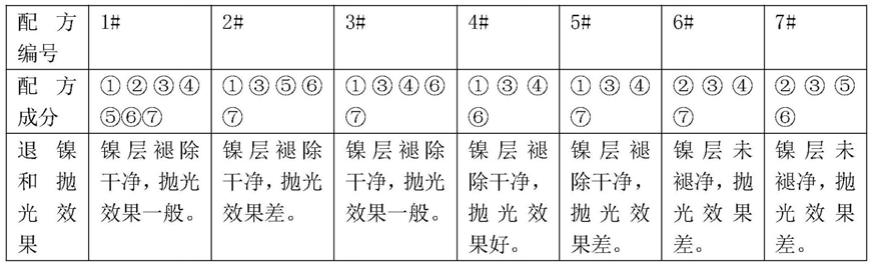
1.本发明涉及化学腐蚀技术领域,具体为一种纯铁材料表面镀镍层的低腐蚀褪镍组合物及方法。
背景技术:2.纯铁材料由于其良好的导磁性,广泛应用于以行波管为代表的电真空产品,纯铁材料的焊接性能较差,为了提高焊接性能,往往需要在纯铁材料表面电镀一层镍,往往会因镀层不合格或其他原因,需对零件表面镍层进行褪除。由于电真空产品的零件需要经过高温热处理,铁基体与镍层相互渗透,形成铁镍过渡层,采用氰化物体系溶液或强酸体系溶液进行褪除,由于过渡层的存在,会对铁材料造成腐蚀,腐蚀量可达30μm,导致铁件全部报废。
3.本专利介绍了一种纯铁材料表面镀镍层的低腐蚀褪镍组合物及方法,可以去除铁材料表面的镀镍层,对基体的腐蚀量可以达到5μm以下。
技术实现要素:4.为克服现有技术存在的不足,本发明提供一种纯铁材料表面镀镍层的无损褪镍组合物及方法,用于镀镍铁件返工处理,降低生产成本,本发明提供了如下的技术方案:
5.本发明一种纯铁材料表面镀镍层的低腐蚀褪镍组合物,所述褪镍组合物由以下原料组成:硝酸、硫酸、过氧化氢、三氯化铁、硫酸亚铁、六次甲基四胺、硫脲和水,按照所起的作用进行分类,如下:
6.镍层去除:硝酸
①
、硫酸
②
7.化学抛光:过氧化氢
③
、三氯化铁
④
、硫酸亚铁
⑤
8.缓蚀:六次甲基四胺
⑥
、硫脲
⑦
9.优选试验情况如下表所示:
[0010][0011]
在优选试验的基础上,进行了进一步试验,确定了最优的褪镍组合物配比,每配制1l褪镍组合物,各溶质的用量分别为硝酸:250
‑
300ml/l;过氧化氢:180
‑
200ml/l;三氯化铁:8
‑
10g/l;六次甲基四胺:1.5
‑
2g/l。
[0012]
一种纯铁材料表面镀镍层的低腐蚀褪镍组合物的方法,所述方法包括如下步骤:
[0013]
s1、配制褪镍组合物:a、根据要配制的组合物总体积计算各种溶质的用量;b、根据计算结果,量取硝酸、过氧化氢倒入至耐腐蚀容器中,加水至总体积的2/3,搅拌后得到第一
中间组合物;c、根据计算结果,称取三氯化铁、六次甲基四胺倒入至耐腐蚀容器中,加水至总体积的1/4,搅拌溶解后,得到第二中间液;d、将第二中间液倒入至第一中间液,加水至总体积,搅拌均匀得到所述的褪镍组合物;
[0014]
s2、将待褪镍的铁件浸入褪镍组合物中。
[0015]
作为本发明的一种优选技术方案,所述s2中褪镍时间为当气泡由小变大时,取出观察表面是否光亮,若不光亮,则继续浸泡,每5s取出观察,直至表面光亮为止,褪镍在室温下进行。
[0016]
原理:选择上述组分及范围的原因是:
[0017]
硝酸:硝酸的作用主要是腐蚀基体表面的镀镍层,如添加硝酸高于本发明范围,镀镍层易出现钝化,导致镍层无法去除,而当硝酸的量低于本发明范围,则镀镍层去除不均匀,易出现铁基体腐蚀。因此,上述范围为本发明最佳范围。
[0018]
过氧化氢:过氧化氢的作用主要是在镍层被去除后,对铁基体表面进行抛光,如添加过氧化氢高于本发明范围,产生的气体无法快速排出,会形成针孔,而当过氧化氢的量低于本发明范围,则成膜不连续,导致抛光效果差。因此,上述范围为本发明最佳范围。
[0019]
三氯化铁:三氯化铁可以辅助过氧化氢在表面成膜,同时铁离子可以减缓铁基体的腐蚀速度,如添加三氯化铁高于本发明范围,成膜过厚,且不均匀,如三氯化铁低于本发明范围,则成膜不连续。因此,上述范围为本发明最佳范围。
[0020]
