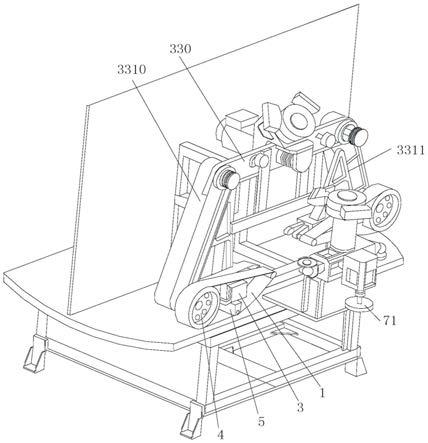
柔性力抵靠对焊瘤进行抛光去材;第一打磨轨迹和第二打磨轨迹分别对应一侧轨腰,第一打磨轨迹覆盖轨顶面、第二打 磨轨迹覆盖轨底面,或者第一打磨轨迹覆盖轨底面、第二打磨轨迹覆盖轨顶面;纵向修磨时,用砂轮沿钢轨纵向进给。
9.将焊瘤分为两条打磨轨迹,每条打磨轨迹均从上向下打磨,实现轨顶、轨腰和轨底的连续自动化打磨。打磨单元 以柔性力抵靠钢轨,避免了刚性力打磨造成硬伤的问题,并且、若焊瘤的强度过大,则打磨单元打滑,避免打磨单元自 身损坏。
10.进一步,横向打磨时,砂带除了沿钢轨横向的运动以外,同时具有沿钢轨纵向的运动。
11.进一步,砂带作为打磨单元的一部分,打磨单元包括打磨轮和传动轮,砂带张紧于打磨轮和传动轮,砂带、打磨 轮和传动轮形成一个带传动机构,横向打磨时,打磨轮的轴向顺应钢轨的长度方向,打磨轮抵靠钢轨,砂带位于打磨轮 和钢轨之间,打磨轮自转、砂带沿打磨轮的切向去除焊瘤。
12.进一步,在横向打磨时,监测打磨轮与钢轨之间的作用力,监测获得的作用力高于设定的力阈值时,发出报警。
13.进一步,纵向修磨时,包括对轨腰的打磨,对轨顶面的打磨和对轨底面的打磨,采用千叶轮对轨腰打磨,采用第 一盘式砂轮对轨顶面进行打磨,盘式角砂轮的打磨面为砂轮底面;采用第二盘式砂轮对轨底面进行打磨,盘式角砂轮的 打磨面为砂轮底面。
14.进一步,采用第一盘式砂轮打磨轨腰向轨底过渡的曲面,采用第二盘式砂轮打磨轨顶下方、与轨腰过渡的曲面; 第一盘式砂轮与水平面成第一夹角,第一夹角的角度为0
°
到
‑
10
°
;第二盘式砂轮与水平面成第二夹角,第二夹角的 角度为0
°
到10
°
。
15.进一步,第二盘式砂轮具有第一打磨部和第二打磨部,第一打磨部与第二打磨部同心,第一打磨部在内,第二打 磨部在外;从砂轮沿轴向的截面看,第二打磨部呈圆弧,第二打磨部在砂轮沿轴向的截面上的圆心角与轨顶下方、与轨 腰过渡的曲面的圆心角一致。这里的一致并非是指数学意义的相等,指的是第二打磨部的圆心角接近曲面的圆心角,小 于等于曲面的圆心角。
16.进一步,打磨轮与砂带接触的部分为柔性件;打磨轮打磨轨顶面时,打磨轮自转、打磨轮向靠近钢轨宽度方向中 心线进给的同时从一侧轨腰向另一侧轨腰进给,同时、打磨轮沿钢轨纵向往复进给,横向进给距离不小于35mm;打磨 轮打磨轨腰时,打磨轮自转的、打磨轮向靠近钢轨宽度方向中心线进给的同时、打磨轮沿高度方向顺应轨腰的曲面进给, 同时打磨轮沿钢轨纵向往复进给,横向进给距离不小于35mm。横向进给距离的限定,使得砂带只对焊瘤进行去材打磨, 不伤及钢轨母材。
17.进一步,横向进给距离为3.5cm~5cm。该横向进给距离下,焊瘤去除干净且不伤钢轨母材。
18.进一步,焊接后的钢轨经过错边量检测后,使用该打磨方法对错边量合格的钢轨焊瘤进行去材打磨。
19.进一步,在打磨前,获取钢轨错边量数据,找到钢轨焊缝两边的高的母材,使打磨轮从高的母材向低的母材横向 进给。如此,达到横向打磨不伤钢轨母材的目的。
20.进一步,在打磨前,测量焊缝与母材之间的高度差,打磨轮向靠近钢轨宽度方向中心线进给量小于该高度差。可 选的,该高度差为焊缝与母材之间的平均高度差,或者该高
度差为焊缝与母材之间的最低高度,或者该高度差为焊缝与 母材之间的中位高度。如此,避免过度进给而导致的打伤钢轨母材。
21.可选的,砂带、打磨轮和传动轮形成的带传动机构安装在一个支架上,在打磨作业过程中,当砂带上与钢轨接触 的位置停滞时间超过设定时间阈值时,整个带传动机构停止向靠近钢轨的方向进给,支架带动打磨轮向远离钢轨的方向 后撤,直到打磨轮与钢轨之间的作用力降低到允许范围内为止。如此,避免带传动机构损坏、失效。
22.有一种支架带动打磨轮向远离钢轨的方向后撤的方案为:安装打磨轮的支架部分和安装传动轮的支架部分相互独 立,两个支架部分之间通过柔性件或弹性件连接在一起,当砂带上与钢轨接触的位置停滞时间未超过设定时间阈值时, 柔性件或弹性件使两个支架部分保持打磨轮和传动轮的相对位置稳定,打磨轮实现打磨作业;当砂带上与钢轨接触的位 置停滞时间超过设定时间阈值时,柔性件或弹性件形变、使打磨轮向靠近传动轮的方向运动。
23.有另一种支架带动打磨轮向远离钢轨的方向后撤的方案为:安装打磨轮的支架装在一个机架上,支架和机架之间 设置弹性件或柔性件、形成打磨作业时的柔性力,当砂带上与钢轨接触的位置停滞时间未超过设定时间阈值时,柔性件 或弹性件使支架和机架的相对位置稳定,打磨轮实现打磨作业;当砂带上与钢轨接触的位置停滞时间超过设定时间阈值 时,柔性件或弹性件形变、使支架向靠近机架的方向运动。机架可以与机械化、自动化的进给动力装置相连,实现打磨 轮的进给。
24.这两种支架带动打磨轮向远离钢轨的方向后撤的方案可以独立使用,也可以组合在一起,形成复合柔性力机制。
25.第二方面,一种钢轨打磨系统,包括打磨单元、钢轨支撑机构和实现打磨单元打磨进给的进给机构,进给机构与 打磨单元相连,打磨单元与进给机构之间设有缓冲组件,缓冲组件包括弹簧或弹簧以外的柔性件;打磨单元包括打磨轮、 传动轮和砂带,砂带张紧于打磨轮和传动轮,砂带、打磨轮和传动轮形成一个带传动机构,横向打磨时,打磨轮的轴向 顺应钢轨的长度方向。
26.进一步,打磨单元包括安装架,打磨轮和传动轮设置于安装架,安装架上设有张紧轮,张紧轮与张紧驱动件相连, 张紧轮使砂带张紧于打磨轮和传动轮;进行打磨任务时,打磨轮抵靠钢轨;打磨单元具有限制打磨轮受力阈值的阻尼机 构,打磨轮与钢轨之间的作用力大于受力阈值时,打磨轮向靠近传动轮的方向位移。
27.进一步,打磨轮包括转轴和柔性套筒,转轴在内,柔性套筒在外,砂带与柔性套筒接触。
28.进一步,安装架上设置有张紧驱动件和张紧轮,张紧驱动件包括固定部和可动部,张紧轮设置于可动部,固定部设 置于安装架。
29.进一步,安装架上设有限位滚轮,限位滚轮的轴与打磨轮的轴平行;限位滚轮触碰到钢轨时,打磨轮到达向钢轨内 进给的极限位置。
30.进一步,安装架包括固定部和可动部,打磨轮位于可动部,传动轮位于固定部;打磨轮与钢轨之间的作用力大于受 力阈值时,可动部后撤;打磨轮与钢轨之间的作用力小于受力阈值时,可动部和固定部的相对位置固定。
31.进一步,安装架上设有阻尼机构,阻尼机构包括弹簧和锁止件,弹簧设置于可动部
和固定部之间,弹簧和锁止件共 同作用使可动部处于平衡位置,打磨轮和传动轮之间的距离固定。
32.进一步,固定部设有第一弹簧安装件,可动部设有第二弹簧安装件,弹簧的两端分别与第一弹簧安装件、第二弹 簧安装件固定。
33.可选的,打磨轮的轮心和传动轮的轮心一个高、一个低,张紧轮位于打磨轮和传动轮之间,打磨轮的轮心、传动 轮的轮心和张紧轮的轮心形成的三角形位于砂带包围的区域之内。如此设置,砂带的张紧稳定性好,且砂带与打磨轮之 间的摩擦力可调,有利于在打磨轮高速转动时,保持砂带与打磨轮之间的相对位置稳定。
34.进一步,张紧驱动件是气缸、油缸或者电动推杆,张紧驱动件与打磨轮轮心
‑
传动轮轮心形成的直线相交,张紧 轮相比打磨轮更靠近传动轮。
35.进一步,砂带张紧时,打磨轮与传动轮之间的砂带段与水平面成斜角,打磨轮与张紧轮之间的砂带段与水平面成 斜角,打磨轮与传动轮之间的砂带段和打磨轮与张紧轮之间的砂带段形成锐角,传动轮与张紧轮之间的砂带段跟打磨轮 与张紧轮之间的砂带段形成钝角。这样,保持打磨单元的稳定性和砂带的稳定性。
36.进一步,锐角小于45
°
,钝角小于150
°
且大于120
°
。
