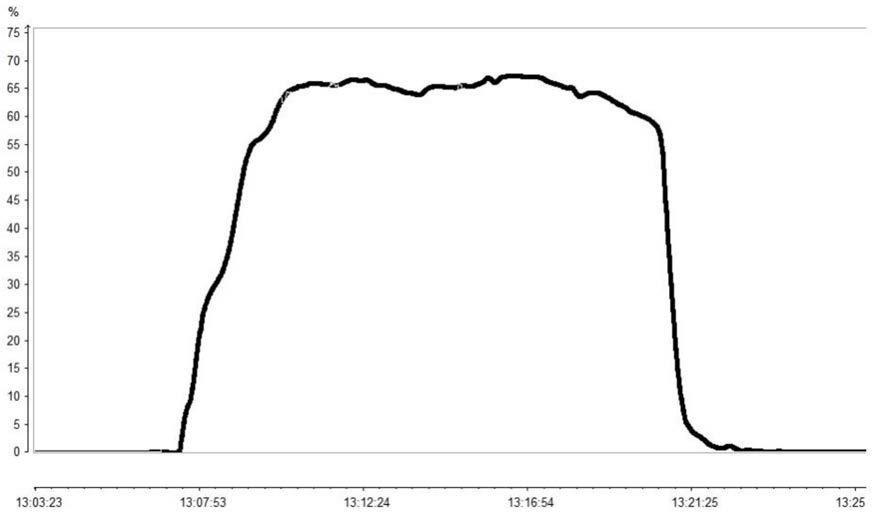
一种低碳lf炉工艺钢转炉冶炼方法
技术领域
1.本发明涉及转炉炼钢技术领域,具体为一种低碳lf炉工艺钢转炉冶炼方法。
背景技术:2.节能降耗是建设资源节约型、环境友好型社会的必然选择,是推进经济结构调整、转变发展方式的必由之路。传热的基本方式有热传导、热对流和热辐射三种,其对应傅里叶定律、牛顿冷却公式、斯忒藩
‑‑
玻耳兹曼定律,如式(1)、(2)、(3),结合式(1)
‑
(3)可知,缩短冶炼工序周期减少过程散热是降低能源消耗的重要途径之一。
3.(a)热传导傅里叶定律:
[0004][0005]
λ
‑‑
比例常数,导热率(导热系数)。
[0006]
(b)对流传热牛顿冷却公式:
[0007]
q=hδt w/m2ꢀꢀꢀꢀꢀꢀꢀꢀꢀꢀꢀꢀ
(2)
[0008]
h
‑‑
比例系数(表面传热系数)单位w/(m2·
k)。
[0009]
h的物理意义:单位温差作用下通过单位面积的热流量。
[0010]
(c)辐射传热斯忒藩
‑‑
玻耳兹曼定律:
[0011]
e=εσt
4 w/m2ꢀꢀꢀꢀꢀꢀꢀꢀꢀꢀꢀ
(3)
[0012]
t
‑‑
黑体的热力学温度k;
[0013]
σ
‑‑
斯忒潘—玻耳兹曼常数(黑体辐射常数),5.67
×
10
‑
8w/(m2·
k);
[0014]
ε
‑‑
辐射表面积m2。
[0015]
转炉炼钢过程实际的脱碳速度是“两头慢,中间快”。吹炼初期脱碳速度随吹炼时间几乎成直线增加,吹炼中期脱碳速度几乎只取决于供氧强度。当碳的含量降到一定程度后,碳的扩散速度下降了,碳的氧化速度急剧下降,这时的氧化速度与吹炼初期相似,但取决于碳的浓度和扩散速度,并与含碳量成正比。冶炼初期和冶炼低碳钢的末期由于脱碳反应缓慢,生成的一氧化碳很少,因此熔池的搅拌很弱,结果冶金反应随之减慢,很难趋近于平衡状态,这是氧气顶吹转炉炼钢法工艺本身的弱点。采用复合吹炼法后,由于有底吹气体强化了金属熔池的搅拌,使冶炼反应比较容易趋近于平衡状态,从而克服了单纯顶吹的弱点。其结果是降低钢铁料消耗,并节约铁合金的用量,有利于低碳钢的冶炼和减少造渣材料的用量。顶底复吹转炉在炉底安装底吹供气元件,由底吹供气元件向转炉炉内喷吹氮气/氩气等气体搅拌金属熔池。底吹气体搅拌促进了熔池内渣
‑
钢反应趋于平衡,改善了冶炼动力学条件,冶炼终点碳氧积低,且复吹转炉底吹搅拌强度越大,终点碳氧积越低。
[0016]
铁水预处理
‑
转炉
‑
lf炉
‑
连铸工艺流程生产时,由于lf炉具有电极升温功能,对于转炉出钢温度的适应性强。转炉生产遇到副枪故障或者副枪粘钢时,均不能进行测温、取样,就要进行出钢作业,在保证钢水磷合格的前提下,都未对lf炉生产造成过多影响。
[0017]
然而,随着转炉炼钢工艺日渐成熟,对于转炉冶炼控制水平要求不断提高。一般转炉在冶炼中后期进行测温取样、化验等样,钢样合格后才进行出钢作业,已不能适应转炉高
效生产缩短冶炼周期的发展趋势。冶炼中后期测温取样、化验等样过程,钢水温度及其氧化性都处于炼钢过程峰值,对于炉况损害极大。同时冶炼中后期测温取样等待过程温度降低,热量流失,增加了炼钢工序能源消耗。因此,亟需一种低碳lf炉工艺钢转炉冶炼方法来解决这个问题。
技术实现要素:[0018]
本发明的目的在于提供一种低碳lf炉工艺钢转炉冶炼方法,以解决低碳lf炉工艺钢转炉冶炼过程中需要测温取样对炉况损害大的问题。
[0019]
