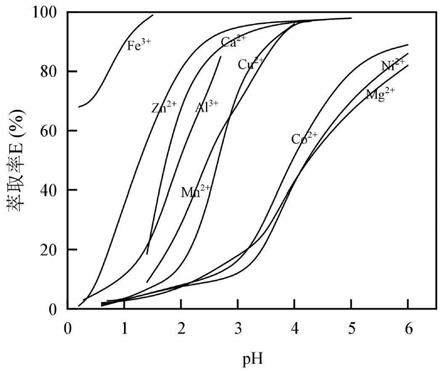
二(2
‑
乙基己基)磷酸酯萃取剂的预处理方法与萃取方法
技术领域
1.本发明涉及萃取剂的技术领域,更具体地,涉及酸性萃取剂二(2
‑
乙基己基)磷酸酯的技术领域。
背景技术:2.二(2
‑
乙基己基)磷酸酯(p204)是一种酸性萃取剂,在75%乙醇水溶液中的pk
a
值为3.42,可与多种金属离子结合,广泛应用于金属的萃取分离。p204对不同金属离子的萃取率与料液的酸度有关,其萃取常见金属离子的顺序如说明书附图1所示。因此,在控制料液酸度的条件下,萃取剂p204可使不同金属离子实现萃取分离。例如,萃取剂p204可从含锌料液中萃取锌而实现与铜、锰的分离,从含钴料液中萃取铜、锰而达到从料液中除杂的目的。
3.然而,p204在萃取过程中发生金属离子与h
+
的交换反应,如反应式(1)所示,使料液ph值下降,显著降低待萃取金属离子的萃取率。为提高p204的萃取率,现有技术常采用强碱对萃取剂进行皂化处理,将部分萃取剂转化为钠盐后再进行萃取。
[0004][0005]
经过皂化处理的萃取剂在萃取时,料液ph值下降得到有效控制,可以获得较高的萃取率。
[0006]
但皂化p204萃取时可能引起料液ph值上升,使萃取顺序排在待萃取金属离子之后的金属离子的共萃取程度增加,进而影响金属离子的分离效果。如皂化后的p204在萃取锰时,料液中共存的钴萃取率上升。为降低共萃取程度,常采用加酸对料液中的h
+
进行补充的技术手段。
[0007]
上述通过强碱皂化处理酸性萃取剂的方法,存在以下弊端:(1)每次进行萃取剂的皂化处理都要求重新配制强碱溶液;(2)当萃取剂的皂化率相对过高时,萃取过程中需要用酸对料液的ph值进行调控,额外增加酸的消耗,并产生高盐废水。
技术实现要素:[0008]
本发明的目的在于提供一种新的萃取剂预处理方法及相应的萃取方法,其可有效替换现有的强碱皂化工艺、简化皂化工艺和萃取工艺,降低萃取过程中酸碱的消耗以及二次污染物的排放,同时在多种金属离子的萃取分离中广泛适用,对多种金属离子均具有较高的萃取分离效率和循环利用率。
[0009]
本发明首先公开了如下的技术方案:
[0010]
二(2
‑
乙基己基)磷酸酯萃取剂的预处理方法,其包括:通过作为预处理剂的缓冲溶液对酸性萃取剂二(2
‑
乙基己基)磷酸酯进行预处理,得到预处理后的萃取剂,其中,所述缓冲溶液的浓度为1
‑
5mol/l、且ph值为3.6~5.0。
[0011]
根据本发明的一些优选实施方式,所述缓冲溶液包括甲酸
‑
甲酸盐、乙酸
‑
乙酸盐、乳酸
‑
乳酸盐、酒石酸的酸式盐中的一种或多种。
[0012]
根据本发明的一些优选实施方式,所述盐选自钠盐。
[0013]
根据本发明的一些优选实施方式,所述萃取剂的预处理方法包括以下步骤:
[0014]
通过稀释剂将所述二(2
‑
乙基己基)磷酸酯配制为适当浓度的有机溶液;
[0015]
将所述预处理剂与所得有机溶液等体积比混合,其后静置分相,所得有机相即为预处理后的萃取剂有机相。
[0016]
根据本发明的一些优选实施方式,所述稀释剂选自磺化煤油。
[0017]
根据本发明的一些优选实施方式,所述有机溶液中所述萃取剂的浓度为0.2
‑
0.5mol/l。
[0018]
根据本发明的一些优选实施方式,所述预处理剂与所述有机溶液的混合时间为10
‑
20min。
[0019]
根据本发明的一些优选实施方式,所述静置分相后得到的水相溶液用作所述预处理剂,进行循环使用。
[0020]
本发明进一步公开了一种萃取方法,其包括:将经上述预处理方法得到的所述预处理后的萃取剂有机相加入含多种金属离子的混合料液的稀硫酸水溶液中,在常温下进行萃取,其中,有机相与水相的体积比为1:1。
[0021]
根据本发明的一些优选实施方式,所述混合料液含有钴、锰、铜、锌金属离子中的一种或多种。
[0022]
根据本发明的一些优选实施方式,所述萃取剂有机相为通过3mol/l的预处理剂缓冲溶液对0.2
