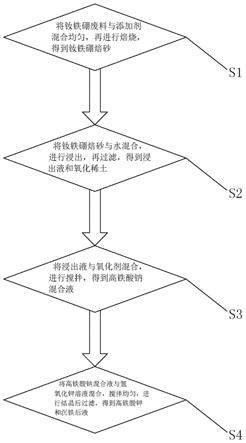
1.本发明涉及钕铁硼废料回收技术领域,特别涉及一种钕铁硼废料分离回收稀土和铁的方法。
背景技术:2.钕铁硼是一种优良的永磁体,2020年其产量超过20万吨,且每年以10%的速度递增。随着钕铁硼需求量越来越大以及产品寿命到期,废弃钕铁硼越来越多,钕铁硼废料是指失效钕铁硼磁体或在钕铁硼磁体磨、削、切加工过程中产生的油泥和边角料等固体废料。
3.在钕铁硼磁体磨、削、切加工过程中,每生产一吨钕铁硼磁铁会产生30%左右的钕铁硼废料,这些废料因含有20~30%的稀土和60~70%的铁而具有极高的价值,因此,从钕铁硼废料中回收稀土和铁等有价金属对于资源循环利用具有重要意义。
4.目前国内,主要是从钕铁硼废料中回收稀土,比如,采用焙烧
‑
盐酸浸出工艺回收钕铁硼废料中的稀土,尽管其稀土浸出率高,但对于回收稀土后液中的铁以及富铁渣没有进一步处理和回收,而且采用酸浸不仅腐蚀设备,且产生大量含氯废水。钕铁硼废料回收过程中学者大部分关注价值高的稀土选择性分离和回收,但对于占比最大的铁资源却鲜有研究,导致产生大量铁渣或含铁废水,直接堆存或排放不仅浪费铁资源,还污染环境。
技术实现要素:5.为了克服上述所述的不足,本发明的目的是提供一种钕铁硼废料分离回收稀土和铁的方法,其采用添加剂在高温条件下与钕铁硼焙砂内的氧化铁反应,生成溶于水的铁酸化物,再采用水浸出,将溶于水的铁酸化物溶出,获得浸出液,而氧化稀土不溶于水,仍属于固态,从而实现稀土高效回收以及稀土和铁选择性分离的目的,再采用氧化剂氧化浸出液中铁酸化物,生成高铁酸化物,然后采用氢氧化钾与之反应,形成结晶,再过滤,从而得到高附加值的高铁酸钾,达到回收铁的目的。
6.本发明解决其技术问题的技术方案是:一种钕铁硼废料分离回收稀土和铁的方法,其中,包括如下步骤:s1、将钕铁硼废料与添加剂混合均匀,再进行焙烧,得到钕铁硼焙砂;s2、将所述钕铁硼焙砂与水混合,进行浸出,再过滤,得到浸出液和氧化稀土;s3、将所述浸出液与氧化剂混合,进行搅拌,得到高铁酸钠混合液;s4、将所述高铁酸钠混合液与氢氧化钾溶液混合,搅拌均匀,进行结晶后过滤,得到高铁酸钾和沉铁后液。
7.作为本发明的一种改进,在步骤s1内,按照质量比为1:(2~5),将所述钕铁硼废料与添加剂混合均匀。
8.作为本发明的进一步改进,在步骤s1内,所述钕铁硼废料与添加剂混合后,在600℃~1200℃的条件下焙烧2h~6h,从而得到钕铁硼焙砂。
9.作为本发明的更进一步改进,所述添加剂包括碳酸钠、碳酸氢钠、氢氧化钠和氧化
钠中至少一种。
10.作为本发明的更进一步改进,所述添加剂包括碳酸钾、碳酸氢钾、氢氧化钾和氧化钾中至少一种。
11.作为本发明的更进一步改进,在步骤s2内,按照质量与体积比为1:(3~8),将所述钕铁硼焙砂与水混合。
12.作为本发明的更进一步改进,在步骤s2内,将所述钕铁硼焙砂与水混合后,在60℃~90℃条件下浸出0.5h~4h,再过滤,从而得到浸出液和氧化稀土。
