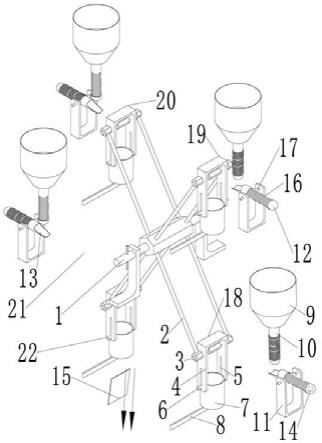
1.本发明涉及用于汽车的压铸高导热铝合金制作工艺。
背景技术:2.高压铸造成型技术是铝及铝合金材料铸件最为常用的成型方法之一,广泛的应用于汽车,通讯,能源,消费电子等行业。通常来说,压力铸造铝合金部件具有结构复杂,薄壁轻量化,易回收等优点。如今,随着新能源和通讯技术的快速发展,对于大型结构和功能一体化要求对先进材料提出了苛刻的要求。以往的铝合金材料设计,是在高强度与高塑性之间平衡的二维优化,即强度和塑性的乘积最大化,简称强塑积最大化。由于一些压铸铝合金部件,特别是通讯和新能源汽车的散热部件需求激增,又增加了导热方面的要求,需要提供一个强度,塑性和导热率的三维优化体系,同时还要兼顾大型复杂结构件的超高流动性和凝固特性等工艺方面的要求,需要对压铸铝合金材料进行重新设计。因此,需要从材料设计和熔炼制备工艺相结合,大幅度提到铸件产品的机械性能和导热性能。
3.目前,普通压铸铝合金以alsi9cu3和adc12为例,导热系数为100~120w/m
•
k左右,铸态屈服强度在130
‑
150mpa之间,延伸率在3%以内(强塑积小于500mpa%)。虽然传统压铸材料的成形性较好,但是不能有效满足电子、电气、通讯、机电等结构部件在服役过程中因元器件等发热过大的现象。普通压铸铝合金不能很好的解决上述结构功能一体化的需求。
技术实现要素:4.本发明所要解决的技术问题总的来说是提供一种压铸用高导热铝合金制备设备及其制备方法。本发明是为了解决上述不足,从合金的组分设计开始,采用热力学计算的方法,优化强化相和阻碍散热的固溶原子和析出相的体积分数,同时根据实验结果优化材料的流动和凝固特性。提供一种合金流动性好、机械性能优异、导热系数高耐腐蚀性良好的压铸用高导热铝合金及其制备方法。母案cn202010856218.2 压铸用高导热铝合金制备设备及其制备方法;申请号cn202010856218.2;申请日20200824。
5.为解决上述问题,本发明所采取的技术方案是:一种压铸用高导热铝合金制备方法,该高导热铝合金,各个配料组分含量为:硅7.0~11.5%;镁0.15~0.65%;铁0.10
‑
0.65%;锰≤0.15%;铜≤1.5%;硼0.01~0.05%;钛0.01~0.05%;铬0.05~0.25%;锌≤0.03%;其余为铝;镁含量、钛含量及十倍的硼含量的总和区间为0.3%
‑
0.8%之间,即0.3%≤mg%+5
×
ti%+10
×
b%≤0.8%;该高导热铝合金其取样导热系数大于180w/m
•
k,强塑积> 1000mpa%;该方法包括以下步骤:s1,根据成分配料;其各个配料组分含量为:硅7.0~11.5%;镁0.15~0.65%;铁0.10
‑
0.65%;锰≤0.15%;铜≤1.5%;硼0.01~0.05%;钛0.01~0.05%;铬0.05~0.25%;锌≤0.03%;其余为铝;镁含量、钛含量及十倍的硼含量的总和区间为0.3%
‑
0.8%之间,即0.3%≤mg%+5
×
ti%+10
×
b%≤0.8%;
s2,将配好的纯度铝合金锭加入熔炉中保温在t1,t1的范围760℃
‑
780℃;s3,加入纯硅熔炼熔炼后保持温度在t2,t2的范围720℃
‑
740℃;s4,加入铝锰中间合金、铝铬中间合金和铝钛中间合金熔炼熔炼后降温,保持t3,t3的范围680℃
