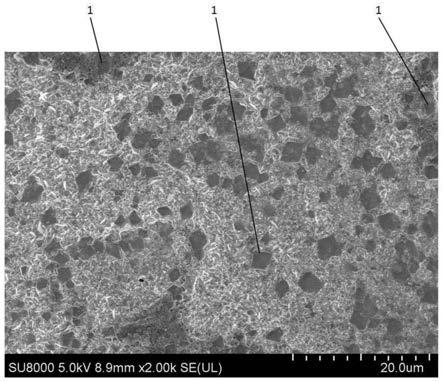
1.本发明涉及铅酸蓄电池技术领域,具体涉及一种含石墨烯的正极板栅合金及制备方法与应用。
背景技术:2.在铅酸蓄电池中,正极板栅在长时间使用过程中易形成导电性差的化合物,影响正极板栅界面的导电性能,使得正极板栅与活性物质的结合能力变差,进而导致电池的循环性能衰减,充电恢复能力降低。
3.为解决上述问题,通常采用的方法是在正极板栅合金中加入导电性较好的金属元素,例如ag或sn,但这些金属价格较高,大量使用会带来较大生产成本负担。另外的方法就是在正极板栅合金中加入石墨烯,形成石墨烯/金属复合材料,石墨烯的作用包括:(1)提高正极板栅合金的导电性能;(2)降低板栅的重量,提高能量密度;(3)提升腐蚀层的导电性能,避免栅膏分离;(4)避免腐蚀界面生成导电性差的氧化铅,提高充电恢复能力。但是在将石墨烯掺入铅合金基体的过程中,由于碳与铅的密度相差较大,如何实现将石墨烯均匀分散在合金中是获得性能优良的正极板栅合金的关键。
4.cn105977496b公开了一种包含铅锡
‑
稀土
‑
石墨烯的铅蓄电池板栅合金的制备方法,该方法包括:(1)制备铅
‑
石墨烯复合材料:向含铅离子的弥散电镀液中加入改性石墨烯粉末,以惰性导电基体为阳极,以纯铅板为阴极,电化学沉积获得沉积有铅
‑
石墨烯复合材料的纯铅板;(2)制备板栅母合金;(3)制备板栅合金:a、将占铅总质量70
‑
80%的铅锭加入中频炉中,加热熔化;b、向熔体中加入步骤(2)中制备的板栅母合金锭,继续加热使其熔化并搅拌均匀;c、停止加热,待合金液温度降至350
‑
400℃,加入步骤(1)中制备的沉积有铅
‑
石墨烯复合材料的纯铅板,熔化、搅拌均匀;d、加入剩余铅锭,熔化、搅拌,清渣后浇铸合金锭。该方法采用复合电镀技术将石墨烯粉末与金属铅进行共沉积,制备出石墨烯均匀分散在铅基体中的合金材料,但该方法需在先前步骤中制备铅
‑
石墨烯复合材料和板栅母合金,这需要增加专门的电镀设备和工序以及表面活性剂的使用,并使得整体工艺冗长,延长制备周期。
5.cn104993154b公开了一种含有石墨烯的铅蓄电池板栅用铅合金,按重量百分比计算,其包含0.015
‑
0.15%的石墨烯,1.0
‑
1.5%的锡,0.02
‑
0.04%的铝,0.05
‑
0.1%的钙和98.21
‑
98.915%的铅;其由以下制作方法制成,(1)将所述量的2/3的铅置入熔铅锅中,加热到680℃至铅完全熔化;(2)然后开启离心搅拌机,将所述量的石墨烯在中速搅拌的情况下缓慢连续添加或分批次间断添加加入到铅液中;(3)20分钟后,先后加入所述量的纯锡条和纯铝条,离心搅拌机继续搅拌混合半小时以上;(4)关闭离心搅拌机,加入所述量的用铅皮包封好的钙,将铅皮包封好的钙用底部有漏孔的钟罩压入铅液底部,当铅液不再冒泡时,开动离心搅拌机慢速搅拌混合;(5)半小时后,关闭离心搅拌机,把剩余量的铅加入熔铅锅中,待铅完全熔解,开启离心搅拌机,继续慢速搅拌,一小时后铸锭。该方法在调配铅钙合金的过程中加入石墨烯成品,加以机械搅拌,实现石墨烯分散在铅钙合金内,制备周期短。但由
于使用简单的机械搅拌方法,在实际生产中石墨烯在合金中的分散效果难以保证,且易产生有效元素烧损等问题。
6.综上,仍需要研究和开发新的正极板栅合金的制备方法,以保证石墨烯在合金中均匀分散的效果,同时能够避免合金组分偏析、有效元素烧损的问题。
技术实现要素:7.本发明的目的是为了克服现有技术存在石墨烯难以均匀分散在合金铅液中进而导致所制备的合金不均匀的问题,以及在制备过程中易造成合金组分偏析、有效元素烧损的问题,提供了一种含石墨烯的正极板栅合金及制备方法与应用。
8.为实现上述目的,本发明第一方面提供一种含石墨烯的正极板栅合金的制备方法,该方法包括:
