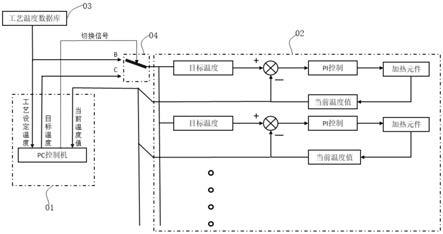
1.本发明属于热成型领域,具体涉及一种热成型炉温度控制方法。
背景技术:2.热成型炉用于加热钢坯,是热轧生产的重要工序,其由前至后设有多个温控段;根据工艺要求,使得各温控段的温度维持在一定误差范围内,以便钢坯在热成型炉中输送棍的输送下能稳定加热,完成热冲前钢坯的加热要求。但是一旦热成型炉需要进入非生产阶段(临时停工、检修)或者重新投入生产时,需要降低或者升高钢坯加热炉的温度。而热成型炉内部的输送棍在快速降温或快速升温过程中,极易发生断裂,造成不必要的损失。因此,在升温或降温过程中,需要人员不断根据热成型炉的当前温度设置目标温度,使热成型炉缓慢降温或缓慢升温,整个过程至少需要耗时8小时,极大地增加了人员的劳动强度。
技术实现要素:3.鉴于以上所述现有技术的缺点,本发明设计的目的在于提供一种热成型炉温度控制方法,可以根据热成型炉的当前温度自动给出下一次需达到的目标温度,自动实现热成型炉温度的缓慢上升或缓慢下降,极大地降低了人员的劳动强度,避免因人员设定目标温度过高或过低导致的断棍情况。
4.为实现上述目的及其他相关目的,本发明提供一种热成型炉温度控制方法,其采用热成型炉温度控制系统进行控制,所述热成型炉温度控制系统包括第一控制器、第二控制器、工艺温度数据库和模式开关;所述模式开关用于切换第二控制器与第一控制器或工艺温度数据库连接;所述热成型炉具有至少一个温控段,所述第二控制器包括与温控段一一对应的温控单元;每个温控单元均包括温度调节模块、温度传感器和加热元件;所述工艺温度数据库包含不同零件在各个温控段的工艺设定温度;所述热成型炉温度控制方法包括以下步骤:
5.当模式开关收到升温信号时,模式开关切换第二控制器与第一控制器连接,使热成型炉进入阶梯升温模式;
6.所述第一控制器接收工艺温度数据库传来的当前零件在各个温控段的工艺设定温度,并根据各个温控段的工艺设定温度,调出预先设置的各个温控段的温度参数集;所述温度参数集包括温度节点参数集和温度节点维持时间参数集,所述温度节点参数集包括依次递增的温度节点t1、温度节点t2、温度节点t3……
温度节点t
n
;所述温度节点t
n
等于对应温控段的工艺设定温度;所述温度节点维持时间参数集包括与各个温度节点一一对应的温度节点维持时间t1、温度节点维持时间t2、温度节点维持时间t3
……
温度节点维持时间tn;
7.温度传感器实时采集各个温控段的当前温度值t,并将采集的当前温度值t传输给第一控制器和第二控制器对应的温控单元;
8.第一控制器根据获取的各个温控段的当前温度值t,在对应温控段的温度节点参数集中顺序寻找第一目标温度t
a
,并确定第一目标温度维持时间t
a
;然后将第一目标温度t
a
和第一目标温度维持时间t
a
发送给第二控制器中对应的温控单元,以对加热元件的参数进行调节,使热成型炉内对应温控段升温,直至对应温控段的当前温度值t达到第一目标温度t
a
,并保持第一目标温度维持时间t
a
时间;循环此步骤,直至各温控段的当前温度值t达到对应温控段的温度节点t
n
;所述第一目标温度t
a
为对应温度节点参数集中所有大于当前温度值t的各温度节点中的最小温度节点,第一目标温度维持时间t
a
为该最小温度节点对应的温度节点维持时间。
9.于本发明的一实施例中,所述热成型炉温度控制方法还包括:当所有温控段的当前温度值t均达到对应温控段的温度节点t
n
时,模式开关切换第二控制器与工艺温度数据库连接,使热成型炉进入高温保温模式;工艺温度数据库将当前零件在各个温控段的工艺设定温度分别发送给第二控制器中对应的温控单元,以对各加热元件参数进行调节,使热成型炉各温控段的温度维持在对应的工艺设定温度。
10.于本发明的一实施例中,所述热成型炉温度控制方法还包括:
11.当模式开关收到降温信号时,切换第二控制器与第一控制器连接,使热成型炉进入阶梯降温模式;
12.第一控制器根据获取的各个温控段的当前温度值t,在对应温控段的温度设定参数集中逆序寻找第二目标温度t
b
,并确定第二目标温度维持时间t
b
;然后,第一控制器将第二目标温度t
b
和第二目标温度维持时间t
b
发送给对应的温控单元,以控制加热元件的参数,使热成型炉内对应温控段降温,直至对应温控段的当前温度值t达到第二目标温度t
b
,并在第二目标温度t
b
处维持t
b
