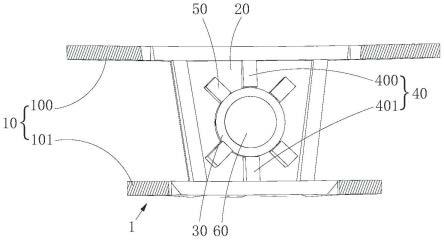
1.本发明涉及渣包及渣包制造方法,特别是涉及耳轴组件、渣包及渣包制造方法。
背景技术:2.国内外冶金企业大量使用渣包处理冶金渣,长期以来使用的是铸造渣包。焊接渣包技术诞生时间较短,与铸造渣包相比,具有焊接性能好、结构强度高、使用寿命长、制作环保、性价比高等显著优势,因此焊接渣包替代铸造渣包具有显著的经济效益和社会效益。本发明人在研究中发现,在焊接渣包的耳轴座组件结构降低成本上,还有潜力可挖。现有的耳轴在固定时采用销钉固定在立板上并在立板后面固定方形板以增加立板的整体强度。在立板后面设置方形板,会因为方形板的尺寸过大,制作方形板需要较多的材料而导致制作成本比较高。而且方形板尺寸大,需要焊接的焊缝总长度也比较长,焊接质量不好控制,焊接成本和难度比较高。在立板的侧面开设通孔让销钉通过,会因为立板的侧面薄,通孔深度较深,容易偏斜导致损坏立板。
技术实现要素:3.针对现有技术的不足,本发明要解决的技术问题是现有耳轴组件、渣包及渣包制造方法加工难度大、用料多以及制作成本高。为减少耳轴组件的材料使用并保持耳轴组件的结构强度不变,本发明提供了一种耳轴组件,耳轴组件包括:环板、立板、固定套、筋板、斜筋板和耳轴。所述立板设置有耳轴孔,所述立板固定于所述环板。所述固定套一端固定于所述立板。所述筋板固定于所述立板及所述环板,所述筋板固定于所述固定套的侧外壁。所述斜筋板固定于所述立板,所述斜筋板抵接于所述固定套的侧外壁。所述耳轴穿过所述耳轴孔以及所述固定套,并与所述耳轴孔以及所述固定套形成孔轴配合。
4.优选地,所述环板包括上环板和下环板,所述上环板和所述下环板间隔相对设置,所述上环板固定于所述立板的一端,所述下环板固定于所述立板的另一端。
5.优选地,所述固定套的径向设置有通孔。
6.优选地,所述耳轴的径向设置有销孔,所述销孔参照所述耳轴的中心轴线均布设置。
7.优选地,本发明还包括销钉,所述销钉一端固定于所述固定套,所述销钉另一端穿过所述通孔,并与所述通孔以及所述销孔孔轴配合。
8.优选地,所述筋板包括上筋板和下筋板,所述上筋板和所述下筋板间隔相对设置,所述上筋板和所述下筋板固定于所述立板,所述上筋板的一端固定于所述上环板,所述上筋板的另一端固定于所述固定套的侧外壁,所述下筋板的一端固定于所述下环板,所述下筋板的另一端固定于所述固定套的侧外壁。
9.优选地,所述斜筋板参照所述固定套的中心轴线均布设置。
10.为减少渣包的材料使用并保持渣包的结构强度不变,本发明还提供了一种渣包,包括:耳轴组件、罐体和主筋板,所述主筋板套设于所述罐体。所述耳轴组件参照所述罐体
的中心轴线均布设置,所述耳轴组件固定于所述罐体及所述主筋板。
11.优选地,所述筋板和所述斜筋板固定于所述罐体。
12.为减少渣包的材料使用并保持渣包的结构强度不变,本发明还提供了一种渣包制造方法,包括以下步骤:
13.耳轴预加工,包括耳轴锻造及无损检测和耳轴机加工;
14.立板预加工,包括立板下料、立板开设坡口以及立板镗孔;
15.耳轴与立板装配;
16.固定套套装到耳轴并安装销钉;
17.筋板以及环板分别与立板组焊;
18.除斜筋板外的耳轴组件与罐体组焊;
19.筋板与立板及罐体组焊;以及
20.检验。
