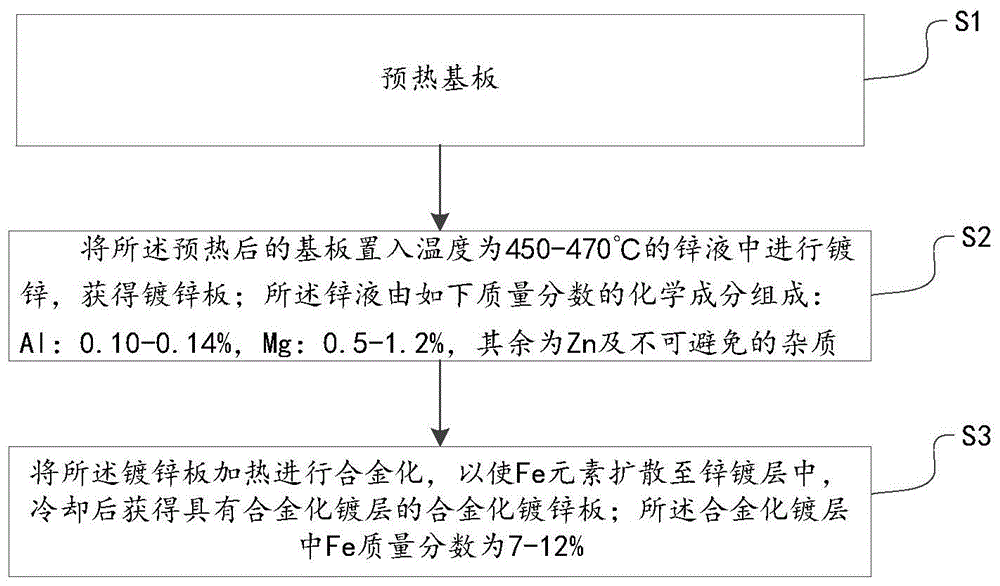
本发明属于镀锌板生产
技术领域:
,尤其涉及一种合金化镀锌板及其制备方法和应用。
背景技术:
:镀锌板是在带钢的上下两个表面均覆盖一层锌层的钢板,可用于汽车车身和汽车零部件。近年来,为满足镀锌板焊接的性能的要求,合金化镀锌产品广泛应用于汽车车身零件,但由于镀层内部铁含量增加,镀层耐蚀性及其切口耐蚀性往往有一定程度的降低。而近年来,锌铝镁镀层产品由于其良好的耐蚀性,成为车身零部件产品的替代产品之一,但焊接过程中容易出现点焊飞溅等问题。技术实现要素:为了解决上述的技术问题,本发明提供了一种合金化镀锌板及其制备方法和应用,本发明生产的合金化镀锌产品,在保证良好耐蚀性的同时,也可以兼顾镀层对焊接性能的要求,具有广阔的应用前景。一方面,本发明提供了一种合金化镀锌板,所述合金化镀锌板包括基板以及附着在所述基板表面的合金化镀层,所述合金化镀层由如下质量分数的化学成分组成:al:0.10-0.14%,mg:0.5-1.2%,fe:7-12%,其余为zn及不可避免的杂质。进一步地,所述al的质量分数为0.12-0.13%,所述mg的质量分数为0.7-1.0%。进一步地,所述al为0.15%,所述mg的质量分数为0.8%。进一步地,所述合金化镀层的厚度为2-10μm,所述基板的厚度为0.4-3mm。另一方面,本发明提供了上述的一种合金化镀锌板的制备方法,所述方法包括,预热基板;将预热后的所述基板置入温度为450-470℃的锌液中进行镀锌,获得镀锌板;所述锌液由如下质量分数的化学成分组成:al:0.10-0.14%,mg:0.5-1.2%,其余为zn及不可避免的杂质将所述镀锌板加热进行合金化处理,以使fe元素扩散至锌镀层中,冷却后获得具有合金化镀层的合金化镀锌板;所述合金化镀层中fe质量分数为7-12%。进一步地,所述基板的粗糙度为0.7-1.5μm。进一步地,所述预热基板包括:预热基板至温度≥460℃。进一步地,所述合金化处理的温度为480-530℃,所述合金化处理的时间为20-25s。进一步地,所述冷却速率为10-20℃/s,所述冷却结束温度为260-280℃。再一方面,本发明提供了上述的一种合金化镀锌板的应用,将所述合金化镀锌板用于制作汽车车身和汽车零部件。本发明实施例中的一个或多个技术方案,至少具有如下技术效果或优点:本发明提供了一种合金化镀锌板及其制备方法和应用,该合金化镀锌板的合金化镀层由特定成分的al、mg、fe和zn组成,其中,mg元素可以与空气中的水形成氯水锌矿,从而隔绝钢基体和大气接触,从而提高了合金化镀锌板镀层表面和切口的耐蚀性;fe元素可以使合金化镀层板具有良好的焊接性能,再配合al元素形成抑制层来约束fe元素的含量,使合金化镀锌板同时具备良好的耐蚀性能和焊接性能。本发明提供的合金化镀锌板的剥离比例为2.3-2.8%,粘附性好,红锈发生时间为810-1020h,耐蚀性好,在焊接过程中没有发生点焊飞溅,焊接性能良好。附图说明为了更清楚地说明本发明实施例中的技术方案,下面将对实施例描述中所需要使用的附图作一简单地介绍,显而易见地,下面描述中的附图是本发明的一些实施例,对于本领域普通技术人员来讲,在不付出创造性劳动的前提下,还可以根据这些附图获得其它的附图。图1为本发明实施例提供的一种合金化镀锌板的制备方法工艺图。具体实施方式下文将结合具体实施方式和实施例,具体阐述本发明,本发明的优点和各种效果将由此更加清楚地呈现。