时间;循环此步骤,直至各温控段的当前温度值t达到对应温控段的温度节点t1;所述第二目标温度t
b
为对应温度节点参数集中所有小于当前温度值t的各温度节点中的最大温度节点,第二目标温度维持时间t
b
为该最大温度节点对应的温度节点维持时间。
13.于本发明的一实施例中,所述温度调节模块为pi温度调节模块。
14.于本发明的一实施例中,所述第一控制单元为pc控制机。
15.于本发明的一实施例中,所述温度节点t1为环境温度或者用户设定的初始温度。
16.于本发明的一实施例中,所述温度节点t1与温度节点t
n
之间各温度节点由实验获取。
17.如上所述,本发明的热成型炉温度控制方法,具有以下有益效果:
18.当第一控制器接收到升温信号或降温信号时,模式开关自动切换第二控制器与第一控制器连接,使第一控制器根据热成型炉各温控段的工艺设定温度,调用出预先设置的各温控段的温度参数集;然后第一控制器实时根据各温控段的当前温度自动在对应的温度参数集中寻找目标温度和目标温度维持时间,并将其发送给第二控制器中对应的温控单元采用pi控制方式完成各温控段的升温或降温,直至各温控段的当前温度符合要求,实现热成型的阶梯式升温或阶梯式降温,避免输送棍内外温差太大造成的断辊问题;由于本发明能自动根据各温控段的当前温度,实现目标温度的实时设定,极大地降低了人员的劳动强度;此外,本发明的控制系统是在现有热成型炉控制系统(即第二控制器)的基础上增设第一控制器和模式开关获得,改造成本较低,便于推广应用。
附图说明
19.图1为本发明中热成型炉温度控制系统的原理图;
20.图2为本发明中热成型炉升温的方法流程图;
21.图3为本发明中热成型炉高温保温的方法流程图;
22.图4为本发明中热成型炉降温的方法流程图;
23.附图标记说明
24.第一控制器01,第二控制器02,工艺温度数据库03,模式开关04。
具体实施方式
25.以下通过特定的具体实例说明本发明的实施方式,本领域技术人员可由本说明书所揭露的内容轻易地了解本发明的其他优点与功效。本发明还可以通过另外不同的具体实施方式加以实施或应用,本说明书中的各项细节也可以基于不同观点与应用,在没有背离本发明的精神下进行各种修饰或改变。需说明的是,在不冲突的情况下,以下实施例及实施例中的特征可以相互组合。
26.需要说明的是,以下实施例中所提供的图示仅以示意方式说明本发明的基本构想,遂图式中仅显示与本发明中有关的组件而非按照实际实施时的组件数目、形状及尺寸绘制,其实际实施时各组件的型态、数量及比例可为一种随意的改变,且其组件布局型态也可能更为复杂。
27.本发明提供一种热成型炉温度控制系统,用于控制热成型炉的温度。
28.如图1所示,热成型炉温度控制系统包括第一控制器01、第二控制器02、工艺温度数据库03和模式开关04;第一控制器01与工艺温度数据库03连接;模式开关04用于切换第二控制器02与第一控制器01或工艺温度数据库03连接,以通过第一控制器01或工艺温度数据库03自动向第二控制器02输送目标温度;所述热成型炉具有至少一个温控段,第二控制器02包括与温控段一一对应的温控单元;每个温控单元均包括温度调节模块、温度传感器和加热元件,温度传感器实时采集对应温控段的当前温度值t,温度调节模块根据对应温控段的目标温度与当前温度值t的差值调节对应加热元件的参数,达到控制对应温控段温度的目的;所述工艺温度数据库03包括不同零件在各个温控段的工艺设定温度以将当前零件在各温控段的工艺设定温度输送给第一控制器01或第二控制器02。
29.可以理解的是,第一控制器为pc控制机等具有输入端和显示端的控制设备,对此不作限定,本实施例优选选用pc控制机。
30.可以理解的是,温度调节模块为pi控制模块、pid控制模块、模糊pid控制模块等各种纠正系统相应的控制模块,对此不作限定,本实施例优选选用pi控制模块。
31.由于本发明的热成型炉温度控制系统,是在热成型炉原本的控制系统上增设第一控制器01和模式开关03,通过切换热成型炉的温度模式,切换目标温度的来源,以自动输出目标温度设定值实现热成型炉温度的自动控制,以满足热成型炉自动缓慢降温或缓慢升温的要求,极大地降低了人员的劳动强度。
32.如图2至图4所示,采用上述热成型炉温度控制系统的温度控制方法包括三种运行模式,分别为阶梯升温模式、高温保温模式和阶梯降温模式。
33.热成型炉需要复工时,只需通过第一控制器01输入升温信号,并将该升温信号发