为实现上述目的,本发明提供如下技术方案:一种低碳lf炉工艺钢转炉冶炼方法:通过实验,分别以氧枪枪位、氧枪供氧流量、底吹气流量其中之一单独作为变量,监控转炉煤气co含量的变化规律,根据寻得的变化规律,在冶炼时控制这些因素,消除其对脱碳的干扰;转炉冶炼时,实时测定转炉煤气co含量并绘制曲线图,并以该曲线图作为冶炼终点提枪时机的判定依据,将转炉煤气co含量从50%降到28%所经过的时间记为t秒,当转炉煤气co含量由28%继续下降t秒时,即达到冶炼终点,提枪停止供氧。
[0020]
在本发明的一种较优方案中,转炉冶炼时,在氧枪供氧200m3‑
500m3时加入第一批料,包括80%石灰和80%生白云石;在氧枪供氧2500m3‑
2800m3时加入第二批料,包括20%石灰和20%生白云石。
[0021]
在本发明的一种较优方案中,在氧枪供氧0m3‑
3000m3时,控制氧枪枪位为1.95
±
0.05m;在氧枪供氧3000m3‑
12000m3时,控制氧枪枪位为2.15
±
0.15m;在氧枪供氧12000m3‑
冶炼终点时,控制氧枪枪位为1.8m。
[0022]
在本发明的一种较优方案中,在氧枪供氧0m3‑
3000m3时,控制底吹气流量为594m3/h,底吹气体为氮气;在氧枪供氧3000m3‑
12000m3时,控制底吹气流量为594m3/h,底吹气体为氩气;在氧枪供氧12000m3‑
冶炼终点时,控制底吹气流量为1980m3/h,底吹气体为氩气。
[0023]
在本发明的一种较优方案中,转炉冶炼时,控制氧枪全程供氧流量63000m3/h。
[0024]
在本发明的一种较优方案中,转炉冶炼前,前一炉出完钢后,正常翻渣留渣,溅渣护炉,加废钢,兑铁水,其入炉条件为,铁水中以重量百分比计:c4.40%
‑
4.80%、si0.20%
‑
0.50%、mn0.12%
‑
0.18%、p0.095%
‑
0.155%、s0.013%
‑
0.400%、v0.035%
‑
0.065%、ti0.034%
‑
0.118%,铁水预处理后温度1285℃
‑
1385℃,铁水重量265
‑
325吨,普通废钢重量25
‑
75吨,污泥0
‑
5.5吨,渣钢0
‑
9吨。
[0025]
在上述任一方案中较优的,钢水转炉冶炼后,氩前钢水碳含量≤0.060%,钢水磷含量≤0.0250%。
[0026]
与现有技术相比,本发明的有益效果是:
[0027]
1、该低碳lf炉工艺钢转炉冶炼方法,冶炼过程不测温、不取样,温度和热量流失更少,且可以缩短转炉冶炼后期时间,利于降低低碳lf炉工艺钢转炉冶炼工序能源消耗;此外,由于在转炉冶炼后期,钢水温度及其氧化性都处于炼钢过程峰值,不进行测温取样和化验等样过程,对于炉况损害可极大地降低,有利于缓解转炉炉衬侵蚀,延长转炉使用寿命,对其质量百利而无一害。
[0028]
2、该低碳lf炉工艺钢转炉冶炼方法,根据转炉煤气回收co规律,在冶金热力学基础上,利用底吹强搅拌,强化冶炼后期底吹搅拌动力学条件,进一步确保冶炼终点钢水磷含
量和钢水碳含量合格。
[0029]
3、该低碳lf炉工艺钢转炉冶炼方法,由于无需测温和取样,可以减少测温取样装置的使用,节约开支,并且可以减少测温取样的工作,减少劳动强度,节约检测成本。
附图说明
[0030]
图1为本发明的实施例1中转炉煤气co含量
‑
时间曲线图,图中横坐标为时间,纵坐标为转炉煤气co含量。
具体实施方式
[0031]
