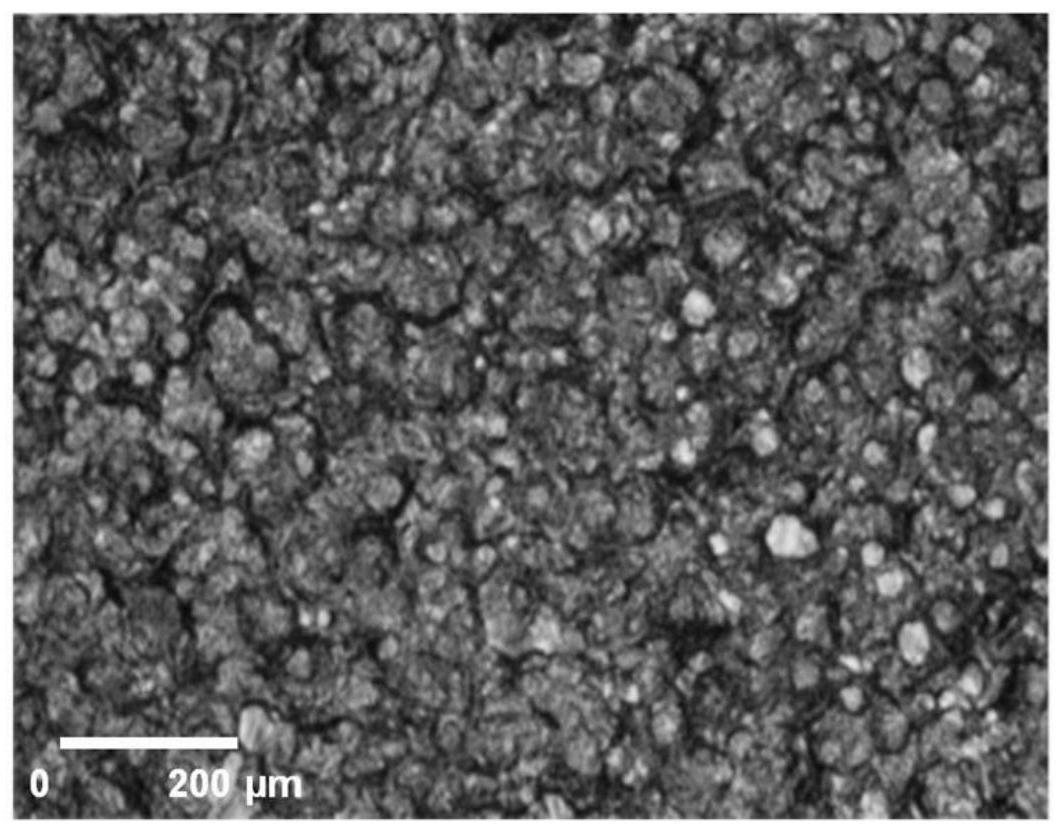
1.本发明关于一种防污膜,特别是关于一种用于薄膜沉积设备的防污膜。
背景技术:2.物理气相沉积(physical vapor deposition,pvd)技术中的溅镀沉积(sputter deposition)和蒸镀(evaporation deposition)是常见的薄膜沉积制程,两者皆常用于生产积体电路电极与扩散阻挡层薄膜、磁记录介质用磁性薄膜铟锡氧化物(indium tin oxide,ito)透明导电膜。
3.现有物理气相沉积技术通常会导致所制得的薄膜上积聚粗大颗粒。所述粗大颗粒由数个细颗粒在基板上积聚形成。所述粗大颗粒的直径可达数微米,其在大型积体电路(large scale integration,lsi)等基板上积聚会造成互连短接、断接或导致不合格产品的比例增加等问题。
4.粗大颗粒主要是由薄膜沉积设备产生,大部分源自于沉积到基板和薄膜沉积设备内壁(例如室壁)、护板和薄膜沉积设备其他部件上后又剥离的薄膜。颗粒以破碎状态四散再随机堆积于基板上,构成一种主要污染源。然而,薄膜沉积设备内壁实际上非常难以保持清洁。完全清洁内部通常需要较长时间,而且清洁工人(即清洁技术人员)有时根本无法接近薄膜沉积设备内壁和内部各部件。为减少内壁粗颗粒数量,通常需要先对最容易受污染影响的内壁表面进行物理粗糙化,例如:喷砂处理或铝熔射处理,从而整体固定或捕集沉淀物。此种方法要求对设备进行精心维护,然而对沉淀物的抗剥落效果仍然相当弱。
技术实现要素:5.有鉴于现有技术的经过粗糙化处理的薄膜沉积设备上的沉积物仍容易剥落、无法避免薄膜沉积设备的腔体内的产品污染,本发明提供一种防污膜,其具有强大抓附力,而能延长薄膜沉积制程中沉淀物自薄膜沉积设备的剥落时间,进一步使操作薄膜沉积设备进行薄膜沉积的上机时间增长且提高上机使用效率。
6.为达成前述目的,本发明提供一种防污膜,包含:一软片材,其中,所述软片材包含一金属材料;所述软片材的中心线算术平均粗糙度(arithmetic mean deviation of the assessed profile,ra)为0.1微米(μm)至6μm、面的算术平均高度(arithmetical mean height of the scale limited surface,sa)为0.1μm至6μm、界面展开面积比(面积增大程度)(developed interfacial area ratio of the scale-limited surface,sdr)为0.1至6、相对于光滑面的比例(surf(%))为160%至700%。
7.当使用本发明的防污膜时,因防污膜具有特定的ra、sa、sdr、以及surf(%)数值范围,因此可具有强大抓附力、能延长薄膜沉积制程中产生的沉淀物自薄膜沉积设备的剥落时间、进一步使薄膜沉积设备的上机时间增长,且能避免所得的薄膜沉积产品于制程中受到污染、进而提升前述产品的品质及良率,并能保护并降低设备损耗。
8.依据本发明,所述ra根据iso 4287规定的标准方法定义。较佳的,所述软片材的ra
