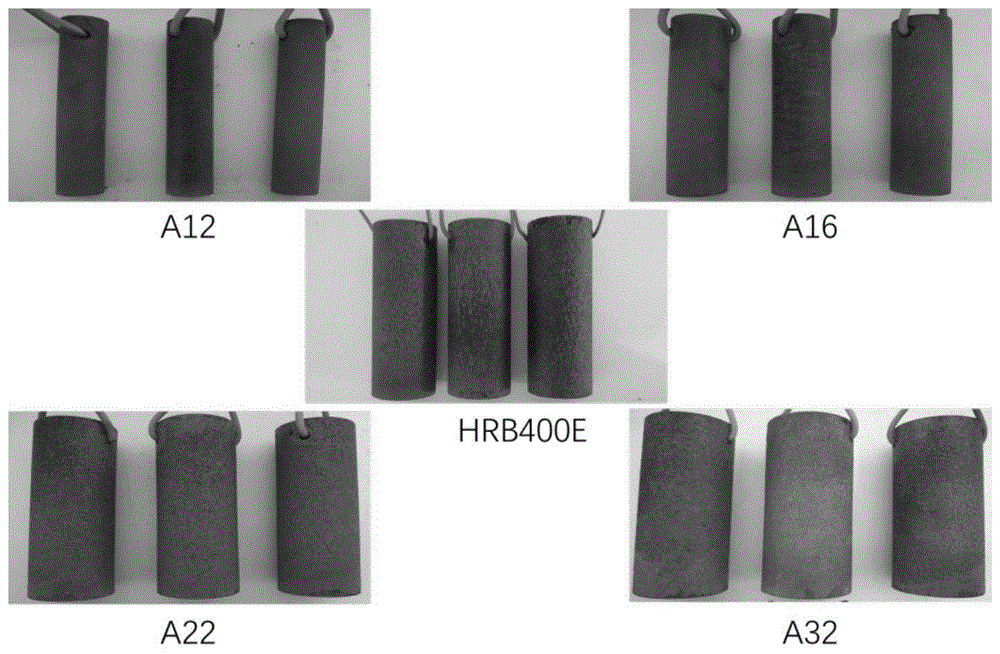
本发明涉及耐腐蚀钢筋
技术领域:
,具体为一种400mpa级耐工业大气腐蚀钢筋的制备方法。
背景技术:
:腐蚀被誉为材料的“癌症”,是全人类共同面对的难题,作为基建强国,国内建筑钢材的腐蚀破坏造成的严重经济损失数见不鲜。建筑钢材长期暴露于大气中,大气中的污染物等对钢材的腐蚀起到了加速作用,提高的建筑钢材的耐大气腐蚀性能意义重大。对于钢材来说,提高其耐蚀性最常见的方法是提高钢材自身的耐蚀性、表面涂镀层保护、牺牲阳极阴极保护等,采用不锈钢钢筋、不锈钢-碳钢复合钢筋、环氧树脂钢筋、镀锌钢筋等方法是提高钢筋耐蚀性的常见方法,其中不锈钢钢筋一般含有较多cr、ni、mo等合金元素,成本较高,不宜大规模使用;不锈钢-碳钢复合钢筋比起不锈钢成本大大下降,但其成本仍然远高于普通钢筋,其激光熔覆、喷射沉积、焊机、爆炸等复合方法不适宜大批量生产。轧制、旋压、拉拔挤压等压力加工手段不能保证覆层和基体金属良好的结合;环氧树脂钢筋、镀锌钢筋等涂镀钢筋等涂镀钢筋,施工困难,且其抗腐蚀效果主要取决于涂镀层,涂镀层自身的腐蚀或者破坏,使得其抗腐蚀寿命有限。典型的耐工业大气腐蚀钢筋工艺,如发明专利cn108286026a一种耐工业大气腐蚀钢筋及其制备方法设计了一种耐工业大气腐蚀钢筋,但其v含量远高于普通钒微合金钢筋,同时成本含包含了ni元素,这使得与普通钢筋相比,合金化成本有较大的增加;发明cn103233167a一种耐工业大气腐蚀钢筋及其生产方法,设计了一种无ni的耐工业大气腐蚀钢筋,其成分中碳含量包含了亚包晶区,连铸时亚包晶区成分的钢连铸时收缩不均匀,易诱发裂纹产生;发明专利cn103060541a一种表面纳米化耐蚀钢筋的连续加工方法,通过钢筋的表层附近组织纳米化,使得表面更易钝化从而增强钢筋的耐蚀性能,但并未从本质上增强钢筋的耐蚀性能。技术实现要素:本发明的目的在于提供一种400mpa级耐工业大气腐蚀钢筋的制备方法,以解决现有技术中耐工业大气腐蚀钢筋不能兼顾强度、耐蚀性能、焊接性能、成本等诸多因素,从而限制其推广应用的问题。一种400mpa级耐工业大气腐蚀钢筋的制备方法,主要包括以下制备步骤:铁水脱硫,转炉冶炼,吹氩,连铸,方坯加热,轧制,控冷和冷床空冷,其特征在于,所述铁水脱硫中控制出站铁水中硫含量s≤0.030%,所述转炉冶炼中出钢温度为1680~1720℃,出钢时间3~9min,出钢量约1/4~1/3时开始随钢流按照吨钢加入20~22kg硅锰铁,1.4~1.6kg碳化硅合金进行脱氧,然后按照吨钢加入0.2~0.8kg钒氮合金,0.1~0.5kg硅铁,0.15~0.45kg磷铁和2~10kg铜,在出钢约3/4的时候加完。作为优化,所述吹氩时间为5~8min,并在吹氩后调整c含量为0.18~0.21%,si含量为0.40~0.60%,mn含量为1.30~1.50%,p含量为0.08~0.15%,cu含量为0.20~0.40%,v含量为0.03~0.05%,n含量为0.008~0.012%。作为优化,所述连铸过程中采取保护浇注,控制过热度20~30℃,拉速为2.1±0.2m/min,并适当降低二冷区冷却强度,确保拉矫段温度950~1000℃。作为优化,所述方坯加热条件为方坯加热温度1000±20℃,加热时间130~160min,均热温度1100±20℃,均热时间20~30min,保证开轧时温度1050~1080℃。作为优化,所述轧制条件为粗轧开轧温度1050~1080℃,精轧开轧温度880~920℃,终轧温度900~950℃。