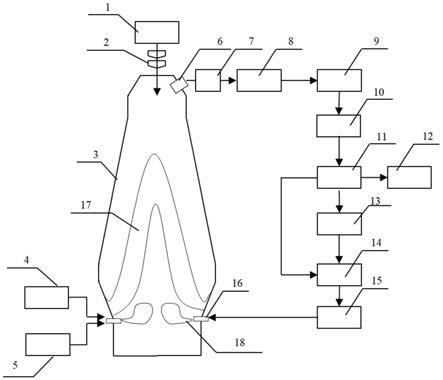
1.本发明属于高炉炼铁技术领域,特别是涉及一种低碳高炉炼铁方法。
背景技术:2.绿色化、低碳化发展是当今世界钢铁工业发展的主旋律,而高炉炼铁工序的碳排放占钢铁冶金工业的碳排放的70%以上,因此发展低碳高炉是实现钢铁工业碳减排的主要方向之一。如今,各大钢铁企业已经通过优化原燃料条件、优化炉型设计、强化冶炼等技术手段,使高炉燃料比降低到了较低水平。然而,通过理论计算发现,传统高炉由于炉腹煤气中含有大量的n2,导致与铁矿石发生间接还原反应的还原性气体含量不高,煤气利用不充分,铁矿石到达软熔带时,仍然含有大量的铁氧化物,这些铁氧化物与焦炭中的碳素发生强吸热的直接还原反应,进一步消耗了碳素以补充这部分热量,最终致使传统高炉炼铁燃料比降低到480
‑
490kg/thm已是极限,吨铁碳排放量仍然很高。因此,有必要发展有别于传统高炉的新的低碳高炉炼铁工艺技术。
3.如今,现有的低碳高炉技术有高炉喷吹富氢气体、氧气高炉和炉顶煤气循环等。由于氢气还原铁氧化物反应会吸收大量热量,导致高炉喷吹富氢气体的减碳效果十分有限,且我国富氢气体气源有限,因而成本较高;氧气高炉和炉顶煤气循环技术,下部回旋区的高氧浓度致使回旋区局部燃烧焦点温度高,而且热载体
‑
鼓风n2减少致使吨铁煤气量大幅减少,导致风口鼓风动能不足,为了维持必要的鼓风动能不得不将风口直径大幅减小;同时吨铁煤气量减少导致炉上部热量供应不足,被迫考虑炉身喷吹热还原气,从而导致风口燃烧带进一步萎缩,无法保证下部气流分布的合理性和炉缸的活跃性,致使高炉容积适当扩大后就难于保证高炉的稳定顺行。
技术实现要素:4.鉴于以上所述现有技术的缺点,本发明的目的在于提供一种低碳高炉炼铁方法,用于解决现有技术中炼铁燃料比降低有限且吨铁碳排放量高的问题,以达到降低高炉燃料比,提升高炉炼铁效率和降低高炉炼铁过程co2排放的目的。
5.为实现上述目的及其他相关目的,本发明提供一种低碳高炉炼铁方法,包括:
6.将经加热加压后的回喷煤气喷入高炉,将纯氧喷入高炉或将富氧热风喷入高炉,将煤粉喷入高炉,将铁矿石和焦炭交替装入高炉;
7.高炉内发生化学反应后形成有炉顶煤气;
8.所述炉顶煤气在经过一系列的处理工序后,再经过加压和加热处理后的炉顶煤气作为回喷煤气喷入高炉,剩余的炉顶煤气被送至煤气管网。
9.本发明采用富氧冶炼和炉顶煤气循环相耦合的工艺,通过喷吹常温纯氧,以及将经脱硫、脱除co2、脱除n2后并加热加压的炉顶煤气回喷进入高炉,从而提高所述低碳高炉炉腹煤气中的还原性气体含量。高还原性气体含量的炉腹煤气向高炉中上部运动,与向高炉下部运动的铁矿石充分接触,发展间接还原反应。
10.进一步,若采用将纯氧喷入高炉,所述处理工序包括除尘、脱水、脱硫、脱除co2,吨铁纯氧喷吹量与吨铁炉顶煤气回喷量之和与同炉容的高炉吨铁耗热风量相近;若采用将富氧热风喷入高炉,所述处理工序包括除尘、脱水、脱硫、脱除co2以及脱除n2,吨铁富氧热风喷吹量与吨铁炉顶煤气回喷量之和与同炉容的高炉吨铁耗热风量相近。相较于喷吹富氧热风工艺,喷吹纯氧工艺可减少n2进入高炉,可提升炉腹煤气中的还原性气体含量,提升高炉中上部的间接还原效率。若喷吹富氧热风,则需脱除炉顶煤气中的n2,以提高所述回喷煤气中还原性气体含量。
11.进一步,所述炉顶煤气经除尘后的颗粒物含量小于20mg/nm3。经除尘后的炉顶煤气,一方面可以直接进入煤气管网,另一方面可确保后续的炉顶煤气脱硫、co2脱除工序不因煤气中的颗粒物而减弱或失去效果。
