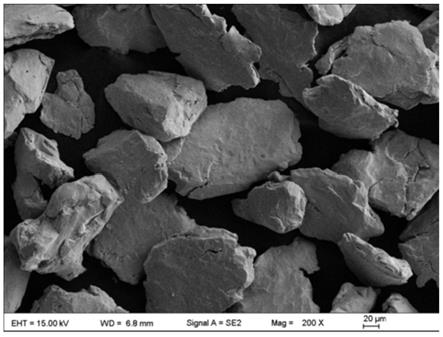
1.本发明涉及金属材料领域,尤其涉及一种基于高压氢还原法的铜包覆铬复合粉末的制备方法及其应用。
背景技术:2.自20世纪70年代铜铬触头材料被发明以来,因其同时独立保留了铜和铬优异的电性能及物理化学性质,被广泛应用于真空开关中。不同于传统的铸造合金材料,铜和铬不互溶,且密度和熔点都有较大差异,因此主要以粉末冶金方式来制备,包括混粉压制烧结法和熔渗法。混粉压制烧结法具有成分控制精确、材料浪费少、单位能耗低以及效率高的优点,然而混料的均匀性一直是工艺控制的难点之一;熔渗法制备的触头铜和铬结合强度好,抗电弧烧蚀能力强的特点,然而在熔渗过程中因铬和铜的润湿性问题,容易产生孔洞。
3.包覆粉体材料能够较好解决粉末均匀性和润湿性问题,如专利cn201410152550.5以化学镀的方式对铬粉进行了包覆铜处理,其制备方法包括:先对铬粉进行预处理,再对铬粉外表面进行化学镀铜,化学镀液由可溶性铜盐、络合剂、强碱、还原剂、亚铁氰化钾及助剂组成,在化学镀铜过程中实时监测化学镀液的酸碱度和汽包,并据此变化不断补充化学镀液中的主要成分,最后对复合粉体进行表面钝化处理,得到铜包覆铬复合粉末。这种方法的缺点是流程过长且使用了多种化学试剂,后续处理难度大。cn201610789918.8公开了一种铜包铬合金粉的制备方法,选择合格的高纯铬块制备出高纯低气且粒径为30~200微米的铬粉,将铬粉均布在用于电解铜的电解槽的阴极板上,通过电解还原法在铬粉表面均匀镀覆一层铜形成铜包铬合金粉,从阴极板上收集镀覆得到的铜包铬合金粉,进行处理后得到均匀的铜包铬合金粉。该方法的缺点在于电解车间环境恶劣,对操作的人员的职业健康有很大的危害。
4.为此,亟需开发出一种工艺简单,成本低,且对环境和操作人员友好的铜包覆铬复合粉末制备方法。
技术实现要素:5.为了解决上述技术问题,本发明提供了一种基于高压氢还原法的铜包覆铬复合粉末的制备方法及其应用。本发明基于高压氢还原法并通过进一步优化来制备铜包覆铬复合粉末,具有环境友好、产品纯度高,材料中金属元素混合均匀性以及产品性能好的优点。
6.本发明的具体技术方案为:第一方面,本发明提供了一种基于高压氢还原法的铜包覆铬复合粉末的制备方法,包括以下步骤:(1)铬粉的预处理:在惰性气氛下对铬粉和钯粉进行液相球磨处理,然后将所得铬钯混合粉进行高温干氢处理,获得表面附着纳米钯的铬粉。
7.(2)高压氢还原法制备铜包覆铬复合粉末粗品:将硫酸铜和/或硝酸铜溶液和表面
附着有钯的铬粉添加至反应器中,通氢气至0.5~5mpa并加热至140
‑
250℃进行还原反应,反应结束后冷却、过滤,得到铜包覆铬复合粉末粗品。
8.(3)后处理:对铜包覆铬复合粉末粗品进行清洗、干燥,得到铜包覆铬复合粉末成品。
9.在步骤(1)的过程中,纳米钯粉在液相球磨时,因小尺寸而容易附着在大尺寸的铬粉表面,在后续的高温干氢处理过程中,钯和铬经互扩散而紧密结合在一起并形成了烧结颈,此外,钯还有最强的吸放氢能力,能吸附700倍体积含量的氢,氢的吸收与释放有利于铬在干氢气氛下的脱氧。
10.在步骤(2)中,氢气在高压的情况下溶于溶液中,和钯一起形成钯氢,此时钯上的氢原子处于活跃状态,极易与溶液中铜离子进行还原反应,反应的方程式如下:生成的铜单质沉积于铬粉表面,得到铜包覆铬复合粉末粗品,而钯由于氢原子的损失而形成钯单质,钯单质继续与氢气形成钯氢,并以此为循环起着催化作用。其中,本发明巧妙地通过在铬粉表面引入钯而非直接在步骤(2)中添加钯的好处在于:钯附着在铬粉上面,溶液中铜离子以钯为形核核心进行沉积,从而形成铜包覆铬粉末;如果钯是单独存在于溶液中的,那铜离子将以钯为核心形成铜粉,而不是以铜包覆铬的形式存在,仍会产生两种粉末不均匀的现象。