为解决冶炼中后期钢水温度及其氧化性都处于炼钢过程峰值,测温取样、化验等样过程对于炉况损害极大,同时冶炼中后期测温取样等待过程温度降低,热量流失,增加了炼钢工序能源消耗的问题,本发明提供一种低碳lf炉工艺钢转炉冶炼方法,首先通过实验,分别以氧枪枪位、氧枪供氧流量、底吹气流量其中之一单独作为变量,对其进行标准化操作固化,监控转炉煤气co含量的变化规律,根据寻得的规律,在冶炼时控制这些因素,消除其对脱碳的干扰;
[0032]
转炉冶炼时,在湿法净化煤气蒸汽回收og系统中实时测定转炉煤气co含量并绘制曲线图,并以该曲线图作为冶炼终点提枪时机的判定依据,将转炉煤气co含量从50%降到28%所经过的时间记为t秒,当转炉煤气co含量由28%继续下降t秒时,即达到冶炼终点,提枪停止供氧。
[0033]
实施例1:
[0034]
300吨转炉,前一炉出完钢,正常翻渣留渣,溅渣护炉,加废钢,兑铁水,开始冶炼,入炉时铁水中以重量百分比计:c4.48%,si0.33%,mn0.13%,p0.118%,s0.036%,v0.050%,ti0.067%,铁水预处理后温度1324℃,铁水重量265.7吨,普通废钢重量58.7吨,污泥3.9吨,渣钢4.4吨。
[0035]
在供氧200m3‑
500m3加入第一批料:80%石灰6493kg、80%生白云石1306kg,供氧2500m3‑
2800m3加入第二批料:20%石灰1623kg、20%生白云石326kg。0m3‑
3000m3氧枪枪位为1.95m,3000m3‑
12000m3氧枪枪位为2.15m,12000m3‑
冶炼终点的氧枪枪位为1.8m。全程供氧流量63000m3/h。0m3‑
3000m3底吹氮气流量为594m3/h,3000m3‑
12000m3底吹氩气流量为594m3/h,12000m3‑
冶炼终点的底吹氩气流量为1980m3/h。在转炉煤气co含量从50%降到28%的时间为16秒,当转炉煤气co含量从28%继续下降回收16秒时,达到冶炼终点提枪停止供氧。氩前温度1607℃,氩前钢水碳含量0.038%,钢水磷含量0.0159%。
[0036]
实施例2
[0037]
300吨转炉,前一炉出完钢,正常翻渣留渣,溅渣护炉,加废钢,兑铁水,开始冶炼,入炉时铁水中以重量百分比计:c4.72%,si0.42%,mn0.17%,p0.149%,s0.018%,v0.050%,ti0.100%,铁水预处理后温度1351℃,铁水重量272.2吨,普通废钢重量48.2吨,污泥3.0吨,渣钢0吨。
[0038]
在供氧200m3‑
500m3加入第一批料:80%石灰10474kg、80%生白云石3606kg,供氧2500m3‑
2800m3加入第二批料:20%石灰2619kg、20%生白云石902kg。0m3‑
3000m3氧枪枪位为1.9m,3000m3‑
12000m3氧枪枪位为2.1m,12000m3‑
冶炼终点的氧枪枪位为1.8m。全程供氧
流量63000m3/h。0m3‑
3000m3底吹氮气流量为594m3/h,3000m3‑
12000m3底吹氩气流量为594m3/h,12000m3‑
冶炼终点的底吹氩气流量为1980m3/h。在转炉煤气co含量从50%降到28%的时间为15秒,当转炉煤气co含量从28%继续下降回收15秒时,达到冶炼终点提枪停止供氧。氩前温度1603℃,氩前钢水碳含量0.050%,钢水磷含量0.0160%。
[0039]
实施例3
[0040]
300吨转炉,前一炉出完钢,正常翻渣留渣,溅渣护炉,加废钢,兑铁水,开始冶炼,入炉时铁水中以重量百分比计:c4.56%,si0.38%,mn0.13%,p0.120%,s0.022%,v0.045%,ti0.072%,铁水预处理后温度1297℃,铁水重量281.1吨,普通废钢重量42.9吨,污泥0吨,渣钢8.7吨。
