s4中,向炉内充入氮气进行氮合金化后,还包括:依次向炉内添加脱氧剂和脱硫剂,其中脱氧剂包括镍镁合金,脱硫剂包括电解铝。(三)有益效果本发明的有益效果是:1、本发明实施例提出的加压电渣重熔高氮钢用自耗电极,通过采用铁管紧密包裹氮化合金,避免了电渣重熔过程中氮化合金料的渗漏,通过在自耗电极母材内部嵌入包芯管,避免了在自耗电极周围焊接合金管带来钢液增氧的发生,并改善了重熔钢锭心部到边部的成分分布,同时较自耗电极母材外焊接合金管的方式而言,将包芯管置于自耗电极内部大大增加了自耗电极母材的外径尺寸,在同等条件下提高了生产效率。2、本发明实施例提出的加压电渣重熔高氮钢用自耗电极的制备方法中,使用氮气保护的真空感应炉冶炼自耗电极母材,起到了渗氮合金化的作用,可以精确控制母材中的氮含量。3、加压电渣炉充入氮气加压冶炼,既保证了冶炼压力又增大了钢液中的氮溶解度,又保证了目标钢种的氮含量。附图说明本发明借助于以下附图进行描述:图1为根据本发明一个实施例的插入6根包芯管时的自耗电极横截面示意图;图2为根据本发明一个实施例的包芯管横截面示意图;图3为根据本发明一个实施例的包芯管固定盘的俯视图;图4为根据本发明实施例1的插入2根包芯管时的自耗电极横截面示意图;图5为根据本发明实施例1的电渣重熔铸锭中部的板片选取示意图;图6为根据本发明实施例2的插入3根包芯管时的自耗电极横截面示意图;图7为根据本发明实施例2的自耗电极横截面实际形貌图;图8为根据本发明实施例2的电渣重熔铸锭中部的板片选取示意图。【附图标记说明】1:自耗电极母材;2:包芯管;21:铁管;22:氮化合金;3:包芯管固定盘;31:包芯管安装孔;32:钢液浇注孔。具体实施方式为了更好的解释本发明,以便于理解,下面结合附图,通过具体实施方式,对本发明作详细描述。本发明实施例提出的加压电渣重熔高氮钢用自耗电极,如图1所示,包括自耗电极母材1和至少两个嵌入自耗电极母材内部的包芯管2,如图2所示,包芯管2包括铁管21和填充于铁管21内的氮化合金22,包芯管2的第一端位于自耗电极母材1插入渣池的一端,包芯管2的第二端位于自耗电极母材1远离渣池的一端。通过采用铁管紧密包裹氮化合金,避免了电渣重熔过程中氮化合金料的渗漏,通过在自耗电极母材内部嵌入包芯管,避免了在自耗电极周围焊接合金管带来钢液增氧的发生,并改善了重熔钢锭心部到边部的成分分布,同时较自耗电极母材外焊接合金管的方式而言,将包芯管置于自耗电极内部大大增加了自耗电极母材的外径尺寸,在同等条件下提高了生产效率。进一步地,自耗电极母材1为圆柱状,铁管21为圆筒状;铁管21的轴向平行于自耗电极母材1的轴向进行设置,铁管21在距离自耗电极母材1中心轴预定距离的圆周上均匀分布。保证了电渣重熔过程中,氮化合金熔化后可以在金属熔池内均匀分布。进一步地,预定距离为自耗电极母材1直径的1/5~1/3,铁管21的直径为自耗电极母材1直径的1/6~1/5。优选地,预定距离为自耗电极母材直径的1/4。保证了电渣重熔过程中,氮化合金熔化后可以在金属熔池内均匀分布。本发明实施例还提出一种加压电渣重熔高氮钢用自耗电极的制备方法,包括以下步骤:步骤s1、根据设计钢种的化学成分,确定自耗电极母材的氮含量,根据设计钢种的目标重量、设计钢种的氮含量和自耗电极母材的氮含量,确定包芯管中氮化合金的用量并准备氮化合金。具体地,根据设计钢种的化学成分,确定自耗电极母材的氮含量,包括:根据设计钢种的化学成分,确定出设计钢种在常压下的极限氮含量,根据设计钢种在常压下的极限氮含量和经验修正值,确定自耗电极母材的氮含量;经验修正值为0.7~0.8。