12.进一步,所述炉顶煤气经脱水后的脱水效率大于95%。
13.进一步,所述炉顶煤气经脱硫后的s含量低于0.015%。炉顶煤气中硫含量较高一方面会对管线造成腐蚀,另一方面也不符合超低排放的要求。
14.进一步,所述炉顶煤气经脱除co2后的co2脱除率大于95%。经co2脱除后形成的回喷煤气,一方面可提高回喷煤气中还原气体浓度,确保炉身中上部能够充分发展h2和co与铁氧化物之间的间接还原反应,另一方面如果回喷煤气中co2脱除率小于95%,co2会与焦炭发生大量的碳的熔损反应,导致燃料比升高。
15.进一步,所述回喷煤气需加压至0.5mpa以上。较高压力的回喷煤气可保证风口回旋区的风速和鼓风动能与同级别常规高炉的风速和鼓风动能相当,确保风口回旋区相较于同级别常规高炉不会大幅度萎缩,活跃炉缸,保证高炉高效、稳定、顺行。
16.进一步,所述回喷煤气需加热至950℃以上。高温煤气可弥补部分炉内化学反应及加热炉料所需热量,达到进一步降低燃料消耗的目的。
17.进一步,所述纯氧的纯度大于99%。高纯氧气可以强化冶炼,提高高炉的利用系数。特别的是,高纯氧气中杂质元素含量较少,可以避免其他杂质气体进入炉内,其与风口回旋区中过量的煤粉和焦炭等炭质原料反应后产生co等还原性气体,保证炉身中上部还原气体含量较高。
18.进一步,所述纯氧由氧气喷管喷入高炉,且所述纯氧的喷吹压力高于回喷煤气的喷吹压力。较高的氧气喷吹压力一方面可以保证高纯氧气能够有效地喷吹进入炉缸中心,另一方面可防止氧气管道内部发生回火等安全事故。
19.进一步,所述煤粉由煤载气经煤枪喷吹进入高炉,所述煤载气为从所述炉顶煤气脱除的co2气体。co2进入风口区域后,会在高温下与炉缸中的碳发生熔损反应,产生还原性气体co。煤载气采用co2气体一方面可以消耗部分炉顶煤气中脱除的co2,达到co2在高炉炉内循环的目的,另一方面可避免其他成分的载气进入高炉,降低了炉腹煤气中还原性气体含量的同时,增加后续其他气体脱除工序。
20.进一步,优选地,所述煤粉为挥发分大于21%的高挥发分煤粉,所述高挥发性煤粉中的挥发分裂解后产生的h2用于参与间接还原反应。挥发分裂解后产生的h2代替部分参与间接还原反应的co的量,最终达到减少co2的产生与排放的目的。
21.进一步,所述铁矿石为高还原性铁矿石,包括烧结矿、球团矿、块矿和复合铁焦中的一种或几种,其综合入炉品位大于58%,其还原度指数ri大于80%。入炉品位大于58%可
降低炉渣产生量,减少高炉炉内热量消耗。较高的还原度(ri>80%)可确保炉身中上部的铁矿石与还原性气体充分发生间接还原反应。
22.如上所述,本发明的一种低碳高炉炼铁方法,具有以下有益效果:
23.在不对传统高炉体系进行较大改动的前提下,本发明采用富氧冶炼和炉顶煤气循环工艺,大幅度提升高炉炉内碳素的利用率,并提高炉腹煤气中还原性气体的浓度,降低高炉炉缸内部直接还原度,节省燃料消耗,降低了高炉燃料比,提升了高炉炼铁效率和降低了高炉炼铁过程co2排放。
附图说明
24.图1为本发明实施例一的一种低碳高炉炼铁方法采用的系统示意图;
25.图2为本发明实施例二的一种低碳高炉炼铁方法采用的系统示意图。
26.零件标号说明
[0027]1‑
炉料;2
‑
布料组件;3
‑
高炉本体;4
‑
喷煤装置;5
‑
制氧装置;6
‑
炉顶煤气管道;7
‑
炉顶湿煤气;8
‑
除尘装置;9
‑