37.进一步,构建第一基准面,第一基准面经过打磨轮的轮轴线和传动轮的轮轴线,以打磨轮宽度方向的中心面为第 二基准面,第二基准面与第一基准面垂直,以第二基准面与张紧轮的轮轴线的交点向第一基准面和第二基准面的交线投 影,获得张紧轮投影点,打磨轮的轮轴线在第一基准面和第二基准面的交线的点作为打磨轮投影点,传动轮的轮轴线在 第一基准面和第二基准面的交线的点作为传动轮投影点,张紧轮投影点与打磨轮投影点的距离与张紧轮投影点与传动轮 投影点的距离比至少为5:4。
38.可选的,钢轨打磨系统具有两个上述打磨单元,打磨单元分别设置于钢轨宽度方向的两侧,一个打磨单元高、另 一个打磨单元低。
39.进一步,一个打磨单元的张紧轮朝上,另一个打磨单元的张紧轮朝下。
40.进一步,打磨系统包括安装打磨单元的支架,两个打磨单元安装于同一个支架;支架包括横臂和位于横臂两侧的两 个连接臂,每个连接臂上安装有一个打磨单元,连接臂与横臂之间设有弹性机构;横臂上设有与机器人连接的电气接头。
41.可选的,高的打磨单元的打磨轮的轮心到横臂的距离和低的打磨单元的打磨轮的轮心到横臂的距离的比值为 0.7~0.9。如此设置,从对一侧轨腰的打磨切换到对另一侧轨腰时,机械臂活机器人本身的位姿基本不变,只需切换支 架的位姿即可。
42.进一步,连接臂包括与横臂相连的斜板和与斜板连接的三角架,打磨单元的安装架与斜板、三角架相连,安装架 位于斜板、三角架的底部,安装架和斜板、三角架形成三角结构,传动轮的轮心位于三角结构覆盖的区域内,主动轮位 于三角结构之外。斜板和横臂之间可设置柔性机制,比如斜板和横臂之间设置阻尼器,允许斜板和横臂能够有毫米级的 转动位移。阻尼器可以是弹簧、橡胶垫、齿槽相对的连接器等等。三角架与斜杆之间也可以设置柔性机制。三角架与斜 板之间的连接刚性(或柔性)跟斜板和横臂之间的连接刚性(或柔性)等级或程度可以不一样,使得整个支架具有多重 柔性机制。
43.进一步,安装架的可动部位于三角结构之外,固定部作为三角结构的一部分;安装架上设有限位块,三角架实现 对限位块的阻挡限位。
44.进一步,连接臂上设有冷却介质管道和冷却控制阀,冷却介质管道从斜板向三家架方向伸出,三角架上设有冷却 介质管道定位件。冷却介质管道包括刚性管和柔性管,刚性管与定位件相连,柔性管连接冷却控制阀和刚性管。
45.可选的,进给机构是机械臂,横臂上设置快换接口,快换接口与机械臂的连接面相对横臂倾斜。
46.可选的,进给机构为三维移动平台,横臂中心与三维移动平台相连,三自由度移动平台提供支架在x、y、z轴的 平移位移。
47.可选的,进给机构为三维移动平台,三维移动平台与每个打磨单元安装架相连。这种情况下,打磨单元直接跟三 维移动平台连接,无需支架结构。比如,三维移动平台以跟轨底平行的平面作为xoy平面,以钢轨的长度方向为x轴, 钢轨的高度方向为z轴,三维移动平台使砂带机构沿x轴、y轴和z轴平动实现打磨进给;每个打磨单元安装于各自的 z轴平移模组上,两个打磨单元共用x轴和y轴的平移模组。
48.可选的,上述钢轨打磨系统设置于打磨房内,打磨房将打磨作业空间围成与外界环境隔开的独立环境。实现无人化 打磨作业。
49.可选的,打磨房有能绕其中线自转的转动墙,转动墙的边界与打磨房之间有密封机构,转动墙设置在转盘上,转盘 中心与转盘电机相连,转盘上设有一对搁架,两个搁架分别位于转动墙的两侧。
50.如此,可以实现打磨房内不停机,打磨房外更换损耗砂带、砂轮等耗损件、或进行维修。
51.可选的,张紧驱动件为张紧气缸,搁架上设有送气口,砂带机构上设有进气口,当打磨单元的支架放置在搁架上 时,送气口与进气口连通;送气口与气源相连;搁架上设有感应力传感器传感器,感应受力时,气源开启;感应受力为 0时,气源关闭。
52.上述钢轨打磨系统应用长轨生产线上,使用抛光研磨的方式去除钢轨焊缝上的焊瘤,形成用于长轨生产线的钢轨 粗磨工作站。
53.一种用于长轨生产线的钢轨粗磨工作站,上述钢轨打磨系统设置于长轨生产线上,在焊接后的错边量检测工位之后。
54.第三方面,本发明提供一种对钢轨表面质量进行检测的自动化钢轨检测系统。例如对打磨后的钢轨表面质量进行 定量和定性检测。
55.一种自动化检测装置,包括相机,点光源和检测单元支架,相机和点光源设置于检测单元支架上;以一个相机和 为该相机配置的多个点光源作为一个检测单元,同一个检测单元内的点光源的光斑在被测物体上的覆盖区域相互独立, 同一个检测单元在进行一次拍摄任务时、点光源依次点亮,点光源亮一次则相机拍摄一次待测物体的图像,相机每次拍 摄有且仅有一个点光源点亮;在单个拍摄任务过程中,点光源和相机的位置相对固定;每次拍摄任务获取多幅待测物体 图像,每张待测物体图像对应一个点光源照亮待测物体时、同时具有物体信息和光照信息的图像;融合待测物体图像的 空间特征和帧间特征获得待测物体表面纹理的三维图像。
56.可选的,提取待测物体图像中的空间特征和帧间特征,空间特征和帧间特征均以三维卷积分别表示,其中,三维 卷积包括二维空间维度和一维帧间维度,空间特征的三维卷积中的一维帧间维度的值为设定值、二维空间维度为图像的 空间特征值,帧间特征的三
维卷积中的二维空间维度的值为设定值,一维帧间维度为帧间特征值;进行图像信息融合时, 先处理帧间特征,再处理空间特征,再融合帧间特征和空间特征获得待测物体表面纹理的三维图像。
57.可选的,点光源受控于控制器,控制器中预设有点光源的点亮规则,每个点光源具有各自的唯一的光源编码,相 机具有其唯一的相机编码;点亮规则包括相机编码与光源编码的对应,以及点光源的点亮顺序。相机编码与光源编码的 对应,比如,1号相机对应01号光源、04号光源、06号光源。01号光源、04号光源、06号光源依前后次序单独点亮。
58.可选的方案,点光源通过光源支架固定于检测单元支架,每个光源支架上设置一个点光源,光源支架包括挂耳和 挂件,挂耳与检测单元支架固定,挂件上固定光源,挂件和挂耳可转动连接,挂件与挂耳之间有阻尼。
59.可选的,挂耳具有向远离检测单元支架方向延伸的耳部,挂件具有梁和向靠近检测单元支架方向延伸的连接部, 点光源固定于梁;连接部与耳部有重叠,连接部与耳部之间有光源转轴,光源转轴与连接部固定、或者光源转轴与耳部 固定。转动梁可实现调节光源在被测物体上的照射区域。
60.可选的,光源转轴与连接部固定,光源转轴与光源驱动电机的输出轴相连。光源转轴的存在使得光源的位置能够 调整,从而能够适应不同尺寸规格的被测物体。使用编码器或角度测量仪,可获得被测物体尺寸与光源旋转角度的关系, 便于在更换被测物体时、光源位置的快速标定。
61.可选的方案有,以相机为中心,以跟相机轴线垂直的任意一个面为基准面,以光源跟相机的距离对光源进行分组, 同一组的光源、光源与相机的距离相等,不同组的光源、光源与相机的距离随机。同一组的光源至少有3个。
62.可选的,以相机为中心,光源的极坐标角度随机。如此,光源能够尽量离散的照射在被测物体上。
63.可选的,任意相邻两个光源的距离与相机到被测物体的拍摄距离的比值为0.1~0.2。如此设置,相机拍摄的图像 清晰,且光源在被测物体上的照射区域不相重叠,待测物体表面纹理的三维图像重建效果好。
64.在长轨生产时,对于钢轨表面质量要求包括:焊缝及焊缝周围的焊渣清理干净,打磨面必须平顺,轨底脚(轨腰 向轨底面过渡的曲面部分)圆顺,不得横向打磨,不得打亏钢轨母材。
65.将上述自动化检测装置应用于钢轨表面质量检测时,形成自动化钢轨检测系统。一种自动化钢轨检测系统,该检 测系统包括至少一组上述检测装置,该系统的检测对象为位于生产线上、完成焊瘤初铣或完成焊瘤初磨的钢轨,该检测 系统设置于钢轨焊缝的第一次去除工序之后,或该检测系统有两套,第一套检测系统设置于钢轨错变量检测之后、钢轨 焊缝的第一次去除工序之前;第二套检测系统设置于钢轨焊缝的第一次去除工序之后。
66.在一些实施例中,钢轨检测系统具有框架,自动化检测装置安装于框架内,框架具有侧板和顶板,侧板和顶板将 框架内围成暗室,其中一个侧板上设有允许钢轨进入的入口,在相对的侧板上设有允许钢轨输出的出口。