其中,设计钢种在常压下的极限氮含量的计算公式为:式中,为氮压力,p0为标准大气压力,t为出钢温度。具体地,氮化合金为fecrn和crn中的一种或两种,优选地,氮化合金为crn,crn中氮的收得率按80~85%计算。步骤s2、将第一份氮化合金填充进预定数量的铁管内形成包芯管,每一根包芯管的直径和质量均相同,之后将包芯管竖直固定在铸锭模内,包芯管的下端与铸锭模的底部接触,包芯管的上端与铸锭模的顶部齐平。具体地,将氮化合金填充进预定数量的铁管内形成包芯管,包括:将粒径为3~5mm的氮化合金颗粒填充进预定数量的铁管内并压实,形成包芯管,其中包芯铁管外径为d,厚度为δ。具体地,将包芯管竖直固定在铸锭模内,包括:在铸锭模的顶端开口处安装有包芯管固定盘3,如图3所示,包芯管固定盘3上开设有包芯管安装孔31和钢液浇注孔32,包芯管2通过包芯管安装孔31竖直固定在铸锭模内。进一步地,包芯管固定盘3为圆盘状,材质为碳钢,厚度为h,直径为d,钢液浇注孔32位于包芯管固定盘3的中心,钢液浇注孔32的直径为d孔,包芯管安装孔31在距离包芯管固定盘3圆心1/4d的圆周上均匀分布,包芯管安装孔31的直径为d。进一步地,d孔=1/4d,d=1/6d~1/5d。进一步地,选用直径为db(db<d)的组合式铸锭模。需要说明的是,并不是所有的包芯管安装孔都要安插包芯管,安插的数量要根据实验所需要的包芯管的数量决定。步骤s3、根据设计钢种的化学成分、设计钢种的目标重量、氮化合金的重量以及铁管的重量,确定冶炼自耗电极母材所需工业纯铁、金属铬、金属锰、金属镍、金属钼和工业硅的用量并进行准备。步骤s4、将工业纯铁、金属铬、金属锰、金属镍、金属钼和工业硅置于炉内进行冶炼,待炉内炉料澄清后保持熔炼温度,并向炉内充入氮气进行氮合金化,冶炼出自耗电极母材钢液。优选地,将工业纯铁、金属铬、金属锰、金属镍、金属钼和工业硅置于氮气保护的真空感应炉内进行冶炼。优选地,向炉内充入氮气进行氮合金化后,还包括:依次向炉内添加脱氧剂和脱硫剂,其中脱氧剂包括镍镁合金,脱硫机包括电解铝。步骤s5、将钢液从铸锭模顶部进行浇铸,浇铸结束后经冷却泄压获得铸锭,对铸锭的表面进行修整,获得自耗电极。具体地,控制感应炉内氮气压力小于0.1mpa,出钢温度为1510℃~1530℃,将钢液从铸锭模顶部进行浇铸。具体地,对铸锭的表面进行修整,包括:切除铸锭头尾缺陷,打磨铸锭表面至光滑。如图1所示,是插入6根包芯管时的自耗电极横截面效果图。下面具体来描述采用本发明实施例提供的加压电渣重熔高氮钢用自耗电极的制备方法。实施例1制备250kg设计钢种18cr20mn2ni1mo0.3si1n,其成分(wt.%)见表1。表1设计钢种18cr20mn2ni1mo0.3si1n成分元素种类cmncrsinimonpsfe成分范围≤0.0518~2216.5~19.8≤0.3≤2.1≤10.95~1.05≤0.03≤0.01余量目标成分0.0520180.32110.030.01余量步骤s1、根据设计钢种的化学成分,确定出设计钢种18cr20mn2ni1mo0.3si1n在1520℃、0.07mpa氮分压下的极限氮含量[%n]=0.988,根据设计钢种在此压力下的极限氮含量和经验修正值,确定自耗电极母材的氮含量为0.988%×0.7=0.642%。根据设计钢种的目标重量、设计钢种的氮含量、自耗电极母材的氮含量和氮化铬中氮的收得率,得到氮化合金提供的氮含量为(1-0.642)/0.85×100%=0.421%,确定包芯管中氮化铬的用量为9347g并准备氮化合金。