为0.9μm至5.3μm,或为此范围中任两点所形成的范围中的任意值。更佳的,ra为1.2μm至4.8μm,再又更佳的,ra为2.0μm至3.5μm。
9.依据本发明,所述sa根据iso 25178-2:2012规定的标准方法定义。较佳的,所述软片材的sa为0.3μm至5.3μm,或为此范围中任两点所形成的范围中的任意值。更佳的,sa为1μm至5.2μm,再更佳的,sa为1.5μm至3μm。
10.依据本发明,所述sdr根据iso 25178-2:2012规定的标准方法定义。较佳的,所述软片材的sdr为0.6至5.7,或为此范围中任两点所形成的范围中的任意值。更佳的,sdr为2至6,再更佳的,sdr为2至3。
11.依据本发明,防污膜的surf(%)是经过以下公式计算而得:(sdr+1)
×
100%。较佳的,所述软片材的surf(%)为167%至668%,或为此范围中任两点所形成的范围中的任意值。更佳的,surf(%)为210%至580%。再更佳的,surf(%)为320%至450%。
12.较佳的,所述软片材的表面形成有微结构颗粒,且所述微结构颗粒的平均粒径为5μm至100μm,或为此范围中任两点所形成的范围中的任意值。更佳的,为10μm至50μm。在此粒径下,可使抓附沉积物的效果更好,而能进一步延长操作薄膜沉积设备进行薄膜沉积的上机时间、提高上机使用效率。
13.依据本发明,所述金属材料可为铜或镍,另外,所述金属材料还可使用前述金属的合金提供或构造软片材。特别值得注意的是,前述金属可基本接近100%纯度或采用合金形式。举例而言,镍可以使用纯镍金属或是镍合金。
14.依据本发明,所述金属材料可为纯金属、金属氧化物或两者的结合。软片材上可存在纯金属(例如原子量为28的镍或ni<28ni>),即纯度超过90%、95%、99%、99.9%、99.995%或更高的纯金属。基本不含杂质或污染物的纯金属适合用于对污染较敏感的溅射制程。例如,金属层包含纯度超过50%、85%或99.9%的镍箔,室温条件下以及周围环境中呈现金属光泽,银面带金色调。在一实施例中提供了一种镍纯度超过99.9%的镍箔,其表面已经氧化。氧化镍包括nio(绿色氧化镍)、ni2o3和nio2。其他金属实例包括纯铜(cu)箔卷材。
15.软片材还包含一个或多个粗糙化表面(例如无光、粗糙或磨砂表面、不均匀表面或皱褶表面)。例如,软片材氧化面即属于上述粗糙化表面的一种态样。较佳的,软片材氧化面的ra为1.0μm至50μm,更佳的是3.0μm至20μm,最好的情况是5.0μm至10.0μm。在一实施态样中,较佳的,软片材氧化面的ra为1.0μm至5μm,更佳化的情况2.0μm至4.0μm。
16.所述一个或多个粗糙化表面可包含一个电解处理表面(例如电解镍表面)、一个氧化面或者两者的组合。所述一个或多个粗糙化表面还可包含一个喷砂表面。所述一个或多个粗糙化表面还可包含一个雷射或雷射光束处理表面。
17.粗糙化表面额包含一个不均匀表面,包括细粒、褶皱、不规整、压纹、下凹部分或所述任意情况的组合。
18.在一些实施例中,不均匀表面包含凸出部分(例如压纹或压花、凸起)、下凹部分或凸出部分和下凹部分的组合。例如,凸出部分和下凹部分(即凹点、凹处、浅凹和凹槽)彼此相邻,形成具有颗粒感的不均匀表面,无论是否采用规则或不规则形式,是否直线对齐,是否具有方格斑纹。