9.(1)将铅和锡进行第一熔化,得到第一合金液体;
10.(2)在所述第一合金液体中加入熔盐,升温后加入含碳剂进行反应,之后可选地加入钙进行第二熔化,得到第二合金液体与所述熔盐的混合物;
11.(3)将所述混合物进行分离,其中,所述第二合金液体进行铸锭,得到含石墨烯的正极板栅合金;所述熔盐返回步骤(2)中循环使用。
12.本发明第二方面提供由前述第一方面所述的方法制得的含石墨烯的正极板栅合金。
13.本发明第三方面提供由前述第二方面所述的含石墨烯的正极板栅合金通过重力浇铸工艺、冲网工艺和玻璃丝包铅工艺中的至少一种制备得到的正极板栅。
14.本发明第四方面提供由前述第二方面所述的含石墨烯的正极板栅合金和本法明第三方面所述的正极板栅在铅酸蓄电池中的应用。
15.通过上述技术方案,本发明具有如下有益效果:
16.(1)能够使石墨烯均匀分散在合金基体中,同时避免合金元素偏析、有效元素烧损的问题,制备得到均匀稳定的含石墨烯的正极板栅合金;
17.(2)将所制得的合金制备正极板栅,能够提高铅酸蓄电池的循环使用寿命、大电流功率性能及过放电恢复能力;
18.(3)无需引进新的设备,制备工艺简单,周期短,可操作性强。
附图说明
19.附图是用来提供对本发明的进一步理解,并且构成说明书的一部分,与下面的具体实施方式一起用于解释本发明,但并不构成对本发明的限制。在附图中:
20.图1为本发明实施例1中制得的含石墨烯的正极板栅合金的拉曼光谱图;
21.图2为本发明实施例1中制得的含石墨烯的正极板栅合金的扫描电镜图;
22.图3为本发明实施例1中制得的含石墨烯的正极板栅合金的不同位置dsc(差式扫描量热法)测试结果图。
具体实施方式
23.在本文中所披露的范围的端点和任何值都不限于该精确的范围或值,这些范围或
值应当理解为包含接近这些范围或值的值。对于数值范围来说,各个范围的端点值之间、各个范围的端点值和单独的点值之间,以及单独的点值之间可以彼此组合而得到一个或多个新的数值范围,这些数值范围应被视为在本文中具体公开。
24.以下对本发明的具体实施方式进行详细说明。应当理解的是,此处所描述的具体实施方式仅用于说明和解释本发明,并不用于限制本发明。
25.本发明第一方面提供一种含石墨烯的正极板栅合金的制备方法,该方法包括:
26.(1)将铅和锡进行第一熔化,得到第一合金液体;
27.(2)在所述第一合金液体中加入熔盐,升温后加入含碳剂进行反应,之后可选地加入钙进行第二熔化,得到第二合金液体与所述熔盐的混合物;
28.(3)将所述混合物进行分离,其中,所述第二合金液体进行铸锭,得到含石墨烯的正极板栅合金;所述熔盐返回步骤(2)中循环使用。
29.在本发明的一些实施方式中,在步骤(1)中,所述第一熔化的条件包括:温度为400
‑
500℃,搅拌速率为300
‑
900转/分。优选先将铅加热至400
‑
500℃得到铅液,保温15
‑
30分钟,之后在所述铅液中加入锡,并以300
‑
900转/分的速率搅拌15
‑
45min,使得锡熔化并与所述铅液混合均匀,之后保温15
‑
30min,得到第一合金液体。
30.在本发明中,所述铅和锡的纯度满足本领域正极板栅合金中常规的对原料铅和锡的纯度要求,可以采用本领域中常用的块、锭、条、粒的形式入料,本技术对其没有特别的限定。
31.在本发明中,可以采用本领域中常规的用于搅拌的方式,优选采用机械搅拌。
32.在本发明的一些实施方式中,在步骤(1)中,铅的投料量可以为95.38
‑
99.49重量份,锡的投料量可以为0.5
‑
2.5重量份。
33.在本发明的一些实施方式中,在步骤(2)中,所述熔盐以固态的形式加入所述第一合金液体中,能够起到保护的作用,可以避免在合金的制备过程中有效元素烧损。所述熔盐为氯化钾、氯化钠、氯化钙中的至少两种。为使得所述熔盐在合金制备过程中发挥更好的保护作用,优选地,所述熔盐的投料量可以为5