‑
700℃,时间大于30分钟(t4
‑
t3);s5,加入镁熔炼熔炼后,升温到t2,t2的范围720℃
‑
740℃;s6,加入铝硼中间合金熔炼熔炼后升温,保持在t1,t1的范围760℃
‑
780℃;s7,首先,搅拌铝合金液5
‑
15分钟使成分均匀;然后,除渣静置30
‑
60分钟(t6
‑
t5)取样化验;s8,根据化验结果调整各元素成分含量直至达到要求的范围;s9,精炼除气,将精炼剂通过氮气吹入铝合金液底部进行精炼除气直至精炼完毕。
6.作为上述技术方案的进一步改进:在步骤s1与s3中,合金化元素硅为高纯工业硅,纯度高于99.5%,高纯铝合金锭为a00或者纯度为99.8%的纯铝锭;熔炉为电阻炉感应炉或反射炉 。
7.借助于制备设备; 制备设备包括熔炉部和/或除杂部。
8.一种压铸用高导热铝合金制备方法,该方法包括以下步骤;步骤一,首先,将配料在各个上料在加热熔炉中加热到熔融态;然后,熔融态的配料通过配料输出管从豁口滴入到定量存储罐中;其次,当定量存储罐中配料到达设定重量后,定量存储罐在定量支架摆动为头重脚轻,熔融态配料从进料上开口下流到对应工位电加热炉中;再次,根据设定温度,对各个工位的电加热炉加热至设定条件,在定量存储罐的搅拌釜对其搅拌;紧接着,在下出料工位将配置好的配料输出;步骤二,首先,驱动轴驱动偏心轴在吊装孔中转动,带动倾斜底部网框在分装加热炉中晃动,从而对分装加热炉内熔融配件进行搅拌,同时避免杂物堵塞网孔;然后,伸缩杆驱动偏心轴与吊装孔分离,同时,吊耳将存在大于网孔的杂物的倾斜底部网框取出;其次,对分装加热炉进行静置加热。
9.一种压铸用高导热铝合金制备设备,包括熔炉部和/或除杂部。
10.作为上述技术方案的进一步改进:在端铰接轴上铰接有悬挂架,在悬挂架下端两侧设置有导向长槽,在导向长槽中设置有悬挂轴,在悬挂轴之间安装有电加热炉,在电加热炉一侧设置有拨动臂;在旋转中心架上分布有第一配料工位、第二配料工位、第三配料工位、第n配料工位及下出料工位;第一配料工位、第二配料工位、第三配料工位、第n配料工位用于对应的配料的上料部;下出料工位位于旋转中心架下方;上料部包括预加热熔炉,用于将配料加热至熔融态;在预加热熔炉下端输出口设置有带有加热丝的配料输出管,在配料输出管下端设置有定量支架,在定量支架上通过铰接轴铰接有定量存储罐的中前部,在定量存储罐的进料上开口上部具有豁口,该豁口对应配料输出管的下出口且具有截止阀;在定量存储罐上设置有配重件,根据所加入配料重量配置对应重量的配重件;当定量存储罐空载的时候,定量存储罐头轻脚重;当配料输出管加入定量存储罐
的熔融液态的配料,当配料加入重量达到所设重量后,定量存储罐在定量支架摆动为头重脚轻,熔融态配料从进料上开口下流到电加热炉中;在定量存储罐上设置有定量加热线圈,在定量支架的铰接轴上套装有与定量加热线圈连接的定量电滑环,在定量支架上设置有与定量电滑环接触的端子;在下出料工位进入侧设置有导向斜板,导向斜板用于与拨动臂接触,在加热熔炉下降的过程,拨动臂在导向斜板上滑动,使得定量存储罐向下倾翻出料;在下出料工位设置有加热熔炉,加热熔炉具有下排料口;除杂部,包括位于下出料工位下方的分装加热炉,在分装加热炉中设置有带有起吊耳的倾斜底部网框;在倾斜底部网框上方设置有支耳座,在支耳座上设置有吊装孔,在吊装孔上活动有由振动电机的驱动轴通过伸缩杆驱动的偏心轴;偏心轴在吊装孔中转动,带动倾斜底部网框在分装加热炉中晃动。
