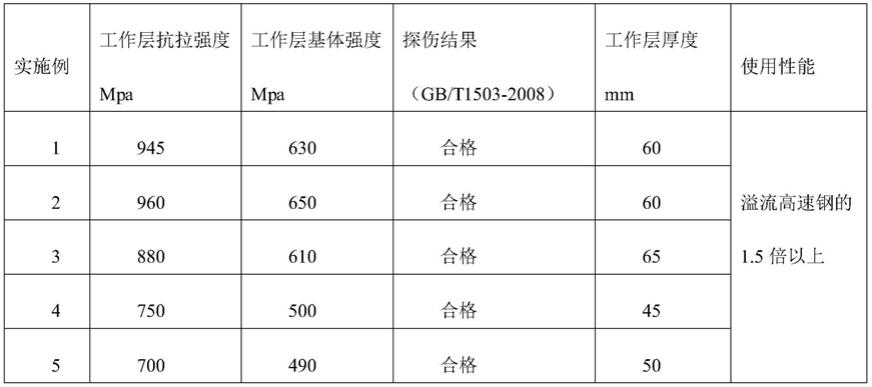
1.本发明属于轧钢技术领域,具体涉及一种高硼高速钢离心复合轧辊的制造方法。
背景技术:2.高速钢轧辊由于含有大量的v、w、cr、mo、nb等合金元素,有较高的常温硬度hs82~90,同时有着良好的高温红硬性特点,在500℃以上仍能保证hs78以上,因此具有优良的高温耐磨性,目前已广泛应用于轧钢生产中。用高速钢轧辊取代半钢轧辊、高铬铸铁轧辊、高镍铬钼无限冷硬轧辊及针状贝氏体球铁轧辊,对于提高轧制量,延长换辊周期,生产实践中都取得了良好的效果。
3.由于高速钢轧辊材质的特殊性,对轧制环境要求也相对较高,在棒材轧机精轧段机架,在采用切分轧制时,切分机架轧制环境尤其恶劣,高速钢轧辊未能得到好的使用效果,目前仍以传统的贝氏体球铁材质居多。提高高速钢轧辊的基体强度,细化晶粒,克服棒材轧机切分机架的轧制环境,适应切分机架轧制。
4.高速钢轧辊为复合轧辊,其铸造方法常用的是用软质和韧性金属液置换轧辊凝固过程中芯部未凝固的硬质金属液的溢流法,但是该工艺劳动强度大,成本高,而且受到溢流生产方式的影响,辊颈铬含量较高,应力较大,在使用过程中,辊颈容易发生断裂事故;同时外层工作层厚度受到溢流铁水的冲刷,个别无法满足用户的使用。
技术实现要素:5.本发明的目的是提供一种适用于棒材切分机架高硼高速钢离心复合轧辊的生产方法,提高高速钢轧辊的基体强度,细化晶粒,克服棒材轧机切分机架的轧制环境,适应切分机架轧制。
6.为实现上述目的,本发明采用的技术方案为:
7.一种高硼高速钢离心复合轧辊的制造方法,包括造型、熔炼、浇注、开箱、热处理,在高速钢外层铁水出炉前,向熔炼炉内加入硼铁,出炉时加入一定量的氮化合金剂,外层浇注一段时间后浇入一次芯,待合箱后再浇入芯部铁水。
8.本发明技术方案的进一步改进在于:所述的复合轧辊的高速钢外层化学组成成分的重量百分比:c:1.2~2.2、cr:7.0~13.5、ni:0.2~1.2、mo:0.5~1.5、v:1.0~2.5、w:1.0~2.5、nb:1.0~3.0、re:0.05~0.1、p≤0.04、s≤0.04、mn≤0.5、si:0.6~1.5,b:0.05~0.5,其余为fe;一次芯半钢熔炼,化学组成成分的重量百分比为:c:1.0~1.5,cr+mo+v+w:0.01~0.15、re:0.1、p≤0.03、s≤0.03、mn:0.3~0.8、si:1.1~1.8,其余为fe;二次芯芯部球墨铸铁熔炼,化学组成成分的重量百分比为为:c:2.9~3.6、cr:0.1~0.5、ni:0.2~0.8、re:0.1、p≤0.03、s≤0.02、mn:0.3~1.0、si:1.3~2.0,其余为fe。
9.一种高硼高速钢离心复合轧辊的制造方法,其特征在于所述制造步骤为:
10.s1、造型,铸型箱包括端盖、辊身型箱、轴颈型箱,轴颈型箱包括底箱和冒口型箱,辊身部分采用金属型喷涂料;轴颈采用水玻璃、固化剂、硅石砂造型,表面刷醇基涂料;端盖
用硅石砂、粘土造型,底箱的底部封闭;
11.s2、中频炉熔炼,分别进行高速钢外层熔炼,一次芯半钢熔炼,二次芯球墨铸铁熔炼;
12.s3、分别对高速钢外层、一次芯及二次芯铁水进行处理,高速钢外层出炉前,在炉内加入硼铁,一次芯出炉前炉内加入0.1%
‑
0.5%硅铝钡合金,二次芯球墨铸铁进行球化孕育处理;
13.s4、高速钢外层出炉时,在包内加入0.2~0.6%稀土、0.3%~1.5%的氮化合金剂进行处理;
14.s5、离心浇注,在离心力下先浇注高速钢工作层,一段时间后浇入一次芯,
15.当铸层冷却至1100
‑
1150℃时停止,进行合箱操作;
16.s6、合箱之后进行二次芯芯部浇注,浇注经球化后的二次芯部铁水;
17.s7、冷却至常温开箱,粗加后热处理。