步骤s2、将粒径为3mm的氮化铬颗粒填充进2个铁管内并压实,形成包芯管,每一根包芯管的直径和质量均相同,其中包芯铁管外径d=36mm,厚度为δ=2mm。选用d=210mm,h=15mm的包芯管固定盘和db<d的组合式铸锭模,将包芯管固定盘安装在铸锭模的顶端开口处,包芯管固定盘上开设有包芯管安装孔和钢液浇注孔,钢液浇注孔位于包芯管固定盘的中心,包芯管安装孔在距离包芯管固定盘圆心1/4d的圆周上均匀分布,包芯管通过包芯管安装孔竖直固定在铸锭模内,包芯管的下端与铸锭模的底部接触,包芯管的上端与铸锭模的顶部齐平。步骤s3、根据设计钢种的化学成分、设计钢种的目标重量、氮化合金的重量以及铁管的重量(2根铁管提供3272g金属铁),确定冶炼自耗电极母材所需工业纯铁、金属铬、金属锰、金属镍、金属钼和工业硅的用量并进行准备,见表3。表2冶炼原料主要成分/wt%表3制备自耗电极所用原料的重量步骤s4、将工业纯铁、金属铬、金属锰、金属镍、金属钼和工业硅置于感应炉的坩埚内进行冶炼,按照0.8kg/t钢另加200gal置于加料仓中,添加250g含镁20%的镍镁合金置于加料仓中;待感应炉内炉料澄清后保持熔炼温度1520℃,并向炉内充入压力为0.07mpa的氮气进行氮合金化,然后依次添加电解铝、镍镁合金进行深脱氧和深脱硫处理,冶炼出自耗电极母材钢液。步骤s5、控制感应炉内氮气压力为0.07mpa,出钢温度为1520℃,将钢液通过浇注孔进行浇铸,浇铸结束后经冷却泄压获得铸锭,切除头尾缺陷,打磨铸锭表面至光滑,得到横截面如图4所示的自耗电极。对获得的自耗电极进行加压电渣重熔,包括以下步骤:步骤a1、将自耗电极焊接到假电极上,将假电极装卡在电极卡头上。步骤a2、实验选用的熔渣组元比例为caf2:cao:al2o3=6:2:2,重量为17.5kg。将熔渣在800℃下烘烤7小时,充分去除熔渣中的水分。步骤a3、将引弧环、550g引弧屑、底铁放在自耗电极下部的加压电渣炉底水板上,使自耗电极、引弧屑、底铁及底水箱紧密接触,确保通电后有电流通过。步骤a4、将熔渣加入到加压电渣炉结晶器内,密封熔炼室。开启供水系统,同时将纯度≥99.999%的氮气以13l/min的速度向熔炼室通入10min,排出熔炼室内的空气,接通电源后进行起弧化渣,在电压为35v,电流为1700a的供电参数下化渣17min,确保化渣成功。步骤a5、化渣结束后,将氮气压力逐步提升至1mpa,同时启用水气自动调节确保结晶器内外壁压力平衡。将电压调节至45v,电流调节至2600a,加压电渣熔炼开始,并将电压、电流维持在相对稳定的状态(电流波动±<2%,电压波动±<0.4%),熔速控制在150kg/h。步骤a6、熔炼后期采用降低电流的方式进行补缩,确保补缩充分,使钢锭上部端面平整。步骤a7、补缩阶段完成后,关闭电源,降低低水箱,同时分阶段降低氮气压力至常压,取出电渣钢锭。实验得到的电渣锭组织致密无氮气孔缺陷,其纵向化学成分如表4所示。表4成品钢的化学成分(纵向)(wt%)成分csimncrnimonspofe上部0.0460.2619.4217.291.970.931.0250.00450.00530.0031余量中部0.0450.2619.2917.141.970.931.0180.00390.00480.0029余量下部0.0420.2418.9517.031.950.911.0070.00380.00440.0028余量图5为所获得的电渣重熔铸锭中部的板片,随机选取不同位置进行成分测定,测定结果在表9中给出。