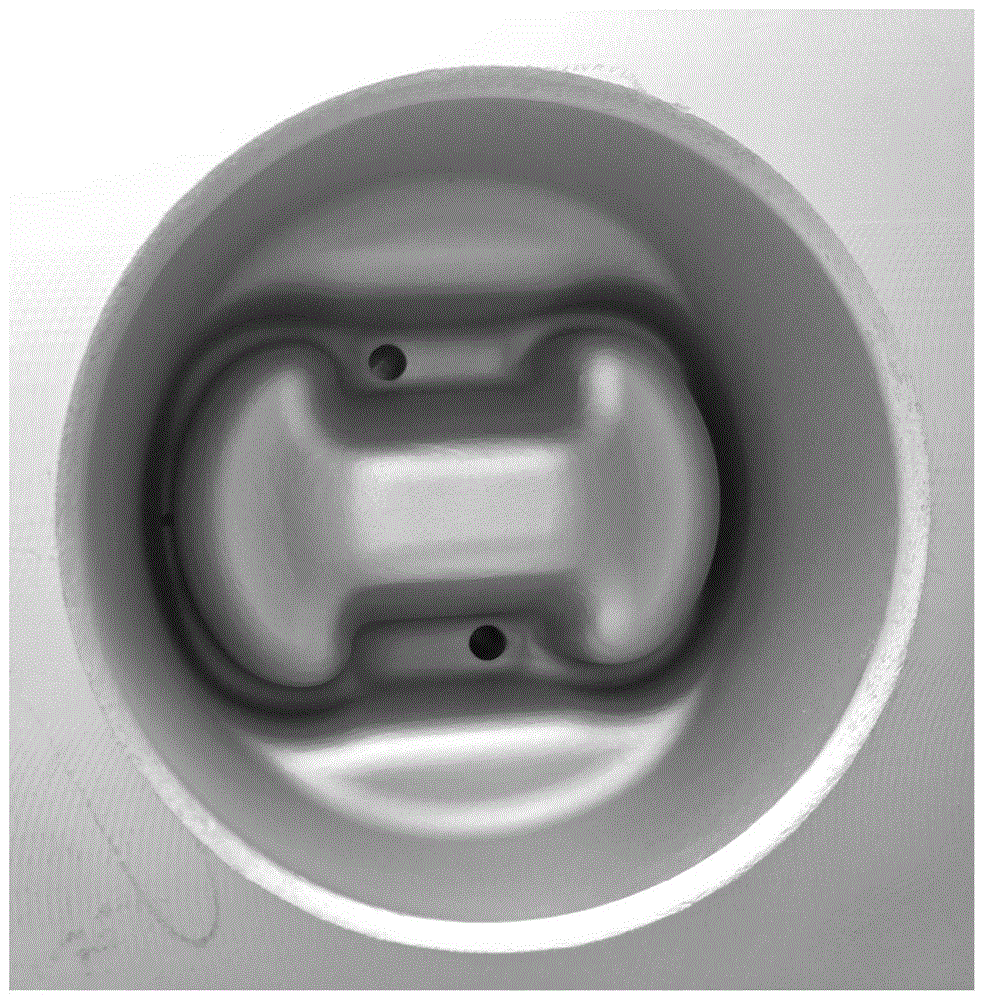
本发明涉及钢质活塞
技术领域:
,更具体地说,关于一种高寿命热锻钢质活塞模具制造方法。
背景技术:
:钢质模锻活塞在国内外市场呈现出井喷式需求。当今国内只有少数锻造企业已经在批量化生产钢质模锻活塞,但实际产能还远远满足不了市场潜在需求。以机器人、步进梁为代表的自动化技术是锻造行业“机器换人”技术发展趋势。目前人工热模锻压力机锻造生产线上批量生产常规钢质模锻活塞,当班8h的锻件产量为1100只左右,若是在全自动热模锻压力机锻造生产线上批量生产常规钢质模锻活塞,当班8h的锻件产量为1500只左右,而高寿命锻造模具是实现自动化锻造的前提和保证,也是锻造行业自动化生产中的共性难题和“卡脖子”技术瓶颈。热锻钢质活塞模具材料多是h13钢,使用寿命大多在3000次锻打范围内,模具在工作中承受着很大的压力和冲击载荷作用,而且冲击频率很高,模腔和高温金属接触,还要经受反复的加热和冷却,在急冷急热状态下,容易使模具的工作表面产生热疲劳裂纹,另外在顶杆凸台和活塞过渡位置与热坯料接触时间最长,出现早期开裂,导致使用寿命难以提高。现有研究主要集中在热锻钢质活塞模具结构设计及加工工艺的改进。经检索,公开号为cn105729079a的专利公开了“一种活塞锻造模具的加工方法”,通过对模具材料和加工工艺的改进,提高了模具的加工精度,减轻了模具的疲劳、裂纹现象,延长了模具的使用寿命,属于模具加工领域。授权公告号为cn211727343u的专利公开了“一种钢活塞锻造模具分块结构”,通过采用钢活塞锻造模具分块结构,提高模具寿命,实现了活塞产品批量生产。上述两项申请专利的技术,虽然可以小幅提高钢质活塞锻模寿命,但是对于热锻领域技术人员来说并没有解决上面提到的技术问题,且性价比都不高。技术实现要素:本发明所要解决的技术问题在于:如何解决现有技术中热锻钢质活塞模具使用寿命短的问题。本发明通过以下技术手段实现解决上述技术问题的:一种高寿命热锻钢质活塞模具制造方法,包括以下步骤:(1)热锻钢质活塞模具基体材料选择;(2)基体预处理:先对热锻钢质活塞模具基体的表面进行喷砂处理,然后对热锻钢质活塞模具基体进行研磨抛光20min,将抛光后热锻钢质活塞模具基体清洗后,置于100-120℃烘干机中烘干600-800s后备用;(3)将步骤(2)中经过预处理后的热锻钢质活塞模具基体进行表面硬化处理;(4)基体表面沉积zr基涂层:将模具有序妥当置于特定镀膜炉内,对炉内抽真空至5×10-2pa后开启辅助加热,待温度升至480℃,且炉腔真空达5×10-3后,开启弧电源引燃特制zr合金靶材开始沉积zr基涂层;沉积结束后,模具随炉冷却至室温后出炉。本发明通过对模具制造工艺的集成创新,包括热锻钢质活塞模具基体材料选择,依次进行基体预处理、基体表面硬化处理以及在基体表面沉积zr基涂层,基体表面硬化处理可提高模具表层硬度,为涂层提供了一个强有力的支撑层,zr基涂层的硬度高,组织较为致密,且空位等缺陷少,优异的耐腐蚀性能可以有效阻止乳喷石墨侵蚀模具基体;经小批量实验,对使用上述方法制备的热锻钢质活塞模具,其使用寿命大大提高,可使得锻造自动化生产线两天不停机,大大提高了工作效率。优选地,所述热锻钢质活塞模具基体材料包括h13钢材料或异于h13钢的材料;采用异于h13钢的新型模具钢,通过对微量元素进行调整,其使用寿命达到h13同等及以上水平,且价格和h13钢接近。