11.经步骤(3)后处理得到铜包覆铬复合粉末,该复合粉末纯度高,材料各组成元素混合性好,性能优异。可以直接进行压制成形,无需混料,也可用于固相烧结或熔渗法制备铜铬触头。
12.作为优选,步骤(1)中,所述铬粉的粒度为100~500目。
13.作为优选,步骤(1)中,所述钯粉为纳米钯粉,粒径小于100nm,添加量为铬粉的0.05~0.2wt%。
14.作为优选,步骤(1)中,所述液相球磨时的惰性气氛为高纯氩气、氦气、氮气或氢气。
15.作为优选,步骤(1)中,所述液相球磨的介质为丙酮、乙醇、环己烷或乙二醇。
16.作为优选,步骤(1)中高温干氢处理温度为900~1200℃,时间为30~90分钟,干氢露点为
‑
70℃。
17.作为优选,步骤(2)具体包括:配制10~100g/l铜离子浓度的硫酸铜和/或硝酸铜溶液,加入氨水调节ph至7~11,形成铜氨络合溶液,再加入碳酸铵稳定反应体系的ph值,然后和表面附着纳米钯的铬粉添加至一起反应器内,先通惰性气体置换反应器内空气,然后再通氢气置换惰性气体,继续通氢气至0.5~5mpa,加热至140
‑
250℃,保温进行还原反应0.5
‑
3h,冷却、过滤,得到铜含量为15~70wt%的铜包覆铬复合粉末粗品。
18.作为优选,步骤(2)中:所述反应器内设有聚四氟乙烯内衬。
19.聚四氟乙烯材质的内衬可以防止铜沉积在反应器的金属内壁上。
20.作为优选,步骤(2)中:先通惰性气体10~60min置换反应器内空气,然后再通氢气10~60min置换惰性气体。
21.作为优选,步骤(3)具体包括:先用去离子水清洗,再用无水乙醇清洗,过滤后在40
~70℃下真空干燥30~120min。
22.第二方面,本发明提供了上述铜包覆铬复合粉末的具体应用:可将所述铜包覆铬复合粉末通过直接压制成形后经固相烧结或熔渗法制备铜铬触头。
23.与现有技术对比,本发明的有益效果是:(1)本发明在高压氢气还原处理前先将纳米钯附着于铬粉表面,然后进行高温干氢处理,在此过程中,钯和铬经互扩散而紧密结合在一起并形成了烧结颈;钯有最强的吸放氢能力,能吸附700倍体积含量的氢,氢的吸收与释放有利于铬在干氢气氛下的脱氧。
24.(2)本发明基于高压氢还原法并通过进一步优化来制备铜包覆铬复合粉末,具有环境友好、产品中金属元素混合均匀和产品性能好的优点。
25.(3)本发明的铜包覆铬复合粉末纯度高,材料各组成元素混合性好,性能优异。可以直接进行压制成形,无需混料,可用于固相烧结或熔渗法制备铜铬触头。
附图说明
26.图1为包覆前铬粉的电镜图;图2为实施例1制得的铜包覆铬复合粉末的电镜图;图3为对比例2制得的铜包覆铬复合粉末的电镜图;图4为对比例1制得的熔渗铜铬40触头金相图;图5为实施例3制得的熔渗铜铬40触头金相图;图6为实施例1制得的固相烧结法铜铬30触头金相图;图7为对比例1制得的固相烧结法铜铬30触头金相图。
具体实施方式
27.下面结合实施例对本发明作进一步的描述。
28.总实施例一种基于高压氢还原法的铜包覆铬复合粉末的制备方法,包括以下步骤:(1)铬粉的预处理:在惰性气氛下对100~500目的铬粉和粒径小于100纳米的钯粉进行液相球磨处理,其中钯添加量为铬粉的0.05~0.2wt%,液相球磨介质为丙酮、乙醇、环己烷、乙二醇,惰性气氛为高纯氩气、氦气、氮气、氢气。然后把球磨后的铬钯混合粉在露点为
‑
70℃的干氢条件下高温处理,保温温度为900~1200℃,时间为30~90分钟,获得表面附着纳米钯的铬粉。
29.(2)高压氢还原法制备铜包覆铬复合粉末粗品:配制10~100g/l铜离子浓度的硫酸铜和/或硝酸铜溶液,加入氨水调节ph至7~11,形成铜氨络合溶液,再加入碳酸铵稳定反应体系的ph值,然后和表面附着纳米钯的铬粉添加至一起设有聚四氟乙烯内衬的反应器内,先通惰性气体10~60min置换反应器内空气,然后再通氢气10~60min置换惰性气体,继续通氢气至0.5~5mpa,加热至140