67.可选的,侧板上有门或床,或者侧板与框架可拆卸式连接。
68.长轨生产中,对于钢轨表面检测要求还有:对钢轨焊缝进行全断面检测。
69.可选的方案是,框架内设有能绕钢轨断面进行360
°
运动的检测驱动装置,检测装置通过接口与检测驱动装置连 接,检测驱动装置带着检测装置步进式的对钢轨各表面进行检测作业。
70.可选的,检测装置只有一个,检测驱动装置带着检测装置步进式对轨顶面、轨腰面、轨底面和另一个轨腰面进行 检测作业。
71.或者,框架内具有上检测作业组件和下检测作业组件,上检测作业组件具有与地面平行的第一检测装置、位于第 一检测装置两侧的第二检测装置和第三检测装置,第二检测装置与第三检测装置关于第一检测装置的相机中心对称。
72.可选的,上检测作业组件与检测驱动装置相连,第二检测装置的检测对象为一个轨腰面,第三检测装置为另一个 轨腰面,第二检测装置和第三检测装置分别具有三个检测位,检测驱动装置使第二检测装置或第三检测装置分别在三个 检测位进行迁移;第一个检测位上,第二检测装置的相机的轴向与水平面的夹角为
‑
25
°
~
‑
38
°
;第二个检测位上,第 二检测装置的轴线与水平面平行;第三个检测位上,第二检测装置的轴线与水平面的夹角为35~55
°
。
73.可选的,第二检测装置进行作业时,第三检测装置不工作;第三检测装置进行工作时,第二检测装置不工作。
74.可选的,下检测作业组件固定于轨底之下。
75.可选的方案是,检测装置有四组,每一组对应一个钢轨的检测区域,检测装置围成检测区域,钢轨沿棱柱的轴向 进入检测区域;两个相对的检测装置的距离不小于1050mm。如此,使检测装置能够适用于长轨生产线上的钢轨检测。
76.可选的,其中一组检测装置对准轨顶面,其中一组检测装置对准轨底面,其中一组检测装置对准一个轨腰面,另 一组检测装置对准另一个轨腰面,轨腰面的任意一组检测装置具有上检测单元、中检测单元和下检测单元,每个检测单 元具有相机、点光源和光源控制器;上检测单元的相机轴线与水平面的夹角为下倾27
°
~34
°
,中检测单元的相机轴线 与水平面平行,下检测单元的相机轴线与水平面的夹角为上仰41
°
~49
°
。
77.可选的,轨腰面的任意一组检测装置包括背板,上检测单元、中检测单元和下检测单元分别通过各自的位置调整 机构安装于背板,背板包括主板、上翼板和下翼板,主板与待测钢轨的高度方向平行;上翼板与主板相交,且上翼板的 顶部相比上翼板的底部更接近待测钢轨;下翼板与主板相交,且下翼板的顶部相比下翼板的底部更远离待测钢轨。
78.可选的,上检测单元的相机靠近上翼板和主板相交的区域,上检测单元的一部分光源设置于上翼板覆盖的区域, 上检测单元的另一部分光源设置于主板覆盖的区域。
79.可选的,中检测单元的相机及其光源设置于主板覆盖的区域内。
80.可选的,下检测单元的相机及其光源设置于下翼板覆盖的区域内。
81.如此,轨腰面的任意一组检测装置能够实现轨腰面的位于轨顶下的面、轨腰侧面、轨顶下的面与轨腰侧面过渡的 小圆弧面,轨腰向轨底过渡的大圆弧面和轨腰与轨底相邻的竖直面的全表面检测。
82.长轨生产中,对于钢轨表面检测要求还有:打磨后轨底焊筋(焊缝)高度不小于0.5mm,因此,还需要对打磨后 的钢轨进行定量测量。
83.定量测量装置的可选方案是:检测装置上具有线激光器,线激光器的轴线与相机
的轴线呈夹角,光源点亮时,线 激光器不发射激光;线激光器发射激光线时,光源不点亮。
84.依据钢轨表面质量要求,我们将打磨后的钢轨表面缺陷检测指标具体为:是否有横向打磨轨迹,打磨面与钢轨母 材之间是否有台阶,并提出一种使用上述检测装置或检测系统进行钢轨表面缺陷检测的方法。
85.一种通过相机和点光源群组实现钢轨表面缺陷检测的方法,该方法以一个相机和为该相机配置的多个点光源作为 一个检测单元,同一个检测单元在进行一次拍摄任务时、点光源依次点亮,点光源亮一次则相机拍摄一次待测物体的图 像,相机每次拍摄有且仅有一个点光源点亮;每次拍摄任务获取多幅待测物体图像,每张待测物体图像对应一个点光源 照亮待测物体时、同时具有物体信息和光照信息的图像;融合待测物体图像的空间特征和帧间特征重建获得待测物体表 面的法向图,寻找法向图中发生满足梯度变化特征阈值的位置,将发生该位置标记为缺陷。如此,能够检测出打磨面与 钢轨母材之间的台阶缺陷。融合待测物体图像的空间特征和帧间特征获得待测物体表面的法向图,能够去除因打磨面的 高光和色差等导致的伪缺陷的干扰,只在法向图中保留真实加工缺陷。
86.可选的,同一个检测单元内的点光源的光斑在被测物体上的覆盖区域相互独立。如此,法向图的重建效果好。
87.可选的,在法向图中提取线条,判断线条方向是平行钢轨长度方向还是垂直于钢轨长度方向,若出现垂直于钢轨 长度方向的线条,则标记为缺陷。在长轨生产线上,钢轨的长度方向是确定的。因此,能够以钢轨的长度方向作为判断 基准。如此,能够识别出钢轨的横向打磨痕迹。
88.可选的,在获得待测物体的法向图之前,先将待测物体图像进行阈值分割,将小于设定阈值的图像区域去除,只 对剩余区域进行帧间特征提取和空间特征提取。
89.使用上述检测装置或检测系统,实现对钢轨焊缝处的加工余量定量测量的方法如下:
90.一种通过激光线和相机进行钢轨表面质量定量测量的方法,该方法通过激光器向钢轨表面照射直线光条,相机获 取钢轨和光条的钢轨
‑
光条图像,从钢轨
‑
光条图像中分割出光条,沿着x向对光条离散取点,提取出各离散点的光条中 心像素坐标,寻找的纵坐标最小的光条中心点作为特征点,从特征点分别向左右两边搜索光条曲线的二阶导数的最小值 点,将特征点左右两边的二阶导数最小值点判定为钢轨焊缝边界特征点,以钢轨焊缝边界内的特征点和钢轨焊缝边界外 的特征点在y轴的差值作为打磨后轨底焊筋高度。两个钢轨焊缝边界特征点作为焊缝所在区域,其余区域为钢轨母材。
91.可选的,提取光条中心点像素坐标的在一些实施例中方法为:以图像中光条上任意一像素点(x0,y0)处的法线方向 的向量记为(n
x
,n
y
),获得光条中心的像素坐标为(x0+tn
x
,y0+tn
y
),其中,
92.;记数字图像的二维灰度分布函数为i(x,y)。如此,利用光条的灰度分布特性,抗干扰能力强,且提取精 度高,能够实现光条的亚像素级别的提取。
93.可选的,在计算光条中心点的坐标之前,利用阈值法对钢轨
‑
光条图像的光条边界进行粗提取,然后通过粗提取 的光条边界计算光条宽度w并生成对应宽度的高斯卷积核,最后再利用该高斯卷积核对光条内部区域使用上述公式计算 进行光条中心的精确提取,从而得到光条中心坐标;
94.记第i个光条中心的像素坐标为(x
i
,y
i
),光条中心点的水平像素坐标为x
i
,寻找光条中心点纵坐标最小的点作为 特征点c;然后分别对各个光条中心点进行微分计算与高斯滤波处理得到滤波后的一阶导数ki, 然后再对滤波后的一阶导数进行微分计算与高斯滤波处理, 得到滤波后的二阶导数d
i
,最后从特征点c分别向左右两侧 搜索二阶导数的最小值来确定钢轨焊缝边界的特征点;以钢轨焊缝边界内的特征点和钢轨焊缝边界外的特征点在y轴的 差值作为打磨后轨底焊筋高度。如此,实现打磨后钢轨的加工余量的定量测量。
95.具体的:光条中心坐标提取方法的具体实现流程如下:
96.step1:设置阈值th,输入待处理的钢轨
‑
光条图像i。
97.step2:对钢轨
‑
光条图像i进行预处理。
98.step3:对所有列像素进行顺序扫描,得到该列上第一个大于th的像素坐标和最后一个大于th的像素坐标,分别 记为(b1,col),(b2,col),该坐标即为粗提取得到光条边界的坐标。
99.step4:利用粗提取得到的光条边界计算每一列上的光条宽度,记第i列的光条宽度为w
