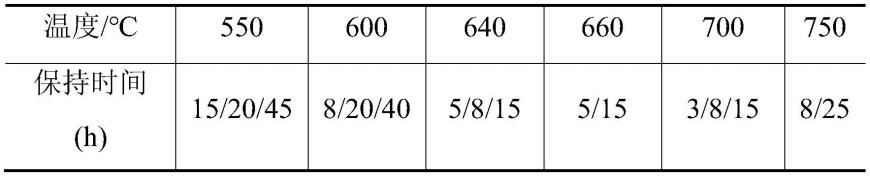
一种cr5型锻钢轧辊锻后重结晶方法
技术领域
1.本发明涉及锻后重结晶技术领域,尤其涉及一种cr5型锻钢轧辊锻后重结晶方法。
背景技术:2.轧辊作为轧钢设备的重要工具及消耗件,每年消耗量大,其中cr5型锻钢轧辊以其优越的耐磨性和抗断裂性,成为带钢轧机轧辊的主流产品。
3.目前cr5型锻钢轧辊的锻后重结晶工序仍沿用传统工艺方式,包括:待料保温、过冷保温、中温保持、限速升温、高温保温等过程。
4.然而传统工艺方式的锻后热处理周期长达15-20天,设备占用时间长,导致cr5型锻钢轧辊的生产效率比较低。
技术实现要素:5.鉴于上述的分析,本发明旨在提出一种cr5型锻钢轧辊锻后重结晶方法,以提高cr5型锻钢轧辊的生产效率。
6.本发明的目的主要是通过以下技术方案实现的:
7.第一方面,本发明实施例提供了一种cr5型锻钢轧辊锻后重结晶方法,包括:
8.步骤1、在640-660℃下,对轧辊进行待料和/或保温,时间为10h-25h;
9.步骤2、对经所述步骤1处理过的轧辊进行高温保温,保温温度为900-950℃,保温时间为15h-40h。
10.进一步地,以不大于50℃/h的速度,升温至900-950℃。
11.进一步地,分别确定所述轧辊表面的第一组织转变温度和所述轧辊心部的第二组织转变温度;其中,所述轧辊心部为轧辊中心区域;
12.根据所述第一组织转变温度和所述第二组织转变温度,确定所述轧辊的待料温度和/或保温温度;所述第一组织转变温度指轧辊表层锻态下粗大奥氏体转变最佳温度;所述第二组织转变温度指轧辊心部锻态下粗大奥氏体转变最佳温度;
13.根据所述轧辊的直径,确定所述轧辊的待料时间和/或保温时间。
14.进一步地,所述轧辊的直径为1000mm-1700mm,所述轧辊的保温时间随轧辊直径的增加而递增。
15.进一步地,在预设温度下,对所述轧辊进行晶粒粗化;
16.对晶粒粗化后的轧辊进行还原试验;
17.针对不同预设温度下的所述轧辊表面做金相检测;
18.根据所述金相检测的结果,确定重结晶前粗大奥氏体完全转变为珠光体组织的轧辊对应的温度为所述第一组织转变温度。
19.进一步地,所述第一组织转变温度为640℃-700℃,组织转变时间为3h-8h。
20.进一步地,所述金相检测的结果为奥氏体转变量。
21.进一步地,选取代表整个工件的轧辊表面为研究对象,确定晶粒粗化最严重的工
艺条件为轧辊材料晶粒粗化工艺参数,在确定的轧辊材料晶粒粗化工艺条件下,对晶粒粗化后的轧辊进行还原试验。
22.进一步地,在预设温度下,对所述轧辊进行晶粒粗化;
23.根据所述预设温度,对所述轧辊进行热处理数值模拟;
24.根据所述热处理数值模拟的结果,对晶粒粗化后的轧辊进行还原模拟试验;
25.针对不同冷却温度下的所述轧辊心部做金相检测;
26.根据所述金相检测的结果,确定重结晶前粗大奥氏体完全转变为珠光体组织的轧辊对应的温度为所述第二组织转变温度。
27.进一步地,所述第二组织转变温度为700℃,组织转变时间不小于25h。
28.与现有技术相比,本发明至少能实现以下技术效果之一:
29.1.削减了传统工艺中的过冷保温过程和中温保持过程,极大的消减了轧辊锻后重结晶的时间。传统重结晶工艺中高温保温前用时为70-115h,本技术工艺中重结晶工艺中高温保温前用时为16-31h。与传统工艺相比,本发明的高温保温前用时缩短了70%以上。