本领域技术人员应理解,这些具体实施方式和实施例是用于说明本发明,而非限制本发明。在整个说明书中,除非另有特别说明,本文使用的术语应理解为如本领域中通常所使用的含义。因此,除非另有定义,本文使用的所有技术和科学术语具有与本发明所属领域技术人员的一般理解相同的含义。若存在矛盾,本说明书优先。除非另有特别说明,本发明中用到的各种原材料、试剂、仪器和设备等,均可通过市场购买得到或者可通过现有方法制备得到。需要说明的是,在本文中,诸如“第一”和“第二”等之类的关系术语仅仅用来将一个实体或者操作与另一个实体或操作区分开来,而不一定要求或者暗示这些实体或操作之间存在任何这种实际的关系或者顺序。本发明实施例提供的技术方案为解决上述技术问题,总体思路如下:一方面,本发明实施例提供了一种合金化镀锌板,所述合金化镀锌板包括基板以及附着在所述基板表面的合金化镀层,所述合金化锌镀层由如下质量分数的化学成分组成:al:0.10-0.14%,mg:0.5-1.2%,fe:7-12%,其余为zn及不可避免的杂质。在本发明中各元素的作用如下:al:铝元素和锌元素会发生反应形成富铝相和富锌相,al元素可以在基板表面形成feal合金抑制层,避免fe元素向锌锅内部过度溶解,并在一定程度上控制合金化速度。铝含量过高,抑制层厚度过大,从而抑制了钢基体中的fe扩散至镀层中,从而使镀层的脆性增加,并且合金化速度受到抑制。al元素含量过低,抑制层过薄,导致钢基体中的fe溶解至锌锅中,形成锌渣,降低锌液的清洁度。mg:镁元素与锌元素会发生化学反应形成mg-zn相,mg-zn相会使得镀层,mg还会与空气中的水形成氯水锌矿(化学式为zn5(oh)8cl2·h2o),氯水锌矿可以隔离钢基体和大气,从而提高镀层表面和切口的耐蚀性。mg含量过高,mg元素氧化严重,并且镀锌完成后共晶组织显著增加,影响表面质量,容易出现花纹,黑变等问题。mg元素含量过低,对于提高镀层表面耐蚀性及切口耐蚀性有限。fe:fe元素可以改善合金化镀层钢的焊接性能,fe元素过多,会导致锌锅内锌液铁含量过高,产生锌渣,且合金化反应速度过快,合金化镀层过脆,冲压变形过脆中容易粉化;fe元素过少,对焊接性能改善不明显。作为本发明实施例的一种实施方式,所述al的质量分数为0.12-0.13%,所述mg的质量分数为0.7-1.0%。作为本发明实施例的一种实施方式,所述al为0.15%,所述mg的质量分数为0.8%。作为本发明实施例的一种实施方式,所述合金化镀层厚度为2-10μm,,所述基板的厚度为0.4-3mm。另一方面,本发明实施例还提供了上述的一种合金化镀锌板的制备方法,结合图1,所述方法包括,s1,预热基板;预热基板主要用于提高镀锌板的可镀性。作为本发明实施例的一种实施方式,所述基板的粗糙度为0.7-1.5μm。控制基板的粗糙度可以提高镀层与钢基体的粘附性能。粗糙度过大,影响镀锌板的表面质量,易出现漏镀问题;粗糙度过小,镀层与钢基体的粘附性差。作为本发明实施例的一种实施方式,所述预热后的基板的温度≥460℃。预热温度过低,不利于带钢表面锌层附着。s2,将预热后的所述基板置入温度为450-470℃的锌液中进行镀锌,获得镀锌板;所述锌液由如下质量分数的化学成分组成:al:0.10-0.14%,mg:0.5-1.2%,其余为zn及不可避免的杂质。镀锌温度过低,不利于锌液附着与钢基板的表面;镀锌温度过高,锌锅内部fe含量会显著增加,形成锌渣,降低锌液的洁净度。