21.本发明的有益效果在于:让环板、筋板、斜筋板以及固定套配合固定使用可以代替现有技术中的方形板,因为筋板、斜筋板以及固定套的尺寸比现有的方形板的尺寸小,所以节省了制作耳轴组件的材料,进而节省了制作耳轴组件材料成本,可以充分利用焊接渣包其它零件的边角余料制作筋板、斜筋板。筋板与立板、环板及固定套固定,斜筋板与立板、环板固定可以增强固定套的结构强度,使得耳轴组件材料用量减少的同时保持耳轴组件整体强度不变。
22.上述说明仅是本发明技术方案的概述,为了能够更清楚了解本发明的技术手段,并可依照说明书的内容予以实施,以下以本发明较佳的实施例并配合附图对本发明进行详细说明。
附图说明
23.图1是本发明第一实施例中,渣包立体图;
24.图2是本发明第一实施例中,渣包俯视图;
25.图3是本发明第一实施例中,渣包分解图;
26.图4是本发明第一及第二实施例中,渣包左视图;
27.图5是本发明第一实施例中,图2的a-a线视图;
28.图6是本发明第一实施例中,图5无环板视图;
29.图7是本发明第一实施例中,图6中无销钉b-b线视图;
30.图8是本发明第一实施例中,图6的含销钉b-b线视图;
31.图9是本发明第一实施例中,图6的c-c线视图;
32.图10是本发明第三实施例中,渣包制造方法方框图;
33.图11是本发明第三实施例中,耳轴预加工方框图;
34.图12是本发明第三实施例中,立板预加工方框图。
35.其中,附图标记:
36.1 耳轴组件
37.10 环板
38.100 上环板
39.101 下环板
40.20 立板
41.200 耳轴孔
42.30 固定套
43.300 通孔
44.40 筋板
45.400 上筋板
46.401 下筋板
47.50 斜筋板
48.60 耳轴
49.600 销孔
50.70 销钉
51.8 罐体
52.9 主筋板
53.s1-s8 步骤
54.s10-s11 为步骤s1的子步骤
55.s20-s22 为步骤s2的子步骤
具体实施方式
56.以下由特定的具体实施例说明本发明的实施方式,熟悉此技术的人士可由本说明书所公开的内容轻易地了解本发明的其他优点及功效。
57.需要说明的是,在不冲突的情况下,本技术中的实施例及实施例中的特征可以互相组合。下面将参考附图并结合实施例来详细说明本发明。为了使本技术领域的人员更好地理解本发明方案,下面将结合本发明实施例中的附图,对本发明实施例中的技术方案进行清楚、完整地描述,显然,所描述的实施例仅仅是本发明一部分的实施例,而不是全部的实施例。基于本发明的实施例,本领域普通技术人员在没有做出创造性劳动前提下所获得的所有其他实施例,都应当属于本发明保护的范围。
58.需要说明的是,本发明的说明书和权利要求书及上述附图中的术语“第一”、“第二”等是用于区别类似的对象,而不必用于描述特定的顺序或先后次序。此外,术语“包括”和“具有”以及他们的任何变形,意图在于包覆不排他的包含,例如,包含了一系列步骤或单元的过程、方法、系统、产品或设备不必限于清楚地列出的那些步骤或单元,而是可包括没有清楚地列出的或对于这些过程、方法、产品或设备固有的其他步骤或单元。
59.需要说明的是,除非另有明确的规定和限定,术语“安装”、“相连”、“连接”应做广义理解,例如,可以是固定连接,也可以是可拆卸连接,或一体地连接;可以是机械连接,也可以是电性连接;可以是直接相连,也可以通过中间媒介间接相连,可以是两个元件内部的连通。对于本领域的普通技术人员而言,可以具体情况理解上述术语在本发明中的具体含义。
60.第一实施例
61.请同时参照图1到图5,本实施例提供了一种耳轴组件1,耳轴组件1包括:环板10、