作为优化,所述控冷条件为控制轧制后方坯上冷床温度为800~900℃。作为优化,所述400mpa级耐工业大气腐蚀钢筋的制备方法制得的400mpa级耐工业大气腐蚀钢筋中各组分质量百分比为:c:0.18~0.21%,si:0.40~0.60%,mn:1.30~1.50%,s:≤0.030%,p:0.08~0.15%,cu:0.20~0.40%,v:0.03~0.05%,n:0.008~0.012%,其余为fe及其他不可避免的杂质元素。与现有技术相比,本发明的有益效果是:本发明在制备400mpa级耐工业大气腐蚀钢筋时采用控制轧制和控制冷却技术,并在产品中加入铜。首先,本发明中加入的铜元素为改善耐蚀性能导电主要元素,与磷协同作用,可以细化锈层,同时使锈层致密,增强锈层对基体的保护效果;并且产品中无cr、ni、mo等元素,有效的控制了合金化成本;其次,耐工业大气腐蚀钢筋的成分组合有效的控制了碳当量,保证了钢筋的焊接性能;再者通过控制轧制和控制冷却技术,生产的钢筋表层具有一定的细晶区,使得腐蚀形成的锈层致密,同时促进了钢筋在腐蚀介质中的钝化,有效保护了基体,进一步增强了钢筋的耐蚀性能。附图说明图1:实施例1所得产品微表层晶粒度突变区处的微观组织图。图2:各实施例所得产品与普通抗震钢筋于浓度为0.01mol/l的nahso3中周浸72h后,不同规格钢筋加工的腐蚀试样的腐蚀外貌图;其中a12为实施例1所得产品,a16为实施例2所得产品,a22为实施例3所得产品,a32为实施例4所得产品,hrb400e为普通抗震钢筋。图3:各实施例所得产品与普通抗震钢筋周浸腐蚀除锈后,不同规格钢筋加工的腐蚀试样的外貌;其中a12为实施例1所得产品,a16为实施例2所得产品,a22为实施例3所得产品,a32为实施例4所得产品,e16为普通抗震钢筋。具体实施方式下面将结合本发明实施例,对本发明实施例中的技术方案进行清楚、完整地描述,显然,所描述的实施例仅仅是本发明一部分实施例,而不是全部的实施例。基于本发明中的实施例,本领域普通技术人员在没有做出创造性劳动前提下所获得的所有其他实施例,都属于本发明保护的范围。为了更清楚的说明本发明提供的方法通过以下实施例进行详细说明,在以下实施例中制作的400mpa级耐工业大气腐蚀钢筋的各指标测试方法如下:力学性能:用万能拉力机测量各实施例所得400mpa级耐工业大气腐蚀钢筋的力学性能。耐腐蚀性:将各实施例所得400mpa级耐工业大气腐蚀钢筋与普通抗震钢筋hrb400e按《yb/t4368-2014钢筋工业大气环境中腐蚀试验方法》在腐蚀液浓度为0.01mol/l的nahso3溶液周浸加速腐蚀72h后,测量腐蚀率,每组样品取三个试样测试,计算平均值。实施例1一种400mpa级耐工业大气腐蚀钢筋的制备方法,所述400mpa级耐工业大气腐蚀钢筋的制备方法主要包括以下制备步骤:(1)铁水脱硫:控制出站铁水硫含量s≤0.030%;(2)转炉冶炼:控制出钢温度为1700℃,出钢时间7min,出钢量约1/4时开始随钢流按照吨钢加入21kg硅锰铁,1.5kg碳化硅合金进行脱氧,然后按照吨钢加入0.6kg钒氮合金,0.4kg硅铁,0.3kg磷铁和8kg铜,在出钢约3/4的时候加完;(3)吹氩:吹氩7min后,调整步骤(2)出钢料中c含量为0.21%,si含量为0.46%,mn含量为1.38%,p含量为0.11%,cu含量为0.27%,v含量为0.039%,n含量为0.009%;(4)连铸:采用保护浇铸,低过热度连铸工艺,其中控制过热度26℃,拉速为2.1m/min,避免p偏析导致铸坯裂纹,确保拉矫段温度在980℃,以避开cu的单相脆性区,全程采用保护浇铸;(5)方坯加热:控制加热段温度1000℃,加热时间136min,均热段温度1100℃,均热时间25min,同时保证开轧时温度为1060℃;(6)轧制:采用四切分轧制方式,控制轧制时粗轧开轧温度1060℃,精轧开轧温度905℃,终轧温度940℃,线速度为12.8m/s;(7)控冷和冷床空冷:控制上冷床温度860℃,冷床上空冷。