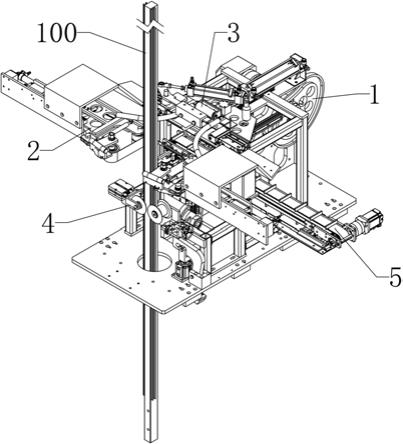
1.本发明涉及铝型材制造的技术领域,尤其是指一种用于铝材表面处理的上排系统。
背景技术:2.在铝材生产领域中,借助于上排设备将若干条铝型材按照所需间距固定于导电架上,随后将固定于导电架上的若干条铝型材进行氧化、着色、电泳、清洗等表面处理工艺,最后借助于下拍设备将若干条铝型材脱离导电架。其中,导电架主要包括大梁和竖装于大梁上的两根导电杆。目前的上排过程一般为:通过一套升降机组承托住导电架的大梁先下移,使导电杆对准预定通孔位同步下移至预定高度位置,随后升降机组承托大梁及导电杆同步逐渐上移,在上移期间,通过人工操作或借助上排设备将通过图10所示的夹钳打开,从而将铝型材逐根夹装至导电杆上。
3.目前的上排设备如专利文件n106011967a公开了一种全自动铝材氧化上下排设备,其公开了包括支架单元、 铝材上排单元、铝材下排单元和排杆输送单元;所述的铝材上排单元包括夹紧上排机构和 绑线上排机构,所述的夹紧上排机构包括上夹机头和上夹伺服升降车,所述的绑线上排机 构包括绑线机头和绑线伺服升降车;所述的铝材下排单元包括夹紧下排机构和绑线下排机 构,所述的夹紧下排机构包括下夹机头和下夹伺服升降车,所述的绑线下排机构包括下线 机头和下线伺服升降车。
4.也有如专利文件cn210593742u公开了一种上排生产线,其机头组件和牵引装置;机头组件包括基座;基座上设有用于输送铝型材的输送带、用于将位于输送带上的铝型材搭接于导电杆上的上料装置、用于打磨导电杆的打磨装置和用于控制夹钳将铝型材夹持于导电杆上的装夹装置;输送带上设有进料位和出料位;上料装置、打磨装置和装夹装置均布置于出料位的周侧;上料装置包括可相对基座翻转上料的夹持部件;打磨装置的顶部设有供导电杆插入于打磨装置内进行打磨的开口;装夹装置包括可往复运动于开口的夹装组件;牵引装置包括工作架及升降装置组。
5.综上,现有的上排设备结构相对复杂,首先对于导电杆预定位及预处理存在一定的缺陷,其次,其采用打开夹钳的开夹机构结构复杂,设计和装配难度高,无法满足厂商的需求。
技术实现要素:6.本发明的目的在于克服现有技术的不足,提供一种稳定可靠、结构设计合理的铝材表面处理的上排系统。
7.为了实现上述的目的,本发明所提供的一种用于铝材表面处理的上排系统,包括设于支架上的开夹机构、打磨机构、上定位机构和下定位机构,其中,所述开夹机构用夹钳的开夹及装夹操作;两组所述打磨机构呈对向临近布置于开夹机构的上方位置且用于对导电杆表面进行打磨抛光处理;所述上定位机构临近布置于打磨机构的上方位置且用于对导
电杆进行上定位;所述下定位机构临近布置于开夹机构的下方位置且用对于导电杆进行下定位。
8.进一步,所述开夹机构包括开夹机座、轨迹活板、开夹滑座和开夹单元,所述轨迹活板相对开夹机座可作水平滑动和/或竖向滑动,所述开夹滑座相对轨迹活板可作水平滑动;所述开夹单元包括推杆、两个开夹连板以及两个分别竖置于两开夹连板前端部的开夹针,两所述开夹连板的尾端部共同铰接于推杆前端且所述推杆固定连接在开夹滑座上。
9.进一步,所述开夹机构还包括中间活板、主水平驱动单元和主竖向驱动单元,所述中间活板与开夹机座之间配置有竖向布置的竖向滑轨;所述中间活板与轨迹活板之间配置有横向布置的横向滑轨;所述主水平驱动单元作用于轨迹活板作水平滑动;所述主竖向驱动单元作用于轨迹活板作竖向滑动。