18.本发明技术方案的进一步改进在于:所述的氮化合金剂的为氮化铬。
19.本发明技术方案的进一步改进在于:步骤s5中外层浇注5分钟后浇入一次芯。
20.本发明技术方案的进一步改进在于:步骤s3中硼铁的加入量为1%
‑
2%,所述球化处理时所用的球化剂为稀土镁硅铁合金,加入量1.0~1.6%,孕育剂为75硅铁,添加量为0.4~1.0%。
21.本发明技术方案的进一步改进在于:步骤s7中热处理的过程:加热温度为20~30℃/h的升温速度升温至1000~1120℃保温2~4h,出炉以130~140℃/h的速度进行冷却至400~450℃,再以20~30℃/h的升温速度升温升至500~550℃保温10~32h,再以20~30℃/h的降温速度降温至室温,再以20~30℃/h的升温速度升温升至500~550℃保温10~32h,再以20~30℃/h的降温速度降温至室温,再以20~30℃/h的升温速度升温升至500~550℃保温10~32h,出炉空冷至室温。
22.本发明技术方案的进一步改进在于:步骤s3中一次芯出炉前炉内加入硅铝钡合金处理,反应温度1580
‑
1650℃,二次芯球墨铸铁进行球化孕育处理,反应温度为1500~1600℃;步骤s4中高速钢外层包内添加0.2~0.6%稀土和氮化合金剂进行处理,反应温度1550~1650℃。
23.由于采用了上述技术方案,本发明取得的有益效果如下:
24.硼铁和氮化合金剂的加入,净化了钢水,细化了晶粒,提高了高速钢轧辊基体强度;铸造的高速钢轧辊能够很好的适用于棒材轧机切分机架。
25.本技术的制造工艺降低了劳动强度,节约生产成本;高速钢轧辊基体强度提高;克服了传统高速钢轧辊在棒材切分机架的使用问题,适应了棒材切分机架轧制环境。采用本技术的技术方案后,外层铁水溶蚀量在10
‑
15mm,而采用溢流方式外层铁水溶蚀20
‑
30mm,可以完全满足用户的使用要求。
具体实施方式
26.下面结合实例对本发明做进一步说明。
27.实施例1
28.一种适用于棒材切分机架高硼高速钢离心复合轧辊的制造方法,包括造型、熔炼、
浇注、开箱、热处理。
29.1、造型,辊身部分采用金属型喷涂料;轴颈采用水玻璃、固化剂、硅石砂造型,表面刷醇基涂料;端盖用硅石砂、粘土造型。
30.2、中工频炉熔炼,进行轧辊外层钢水熔炼,熔炼温度1500~1650℃,化学成分重量百分比为1.2c、13.5cr、0.2ni、1.5mo、1.0v、1.0w、1.0nb、0.1re、p≤0.04、s≤0.04、mn≤0.5、0.6si,0.5b,其余为fe。
31.一次芯芯部半钢熔炼,熔炼温度1580~1650℃,化学成分重量百分比为1.0c、0.15cr+mo+v+w、0.1re、p≤0.03、s≤0.03、mn0.3~0.8、1.1si,其余为fe。
32.二次芯芯部球墨铸铁熔炼,熔炼温度1500~1650℃,化学成分重量百分比为2.9c、0.5cr、0.2ni、0.1re、p≤0.03、s≤0.02、1.0mn、2.0si,其余为fe。
33.3、分别对高速钢外层、一次芯及二次芯铁水进行处理,高速钢外层出炉前,在炉内加入硼铁,硼铁的加入量为1%,出炉时,高速钢外层包内添加0.2%稀土、1.5%的氮化合金剂进行处理,反应温度1550~1650℃;一次芯出炉前炉内加入0.1%硅铝钡合金,反应温度1580
‑
1650℃;二次芯球墨铸铁均进行球化孕育处理,球化剂为稀土镁硅铁合金,加入量1.6%,孕育剂为75硅铁,添加量为1.0%,反应温度为1500~1600℃;
34.4、离心浇注,在离心力下,以1420~1480℃浇注温度浇入高速钢轧辊外层,离心重力倍数50g,5分钟后浇入一次芯。