优选地,所述h13钢材料的组分按重量百分比计为:c:0.32-0.45%、si:0.80-1.20%、mn:0.20-0.50%、s:≤0.030%、p:≤0.030%、cr:4.75-5.50%、mo:1.10-1.75%、v:0.80-1.20%。优选地,所述异于h13钢的材料的组分按重量百分比计为:c:0.35%、si:0.33%、mn:0.74%、s:0.006%、p:0.024%、cr:4.90%、ni:0.23%、cu:0.09%、mo:2.32%、al:0.009%、v:0.72%,余量为fe。优选地,所述异于h13钢的材料的组分按重量百分比计为:c:0.38%、si:0.52%、mn:0.45%、s:0.005%、p:0.02%、cr:5.05%、ni:0.20%、cu:0.07%、mo:1.41%、al:0.017%、v:0.38%,余量为fe。优选地,所述机体喷砂处理过程中,沙粒目数为220-320目的白刚玉、喷砂气压为0.4-0.6pa。优选地,所述基体抛光的方式包括双向磨粒流体抛光或利用机器人进行柔性抛光方法。优选地,所述双向磨粒流体抛光过程中,合模压力800-1000pa、工作压力为1200-1400pa;采用双向磨粒流体抛光技术研磨模具型腔,同时清洁了模具气孔、顶杆孔的微孔。优选地,所述基体清洗的方式包括喷淋清洗、超声清洗或漂洗;采用不同的清洗方式,深度清洁模具表面及型腔。优选地,所述基体表面硬化处理的方式包括离子渗氮、气体渗氮、碳氮共渗或激光表面淬火处理方法。本发明具有如下的有益效果:1、本发明通过对模具制造工艺的集成创新,包括热锻钢质活塞模具基体材料选择,依次进行基体预处理、基体表面硬化处理以及在基体表面沉积zr基涂层,基体表面硬化处理可提高模具表层硬度,为涂层提供了一个强有力的支撑层,zr基涂层的硬度高,组织较为致密,且空位等缺陷少,优异的耐腐蚀性能可以有效阻止乳喷石墨侵蚀模具基体;经小批量实验,对使用上述方法制备的热锻钢质活塞模具,其使用寿命大大提高,可使得锻造自动化生产线两天不停机,大大提高了工作效率。2、本发明倍数级提高锻造钢质活塞模具使用寿命,减少换模时间,提高生产效率,单位锻件成本降低30%以上。附图说明图1为本发明实施例1制造的热锻钢质活塞模具图;图2为本发明实施例1制造的热锻钢质活塞模具经3000次锻造后的状态图;图3为本发明对比例1-1制造的热锻钢质活塞模具图;图4为本发明对比例1-2未经处理的以h13钢作为基体的热锻钢质活塞模具图;图5为本发明对比例1-2热锻钢质活塞模具经2800次锻造后的状态图。具体实施方式为使本发明实施例的目的、技术方案和优点更加清楚,下面将结合本发明实施例和说明书附图,对本发明实施例中的技术方案进行清楚、完整地描述,显然,所描述的实施例是本发明一部分实施例,而不是全部的实施例。基于本发明中的实施例,本领域普通技术人员在没有作出创造性劳动前提下所获得的所有其他实施例,都属于本发明保护的范围。下述实施例中所用的试验材料和试剂等,如无特殊说明,均可从商业途径获得。实施例中未注明具体技术或条件者,均可以按照本领域内的文献所描述的技术或条件或者按照产品说明书进行。