10.进一步,所述开夹机构还包括设于轨迹活板上的开夹伸缩件和复位弹性件,所述开夹伸缩件顶触作用于开夹滑座的尾端以驱使开夹滑座向前水平滑动;所述复位弹性件作用于开夹滑座的前端以驱使开夹滑座向后水平滑动。
11.进一步,所述开夹机构还包括开度板,所述开度板相对轨迹活板可作竖向滑动,所述开度板开设有斜向布置的斜向滑孔,所述开夹滑座上设有与斜向滑孔相活动连接的开度滑轮。
12.进一步,还包括临近布置于开夹机构上方的上夹机构,所述上夹机构包括上夹输送通道和上夹输送履带,所述上夹输送通道用于承载夹钳;所述上夹输送通道开设有出夹口且所述出夹口相对位于开夹单元的上方位置;所述上夹输送履带临近布置于上夹输送通道上方,所述上夹输送履带设有若干个等间距布置的上夹拨块,随着所述上夹输送履带的定向循环动作,从而令各个上夹拨块配合上夹输送通道推送各个夹钳依次朝出夹口方向前移。
13.进一步,每组所述打磨机构包括固定板、安装板、活动板、主动轮、从动轮和活动轮,所述安装板相对固定板可作水平滑动,所述主动轮和从动轮均旋转连接至安装板上,所述活动板通过一竖轴铰接于安装板上以使活动板可相对安装板作水平摆动,所述活动轮可调式活动连接于活动板以使活动轮可相对活动板作上下摆动;所述主动轮、从动轮和活动轮依次循环绕设有砂带。
14.进一步,所述活动轮与活动板之间通过合页组件相连接,其中,所述合页组件包括调节合页和调节螺栓,所述调节合页的旋转轴呈横向延伸布置,所述调节合页的第一页片与活动板相固定连接且第二页片供活动轮相旋转连接,所述调节螺栓的端部竖向贯穿活动板后与调节合页的第二页片相顶触;通过旋拧所述调节螺栓以驱使活动轮作上下摆动。
15.进一步,所述上定位机构包括有定位底板、定位摆板、后定位轮、前定位轮和两个侧定位轮,其中,所述后定位轮固定安装于定位底板上,两所述侧定位轮分别活动设于定位底板的两侧且两所述侧定位轮均可相对定位底板作横向水平移动;所述定位摆板通过一竖轴铰接于定位底板上以使定位摆板可相对定位底板作水平摆动,所述前定位轮固定安装于定位摆板上,通过后定位轮、前定位轮和两个侧定位轮共同对导电杆的前、后、左、右四个自由度进行限位。
16.进一步,所述下定位机构包括下定位座、第一定位轮、第二定位轮和安装于下定位座上的下定位伸缩件,所述第一定位轮旋转连接于下定位座,所述下定位伸缩件的伸缩端
与第二定位轮相旋转连接,所述第一定位轮及第二定位轮的周面成型有供导电杆穿设通过的环形凹槽,通过第一定位轮和第二定位轮共同对导电杆的前、后、左、右四个自由度进行限位。
17.本发明采用上述的方案,其有益效果在于:通过开夹机构、打磨机构、上定位机构、下定位机构和上夹机构相互协作配合,完成对导电杆的定位和打磨抛光处理以及完成夹钳的装夹操作,以便于实现铝型材的上排操作,具有高效率、自动化、稳定可靠的特点。
附图说明
18.图1为上排系统的示意图。
19.图2为开夹机构和上夹机构的示意图。
20.图3为开夹机构的示意图。
21.图4为开夹机构的结构简图。
22.图5为上夹机构的示意图。
23.图6为两组磨机构的组合示意图。
24.图7为单组打磨机构的示意图。
25.图8为上定位机构的示意图。
26.图9为下定位机构的示意图。
27.图10为现有夹钳的结构示意图。
28.其中,100
‑
导电杆,1
‑
开夹机构,11
‑
开夹机座,12
‑
轨迹活板,121
‑
竖向滑孔,122
‑
横向滑孔,123
‑
开夹伸缩件,124
‑
复位弹性件,13
‑
开夹滑座,131
‑
开度滑轮,14
‑
开夹单元,141
‑
推杆,142
‑
开夹连板,143
‑
开夹针,15
‑