作为优化,步骤(6)所述轧制制得的钢筋坯料规格为φ12mm。作为优化,所述400mpa级耐工业大气腐蚀钢筋的制备方法制得的400mpa级耐工业大气腐蚀钢筋中各组分质量百分比为:c:0.21%,si:0.46%,mn:1.38%,s:≤0.030%,p:0.11%,cu:0.27%,v:0.039%,n:0.009%,其余为fe及其他不可避免的杂质元素。实施例2一种400mpa级耐工业大气腐蚀钢筋的制备方法,所述400mpa级耐工业大气腐蚀钢筋的制备方法主要包括以下制备步骤:(8)铁水脱硫:控制出站铁水硫含量s≤0.030%;(9)转炉冶炼:控制出钢温度为1700℃,出钢时间7min,出钢量约1/4时开始随钢流按照吨钢加入21kg硅锰铁,1.5kg碳化硅合金进行脱氧,然后按照吨钢加入0.6kg钒氮合金,0.4kg硅铁,0.3kg磷铁和8kg铜,在出钢约3/4的时候加完;(10)吹氩:吹氩7min后,调整步骤(2)出钢料中c含量为0.21%,si含量为0.49%,mn含量为1.46%,p含量为0.10%,cu含量为0.29%,v含量为0.04%,n含量为0.009%;(11)连铸:采用保护浇铸,低过热度连铸工艺,其中控制过热度26℃,拉速为2.1m/min,避免p偏析导致铸坯裂纹,确保拉矫段温度在980℃,以避开cu的单相脆性区,全程采用保护浇铸;(12)方坯加热:控制加热段温度1000℃,加热时间155min,均热段温度1100℃,均热时间29min,同时保证开轧时温度为1060℃;(13)轧制:采用三切分轧制方式,控制轧制时粗轧开轧温度1060℃,精轧开轧温度905℃,终轧温度940℃,线速度为10.6m/s;(14)控冷和冷床空冷:控制上冷床温度860℃,冷床上空冷。作为优化,步骤(6)所述轧制制得的钢筋坯料规格为φ16mm。作为优化,所述400mpa级耐工业大气腐蚀钢筋的制备方法制得的400mpa级耐工业大气腐蚀钢筋中各组分质量百分比为:c:0.21%,si:0.49%,mn:1.46%,s:≤0.030%,p:0.10%,cu:0.29%,v:0.04%,n:0.009%,其余为fe及其他不可避免的杂质元素。实施例3一种400mpa级耐工业大气腐蚀钢筋的制备方法,所述400mpa级耐工业大气腐蚀钢筋的制备方法主要包括以下制备步骤:(8)铁水脱硫:控制出站铁水硫含量s≤0.030%;(9)转炉冶炼:控制出钢温度为1700℃,出钢时间7min,出钢量约1/4时开始随钢流按照吨钢加入21kg硅锰铁,1.5kg碳化硅合金进行脱氧,然后按照吨钢加入0.6kg钒氮合金,0.4kg硅铁,0.3kg磷铁和8kg铜,在出钢约3/4的时候加完;(10)吹氩:吹氩7min后,调整步骤(2)出钢料中c含量为0.18%,si含量为0.51%,mn含量为1.45%,p含量为0.12%,cu含量为0.30%,v含量为0.043%,n含量为0.009%;(11)连铸:采用保护浇铸,低过热度连铸工艺,其中控制过热度26℃,拉速为2.1m/min,避免p偏析导致铸坯裂纹,确保拉矫段温度在980℃,以避开cu的单相脆性区,全程采用保护浇铸;(12)方坯加热:控制加热段温度1000℃,加热时间141min,均热段温度1100℃,均热时间26min,同时保证开轧时温度为1060℃;(13)轧制:采用二切分轧制方式,控制轧制时粗轧开轧温度1060℃,精轧开轧温度905℃,终轧温度940℃,线速度为8.5m/s;(14)控冷和冷床空冷:控制上冷床温度860℃,冷床上空冷。