11.本发明与现有技术相比的优点是:本发明的导热系数大于160w./m.k高、且压铸性能耐腐蚀性良好且机械加工性能好及原材料成本低等优点可广泛用于电子电气通讯机电行业可有效解决电子电气通讯机电行业存在的许多工作时因元器件等发热而影响工作的现象对降低生产成本有很好的作用。
12.本发明通过调整合金成分和熔炼过程的中间合金添加顺序,及温度和保持时间的调节,保证了压铸铝合金具有铸态条件下的高导热系数(大于180w/m
•
k),强塑积超过1000mpa%,而且压铸性能和耐腐蚀性良好,有效地解决了结构功能一体化压铸件的问题。本发明设计合理、成本低廉、结实耐用、安全可靠、操作简单、省时省力、节约资金、结构紧凑且使用方便。
附图说明
13.图1是本发明的工艺流程图;图2是本发明的温度控制曲线图;图3是本发明的加热使用结构示意图。
14.图4是本发明的熔融结构示意图。
15.图5是本发明的静置结构示意图。
16.图6是本发明的网框结构示意图。其中: 1、旋转中心架;2、加长臂;3、端铰接轴;4、悬挂架;5、导向长槽;6、悬挂轴;7、电加热炉;8、拨动臂;9、预加热熔炉;10、配料输出管;11、定量支架;12、定量存储罐;13、进料上开口;14、配重件;15、导向斜板;16、定量加热线圈;17、定量电滑环;18、第一配料工位;19、第二配料工位;20、第三配料工位;21、第n配料工位;22、下出料工位;23、加热熔炉;24、下排料口;25、分装加热炉;26、支耳座;27、吊装孔;28、偏心轴;29、驱动轴;30、倾斜底部网框;31、起吊耳。
具体实施方式
17.如图1
‑
6所示,本实施例的压铸用高导热铝合金制备方法,该高导热铝合金,各个配料组分含量为:硅7.0~11.5%;镁0.15~0.65%;铁0.10
‑
0.65%;锰≤0.15%;铜≤1.5%;硼0.01~0.05%;钛0.01~0.05%;铬0.05~0.25%;锌≤0.03%;其余为铝;镁含
量、钛含量及十倍的硼含量的总和区间为0.3%
‑
0.8%之间,即0.3%≤mg%+5
×
ti%+10
×
b%≤0.8%;该高导热铝合金其取样导热系数大于180w/m
•
k,强塑积> 1000mpa%;该方法包括以下步骤:s1,根据成分配料;其各个配料组分含量为:硅7.0~11.5%;镁0.15~0.65%;铁0.10
‑
0.65%;锰≤0.15%;铜≤1.5%;硼0.01~0.05%;钛0.01~0.05%;铬0.05~0.25%;锌≤0.03%;其余为铝;镁含量、钛含量及十倍的硼含量的总和区间为0.3%
‑
0.8%之间,即0.3%≤mg%+5
×
ti%+10
×
b%≤0.8%;s2,将配好的纯度铝合金锭加入熔炉中保温在t1,t1的范围760℃
‑
780℃;s3,加入纯硅熔炼熔炼后保持温度在t2,t2的范围720℃
‑
740℃;s4,加入铝锰中间合金、铝铬中间合金和铝钛中间合金熔炼熔炼后降温,保持t3,t3的范围680℃
‑
700℃,时间大于30分钟(t4
‑
t3);s5,加入镁熔炼熔炼后,升温到t2,t2的范围720℃
‑
740℃;s6,加入铝硼中间合金熔炼熔炼后升温,保持在t1,t1的范围760℃
‑
780℃;s7,首先,搅拌铝合金液5
‑
15分钟使成分均匀;然后,除渣静置30
‑
60分钟(t6
‑
