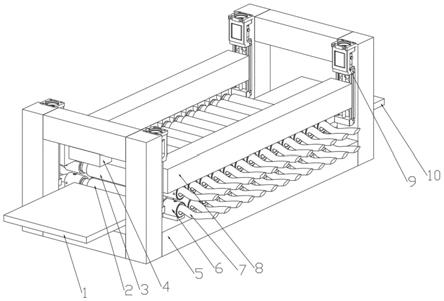
1.本发明涉及一种热处理技术领域,尤其是涉及一种辊式淬火装备。
背景技术:2.钢的淬火是将钢加热到临界点ac3或ac1以上一定温度,保温后以大于临界冷却速度的冷速冷却得到马氏体(或下贝氏体)的一种热处理工艺,通常也将铝合金、铜合金、钛合金等材料的固溶处理或带有快速冷却过程的热处理工艺称为淬火。
3.对于淬火工艺而言,为实现淬火其冷却速度必须大于临界淬火速度,而不同材料的工件临界淬火速度不同,为此必须选择适当的淬火温度和冷却速度。此外,工件在淬火热处理过程中,由于工件内外温差产生热胀冷缩以及相变还会引起淬火应力,甚至引起变形或开裂。所以合理选择淬火冷却介质就尤为重要,常见的淬火介质有水、盐或碱水溶液及各种矿物油等,上述的几种淬火冷却介质各有优缺点,但均不属于理想的冷却介质。水的冷却能力很大,但冷却特性不好,油的冷却特性较好,但其冷却能力又较低,并且油温过高还易着火。同时一些带状工件,在淬火时还要设置固定夹具,以防止淬火变形。在现有技术中,实现工件的淬火,所用的冷却介质成本高、污染大、工作环境对人员具有一定危害性。
技术实现要素:4.为解决现有技术中的淬火耗水量巨大、淬火后瓢曲难矫正且冷却不均导致残余应力不均匀分布而产生的冷加工变形等问题,本发明提供了一种可连续均匀冷却、工作效率高、节能环保的辊式淬火设备。
5.为达到上述目的,本发明的技术方案是:
6.本发明提供一种辊式淬火设备,包括辊道冷却系统、实时检测系统、框架调节系统、第二类冷却介质循环系统,其特征在于所述的辊道冷却系统设置有上下对称布置的冷却辊,上辊道设置在可移动的上机架上,下辊道设置在固定的下机架上。
7.根据上述的一种辊式淬火设备,其特征在于所述的冷却辊采用导热性80w/(m
·
k)以上的金属制造,包括了导热性良好的铜及铜合金,铝及铝合金,银及银合金,所述的上述材料可采用涂层处理以提高导热系数。冷却辊可以是实心的或空心的,采用空心时内部可以采用或不采用水冷处理,采用水冷处理主要目的在于提高金属制品冷却介质对热处理工件的冷却能力以及具有较好的结构强度。内部为空心时,辊筒的两侧设有通孔,第二类冷却介质从一侧的通孔进入辊体内部与辊体进行热交换,随后通过另一侧通孔流出辊体,进一步的所述冷却辊可设置单个或多个工作辊及支撑辊,辊道的排列数量根据工艺要求确定。
8.根据上述的一种辊式淬火设备,其特征在于每根冷却辊配备一套传动系统,该传动系统包括传动齿轮、伺服电机、编码器,驱动电机采用pwm控制,编码器实时反馈实际辊速通过闭环控制精确控制辊速,冷却辊道旋转方向可以根据实际需要迅速调整为正转或反转,辊速调节范围为1r/min
‑
1000r/min。
9.根据上述的一种辊式淬火设备,其特征在于所述的实时监测系统,包括温度及厚
度监测传感器、红外接近传感器等,在进入冷却辊道的上方安装有温度以及厚度监测传感器以获得淬火工件的状态信息,满足设定的淬火要求时才可进入冷却辊道系统,在冷却过程中也实时监测工件的位置、温度等信息,当冷却到指定温度后才可以被冷却辊输送至出料口。
10.根据上述的一种辊式淬火设备,其特征在于所述的框架调节系统包括移动机架、单轴驱动器,所述的移动机架通过单轴驱动器内的电机的正反转带动滚珠丝杠的旋转从而实现上下移动,冷却过程中可根据检测到的工件的温度、厚度等信息调整移动机架的下压量,以得到合适的压力角,移动框架的速度在0.1mm/s
‑
2mm/s减调节,移动范围在0
‑
20mm。