30.2.在确定轧辊的待料温度、保温温度和保温时间时,通过晶粒粗化模拟极端的工艺条件,并在极端的工艺条件下,对轧辊进行组织转变,从而确定该工艺条件下的轧辊表面的组织转变温度(第一组织转变温度)以及轧辊心部的组织转变温度(第二组织转变温度)。最后根据轧辊表面的组织转变温度以及轧辊心部的组织转变温度,确定待料温度、保温温度和保温时间,从而保证在实际工艺中轧辊表面和心部的奥氏体全部转化成珠光体。由于本发明的待料温度、保温温度和保温时间适用于极端的工艺条件,也适用于其他工艺条件,因此本发明具有良好的适用性。
31.3.在锻后重结晶阶段,不同直径的轧辊对应的轧辊心部温度和轧辊表面温度均不同。在本发明中根据轧辊直径的大小及组织转变温度,确定保温时间,以适用实际的工艺场景,从而提高了方法的适用性。
32.4.锻后重结晶需要分批次处理,在处理当前批次的时候,剩余的所有批次均处于待料状态。由于本发明的热处理只有两步,因此可以实现让轧辊在待料状态就开始进行步骤1,并维持待料时间和保温时间之和为10h-25h,以兼顾节省工艺时间和保证热处理效果,从而提高工艺效率。
33.本发明的其他特征和优点将在随后的说明书中阐述,并且,部分的从说明书中变得显而易见,或者通过实施本发明而了解。本发明的目的和其他优点可通过在所写的说明书以及附图中所特别指出的结构来实现和获得。
附图说明
34.附图仅用于示出具体实施例的目的,而并不认为是对本发明的限制,在整个附图中,相同的参考符号表示相同的部件。
35.图1为cr5锻钢轧辊的传统锻后重结晶高温加热段曲线图;
36.图2为cr5锻钢轧辊材料晶粒粗化试验曲线图;
37.图3为cr5锻钢轧辊材料晶粒粗化图;
38.图4为本发明实施例提供的轧辊辊身表层锻态还原模拟试验曲线;
39.图5a为本发明实施例提供的轧辊辊身表层在550℃,保温45h的金相组织图;
25h,轧辊的心部和表层中的奥氏体全部转化成珠光体,没有奥氏体残留的组织结构,因而不需要传统工艺的中温保持过程和过冷保温过程。
66.在本发明实施例中,在重结晶的高温保温阶段前只需一个温度范围内的待料和/或保温,统称为保温阶段。
67.在640℃-660℃下的待料和/或保温的时间满足10-25小时即可。因此,在多批次生产时,处于待料状态的轧辊,其待料温度也控制在640℃-660℃,使得锻后轧辊中的奥氏体在待料阶段就开始转化成珠光体。如此,将传统工艺中部分待料过程合并到保温过程中,在640℃-660℃下的待料和保温总时长需要10-25小时,相比传统工艺的待料保温+过冷保温+中温保持的时长为70-115小时,重结晶的工艺时间缩短了54-84小时。
68.当批次足够多时,待料时间已达上述步骤1中时长的轧辊可直接进行重结晶;待料时间尚未达上述步骤1中时长的轧辊,保温的时间为10-25小时扣除待料时间。
69.步骤2、对经所述步骤1处理过的轧辊进行高温保温。
70.在本发明实施例中,以不大于50℃/h的速度,升温至900-950℃;在900-950℃下,保温15h-40h。
71.与现有技术相比,本发明实施例提供的技术方案通过削减过冷保温过程和中温保持过程,减少轧辊经历的温度变化次数,能够保证在得到没有奥氏体残留组织结构的前提下,减小心部应力;能够保证重结晶后,无论轧辊表层和轧辊心部,晶粒细化明显,晶粒度由0级细化为7.0-8.0级。具体效果参见图8和图9,其中图8对应轧辊心部的晶粒细化情况,图9对应于轧辊表层的晶粒细化情况。
72.在上述步骤1中,确定640℃-660℃下的待料和/或保温的温度和时间的方法包括如下步骤:
73.步骤s1、分别确定轧辊表面的第一组织转变温度和轧辊心部的第二组织转变温度;
74.其中,第一组织转变温度指轧辊表层锻态下粗大奥氏体转变最佳温度;第二组织转变温度指轧辊心部锻态下粗大奥氏体转变最佳温度;
75.定义轧辊的中心区域为轧辊心部;
76.步骤s2、根据第一组织转变温度和第二组织转变温度,确定轧辊的待料温度和/或保温温度;
77.其中待料温度与保温温度相同。
78.步骤s3、根据轧辊的直径、第一组织转变温度和第二组织转变温度,确定轧辊的待料时间和/或保温时间。
79.步骤s1中,取中心区域的直径为轧辊直径的1/2,即轧辊心部为轧辊内部与轧辊同轴且直径为轧辊一半的立体柱状区域。
80.在确定第一组织转变温度和第二组织转变温度时,在预设温度下,对轧辊进行晶粒粗化,并尽可能地提升轧辊的粗化程度,以便于在极端工艺条件下确定第一组织转变温度和第二组织转变温度,以提高方法的适用性。在晶粒粗化后,分别针对轧辊表层和轧辊心部做还原试验,并针对不同冷却温度下的轧辊心部做金相检测,确定第一组织转变温度和第二组织转变温度。
81.步骤s1具体过程包括:
82.s11.轧辊材料晶粒粗化
83.以辊身直径1700mm的轧辊工件为例,选取可代表整个工件的轧辊表面、有效截面最大的轧辊心部为研究对象,确定晶粒粗化最严重的工艺条件为轧辊材料晶粒粗化工艺参数,过程包括:
84.步骤1):试样放入模拟炉内,炉温经1-2h升温至1000℃。
85.步骤2):炉温快速升至材料晶粒粗化温度。
86.轧辊材料晶粒粗化试验曲线如图2所示。
87.在本发明实施例中,选择3组晶粒粗化温度作为研究对象,3组晶粒粗化温度分别是1100℃、1200℃、1250℃,每组升温时间为0.5-1h。
88.步骤3):分别在1100℃、1200℃、1250℃温度下,对上述3组进行保温,保持时间0.5-3h不等,得到材料不同晶粒粗化级别,再现锻造时存在无变形量部位的显微状态。
89.步骤4):根据晶粒粗化级别,确定轧辊材料晶粒粗化工艺参数。
90.在本发明实施例中,金相检测结果显示料晶粒粗化温度为1250℃-1.5h的试样的晶粒粗化级别最小,即晶粒粗化最严重,见图3。因此,后续试验以晶粒粗化条件为1250℃-1.5h的试样为研究对象。需要说明的是,轧辊材料晶粒粗化只是为后续的还原试验准备试验条件,为还原试验提供最极端的工艺条件,即在极端的条件下进行还原试验。
91.s12.确定轧辊表层锻态下粗大奥氏体转变最佳温度(第一组织转变温度);
92.在确定的轧辊材料晶粒粗化工艺条件下,观察检测不同温度条件下的轧辊表层的组织转变,判定该温度段内的奥氏体转变量情况,确定奥氏体完成转变成全珠光体的温度确定为轧辊表层锻态下粗大奥氏体转变最佳温度(第一组织转变温度)。
93.具体的,轧辊辊身表层锻态还原试验曲线如图4所示,过程包括:
94.步骤1:试样放入模拟炉内,炉温经2h升温至1000℃。
95.步骤2:炉温快速升至材料晶粒粗化温度1250℃。
96.步骤3:在1250℃温度下保持1.5h。
97.步骤4:结合实际生产情况,设定降温时间为3-5h,降至500℃-550℃,观察该阶段的组织转变情况。
98.步骤5:炉温分别升至550℃、600℃、640℃、660℃、700℃、750℃,用时0.5-2h。
99.在本发明实施例中,选择6组保温温度。
100.步骤6:550℃-750℃保温,保持时间3-50h不等,观察检测该工艺段内的组织转变,判定该温度段内的奥氏体转变量情况。
