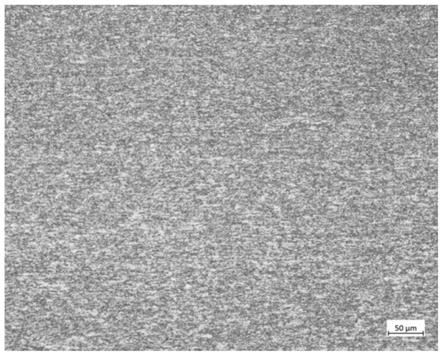
1.本发明涉及连续油管用钢技术领域,更具体地说是一种低屈强比超高强度连续油管用钢及其制造方法。
背景技术:2.连续油管具有效率高、成本低、作业范围广、占地面积小等一系列优点和作业优势,在油气田勘探、开发、作业、增产中发挥着越来越重要的作用。随着油气勘探开发难度的日益增加和油田降低作业成本的需要,连续油管作业已经在全球得到了推广和应用,特别是在发达国家和地区连续油管已经成为油田作业必不可少的装备。同时随着连续油管的发展和页岩气开发工况逐步恶化,使得连续油管综合性能在不断提高,并向超高强度方向发展。
3.随着连续油管向超高强度方向发展,制管企业现有的机组设备的成型能力有限,生产超高强度钢管达到机组成型能力的极限,且对机组设备损耗较大,对制管企业的机组能力是严峻的考验。制管企业要求钢管原料的屈服强度要低,保证在机组设备成形能力范围之内,且在制成钢管后,钢管经过热处理其屈服强度达到超高强度钢管的要求。所以要求超高强度连续油管用钢具有较高的强度和较低的屈强比。
4.经检索,关于解决上述问题,目前已有相关专利公开。如,中国专利申请号为:201711324677.0、申请日为:2017年12月13日、授权公告日为:2019年3月8日,公开了一种ct110级连续管用热轧钢带,其化学成分及重量百分比为:c:0.11~0.15%、si:0.10~0.30%、mn:0.90~1.30%、p:≤0.015%、s:≤0.0020%、cu:0.25~0.40%、ni:0.15~0.35%、cr:0.60~1.00%、nb:0.020~0.050%、v:≤0.010%、ti:0.010~0.030%、n:≤0.0050%、al:0.015~0.060%、mo:0.10~0.30%。该专利的组织类型为粒状贝氏体,屈强比在0.81~0.88,抗拉强度在851~853mpa。
5.又如中国专利申请号为:201410200087.7、申请日为:2014年5月13日、授权公告日为2017年1月18日,公开了一种屈服强度690mpa级低屈强比钢板及其制备方法,其化学成分及重量百分比为:c:0.04~0.10%、si:0.20~0.40%、mn:1.40~1.90%、p≤0.020%、s≤0.008%、nb:0.03~0.06%、ti:0.008~0.025%、cr:0.10~0.40%、ni:0~0.20%、mo:0~0.25%、als:0.015~0.050%,该专利的屈强比在0.79~0.83,抗拉强度在875~900mpa。
6.综上,上述两专利的屈强比均大于0.7,且强度级别较低,因此需要设计出具有较高的强度和较低的屈强比的超高强度连续油管用钢。
技术实现要素:7.1.发明要解决的技术问题
8.针对现有技术中要求超高强度连续油管用钢需具有较高的强度和较低的屈强比,本发明提出一种低屈强比超高强度连续油管用钢及其制造方法,其化学成分及重量百分比含量为c:0.10~0.15%、si:0.30~0.40%、mn:1.5~2.0%、p≤0.015%、s≤0.002%、cr:
0.50~0.70%、mo:0.20~0.50%、nb:0.050~0.070%、v:0.050~0.080%、ti:0.010~0.020%、ni+cu≤0.70%、als:0.020~0.040%,其余为fe及不可避免的夹杂。通过对形变和温度以及冷却速度控制,以生产出具有均匀细小的f+m双相组织的低屈强比的超高强度连续油管用钢,该连续油管用钢的厚度范围为3.0~5.0mm,用于制造140ksi级别的超高强连续油管。
9.2.技术方案
10.为达到上述目的,本发明提供的技术方案为:
11.一种低屈强比超高强度连续油管用钢,其化学成分及重量百分比含量为c:0.10~0.15%、si:0.30~0.40%、mn:1.5~2.0%、p≤0.015%、s≤0.002%、cr:0.50~0.70%、mo:0.20~0.50%、nb:0.050~0.070%、v:0.050~0.080%、ti:0.010~0.020%、ni+cu≤0.70%、als:0.020~0.040%,其余为fe及不可避免的夹杂;所述连续油管用钢厚度范围为3.0~5.0mm;其显微组织为铁素体+马氏体,其中铁素体体积分数为62.7~67.6%,马氏体体积分数为32.4~37.3%,该连续油管用钢的厚度范围为3.0~5.0mm,以用于制造140ksi级别的超高强连续油管。