s3,将所述镀锌板加热进行合金化处理,以使fe元素扩散至锌镀层中,冷却后获得具有合金化镀层的合金化镀锌板;所述合金化镀层中fe质量分数为7-12%。通过合金化处理,钢基体中的fe元素可扩散至镀锌层中,形成合金化镀层,提高镀层熔点和镀层钢板的的焊接性能。作为本发明实施例的一种实施方式,所述合金化处理的温度为480-530℃,所述合金化处理的时间为20-25s。合金化处理温度过高,镀层内部铁含量显著增加,镀层脆性增加,在冲压成型过程中容易形成粉化。合金化处理温度过低,镀层内部铁含量不足,不利于提高镀层板焊接能力。合金化处理时间过长,镀层内部铁含量显著增加,镀层脆性增加,在成型过程中容易形成粉化。合金化处理时间过短,镀层内部铁含量不足,不利于提高镀层板焊接能力。作为本发明实施例的一种实施方式,所述冷却速率为10-20℃/s,所述冷却结束温度为260-280℃。冷却速率过大,带钢表面容易形成条纹缺陷,不利于表面质量提升;冷却速率过小,带钢至塔顶辊温度过高,不利于表面质量控制;冷却结束温度过高,带钢表面处于未完全凝固状态,不利于表面质量提升;冷却结束温度过低,对冷却速度要求过高,容易形成条纹缺陷。再一方面,本发明实施例还提供了一种合金化镀锌板的应用,将所述合金化镀锌板用于制作汽车车身和汽车零部件。下面将结合实施例、对照例及实验数据对本发明的一种合金化镀锌板及其制备方法进行详细说明。实施例1:实施例1提供的一种合金化镀锌板的制备方法,牌号为if,生产方法如下:1、将基板预热至480℃的温度,然后进入锌锅中镀锌,锌液温度控制为465℃,获得镀锌板。2、对步骤1的镀锌板采用感应加热装置加热边部,然后以100m/min的速率进入合金化炉,合金化段温度为520℃,合金化段长度为34米。带钢过合金化炉后到塔顶辊的温度为260℃。3、采用风冷方式将步骤2的合金化带钢冷却至260℃的温度,获得合金化镀锌板。制备的合金化镀锌板的厚度为0.65mm,宽度为1800mm,合金化镀锌层的组成如表1所示,余量为zn及不可避免的杂质。实施例2实施例2提供的一种镀锌板的制备方法,牌号为dx54d+zma,生产方法如下:1、将基板预热至490℃的温度,然后进入锌锅中镀锌,锌液温度控制为455℃,获得镀锌板。2、对步骤1的镀锌板采用感应加热装置加热边部,然后以90m/min的速率进入合金化炉,合金化段温度为500℃,合金化段长度为34米。带钢过合金化炉后到塔顶辊的温度为260℃。3、采用风冷方式将步骤2的合金化带钢冷却至260℃的温度,获得合金化镀锌板。制备的合金化镀锌板的厚度为0.6mm,宽度为1800mm,合金化镀锌层的组成如表1所示,余量为zn及不可避免的杂质,实施例3实施例3提供的一种镀锌板的制备方法,牌号为dx56d+zma,生产方法如下:1、将基板预热至500℃的温度,然后进入锌锅中镀锌,锌液温度控制为458℃,获得镀锌板。2、对步骤1的镀锌板采用感应加热装置加热边部,然后以90m/min的速率进入合金化炉,合金化段温度为500℃,合金化段长度为34米。带钢过合金化炉后到塔顶辊的温度为270℃。3、采用风冷方式将步骤2的合金化带钢冷却至260℃的温度,获得合金化镀锌板。制备的合金化镀锌板的厚度为0.8mm,宽度为1800mm,锌层的组成如表1所示。实施例4实施例4提供了一种合金化镀锌板的制备方法,以实施例1为参照,实施例4与实施例1不同的是,合金化镀层中al的质量分数为0.15%,mg的质量分数为0.8%,fe的质量分数为10%。