t5)取样化验;s8,根据化验结果调整各元素成分含量直至达到要求的范围;s9,精炼除气,将精炼剂通过氮气吹入铝合金液底部进行精炼除气直至精炼完毕。
18.在步骤s1与s3中,合金化元素硅为高纯工业硅,纯度高于99.5%,高纯铝合金锭为a00或者纯度为99.8%的纯铝锭;熔炉为电阻炉感应炉或反射炉 。
19.借助于制备设备; 制备设备包括熔炉部和/或除杂部。
20.本实施例的压铸用高导热铝合金制备方法,该方法包括以下步骤;针对s1
‑
s6,步骤一,首先,将配料在各个上料在加热熔炉9中加热到熔融态;然后,熔融态的配料通过配料输出管10从豁口滴入到定量存储罐12中;其次,当定量存储罐12中配料到达设定重量后,定量存储罐12在定量支架11摆动为头重脚轻,熔融态配料从进料上开口13下流到对应工位电加热炉7中;再次,根据设定温度,对各个工位的电加热炉7加热至设定条件,在定量存储罐12的搅拌釜对其搅拌;紧接着,在下出料工位22将配置好的配料输出;针对s7中 ,步骤二,首先,驱动轴29驱动偏心轴28在吊装孔27中转动,带动倾斜底部网框30在分装加热炉25中晃动,从而对分装加热炉25内熔融配件进行搅拌,同时避免杂物堵塞网孔;然后,伸缩杆驱动偏心轴28与吊装孔27分离,同时,吊耳31将存在大于网孔的杂物的倾斜底部网框30取出;其次,对分装加热炉25进行静置加热。
21.本实施例的压铸用高导热铝合金制备设备,包括熔炉部和/或除杂部。
22.在端铰接轴3上铰接有悬挂架4,在悬挂架4下端两侧设置有导向长槽5,在导向长槽5中设置有悬挂轴6,在悬挂轴6之间安装有电加热炉7,在电加热炉7一侧设置有拨动臂8;在旋转中心架1上分布有第一配料工位18、第二配料工位19、第三配料工位20、第n配料工位21及下出料工位22;第一配料工位18、第二配料工位19、第三配料工位20、第n配料工位21用于对应的配料的上料部;下出料工位22位于旋转中心架1下方;
上料部包括预加热熔炉9,用于将配料加热至熔融态;在预加热熔炉9下端输出口设置有带有加热丝的配料输出管10,在配料输出管10下端设置有定量支架11,在定量支架11上通过铰接轴铰接有定量存储罐12的中前部,在定量存储罐12的进料上开口13上部具有豁口,该豁口对应配料输出管10的下出口且具有截止阀;在定量存储罐12上设置有配重件14,根据所加入配料重量配置对应重量的配重件14;当定量存储罐12空载的时候,定量存储罐12头轻脚重;当配料输出管10加入定量存储罐12的熔融液态的配料,当配料加入重量达到所设重量后,定量存储罐12在定量支架11摆动为头重脚轻,熔融态配料从进料上开口13下流到电加热炉7中;在定量存储罐12上设置有定量加热线圈16,在定量支架11的铰接轴上套装有与定量加热线圈16连接的定量电滑环17,在定量支架11上设置有与定量电滑环17接触的端子;在下出料工位22进入侧设置有导向斜板15,导向斜板15用于与拨动臂8接触,在加热熔炉23下降的过程,拨动臂8在导向斜板15上滑动,使得定量存储罐12向下倾翻出料;在下出料工位22设置有加热熔炉23,加热熔炉23具有下排料口24;除杂部,包括位于下出料工位22下方的分装加热炉25,在分装加热炉25中设置有带有起吊耳31的倾斜底部网框30;在倾斜底部网框30上方设置有支耳座26,在支耳座26上设置有吊装孔27,在吊装孔27上活动有由振动电机的驱动轴29通过伸缩杆驱动的偏心轴28;偏心轴28在吊装孔27中转动,带动倾斜底部网框30在分装加热炉25中晃动。