11.根据上述的一种辊式淬火设备,其特征在于所述的第二类冷却介质循环系统包括旋转滑环、循环管道、循环池、泵机、流量计、分流阀、调节阀。旋转滑环一端与冷却辊一侧的通孔连接,另一端则与循环管道连接,实现冷却辊旋转而循环管道固定且第二类冷却介质在冷却辊内稳定流动,每根循环管道都配有流量计和调节阀和泵机连接后可以实现冷却介质流量实时控制,所述的第二类冷却介质可以是水、碱水、盐水、淬火油和气体等,第二类冷却介质的流量可以在0.1l/s~2000l/s间调节。
12.与现有技术相比,本发明的有益效果在于:(1)易于控制终冷温度。传统水淬、油淬等方式难以控制终冷温度,而辊淬只需要调整工作辊与工件的压力角与冷却介质流量即可很容易地控制终冷温度。(2)冷速快,可连续冷却。辊式淬火设备地综合换热系数可达到1500
‑
2000kcal/m2.h.℃,对于带状工件冷速可达到100
‑
400℃/s,可满足大多数工件淬火的工艺要求。(3)工件板型及表面质量好。辊淬过程中通过连续稳定的快速冷却,使工件各部分均匀冷却,可抑制淬火变形的发生。
附图说明
13.图1为本设备立体图
14.图2为本设备侧视图
具体实施方式
15.参见图1和图2,本发明一种辊式淬火装备包括辊道冷却系统、框架调节系统和第二类冷却介质循环系统。辊道冷却系统的冷却辊沿机架上下对称布置,辊道冷却系统前后分别设置了入料板1和出料板10,下辊道2固定在固定机架5上,上辊道3固定在移动机架8上,固定机架5上设置有温度及厚度检测传感器4,固定机架5的下方设置有红外接近传感器(未示出),以检测辊道内工件位置。框架调节系统包括移动机架8、单轴驱动器9、滚珠丝,移动机架8与单轴驱动器9连接,当传感器4获取工件信息后自动调整移动机架8高度以适应不同厚度的工件,移动机架通过减速电机的正反转带动滚珠丝杠的旋转从而实现上下移动,移动机架的速度在0.1mm/s
‑
2mm/s减调节,移动范围在0
‑
20mm。第二类冷却介质循环系统包括旋转滑环6、循环管道7、循环池(未示出)、泵机(未示出)、流量计(未示出)、分流阀(未示出)、调节阀(未示出)。冷却辊2、3与循环管道7相连接,实时监测冷却介质流量。旋转滑环6一端与冷却辊一侧的通孔连接,另一端则与循环管道7连接,每根循环管道7都配有1台流量计、1台调节阀、1台泵机、1台分流阀和1台调节阀,连接后可以实现冷却介质流量实时控制。并且每根循环管道7配备一套传动系统,包括伺服电机(未示出)、编码器,驱动电机采用pwm
控制,编码器反馈实际辊速,辊速通过闭关控制精确控制辊速,辊速调节范围为1r/min
‑
1000r/min。
16.在本发明的一个实施例中,辊淬装置实现工件的淬火效果包括以下步骤:
17.如图1、2所示,铝板出热处理炉前,开启辊淬装置总电源,系统开始自检,待系统自检通过后,视工件的厚度以及淬火热处理的要求通过控制移动机架8调整上冷却辊3和下冷却辊2的距离,为提升淬火效果可适当增加冷却辊和工件之间的压力角,以减小淬火变形。接下来开启第二类冷却介质输送泵使第二类冷却介质进入冷却辊,与此同时开启冷却辊旋转功能并稳定地循环3~5min,使辊道温度和第二类冷却介质达到一致。再将加热至指定温度的工件放置于进料板1上,使工件可以平直通过淬火辊道进行淬火,在进入淬火辊道前,位于进料口上方的温度及厚度传感器会连续检测工件的表面温度及厚度,将温度数据传送至主控中心,与数据库类的模型进行对比并根据相应算法适当调整淬火辊的转速以及第二类冷却介质的流量。当工件满足设定的淬火要求时,方可进入冷却辊道,在冷却过程中工件冷却至最后一根冷却辊时仍未达到要求的冷却温度,则冷却辊开启反转模式,将工件在辊道内反复冷却直至到达指定温度。冷却结束后,冷却辊将工件输送至出料板10。
18.综上所述,本发明的装置和方法能够有效、快速地对工件进行淬火(固溶)热处理,并能根据不同材质、形状的工件进行淬火工艺参数的调整,所用时间短、周期快,适合工厂的快速生产。并且利用金属介质进行淬火的工艺相较于传统淬火工艺其能耗低、污染小、工作环境好。