实施例1一种高寿命热锻钢质活塞模具制造方法,包括以下步骤:(1)选择h13钢作为热锻钢质活塞模具基体,其组分按重量百分比计为:c:0.32-0.45%、si:0.80-1.20%、mn:0.20-0.50%、s:≤0.030%、p:≤0.030%、cr:4.75-5.50%、mo:1.10-1.75%、v:0.80-1.20%;(2)基体预处理:选择320目的刚玉砂、0.6pa压力,对热锻钢质活塞模具基体的表面进行喷砂处理,然后利用磨粒抛光机对热锻钢质活塞模具基体进行研磨抛光20min,合模压力800pa、工作压力为1200pa,将抛光后热锻钢质活塞模具基体置于自动超声波清洗线中进行清洗后,100℃烘干机中烘干600s后备用;(3)将步骤(2)中经过预处理后的热锻钢质活塞模具基体有序妥当置于特定氮化炉内,对炉内抽真空至20-70pa后开启高压,增加占空比,逐渐增加氢气和氩气流量,将模具梯度加热至500℃,待温度到达500℃且保温一个小时后,往炉腔内通入氮气开始进行离子氮化,其比例为n2:h2=1:5,氮化时间为8h,氮化结束后,模具随炉冷却至室温后出炉;(4)将步骤(3)中经过表面硬化处理后的热锻钢质活塞模具基体有序妥当置于特定镀膜炉内,对炉内抽真空至5×10-2pa后开启辅助加热,待温度升至480℃,且炉腔真空达5×10-3后,开启弧电源引燃特制zr合金靶材开始沉积zr基涂层;沉积结束后,模具随炉冷却至室温后出炉,制造出的模具如图1所示。将本实施例制造的热锻钢质活塞模具投放于下游企业进行使用,对模具进行锻造处理,模具经3000次锻造后的状态如图2所示,可以发现模具经3000次锻造后其型腔过渡区未出现裂纹,在经过7700次锻造后其型腔过渡区出现裂纹。对比例1-1本对比例与实施例1的区别在于:选择h13钢作为热锻钢质活塞模具基体,将模具基体进行预处理和表面硬化处理后,不进行基体表面沉积zr基涂层处理,制造出的热锻钢质活塞模具如图3所示。将本对比例制造的热锻钢质活塞模具投放于下游企业进行使用,对该模具进行锻造处理,模具经3920次锻造后其型腔过渡区出现裂纹。对比例1-2本对比例与实施例1的区别在于:如图4所示,直接将h13钢作为热锻钢质活塞模具基体。将该模具直接投放于下游企业进行使用,对该模具进行锻造处理,如图5所示,该模具经2800次锻造后其型腔过渡区出现裂纹。实施例2一种高寿命热锻钢质活塞模具制造方法,包括以下步骤:(1)选择组分按重量百分比计为:c:0.35%、si:0.33%、mn:0.74%、s:0.006%、p:0.024%、cr:4.90%、ni:0.23%、cu:0.09%、mo:2.32%、al:0.009%、v:0.72%,余量为fe的材料作为热锻钢质活塞模具基体;(2)基体预处理:选择220目的刚玉砂、0.4pa压力,对热锻钢质活塞模具基体的表面进行喷砂处理,然后利用磨粒抛光机对热锻钢质活塞模具基体进行研磨抛光20min,合模压力900pa、工作压力为1300pa,将抛光后热锻钢质活塞模具基体置于自动超声波清洗线中进行清洗后,110℃烘干机中烘干700s后备用;(3)将步骤(2)中经过预处理后的热锻钢质活塞模具基体有序妥当置于特定氮化炉内,对炉内抽真空至20-70pa后开启高压,增加占空比,逐渐增加氢气和氩气流量,将模具梯度加热至500℃,待温度到达500℃且保温一个小时后,往炉腔内通入氮气开始进行离子氮化,其比例为n2:h2=1:5,氮化时间为8h,氮化结束后,模具随炉冷却至室温后出炉;(4)将步骤(3)中经过表面硬化处理后的热锻钢质活塞模具基体有序妥当置于特定镀膜炉内,对炉内抽真空至5×10-2pa后开启辅助加热,待温度升至480℃,且炉腔真空达5×10-3后,开启弧电源引燃特制zr合金靶材开始沉积zr基涂层;沉积结束后,模具随炉冷却至室温后出炉。