i
=|b1‑
b2|,则最大 光条宽度为w
max
=max{w
i
|n≥i≥1},其中n为图像的列数。
100.step5:以10为公差生成等差数组m={10,20,
…
,w
max
}。利用数组中的元素m
i
构造长度和宽度为的高斯 卷积核及其对应的一阶和二阶偏导卷积核。
101.step6:对图像中第i列像素,选择step5生成的数组m中最接近w
i
的元素m
i
所构造的卷积核计算第i列像素上 行坐标在区间内的像素点的法线方向的向量(n
x
,n
y
)。
102.step7:将step5中计算得到的特征向量代入式(3
‑
21)计算t,当|tn
x
|≤0.5且|tn
y
|≤0.5时,光条中心处 于当前像素内。最终求解得光条中心的像素坐标为(x0+tn
x
,y0+tn
y
)。
103.step8:对每一列重复step6至step7,最终可提取得到所有光条中心。
104.具体的,
105.焊缝定位算法的具体算法步骤如下:
106.step1:对线结构光图像进行光条中心提取,记第i个光条中心为p
i
,图像坐标为(x
i
,y
i
)。
107.step2:对step1中提取到的光条中心点p
i
进行遍历搜索,将纵坐标最小的点作为特征点c。
108.step3:对step1中提取到的光条中心点使用式(4
‑
2)计算各个点处的一阶导数,并对计算结果使用一维高斯滤波 器进行滤波。滤波器的大小为51,μ设置为0,σ设置为17。
109.step4:利用step3中高斯滤波后得到的一阶导数使用微分法计算各中心点处的二阶导数d
i
。对计算得到的二阶导 数使用一维高斯滤波器进行滤波,滤波器的大小为51,μ设置为0,σ设置为17。
110.step5:从特征点c分别向左右两边搜索二阶导数的最小值点,将特征点c左右两边的二阶导数最小值点判定为 钢轨焊缝边界特征点。
111.可选的,计算所述光条中心的三维坐标时进行系统矫正:引入水平的辅助测量基准c,先测定所述的辅助测量基 准c到所述的标定基准b的距离m
i
,用测量点到b的距离n
i
减去对应点的c到b的距离m
i
得到hi,通过测量计算位于 焊缝两侧的选定测量点的h1和h2,计算|h1
‑
h2|得到错边量。
112.本发明的第四方面,提供一种能够高精度的控制钢轨打磨区域的表面质量的方法。
113.一种高精度的钢轨打磨方法,使用砂带、或砂纸、或砂轮以磨削的方式对钢轨表面进行去材打磨,其特征在于, 打磨之后,对打磨后的区域进行缺陷检测:以一个相机和为该相机配置的多个点光源作为一个检测单元,同一个检测单 元在进行一次拍摄任务时、点光源依次点亮,点光源亮一次则相机拍摄一次待测物体的图像,相机每次拍摄有且仅有一 个点光源点亮;每次拍摄任务获取多幅待测物体图像,每张待测物体图像对应一个点光源照亮待测物体时、同时具有物 体信息和光照信息的图像;融合待测物体图像的空间特征和帧间特征重建获得待测物体表面的法向图,寻找法向图中发 生满足梯度变化特征阈值的位置,将发生该位置标记为缺陷;若出现缺陷标记,则发出报警。
114.进一步,缺陷检测前或缺陷检测后进行定量检测:通过激光器向钢轨表面照射直线光条,光条照射的区域包括打 磨后的区域和未打磨的区域,相机获取钢轨和光条的钢轨
‑
光条图像,从钢轨
‑
光条图像中分割出光条,沿着x向对光条 离散取点,提取出各离散点的光条中心像素坐标,寻找纵坐标最小的光条中心点作为特征点,从特征点分别向左右两边 搜索光条曲线的二阶导数的最小值点,将特征点左右两边的二阶导数最小值点判定为钢轨焊缝边界特征点,以钢轨焊缝 边界内的特征点和钢轨焊缝边界外的特征点在y轴的差值作为打磨后与打磨前的加工余量,判断加工余量是否在余量范 围之内,若是,则认为定量要求符合;如否,则发出报警。
115.进一步,缺陷检测和定量检测,使用本发明上述的检测单元,或检测装置,或检测系统。缺陷检测的方法使用本 发明上述的方法。定量检测的方法使用本发明上述的方法。
116.与现有技术相比,本发明具有以下优点:1、能够全自动的实现钢轨表面质量的定性缺陷检测和加工余量的定量检 测,替代目前长轨生产线上的人工眼观、千分尺等人工测量,检测效率高,检测准确率高。2、定性缺陷检测能够对钢 轨焊缝处的铣削痕迹、磨削痕迹进行自动化检测,自动识别横向打磨纹路并报警,自动识别焊缝去除不干净、出现棱角、 台阶并报警。3、对钢轨表面的加工余量达到精度在0.05mm之内、测量速度1s以内的定量测量。
附图说明
117.图1是本发明的打磨钢轨设备结构示意图。
118.图2是钢轨横向打磨轨迹的示意图。
119.图3是砂带装置上设置的限位机构的示意图。
120.图4是打磨单元带有弹性机制的示意图。
121.图5是两个打磨单元装在支架上的示意图。
122.图6是放置在打磨房外的打磨单元及其支架的示意图。
123.图7是打磨房内的示意图。
124.图8是机械手与砂带装置的支架相连的示意图。
125.图9是本发明的纵向修磨的结构示意图。
126.图10是本发明的检测装置第一种实施方式的结构示意图。
127.图11是本发明的检测装置局部结构示意图。
128.图12是本发明的检测装置第二种实施方式的结构示意图。
129.图13是本发明的第二检测装置结构示意图。
130.图14是本发明的上检测作业组件和下检测作业组件的结构示意图。
131.图15是本发明上检测作业组件结构示意图。
132.图16是本发明的下检测作业组件的结构示意图。
133.图17是本发明基于三维卷积的非朗伯体表面光度立体模型的网络结构示意图。
134.图18是本发明基于三维卷积的非朗伯体表面光度立体方法的流程示意图。
135.图19是本发明的一个较佳实施例中的条纹中心提取效果图。
136.图20是本发明的精度验证结果示意图。
137.图21是本发明的定量测量方法使用1mm量块单次测量结果。
具体实施方式
138.与列车配合的长型材,钢轨呈工字型,包括轨顶面,轨底面和位于轨顶面、轨底面之间的轨腰曲面。
139.如图1
‑
8所示,在一些实施例中,一种钢轨10打磨方法,该方法的打磨对象是长轨生产线上在线打磨焊接后的 钢轨10,该方法使用砂带1在线打磨钢轨10;该方法分为横向打磨和纵向修磨,横向是指沿钢轨10的高度方向,纵向 是指沿钢轨10的长度方向;横向打磨时、砂带1从钢轨10的宽度方向的两侧分别沿第一打磨轨迹16和第二打磨轨迹 17进行打磨,砂带1以柔性力抵靠对焊瘤进行抛光去材;第一打磨轨迹16和第二打磨轨迹17分别对应一侧轨腰,第 一打磨轨迹16覆盖轨顶面、第二打磨轨迹17覆盖轨底面,或者第一打磨轨迹16覆盖轨底面、第二打磨轨迹17覆盖轨 顶面;纵向修磨时,用砂轮沿钢轨10纵向进给。
140.将焊瘤分为两条打磨轨迹,每条打磨轨迹均从上向下打磨,实现轨顶、轨腰和轨底的连续自动化打磨。打磨单元 以柔性力抵靠钢轨10,避免了刚性力打磨造成硬伤的问题,并且、若焊瘤的强度过大,则打磨单元打滑,避免打磨单 元自身损坏。
141.如图1
‑
8所示,在一些实施例中,横向打磨时,砂带1除了沿钢轨10横向的运动以外,同时具有沿钢轨10纵向 的运动。
142.如图1
‑
7所示,在一些实施例中,砂带1作为打磨单元的一部分,打磨单元包括打磨轮6和传动轮4,砂带1张 紧于打磨轮6和传动轮4,砂带1、打磨轮6和传动轮4形成一个带传动机构,横向打磨时,打磨轮6的轴向顺应钢轨10的长度方向,打磨轮6抵靠钢轨10,砂带1位于打磨轮6和钢轨10之间,打磨轮6自转、砂带1沿打磨轮6的切向 去除焊瘤。
143.如图1
‑
7所示,在一些实施例中,在横向打磨时,监测打磨轮6与钢轨10之间的作用
力,监测获得的作用力高 于设定的力阈值时,发出报警。
