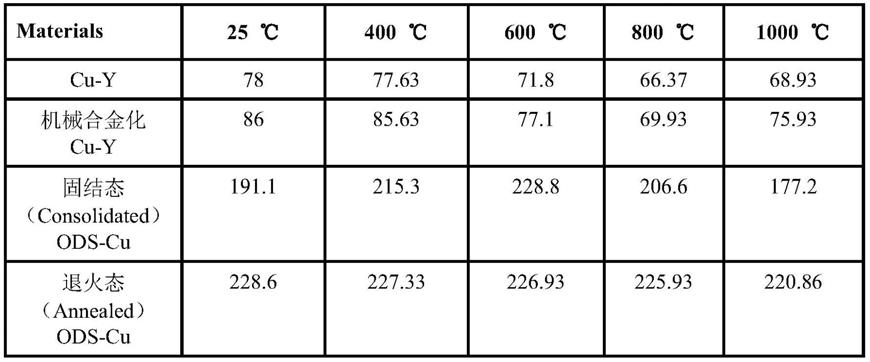
1.本发明属于金属材料加工相关技术领域,更具体地,涉及一种共格纳米氧化物弥散强化铜合金及其制备方法与应用。
背景技术:2.随着现代科技和工业的空前发展,人们对具有优良力学性能和导热性能的先进工程材料的需求越来越大。在有色金属合金中,纯铜是除银以外导电、导热性能最好的金属材料,但其力学性能较低,难以满足工程零件的性能要求。然而,铜基合金可以应用于工业领域,特别是作为火力发电厂的换热器、航空航天飞行器的机身或者壳体等。在传统工艺(如铸造)中,低体积凝固速度会导致组织(枝晶、柱状晶和偏析)的变化。这种微观结构的变化是不可取的,因为它会导致铸造样品的性能发生变化,从而对性能产生不利影响。然而,机械合金化(ma)可以引起多种固体化学反应,形成粒径分布均匀、化学成分均匀的金属粉末颗粒,并实现合金元素在基体中的过饱和固溶,被认为是制备纳米金属基复合粉末的理想方法。通过后续的固相烧结和热处理,过饱和固溶的合金元素在热力学驱动下析出,形成金属间化合物、碳化物、氮化物、氧化物等增强相,即可制备具有优良性能的超细晶金属基复合材料。
3.近年来,由于其优异的物理力学性能,氧化物弥散强化(ods)铜基复合材料受到了科学界的广泛关注。选择生成焓高、熔点高、化学结构稳定、不溶于基体、扩散速度低、界面低、与基体结合力强的氧化物。单一氧化物tho2、al2o3、zro2和y2o3均能满足上述条件,但是由于单一氧化物粒子与基体间的晶格失配度大,往往形成半共格或者不共格界面,在高温处理时,氧化物颗粒容易发生长大和聚集,粒子的尺寸很难达到几纳米,并且随着纳米粒子的生长,其数密度也会逐渐下降。
技术实现要素:4.针对现有技术的以上缺陷或改进需求,本发明提供了一种共格纳米氧化物弥散强化铜合金及其制备方法与应用,其通过形成cu
‑
x(x=al、ti、zr等)合金,一方面通过合金元素固溶增大基体的晶格常数,另一方面在基体中形成y
‑
x
‑
o纳米氧化物弥散相,降低基体与氧化物间的晶格失配度,制备数密度高、弥散分布、具有完全共格界面的纳米氧化物析出相(即析出物的晶格与周围基体几乎相同),提高了铜合金的强度、导热性能和高抗软化性能,制备得到了高性能的ods铜合金。
5.为实现上述目的,按照本发明的一个方面,提供了一种共格纳米氧化物强化铜合金的制备方法,所述制备方法主要包括以下步骤:
6.(1)将铜钇合金粉末与微合金元素粉末进行合金化以得到前驱体粉末;所述微合金元素粉末包括铝粉、硅粉、钛粉及锆粉中的至少一种;
7.(2)对所述前驱体粉末进行固相烧结,进而得到共格纳米氧化物弥散强化铜合金。
8.进一步地,依次对所述前驱体粉末进行固相烧结及退火处理,以得到所述共格纳
米氧化物弥散强化铜合金。
9.进一步地,所述微合金元素粉末包括铝粉,所述前驱体粉末中铝的质量百分数为3%~9%;cu
‑
y合金粉中钇的含量为1wt%。
10.进一步地,机械合金化是在行星球磨机内进行,球磨机转速为350r/min,球磨时间为5h~10h,球磨介质选择不锈钢磨球,大小球的直径分别为10mm和6mm,球料比为15:1。
11.进一步地,机械合金化过程中,使用含量为2wt%~10wt%的乙醇作为过程控制剂。
12.进一步地,固相烧结时,先将温度以50℃/min的速率升至650℃,并保温10min,压力维持在30mpa;然后,将温度以100℃/min的速率升至950℃,并保温10min,压力同步从30mpa均匀加载至40mpa。