13.作为本发明的更进一步改进,在步骤s3内,按照三价铁与氧化剂的摩尔比为1∶(2~6),将所述浸出液与所述氧化剂混合。
14.作为本发明的更进一步改进,在步骤s3内,将所述浸出液与所述氧化剂混合后,在60℃~90℃条件下搅拌1h~4h,得到高铁酸钠混合液。
15.作为本发明的更进一步改进,在步骤s4内,按照高铁酸钠混合液与氢氧化钾溶液的体积比为1:(1~2),将所述高铁酸钠混合液与氢氧化钾溶液混合。
16.在本发明内,采用添加剂在高温条件下与钕铁硼焙砂内的氧化铁反应,生成溶于水的铁酸化物,再采用水浸出,将溶于水的铁酸化物溶出,获得浸出液,而氧化稀土不溶于水,仍属于固态,从而实现稀土高效回收以及稀土和铁选择性分离的目的,再采用氧化剂氧化浸出液中铁酸化物,生成高铁酸化物,然后采用氢氧化钾与之反应,形成结晶,再过滤,从而得到高附加值的高铁酸钾,达到回收铁的目的。
附图说明
17.为了易于说明,本发明由下述的较佳实施例及附图作以详细描述。
18.图1为本发明的框图;图2为本发明的工艺流程图。
具体实施方式
19.为了使本发明的目的、技术方案及优点更加清楚明白,以下结合附图及实施例,对本发明进行进一步详细说明。应当理解,此处所描述的具体实施例仅仅用以解释本发明,并不用于限定本发明。
20.目前国内有多名学者对钕铁硼废料中稀土的回收进行了研究,比如,邓华军(邓华军,段月红,邓庚凤. 钕铁硼废料中稀土的回收[j].矿冶工程,2019,39(1):76
‑
78)采用焙烧
‑
盐酸浸出工艺回收钕铁硼废料中的稀土,实验结果表明,钕铁硼废料的最佳焙烧条件为:焙烧温度700℃、焙烧时间1.5 h,此时铁氧化率可达99.30%;盐酸浸出焙烧料的最佳条件为:盐酸浓度4mol/l、液固比3:1、浸出温度90℃、浸出时间1.5h,此时稀土浸出率可达98.11%,尽管该工艺稀土浸出率高,但对于回收稀土后液中的铁以及富铁渣没有进一步处理和回收,且采用酸浸不仅腐蚀设备,且产生大量含氯废水。
[0021]
再如,刘庆生(刘庆生,吕英威,段旭. 钕铁硼废料(nh4)2so4焙烧法回收稀土[j]. 中国稀土学报,2019,37(1):91
‑
98)将钕铁硼废料与(nh4)2so4混合后焙烧,选择性回收钕铁硼废料中的稀土,结果表明:在焙烧温度400℃,焙烧时间120 min,钕铁硼与(nh4)2so4混料质量比1∶2,该条件下稀土可以获得较高的浸出率,约为92%,而fe浸出率仅为3%,尽管该
工艺稀土与铁实现了选择性分离,但稀土浸出率偏低,且对于富铁浸出渣没有进一步处理和回收。
[0022]
再如,“高温高压浸出回收钕铁硼废料中稀土的方法(cn109554549a)”,首先将钕铁硼废料在800℃条件下氧化焙烧,然后在高温高压下采用盐酸浸出钕铁硼废料,得到浸出液后将浸出液中的fe
2+
进行氧化和除杂净化,得到稀土氯化物浸出液,浸出液通过萃取分离得到稀土,通过沉淀制备稀土碳酸盐,或通过沉淀焙烧制备稀土氧化物,尽管该工艺较好的回收了稀土,但在高温高压下条件苛刻,对设备要求高,且盐酸具有挥发性,极易泄露,造成环境污染,且产生大量含氯废水,此外,该工艺仅回收了稀土,对于富铁浸出渣没有进一步回收。