‑
30重量份。
34.在本发明的一些实施方式中,在步骤(2)中,将含碳剂加入到高温合金液体中进行反应,得到石墨烯材料并能够均匀分散在合金基体中。所述反应的条件包括:温度为700
‑
750℃,时间为15
‑
60min;优选地,所述反应的条件还包括搅拌,搅拌速率为30
‑
600转/分。
35.在本发明中,所述含碳剂能够提供碳源,优选为碳化钙、碳化硼、碳化钛、碳化硅中的至少一种,更优选为碳化钙和/或碳化硼。为使得所制得的正极板栅合金获得更好的机械性能、导电性能和电化学性能,优选地,所述含碳剂的投料量可以为0.05
‑
10重量份。
36.在本发明的一些实施方式中,在步骤(2)中,钙的投料量可以为0
‑
0.12重量份,即可以在所述反应之后加入钙,也可以不加入钙,具体可以根据正极板栅合金目标产品的性能和组分要求进行选择。在加入钙的情况下,即在步骤(2)中包含所述第二熔化,为使得钙更好地熔化并分散在合金基体中,优选地,所述第二熔化的条件包括:温度为700
‑
750℃,搅拌速率为30
‑
600转/分。在不加入钙的情况下,则在步骤(2)中不包含所述第二熔化。
37.在本发明中,所述钙的纯度满足本领域正极板栅合金中常规的对原料钙的纯度要求,本技术对其没有特别的限定。
38.在本发明的一些实施方式中,在步骤(2)中,所述熔盐在合金的制备过程中不消
耗,其与所制得的第二合金液体共存,即在步骤(2)中得到的是第二合金液体与所述熔盐的混合物。
39.在本发明的一些实施方式中,在步骤(3)中,可以利用密度差异对所述混合物进行分离,所述熔盐在所述混合物的上层,对其分离并回收后返回步骤(2)中循环使用。将所述第二合金液体进行铸锭,得到含石墨烯的正极板栅合金。
40.本发明第二方面提供由前述第一方面所述的方法制得的含石墨烯的正极板栅合金。
41.在本发明中,以所述含石墨烯的正极板栅合金的总重为基准,所述合金的组成包括:sn 0.5
‑
2.5重量%、ca 0
‑
0.12重量%、石墨烯0.01
‑
2重量%和pb 95.38
‑
99.49重量%。
42.本发明第三方面提供由前述第二方面所述的含石墨烯的正极板栅合金通过重力浇铸工艺、冲网工艺和玻璃丝包铅工艺中的至少一种制备得到的正极板栅。
43.在本发明中,所述重力浇铸工艺、冲网工艺和玻璃丝包铅工艺为本领域常规的制备铅酸蓄电池正极板栅合金的工艺,本技术对其工艺过程和参数没有特别的限定。
44.本发明第四方面提供由前述第二方面所述的含石墨烯的正极板栅合金和本法明第三方面所述的正极板栅在铅酸蓄电池中的应用。
45.以下将通过实施例对本发明进行详细描述。以下实施例和对比例中,抗蠕变应力根据gb/t 228.1
‑
2010中规定的方法进行测定;
46.拉伸断裂变形率根据gb/t 228.1
‑
2010中规定的方法进行测定。
47.实施例1
48.(1)将铅和锡进行第一熔化,过程为:将97.9重量份的铅块在熔炉中加热至450℃得到铅液,保温30分钟,之后在所述铅液中加入1.2重量份的锡块,并以600转/分的速率进行机械搅拌30min,使得锡熔化并与所述铅液混合均匀,之后保温30min,得到第一合金液体;
49.(2)在所述第一合金液体中加入20重量份的氯化钠和氯化钙的混合熔盐(氯化钠:氯化钙的重量比为1:2),之后升温至700℃,待温度稳定后,将4重量份的碳化硼用底部有孔洞的不锈钢钟罩放入合金液体中进行反应(反应的条件包括:温度为700℃,时间为30min,机械搅拌的速率为300转/分);之后加入0.1重量份的钙,在750℃并以300转/分的机械搅拌条件下进行第二熔化,得到第二合金液体与熔盐的混合物;
50.(3)将所述混合物从熔炉底部放出,将熔盐分离并回收后返回步骤(2)中循环使用,将所述第二合金液体进行铸锭,得到含石墨烯的正极板栅合金,记为s1。