中间活板,16
‑
主水平驱动单元,161
‑
水平驱动凸轮,162
‑
水平驱动连杆,17
‑
主竖向驱动单元,171
‑
竖向驱动凸轮,172
‑
竖向驱动连杆,18
‑
开度板,181
‑
斜向滑孔,2
‑
打磨机构,21
‑
固定板,22
‑
安装板,23
‑
活动板,24
‑
主动轮,25
‑
从动轮,26
‑
活动轮,27
‑
合页组件,28
‑
砂带,201
‑
打磨横向驱动单元,202
‑
打磨伸缩件,3
‑
上定位机构,31
‑
定位底板,311
‑
上定位驱动单元,32
‑
定位摆板,321
‑
前定位伸缩件,33
‑
后定位轮,34
‑
侧定位轮,314
‑
侧定位伸缩件,35
‑
前定位轮,4
‑
下定位机构,41
‑
下定位座,42
‑
第一定位轮,43
‑
第二定位轮,44
‑
下定位伸缩件,5
‑
上夹机构,51
‑
上夹输送通道,52
‑
上夹输送履带,521
‑
上夹拨块。
具体实施方式
29.为了便于理解本发明,下面参照附图对本发明进行更全面地描述。附图中给出了本发明的较佳实施方式。但是,本发明可以以许多不同的形式来实现,并不限于本文所描述的实施方式。提供这些实施方式的目的是使对本发明的公开内容理解得更加透彻全面。
30.参见附图1至10所示,在本实施例中,一种用于铝材表面处理的上排系统,包括设于支架上的开夹机构1、两组打磨机构2、上定位机构3和下定位机构4,其中,开夹机构1用夹钳的开夹及装夹操作;两组打磨机构2呈对向临近布置于开夹机构1的上方位置且用于对导电杆100表面进行打磨抛光处理;上定位机构3临近布置于打磨机构2的上方位置且用于对导电杆100进行上定位;下定位机构4临近布置于开夹机构1的下方位置且用对于导电杆100进行下定位。通过上述的各个机构的相互协作从而完成对导电杆100的定位、打磨抛光操
作,以及将铝型材装夹至导电杆100上。
31.参见附图2
‑
4所示,在本实施例中,开夹机构1包括开夹机座11、轨迹活板12、开夹滑座13、中间活板15、主水平驱动单元16、主竖向驱动单元17、开夹单元14、开度板18、开夹伸缩件123和复位弹性件124,其中,中间活板15与开夹机座11之间配置有竖向布置的竖向滑轨,即,此处的竖向滑轨的轨道安装于开夹机座11上且竖向滑轨的滑块安装于中间活板15上,由此实现中间活板15可相对开夹机座11作竖向滑动;中间活板15与轨迹活板12之间配置有横向布置的横向滑轨,即,此处的横向滑轨的轨道安装于中间活板15上且横向滑轨的滑块安装于轨迹活板12上,由此实现轨迹活板12可相对中间活板15作横向滑动。其次,主水平驱动单元16作用于轨迹活板12作水平滑动;主竖向驱动单元17作用于轨迹活板12作竖向滑动。
32.具体地,主水平驱动单元16包括水平驱动连杆162和可定轴旋转的水平驱动凸轮161,其中,所述水平驱动的前端部与轨迹活板12预开有的竖向滑孔121相活动连接,所述水平驱动连杆162的尾端部与水平驱动凸轮161相活动连接;水平驱动凸轮161旋转安装于开夹机座11上。
33.具体地,主竖向驱动单元17包括竖向驱动连杆172和可定轴旋转的竖向驱动凸轮171,其中,竖向驱动连杆172的上端部与轨迹活板12预开有的横向滑孔122相活动连接,竖向驱动连杆172的下端部与竖向驱动凸轮171相活动连接;竖向驱动凸轮171旋转安装于开夹机座11上。