101.在本发明实施例中,为了获取最优的保温温度和保持时间,针对每一组保温温度,设置了多个保持时间。保温温度和保持时间的对应关系,如表1所示:
102.表1 轧辊辊身表层保温温度和保持时间的对应关系
[0103][0104]
步骤7:对各条件下的轧辊进行空冷,检测空冷后的试样显微组织组成。
[0105]
在本发明实施例中,图4中
①
~
⑥
段内温度均为“非马氏体”转变区间,马氏体量为图4中第
⑥
段结束时的残留奥氏体。
[0106]
试验检测结果如图5a-5e所示,图5a、5b、5c中马氏体组织即为图4第
⑥
段结束时的残留奥氏体;图5d、5e组织为全珠光体,说明在700℃-3h、640℃-8h条件下奥氏体完成转变。
[0107]
由此可知,轧辊辊身表层位置,锻态下粗大奥氏体转变最佳温度640℃-700℃,转变时间≥3h;即确定第一组织转变温度为640℃-700℃,转变时间≥3h。
[0108]
s13.确定轧辊心部锻态下粗大奥氏体转变最佳温度(第二组织转变温度);
[0109]
观察检测不同温度条件下的轧辊心部组织转变,判定该温度段内的奥氏体转变量情况,确定奥氏体完成转变成全珠光体的温度确定为轧辊心部锻态下粗大奥氏体转变最佳温度(第二组织转变温度);
[0110]
具体的,结合实际生产条件,对辊身直径为的轧辊锻造完成后在650℃保温的过程进行热处理数值模拟,结果见图6a。具体地,在abaqus中设置轧辊模型和模拟热处理参数,其中模型辊身直径为φ1700mm的轧辊初始温度1200℃,常温25℃下空冷3小时(即锻造时间),然后在炉温650℃的加热炉中保温40h。之后利用轧辊模型和模拟热处理参数,对轧辊进行温度场数值模拟,得到图6a。
[0111]
结合数值模拟结果,细化温度梯度,制定符合实际生产工艺的试验曲线,心部锻态还原试验曲线见图6b。
[0112]
步骤1:试样放入模拟炉内,炉温经2h升温至1000℃。
[0113]
步骤2:炉温快速升至材料晶粒粗化温度1250℃。
[0114]
步骤3:在1250℃温度下保持1.5h。
[0115]
步骤4:参考数值模拟结果,设定降温时间为5-12h,降至900℃。
[0116]
步骤5:炉温降至780℃,用时6-10h。
[0117]
步骤6:炉温降至750℃,用时2-6h。
[0118]
步骤7:炉温降至720℃,用时2-6h,试样已处于珠光体转变温度区间,进行显微组织观察。
[0119]
步骤8:炉温降至700℃,用时2-6h,进行显微组织观察。
[0120]
步骤9:炉温降至680℃,用时4-8h,进行显微组织观察。
[0121]
在本发明实施例中,步骤7-9均需将待检测试样均应快速冷却至室温(空冷),再观察显微组织,以辨别心部奥氏体转变是否完成。
[0122]
试验检测结果如图7a和图7b所示,可以看出,心部缓慢冷至720℃时,仍存在大量的奥氏体;冷至700℃时,心部位置处奥氏体完成转变。
[0123]
完成上述过程后,确定轧辊表面锻态下粗大奥氏体转变最佳温度(第一组织转变温度)640℃-700℃,转变时间≥3h。对于轧辊心部,锻态下试样冷至720℃时仍存在大量粗大奥氏体,待心部冷至700℃时奥氏体转变完成,且在缓慢冷却过程中未出现魏氏体组织。因此轧辊心部为的第二组织转变温度为700℃。
[0124]