脱水装置;10
‑
脱硫装置;11
‑
co2脱除装置;12
‑
煤气管网;13
‑
加压装置;14
‑
预热装置;15
‑
回喷煤气;16
‑
风口组件;17
‑
软熔带;18
‑
风口回旋区;19
‑
热风炉装置;20
‑
n2脱除装置;21
‑
空气。
具体实施方式
[0028]
以下由特定的具体实施例说明本发明的实施方式,熟悉此技术的人士可由本说明书所揭露的内容轻易地了解本发明的其他优点及功效。
[0029]
须知,本说明书所附图式所绘示的结构、比例、大小等,均仅用以配合说明书所揭示的内容,以供熟悉此技术的人士了解与阅读,并非用以限定本发明可实施的限定条件,故不具技术上的实质意义,任何结构的修饰、比例关系的改变或大小的调整,在不影响本发明所能产生的功效及所能达成的目的下,均应仍落在本发明所揭示的技术内容得能涵盖的范围内。同时,本说明书中所引用的如“上”、“下”、“左”、“右”、“中间”及“一”等的用语,亦仅为便于叙述的明了,而非用以限定本发明可实施的范围,其相对关系的改变或调整,在无实质变更技术内容下,当亦视为本发明可实施的范畴。
[0030]
请结合图1所示,本发明提供一种低碳高炉炼铁方法,包括:
[0031]
将经加热加压后的回喷煤气15喷入高炉,将纯氧喷入高炉或将富氧热风喷入高炉,将煤粉喷入高炉,将铁矿石和焦炭交替装入高炉;
[0032]
高炉内发生化学反应后形成有炉顶煤气;
[0033]
所述炉顶煤气在经过一系列的处理工序后,再经过加压和加热处理后的炉顶煤气作为回喷煤气15喷入高炉,剩余的炉顶煤气被送至煤气管网。
[0034]
具体的,经预热加压后的回喷煤气15由风口喷入高炉,纯氧由氧气喷管经风口喷入高炉,富氧热风由热风围管经风口喷入高炉,煤粉由煤载气经风口喷吹进入高炉,铁矿石和焦炭等炉料1由布料组件2装入高炉。
[0035]
高炉内主要发生煤粉挥发分分解反应、煤粉和焦炭中碳素发生燃烧反应、碳素熔损反应及铁水中c与渣中si、mn、s等的还原反应等;回喷煤气15和高炉中化学反应所形成的煤气组成炉腹煤气,炉腹煤气中co与h2之和占比在90%以上,铁矿石在高炉中上部与高浓
度的还原气体充分发展间接还原反应,使铁矿石在到达软熔带17以下的高温区时金属化率较常规高炉高,确保高炉炉缸内基本不发生c与铁氧化物的直接还原反应;参与间接还原反应后的炉顶煤气主要成分为co、h2、co2和少量的n2。
[0036]
其中,若采用将纯氧由氧气喷管经风口喷入高炉,所述处理操作包括除尘、脱水、脱硫、脱除co2,吨铁炉顶煤气回喷量及吨铁氧气喷吹量之和与同炉容的高炉吨铁耗热风量相近;若采用将富氧热风由热风围管经风口喷入高炉,所述处理操作包括除尘、脱水、脱硫、脱除co2以及脱除n2,吨铁纯氧喷吹量、吨铁富氧热风喷吹量及吨铁炉顶煤气回喷量之和与同炉容的高炉吨铁耗热风量相近。如此,使所述低碳高炉炉内气流分布与料层分布均与传统高炉接近。
[0037]
将所述炉顶煤气经一系列的处理操作后,分解为三部分,一部分用于加热另一部分炉顶煤气,剩余的炉顶煤气被外送至煤气管网,经加热后的炉顶煤气经加压后作为回喷煤气15喷入高炉。
[0038]
所述低碳高炉炼铁方法相较于常规高炉可提高高炉炉内还原剂的利用率,并且由于抑制了高炉炉内强吸热的碳与铁矿石之间的直接还原反应的发生,从而可控制高炉焦比小于220kg/thm(thm为吨铁水),燃料比小于400kg/thm。
[0039]