34.进一步,上述的水平驱动连杆162和竖向驱动连杆172均通过限位滑块安装于开夹机座11上,由此,水平驱动连杆162仅能沿前后方向水平移动,以及竖向驱动连杆172仅能沿上下方向竖向移动。另外,通过设有竖向滑孔121供水平驱动的前端部相活动连接,以及通过设有横向滑孔122供竖向驱动连杆172的上端部相滑动连接,从而使主竖向驱动单元17和主竖向驱动单元17可独立动作,也可同时动作,互不干涉。
35.因此,借助于水平驱动凸轮161及竖向驱动凸轮171的旋转动力,从而通过水平驱动连杆162和竖向驱动连杆172来分别驱使轨迹活板12作水平滑动和/或竖向滑动。
36.在本实施例中,水平驱动凸轮161与竖向驱动凸轮171之间通过同一个驱动电机带动同步旋转,即,通过同步带(可为皮带、链条等形式)依次循环绕穿驱动电机的输出轴、水平驱动凸轮161的轴端和竖向驱动凸轮171的轴端,从而实现轨迹活板12同时进行水平滑动和竖向滑动。
37.在本实施例中,本领域技术人员可根据实际生产的动作要求对应设置水平驱动凸轮161与竖向驱动凸轮171的径宽、形状等参数,以便实现轨迹活板12所需的动作轨迹,此处不作限定,可采用相衍生的技术方案。
38.在本实施例中,开夹滑座13与轨迹活板12之间配置有横向布置的横向滑轨,即,此处的横向滑轨的轨道安装于轨迹活板12上且横向滑轨的滑块安装于开夹滑座13上。其次,开夹伸缩件123和复位弹性件124设于轨迹活板12上,其中,开夹伸缩件123的伸缩端顶触作用于开夹滑座13的尾端,用于驱使开夹滑座13向前水平滑动;复位弹性件124作用于开夹滑座13的前端,用于驱使开夹滑座13向后水平滑动,具体地,当开夹伸缩件123的伸缩端向前伸出,逐渐顶触开夹滑座13向前水平滑动,同时复位弹性件124被压缩储能;而当开夹伸缩件123的伸缩端向后缩回时,复位弹性件124释放弹性动能带动开夹滑座13向后水平滑动。
由此实现了开夹滑座13相对轨迹活板12可作水平滑动。另外,开夹滑座13还可随轨迹活板12同步作竖向及水平移动。
39.进一步,上述的开夹伸缩件123优选为伸缩气缸,复位弹性件124优选为弹簧件,其中,该弹簧件的两端分别与开夹滑座13的前端和轨迹活板12相连。
40.在本实施例中,开夹单元14包括推杆141、两个开夹连板142以及两个分别竖置于两开夹连板142前端部的开夹针143,两开夹连板142的尾端部共同铰接于推杆141前端且推杆141固定连接在开夹滑座13上。两开夹针143用于插接至夹钳的开合控制位内,此时若开夹滑座13向前移动,则经推杆141及两个开夹连板142带动两开夹针143向外移动以克服夹钳的弹力将夹钳打开。反之,在夹钳的弹力作用及复位弹性件124的弹性作用力,使开夹滑座13向后移动。
41.参见附图5所示,在本实施例中,还包括临近布置于开夹机构1上方的上夹机构5,上夹机构5包括上夹输送通道51和上夹输送履带52,上夹输送通道51用于承载夹钳。上夹输送通道51开设有出夹口且所述出夹口相对位于开夹单元14的上方位置,以便于开夹单元14对输送至出夹口处的夹钳进行上夹及开夹操作。上夹输送履带52临近布置于上夹输送通道51上方,所述上夹输送履带52设有若干个等间距布置的上夹拨块521,随着所述上夹输送履带52的定向循环动作,从而令各个上夹拨块521配合上夹输送通道51推送各个夹钳依次朝出夹口方向前移,以便于实现夹钳的连续上料供应功能。
42.具体地,上夹输送履带52由电机配合传动齿轮进行驱动。