对比例1对比例1提供了一种镀锌板的制备方法,以实施例1为参照,对比例1与实施例1的区别在于,al的质量分数为0.25%,mg的质量分数为2.5%,fe的质量分数为20%,其余与实施例1相同。对比例2对比例2提供了一种镀锌板的制备方法,以实施例1为参照,对比例2与实施例1的区别在于,al的质量分数为0.05%,mg的质量分数为0.25%,fe的质量分数为5%,其余与实施例1相同。表1编号al/%mg/%fe/%单面锌镀层的厚度/μm实施例10.111.084实施例20.101.195实施例30.121.0126实施例40.150.8105对比例10.252.5204对比例20.050.2554将实施例1-4以及对比例1-2制备的镀锌板进行镀层粘附性评价。采用折弯方法,将样片折弯180°,然后观察折弯位置镀层发生剥离长度,用剥离长度除以样片折弯宽度,得到镀层剥离的比例。剥离比例越小,表示镀锌板的粘附性越好。镀层剥离比例=剥离长度/样片折弯宽度×100%将实施例1-4以及对比例1-2制备的镀锌板放入中性盐雾箱环境下,进行中性盐雾试验,记录出现腐蚀红锈的时间,红锈发生时间越长,表示镀锌板的耐蚀性越好。对实施例1-4以及对比例1-2制备的合金化镀锌板进行焊接,观察是否出现点焊飞溅,具体如表2所示。未出现点焊飞溅,表面合金化镀锌板具有良好的焊接性能。实验评估结果见表2所示。表2由表2中的内容可知,实施例1-4提供的合金化镀锌板的剥离比例为2.3-2.8%,粘附性好,红锈发生时间为810-1020h,耐蚀性好,在焊接过程中没有发生点焊飞溅,焊接性能良好。对比例1提供的合金化镀锌板的剥离比例为0.5%,粘附性好,红锈发生时间为1900h,耐蚀性好,但是在焊接过程中出现点焊飞溅,焊接性能差。对比例2提供的合金化镀锌板的剥离比例为14%,粘附性差,红锈发生时间为160h,耐蚀性差,焊接过程未出现点焊飞溅,焊接性能好。本发明提供了一种合金化镀锌板及其制备方法和应用,该合金化镀锌板的合金化镀层由特定成分的al、mg、fe和zn组成,其中,mg元素可以与空气中的水形成氯水锌矿,从而隔绝钢基体和大气接触,从而提高了合金化镀锌板镀层表面和切口的耐蚀性;fe元素可以使合金化镀层板具有良好的焊接性能,再配合al元素形成抑制层来约束fe元素的含量,使合金化镀锌板同时具备良好的耐蚀性能和焊接性能;本发明在避免形成过厚抑制层、保证合金化效果的同时,提高了镀层的耐蚀性;通过控制锌锅温度,保证了镀液的流动性及镀层厚度及相结构的均匀性;通过控制合金化温度及时间,在保证合金化效果的同时,保证了镀层内部的铁含量,保证了镀层的焊接性能。本发明提供的合金化镀锌板的剥离比例为2.3-2.8%,粘附性好,红锈发生时间为810-1020h,耐蚀性好,在焊接过程中没有发生点焊飞溅,焊接性能良好。最后,还需要说明的是,术语“包括”、“包含”或者其任何其他变体意在涵盖非排他性的包含,从而使得包括一系列要素的过程、方法、物品或者设备不仅包括那些要素,而且还包括没有明确列出的其他要素,或者是还包括为这种过程、方法、物品或者设备所固有的要素。尽管已描述了本发明的优选实施例,但本领域内的技术人员一旦得知了基本创造性概念,则可对这些实施例作出另外的变更和修改。所以,所附权利要求意欲解释为包括优选实施例以及落入本发明范围的所有变更和修改。显然,本领域的技术人员可以对本发明进行各种改动和变型而不脱离本发明的精神和范围。这样,倘若本发明的这些修改和变型属于本发明权利要求及其等同技术的范围之内,则本发明也意图包含这些改动和变型在内。当前第1页12