采用富氧冶炼和炉顶煤气循环相耦合的工艺,将炉顶煤气进行除尘、脱硫、脱除co2、脱除n2、加压和加热后回喷进入高炉,使炉腹煤气中还原气体含量较常规高炉高,发展高炉内的间接还原反应,使铁矿石在到达软熔带17下方时金属化率较常规高炉高,使高炉高温区基本不发生高吸热的c与铁氧化物的直接还原反应,达到减少高炉炼铁co2排放的目的。
[0040]
由于炉内充分发展放热的间接还原反应,而减少吸热的c与铁氧化物的直接还原反应发生,降低了燃料消耗,达到了碳减排的目的,且由于风口富氧冶炼,可达到强化冶炼的目的。
[0041]
实施例1
[0042]
本实施例以炉容为1580m3的高炉为例,参阅图1所示,采用如上所述的低碳高炉炼铁方法,本实施例采用的低碳高炉炼铁系统包括高炉本体装置、喷煤装置4、制氧装置5、除尘装置8、脱水装置9、脱硫装置10、co2脱除装置11、加压装置13及预热装置14,其中:高炉本体装置,包括高炉本体3、设置于所述高炉本体3上的布料组件2和风口组件16,高炉本体3的顶部还设置有炉顶煤气管道6。并且,布料组件2、高炉本体3、喷煤装置4、制氧装置5、炉顶煤气管道6、除尘装置8、脱水装置9、脱硫装置10与常规高炉一致。
[0043]
高炉本体3为构筑在基础地基上的筒状炉体。与常规高炉不同的是,该低碳高炉炼铁系统取消了热风炉装置,而是采用制氧装置5制备的高纯氧和经脱除co2后的高炉炉顶煤气代替热风,由管道输送至高炉本体3后,经风口组件16喷入高炉。如此,一方面可以提高高炉炉内碳素的利用率,另一方面可进一步提升炉腹煤气中还原气体的浓度,使高炉炉内的铁矿石与还原性气体充分发展间接还原反应,使铁矿石在到达软熔带17时金属化率接近100%,从而避免铁氧化物与碳发生强吸热的直接还原反应,以减少供直接还原反应热量的碳素消耗。最终可实现高炉燃料比达370kg/thm以下,计算理论焦比可达200kg/thm以下。
[0044]
本发明为达到上述目的,采用了以下的方法:
[0045]
块状或球状的铁矿石和焦炭等炉料1经布料组件2交替布入高炉本体3,炉料1受重
力作用从高炉本体3的上部向高炉本体3的下部运动,炉缸内风口回旋区18产生的大量高温炉腹煤气向炉身上部流动。一方面,将其携带的高热量传递给铁矿石和焦炭等炉料1,使铁矿石升温至可与还原性气体充分发生间接反应的温度;另一方面,炉腹煤气中的还原性气体与铁矿石发生间接还原反应,将铁矿石还原为金属铁。
[0046]
制氧装置5制备的纯度为99%的氧气由氧气喷管经风口组件16喷吹进入高炉中,喷吹量约为223nm3/thm。
[0047]
挥发分含量为30%的煤粉经喷煤装置4由风口组件16喷吹进入高炉中,吨铁喷煤量约为170kg/thm,煤粉喷吹采用的煤载气为co2气体。煤粉挥发分中的甲烷、乙烷等在风口回旋区18发生裂解反应,产生co和h2可进一步提升炉腹煤气中还原性气体的含量。同时,h2还可以替代部分co参与与铁矿石的间接还原反应,可进一步降低高炉冶炼过程中co2的产生与排放。
[0048]
实施例1中的高炉炉顶湿煤气7经除尘、脱水、脱硫、脱除co2、加压、加热后回喷进入所述高炉本体3,剩余炉顶煤气送入煤气管网12。为保证下部高炉内部气流分布的合理性和炉缸的活跃性,计算得到回喷煤气量约为606nm3/thm。喷氧量与回喷煤气量之和约为829nm3/thm,保证吨铁纯氧喷吹量与吨铁炉顶煤气回喷量之和与传统同炉容的高炉吨铁耗热风量相近。
[0049]