[0023]
本发明针对钕铁硼废料中稀土和铁回收,进行了改进,在稀土回收的同时,也将铁进行回收。
[0024]
如图1和图2所示,本发明的一种钕铁硼废料分离回收稀土和铁的方法,包括如下步骤:s1、将钕铁硼废料与添加剂混合均匀,再进行焙烧,得到钕铁硼焙砂;s2、将钕铁硼焙砂与水混合,进行浸出,再过滤,得到浸出液和氧化稀土;s3、将浸出液与氧化剂混合,进行搅拌,得到高铁酸钠混合液;s4、将高铁酸钠混合液与氢氧化钾溶液混合,搅拌均匀,进行结晶后过滤,得到高铁酸钾和沉铁后液。
[0025]
在本发明内,采用添加剂在高温条件下与钕铁硼焙砂内的氧化铁反应,生成溶于水的铁酸化物,再采用水浸出,将溶于水的铁酸化物溶出,获得浸出液,而氧化稀土不溶于水,仍属于固态,从而实现稀土高效回收以及稀土和铁选择性分离的目的,再采用氧化剂氧化浸出液中铁酸化物,生成高铁酸化物,然后采用氢氧化钾与之反应,形成结晶,再过滤,从而得到高附加值的高铁酸钾,达到回收铁的目的。
[0026]
在本发明内,在步骤s1内,按照质量比为1:(2~5),将钕铁硼废料与添加剂混合均匀后,在600℃~1200℃的条件下焙烧2h~6h,从而得到钕铁硼焙砂;添加剂包括碳酸钠、碳酸氢钠、氢氧化钠和氧化钠中至少一种,或者添加剂包括碳酸钾、碳酸氢钾、氢氧化钾和氧化钾中至少一种,如果添加剂包括碳酸钠、碳酸氢钠、氢氧化钠和氧化钠中至少一种时,钕铁硼废料与添加剂混合均匀,再进行焙烧,得到的为铁酸钠;如果添加剂包括碳酸钾、碳酸氢钾、氢氧化钾和氧化钾中至少一种时,钕铁硼废料与添加剂混合均匀,再进行焙烧,得到的为铁酸钾,铁酸钠和铁酸钾均溶于水。在步骤s1内,添加剂不易过多也不易过少,过多的话,浪费添加剂,增加成本,如果过少的话,就不能将钕铁硼废料中的铁分离出来。
[0027]
在步骤1中,焙烧温度为600℃~1200℃,不能过低,因为低于600℃,会反应不充分,如果温度过高,会有多余杂质。
[0028]
在本发明内,在步骤s2内,按照质量与体积比为1:(3~8),将钕铁硼焙砂与水混合后,在60℃~90℃条件下浸出0.5h~4h,再过滤,从而得到浸出液和氧化稀土;氧化稀土可通过酸溶解后采用溶剂萃取法获得单一的稀土产品,或采用熔盐电解法制备单一的稀土金属,从而达到稀土的回收;采用水浸法浸出氧化稀土,浸出时间为0.5h~4h,不能低于半小时,要不然,会浸出不完全,在60℃下浸出4小时,在钕铁硼焙砂与水按质量与体积比为1:(3~8)混合情况下,可以比较好的浸出氧化稀土。
[0029]
在步骤s3内,按照三价铁与氧化剂的摩尔比为1∶(2~6),将浸出液与氧化剂混合后,在60℃~90℃条件下搅拌1h~4h,得到高铁酸钠混合液,氧化剂包括次氯酸钠、次氯酸钾和次氯酸钙中至少一种,采用强氧化剂,可以与铁酸钠反应生成高铁酸钠混合液,将浸出液与氧化剂混合,则三价铁与氧化剂的摩尔比为1∶(2~6)进行混合,才能更好地氧化反应,氧化剂过高,则过剩,如果其过低,则氧化不完全,需要在最少搅拌氧化1小时,在60℃条件下搅拌4h,可以更好地反应氧化完全。