上述温度均为轧辊的温度,而实际工艺中均采用炉温。基于步骤s1的结果,将轧辊的温度转化为炉温,从而确定待料及入炉温度为640℃-660℃。入炉温度为640℃-660℃时,轧辊表面返温至700℃(见图6a),如此既能保证轧辊表面的奥氏体快速转变,又能保证轧辊心部的奥氏体快速转变。因此本发明可以省去冷保温过程和中温保持过程,从而缩短工艺
时间。
[0125]
之后根据轧辊直径,对保温时间进行调整,确保轧辊心部完成组织转变,并保证保温时间和待料时间之和在10h-25h。如轧辊保温时间≥25h,辊身心部温度达695℃,心部奥氏体转变完全。具体参见表2:
[0126]
表2 轧辊直径和保温时间的对应关系
[0127][0128][0129]
为了说明上述实施例的可行性,本发明给出下述实施例:
[0130]
需要说明的是,下述实施例针对带钢轧机上的支承辊,支承辊材质为cr5锻钢,其主要化学成分如表3所示:
[0131]
表3 轧辊的化学成分
[0132][0133]
实施例1
[0134]
本发明的生产转化应用于某钢厂热轧支承辊,支承辊锻件直径与其它5支同规格支承辊同炉进行锻后重结晶,采用取消过冷保温的工艺,各步骤如下所述:
[0135]
步骤1:640-660℃待料,待料时间最少的一支为20h。
[0136]
步骤2:640-660℃保温,保温时间大于5h,保证工件完成重结晶前的组织转变。
[0137]
步骤3:40℃/h的速度升温至900-950℃。
[0138]
步骤4:900-950℃保温,保温时间>30h。
[0139]
步骤5:待完成锻后重结晶工艺后,对每支支承辊进行超声波探伤检测,并对辊颈心部取样检测,考察重结晶效果。
[0140]
结果表明,试制的6支规格的支承辊探伤均无草状波情况,在辊颈心部取料检测晶粒度为7.5-8.0级如图8所示,属细晶粒范畴,重结晶效果好。
[0141]
实施例2
[0142]
本发明的生产转化应用于某钢厂冷轧支承辊,支承辊锻件辊身直径1000mm。与其它9支支承辊同炉进行锻后重结晶,采用取消过冷保温的工艺,各步骤如下所述:
[0143]
步骤1:640-660℃待料,待料时间最短的一支为10h。
[0144]
步骤2:640-660℃保温,保温时间大于2h,心部可达到700℃,工件整体可完成重结
晶前的组织转变。
[0145]
步骤3:50℃/h的速度升温至900-950℃。
[0146]
步骤4:900-950℃保温,保温时间大于8h。
[0147]
步骤5:待完成锻后重结晶工艺后,对每支支承辊进行探伤检测,并对辊身表层取环检测,考察重结晶效果。
[0148]
结果表明,试制的10支辊身直径规格的支承辊探伤均无草状波情况,在辊身表层取料检测晶粒度为8.0-8.5级,如图9所示,属细晶粒范畴,重结晶效果好。
[0149]
实施例1和实施例2的热处理高温加热段曲线如图10所示,与传统技术的热处理高温加热段曲线(图1)相比,图10的
①‑④
对应于图1的
①
、
②
、
⑦
、
⑧
。因此,仅削减过冷保温过程(图1中的
③
、
④
)和中温保温(图1中的
⑤
、
⑥
)过程就减少了55-90个小时。传统工艺中待料时间通常为几天,而再执行工艺时由于过冷保温过程和中温保温过程的存在,无法未对待料时间进行合理利用;本发明在重结晶前只有一步保温过程,因此让待料温度与保温温度保持一致,就可以充分利用待料段,从而进一步缩短了工艺时间。
[0150]
以上所述,仅为本发明较佳的具体实施方式,但本发明的保护范围并不局限于此,任何熟悉本技术领域的技术人员在本发明揭露的技术范围内,可轻易想到的变化或替换,都应涵盖在本发明的保护范围之内。