19.软片材厚度从1μm至1mm不等。例如,软片材均匀厚度为10μm至750μm、15μm至550μm、18μm至300μm、30μm至200μm、40μm至100μm或上述任意厚度范围的组合。
20.软片材可以是一次性或可回收利用材料。例如,软片材在真空室内经过预定次数(例如10次、50次、100次和500次)的溅射后可作废弃处置。例如,软片材经过多次薄膜沉积后可进行清洁或处理(例如:以电解法翻新)。清洁或处理后的软片材经过清洁或翻修重新用于薄膜沉积。
21.防污膜可包含一种预定特性(例如形状、尺寸和边界),以便贴附到薄膜沉积设备上。例如,防污膜可以卷材形式出现。当然,防污膜可以呈长方形、正方形、环形、圆形、椭圆形或这些形状的任意组合。
22.依据本发明,本发明的防污膜可以用于薄膜沉积设备中,其中配有真空室或溅射室。薄膜沉积设备包含一个罩壳(阳极锥、挡板、基板罩和靶材罩壳),罩壳的表面一个或多个部分由防污膜遮盖。例如,真空室内壁表面部分或完全由防污膜覆盖。薄膜沉积设备还包含一个固定架(又称定位架),用于紧固薄膜生长用基板和一个或多个溅射源(例如磁控管),使带电等离子体粒子始终位于溅镀靶材表面附近。罩壳包含一个能抽真空或全密封的容器,设有一个侧壁围住固定架或更多溅射源。前述内壁表面的一个或多个部分由防污膜覆盖。
23.某些情况下,防污膜以可拆离的方式与容器内壁表面连接。其他情况,所述设备的一个或多个部分或器内壁表面包含由第一片防污膜覆盖的表面或第一个内表面,第二个表面或内表面由第二张防污膜覆盖。薄膜沉积设备部件由多个防污膜覆盖,防污膜可具有不同的轮廓、产品规格、性能指标或其他特性。需要更强污染物吸收能力的部位或表面由更高性能的防污膜覆盖或包覆。受污染物影响较小的部位或表面可重复使用、回收利用或在薄膜沉积过程中使用更少的次数。
24.依据本发明,本发明的防污膜制备方法可包含以下步骤:第一步,提供一种包含金属材料的软片材;第二步,曝置(expose)至少一部分的软片材;第三步,软片材一个或多个部分的表面进行粗糙化处理,使所述软片才得以具有特定的ra、sa、sdr、以及surf(%)数值范围;第四步,软片材至少拆离一部分。上述某些步骤可进行组合、分割或顺序调整。例如,第二步曝置软片材的一个或多个部分以及软片材一个或多个部分表面的粗糙化可通过对软片材进行一次或多次电解程序实现。所述防污膜有助于实现高效率和高品质的薄膜沉积过程,因为其可在较长的过程中甚至是较高或回圈温度条件下有效吸收或捕集游散的颗粒。
25.软片材一个或多个部分的表面粗糙化可包括利用电解进行表面处理。电解过程或电解能够提供均匀的粗糙化表面,其表面粗糙度可准确或精确调节。
26.软片材一个或多个部分的表面粗糙化可包括在软片材一个或多个部分表面形成一个或多个表面结构。一个或多个表面结构包括凹槽、凹点、压纹或其他任何可见或不可见的表面纹理。
27.前述制备方法可包括对软片材一个或多个部分表面进行氧化。所述方法还可对软片材一个或多个部分表面进行电解,从而产生一个电解表面(例如铜或镍)或电解材料(例如电解铜或电解镍)。