立板20、固定套30、筋板40、斜筋板50和耳轴60。立板20设置有耳轴孔200,立板20固定于环板10。例如,立板20可以采用焊接或一体成型的方式固定于环板10。固定套30一端固定于立板20。例如,固定套30一端可以通过焊接或一体成型的方式固定于立板20。筋板40固定于立板20及环板10,筋板40固定于固定套30的侧外壁。筋板40与环板10、固定套30的侧外壁的优选固定方式为焊接。斜筋板50固定于立板20,斜筋板50抵接于固定套30的侧外壁。斜筋板50与立板20的优选固定方式为焊接。耳轴60穿过耳轴孔200以及固定套30,并与耳轴孔200以及固定套30形成孔轴配合。让环板10、筋板40、斜筋板50以及固定套30配合使用可以代替现有技术中的方形板,因为筋板40、斜筋板50以及固定套30的尺寸比现有的方形板的尺寸小,所以节省了制作耳轴组件1的材料,进而节省了制作耳轴组件1材料成本,可以充分利用焊接渣包其它零件的边角余料制作筋板40、斜筋板50以及固定套30。筋板40与立板20、环板10及固定套30固定,斜筋板50与立板20、环板10固定可以增强固定套30的结构强度,使得耳轴组件1材料用量减少的同时保持耳轴组件1整体强度不变。
62.优选地,如图5所示,环板10包括上环板100和下环板101,上环板100和下环板101间隔设置,上环板100固定于立板20的一端,下环板101固定于立板20的另一端。上环板100及下环板101可以是平行配置。上环板100及下环板101与立板20的优选固定方式为焊接。
63.优选地,请同时参照图6和图7,固定套30的径向设置有通孔300。在固定套30的径向设置通孔300,因为固定套30的壁厚不大,所以在开孔时不容易发生偏斜。
64.优选地,请同时参照图6和图7,耳轴60的径向设置有销孔600。销孔600参照耳轴60的中心轴线均布设置。销孔600参照耳轴60的中心轴线对称设置有助于分散销孔600的受力,使得销孔600的受力更均匀。
65.优选地,请同时参照图7和图8,本实施例还包括销钉70,销钉70一端固定于固定套30,销钉70另一端穿过通孔300,并与通孔300以及销孔600孔轴配合。例如销钉70一端可以通过焊接的方式固定于固定套30。销钉70一端固定于固定套30,可以防止耳轴60转动时,销钉70从销孔600中掉出。销钉70可以选用标准件,制作简单,成本低。
66.优选地,请同时参照图5和图9,筋板40包括上筋板400和下筋板401,上筋板400和下筋板401间隔相对设置,上筋板400和下筋板401固定于立板20,上筋板400的一端固定于上环板100,上筋板400的另一端固定于固定套30的侧外壁,下筋板401的一端固定于下环板101,下筋板401的另一端固定于固定套30的侧外壁。上筋板400和下筋板401分别和固定套30的侧外壁接触,可以使得固定套30的受力更均匀。
67.优选地,如图5所示,斜筋板50参照固定套30的中心轴线均布设置,斜筋板50固定于立板20并与固定套30的侧外壁抵接。斜筋板50与固定套30的侧外壁抵接,可以承接来自固定套30的受力,增强固定套30的结构强度。斜筋板50的数量至少为四个,优选地,斜筋板50的数量为四个,参照固定套30的中心轴线均布设置。斜筋板50参照固定套30的中心轴线均布设置,有助于分散来自固定套30各个方向的受力,保护固定套30在各个方向不变形失效。
68.第二实施例