144.如图1和9所示,在一些实施例中,纵向修磨时,包括对轨腰的打磨,对轨顶面的打磨和对轨底面的打磨,采用 千叶轮71对轨腰打磨,采用第一盘式砂轮80对轨顶面进行打磨,盘式角砂轮的打磨面为砂轮底面;采用第二盘式砂轮 90对轨底面进行打磨,盘式角砂轮的打磨面为砂轮底面。
145.如图1和9所示,在一些实施例中,采用第一盘式砂轮80打磨轨腰向轨底过渡的曲面,采用第二盘式砂轮90打 磨轨顶下方、与轨腰过渡的曲面;第一盘式砂轮与水平面成第一夹角,第一夹角的角度为0
°
到
‑
10
°
;第二盘式砂轮 与水平面成第二夹角,第二夹角的角度为0
°
到10
°
。
146.如图1和9所示,在一些实施例中,第二盘式砂轮90具有第一打磨部和第二打磨部,第一打磨部与第二打磨部 同心,第一打磨部在内,第二打磨部在外;从砂轮沿轴向的截面看,第二打磨部呈圆弧,第二打磨部在砂轮沿轴向的截 面上的圆心角与轨顶下方、与轨腰过渡的曲面的圆心角一致。这里的一致并非是指数学意义的相等,指的是第二打磨部 的圆心角接近曲面的圆心角,小于等于曲面的圆心角。
147.如图1
‑
8所示,在一些实施例中,打磨轮6与砂带1接触的部分为柔性件;打磨轮6打磨轨顶面时,打磨轮6自 转、打磨轮6向靠近钢轨10宽度方向中心线进给的同时从一侧轨腰向另一侧轨腰进给,同时、打磨轮6沿钢轨10纵向 往复进给,横向进给距离不小于35mm;打磨轮6打磨轨腰时,打磨轮6自转的、打磨轮6向靠近钢轨10宽度方向中心 线进给的同时、打磨轮6沿高度方向顺应轨腰的曲面进给,同时打磨轮6沿钢轨10纵向往复进给,横向进给距离不小 于35mm。横向进给距离的限定,使得砂带1只对焊瘤进行去材打磨,不伤及钢轨10母材。
148.如图1
‑
8所示,在一些实施例中,横向进给距离为3.5cm~5cm。该横向进给距离下,焊瘤去除干净且不伤钢轨10 母材。
149.如图1
‑
8所示,在一些实施例中,焊接后的钢轨10经过错边量检测后,使用该打磨方法对错边量合格的钢轨10 焊瘤进行去材打磨。
150.如图1
‑
8所示,在一些实施例中,在打磨前,获取钢轨10错边量数据,找到钢轨10焊缝两边的高的母材,使打 磨轮6从高的母材向低的母材横向进给。如此,达到横向打磨不伤钢轨10母材的目的。
151.如图1
‑
7所示,在一些实施例中,在打磨前,测量焊缝与母材之间的高度差,打磨轮6向靠近钢轨10宽度方向 中心线进给量小于该高度差。在一些实施例中,该高度差为焊缝与母材之间的平均高度差,或者该高度差为焊缝与母材 之间的最低高度,或者该高度差为焊缝与母材之间的中位高度。如此,避免过度进给而导致的打伤钢轨10母材。
152.如图1
‑
7所示,在一些实施例中方案,砂带1、打磨轮6和传动轮4形成的带传动机构安装在一个支架上,在打 磨作业过程中,当砂带1上与钢轨10接触的位置停滞时间超过设定时间阈值时,整个带传动机构停止向靠近钢轨10 的方向进给,支架带动打磨轮6向远离钢轨10的方向后撤,直到打磨轮6与钢轨10之间的作用力降低到允许范围内为 止。如此,避免带传动机构损坏、失效。
153.有一种支架带动打磨轮6向远离钢轨10的方向后撤的方案为:安装打磨轮6的支架部分和安装传动轮4的支架 部分相互独立,两个支架部分之间通过柔性件或弹性件连接在
一起,当砂带1上与钢轨10接触的位置停滞时间未超过 设定时间阈值时,柔性件或弹性件使两个支架部分保持打磨轮6和传动轮4的相对位置稳定,打磨轮6实现打磨作业; 当砂带1上与钢轨10接触的位置停滞时间超过设定时间阈值时,柔性件或弹性件形变、使打磨轮6向靠近传动轮4的 方向运动。
154.有另一种支架带动打磨轮6向远离钢轨10的方向后撤的方案为:安装打磨轮6的支架装在一个机架上,支架和 机架之间设置弹性件或柔性件、形成打磨作业时的柔性力,当砂带1上与钢轨10接触的位置停滞时间未超过设定时间 阈值时,柔性件或弹性件使支架和机架的相对位置稳定,打磨轮6实现打磨作业;当砂带1上与钢轨10接触的位置停 滞时间超过设定时间阈值时,柔性件或弹性件形变、使支架向靠近机架的方向运动。机架可以与机械化、自动化的进给 动力装置相连,实现打磨轮6的进给。
155.这两种支架带动打磨轮6向远离钢轨10的方向后撤的方案可以独立使用,也可以组合在一起,形成复合柔性力 机制。
156.如图1
‑
8所示,在一些实施例中,一种钢轨10打磨系统,包括打磨单元、钢轨10支撑机构和实现打磨单元打磨 进给的进给机构,进给机构与打磨单元相连,打磨单元与进给机构之间设有缓冲组件,缓冲组件包括弹簧或弹簧以外的 柔性件;打磨单元包括打磨轮6、传动轮4和砂带1,砂带1张紧于打磨轮6和传动轮4,砂带1、打磨轮6和传动轮4 形成一个带传动机构,横向打磨时,打磨轮6的轴向顺应钢轨10的长度方向。
157.如图1
‑
8所示,在一些实施例中,打磨单元包括安装架,打磨轮6和传动轮4设置于安装架,安装架上设有张紧轮 5,张紧轮5与张紧驱动件3相连,张紧轮5使砂带1张紧于打磨轮6和传动轮4;进行打磨任务时,打磨轮6抵靠钢 轨10;打磨单元具有限制打磨轮6受力阈值的阻尼机构,打磨轮6与钢轨10之间的作用力大于受力阈值时,打磨轮6 向靠近传动轮4的方向位移。
158.如图8所示,在一些实施例中,打磨轮6包括转轴和柔性套筒8,转轴在内,柔性套筒8在外,砂带1与柔性套筒 8接触。
159.如图1
‑
8所示,在一些实施例中,安装架上设置有张紧驱动件3和张紧轮5,张紧驱动件3包括固定部9和可动部 7,张紧轮5设置于可动部7,固定部9设置于安装架。
160.如图1
‑
8所示,在一些实施例中,安装架上设有限位滚轮,限位滚轮的轴与打磨轮6的轴平行;限位滚轮触碰到钢 轨10时,打磨轮6到达向钢轨10内进给的极限位置。
161.如图1
‑
8所示,在一些实施例中,安装架包括固定部9和可动部7,打磨轮6位于可动部7,传动轮4位于固定部9; 打磨轮6与钢轨10之间的作用力大于受力阈值时,可动部7后撤;打磨轮6与钢轨10之间的作用力小于受力阈值时, 可动部7和固定部9的相对位置固定。
162.如图1
‑
8所示,在一些实施例中,安装架上设有阻尼机构,阻尼机构包括弹簧和锁止件,弹簧设置于可动部7和固 定部9之间,弹簧和锁止件共同作用使可动部7处于平衡位置,打磨轮6和传动轮4之间的距离固定。
163.如图4所示,在一些实施例中,固定部9设有第一弹簧安装件12,可动部7设有第二弹簧安装件13,弹簧的两 端分别与第一弹簧安装件12、第二弹簧安装件13固定。
164.如图5
‑
6所示,在一些实施例中,打磨轮6的轮心和传动轮4的轮心一个高、一个低,张紧轮5位于打磨轮6和 传动轮4之间,打磨轮6的轮心、传动轮4的轮心和张紧轮5的轮心形成的三角形位于砂带1包围的区域之内。如此设 置,砂带1的张紧稳定性好,且砂带1与打磨
轮6之间的摩擦力可调,有利于在打磨轮6高速转动时,保持砂带1与打 磨轮6之间的相对位置稳定。
165.如图5所示,在一些实施例中,张紧驱动件3是气缸、油缸或者电动推杆,张紧驱动件3与打磨轮6轮心
‑
传动 轮4轮心形成的直线相交,张紧轮5相比打磨轮6更靠近传动轮4。
166.如图1
‑
7所示,在一些实施例中,砂带1张紧时,打磨轮6与传动轮4之间的砂带1段与水平面成斜角,打磨轮 6与张紧轮5之间的砂带1段与水平面成斜角,打磨轮6与传动轮4之间的砂带1段和打磨轮6与张紧轮5之间的砂带 1段形成锐角,传动轮4与张紧轮5之间的砂带1段跟打磨轮6与张紧轮5之间的砂带1段形成钝角。这样,保持打磨 单元的稳定性和砂带1的稳定性。
167.在一些实施例中,锐角小于45
°
,钝角小于150
°
且大于120
°
。
168.如图1
‑