12.一种低屈强比超高强度连续油管用钢的制造方法,采用传统热连轧板带工艺生产,包括如下步骤:铁水预处理
→
转炉冶炼
→
炉外精炼
→
连铸
→
板坯清理
→
板坯加热
→
控制轧制
→
控制冷却
→
卷取,通过各步骤对形变和温度以及冷却速度控制,形成均匀细小的f+m双相组织,实现低屈强比超高强度连续油管用钢控制,该钢的力学性能:rt0.5:700~762mpa,rm:1100~1141mpa,a50:10%~16%,屈强比:0.63~0.68;冷弯性能180
°
,d=4a合格,具有较高的强度、较低的屈强比、较好的成形性能。
13.进一步的技术方案,冶炼过程采用洁净钢冶炼技术,经过rh炉、lf炉处理和进行钙处理,以控制非金属夹杂物形态数量、形态和尺寸,减少非金属夹杂物的形成。
14.进一步的技术方案,连铸过程中投用动态轻压下和电磁制动,以减少铸坯内部缺陷,提高材料的塑韧性。
15.进一步的技术方案,板坯切割完成后对板坯表面进行检查和清理,避免热轧过程中带钢产生边部缺陷。
16.进一步的技术方案,板坯入加热炉进行加热,其均热温度控制在1230~1270℃,以促进奥氏体均匀化和合金元素在奥氏体中充分固溶,同时避免奥氏体晶粒过分粗化。
17.进一步的技术方案,板坯出炉经过高压水除鳞去除表面氧化铁皮后进行轧制,轧制分为粗轧和精轧两个阶段。粗轧阶段在奥氏体再结晶区进行多道次轧制,轧制温度控制在1000~1060℃,粗轧累计压下率≥82%,促进形变奥氏体晶粒进行多次回复再结晶细化,粗轧后板坯厚度控制在39~45mm。精轧开轧温度控制在1000℃左右,通过累计大变形增加形变奥氏体内的形变带和位错密度,从而增加相变形核点细化晶粒尺寸,精轧累计压下率≥89%。精轧终轧温度控制在840~880℃,避免在低温双相区轧制导致轧机负荷过大,同时避免造成混晶,也要避免终轧温度过高导致奥氏体晶粒粗化。
18.进一步的技术方案,精轧结束后进行前段层流冷却,冷却速度控制在30~40℃/s,控制冷却后的钢板卷取温度在400~500℃。
19.3.有益效果
20.采用本发明提供的技术方案,与现有技术相比,具有如下有益效果:
21.(1)本发明的一种低屈强比超高强度连续油管用钢及其制造方法,其化学成分及重量百分比含量为c:0.10~0.15%、si:0.30~0.40%、mn:1.5~2.0%、p≤0.015%、s≤0.002%、cr:0.50~0.70%、mo:0.20~0.50%、nb:0.050~0.070%、v:0.050~0.080%、ti:0.010~0.020%、ni+cu≤0.70%、als:0.020~0.040%,其余为fe及不可避免的夹杂;所述连续油管用钢厚度范围为3.0~5.0mm;其显微组织为铁素体+马氏体,其中铁素体体积分数为62.7~67.6%,马氏体体积分数为32.4~37.3%,该连续油管用钢的厚度范围为3.0~5.0mm,以用于制造140ksi级别的超高强连续油管;
22.(2)本发明的一种低屈强比超高强度连续油管用钢及其制造方法,按照上述化学成分进行钢水冶炼,并进行铁水预处理
→
转炉冶炼
→
炉外精炼
→
连铸
→
板坯清理
→
板坯加热
→
控制轧制
→
控制冷却
→
卷取,通过各步骤对形变和温度以及冷却速度控制,进而形成均匀细小的f+m双相组织,实现低屈强比钢控制;
23.(3)本发明的一种低屈强比超高强度连续油管用钢及其制造方法,采用洁净钢冶炼技术,经过rh炉、lf炉处理和进行钙处理提高钢水纯净度,控制非金属夹杂物形态数量、形态和尺寸,减少非金属夹杂物的形成;
24.(4)本发明的一种低屈强比超高强度连续油管用钢及其制造方法,连铸过程中投用动态轻压下和电磁制动,减少铸坯内部缺陷,提高材料的塑韧性;