‑
250℃,保温进行还原反应0.5
‑
3h,冷却、过滤,得到铜含量为15~70wt%的铜包覆铬复合粉末粗品。
30.(3)后处理:对铜包覆铬复合粉末粗品先用去离子水清洗,再用无水乙醇清洗,过滤后在40~70℃下真空干燥30~120min,得到铜包覆铬复合粉末成品。
31.可将所述铜包覆铬复合粉末通过直接压制成形后经固相烧结或熔渗法制备铜铬
触头。
32.实施例1在球磨罐内加入300克粒度为120目的铬粉和0.3克粒径小于100纳米的钯粉,继续添加丙酮作为液相球磨介质,拧上盖子后抽真空,然后加入高纯氩气作为保护气氛,球磨后取出过滤干燥,然后把球磨好的铬钯混合粉在露点为
‑
70℃的干氢条件下高温处理,保温温度为1100℃,时间为60分钟,获得表面附着纳米钯的铬粉。
33.使用去离子水配制14l铜离子浓度为50g/l的硫酸铜溶液,加入氨水调节ph至8,再加入200克碳酸铵,搅拌溶解,然后和上步骤所得到铬粉一起加入到内衬聚四氟乙烯反应容器的高压釜内,合上高压釜盖,通以氮气50min置换高压釜内空气,然后再通以氢气30min置换釜内氮气,继续通氢至2mpa,加热至200℃,保温2小时,冷却后过滤。
34.使用去离子水清洗三次上步骤所得粉末,再经无水乙醇清洗两次,过滤后在50℃真空干燥箱内干燥100min,得到铜铬30包覆型复合粉末。
35.实施例2在球磨罐内加入400克粒度为200目的铬粉和0.2克粒径小于100纳米的钯粉,继续添加环己烷作为液相球磨介质,拧上盖子后抽真空,然后加入高纯氦气作为保护气氛,球磨后取出过滤干燥,然后把球磨好的铬钯混合粉在露点为
‑
70℃的干氢条件下高温处理,保温温度为950℃,时间为85分钟,获得表面附着纳米钯的铬粉。
36.使用去离子水配制7.5l铜离子浓度为80g/l的硫酸铜溶液,加入氨水调节ph至9,再加入120克碳酸铵,搅拌溶解,然后和上步骤所得到铬粉一起加入到内衬聚四氟乙烯反应容器的高压釜内,合上高压釜盖,通以氮气30min置换高压釜内空气,然后再通以氢气60min置换釜内氮气,继续通氢至4.7mpa,加热至140℃,保温0.5小时,冷却后过滤。
37.使用去离子水清洗三次上步骤所得粉末,再经无水乙醇清洗两次,过滤后在60℃真空干燥箱内干燥60min,得到铜铬40包覆型复合粉末。
38.实施例3在球磨罐内加入500克粒度为300目的铬粉和0.8克粒径小于100纳米的钯粉,继续添加乙二醇作为液相球磨介质,拧上盖子后抽真空,然后加入高纯氢气作为保护气氛,球磨后取出过滤干燥,然后把球磨好的铬钯混合粉在露点为
‑
70℃的干氢条件下高温处理,保温温度为1200℃,时间为40分钟,获得表面附着纳米钯的铬粉。
39.使用去离子水配制25l铜离子浓度为20g/l的硝酸铜溶液,加入氨水调节ph至9.5,再加入90克碳酸铵,搅拌溶解,然后和上步骤所得到铬粉一起加入到内衬聚四氟乙烯反应容器的高压釜内,合上高压釜盖,通以氮气15min置换高压釜内空气,然后再通以氢气55min置换釜内氮气,继续通氢至0.7mpa,加热至250℃,保温3小时,冷却后过滤。
40.使用去离子水清洗三次上步骤所得粉末,再经无水乙醇清洗两次,过滤后在65℃真空干燥箱内干燥30min,得到铜铬50包覆型复合粉末。
41.对比例1与实施例1的区别仅在于,未采用高压氢还原的常规混料方法:按比例称取120目铬粉和200目电解铜粉,倒入不锈钢v型混料机中,拧上盖子抽真空,然后充入高纯氩气作为保护气氛,混料3小时后倒出,得到铜铬混合粉。
42.对比例2