28.所述方法还可将一个基片贴附到软片材上。所述基片包含一基础结构、一基板、一涂层、一镀层、一层压材料层或一无害或在气相沉积过程不会向薄膜释放有害颗粒的胶黏层。所述基片提供的附加结构支援可防止防污膜剥落或回圈受热和冷却。
29.依据本发明,本发明的防污膜可依据以下步骤进行使用:第一步是提供一前述防污膜;第二步是提供一台薄膜沉积设备;第三步是以可拆离的方式将防污膜附着到(例如点焊或精密点焊)所述薄膜沉积设备的内壁上。上述某些步骤可进行组合、分割或顺序调整。利用防污膜使用方法可移除耗尽或用过的防污膜,并将新防污膜附着至前述薄膜沉积设备(例如阳极锥、收集器或颗粒收集器)壁上。用过的防污膜可回收利用(例如清洁或翻修),然后可再次用于薄膜沉积或其他过程。
30.所述方法还可利用防污膜进行薄膜沉积(例如溅射)。经过几次薄膜沉积后,用过的防污膜有时会从薄膜沉积设备内壁上移除,随后可进行处理。用过的防污膜可更换为新制、新的(即之前未用过)或经过清洁或返修的防污膜。
31.所述方法还可包括防污膜附着之前或之后对设备内壁进行处理(例如清洁)。设备壁(例如薄膜沉积设备内壁或表面)可进行粗糙化、氧化、喷砂或磨光处理,以改善防污膜附着力。
32.所述方法实施例还包括使用一前述基片或将其贴附(即固定)至所述软片材,以提供防污膜。基片有助于增强结构完整性或降低防污膜成本。例如,防污膜包含一带镍层的金属板例如不锈钢箔材。金属板和/或镍层在贴附至真空室内壁进行薄膜沉积之前还可接受其他处理(例如氧化和电解)。
33.依据本发明,本发明的防污膜可通过一个基板(例如基片)支撑靶材,且基板上的靶材(或目标)产生不规则表面。靶材和基板可采用同种材质(例如镍)。基板一个或多个表面(例如两侧的两个表面)可以是不规则或不均匀表面。前述基板可采用柔韧或柔软材质,以便附到一个或多个不平表面或部位(例如机器或其他适用部分)。
34.依据本发明,本发明的防污膜可依据以下步骤生产:第一步是将基板固定到固定架(即定位器)上;第二步是将靶材放到一个或多个喷射器(例如磁控管)上;第三步是排空环绕固定架的腔室;第四步是向腔室内充入惰性气体(例如氩气);第五步是将一个或多个喷射器通电产生磁流。上述方法中某些步骤可进行组合、分割或顺序调整。
35.依据本发明,本发明的防污膜生产方法可借由如下步骤:第一步是处理基板(例如镍箔)表面;第二部是将基板浸入电解液(例如包含硫酸镍和硫酸铵);第三步是在另一种电解液(例如硫酸镍、硼酸和氯化镍)中处理基板新形成表面;第四步是将经电解处理后的基板放入烘箱烘干。上述方法中某些步骤可进行组合、分割或顺序调整。
36.依据本发明,本发明的防污膜生产方法可借由如下步骤:第一步是将基板附到固定架上;第二步是将靶材(例如镍靶)加热至其沸点(即2730℃);第三步是将靶材蒸发到固定架(即定位器)上的基板上。上述方法中某些步骤可进行组合、分割或顺序调整。
37.依据本发明,本发明的防污膜生产方法可借由如下步骤:第一步是将基板(例如镍箔)放到卡盘上的多孔金属上;第二步是将主箔材放到基板上方;第三步是将聚酰亚胺箔材放到主箔材上方;第四步是抽真空;第五步是将雷射投射到基板或主箔材上,或者两者同时照射。上述方法中某些步骤可进行组合、分割或顺序调整。多个基板可垂直排列,各基板之间设置一个分隔物(例如纸张等非金属材料)。上述方法中某些步骤可进行组合、分割或顺序调整。基板可放到相关部件上存放。所述方法还可利用机械方式(例如末端执行器抓取或真空吸取)输送基板。