23.实施例1准备如下组分:硅:7.5%;镁0.3%5%;铁:0.3%5%;锰:0.3%5%;铜:0.05%;硼:0.013%;钛:0.02%;铬:0.25%;锌:0.02%;其余为铝;mg%+5ti%+10
×
b%=0.58%<0.8%如图1所示,将上述材料按如下步骤:(1)根据成分配料;(2)将配好的纯度铝合金锭加入熔炉中保温在t1(760℃);(3)加入纯硅熔炼熔炼后保持温度在t2(740℃);(4)加入铝锰中间合金、铝铬中间合金和铝钛中间合金熔炼熔炼后降温,保持t3(700℃),时间60分钟(t4
‑
t3);(5)加入镁熔炼熔炼后,升温到t2(720℃);(6)加入铝硼中间合金熔炼熔炼后升温,保持在t1(77℃);(7)搅拌铝合金液5
‑
15分钟使成分均匀然后除渣静置45分钟(t6
‑
t5)取样化验;(8)根据化验结果调整各元素成分含量直至达到要求的范围;(9)精炼除气将精炼剂通过氮气吹入铝合金液底部进行精炼除气直至精炼完毕。
24.实施例1所获得的高导热高强韧铝合金的导热率为182w/m
•
k,屈服强度145mpa,延伸率8.5%,强塑积1232.5mpa% > 1000mpa% ;实施例2准备如下组分:硅:9.5%;镁0.28%;铁:0.45%;锰:0.45%;铜:0.25%;硼:0.018%;钛:0.03%;铬:0.25%;锌:0.02%;其余为铝;mg%+5ti%+10
×
b%=0.61%<0.8%;如图1所示,将上述材料按如下步骤:
(1)根据成分配料;(2)将配好的纯度铝合金锭加入熔炉中保温在t1(770℃);(3)加入纯硅熔炼熔炼后保持温度在t2(730℃);(4)加入铝锰中间合金、铝铬中间合金和铝钛中间合金熔炼熔炼后降温,保持t3(690℃),时间45分钟(t4
‑
t3);(5)加入镁熔炼熔炼后,升温到t2(720℃);(6)加入铝硼中间合金熔炼熔炼后升温,保持在t1(780℃);(7)搅拌铝合金液5
‑
15分钟使成分均匀然后除渣静置60分钟(t6
‑
t5)取样化验;(8)根据化验结果调整各元素成分含量直至达到要求的范围;(9)精炼除气将精炼剂通过氮气吹入铝合金液底部进行精炼除气直至精炼完毕。
25.所获得的高导热高强韧铝合金的导热率为187w/m
•
k,屈服强度132mpa,延伸率9.5%,强塑积1254mpa% > 1000mpa%;实施例3准备如下组分:硅:8.5%;镁0.48%;铁:0.25%;锰:0.55%;铜:0.25%;硼:0.025%;钛:0.01%;铬:0.20%;锌:0.03%;其余为铝;mg%+5ti%+10
×
b%=0.78%<0.8%如图1所示,将上述材料按如下步骤:(1)根据成分配料;(2)将配好的纯度铝合金锭加入熔炉中保温在t1(760℃);(3)加入纯硅熔炼熔炼后保持温度在t2(720℃);(4)加入铝锰中间合金、铝铬中间合金和铝钛中间合金熔炼熔炼后降温,保持t3(690℃),时间45分钟(t4
‑
t3);(5)加入镁熔炼熔炼后,升温到t2(720℃);(6)加入铝硼中间合金熔炼熔炼后升温,保持在t1(770℃);(7)搅拌铝合金液5
‑
15分钟使成分均匀然后除渣静置60分钟(t6
‑
t5)取样化验;(8)根据化验结果调整各元素成分含量直至达到要求的范围;(9)精炼除气将精炼剂通过氮气吹入铝合金液底部进行精炼除气直至精炼完毕。