为保证回喷煤气15能吹到炉缸中心,并提高冶炼效率,回喷煤气15需由加压装置13加压至与常规高炉风压相当,即达到0.5mpa以上。同时,为防止氧气喷管内出现回火等安全问题,纯氧的喷吹压力高于回喷煤气15的喷吹压力。
[0050]
根据热量平衡和物料平衡计算,为保证足够的热量供应,从风口喷入的回喷煤气15需加热至950℃以上。风口喷入的纯氧,一部分与喷入的煤粉的发生燃烧反应,另一部分与部分焦炭发生燃烧反应,这两个反应均放出大量的热量,为炉内煤粉挥发分分解和铁水、炉渣熔化提供热量。剩余焦炭中的碳分别与回喷煤气15及煤载气中的co2发生熔损反应、与炉渣中sio2和mno等发生还原反应、溶解进入铁水中作为铁水渗碳等。产生炉腹煤气量约为1200nm3/thm,炉腹煤气成分如下表1所示。
[0051]
表1炉腹煤气成分
[0052][0053]
炉腹煤气中还原气体含量约为95%。充足的炉腹煤气量及高还原性气体含量的炉腹煤气可以保证铁矿石在到达软熔带17时金属化率接近100%,确保高炉高温区不发生碳与铁氧化物的直接还原反应,直接还原度降低为接近0。此时,低熔点的铁水和炉渣受到炉缸风口回旋区18产生的高热量的加热成为液态,铁水和液态炉渣经焦炭层渗透进入炉缸,软熔带17也可能不存在。
[0054]
为保证高炉上部的铁矿石与还原性气体能充分发展间接还原反应,较佳的,使用还原性ri大于80、综合入炉品位大于58%的铁矿石,铁矿石的冷态强度和焦炭的性能指标满足同级别高炉冶炼即可。
[0055]
经过间接还原反应后,炉顶干煤气量约为1119nm3/thm,其中co2含量约为38%,co含量约为31.6%,h2含量约为8.6%,n2含量约为28.1%。
[0056]
炉顶煤气经除尘、脱水、脱硫和脱除co2后,炉顶煤气中co含量约为67%,h2含量约
为24%,还原性气体含量高的气体热值较高。炉顶煤气经上述处理工序后,被分解为三部分,其中606nm3/thm作为回喷煤气15,110nm3/thm用于加热回喷煤气15,剩余煤气15.2nm3/thm外供至煤气管网12。回喷煤气15经加压装置13加压后即可由风口组件16回喷进入高炉。如此循环,可实现高炉高效化冶炼,高炉炼铁生产效率提升超过20%,吨铁co2排放减少25%的目标。
[0057]
实施例2
[0058]
本实施例以炉容为850m3的高炉为例,参阅图2所示,采用如上所述的低碳高炉炼铁方法,本实施例采用的低碳高炉炼铁系统包括高炉本体装置、喷煤装置4、除尘装置8、脱水装置9、脱硫装置10、co2脱除装置11、加压装置13、预热装置14、热风炉装置19及n2脱除装置20,其中:高炉本体装置,包括高炉本体3、设置于所述高炉本体3上的布料组件2和风口组件16,高炉本体3的顶部还设置有炉顶煤气管道6。并且,布料组件2、高炉本体3、喷煤装置4、炉顶煤气管道6、除尘装置8、脱水装置9、脱硫装置10、co2脱除装置11、加压装置13、预热装置14与所述实施例1中的低碳高炉炼铁系统一致。本实施例中,只将72%的高炉炉顶湿煤气7经处理后回喷进入高炉,因此,为保证风口充足的风量,需与常规高炉一样采用热风炉装置19,制氧装置5制备的氧气混入空气21中通入热风炉装置19中加热,形成富氧热风,并增设n2脱除装置20。对于与所述实施例1的共同部分省略说明,以下只对不同的部分进行说明。
[0059]