69.如图4所示,本实施例提供了一种渣包,包括:耳轴组件1、罐体8和主筋板9,主筋板9套设于罐体8,耳轴组件1参照罐体8的中心轴线均布设置,耳轴组件1固定于罐体8及主筋板9。例如,耳轴组件1可以采用焊接的方式固定于罐体8及主筋板9。耳轴组件1的数量至少
有两组,优选地,耳轴组件1的数量为两组,参照罐体8的中心轴线对称设置。因为耳轴组件1是渣包的一部分,耳轴组件1用料减少,会降低整个渣包的用料。按常用规格渣包计算,每套降本约1000元,按年产500套渣包计算,可以降本50万元。
70.优选地,请同时参照图4和图5,筋板40和斜筋板50固定于罐体1。筋板40和斜筋板50与罐体1的优选固定方式为焊接。因为筋板40和斜筋板50是耳轴组件的一部分,筋板40和斜筋板50固定于罐体1让耳轴组件1固定到了罐体1上。因为筋板40和斜筋板50的尺寸小,与罐体1固定时固定处尺寸也小,避免了现有技术中将耳轴60直接固定于罐体1,降低了耳轴组件1的固定难度。
71.第三实施例
72.请同时参照图10、图11和图12,本实施例提供了一种渣包制造方法,包括以下步骤:
73.s1:耳轴60预加工。步骤s1包括:s10:耳轴60锻造及无损检测;s11:耳轴60机加工。其中,步骤s10中的耳轴60锻造时,锻压比不小于4,粗加工后进行无损检测,例如使用超声波探伤进行无损检测。无损检测后再进行调质处理,然后再次进行无损检测。耳轴60精加工后,用定位套对固定套30进行定位,固定耳轴60及固定套30,加工出通孔300以及销孔600。然后对耳轴60再次无损检测。
74.s2:立板20预加工。s2包括以下步骤:s20:立板20下料;s21:立板20开设坡口,其中坡口开设可以采用机器人或坡口专用设备;s22:立板20镗孔。
75.s3:耳轴60与立板20装配。
76.s4:固定套30套装到耳轴60并安装销钉70。
77.s5:筋板40以及环板10分别与立板20组焊。
78.s6:除斜筋板50外的耳轴组件1与罐体8组焊。
79.s7:筋板40与立板20及罐体8组焊。
80.s8:检验。
81.以上所述组焊可以采用埋弧焊。焊材为:h10mn2+hj431。焊接参数如下:
[0082][0083]
焊接预热采用电加热或火焰加热法,焊前预热和层间温度为90℃~150℃。预热的加热区域应在焊接坡口两侧,宽度应各为焊件施焊处焊件的1.5倍以上,且不小于120mm。
[0084]
使用上述方法制作渣包,让筋板40、斜筋板50以及固定套30配合使用形成的耳轴组件1,会因为筋板40、斜筋板50以及固定套30的尺寸比现有的方形板的尺寸小,节省了制作耳轴组件1材料,进而节省了制作耳轴组件1材料成本,可以充分利用焊接渣包其它零件的边角余料制作筋板40、斜筋板50以及固定套30。因为耳轴组件1是渣包的一部分,耳轴组件1用料减少,会降低整个渣包的用料,以降低渣包的加工成本。筋板40与立板20、环板10及固定套30焊接,斜筋板50与立板20、环板10焊接可以增强固定套30的结构强度,使得耳轴组件1材料用量减少的同时保持耳轴组件1整体强度不变。
[0085]
以上对本发明实施例所提供的一种耳轴组件、渣包及渣包制造方法进行了详细介绍,对于本领域的一般技术人员,依据本发明实施例的思想,在具体实施方式及应用范围上
均会有所改变之处。综上所述,本说明书内容不应理解为对本发明的限制,凡依据本发明的精神与技术思想所做的一切等效修饰或改变,仍应由本发明的权利要求所涵盖。