‑
0.5mol/l的萃取剂二(2
‑
乙基己基)磷酸酯的磺化煤油有机溶液进行所述预处理得到,所述混合金属离子料液的稀硫酸溶液的ph值为2.7
‑
4.6。
[0023]
本发明具备以下有益效果:
[0024]
本发明提供的萃取剂预处理方法,预处理剂可多次循环对萃取剂p204进行预处理,无需在每次处理萃取剂时重新配制,仅当多次使用后、其ph值偏离正常范围时,加入naoh调整其ph值又可正常使用。相对于现有技术中的强碱皂化的预处理方法,可大大简化萃取剂的皂化工艺、提高工效。
[0025]
本发明提供的萃取剂预处理方法,萃取剂的皂化率通过缓冲溶液的种类、浓度、ph值等参数进行调控。相对于强碱皂化萃取剂只能通过萃取剂与naoh的投料比控制皂化率的方法,更容易控制萃取剂的皂化率以达到理想的萃取分离效果。
[0026]
本发明提供的预处理方法及萃取方法,在萃取过程中不需对料液ph值进行调控,萃取工艺得到简化,同时基本无高盐废水的产生。
[0027]
本发明提供的预处理方法及萃取方法,所用预处理剂未加入料液中,可以重复循环利用,且不会产生含有机物的萃取废水。
[0028]
通过本发明的优选实施方式对含锰、钴的混合料液进行萃取时,所得锰一级萃取率在90%以上,所得钴、锰的分离因子可达67以上。
[0029]
通过本发明的优选实施方式对含铜、钴的混合料液进行萃取时,所得铜一级萃取率在85%以上,所得钴、铜的分离因子可达77以上。
[0030]
通过本发明的优选实施方式对含锌、铜的混合料液进行萃取时,所得锌一级萃取率在85%以上,所得锌、铜的分离因子可达92以上。
[0031]
通过本发明的优选实施方式对含锌、锰的混合料液进行萃取时,所得锌一级萃取率在85%以上,所得锌、锰的分离因子可达1370以上。
附图说明
[0032]
图1为不同ph值下p204萃取金属的顺序。
具体实施方式
[0033]
以下结合实施例和附图对本发明进行详细描述,但需要理解的是,所述实施例和附图仅用于对本发明进行示例性的描述,而并不能对本发明的保护范围构成任何限制。所有包含在本发明的发明宗旨范围内的合理的变换和组合均落入本发明的保护范围。
[0034]
实施例1
[0035]
通过乙酸缓冲溶液预处理萃取剂p204:
[0036]
以磺化煤油为稀释剂,将萃取剂p204配制成浓度为0.25mol/l的有机相;
[0037]
使用总浓度为3mol/l、ph为4.27的hac
‑
naac水溶液与上述萃取剂有机相等体积比混合15min,其后静置分相,取所得有机相作为预处理后的萃取剂,剩余的水相循环用于对p204的预处理,对多次循环预处理后得到的水相,即预处理液的ph值进行测试,其结果如表1所示:
[0038]
表1循环使用次数对预处理溶液ph值的影响
[0039][0040]
可以看出,预处理溶液具有较高的缓冲容量,对p204释放的h
+
具有良好的缓冲作用。每次处理萃取剂后,ph值略降。
[0041]
实施例2
[0042]
将实施例1所得预处理后的萃取剂对钴、锰混合料液进行萃取分离,其中料液为含2g/l co
2+
和2g/l mn
2+
的稀硫酸水溶液,萃取条件为:温度25℃、相比o/a为1∶1,萃取平衡时间为15min,锰、钴萃取分离结果如表2所示:
[0043]
表2锰、钴萃取分离结果
[0044][0045]
可以看出,料液初始ph值在3.60~4.60范围内的料液所得萃余液ph值相近,萃取效果相当。因此,萃取前不需严格控制料液酸度,萃取过程中亦不需添加任何酸、碱进行酸度调节。分离所得锰的一级萃取率>90%,萃取效率高;锰、钴分离因子56~68,具有较高的分离效果。
[0046]
实施例3
[0047]
按实施例1相同的预处理方法处理0.25mol/l的p204,仅改变预处理溶液的ph值为3.64。预处理后的萃取剂对上述钴、锰混合料液进行萃取分离,料液的ph=4.00,co
2+
和mn
2+
的浓度均为2g/l,萃取条件与实施例2相同。萃取后,萃余液ph值为3.16,锰、钴的萃取率分别为89.5%、13.3%,分离因子为55.5。