与实施例1的区别仅在于,步骤(1)中不添加钯粉,改为在步骤(2)中添加:使用去离子水配制14l铜离子浓度为50g/l的硫酸铜溶液,加入氨水调节ph至8,再加入200克碳酸铵,搅拌溶解,然后和0.3公斤120目铬粉以及0.3克粒径小于100纳米的钯粉一起加入到内衬聚四氟乙烯反应容器的高压釜内,合上高压釜盖,通以氮气50min置换高压釜内空气,然后再通以氢气30min置换釜内氮气,继续通氢至2mpa,加热至200℃,保温2小时,冷却后过滤。
43.使用去离子水清洗三次上步骤所得粉末,再经无水乙醇清洗两次,过滤后在50℃真空干燥箱内干燥100min,得到铜铬30复合粉末。
44.对比例3与实施例1的区别仅在于,步骤(1)中不进行高温干氢处理:在球磨罐内加入300克粒度为120目的铬粉和0.3克粒径小于100纳米的钯粉,继续添加丙酮作为液相球磨介质,拧上盖子后抽真空,然后加入高纯氩气作为保护气氛,球磨后取出过滤干燥得到铬钯混合粉。
45.使用去离子水配制14l铜离子浓度为50g/l的硫酸铜溶液,加入氨水调节ph至8,再加入200克碳酸铵,搅拌溶解,然后和上步骤所得到铬粉一起加入到内衬聚四氟乙烯反应容器的高压釜内,合上高压釜盖,通以氮气50min置换高压釜内空气,然后再通以氢气30min置换釜内氮气,继续通氢至2mpa,加热至200℃,保温2小时,冷却后过滤。
46.使用去离子水清洗三次上步骤所得粉末,再经无水乙醇清洗两次,过滤后在50℃真空干燥箱内干燥100min,得到铜铬30复合粉末。
47.形貌检测图1为未包覆前铬粉的电镜图,可见铬粉表面光滑;图2为实施例1制得的铜包覆铬复合粉末的电镜图,可见铜粉完全包覆铬粉。图3为对比例2制得的铜包覆铬复合粉末的电镜图,可知只有较少铜粉沉积在铬粉上。
48.应用例上述实施例和对比例制备的铜包覆铬复合粉末通过固相烧结法和熔渗法制备为铜铬触头。其中:固相烧结法是把所得粉末直接装入涂有氮化铝钛涂层的硬质合金模具内进行模压成形,模压所需压力为500mpa,然后在
‑
70℃露点的氢气下烧结,保温温度为为900℃,保温2小时后,随炉冷却得到烧结法铜铬触头。
49.熔渗法是把所得复合粉末直接装入涂有氮化铝钛涂层的硬质合金模具内进行限位高度法成形(通过铬在触头中的体积含量来计算压坯体积从而得到压坯理论高度),然后在限位法成形的铜铬压坯上面放在一块无氧铜片,然后在
‑
70℃露点的氢气下熔渗,温度为1230℃,保温0.2小时后,随炉冷却得到熔渗法铜铬触头。
50.上述方法制备的各铜铬触头的性能测试数据如下表所示:序号材料成分氧含量(ppm)氮含量(ppm)富集相孔洞实施例1cucr30(烧结)2736无无实施例2cucr40(烧结)3017无无实施例3cucr50(烧结)3398无无实施例3cucr40(熔渗)2938无无对比例1cucr30(烧结)5787有无
对比例1cucr40(熔渗)6228较少有对比例2cucr30(烧结)61110有无对比例3cucr30(烧结)6089较少无由上表数据可知,实施例1
‑
3制得的铜铬触头氧含量和氮含量均较低,金相图中铜铬分布均匀,无富集相出现,且无孔洞(图5
‑
6)。而对比例1中,由于步骤(2)未采用高压氢还原,因此氧含量较高,且金相图中有富集相出现,熔渗法铜铬触头中甚至有孔洞出现(图4),而对比例1制得的固相烧结法铜铬30触头金相图中可见铜铬分布不均匀(图7)。对比例2中,由于步骤(1)中不添加钯粉,改为在步骤(2)中添加,导致其氧含量较高,且金相图中有富集相出现。对比例3中,步骤(1)中未进行高温干氢处理,同样氧含量过高,,且金相图中有少量富集相出现。由此可知本实施例制得的铜铬触头的性能显著优于各对比例。
51.本发明中所用原料、设备,若无特别说明,均为本领域的常用原料、设备;本发明中所用方法,若无特别说明,均为本领域的常规方法。
52.以上所述,仅是本发明的较佳实施例,并非对本发明作任何限制,凡是根据本发明技术实质对以上实施例所作的任何简单修改、变更以及等效变换,均仍属于本发明技术方案的保护范围。