35.5、二次芯芯部浇注,将上一步骤的铸件与辊颈模具合箱,要求离心机停转至合完箱浇注芯部铁水控制在7分钟以内,合完箱静态下浇注步骤2经球化处理的二次芯球墨铸铁铁水,浇注温度为1400~1550℃;
36.6、常温冷却至200~320℃开箱,粗加后热处理,以加热温度为20~30℃/h的升温速度升温至1000~1120℃保温2~4h,出炉以130~140℃/h的速度进行冷却至400~450℃,再以20~30℃/h的升温速度升温升至500~550℃保温10~32h,再以20~30℃/h的降温速度降温至室温,再以20~30℃/h的升温速度升温升至500~550℃保温10~32h,再以20~30℃/h的降温速度降温至室温,再以20~30℃/h的升温速度升温升至500~550℃保温10~32h,出炉空冷至室温。
37.实施例2
38.本实施例和实施例1的区别在于:
39.中工频炉熔炼,轧辊外层钢水熔炼的熔炼温度1500~1650℃,化学成分重量百分比为2.2c、7.0cr、0.2ni、0.5mo、2.5v、1.0w、3.0nb、0.05re、p≤0.04、s≤0.04、mn≤0.5、1.5si,0.05b,其余为fe。
40.一次芯芯部半钢熔炼的熔炼温度1580~1650℃,化学成分重量百分比为1.5c、0.01cr+mo+v+w、0.1re、p≤0.03、s≤0.03、mn0.8、1.8si,其余为fe。
41.二次芯芯部球墨铸铁熔炼,熔炼温度1500~1650℃,化学成分重量百分比为3.6c、0.1cr、0.8ni、0.1re、p≤0.03、s≤0.02、mn0.3、1.3si,其余为fe
42.分别对高速钢外层、一次芯及二次芯铁水进行处理,高速钢外层出炉前,在炉内加入硼铁,硼铁的加入量为2%,出炉时,高速钢外层包内添加0.6%稀土、0.3%的氮化合金剂进行处理,反应温度1550~1650℃;一次芯出炉前炉内加入0.5%硅铝钡合金,反应温度1580
‑
1650℃;二次芯球墨铸铁均进行球化孕育处理,球化剂为稀土镁硅铁合金,加入量
1.0%,孕育剂为75硅铁,添加量为0.4%,反应温度为1500~1600℃;
43.离心浇注,以1420~1480℃浇注温度浇入高速钢轧辊外层,离心重力倍数70g,5分钟后浇入一次芯。
44.二次芯芯部浇注,将上述步骤的铸件与辊颈模具合箱,要求离心机停转至合完箱浇注芯部铁水控制在7分钟以内,合完箱静态下浇注上述步骤经球化处理的二次芯球墨铸铁铁水,浇注温度为1400~1550℃;
45.常温冷却至200~320℃开箱,粗加后热处理,以加热温度为20~30℃/h的升温速度升温至1000~1120℃保温2~4h,出炉以130~140℃/h的速度进行冷却至400~450℃,再以20~30℃/h的升温速度升温升至500~550℃保温10~32h,再以20~30℃/h的降温速度降温至室温,再以20~30℃/h的升温速度升温升至500~550℃保温10~32h,再以20~30℃/h的降温速度降温至室温,再以20~30℃/h的升温速度升温升至500~550℃保温10~32h,出炉空冷至室温。
46.实施例3
47.本实施例和实施例1的区别在于:
48.中工频炉熔炼,轧辊外层钢水熔炼的熔炼温度1500~1650℃,化学成分重量百分比为1.8c、10.5cr、0.9ni、1.0mo、2.1v、1.8w、2.3nb、0.08re、p≤0.04、s≤0.04、mn≤0.5、1.2si,0.3b,其余为fe。
49.一次芯芯部半钢熔炼的熔炼温度1580~1650℃,化学成分重量百分比为1.2c、0.09cr+mo+v+w、0.1re、p≤0.03、s≤0.03、mn0.5、1.5si,其余为fe。
50.二次芯芯部球墨铸铁熔炼,熔炼温度1500~1650℃,化学成分重量百分比为3.2c、0.2cr、0.5ni、0.1re、p≤0.03、s≤0.02、mn0.8、1.7si,其余为fe