[0048]
实施例4
[0049]
按实施例1相同的预处理过程处理0.25mol/l的p204,仅改变预处理溶液的ph值为4.42。预处理后的萃取剂对上述钴、锰混合料液进行萃取分离,料液的ph=4.00,co
2+
和mn
2+
的浓度均为2g/l,萃取条件与实施例2相同。萃取后,萃余液ph值为3.80,锰、钴的萃取率分别为97.0%、37.1%,分离因子为54.4。
[0050]
可见,预处理溶液的ph值对p204萃取分离co
2+
、mn
2+
的效果存在一定影响;预处理溶液的ph值在3.60~4.40范围内,均可获得较好的co
2+
、mn
2+
分离效果。
[0051]
实施例5
[0052]
甲酸缓冲溶液预处理p204萃取分离锰、钴:
[0053]
使用浓度为3mol/l、ph为4.42的hcooh
‑
hcoona水溶液与0.25mol/lp204有机相等体积比混合15min,其后静置分相,所得有机相作为预处理后的萃取剂,对钴、锰混合料液进行萃取分离,其中料液为含2.4g/l co
2+
和2.5g/l mn
2+
的稀硫酸水溶液,萃取条件同实施例2,锰、钴萃取分离结果如表3所示:
[0054]
表3锰、钴萃取分离结果
[0055][0056]
可以看出,使用甲酸缓冲溶液处理萃取剂,与相同浓度、相同ph值的乙酸缓冲溶液处理萃取剂,锰、钴的萃取分离效果相当。
[0057]
实施例6
[0058]
甲酸缓冲溶液预处理p204萃取分离铜、钴:
[0059]
以磺化煤油为稀释剂,将萃取剂p204配制成浓度为0.25mol/l的有机相;使用浓度为3mol/l、ph为4.01的hcooh
‑
hcoona水溶液与上述萃取剂有机相等体积比混合15min,其后静置分相,取所得有机相作为预处理后的萃取剂。
[0060]
将上述所得预处理后的萃取剂对铜、钴混合料液进行萃取分离,其中料液为含1.9g/l cu
2+
和2.0g/l co
2+
的稀硫酸水溶液,萃取条件为:温度25℃、相比o/a为1∶1,萃取平衡时间为15min。铜、钴萃取分离结果如表4所示:
[0061]
表4铜、钴萃取分离结果
[0062][0063]
可以看出,料液初始ph值在2.90~4.00范围内,所得萃余液ph值相近,萃取效果相当。分离所得铜的一级萃取率>80%,而钴的一级萃取率<10%,萃取效率高;铜、钴分离因子47~77,具有较高的分离效果。
[0064]
实施例7
[0065]
乙酸缓冲溶液预处理p204萃取分离锌、铜:
[0066]
以磺化煤油为稀释剂,将萃取剂p204配制成浓度为0.5mol/l的有机相;使用浓度为3mol/l、ph为4.55的hac
‑
naac水溶液与上述萃取剂有机相等体积比混合15min,其后静置分相,取所得有机相作为预处理后的萃取剂。
[0067]
将上述所得预处理后的萃取剂对锌、铜混合料液进行萃取分离,其中料液为含11.1g/l zn
2+
和3.8g/l cu
2+
的稀硫酸水溶液,萃取条件为:温度25℃、相比o/a为1∶1,萃取平衡时间为15min。锌、铜萃取分离结果如表5所示:
[0068]
表5锌、铜萃取分离结果
[0069][0070][0071]
料液初始ph值在2.70~3.85范围内,所得萃余液ph值相近,萃取效果相当。分离所得锌的一级萃取率>85%,萃取效率高;锌、铜分离因子73~92,具有较高的分离效果。
[0072]
进一步的,用不同ph值的3mol/l hac
‑
naac水溶液对p204进行预处理,对p204萃取分离zn
2+
、cu
2+
的效果存在一定影响。但预处理溶液的ph值在4.0~5.0范围内,均可获得较好的zn
2+
、cu
2+
分离效果。
[0073]
实施例8
[0074]
萃取分离锌、锰:
[0075]
以磺化煤油为稀释剂,将萃取剂p204配制成浓度为0.5mol/l的有机相;使用浓度为3mol/l、ph为4.85的hac
‑