25.(5)本发明的一种低屈强比超高强度连续油管用钢及其制造方法,板坯切割完成后对板坯表面进行检查和清理,避免热轧过程中带钢产生边部缺陷;
26.(6)本发明的一种低屈强比超高强度连续油管用钢及其制造方法,板坯首先入加热炉进行加热,均热温度控制在1230~1270℃,促进奥氏体均匀化和合金元素在奥氏体中充分固溶,同时避免奥氏体晶粒过分粗化;
27.(7)本发明的一种低屈强比超高强度连续油管用钢及其制造方法,板坯出炉经过高压水除鳞去除表面氧化铁皮后进行轧制,轧制分为粗轧和精轧两个阶段。粗轧阶段在奥氏体再结晶区进行多道次轧制,轧制温度控制在1000~1060℃,粗轧累计压下率≥82%,促进形变奥氏体晶粒进行多次回复再结晶细化,粗轧后板坯厚度控制在39~45mm。精轧开轧温度控制在1000℃左右,通过累计大变形增加形变奥氏体内的形变带和位错密度,从而增加相变形核点细化晶粒尺寸,精轧累计压下率≥89%。精轧终轧温度控制在840~880℃,避免在低温双相区轧制导致轧机负荷过大,同时避免造成混晶,也要避免终轧温度过高导致奥氏体晶粒粗化;
28.(8)本发明的一种低屈强比超高强度连续油管用钢及其制造方法,精轧结束后进行前段层流冷却,冷却速度控制在30~40℃/s,控制冷却后的钢板卷取温度在400~500℃。
附图说明
29.图1为本发明的显微组织图。
具体实施方式
30.为进一步了解本发明的内容,结合附图对发明作详细描述。
31.实施例1
32.本实施例的一种低屈强比超高强度连续油管用钢,其化学成分及重量百分比含量
为c:0.10~0.15%、si:0.30~0.40%、mn:1.5~2.0%、p≤0.015%、s≤0.002%、cr:0.50~0.70%、mo:0.20~0.50%、nb:0.050~0.070%、v:0.050~0.080%、ti:0.010~0.020%、ni+cu≤0.70%、als:0.020~0.040%,其余为fe及不可避免的夹杂;所述连续油管用钢厚度范围为3.0~5.0mm;其显微组织为铁素体+马氏体,其中铁素体体积分数为62.7~67.6%,马氏体体积分数为32.4~37.3%,该连续油管用钢的厚度范围为3.0~5.0mm,以用于制造140ksi级别的超高强连续油管。图1所示为本发明的连续油管用钢在光学显微镜下的显微组织形貌,可见显微组织为铁素体+马氏体,晶粒度细于13级。
33.本发明的低屈强比超高强度连续油管用钢各合金元素及其质量百分比设计原理如下:
34.1)c是最基本的强化元素,c溶解在钢中形成间隙固溶体,起固溶强化的作用,与强碳化物形成元素形成碳化物析出,则起到沉淀强化的作用。但c含量太高对钢的韧性和焊接性能不利,c含量太低会降低钢的强度,所以c控制在0.10~0.15%。
35.2)si在钢中起到固溶强化作用,从而提高钢的强度,同时也是钢中的脱氧元素,但过高的si含量会影响钢材的表面质量,所以si控制在0.30~0.40%。
36.3)mn是廉价元素,其可通过固溶强化提高钢的强度,还可以提高钢的淬透性,有利于马氏体生成,但过高的mn元素易造成严重的中心偏析,所以mn控制在1.5~2.0%。
37.4)p、s是有害的残余元素,易引起偏析、聚集,尽量降低钢中的p、s含量,所以将p、s控制为p≤0.015%、s≤0.002%。
38.5)cr是提高钢的淬透性的重要元素,有利于生成马氏体组织,有效提高钢的强度,而且cr含量在0.20%以上时,能有效改善钢的耐腐蚀性能。但太高的cr和mn同时加入钢中,会导致低熔点cr
‑
mn复合氧化物形成,在热加工过程中形成表面裂纹,同时会严重恶化焊接性能,所以cr控制在0.50~0.70%。
39.6)mo是强淬透性元素,显著推迟铁素体相变,抑制铁素体和珠光体的形成,有利于马氏体形成,mo还能起到克服热处理过程中的回火脆性,改善热处理性能、疲劳性能的作用。但太高的mo有损塑性且mo价格比较昂贵,所以mo控制在0.20~0.50%。
40.7)nb是管线钢中不可缺少的微合金元素,能同时提高材料的强度和低温韧性,但nb含量过高时,不仅难以充分发挥作用,同时可能导致析出颗粒粗大不利于钢的韧性。所以nb控制在0.050~0.070%。