51.分别对高速钢外层、一次芯及二次芯铁水进行处理,高速钢外层包内添加0.4%稀土、0.7%的氮化合金剂进行处理,反应温度1550~1650℃;一次芯出炉前炉内加入0.3%硅铝钡合金,反应温度1580
‑
1650℃;二次芯球墨铸铁均进行球化孕育处理,球化剂为稀土镁硅铁合金,加入量1.3%,孕育剂为75硅铁,添加量为0.7%,反应温度为1500~1600℃;
52.离心浇注,以1420~1480℃浇注温度浇入高速钢轧辊外层,离心重力倍数60g,5分钟后浇入一次芯。
53.二次芯芯部浇注,将上述步骤的铸件与辊颈模具合箱,要求离心机停转至合完箱浇注芯部铁水控制在7分钟以内,合完箱静态下浇注上述步骤经球化处理的二次芯球墨铸铁铁水,浇注温度为1400~1550℃;
54.常温冷却至200~320℃开箱,粗加后热处理,以加热温度为20~30℃/h的升温速度升温至1000~1120℃保温2~4h,出炉以130~140℃/h的速度进行冷却至400~450℃,再以20~30℃/h的升温速度升温升至500~550℃保温10~32h,再以20~30℃/h的降温速度降温至室温,再以20~30℃/h的升温速度升温升至500~550℃保温10~32h,再以20~30℃/h的降温速度降温至室温,再以20~30℃/h的升温速度升温升至500~550℃保温10~32h,出炉空冷至室温。
55.实施例4
56.本实施例采用的是溢流工艺:
57.造型,其他和实施例1相同,不同点在于本实施例的底箱连接溢流管;
58.中工频炉熔炼所用的轧辊外层钢、一次芯、二次芯的钢水的化学成分和实施例1中的成分相同,对高速钢外层、一次芯及二次芯铁水进行的处理方法也相同。
59.离心浇注,以1420~1480℃浇注温度浇入高速钢轧辊外层,离心重力倍数50g,当高速钢轧辊外层型腔温度达到1220~1280℃时,离心机停转,将放置浇注好的高速钢轧辊外层的型箱与用于浇注辊颈的型箱进行合箱,合完箱静态下将经过处理好的一次芯铁水浇注到合并后的型箱内,浇至一次芯铁水从溢流槽流出停止,浇注温度为1400~1550℃;一次芯浇注完成后紧接着浇注处理好的二次芯铁水,浇注温度为1280~1400℃,浇入量为一次芯铁水质量的3倍,确保将上一步骤所浇入的过渡层铁水全部冲洗并置换掉。确保将上一步骤中所浇入的一次芯铁水全部冲洗并置换掉。
60.常温冷却至200~320℃开箱,粗加后热处理,热处理方式和实施例1相同。
61.实施例5
62.本实施例采用的是溢流工艺:
63.造型,其他和实施例2相同,不同点在于本实施例的底箱连接溢流管;
64.中工频炉熔炼所用的轧辊外层钢、一次芯、二次芯的钢水的化学成分和实施例2中的成分相同,对高速钢外层、一次芯及二次芯铁水进行的处理方法也相同。
65.离心浇注,以1420~1480℃浇注温度浇入高速钢轧辊外层,离心重力倍数50g,当高速钢轧辊外层型腔温度达到1220~1280℃时,离心机停转,将放置浇注好的高速钢轧辊外层的型箱与用于浇注辊颈的型箱进行合箱,合完箱静态下将经过处理好的一次芯铁水浇注到合并后的型箱内,浇至一次芯铁水从溢流槽流出停止,浇注温度为1400~1550℃;一次芯浇注完成后紧接着浇注处理好的二次芯铁水,浇注温度为1280~1400℃,浇入量为一次芯铁水质量的3倍,确保将上一步骤所浇入的过渡层铁水全部冲洗并置换掉。确保将上一步骤中所浇入的一次芯铁水全部冲洗并置换掉。
66.常温冷却至200~320℃开箱,粗加后热处理,热处理方式和实施例2相同。
67.对上述各实施例制备的复合轧辊进行力学性能检测,超声波探伤执行标准gb/t1503
‑
2008。结果及使用性能见表1
68.表1
69.