38.依据本发明,本发明的防污膜可为金属箔的软片材。金属箔的厚度约为0.1毫米,
金属箔的一表面经过粗糙处理。金属箔的材料包括镍(ni)或镍合金,例如:坡莫合金、镍铬恒弹性钢、殷钢、镍铁、镍铸铁、镍黄铜、镍青铜以及与铜、铬、铝、铅、钴、银和金的合金(例如因科镍合金、因科镍铬不锈钢、蒙乃尔合金和镍铬钛合金)。粗糙表面可进行电解而形成。金属箔在电解侧或表面可包含凸起或凸出部分。凸起可包含肉眼无法辨识的细粒(看到的只是无光泽面)。金属箔一个或多个部分可进行氧化。金属箔可与薄膜沉积设备部件(例如颗粒收集器)分离(例如不可分割片)进行处置;因此,金属箔是一种可处置箔材。且金属箔的ra为0.1μm至6μm、sa为0.1μm至6μm、sdr为0.1至6、surf(%)为160%至700%。
39.依据本发明,本发明的防污膜可用于配备一个或多个颗粒收集器的溅射沉积设备。至少有一个颗粒收集器连接电源阳极;颗粒收集器可以是圆锥形或方便安装设备部件的任何形状。
40.依据本发明,本发明的防污膜应用方法可为:第一步是提供一种金属材料(铜或镍)的软片材;第二步是将金属材料的软片材附到薄膜沉积设备部件上,在薄膜沉积过程中捕集散射粒子。金属材料的软片材附到薄膜沉积设备部件上时可将金属材料的软片材焊接(例如精密点焊)至薄膜沉积设备部件。或可在将金属材料附到薄膜沉积设备(例如溅射沉积设备)零件之前对金属材料进行电解。或可在金属材料的软片材附到薄膜沉积设备部件上之前对金属材料的软片材进行粗糙化处理。所述方法还可在将金属材料的软片材附到薄膜沉积设备部件上之前对金属材料进行压纹处理。
41.所述一种或多种箔材可包括一种或多种镍箔,其能用于铜和非铜薄膜沉积设备和溅射制程。薄膜沉积溅射过程中利用镍箔覆盖或制作的颗粒收集器很容易捕捉散射粒子。镍箔覆盖颗粒收集器,形成用于非铜薄膜沉积的镍颗粒收集器。镍颗粒收集器的颗粒吸收能力更强,在薄膜沉积过程中持续时间更长。所述一种或多种镍箔上有圆形凸纹,方便所述一种或多种镍箔表面区域的扩展,可用于非铜薄膜沉积过程。镍箔表面吸收能力强于铜箔,因此能在薄膜沉积过程中捕集更多颗粒。镍箔还能承受高温。例如,镍的熔点是1455℃,比铜的熔点高出370℃。此外,镍材料的热膨胀率也小于铜材料。镍箔最高工作温度通常为600℃左右,比铜箔高出200℃。
42.薄膜沉积用镍箔的颗粒吸收能力更强,更加耐用,且在薄膜沉积过程中寿命更长。镍箔特别适合非铜薄膜沉积过程。由于镍箔性能出色,薄膜沉积采用镍箔能够开发出先进的半导体制造制程。
43.依据本发明,本发明的防污膜可包括:一种经处理的电解镍箔、一种经过表面处理的电解镍箔,所述电解镍箔涂覆有与通过在衬底上气相生长而作为薄膜沉积的材料相同或者无害的材料、一种皱褶金属箔或带有许多不规则体(即凹坑和压纹)的金属箔。
44.依据本发明,本发明的防污膜可用于薄膜沉积设备防止设备内部装置污染以及沉积薄膜中形成颗粒,且防污膜可包括:(1)电解镍箔或通过镍箔无光面镀镍形成镍或/和氧化镍细粒薄层的镍箔;(2)一种镍箔或电解镍箔,其通过箔材无光面镀镍形成镍或/和氧化镍细粒薄层,镀层材料与将要通过基板气相生长制成的沉淀薄膜的材料相同或对其无害且与其相似;(3)一种皱褶镍箔;(4)通过压纹处理产生若干不规则体的镍箔。依据本发明,本发明的防污膜还可用于薄膜气相沉积设备的防污方法,其从上述(1)~(4)范围内选择。