7所示,在一些实施例中,构建第一基准面,第一基准面经过打磨轮6的轮轴线和传动轮4的轮轴线,以 打磨轮6宽度方向的中心面为第二基准面,第二基准面与第一基准面垂直,以第二基准面与张紧轮5的轮轴线的交点向 第一基准面和第二基准面的交线投影,获得张紧轮5投影点,打磨轮6的轮轴线在第一基准面和第二基准面的交线的点 作为打磨轮6投影点,传动轮4的轮轴线在第一基准面和第二基准面的交线的点作为传动轮4投影点,张紧轮5投影点 与打磨轮6投影点的距离与张紧轮5投影点与传动轮4投影点的距离比至少为5:4。
169.如6
‑
7所示,在一些实施例中,钢轨10打磨系统具有两个上述打磨单元,打磨单元分别设置于钢轨10宽度方向 的两侧,一个打磨单元高、另一个打磨单元低。
170.如图9所示,在一些实施例中,一个打磨单元的张紧轮5朝上,另一个打磨单元的张紧轮5朝下。
171.如图1和5所示,在一些实施例中,打磨系统包括安装打磨单元的支架,两个打磨单元安装于同一个支架;支架包 括横臂330和位于横臂330两侧的两个连接臂,每个连接臂上安装有一个打磨单元,连接臂与横臂330之间设有弹性机 构;横臂330上设有与机器人连接的电气接头332。
172.如图1和5所示,在一些实施例中,高的打磨单元的打磨轮6的轮心到横臂330的距离和低的打磨单元的打磨轮 6的轮心到横臂330的距离的比值为0.7~0.9。如此设置,从对一侧轨腰的打磨切换到对另一侧轨腰时,机械臂活机器 人本身的位姿基本不变,只需切换支架的位姿即可。
173.如图5所示,在一些实施例中,连接臂包括与横臂330相连的斜板3310和与斜板3310连接的三角架3311,打磨 单元的安装架与斜板3310、三角架3311相连,安装架位于斜板3310、三角架3311的底部,安装架和斜板3310、三角 架3311形成三角结构,传动轮4的轮心位于三角结构覆盖的区域内,打磨轮6位于三角结构之外。斜板3310和横臂 330之间可设置柔性机制,比如斜板3310和横臂330之间设置阻尼器,允许斜板3310和横臂330能够有毫米级的转动 位移。阻尼器可以是弹簧、橡胶垫、齿槽相对的连接器等等。三角架3311与斜板3310之间也可以设置柔性机制。三角 架3311与斜板3310之间的连接刚性(或柔性)跟斜板3310和横臂330之间的连接刚性(或柔性)等级或程度可以不 一样,使得整个支架具有多重柔性机制。
174.如图5所示,在一些实施例中,安装架的可动部7位于三角结构之外,固定部9作为
三角结构的一部分;安装架 上设有限位块,三角架3311实现对限位块的阻挡限位。
175.如图8所示,在一些实施例中,连接臂上设有冷却介质管道和冷却控制阀,冷却介质管道从斜板3310向三角架 3311方向伸出,三角架3311上设有冷却介质管道的定位件142。冷却介质管道包括刚性管140和柔性管141,刚性管 140与定位件142相连,柔性管141连接冷却控制阀和刚性管140。
176.如图5所示,在一些实施例中,进给机构是机械臂,横臂330上设置快换接口,快换接口与机械臂的连接面相对 横臂330倾斜。
177.在一些实施例中,进给机构为三维移动平台,横臂330中心与三维移动平台相连,三自由度移动平台提供支架在 x、y、z轴的平移位移。
178.在一些实施例中,进给机构为三维移动平台,三维移动平台与每个打磨单元安装架相连。这种情况下,打磨单元 直接跟三维移动平台连接,无需支架结构。比如,三维移动平台以跟轨底平行的平面作为xoy平面,以钢轨10的长度 方向为x轴,钢轨10的高度方向为z轴,三维移动平台使砂带1机构沿x轴、y轴和z轴平动实现打磨进给;每个打 磨单元安装于各自的z轴平移模组上,两个打磨单元共用x轴和y轴的平移模组。
179.如图6
‑
7所示,作为在一些实施例中方案,上述钢轨10打磨系统设置于打磨房内,打磨房将打磨作业空间围成与 外界环境隔开的独立环境。实现无人化打磨作业。
180.在一些实施例中,打磨房有能绕其中线自转的转动墙,转动墙的边界与打磨房之间有密封机构,转动墙设置在转盘 上,转盘中心与转盘电机相连,转盘上设有一对搁架,两个搁架分别位于转动墙的两侧。
181.如此,可以实现打磨房内不停机,打磨房外更换损耗砂带1、砂轮等耗损件、或进行维修。
182.如图5所示,在一些实施例中,张紧驱动件3为张紧气缸,搁架上设有送气口,砂带1机构上设有进气口,当打 磨单元的支架放置在搁架上时,送气口与进气口连通;送气口与气源相连;搁架上设有感应力传感器传感器,感应受力 时,气源开启;感应受力为0时,气源关闭。
183.上述钢轨10打磨系统应用长轨生产线上,使用抛光研磨的方式去除钢轨10焊缝上的焊瘤,形成用于长轨生产线的 钢轨10粗磨工作站。
184.在一些实施例中,用于长轨生产线的钢轨10粗磨工作站,上述钢轨10打磨系统设置于长轨生产线上,在焊接后的 错边量检测工位之后。
185.本发明提供一种对钢轨表面质量进行检测的自动化钢轨检测系统。例如对打磨后的钢轨表面质量进行定量和定性检 测。
186.如图10
‑
16所示,在一些实施例中,一种自动化检测装置,包括相机403,点光源402和检测单元支架440,相机 403和点光源402设置于检测单元支架440上;以一个相机403和为该相机403配置的多个点光源402作为一个检测单 元,同一个检测单元内的点光源402的光斑在被测物体上的覆盖区域相互独立,同一个检测单元在进行一次拍摄任务时、 点光源402依次点亮,点光源402亮一次则相机403拍摄一次待测物体的图像,相机403每次拍摄有且仅有一个点光源 402点亮;在单个拍摄任务过程中,点光源402和相机403的位置相对固定;每次拍摄任务获取多幅待测物体图像,每 张待测物体图像对应一个点光源402照亮待测物体时、同时具有物体信息和光照信息的图像;融合待测物体图像的空间 特征和帧间特
征获得待测物体表面纹理的三维图像。
187.在一些实施例中,提取待测物体图像中的空间特征和帧间特征,空间特征和帧间特征均以三维卷积分别表示,其中, 三维卷积包括二维空间维度和一维帧间维度,空间特征的三维卷积中的一维帧间维度的值为设定值、二维空间维度为图 像的空间特征值,帧间特征的三维卷积中的二维空间维度的值为设定值,一维帧间维度为帧间特征值;进行图像信息融 合时,先处理帧间特征,再处理空间特征,再融合帧间特征和空间特征获得待测物体表面纹理的三维图像。
188.如图11所示,在一些实施例中,点光源402通过光源支架50固定于检测单元支架440,每个光源支架50上设置 一个点光源402,光源支架50包括挂耳500和挂件501,挂耳500与检测单元支架440固定,挂件501上固定光源,挂 件501和挂耳500可转动连接,挂件501与挂耳500之间有阻尼。
189.如图11所示,在一些实施例中,挂耳500具有向远离检测单元支架440方向延伸的耳部5000,挂件501具有梁 和向靠近检测单元支架440方向延伸的连接部5010,点光源402固定于梁;连接部5010与耳部5000有重叠,连接部 5010与耳部5000之间有光源转轴,光源转轴与连接部5010固定、或者光源转轴与耳部5000固定。转动梁可实现调节 光源在被测物体上的照射区域。
190.如图11所示,在一些实施例中,光源转轴与连接部5010固定,光源转轴与光源驱动电机的输出轴相连。光源转 轴的存在使得光源的位置能够调整,从而能够适应不同尺寸规格的被测物体。使用编码器或角度测量仪,可获得被测物 体尺寸与光源旋转角度的关系,便于在更换被测物体时、光源位置的快速标定。
191.在一些实施例中,以相机403为中心,以跟相机403轴线垂直的任意一个面为基准面,以光源跟相机403的距离对 光源进行分组,同一组的光源、光源与相机403的距离相等,不同组的光源、光源与相机403的距离随机。同一组的光 源至少有3个。
192.在一些实施例中,以相机403为中心,光源的极坐标角度随机。如此,光源能够尽量离散的照射在被测物体上。