将本实施例制造的热锻钢质活塞模具投放于下游企业进行使用,通过对制造的热锻钢质活塞模具进行锻造,发现本实施例工艺下制造的模具经经过6801次锻造后其型腔过渡区出现裂纹。对比例2本对比例与实施例2的区别在于:直接将实施例2中未经处理的热锻钢质活塞模具投放于下游企业进行使用,对该模具进行锻造处理,该模具经4352次锻造后其型腔过渡区出现裂纹。实施例3一种高寿命热锻钢质活塞模具制造方法,包括以下步骤:(1)选择组分按重量百分比计为:c:0.38%、si:0.52%、mn:0.45%、s:0.005%、p:0.02%、cr:5.05%、ni:0.20%、cu:0.07%、mo:1.41%、al:0.017%、v:0.38%,余量为fe的材料作为热锻钢质活塞模具基体;(2)基体预处理:选择320目的刚玉砂、0.6pa压力,对热锻钢质活塞模具基体的表面进行喷砂处理,然后利用磨粒抛光机对热锻钢质活塞模具基体进行研磨抛光20min,合模压力1000pa、工作压力为1300pa,将抛光后热锻钢质活塞模具基体置于自动超声波清洗线中进行清洗后,120℃烘干机中烘干800s后备用;(3)采用激光表面淬火的方法对步骤(2)中经过预处理后的热锻钢质活塞模具基体表面进行硬化处理;(4)将步骤(3)中经过表面硬化处理后的热锻钢质活塞模具基体有序妥当置于特定镀膜炉内,对炉内抽真空至5×10-2pa后开启辅助加热,待温度升至480℃,且炉腔真空达5×10-3后,开启弧电源引燃特制zr合金靶材开始沉积zr基涂层;沉积结束后,模具随炉冷却至室温后出炉。将本实施例制造的热锻钢质活塞模具投放于下游企业进行使用,通过对制造的热锻钢质活塞模具进行锻造,发现本实施例工艺下制造的模具经7281次锻造后,模具的型腔过渡区出现裂纹。对比例3本对比例与实施例3的区别在于:直接将实施例3中未经处理的热锻钢质活塞模具投放于下游企业进行使用,对该模具进行锻造处理,该模具经4756次锻造后其型腔过渡区出现裂纹。表1为上述实施例和对比例制造的模具的使用寿命统计结果组别使用寿命/可锻造次数实施例17700次对比例1-13920次对比例1-22800次实施例26801次对比例24352次实施例37281次对比例24756次综上所述,本发明通过对模具制造工艺的集成创新,包括热锻钢质活塞模具基体材料选择,依次进行基体预处理、基体表面硬化处理以及在基体表面沉积zr基涂层,基体表面硬化处理可提高模具表层硬度,为涂层提供了一个强有力的支撑层,zr基涂层的硬度高,组织较为致密,且空位等缺陷少,优异的耐腐蚀性能可以有效阻止乳喷石墨侵蚀模具基体;经小批量实验,对使用上述方法制备的热锻钢质活塞模具,其使用寿命大大提高,可使得锻造自动化生产线两天不停机,大大提高了工作效率。以上实施例仅用以说明本发明的技术方案,而非对其限制;尽管参照前述实施例对本发明进行了详细的说明,本领域的普通技术人员应当理解:其依然可以对前述各实施例所记载的技术方案进行修改,或者对其中部分技术特征进行等同替换;而这些修改或者替换,并不使相应技术方案的本质脱离本发明各实施例技术方案的精神和范围。当前第1页12