[0030]
在步骤s4内,按照高铁酸钠混合液与氢氧化钾溶液的体积比为1:(1~2),将高铁酸钠混合液与氢氧化钾溶液混合,搅拌均匀,在0℃~5℃条件下结晶,再过滤,而后再用氢氧化钾溶液洗涤2~3次,得到高铁酸钾和沉铁后液,氢氧化钾溶液的浓度为40wt%~60wt%;具体地说,采用40wt%~60wt%浓度的氢氧化钾溶液与高铁酸钠混合液反应,其配比为按高铁酸钠混合液与氢氧化钾溶液的体积比为1:(1~2)进行,氢氧化钾溶液不易过多,否则浪费,其过少,则置换不充分;高铁酸钠混合液与氢氧化钾溶液混合,搅拌均匀在0℃~5℃条件下结晶,温度不能超过5℃,否则,结晶不了,最后用氢氧化钾溶液洗涤2~3次,可以得到高铁酸钾和沉铁后液,铁酸钾是极好的氧化剂,具有高效的消毒作用,为一种新型非氯高效消毒剂,主要用于饮水处理,化工生产中用作磺酸、亚硝酸盐、亚铁氰化物和其他无机物的氧化剂,在炼锌时用于除锰、锑和砷,烟草工业用于香烟过滤嘴等。
[0031]
本发明为了更好地进行说明及解释,举例几个实施例如下:为了避免重复,实施例中钕铁硼废料化学成分如下:nd 5~15%、ce 5~15%、pr 1~5%、gd 1~5%、dy 1~5%、sm 0.5~3%、fe 40~70%。
[0032]
实施例一:(1)按照质量比为1∶2,将钕铁硼废料与碳酸钠混合均匀,在800℃条件下焙烧6h,得到钕铁硼焙砂;(2)按照质量与体积比为1∶3,将钕铁硼焙砂与水混合,在60℃条件下搅拌4h,过滤,得到浸出液和氧化稀土;(3)按照三价铁与氧化剂的摩尔比为1∶2,将浸出液与氧化剂混合,在60℃条件下搅拌3h,得到高铁酸钠混合液;(4)按照高铁酸钠混合液与氢氧化钾溶液的体积比为1∶1,将高铁酸钠混合液与氢氧化钾溶液混合,搅拌均匀,在0℃条件下结晶,过滤,用氢氧化钾溶液洗涤3次,得到高铁酸钾和沉铁后液;氢氧化钾溶液浓度为40wt%。
[0033]
本实施例一所得结果如下:铁浸出率为98.85%,稀土浸出率为0.26%;铁总回收率为96.54%,稀土总回收率为97.42%;高铁酸钾纯度为99.23%。
[0034]
实施例二:(1)按照质量比为1∶3,将钕铁硼废料与氢氧化钠混合均匀,在900℃条件下焙烧4h,得到钕铁硼焙砂;(2)按照质量与体积比为1∶4,将钕铁硼焙砂与水混合,在90℃条件下搅拌2h,过滤,得到浸出液和氧化稀土;(3)按照三价铁与氧化剂的摩尔比为1∶3,将浸出液与氧化剂混合,在90℃条件下搅拌3.5h,得到高铁酸钠混合液;(4)按照高铁酸钠混合液与氢氧化钾溶液的体积比为1∶1.2,将高铁酸钠混合液与
氢氧化钾溶液混合,搅拌均匀,在5℃条件下结晶,过滤,用氢氧化钾溶液洗涤3次,得到高铁酸钾和沉铁后液;氢氧化钾溶液浓度为45wt%。
[0035]
本实施例二所得结果如下:铁浸出率为99.04%,稀土浸出率为0.35%;铁总回收率为97.16%,稀土总回收率为98.13%;高铁酸钾纯度为99.42%。