51.以合金的总重为基准,s1的组成包括:sn 1.2重量%
‑
ca 0.1重量%
‑
石墨烯0.8重量%
‑
pb 97.9重量%。
52.图1为本发明实施例1中制得的含石墨烯的正极板栅合金的拉曼光谱图。由图1可以看出,其中存在明显的特征峰:d
‑
1343.86/厘米,g
‑
1577.5/厘米,2d
‑
2695.21/厘米,这些是典型的石墨烯的拉曼光谱特征,说明在所制备的合金中存在石墨烯。
53.图2为本发明实施例1中制得的含石墨烯的正极板栅合金的扫描电镜图。图2中黑色多边形颗粒(如图中标号1所示)为石墨烯,其在合金中分散均匀,没有出现团聚现象。
54.图3为本发明实施例1中制得的含石墨烯的正极板栅合金的不同位置的dsc(差式扫描量热法)测试结果图。由图3可以看出,合金中不同点位的热量差非常接近,说明这些点
位的合金成分基本相同,合金的均匀性好。
55.s1的抗蠕变应力不小于65mpa,能够满足重力浇铸工艺加工制备正极板栅的要求。将s1采用重力浇铸工艺制得正极板栅,记为a1。
56.实施例2
57.(1)将铅和锡进行第一熔化,过程为:将97.63重量份的铅块在熔炉中加热至450℃得到铅液,保温15分钟,之后在所述铅液中加入0.8重量份的锡块,并以300转/分的速率进行机械搅拌20min,使得锡熔化并与所述铅液混合均匀,之后保温30min,得到第一合金液体;
58.(2)在所述第一合金液体中加入25重量份的氯化钠和氯化钙的混合熔盐(氯化钠:氯化钙的重量比为1:2),之后升温至700℃,待温度稳定后,将7.5重量份的含碳剂(碳化钙和碳化硼以重量比1:1混合)用底部有孔洞的不锈钢钟罩放入合金液体中进行反应(反应的条件包括:温度为700℃,时间为50min,机械搅拌的速率为300转/分);之后加入0.07重量份的钙,在700℃并以200转/分的机械搅拌条件下进行第二熔化,得到第二合金液体与熔盐的混合物;
59.(3)将所述混合物从熔炉底部放出,将熔盐分离并回收后返回步骤(2)中循环使用,将所述第二合金液体进行铸锭,得到含石墨烯的正极板栅合金,记为s2。
60.以合金的总重为基准,s2的组成包括:sn 0.8重量%
‑
ca 0.07重量%
‑
石墨烯1.5重量%
‑
pb 97.63重量%。
61.s2的抗蠕变应力不小于65mpa,能够满足重力浇铸工艺加工制备正极板栅的要求。将s2采用重力浇铸工艺制得正极板栅,记为a2。
62.实施例3
63.(1)将铅和锡进行第一熔化,过程为:将97.4重量份的铅块在熔炉中加热至500℃得到铅液,保温15分钟,之后在所述铅液中加入2重量份的锡块,并以900转/分的速率进行机械搅拌30min,使得锡熔化并与所述铅液混合均匀,之后保温45min,得到第一合金液体;
64.(2)在所述第一合金液体中加入20重量份的氯化钾和氯化钠的混合熔盐(氯化钾:氯化钠的重量比为5:4),之后升温至750℃,待温度稳定后,将2.5重量份的含碳剂(碳化硼和碳化硅以重量比2:1混合)用底部有孔洞的不锈钢钟罩放入合金液体中进行反应(反应的条件包括:温度为750℃,时间为25min,机械搅拌的速率为200转/分);之后加入0.1重量份的钙,在750℃并以300转/分的机械搅拌条件下进行第二熔化,得到第二合金液体与熔盐的混合物;
65.(3)将所述混合物从熔炉底部放出,将熔盐分离并回收后返回步骤(2)中循环使用,将所述第二合金液体进行铸锭,得到含石墨烯的正极板栅合金,记为s3。
66.以合金的总重为基准,s3的组成包括:sn 2重量%
‑
ca 0.1重量%
‑
石墨烯0.5重量%
‑
pb 97.4重量%。
67.s3的抗蠕变应力不小于50mpa,拉伸断裂变形率不小于20%,能够满足冲网工艺加工制备正极板栅的要求。将s3采用冲网工艺制得正极板栅,记为a3。