表5成品钢的化学成分(横向)(wt%)成分csimncrnimonspofe10.0450.2619.1817.151.970.931.0170.00380.00470.0029余量20.0450.2619.1617.201.960.941.0220.00370.00460.0028余量30.0440.2519.2017.141.960.941.0150.00380.00460.0029余量40.0450.2519.1017.191.970.931.0170.00380.00470.0029余量50.0450.2619.1717.121.960.931.0230.00370.00470.0028余量60.0440.2519.2317.161.960.931.0190.00380.00460.0028余量70.0440.2519.2517.151.970.941.0180.00390.00460.0029余量80.0450.2619.1917.201.970.941.0130.00370.00470.0028余量上表中的氮含量结果表明,本实施例所得到的高氮钢电渣锭氮含量达到目标钢种18cr20mn2ni1mo0.3si1n标准要求,氮含量与其他化学成分在纵向高度上分布均匀。实施例2制备200kg设计钢种21cr23mn2.5ni1mo0.5si1.6n,其成分(wt.%)见表6。表6设计钢种21cr23mn2.5ni1mo0.5si1.6n成分步骤s1、根据设计钢种的化学成分,确定出设计钢种21cr23mn2.5ni1mo0.5si1.6n在1510℃、0.07mpa氮分压下的极限氮含量[%n]=1.635,根据设计钢种在此压力下的极限氮含量和经验修正值,确定自耗电极母材的氮含量为1.635%×0.7=1.063%。根据设计钢种的目标重量、设计钢种的氮含量、自耗电极母材的氮含量和氮化铬中氮的收得率,得到氮化合金提供的氮含量为(1.6-1.063)/0.80×100%=0.67%,确定包芯管中氮化铬的用量为14005g并准备氮化合金。步骤s2、将粒径为5mm的氮化铬颗粒填充进3个铁管内并压实,形成包芯管,每一根包芯管的直径和质量均相同,其中包芯铁管外径d=34mm,厚度为δ=2mm。选用d=200mm,h=15mm的包芯管固定盘和db<d的组合式铸锭模,将包芯管固定盘安装在铸锭模的顶端开口处,包芯管固定盘上开设有包芯管安装孔和钢液浇注孔,钢液浇注孔位于包芯管固定盘的中心,包芯管安装孔在距离包芯管固定盘圆心1/4d的圆周上均匀分布,包芯管通过包芯管安装孔竖直固定在铸锭模内,包芯管的下端与铸锭模的底部接触,包芯管的上端与铸锭模的顶部齐平。步骤s3、根据设计钢种的化学成分、设计钢种的目标重量、氮化合金的重量以及铁管的重量(3根铁管提供5248g金属铁),确定冶炼自耗电极母材所需工业纯铁、金属铬、金属锰、金属镍、金属钼和工业硅的用量并进行准备,见表7。表7制备自耗电极所用原料的重量步骤s4、将工业纯铁、金属铬、金属锰、金属镍、金属钼和工业硅置于氮气保护的真空感应炉内进行冶炼,按照0.8kg/t钢将电解铝置于加料仓中,将200g含镁20%的镍镁合金置于加料仓中;待感应炉内炉料熔清后保持熔炼温度1510℃,并向炉内充入压力为0.07mpa的氮气进行氮合金化,然后依次添加电解铝、镍镁合金进行深脱氧和深脱硫处理,冶炼出自耗电极母材钢液。步骤s5、控制感应炉内氮气压力为0.07mpa,出钢温度为1510℃,将钢液通过浇注孔进行浇铸,浇铸结束后经冷却泄压获得铸锭,切除头尾缺陷,打磨铸锭表面至光滑,得到横截面如图6所示的自耗电极。图7为实施例二中获得的自耗电极横截面实际形貌图。对获得的自耗电极进行加压电渣重熔,包括以下步骤:步骤a1、将自耗电极焊接到假电极上,将假电极装卡在电极卡头上。