[0036]
实施例三:(1)按照质量比为1∶4,将钕铁硼废料与碳酸氢钠混合均匀,在1000℃条件下焙烧3h,得到钕铁硼焙砂;(2)按照质量与体积比为1∶5,将钕铁硼焙砂与水混合,在60℃条件下搅拌4h,过滤,得到浸出液和氧化稀土;(3)按照三价铁与氧化剂的摩尔比为1∶4,将浸出液与氧化剂混合,在60℃条件下搅拌4h,得到高铁酸钠混合液;(4)按照高铁酸钠混合液与氢氧化钾溶液的体积比为1∶1.5,将高铁酸钠混合液与氢氧化钾溶液混合,搅拌均匀,在0℃条件下结晶,过滤,用氢氧化钾溶液洗涤3次,得到高铁酸钾和沉铁后液;所述氢氧化钾溶液浓度为50wt%。
[0037]
本实施例三所得结果如下:铁浸出率为98.47%,稀土浸出率为0.57%;铁总回收率为96.72%,稀土总回收率为98.28%;高铁酸钾纯度为99.20%。
[0038]
实施例四:(1)按照质量比为1∶3,将钕铁硼废料与碳酸钾混合均匀,在600℃条件下焙烧4h,得到钕铁硼焙砂;(2)按照质量与体积比为1∶7,将钕铁硼焙砂与水混合,在90℃条件下搅拌2h,过滤,得到浸出液和氧化稀土;(3)按照三价铁与氧化剂的摩尔比为1∶5,将浸出液与氧化剂混合,在90℃条件下搅拌3.5h,得到高铁酸钾溶液;(4)按照高铁酸钠混合液与氢氧化钾溶液的体积比为1∶2,将高铁酸钠混合液与氢氧化钾溶液混合,搅拌均匀,在5℃条件下结晶,过滤,用氢氧化钾溶液洗涤3次,得到高铁酸钾和沉铁后液;氢氧化钾溶液浓度为55wt%。
[0039]
本实施例四所得结果如下:铁浸出率为99.06%,稀土浸出率为0.30%;铁总回收率为97.20%,稀土总回收率为98.08%;高铁酸钾纯度为99.46%。
[0040]
实施例一至四的结果对比如下:本发明具备如下优点:
1、在本发明内,采用添加剂在高温条件下与氧化铁反应生成溶于水的铁酸钠(或铁酸钾),然后采用水浸出,将溶于水的铁酸钠(或铁酸钾)溶出,而氧化稀土不溶于水,仍保留于渣中,从而实现稀土和铁的选择性分离,相对于各种强酸浸出,采用水浸出成本更低,不污染环境,具有成本低、稀土与铁分离效果好和稀土回收率高的特点。
[0041]
、本发明采用强氧化剂氧化浸出液中的铁酸钠,使之氧化为高铁酸钠(或高铁酸钾),然后采用氢氧化钾置换钠,进一步结晶,得到高附加值产品高铁酸钾,铁得到综合回收,具有资源综合利用率高的特点。
[0042]
、本发明采用钠(钾)化焙烧
‑
水浸工艺实现了钕铁硼废料稀土和铁的选择性分离,铁浸出率大于98%以上,稀土浸出率低于1%,氧化稀土可通过酸溶解后采用溶剂萃取法获得单一的稀土产品,或采用熔盐电解法制备单一的稀土金属;富铁浸出液采用氧化
‑
结晶法获得高铁酸钾,其纯度大于99%;稀土和铁的总回收率均大于96%。
[0043]
因此,本发明具有成本低、稀土和铁分离效果好、稀土和铁回收率高和资源综合利用率高的特点。
[0044]
以上所述仅为本发明的较佳实施例,并不用以限制本发明,凡在本发明的精神和原则之内所作的任何修改、等同替换和改进等,均应包含在本发明的保护范围之内。