45.依据本发明,本发明的防污膜可用于基于气相生长的薄膜沉积系统或装置。系统采用适当的防污方法。防污方法包括一种经处理的电解镍箔,上有镍、氧化镍或镍与氧化镍
混合物的细粒,通过电解镍箔无光面大量凸起部位的镀镍实现沉淀。可避免、减少或减轻系统内装置的污染以及沉积薄膜中颗粒的形成。经处理的电解镍箔(即箔材)其中一侧可以有细粒,用于捕集气相生长过程中散逸的颗粒。箔材可以是一种可处理的电解镍箔,系统可以是一种溅射系统。
46.依据本发明,本发明的的防污膜可用于一种防污方法。所述防污方法包括一种经处理的电解镍箔,其上有镍、氧化镍或镍与氧化镍混合物的细粒,通过电解镍箔无光面大量凸起部位的镀镍实现沉淀。箔材镀层材料与将要通过基板(例如硅片)气相生长制成的沉淀薄膜的材料相同或对其无害且与其相似,从而防止系统内部装置污染以及沉积薄膜中形成颗粒。箔材其中一侧可以有细粒,用于捕集气相生长过程中散逸的颗粒。
47.镍箔可以有镍、氧化镍或镍和氧化镍的细粒,其通过镀镍沉淀在镍箔表面,可以使用或不使用基于气相生长或基板的材料与待制成沉淀薄膜的材料相同或对其无害且与其相似的镀层。防污材料可通过点焊连接系统(例如溅射系统)内部一种或多种装置,从而将其覆盖。
48.本发明另提供一种防污膜的用途,其用于增长一薄膜沉积设备进行一薄膜沉积制程的上机时间,其中,所述防污膜是前述的防污膜。
49.较佳的,所述薄膜沉积制程为制备有机发光二极体(organic light-emitting diode,oled)的电洞注入层(hole injection layer,hil)的制程。
50.依据本发明,所述防污膜附着于所述薄膜沉积设备的内壁表面上。
51.较佳的,所述防污膜以点焊的方式附着于所述薄膜沉积设备的表面上。由于焊点之间产生缓冲空间,镀层厚植后,防污膜能膨起以缓冲应力,不会导致镀层破裂剥落。
52.本发明的优点在于,利用同时具有特定ra、sa、sdr、surf(%)数值范围的软片材作为薄膜沉积制程中使用于薄膜沉积设备的防污膜,能具有强大抓附力,且优于先前技术的喷砂处理或铝熔射处理而能延长薄膜沉积制程中产生的沉淀物自薄膜沉积设备的剥落时间,进一步使操作薄膜沉积设备进行薄膜沉积的上机时间增长、提高上机使用效率。此外,能避免所得的薄膜沉积产品于制程中受到污染、进而提高前述产品的品质及良率,并能保护并降低设备损耗。
附图说明
53.图1a为实施例5的防污膜的表面微结构显微放大图;
54.图1b为比较例7的表面微结构显微放大图;
55.图1c为比较例10的表面微结构显微放大图。
具体实施方式
56.本发明将由下列的实施例做为进一步说明,这些实施例并不限制本发明前面所揭示的内容。熟习本发明的技艺者,可以做些许的改良与修饰,但不脱离本发明的范畴。
57.制备例
58.第一步,提供一纯铜的软片材;第二步,进行电解以曝置至少一部分的软片材;第三步,对经曝置的软片材一个或多个部分的表面进行电解程序以使所述表面进行粗糙化处理;第四步,拆离未经曝置及粗糙化处理的一部分软片材,而得到制备例1至9、比较例1至5