193.在一些实施例中,任意相邻两个光源的距离与相机403到被测物体的拍摄距离的比值为0.1~0.2。如此设置,相 机403拍摄的图像清晰,且光源在被测物体上的照射区域不相重叠,待测物体表面纹理的三维图像重建效果好。
194.在长轨生产时,对于钢轨10表面质量要求包括:焊缝及焊缝周围的焊渣清理干净,打磨面必须平顺,轨底脚(轨 腰向轨底面过渡的曲面部分)圆顺,不得横向打磨,不得打亏钢轨10母材。
195.将上述自动化检测装置应用于钢轨表面质量检测时,形成自动化钢轨检测系统。在一些实施例中,一种自动化钢 轨10检测系统,该检测系统包括至少一组上述检测装置,该系统的检测对象为位于生产线上、完成焊瘤初铣或完成焊 瘤初磨的钢轨10,该检测系统设置于钢轨10焊缝的第一次去除工序之后,或该检测系统有两套,第一套检测系统设置 于钢轨10错变量检测之后、钢轨10焊缝的第一次去除工序之前;第二套检测系统设置于钢轨10焊缝的第一次去除工 序之后。
196.如图12所示,在一些实施例中,钢轨10检测系统具有框架60,自动化检测装置安装于框架60内,框架60具有 侧板和顶板,侧板和顶板将框架60内围成暗室,其中一个侧板上
设有允许钢轨10进入的入口,在相对的侧板上设有允 许钢轨10输出的出口。
197.如图12所示,在一些实施例中,侧板上有门或床,或者侧板与框架60可拆卸式连接。
198.长轨生产中,对于钢轨10表面检测要求还有:对钢轨10焊缝进行全断面检测。
199.如图12所示,在一些实施例中,框架60内设有能绕钢轨10断面进行360
°
运动的检测驱动装置,检测装置通过 接口与检测驱动装置连接,检测驱动装置带着检测装置步进式的对钢轨10各表面进行检测作业。
200.在一些实施例中,检测装置只有一个,检测驱动装置带着检测装置步进式对轨顶面、轨腰面、轨底面和另一个轨 腰面进行检测作业。
201.如图12
‑
16所示,在一些实施例中,框架60内具有上检测作业组件和下检测作业组件62,上检测作业组件具有 与地面平行的第一检测装置610、位于第一检测装置610两侧的第二检测装置611和第三检测装置612,第二检测装置 611与第三检测装置612关于第一检测装置610的相机403中心对称。
202.如图13
‑
14所示,在一些实施例中,上检测作业组件与检测驱动装置相连,第二检测装置611的检测对象为一个 轨腰面,第三检测装置612为另一个轨腰面,第二检测装置611和第三检测装置612分别具有三个检测位,检测驱动装 置使第二检测装置611或第三检测装置612分别在三个检测位进行迁移;第一个检测位上,第二检测装置611的相机 403的轴向与水平面的夹角为
‑
25
°
~
‑
38
°
;第二个检测位上,第二检测装置611的轴线与水平面平行;第三个检测位 上,第二检测装置611的轴线与水平面的夹角为35~55
°
。
203.如图12和16所示,在一些实施例中,第二检测装置611进行作业时,第三检测装置612不工作;第三检测装置 612进行工作时,第二检测装置611不工作。
204.如图12和16所示,在一些实施例中,下检测作业组件62固定于轨底之下。
205.在一些实施例中,检测装置有四组,每一组对应一个钢轨10的检测区域,检测装置围成检测区域,钢轨10沿棱 柱的轴向进入检测区域;两个相对的检测装置的距离不小于1050mm。如此,使检测装置能够适用于长轨生产线上的钢 轨10检测。
206.如图13
‑
14所示,在一些实施例中,其中一组检测装置对准轨顶面,其中一组检测装置对准轨底面,其中一组检 测装置对准一个轨腰面,另一组检测装置对准另一个轨腰面,轨腰面的任意一组检测装置具有上检测单元64、中检测 单元65和下检测单元66,每个检测单元具有相机403、点光源402和光源控制器;上检测单元64的相机403轴线与水 平面的夹角为下倾27
°
~34
°
,中检测单元65的相机403轴线与水平面平行,下检测单元66的相机403轴线与水平面 的夹角为上仰41
°
~49
°
。
207.如图13
‑
14所示,在一些实施例中,轨腰面的任意一组检测装置包括背板,上检测单元64、中检测单元65和下 检测单元66分别通过各自的位置调整机构安装于背板,背板包括主板630、上翼板631和下翼板632,主板630与待测 钢轨10的高度方向平行;上翼板631与主板630相交,且上翼板631的顶部相比上翼板631的底部更接近待测钢轨10; 下翼板632与主板630相交,且下翼板632的顶部相比下翼板632的底部更远离待测钢轨10。
208.如图13所示,在一些实施例中,上检测单元64的相机403靠近上翼板631和主板630相交的区域,上检测单元 64的一部分光源设置于上翼板631覆盖的区域,上检测单元64的另一部分光源设置于主板630覆盖的区域。
209.如图13所示,在一些实施例中,中检测单元65的相机403及其光源设置于主板630覆盖的区域内。
210.如图13所示,在一些实施例中,下检测单元66的相机403及其光源设置于下翼板632覆盖的区域内。
211.如此,轨腰面的任意一组检测装置能够实现轨腰面的位于轨顶下的面、轨腰侧面、轨顶下的面与轨腰侧面过渡的 小圆弧面,轨腰向轨底过渡的大圆弧面和轨腰与轨底相邻的竖直面的全表面检测。
212.长轨生产中,对于钢轨10表面检测要求还有:打磨后轨底焊筋(焊缝)高度不小于0.5mm,因此,还需要对打磨 后的钢轨10进行定量测量。
213.如图17所示,定量测量装置的可选方案是:检测装置上具有线激光器67,线激光器67的轴线与相机403的轴线 呈夹角,光源点亮时,线激光器67不发射激光;线激光器67发射激光线时,光源不点亮。
214.依据钢轨10表面质量要求,我们将打磨后的钢轨10表面缺陷检测指标具体为:是否有横向打磨轨迹,打磨面与 钢轨10母材之间是否有台阶,并提出一种使用上述检测装置或检测系统进行钢轨10表面缺陷检测的方法。
215.在一些实施例中,一种通过相机403和点光源402群组实现钢轨10表面缺陷检测的方法,该方法以一个相机403 和为该相机403配置的多个点光源402作为一个检测单元,同一个检测单元在进行一次拍摄任务时、点光源402依次点 亮,点光源402亮一次则相机403拍摄一次待测物体的图像,相机403每次拍摄有且仅有一个点光源402点亮;每次拍 摄任务获取多幅待测物体图像,每张待测物体图像对应一个点光源402照亮待测物体时、同时具有物体信息和光照信息 的图像;融合待测物体图像的空间特征和帧间特征重建获得待测物体表面的法向图,寻找法向图中发生满足梯度变化特 征阈值的位置,将发生该位置标记为缺陷。如此,能够检测出打磨面与钢轨10母材之间的台阶缺陷。融合待测物体图 像的空间特征和帧间特征获得待测物体表面的法向图,能够去除因打磨面的高光和色差等导致的伪缺陷的干扰,只在法 向图中保留真实加工缺陷。
216.在一些实施例中,同一个检测单元内的点光源402的光斑在被测物体上的覆盖区域相互独立。如此,法向图的重 建效果好。
217.在一些实施例中,在法向图中提取线条,判断线条方向是平行钢轨10长度方向还是垂直于钢轨10长度方向,若出 现垂直于钢轨10长度方向的线条,则标记为缺陷。在长轨生产线上,钢轨10的长度方向是确定的。因此,能够以钢轨 10的长度方向作为判断基准。如此,能够识别出钢轨10的横向打磨痕迹。
218.如图15
‑
18所示,在一些实施例中,在获得待测物体的法向图之前,先将待测物体图像进行阈值分割,将小于设定 阈值的图像区域去除,只对剩余区域进行帧间特征提取和空间特征提取。
219.本发明公开了基于三维卷积的非朗伯体表面光度立体模型,包括信息融合层100、帧间特征提取101、空间特征提取 102、最大池化层103和回归层104;