实施例2中的高炉炉顶湿煤气7经除尘、脱水、脱硫、脱除co2、脱除n2、加压、加热后回喷进入所述高炉本体3,剩余炉顶煤气送入煤气管网12。相较于实施例1,此处需新增煤气脱除n2装置,以脱除炉顶煤气中由于鼓风带入的n2,提升回喷煤气15中还原性气体的含量。经计算回喷煤气量为376nm3/thm。回喷煤气温度为950℃。
[0060]
实施例2采用热风炉装置19,富氧热风鼓风量为587.3nm3/thm。富氧热风鼓风量与回喷煤气量之和约为963.3nm3/thm,保证吨铁富氧热风喷吹量与吨铁炉顶煤气回喷量之和与传统同炉容的高炉吨铁耗热风量相当,高炉操作和生产运行不发生较大的改变。
[0061]
鼓风富氧率为17.9%,较高富氧率可促进煤粉充分燃烧,提升冶炼效率。鼓风温度为1200℃,与常规高炉接近。
[0062]
为保证回喷煤气15能吹到炉缸中心,并提高冶炼效率,回喷煤气15的喷吹压力与常规高炉风压相当,即达到0.5mpa以上。富氧热风压力在0.35mpa~0.5mpa以下,为防止热风围管内出现回火等安全问题,回喷煤气15的喷吹压力应高于富氧热风喷吹压力。
[0063]
由于鼓风中氧含量相较于实施例1中富氧冶炼方式的氧含量少,因此,实施例2不宜采用过高挥发分含量的煤粉喷吹,以避免大量挥发性物质分解耗热,致使理论燃烧温度偏低。故实施例2选用挥发分含量约为21%的煤粉进行喷吹,喷煤量约为180kg/thm,根据热量平衡计算可得理论焦比约为200.2kg/thm,理论燃料比约为380.2kg/thm。
[0064]
高炉炉内发生的主要化学反应及热量传输、炉料1和煤气的运行与实施例1一致。产生炉腹煤气量约为1294nm3/thm,炉腹煤气成分如下表2所示。
[0065]
表2炉腹煤气成分
[0066][0067]
炉腹煤气中还原气体含量约为71.8%。充足的炉腹煤气量及高还原性气体含量的
炉腹煤气可以确保高炉中上部充分发展间接还原反应,最终直接还原度降低至约为0.182。
[0068]
喷吹煤粉用的煤载气、入炉铁矿石冶金性能要求均与实施例1一致。经过间接还原反应后,炉顶干煤气量约为1300.3nm3/thm,其中co2含量约为31.7%,co含量约为31.6%,h2含量约为8.6%,n2含量约为28.1%。
[0069]
与实施例1不同的是,实施例2的炉顶湿煤气7经除尘后,分出其中316.3nm3/thm用以加热回喷煤气15和富氧热风,其中936.2nm3/thm(占炉顶湿煤气总量的72%)煤气继续经co2脱除装置11脱除co2、n2脱除装置20脱除n2、加压装置13加压、预热装置14加热后回喷进入高炉,经脱除co2和脱除n2后回喷煤气量为376nm3/thm,剩余47.8nm3/thm炉顶煤气进入煤气管网12。
[0070]
经脱除co2、脱除n2后的回喷煤气15中co含量约为78.7%,h2含量约为21.3%,由风口组件16回喷进入高炉。如此循环,可实现高炉高效化冶炼,高炉炼铁生产效率提升超过12%,吨铁co2排放减少20%的目标。显然,相较于实施例1,实施例2只回喷72%的炉顶煤气在强化高炉冶炼和碳排放的效果要降低很多。
[0071]
实施例3
[0072]
本实施例以炉容为2850m3的高炉为例进行说明。实施例3的实施方式也如图2所示。
[0073]
实施例3的工艺流程均与实施例2一致,所不同的是实施例3是基于2850m3的中大型高炉实施,较大炉型的高炉改变操作方法较为困难,且风口所需风量较高。若还是维持较高的回喷煤气量,一方面后续需脱除co2和脱除n2、加压、加热的煤气量较大,另一方面,较大的煤气量回喷进入高炉,安全性和稳定性无法得到保障。因此,本实施例仅将25%的高炉炉顶湿煤气7经处理后回喷进入高炉。