naac水溶液与上述萃取剂有机相等体积比混合15min,其后静置分相,取所得有机相作为预处理后的萃取剂。
[0076]
将上述所得预处理后的萃取剂对锌、锰混合料液进行萃取分离,其中料液为含10.4g/l zn
2+
和4.3g/l mn
2+
的稀硫酸水溶液,萃取条件为:温度25℃、相比o/a为1∶1,萃取
平衡时间为15min。锌、锰萃取分离结果如表6所示:
[0077]
表6锌、锰萃取分离结果
[0078][0079]
分离所得锌的一级萃取率达90%左右,萃取效率高;锌、锰分离因子218~1375,具有极高的分离效果。
[0080]
对比例1
[0081]
使用未经任何处理的0.25mol/l的p204作为萃取剂直接萃取ph值分别为3.64、4.00、4.18、4.55的含2g/lmn
2+
的稀硫酸水溶液,萃取条件与实施例2的萃取条件相同。萃取结果如表7所示:
[0082]
表7未处理p204对锰的萃取率
[0083]
料液初始ph萃余液phmn萃取率(%)3.642.0031.44.002.0032.84.182.0028.04.552.0030.4
[0084]
可以看出,萃取时,由于p204释放h+,使料液ph值下降,锰的萃取率过低。
[0085]
对比例2
[0086]
使用naoh对0.25mol/l的p204进行皂化处理,皂化率50%,其后使用处理后的萃取剂对ph值分别为3.64、4.00、4.18、4.55的含2g/lco
2+
和2g/l的mn
2+
的稀硫酸水溶液进行萃取,萃取条件与实施例2的萃取条件相同。萃取结果如下表8所示:
[0087]
表8 50%皂化的p204萃取锰、钴的萃取率
[0088]
料液初始ph萃余液phmn萃取率(%)co萃取率(%)3.644.2797.454.84.004.2798.262.94.184.3297.251.24.554.2497.655.6
[0089]
可以看出,用氢氧化钠皂化的p204进行萃取后,萃余液ph>4.2,锰的萃取率较高,但钴的萃取率>50%,分离效果不佳。
[0090]
对比例3
[0091]
分别使用未经任何处理的0.25mol/l的p204和经naoh皂化处理的0.25mol/l p204作为萃取剂,对实施例6的铜、钴混合料液(ph=3.99)进行萃取,不改变萃取条件,萃取结果
如表9所示:
[0092]
表9 naoh皂化p204对铜、钴萃取分离效果的影响
[0093][0094]
可见,未皂化p204对铜的萃取率太低。naoh皂化p204可以提高铜的萃取率,但铜、钴的分离效果远低于本发明的分离效果。
[0095]
对比例4
[0096]
分别使用未经任何处理的0.5mol/l的p204和经naoh皂化处理的0.5mol/l p204作为萃取剂,对实施例7的锌、铜混合料液(ph=3.16)进行萃取,不改变萃取条件,萃取结果如表10所示:
[0097]
表10 naoh皂化p204对锌、铜萃取分离效果的影响
[0098][0099]
可见,未皂化p204对锌的萃取率太低。naoh皂化p204可以提高锌的萃取率,但锌、铜的分离效果远低于本发明的分离效果。
[0100]
对比例5
[0101]
分别使用未经任何处理的0.5mol/l的p204和经naoh皂化处理的0.5mol/l p204作为萃取剂,对实施例8的锌、锰混合料液(ph=3.52)进行萃取,不改变萃取条件,萃取结果如表11所示:
[0102]
表11 naoh皂化p204对锌、锰萃取分离效果的影响
[0103][0104][0105]
可见,未皂化p204对锌的萃取率太低。naoh皂化p204可以提高锌的萃取率,但锌、锰的分离效果远低于本发明的萃取分离效果。
[0106]
以上实施例仅是本发明的优选实施方式,本发明的保护范围并不仅局限于上述实施例。凡属于本发明思路下的技术方案均属于本发明的保护范围。应该指出,对于本技术领域的普通技术人员来说,在不脱离本发明原理的前提下的改进和润饰,这些改进和润饰也应视为本发明的保护范围。