步骤a2、实验选用的熔渣组元比例为caf2:cao:al2o3=4:3:3,重量为17kg。将熔渣在750℃下烘烤6小时,充分去除熔渣中的水分。步骤a3、将引弧环、500g引弧屑、底铁放在自耗电极下部的加压电渣炉底水板上,使自耗电极、引弧屑、底铁及底水箱紧密接触,确保通电后有电流通过。步骤a4、将熔渣加入到加压电渣炉结晶器内,密封熔炼室。开启供水系统,同时将纯度≥99.999%的氮气以12l/min的速度向熔炼室通入9min,排出熔炼室内的空气,接通电源后进行起弧化渣,在电压为33v,电流为1500a的供电参数下化渣15min,确保化渣成功。步骤a5、化渣结束后,将氮气压力逐步提升至1.2mpa,同时启用水气自动调节确保结晶器内外壁压力平衡。将电压调节至43v,电流调节至2400a,加压电渣熔炼开始,并将电压、电流维持在相对稳定的状态(电流波动±<2%,电压波动±<0.4%),熔速控制在140kg/h。步骤a6、熔炼后期采用降低电流的方式进行补缩,确保补缩充分,使钢锭上部端面平整。步骤a7、补缩阶段完成后,关闭电源,降低低水箱,同时分阶段降低氮气压力至常压,取出电渣钢锭。实验得到的电渣锭组织致密无氮气孔缺陷,其纵向化学成分如表8所示。表8成品钢的化学成分(纵向)(wt%)成分csimncrnimonspofe上部0.0430.4822.5221.192.360.961.6070.00210.00350.0023余量中部0.0430.4722.4021.112.350.951.6030.00200.00330.0023余量下部0.0420.4722.3821.022.310.951.6110.00190.00300.0024余量图8为所获得的电渣重熔铸锭中部的板片,随机选取不同位置进行成分测定,测定结果在表9中给出。表9成品钢的化学成分(横向)(wt%)成分csimncrnimonspofe10.0410.4622.4121.172.330.951.6050.00200.00340.0024余量20.0400.4522.3221.132.340.941.6130.00210.00320.0024余量30.0410.4522.4421.152.350.961.6090.00230.00330.0022余量40.0420.4722.4221.262.360.921.6000.00220.00330.0023余量50.0420.4622.3721.142.330.941.6120.00210.00310.0022余量60.0420.4522.4321.202.350.941.5940.00220.00320.0023余量70.0410.4522.3921.212.360.951.5980.00220.00320.0022余量80.0400.4722.4021.182.340.941.6070.00210.00340.0023余量90.0410.4622.5121.162.330.961.6200.00230.00320.0023余量上表中的氮含量结果表明,本实施例所得到的高氮钢电渣锭氮含量达到目标钢种21cr23mn2.5ni1mo0.5si1.6n标准要求,氮含量与其他化学成分在纵向高度与横向分布上分布均匀。需要理解的是,以上对本发明的具体实施例进行的描述只是为了说明本发明的技术路线和特点,其目的在于让本领域内的技术人员能够了解本发明的内容并据以实施,但本发明并不限于上述特定实施方式。凡是在本发明权利要求的范围内做出的各种变化或修饰,都应涵盖在本发明的保护范围内。当前第1页12