43.在本实施例中,开度板18相对轨迹活板12可作竖向滑动,其中,本实施例的开度板18与轨迹活板12之间配置有竖向滑轨,此处的竖向滑轨的导轨安装于轨迹活板12上且竖向滑轨的滑块与开度板18相连。其次,开度板18上开设有斜向布置的斜向滑孔181,开夹滑座13上设有与斜向滑孔181相活动连接的开度滑轮131,由此,利用斜向滑孔181与开度滑轮131相对滑动配合,从而借助于斜向滑孔181同时对开夹滑座13相对于轨迹活板12的前后滑动距离及推杆141的前后移动距离进行限制,进而起到限制两开夹连板142的开合角度,最终实现对两开夹针143的开度大小的控制,即,当斜向滑孔181供开度滑轮131的相对滑动距离越长,则两开夹针143的开度越大;反之,当斜向滑孔181供开度滑轮131的相对滑动距离越短,则两开夹针143的开度越小。
44.为便于对上述的开夹机构1和上夹机构5的理解,以下结合具体工作原理进行解释说明。
45.工作时,首先利用主水平驱动单元16和主竖向驱动单元17驱使开夹滑座13和轨迹活板12同步移动,从而使开夹单元14的两开夹针143对准位于上夹输送通道51的出夹口处的夹钳。随后,由主竖向驱动单元17驱使开夹滑座13和轨迹活板12同步上移,从而使开夹单元14的两开夹针143插接至夹钳的开合控制位内。紧接着,由开夹伸缩件123伸出动作驱使开夹滑座13向前滑动以使两开夹针143撑开夹钳,最后,利用主水平驱动单元16和主竖向驱动单元17驱使开夹滑座13和轨迹活板12同步移动,使夹钳移动至预定位置后,由开夹伸缩件123缩回动作及复位弹性件124的弹性作用,令两开夹针143不再顶撑夹钳,从而使夹钳闭合将铝材夹紧在导电杆100上,最终各个驱动元件复位使两开夹针143脱离夹钳便完成了单次的装夹操作。
46.通过重复上述动作以及配合上夹机构5的夹钳连续上料供应,由此实现夹钳的连
续装夹操作。
47.参见附图6和7所示,在本实施例中,两组打磨机构2位于导电杆100的左右两侧位置。每组打磨机构2包括固定板21、安装板22、活动板23、主动轮24、从动轮25和活动轮26,其中,本实施例的固定板21与安装板22之间设置有打磨横向滑轨,即,打磨横向滑轨的轨道沿左右水平方向延伸布置在固定板21上,打磨横向滑轨的滑块与安装板22相连;其次,固定板21设有用于驱使安装板22水平滑动的打磨横向驱动单元201,即,打磨横向驱动单元201优选为伸缩气缸,其伸缩端与安装板22相连接。由此,在打磨横向驱动单元201的驱使下,实现了安装板22相对固定板21可作水平滑动。
48.在本实施例中,主动轮24和从动轮25均旋转连接至安装板22上,其中,从动轮25位于安装板22的前端位置。另外。主动轮24及从动轮25的旋转轴均为竖向布置。
49.本实施例的活动板23通过一竖轴铰接于安装板22上以使活动板23可相对安装板22作水平摆动,具体地,活动板23与安装板22之间配置有打磨伸缩件202,打磨伸缩件202的尾端部铰接于安装板22上且其伸缩端与活动板23相铰接;通过调节打磨伸缩件202的伸缩动作以驱使活动轮26作水平摆动。由此,当打磨伸缩件202的伸缩端伸长时,则驱使活动板23相对于安装板22水平向外摆动;反之,当打磨伸缩件202的伸缩端伸长时,则驱使活动板23相对于安装板22水平向内摆动。
50.本实施例的活动轮26可调式活动连接于活动板23以使活动轮26可相对活动板23作上下摆动,具体地,活动轮26与活动板23之间通过合页组件27相连接,其中,合页组件27包括调节合页和调节螺栓,所述调节合页的旋转轴呈横向延伸布置,所述调节合页的第一页片与活动板23相固定连接且第二页片供活动轮26相旋转连接,所述调节螺栓的端部竖向贯穿活动板23后与调节合页的第二页片相顶触;通过旋拧所述调节螺栓以驱使活动轮26作上下摆动。由此,当旋拧调节螺栓向上移动时,则调节螺栓会顶触第二页片绕调节合页的旋转轴逐渐向上摆动,从而使活动轮26同步向上摆动;反之,当旋拧调节螺栓向下移动时,则第二页片会绕调节合页的旋转轴逐渐向下摆动,从而使活动轮26同步向下摆动。