六次甲基四胺:六次甲基四胺起到缓蚀作用,降低反应速度,防止基体发生过腐蚀,如添加六次甲基四胺高于本发明范围,反应缓慢,效率低下,如六次甲基四胺低于本发明范围,则反应速度过快,基体易发生过腐蚀。因此,上述范围为本发明最佳范围。
[0021]
褪镍时间:褪镍时间主要与基体表面粗糙度和基体腐蚀量有关,如褪镍时间超出本发明的规定,则基体腐蚀量过大,如褪镍时间小于本发明范围,则镍层无法完全褪除或表面不光亮。
[0022]
有益效果:与现有技术相比,本发明利用硝酸对镍层的腐蚀作用来去除铁基体表面镍层;采用铁离子和六次甲基四胺的缓蚀作用,可以防止铁基体被腐蚀;采用过氧化氢和三价铁离子的成膜作用,来提高铁基体表面的光洁度。本发明与现有常规的褪镍技术相比,对基体的腐蚀量从30μm降低至5μm以下。
具体实施方式
[0023]
以下对本发明的优选实施例进行说明,应当理解,此处所描述的优选实施例仅用于说明和解释本发明,并不用于限定本发明。
[0024]
实施例1
[0025]
一种纯铁材料表面镀镍层的低腐蚀褪镍组合物的方法,所述方法包括如下步骤:
[0026]
s1、配制总体积为1l的褪镍组合物,具体包括:
[0027]
a、量取250ml硝酸、180ml过氧化氢倒入至耐腐蚀容器中,加水至总体积的2/3,搅拌后得到第一中间组合物;
[0028]
b、称取8g三氯化铁、1.5g六次甲基四胺倒入至耐腐蚀容器中,加水至总体积的1/4,搅拌溶解后,得到第二中间液;
[0029]
c、将第二中间液倒入至第一中间液,加水至1l,搅拌均匀得到所述的褪镍组合物。
[0030]
s2、将待褪镍的铁件浸入褪镍组合物中,温度为室温,当气泡由小变大时,取出观察表面是否光亮,若不光亮,则继续浸泡,每5s取出观察,直至表面光亮为止。
[0031]
s3、取出铁基体,冲洗干净,用乙醇脱水,烘干机烘干。
[0032]
实施例2
[0033]
与实施例1不同,步骤s1中,各化学品的组分含量分别为:
[0034]
硝酸:270ml
[0035]
过氧化氢:190ml
[0036]
三氯化铁:9g
[0037]
六次甲基四胺:1.8g。
[0038]
实施例3
[0039]
与实施例2不同,步骤s1中,各化学品的组分含量分别为:
[0040]
硝酸:300ml
[0041]
过氧化氢:200ml
[0042]
三氯化铁:10g
[0043]
六次甲基四胺:2g。
[0044]
实施例4
[0045]
与实施例3不同,步骤s1中,各化学品的组分含量分别为:
[0046]
硝酸:250ml
[0047]
过氧化氢:200ml
[0048]
三氯化铁:10g
[0049]
六次甲基四胺:2g。
[0050]
实施例5
[0051]
与实施例4不同,步骤s1中,各化学品的组分含量分别为:
[0052]
硝酸:270ml
[0053]
过氧化氢:200ml
[0054]
三氯化铁:8g
[0055]
六次甲基四胺:2g。
[0056]
各实施例的尺寸腐蚀情况见下表,从表中可看出,褪镍后的铁基体在1
‑
3μm,基体腐蚀量在可控范围内。
[0057][0058][0059]
以上所述仅为本发明的优选实施例而已,并不用于限制本发明,尽管参照前述实施例对本发明进行了详细的说明,对于本领域的技术人员来说,其依然可以对前述各实施例所记载的技术方案进行修改,或者对其中部分技术特征进行等同替换。凡在本发明的精
神和原则之内,所作的任何修改、等同替换、改进等,均应包含在本发明的保护范围之内。