[0074]
实施例3中的高炉炉顶湿煤气7进行除尘、脱水、脱硫、脱除co2、脱除n2、加压、加热后回喷进入所述高炉本体3,剩余煤气送入煤气管网12。经脱除co2和脱除n2回喷煤气量为126nm3/thm。回喷煤气温度为950℃。
[0075]
实施例3的富氧热风鼓风量为813.3nm3/thm。富氧热风鼓风量与回喷煤气量之和约为939.3nm3/thm,保证吨铁富氧热风喷吹量与吨铁炉顶煤气回喷量之和与传统同炉容的高炉吨铁耗热风量相当,高炉操作和生产运行不发生较大的改变。
[0076]
鼓风富氧率为6.0%,鼓风温度为1200℃,与常规高炉接近。
[0077]
高炉富氧热风的压力与实施例2中的要求一致。同时,回喷煤气15的喷吹压力也应高于富氧热风喷吹压力。
[0078]
同实施例2相同的是,实施例3也选用挥发分含量约为21%的煤粉进行喷吹,喷煤量约为170kg/thm,根据热量平衡计算可得理论焦比约为306.6kg/thm,理论燃料比约为476.6kg/thm,较常规高炉略有降低。
[0079]
高炉炉内发生的主要化学反应及热量传输、炉料1和煤气的运行与实施例2一致。产生炉腹煤气量约为1379nm3/thm,炉腹煤气成分如下表3所示。
[0080]
表3炉腹煤气成分
[0081][0082]
炉腹煤气中还原气体含量约为52.4%。充足的炉腹煤气量及高还原性气体含量的
炉腹煤气可以确保高炉中上部充分发展间接还原反应,最终直接还原度约为0.432。
[0083]
喷吹煤粉用的煤载气、入炉铁矿石冶金性能要求均与实施例2一致。经过间接还原反应后,炉顶干煤气量约为1504nm3/thm,其中co2含量约为22.7%,co含量约为28.5%,h2含量约为5.0%,n2含量约为43.7%。
[0084]
实施例3与实施例2相同,其炉顶湿煤气7经除尘后,分出其中455.3nm3/thm用以加热回喷煤气15和富氧热风,其中376.1nm3/thm(占炉顶湿煤气总量的25%)煤气继续经co2脱除装置11脱除co2、n2脱除装置20脱除n2、加压装置13加压、预热装置14加热后回喷进入高炉,经脱除co2和脱除n2后回喷煤气量为126nm3/thm,剩余672.5nm3/thm炉顶煤气进入煤气管网12。
[0085]
经脱除co2、脱除n2后的回喷煤气15中co含量约为85%,h2含量约为15%,由风口组件16回喷进入高炉。如此循环,可实现9吨铁co2排放减少9%的目标,由于鼓风富氧率与常规高炉接近,实施例3并不具备强化高炉冶炼的效果。显然,相较于实施例2,实施例3只回喷25%的炉顶煤气在强化高炉冶炼和碳排放的效果进一步降低。
[0086]
综上,在本发明实施例提供的一种低碳高炉炼铁方法中,在不对传统高炉体系进行较大改动的前提下,本发明采用富氧冶炼和炉顶煤气循环工艺,大幅度提升高炉炉内碳素的利用率,并提高炉腹煤气中还原性气体的浓度,降低高炉炉缸内部直接还原度,节省燃料消耗,降低了高炉燃料比,提升了高炉炼铁效率和降低了高炉炼铁过程co2排放。
[0087]
上述实施例仅例示性说明本发明的原理及其功效,而非用于限制本发明。任何熟悉此技术的人士皆可在不违背本发明的精神及范畴下,对上述实施例进行修饰或改变。因此,举凡所属技术领域中具有通常知识者在未脱离本发明所揭示的精神与技术思想下所完成的一切等效修饰或改变,仍应由本发明的权利要求所涵盖。