51.另外,主动轮24、从动轮25和活动轮26依次循环绕设有砂带28,并且在安装板22上配置有驱动主动轮24进行旋转动作的打磨驱动电机,在打磨驱动电机的动力输入下,使主动轮24、从动轮25和活动轮26共同驱使砂带28进行循环转动。
52.进一步,本实施例的活动板23铰接于安装板22的前端位置,令活动轮26相对位于安装板22的前端位置,以便于活动轮26与从动轮25之间的砂带28段用于与导电杆100相打磨接触。
53.综上,通过利用合页组件27的调节功能来控制活动轮26相对于活动板23的角度大小,主要用于调整活动轮26与从动轮25之间的砂带28段的打磨角度;而利用打磨伸缩件202的伸缩功能来控制活动板23相对于安装板22之间的角度大小,主要是用于调整砂带28的张紧程度。
54.为便于对上述打磨设备的理解,以下结合具体的工作原理进行解释说明。
55.工作时,首先通过打磨横向驱动单元201调节安装板22安装的位置,令两组打磨机构2调整至适当位置,使活动轮26与从动轮25之间的砂带28段与导电杆100相接触。随后,通过调节打磨伸缩件202及调节螺栓来调整砂带28的张紧程度和打磨角度,最后在打磨驱动电机的带动使两组打磨机构2的砂带28同时对导电杆100的两侧进行打磨抛光。
56.由此,通过两组打磨机构2对导电杆100进行表面处理,打磨除去导电杆100表面的绝缘氧化层,从而使铝型材由夹钳固定在导电杆100上能够保持电接触,以便于下游工位对铝型材进行铝材氧化、电镀等表面处理工序。
57.进一步,上述的打磨伸缩件202优选为伸缩气缸。
58.参见附图8所示,在本实施例中,所述上定位机构3包括有定位底板31、定位摆板32、后定位轮33、前定位轮35和两个侧定位轮34,其中,后定位轮33固定安装于定位底板31上,具体地,后定位轮33沿左右水平方向延伸且其两端通过轴承座固定安装于定位底板31的顶面。两侧定位轮34分别活动设于定位底板31的两侧且两侧定位轮34均可相对定位底板31作横向水平移动,侧定位轮34沿前后水平方向延伸。定位底板31的两侧均设有侧定位轮314,两侧定位轮34分别连接于两侧定位轮314的伸缩端,具体地,侧定位轮314的伸缩端通过轴承座与定位轮相旋转连接,通过侧定位轮314的伸缩动作以驱使定位轮沿左右水平方向平移。定位摆板32通过一竖轴铰接于定位底板31上以使定位摆板32可相对定位底板31作水平摆动,前定位轮35固定安装于定位摆板32上,具体地,安装于定位摆板32上的前定位轮35位于后定位轮33的前方位置,并且定位底板31与定位摆板32之间配置有前定位伸缩件321,前定位伸缩件321的尾端部铰接与定位定板上且其伸缩端与定位摆动相铰接,通过调节前定位伸缩件321的伸缩动作以驱使定位摆板32作水平摆动。
59.进一步,定位底板31配置有驱动其沿前后方向移动的上定位驱动单元311,其中,上定位驱动单元311的伸缩端与定位底板31相连接,通过上定位驱动单元311的伸缩动作驱使定位底板31作前后方向水平移动,进而带动后定位轮33、前定位轮35和两个侧定位轮34同步前后水平移动。
60.进一步,为避免侧定位轮34与后定位轮33或前定位轮35发生碰撞干涉,本实施例的侧定位轮34与后定位轮33或前定位轮35布置在不同的高度位置。