68.实施例4
69.(1)将铅和锡进行第一熔化,过程为:将97.94重量份的铅块在熔炉中加热至450℃得到铅液,保温15分钟,之后在所述铅液中加入1.2重量份的锡块,并以600转/分的速率进
行机械搅拌30min,使得锡熔化并与所述铅液混合均匀,之后保温30min,得到第一合金液体;
70.(2)在所述第一合金液体中加入20重量份的氯化钠和氯化钙的混合熔盐(氯化钠:氯化钙的重量比为1:2),之后升温至750℃,待温度稳定后,将4重量份的含碳剂(碳化钙和碳化钛以重量比1:1混合)用底部有孔洞的不锈钢钟罩放入合金液体中进行反应(反应的条件包括:温度为750℃,时间为30min,机械搅拌的速率为300转/分);之后加入0.06重量份的钙,在700℃并以200转/分的机械搅拌条件下进行第二熔化,得到第二合金液体与熔盐的混合物;
71.(3)将所述混合物从熔炉底部放出,将熔盐分离并回收后返回步骤(2)中循环使用,将所述第二合金液体进行铸锭,得到含石墨烯的正极板栅合金,记为s4。
72.以合金的总重为基准,s4的组成包括:sn 1.2重量%
‑
ca 0.06重量%
‑
石墨烯0.8重量%
‑
pb 97.94重量%。
73.s4的抗蠕变应力不小于50mpa,拉伸断裂变形率不小于20%,能够满足冲网工艺加工制备正极板栅的要求。将s4采用冲网工艺制得正极板栅,记为a4。
74.实施例5
75.(1)将铅和锡进行第一熔化,过程为:将98.8重量份的铅块在熔炉中加热至450℃得到铅液,保温15分钟,之后在所述铅液中加入1重量份的锡块,并以300转/分的速率进行机械搅拌15min,使得锡熔化并与所述铅液混合均匀,之后保温15min,得到第一合金液体;
76.(2)在所述第一合金液体中加入10重量份的氯化钠和氯化钙的混合熔盐(氯化钠:氯化钙的重量比为1:2),之后升温至700℃,待温度稳定后,将1重量份的碳化钙用底部有孔洞的不锈钢钟罩放入合金液体中进行反应(反应的条件包括:温度为700℃,时间为20min,机械搅拌的速率为100转/分),得到第二合金液体与熔盐的混合物;
77.(3)将所述混合物从熔炉底部放出,将熔盐分离并回收后返回步骤(2)中循环使用,将所述第二合金液体进行铸锭,得到含石墨烯的正极板栅合金,记为s5。
78.以合金的总重为基准,s5的组成包括:sn 1重量%
‑
石墨烯0.2重量%
‑
pb98.8重量%。
79.s5的拉伸断裂变形率不小于30%,能够满足玻璃丝包铅工艺加工制备正极板栅的要求。将s5采用玻璃丝包铅工艺制得正极板栅,记为a5。
80.实施例6
81.(1)将铅和锡进行第一熔化,过程为:将98.9重量份的铅块在熔炉中加热至400℃得到铅液,保温15分钟,之后在所述铅液中加入0.6重量份的锡块,并以300转/分的速率进行机械搅拌15min,使得锡熔化并与所述铅液混合均匀,之后保温15min,得到第一合金液体;
82.(2)在所述第一合金液体中加入20重量份的氯化钾和氯化钙的混合熔盐(氯化钾:氯化钙的重量比为2:1),之后升温至750℃,待温度稳定后,将2.5重量份的含碳剂(碳化钛和碳化硅以重量比1:2混合)用底部有孔洞的不锈钢钟罩放入合金液体中进行反应(反应的条件包括:温度为750℃,时间为30min,机械搅拌的速率为200转/分),得到第二合金液体与熔盐的混合物;
83.(3)将所述混合物从熔炉底部放出,将熔盐分离并回收后返回步骤(2)中循环使
用,将所述第二合金液体进行铸锭,得到含石墨烯的正极板栅合金,记为s6。
84.以合金的总重为基准,s6的组成包括:sn 0.6重量%
‑
石墨烯0.5重量%
‑
pb98.9重量%。
85.s6的拉伸断裂变形率不小于30%,能够满足玻璃丝包铅工艺加工制备正极板栅的要求。将s6采用玻璃丝包铅工艺制得正极板栅,记为a6。