26.实施例3所获得的高导热高强韧铝合金的导热率为185w/m
•
k,屈服强度165mpa,延伸率6.4%,强塑积1256mpa% > 1000mpa%。
27.实施例4,准备如下组分:硅:7%;镁0.15%;铁:0.1%;锰:0.01%;铜:0.01%;硼:0.05%;钛:0.01%;铬:0.05%;锌:0.01%;其余为铝;t1(760℃);t2(720℃); t3(680℃), mg%+5ti%+10
×
b%=0.5%<0.8%;所获得的高导热高强韧铝合金的导热率为192w/m
•
k,屈服强度148mpa,延伸率8.7%,强塑积1210mpa% > 1000mpa% ;实施例5,准备如下组分:硅:11.5%;镁0.45%;铁:0.65%;锰:0.15%;铜:1.5%;硼:0.01%;钛:0.01%;铬:0.25%;锌:0.03%;其余为铝;mg%+5ti%+10
×
b%=0.6%<0.8% ;t1(760℃);t2(720℃); t3(680℃),所获得的高导热高强韧铝合金的导热率为188w/m
•
k,屈服强度135mpa,延伸率8.1%,强塑积1278mpa% > 1000mpa% ;实施例6,准备如下组分:硅:11.5%;镁0.15%;铁:0.65%;锰:0.14%;铜:1.4%;
硼:0.01%;钛:0.05%;铬:0.25%;锌:0.03%;其余为铝;mg%+5ti%+10
×
b%=0.7%<0.8%;t1(780℃);t2(740℃); t3(700℃)。
28.所获得的高导热高强韧铝合金的导热率为190w/m
•
k,屈服强度151mpa,延伸率8.9%,强塑积1278mpa% > 1000mpa% 。
29.本发明通过旋转中心架1实现各个工序的衔接,加长臂2从而扩展空间,实现对各个工位的兼容,端铰接轴3为短轴结构,从而避开中间,而不沾染熔融配料,悬挂架4实现悬挂,导向长槽5从而实现兼容从而减少轴承等部件。同样保证了灵活转动,长槽上优选有开口。从而方便拆装,悬挂轴6,电加热炉7,实现了分装加热,将整个划分为若干单个,从而满足不同区域的加热,降低能耗,拨动臂8上可以带有滚轮,以降低摩擦力,预加热熔炉9实现对各个配料的单独加热为熔融态,从而避免固体加入等待变为熔融态的时间,配料输出管10实现精确输出,定量支架11为支撑,定量存储罐12利用重力与配重件14实现称量,当罐中熔融态配料大于设定重量,罐体的进料上开口13下摆送料,利用豁口进料,导向斜板15与拨动臂8使得电加热炉7逐渐倾倒,从而使得熔融液流出,定量加热线圈16实现持续加热,定量电滑环17实现在摆动中与端子接触通电,第一配料工位18,第二配料工位19,第三配料工位20,第n配料工位21可以根据配料来增减,下出料工位22实现输出,加热熔炉23实现持续加热,下排料口24实现加热,分装加热炉25实现保温加热,支耳座26实现悬挂,吊装孔27与偏心轴28配合实现了倾斜底部网框30在分装加热炉25的晃动搅拌与分离,从而将大颗粒杂质的存留,起吊耳31实现了吊装,驱动轴29实现偏心驱动,通过伸缩杆实现分离,本发明通过上下分布,从而利用热气上升原理,对各个工位件进行热辐射与热对流。将整体加热分为单个加热,提高效率,节能。维修与拆卸方便。
30.本发明充分描述是为了更加清楚的公开,而对于现有技术就不再一一列举。