的防污膜。
59.制备例1至4、比较例1至5的防污膜的ra、sa、sdr、surf(%)依据iso 4287标准方法、iso 25178-2:2012标准方法,以keyence vk光学显微镜量测并计算后而得,其中,防污膜的surf(%)是经过以下公式计算而得:(sdr+1)
×
100%。结果分别如表1所示。此外,表1中更进一步列出比较例6至11的ra、sa、sdr、surf(%)分析结果;其中,比较例6至8为于薄膜沉积设备内壁表面进行如习知技术的喷砂处理;以及,比较例9至11为于薄膜沉积设备内壁表面进行如习知技术的铝熔射处理。
60.表1实施例1至4及比较例1至11的ra、sa、sdr、surf(%)
61.[0062][0063]
测试例
[0064]
分别将实施例1至4的防污膜及比较例1至5的防污膜分别点焊于薄层沉积设备的内壁及表面,并用于有机发光二极体中的电洞注入层制备过程,另将薄层沉积设备的内壁及表面进行粗糙化处理后的比较例6至11进行oled的hil制备,测试沉积到薄层沉积设备的内壁的沉积物的剥落时间,并以最长未发生剥落的时间界定出各实施例或比较例的上机时间,测试结果如表2所示。
[0065]
表2实施例1至9及比较例1至11用于oled的hil制备的沉积物的剥落时间
[0066]
[0067][0068]
从表2结果可知,实施例1至9的上机时间均高于比较例1至11的上机时间,其中,实施例以实施例5的上机时间148小时为最高。比较例1至5、8至11因为ra、sa、sdr、surf(%)数值没有同时落入本发明所界定的范围,因此无法具有强力的沉积物抓附效果,最高上机时间顶多为61小时,比较例6、7虽有较接近实施例的上机时间(最高可达到如比较例7的72小时),然比较例6、7直接于薄膜沉积设备内壁进行喷砂处理所得的粗糙化表面,所述粗糙化表面产生的微结构粒径尺寸分布广且较不均匀,且微结构颗粒的平均粒径较大,因此仍然无法具有足够好的抓附效果。进一步将本发明的防污膜、习知技术的喷砂处理、习知技术的铝熔射处理各选取一例于keyence vk光学显微镜观察下观察,结果如图1a、1b、1c所示,本发明实施例5的防污膜与比较例7、比较例10的表面微结构请分别见图1a、1b、1c,可得出实施例5的表面微结构颗粒约的平均粒径为10μm至50μm、比较例7的表面微结构颗粒约的平均粒径为200μm至300μm,而比较例10的表面微结构颗粒的平均粒径约为200μm至400μm,比较例7与比较例10的表面微结构颗粒的平均粒径皆远大于实施例5。此外,可看出比较例7与比较例10的表面微结构颗粒的大小与图1a的实施例5相比显得较不规则。
[0069]
另外,比较例1至5虽亦为粗糙化的软片材,然比较例1因为sa、surf(%)的值低于本发明界定的范围内,而上机时间较短,比较例2因为surf(%)的值低于本发明界定的范围,而上机时间较短。比较例3防污膜虽然sdr、surf(%)的值高于本发明所界定的数值范围、比较例4、5的防污膜的ra、sa、sdr、surf(%)的值虽均高于本发明所界定的数值范围,却仍无法达到87小时以上的上机时间,而仅有50至61小时的上机时间,远低于实施例1至9的本发明防污膜的上机时间87至148小时。因此证明本发明的防污膜因同时具有特定数值范围的ra、sa、sdr、surf(%)而有强大抓附力,能延长薄膜沉积制程中沉淀物自薄膜沉积设备的剥落时间,进一步使操作薄膜沉积设备进行薄膜沉积的上机时间增长。