220.使用上述检测装置或检测系统,实现对钢轨焊缝处的加工余量定量测量的方法如下:
221.一种通过激光线和相机进行钢轨表面质量定量测量的方法,该方法通过激光器67
向钢轨表面照射直线光条,相 机获取钢轨和光条的钢轨
‑
光条图像,从钢轨
‑
光条图像中分割出光条,沿着x向对光条离散取点,提取出各离散点的光 条中心像素坐标,寻找的纵坐标最小的光条中心点作为特征点,从特征点分别向左右两边搜索光条曲线的二阶导数的最 小值点,将特征点左右两边的二阶导数最小值点判定为钢轨焊缝边界特征点,以钢轨焊缝边界内的特征点和钢轨焊缝边 界外的特征点在y轴的差值作为打磨后轨底焊筋高度。两个钢轨焊缝边界特征点作为焊缝所在区域,其余区域为钢轨母 材。
222.可选的,提取光条中心点像素坐标的在一些实施例中方法为:以图像中光条上任意一像素点(x0,y0)处的法线方向 的向量记为(n
x
,n
y
),获得光条中心的像素坐标为(x0+tn
x
,y0+tn
y
),其中,
223.;记数字图像的二维灰度分布函数为i(x,y)。如此,利用光条的灰度分布特性,抗干扰能力强,且提取精 度高,能够实现光条的亚像素级别的提取。
224.可选的,在计算光条中心点的坐标之前,利用阈值法对钢轨
‑
光条图像的光条边界进行粗提取,然后通过粗提取 的光条边界计算光条宽度w并生成对应宽度的高斯卷积核,最后再利用该高斯卷积核对光条内部区域使用上述公式计算 进行光条中心的精确提取,从而得到光条中心坐标;
225.记第i个光条中心的像素坐标为(x
i
,y
i
),光条中心点的水平像素坐标为x
i
,寻找光条中心点纵坐标最小的点作为 特征点c;然后分别对各个光条中心点进行微分计算与高斯滤波处理得到滤波后的一阶导数ki, 然后再对滤波后的一阶导数进行微分计算与高斯滤波处理, 得到滤波后的二阶导数d
i
,最后从特征点c分别向左右两侧 搜索二阶导数的最小值来确定钢轨焊缝边界的特征点;以钢轨焊缝边界内的特征点和钢轨焊缝边界外的特征点在y轴的 差值作为打磨后轨底焊筋高度。如此,实现打磨后钢轨的加工余量的定量测量。
226.具体的:光条中心坐标提取方法的具体实现流程如下:
227.step1:设置阈值th,输入待处理的钢轨
‑
光条图像i。
228.step2:对钢轨
‑
光条图像i进行预处理。
229.step3:对所有列像素进行顺序扫描,得到该列上第一个大于th的像素坐标和最后一个大于th的像素坐标,分别 记为(b1,col),(b2,col),该坐标即为粗提取得到光条边界的坐标。
230.step4:利用粗提取得到的光条边界计算每一列上的光条宽度,记第i列的光条宽度为w
i
=|b1‑
b2|,则最大 光条宽度为w
max
=max{w
i
|n≥i≥1},其中n为图像的列数。
231.step5:以10为公差生成等差数组m={10,20,
…
,w
max
}。利用数组中的元素m
i
构造
长度和宽度为的高斯 卷积核及其对应的一阶和二阶偏导卷积核。
232.step6:对图像中第i列像素,选择step5生成的数组m中最接近w
i
的元素m
i
所构造的卷积核计算第i列像素上 行坐标在区间内的像素点的法线方向的向量(n
x
,n
y
)。
233.step7:将step5中计算得到的特征向量代入式(3
‑
21)计算t,当|tn
x
|≤0.5且|tn
y
|≤0.5时,光条中心处 于当前像素内。最终求解得光条中心的像素坐标为(x0+tn
x
,y0+tn
y
)。
234.step8:对每一列重复step6至step7,最终可提取得到所有光条中心。
235.具体的,
236.焊缝定位算法的具体算法步骤如下:
237.step1:对线结构光图像进行光条中心提取,记第i个光条中心为p
i
,图像坐标为(x
i
,y
i
)。
238.step2:对step1中提取到的光条中心点p
i
进行遍历搜索,将纵坐标最小的点作为特征点c。
239.step3:对step1中提取到的光条中心点使用式(4
‑
2)计算各个点处的一阶导数,并对计算结果使用一维高斯滤波 器进行滤波。滤波器的大小为51,μ设置为0,σ设置为17。
240.step4:利用step3中高斯滤波后得到的一阶导数使用微分法计算各中心点处的二阶导数d
i
。对计算得到的二阶导 数使用一维高斯滤波器进行滤波,滤波器的大小为51,μ设置为0,σ设置为17。
241.step5:从特征点c分别向左右两边搜索二阶导数的最小值点,将特征点c左右两边的二阶导数最小值点判定为 钢轨焊缝边界特征点。
242.可选的,计算所述光条中心的三维坐标时进行系统矫正:引入水平的辅助测量基准c,先测定所述的 辅助测量基准c到所述的标定基准b的距离m
i
,用测量点到b的距离n
i
减去对应点的c到b的距离m
i
得到 hi,通过测量计算位于焊缝两侧的选定测量点的h1和h2,计算|h1
‑
h2|得到错边量。使用上述定量测量方 法,对待测物体图像进行光条中心提取并转换为世界坐标系下的坐标,由于线结构光在测量时是斜射在量 块上的,因此量块部分的点云呈现倾斜状态,要得到量块的厚度的测量值只需取点云在z
w
轴方向上的坐标 即可,最终得到1mm量块的测量结果如图21所示。
243.重复测量10次,最终结果如表3.4所示。
244.表3.4 1mm量块测量结果
[0245][0246]
由表3.4可知,对1mm量块进行测量,测量均值为1.0161mm,偏差均值为0.0161mm,测量值的标准差为0.0083mm, 极差为0.0255mm,因此该测量系统的测量精度满足测量需求。
[0247]
本发明的第四方面,提供一种能够高精度的控制钢轨打磨区域的表面质量的方法。
[0248]
在一些实施例中,一种高精度的钢轨打磨方法,使用砂带、或砂纸、或砂轮以磨削的方式对钢轨表面进行去材打 磨,打磨之后,对打磨后的区域进行缺陷检测:以一个相机403和为该相机配置的多个点光源402作为一个检测单元, 同一个检测单元在进行一次拍摄任务时、点光源依次点亮,点光源亮一次则相机拍摄一次待测物体的图像,相机每次拍 摄有且仅有一个点光源点亮;每次拍摄任务获取多幅待测物体图像,每张待测物体图像对应一个点光源照亮待测物体时、 同时具有物体信息和光照信息的图像;融合待测物体图像的空间特征和帧间特征重建获得待测物体表面的法向图,寻找 法向图中发生满足梯度变化特征阈值的位置,将发生该位置标记为缺陷;若出现缺陷标记,则发出报警。
[0249]
在一些实施例中,缺陷检测前或缺陷检测后进行定量检测:通过激光器67向钢轨表面照射直线光条,光条照射 的区域包括打磨后的区域和未打磨的区域,相机获取钢轨和光条的钢轨
‑
光条图像,从钢轨
‑
光条图像中分割出光条,沿 着x向对光条离散取点,提取出各离散点的光条中心像素坐标,寻找纵坐标最小的光条中心点作为特征点,从特征点分 别向左右两边搜索光条曲线的二阶导数的最小值点,将特征点左右两边的二阶导数最小值点判定为钢轨焊缝边界特征 点,以钢轨焊缝边界内的特征点和钢轨焊缝边界外的特征点在y轴的差值作为打磨后与打磨前的加工余量,判断加工余 量是否在余量范围之内,若是,则认为定量要求符合;如否,则发出报警。
[0250]
在一些实施例中,缺陷检测和定量检测,使用本发明上述的检测单元,或检测装置,或检测系统。缺陷检测的方 法使用本发明上述的方法。定量检测的方法使用本发明上述的方法。
[0251]
本发明的各实施例既可以独立的作为技术方案,也可以相互组合形成组合方案。
[0252]
可以理解,本发明所描述的实施例都是一些优选的实施例子和特点,任何本领域的一般技术人员都可以根据本发明 描述的精髓下做一些更改和变化,这些更改和变化也
被认为属于本发明的范围和独立权利要求以及附属权利要求所限制 的范围内。