41.8)v有较高的沉淀强化和较弱的细化晶粒作用,对钢的强化做出贡献,同时,还可以在一定程度上改善钢的焊接韧性。但如含量太高,则成本增加显著。所以v控制在0.050~0.080%。
42.9)ti与钢中的c、n等形成化合物,为了降低钢中固溶氮含量,通常采用微ti处理,使钢中的n被ti固定,钢中加入微量的ti,可以通过提高钢板强度和韧性。但超过0.020%的ti易引起ti的碳/氮化物的粗化和过度析出,导致韧性大幅降低。所以ti控制在0.010~0.020%。
43.10)al是钢中主要的脱氧元素,能够显著降低钢中的o含量,同时al与n的结合形成aln,能够有效地细化晶粒。但是钢中铝含量过高,易导致al的氧化物夹杂明显增加,降低钢的洁净度,对钢的低温韧性不利。所以al控制在0.020~0.040%。
44.实施例2
45.本实施例的一种低屈强比超高强度连续油管用钢的制造方法,基本结构同实施例1,不同和改进之处在于:采用传统热连轧板带工艺生产,包括如下步骤:铁水预处理
→
转炉冶炼
→
炉外精炼
→
连铸
→
板坯清理
→
板坯加热
→
控制轧制
→
控制冷却
→
卷取,通过各步骤对形变和温度以及冷却速度控制。
46.1)冶炼、精炼、连铸工艺
47.按照上述化学成分进行钢水冶炼。采用洁净钢冶炼技术,经过rh炉、lf炉处理和进行钙处理,以提高钢水纯净度,控制非金属夹杂物形态数量、形态和尺寸,减少非金属夹杂物的形成。连铸过程中投用动态轻压下和电磁制动,减少铸坯内部缺陷,提高材料的塑韧性。板坯切割完成后对板坯表面进行检查和清理,避免热轧过程中带钢产生边部缺陷。
48.2)控制轧制和控制冷却工艺
49.板坯首先入加热炉进行加热,均热温度控制在1230~1270℃,促进奥氏体均匀化和合金元素在奥氏体中充分固溶,同时避免奥氏体晶粒过分粗化。板坯出炉经过高压水除鳞去除表面氧化铁皮后进行轧制,轧制分为粗轧和精轧两个阶段。粗轧阶段在奥氏体再结晶区进行多道次轧制,轧制温度控制在1000~1060℃,粗轧累计压下率≥82%,促进形变奥氏体晶粒进行多次回复再结晶细化,粗轧后板坯厚度控制在39~45mm。精轧开轧温度控制在1000℃左右,通过累计大变形增加形变奥氏体内的形变带和位错密度,从而增加相变形核点细化晶粒尺寸,精轧累计压下率≥89%。精轧终轧温度控制在840~880℃,避免在低温双相区轧制导致轧机负荷过大,同时避免造成混晶,也要避免终轧温度过高导致奥氏体晶粒粗化。精轧结束后进行前段层流冷却,冷却速度控制在30~40℃/s,控制冷却后的钢板卷取温度在400~500℃。
50.本实施例中,通过各步骤对形变和温度以及冷却速度控制,进而形成均匀细小的f+m双相组织,实现低屈强比超高强度连续油管用钢控制,该钢的力学性能:rt0.5:700~762mpa,rm:1100~1141mpa,a50:10%~16%,屈强比:0.63~0.68;冷弯性能180
°
,d=4a合格,具有较高的强度、较低的屈强比、较好的成形性能。
51.结合下列表格中的实施例可以看出,本发明的一种低屈强比超高强度连续油管用钢的给出的化学成分重量百分比进行原料选取,再按照本发明给出的制造方法生产,就可以得到具有较高的强度、较低的屈强比、较好的成形性能的超高强度连续油管用钢,用于制造140ksi级别的超高强连续油管。
52.本发明各实施例和对比例的化学成分如表1所示。
53.表1本发明各实施例的化学成分
[0054][0055]
本发明各实施例和对比例的主要轧制工艺参数如表2所示。
[0056]
表2轧制工序主要工艺参数
[0057][0058]
本发明各实施例和对比例的力学性能如表3所示。
[0059]
表3力学性能
[0060][0061]
以上示意性的对本发明及其实施方式进行了描述,该描述没有限制性,附图中所示的也只是本发明的实施方式之一,实际的结构并不局限于此。所以,如果本领域的普通技术人员受其启示,在不脱离本发明创造宗旨的情况下,不经创造性的设计出与该技术方案相似的结构方式及实施例,均应属于本发明的保护范围。