[0070]
喷砂处理的比较例6至8中,而比较例8虽然ra高于本发明界定的范围,上机时间仍
低于本发明实施例的上机时间。比较例6、7虽然落在本发明所界定的ra、sa、sdr、surf(%)的数值范围,然从图1b得知,喷砂处理的表面微结构的颗粒较不规则、不均匀,其表面微结构颗粒的平均粒径为200μm至300μm,远大于实施例5的10μm至50μm,因此其抓附力相较于本发明防污膜的均匀分布的较小颗粒状的表面仍较弱。
[0071]
铝熔射处理的比较例9至10中,虽ra、sa、sdr、surf(%)的数值范围均高于本发明所界定的范围,然上机时间仍低于本发明实施例的上机时间。而比较例9至10中,最长上机时间仅为61小时。并可从图1c得知铝熔射处理的表面微结构的颗粒较不均匀,其表面微结构颗粒的平均粒径为200μm至400μm,远大于实施例5的10μm至50μm,因此抓附力相较于本发明防污膜的均匀颗粒状且颗粒较小的表面要来的弱。
[0072]
另外,进一步将实施例1至9及比较例1至11用于oled的hil制备的沉积物的剥落时间测试结果,以上机时间最长的比较例7为基准(100%),换算实施例1至4及比较例1至11的上机使用效率,并将计算结果纪录如下表3。举例而言,表2中的实施例1的上机时间为87小时,比较例7的上机时间为72小时,因此,实施例1的上机使用效率为87与72的比值,以百分比表示为120.8%。
[0073]
表3实施例1至9及比较例1至11用于oled的hil制备的上机使用效率
[0074][0075][0076]
从表3结果可知,实施例1至9的上机使用效率均高于120%,介于120.8%至205.6%。也就是相较于比较例的最佳组别,实施例的上机使用效率至少均高出20%,而最佳的实施例5的上机使用效率更是比较例的最佳组别的200%以上。因此证实本发明的防污膜确实能延长上机时间、且大幅提高上使用效率。
[0077]
综上,本发明的防污膜因ra、sa、sdr、surf(%)的值具有特定范围,因此可具有优
于习知技术的喷砂处理或铝熔射处理后所得的粗糙化表面,从而能延长薄膜沉积制程中沉淀物自薄膜沉积设备的剥落时间,进一步使操作薄膜沉积设备进行薄膜沉积的上机时间增长,有更佳的上机使用效率。此外,能避免所得的薄膜沉积产品于制程中受到污染、进而提高前述产品的品质及良率,并能保护并降低设备损耗。
[0078]
以上所述仅是为方便说明本发明的较佳实施例,并非用于限定本发明的范围,本发明所主张的权利范围自应以申请专利范围所述为主。
[0079]
根据本发明可作的不同修正及变化对于熟悉该项技术者而言均显然不会偏离本发明的范围与精神。虽然本发明已叙述特定的较佳具体事实,必须了解的是本发明不应被不当地限制于该多个特定具体事实上。事实上,在实施本发明的已述模式方面,对于熟习该项技术者而言显而易知的不同修正亦被涵盖于下列申请专利范围之内。