61.为便于理解,以下结合上定位机构3对其工作原理作出进一步解释说明。
62.工作时,首先,由前定位伸缩件321伸长驱使定位摆板32及前定位轮35同步向外水平摆动,随后,由上定位驱动单元311伸长驱使定位底板31向前水平移动,直至前定位轮35与导电杆100相抵触;紧接着,由两组侧定位轮314伸长分别驱使两侧定位轮34相向移动以及由前定位伸缩件321缩回驱使定位摆板32及前定位轮35同步向内水平摆动,直至两侧定位轮34及前定位轮35均与导电杆100相抵触。此时的通过后定位轮33、前定位轮35和两个侧定位轮34的抵触作用,共同对导电杆100的前、后、左、右四个自由度进行限位,从而便完成了对导电杆100的上定位作用。
63.参见附图9所示,在本实施例中,下定位机构4包括下定位座41、第一定位轮42、第二定位轮43和安装于下定位座41上的下定位伸缩件44,第一定位轮42旋转连接于下定位座41上,下定位伸缩件44的伸缩端与第二定位轮43相旋转连接。第一定位轮42和第二定位轮43位于左右水平方向上。通过下定位伸缩件44的伸缩动作以带动第二定位轮43接近或远离第一定位轮42。其次,第一定位轮42及第二定位轮43的周面均成型有供导电杆100穿设通过的环形凹槽。
64.进一步,上述的上定位驱动单元311、侧定位轮314、下定位伸缩件44、前定位伸缩件321均优选为伸缩气缸。
65.为便于理解,以下结合具体的下定位机构4及其工作原理作出进一步的解释说明。
66.工作时,首先,导电杆100从第一定位轮42和第二定位轮43之间的间隙穿过且第一定位轮42的环形凹槽与导电杆100相配合,随后由下定位伸缩件44伸长驱使第二定位轮43朝第一定位轮42相向前移,从而使第一定位轮42和第二定位轮43的环形凹槽共同限制住导电杆100,便完成了导电杆100的下定位。通过第一定位轮42和第二定位轮43共同对导电杆100的前、后、左、右四个自由度进行限位。
67.在本实施例中,下定位机构4始终保持限位状态,直至导电杆100完成铝型材的上排操作,完全脱离了下定位机构4后,则下定位伸缩件44缩回复位,使第二定位轮43原理第一定位轮42,等待下一组上排操作的导电杆100到位。而上定位机构3更多的是起到预定位的效果,具体地,导电杆100在到达上排系统的预定工位时,借助于预设定的升降滑车驱使其由上至下逐渐移动,此时的上定位机构3预先动作对导电杆100进行上定位操作,经上定位机构3定位后的导电杆100能够更准确地从下定位机构4的第一定位轮42和第二定位轮43之间穿过,随后启用下定位机构4同时对导电杆100进行下定位操作。待导电杆100下降至预定的高度位置后,上定位机构3复位脱离导电杆100,仅保持下定位机构4的下定位操作,随后启用开夹机构1及上夹机构5进行夹钳的装夹。另外,在导电杆100经上定位机构3预定位后且持续下移的期间,启用打磨机构2对导电杆100的表面进行打磨抛光处理,直至导电杆100下移到位后,打磨机构2复位脱离导电杆100,有效地避免打磨机构2及上定位机构3对装夹操作发生干涉。
68.以上所述之实施例仅为本发明的较佳实施例,并非对本发明做任何形式上的限制。任何熟悉本领域的技术人员,在不脱离本发明技术方案范围情况下,利用上述揭示的技术内容对本发明技术方案作出更多可能的变动和润饰,或修改均为本发明的等效实施例。故凡未脱离本发明技术方案的内容,依据本发明之思路所做的等同等效变化,均应涵盖于本发明的保护范围内。