送给模式开关03,使模式开关03自动切换第二控制器02与第一控制器01连接,使热成型炉进入阶梯升温模式;如图2所示,其展示了阶梯升温模式下热成型炉的温度控制方法:
34.第一控制器01接收工艺温度数据库03传来的当前零件在各个温控段的工艺设定温度,并根据各个温控段的工艺设定温度,调出预先设置的各个温控段的温度参数集;所述温度参数集包括温度节点参数集和温度节点维持时间参数集,所述温度节点参数集包括依次递增的温度节点t1、温度节点t2、温度节点t3……
温度节点t
n
;所述温度节点t
n
为对应温控段的工艺设定温度;温度节点t1为用户设定的初始温度或者环境温度;所述温度节点维持时间参数集包括与各个温度节点一一对应的温度节点维持时间t1、温度节点维持时间t2、温度节点维持时间t3
……
温度节点维持时间tn;
35.温度传感器实时采集各个温控段的当前温度值t,并将采集的当前温度值t传输给第一控制器01和第二控制器02对应的温控单元;
36.第一控制器01根据获取的各个温控段的当前温度值t,在对应温控段的温度节点参数集中顺序寻找第一目标温度t
a
,并确定第一目标温度维持时间t
a
;然后将第一目标温度t
a
和第一目标温度维持时间t
a
发送给第二控制器中对应的温控单元,以对加热元件的参数进行调节,使热成型炉内对应温控段升温,直至对应温控段的当前温度值t达到第一目标温度t
a
,并在第一目标温度t
a
处维持t
a
时间;循环此步骤,不断获取新的第一目标温度t
a
和第一目标温度维持时间t
a
,直至各温控段的当前温度值t达到对应温控段的温度节点t
n
;所述第一目标温度t
a
为对应温度节点参数集中所有大于当前温度值t的各温度节点中的最小温度节点,第一目标温度维持时间t
a
为该最小温度节点对应的温度节点维持时间。
37.如图3所示,当所有温控段的当前温度值t均达到对应温控段的温度节点t
n
时,模式开关04自动切换第二控制器02与工艺温度数据库03连接,使热成型炉进入高温保温模式(即正常工作模式);
38.工艺温度数据库03将当前零件在各个温控段的工艺设定温度分别发送给第二控制器02中对应的温控单元,以对各加热元件参数进行调节,使热成型炉各温控段的温度维持在对应的工艺设定温度。
39.热成型炉需要停工时,只需通过第一控制器01输入降温信号,并将该降温信号发送给模式开关03,使模式开关03自动切换第二控制器02与第一控制器01连接,使热成型炉进入阶梯降温模式;如图4所示,其展示了阶梯降温模式下热成型炉的温度控制方法:
40.第一控制器01根据获取的各个温控段的当前温度值t,在对应温控段的温度设定参数集中逆序寻找第二目标温度t
b
,并确定第二目标温度维持时间t
b
;然后,第一控制器将第二目标温度t
b
和第二目标温度维持时间t
b
发送给对应的温控单元,以控制加热元件的参数,使热成型炉内对应温控段降温,直至对应温控段的当前温度值t达到第二目标温度t
b
,并在第二目标温度t
b
处维持t
b
时间;循环此步骤,不断获取新的第二目标温度t
b
和第二目标温度维持时间t
b
,直至各温控段的当前温度值t达到对应温控段的温度节点t1;所述第二目标温度t
b
为对应温度节点参数集中所有小于当前温度值t的各温度节点中的最大温度节点,第二目标温度维持时间t
b
为该最大温度节点对应的温度节点维持时间。
41.进一步地,各温度节点及对应的温度节点维持时间由实验获取,避免因人工经验确定的相邻两个温度节点的温度差过大,使得输送棍断裂。
42.综上所述,本发明的热成型炉温度控制方法,在升降温模式下,能通过第一控制器
自动给出各个目标温度参数,使得热成型炉温度呈阶梯式缓慢上升或缓慢下降,避免因热成型炉升温过快或降温过快,导致输送棍内外温差加大,从而断裂的问题;同时降低人员的劳动强度,避免人员因失误造成目标温度参数设置过低导致输送棍断裂;此外,本发明高温保温模式由原本热成型炉的控制系统进行控制,有效降低整个控制系统的能耗。
43.综上所述,本发明有效克服了现有技术中的种种缺点并具有高度产业利用价值。
44.上述实施例仅例示性说明本发明的原理及其功效,而非用于限制本发明。任何熟悉此技术的人士皆可在不违背本发明的精神及范畴下,对上述实施例进行修饰或改变。因此,举凡所属技术领域中具有通常知识者在未脱离本发明所揭示的精神与技术思想下所完成的一切等效修饰或改变,仍应由本发明的权利要求所涵盖。