作为优化,步骤(6)所述轧制制得的钢筋坯料规格为作为优化,所述400mpa级耐工业大气腐蚀钢筋的制备方法制得的400mpa级耐工业大气腐蚀钢筋中各组分质量百分比为:c:0.18%,si:0.51%,mn:1.45%,s:≤0.030%,p:0.12%,cu:0.30%,v:0.043%,n:0.009%,其余为fe及其他不可避免的杂质元素。实施例4一种400mpa级耐工业大气腐蚀钢筋的制备方法,所述400mpa级耐工业大气腐蚀钢筋的制备方法主要包括以下制备步骤:(8)铁水脱硫:控制出站铁水硫含量s≤0.030%;(9)转炉冶炼:控制出钢温度为1700℃,出钢时间7min,出钢量约1/4时开始随钢流按照吨钢加入21kg硅锰铁,1.5kg碳化硅合金进行脱氧,然后按照吨钢加入0.6kg钒氮合金,0.4kg硅铁,0.3kg磷铁和8kg铜,在出钢约3/4的时候加完;(10)吹氩:吹氩7min后,调整步骤(2)出钢料中c含量为0.19%,si含量为0.50%,mn含量为1.45%,p含量为0.11%,cu含量为0.25%,v含量为0.042%,n含量为0.009%;(11)连铸:采用保护浇铸,低过热度连铸工艺,其中控制过热度26℃,拉速为2.1m/min,避免p偏析导致铸坯裂纹,确保拉矫段温度在980℃,以避开cu的单相脆性区,全程采用保护浇铸;(12)方坯加热:控制加热段温度1000℃,加热时间141min,均热段温度1100℃,均热时间26min,同时保证开轧时温度为1060℃;(13)轧制:采用单线轧制方式,控制轧制时粗轧开轧温度1060℃,精轧开轧温度905℃,终轧温度940℃,线速度为8m/s;(14)控冷和冷床空冷:控制上冷床温度860℃,冷床上空冷。作为优化,步骤(6)所述轧制制得的钢筋坯料规格为作为优化,所述400mpa级耐工业大气腐蚀钢筋的制备方法制得的400mpa级耐工业大气腐蚀钢筋中各组分质量百分比为:c:0.19%,si:0.50%,mn:1.45%,s:≤0.030%,p:0.11%,cu:0.25%,v:0.042%,n:0.009%,其余为fe及其他不可避免的杂质元素。效果例1下表1给出了采用本发明实施例1至4所得400mpa级耐工业大气腐蚀钢筋的力学性能分析结果。表1效果例2下表2给出了采用本发明实施例1至4所得400mpa级耐工业大气腐蚀钢筋的耐腐蚀性能分析结果。表2钢种耐候指数(i)平均腐蚀率(g/m2·h)hrb400e1.774.35实施例17.171.51实施例27.191.65实施例37.631.64实施例47.061.82从表1和表2中各实施例实验数据表面,本发明制备的各规格耐工业大气腐蚀钢筋的钢筋都具备良好的力学性能,且与普通抗震钢筋hrb400e的相对腐蚀率在34.71%~41.84%之间,即耐蚀性能是普通钢筋的2~3倍,具备优良的耐腐蚀性能。对于本领域技术人员而言,显然本发明不限于上述示范性实施例的细节,而且在不背离本发明的精神或基本特征的情况下,能够以其他的具体形式实现本发明。因此,无论从哪一点来看,均应将实施例看作是示范性的,而且是非限制性的,本发明的范围由所附权利要求而不是上述说明限定,因此旨在将落在权利要求的等同要件的含义和范围内的所有变化囊括在本发明内。不应将权利要求中的任何标记视为限制所涉及的权利要求。当前第1页12