86.对比例1
87.在20重量份的熔融态的氯化钠和氯化钙混合物(氯化钠:氯化钙的重量比为1:2)中加入4重量份的碳化硼颗粒,充分混合后冷却并粉碎,得到粒径为45
‑
70μm的第一混合粉末。将97.9重量份的铅粉和1.2重量份的锡粉、0.1重量份的钙混匀得到第二混合粉末并置于熔炉底部,将所述第一混合粉末平铺在所述第二混合粉末的表面,二者在接触的界面处有部分共混。封闭熔炉,然后加热升温至750℃,保温1h,然后在0.5h内降至室温。刷除合金表面的杂质,得到含石墨烯的正极板栅合金,记为d1。
88.以合金的总重为基准,d1的组成包括:sn 1.2重量%
‑
ca 0.1重量%
‑
石墨烯0.8重量%
‑
pb 97.9重量%。
89.d1的力学性能指标为抗蠕变应力不小于65mpa,能够满足重力浇铸工艺加工制备正极板栅的要求。将d1采用重力浇铸工艺制得正极板栅,记为ad1。
90.对比例2
91.按照实施例1的方法,不同的是,各原料的投料量:铅为99.46重量份,锡为0.4重量份,氯化钠和氯化钙的混合熔盐为15重量份,碳化硼为0.2重量份,钙为0.1重量份。其它条件与实施例1相同,得到含石墨烯的正极板栅合金,记为d2。
92.以合金的总重为基准,d2的组成包括:sn 0.4重量%
‑
ca 0.1重量%
‑
石墨烯0.04重量%
‑
pb 99.46重量%。
93.d2的力学性能指标为抗蠕变应力不小于65mpa,能够满足重力浇铸工艺加工制备正极板栅的要求。将d2采用重力浇铸工艺制得正极板栅,记为ad2。
94.测试例
95.将实施例1
‑
6、对比例1
‑
2所制得的正极板栅a1
‑
a6、ad1
‑
ad2以及使用普通的石墨烯
‑
铅合金(sn 1.2重量%
‑
al 0.02重量%
‑
ca 0.1重量%
‑
石墨烯0.1重量%
‑
pb 98.58重量%)基于重力浇铸工艺制得的正极板栅(记为ad3)按照常规工艺制备铅酸电池,并对铅酸电池进行性能评价。以下测试例中,
96.36a大电流放电性能:按照gb/t 22199
‑
2017进行测试;
97.循环寿命:按照gb/t 22199
‑
2017进行测试;
98.过放电后容量恢复性能:按照如下操作进行测试,
99.1、电池过放电:使用6
‑
dzf
‑
20ah电池外接0.5ω定值电阻,连续放电15天。
100.2、充电恢复测试:
101.充电工艺为:(1)恒流恒压充电,电流为2.5a,电压为14.7v,当电流小于0.5a时跳转至下一步;(2)电池静置5min;(3)恒流恒压充电,电流为1a,电压为13.8v,充电时间为2h;(4)电池静置1h。
102.放电工艺为:恒流放电,电流为10a,截止电压为10.5v。
103.以电池放电容量(ah)作为衡量电池过放电性能的指标。
104.测试结果如表1所示。
105.表1
[0106][0107]
从表1可以看出,本发明提供的含石墨烯的正极板栅合金能够使得铅酸电池在循环使用寿命、大电流功率性能及过放电后容量恢复性能方面具有较优异的表现,与采用普通的石墨烯
‑
铅合金板栅(即ad3)的电池相比,上述三项指标均显著提升。
[0108]
特别地,对比例1和对比例2没有采用本发明的制备方法,所制得的铅酸电池的综合性能显著差于本发明中的效果。
[0109]
此外,本发明提供的正极板栅合金根据合金成分和力学性能的不同,可分别应用于重力浇铸工艺、冲网工艺和玻璃丝包铅工艺中来制备正极板栅,并均能获得上述使用效果。
[0110]
以上详细描述了本发明的优选实施方式,但是,本发明并不限于此。在本发明的技术构思范围内,可以对本发明的技术方案进行多种简单变型,包括各个技术特征以任何其它的合适方式进行组合,这些简单变型和组合同样应当视为本发明所公开的内容,均属于本发明的保护范围。