[0041]
在供氧200m3‑
500m3加入第一批料:80%石灰7042kg、80%生白云石1345kg,供氧2500m3‑
2800m3加入第二批料:20%石灰1760kg、20%生白云石336kg。0m3‑
3000m3氧枪枪位为1.95m,3000m3‑
12000m3氧枪枪位为2.15m,12000m3‑
冶炼终点的氧枪枪位为1.8m。全程供氧流量63000m3/h。0m3‑
3000m3底吹氮气流量为594m3/h,3000m3‑
12000m3底吹氩气流量为594m3/h,12000m3‑
冶炼终点的底吹氩气流量为1980m3/h。在转炉煤气co含量从50%降到28%的时间为18秒,当转炉煤气co含量从28%继续下降回收18秒时,达到冶炼终点提枪停止供氧。氩前温度1610℃,氩前钢水碳含量0.029%,钢水磷含量0.0109%。
[0042]
实施例4
[0043]
300吨转炉,前一炉出完钢,正常翻渣留渣,溅渣护炉,加废钢,兑铁水,开始冶炼,入炉时铁水中以重量百分比计:c4.44%,si0.45%,mn0.15%,p0.121%,s0.026%,v0.062%,ti0.053%,铁水预处理后温度1351℃,铁水重量272.8吨,普通废钢重量52.5吨,污泥0吨,渣钢6.3吨。
[0044]
在供氧200m3‑
500m3加入第一批料:80%石灰11762kg、80%生白云石2771kg,供氧2500m3‑
2800m3加入第二批料:20%石灰2940kg、20%生白云石693kg。0m3‑
3000m3氧枪枪位为1.9m,3000m3‑
12000m3氧枪枪位为2.1m,12000m3‑
冶炼终点的氧枪枪位为1.8m。全程供氧流量63000m3/h。0m3‑
3000m3底吹氮气流量为594m3/h,3000m3‑
12000m3底吹氩气流量为594m3/h,12000m3‑
冶炼终点的底吹氩气流量为1980m3/h。在转炉煤气co含量从50%降到28%的时间为17秒,当转炉煤气co含量从28%继续下降回收17秒时,达到冶炼终点提枪停止供氧。氩前温度1587℃,氩前钢水碳含量0.030%,钢水磷含量0.0079%。
[0045]
图1为上述实施例1的转炉煤气co含量
‑
时间曲线图,(实施例2
‑
4的曲线图与之相近,不再重复展示),从图中可以看出,转炉煤气co含量从60%开始下降时速率较快,按照本发明的方法在转炉煤气co含量从50%降至28%时记下时间为16秒,再经过16秒后提枪停止供氧,可缩短转炉冶炼后期时间3.5分钟,降低低碳lf炉工艺钢转炉冶炼工序能源消耗;
[0046]
在本发明的较优实施方式中,对比现有需测温、采样的方法,在相同的入炉铁水、废钢条件下,氩前温度提高超过10.5℃;在相同的氩前温度下,入炉废钢增加3
‑
5吨;除了节约以外,由于在转炉冶炼后期,钢水温度及其氧化性都处于炼钢过程峰值,不进行测温取样和化验等样过程,对于转炉炉况损害可极大地降低,对其质量百利而无一害。
[0047]
以上仅为本发明的较佳实施例,但本发明的保护范围并不局限于此,任何熟悉本技术领域的技术人员在本发明揭露的技术范围内,可轻易想到的变化或替换,都应涵盖在本发明的保护范围之内。因此,本发明的保护范围应该以权利要求所界定的保护范围为准。
[0048]
本发明未详述之处,均为本技术领域技术人员的公知技术。