13.进一步地,冷却阶段采用的降温速率为100℃/min,且压力同步均匀泄压。
14.按照本发明的另一个方面,提供了一种采用如上所述的共格纳米氧化物弥散强化铜合金的制备方法制备而成的共格纳米氧化物弥散强化铜合金。
15.本发明还提供了一种如上所述的共格纳米氧化物弥散强化铜合金在换热器中的应用。
16.总体而言,通过本发明所构思的以上技术方案与现有技术相比,本发明提供的共格纳米氧化物弥散强化铜合金及其制备方法与应用主要具有以下有益效果:
17.1.通过形成cu
‑
x(x=al、ti、zr等)合金,一方面通过合金元素固溶来增大基体的晶格常数,另一方面在基体中形成y
‑
x
‑
o纳米氧化物弥散相,降低基体与氧化物间的晶格失配度,制备数密度高、弥散分布、具有完全共格界面的纳米氧化物析出相。
18.2.通过机械合金化的方式在铜基体中固溶3wt%~9wt%的铝,形成铜
‑
铝固溶体,增大了基体的晶格常数;经热处理后,过饱和固溶在基体中的y、o在al的参与下弥散析出,铜
‑
铝合金基体中生成y
‑
al
‑
o复杂氧化物纳米颗粒作为强化相,弥散分布的纳米氧化物颗粒与基体形成完全共格界面(析出物的晶格与周围基体的晶格几乎相同),具有高的反相畴界能,从而将合金的硬度从85hv提高到225hv,同时共格界面降低了声子、电子在氧化物弥散析出相与基体界面上的散射,使得合金保持了较高的导热性和导电性,在600℃下的导热系数可以达到270w/(m
·
k),与cu
‑
y合金300w/(m
·
k)的导热系数接近。
19.3.铜
‑
铝合金基体和y4al2o9弥散相之间具有极低的晶格失配度(0.337%
±
0.002%),是常见的ods铜合金中基体与弥散相间晶格失配度的十分之一,从而降低了氧化物析出的成核势垒,实现了纳米氧化物的均相析出,形成了具有极高数密度的纳米氧化物颗粒(数密度约为2.16
×
10
24
/m3,平均粒径约4.8nm)弥散分布于基体中。共格界面进一步提高纳米氧化物的稳定性,在高温下没有发生明显的长大和聚集;通过这种高数密度的纳米氧化物颗粒对晶粒的钉扎作用,阻碍晶粒生长和晶界迁移所制备的ods铜合金的软化温度被提高到1000℃以上,在1000℃保温后基体晶粒没有发生再结晶和长大。
20.4.本发明所制备的纳米y4al2o9弥散强化铜合金在600℃时的维氏硬度为227.33hv,导热系数为269.37w/(m
·
k),具有优异的高温性能,能够满足高温导热散热器的应用。
附图说明
21.图1是本发明提供的一种共格纳米氧化物弥散强化铜合金的制备方法的流程示意图;
22.图2中的(a)、(b)、(c)、(d)、(e)分别是本发明实施例1
‑
3的xrd图及sem图,(a)cu
‑
y粉末、maed cu
‑
y粉末、固结ods铜合金和退火ods铜合金的xrd图谱,(b)机械合金化(maed)cu
‑
y粉末的微观结构,(c)maed ods铜合金粉末的微观结构和eds图谱,(d,e)sem和ebse
‑
sem下的sps烧结后的示意图;
23.图3中的(a)、(b)、(c)、(d)、(e)、(f)分别是实施例2制备的高密度共格纳米氧化物弥散强化铜合金的tem图,(a)、(b)分别为退火ods铜合金的明场tem图像、(c)暗场tem图像,(d)退火ods铜合金的tem图像和相应的元素分布结果,(e)、(f)分别为haadf
‑
stem图像和纳米氧化物数密度的统计分布图;
24.图4中的(a)、(b)、(c)、(d)、(e)、(f)分别是实施例3制备得到的高密度共格纳米氧化物弥散强化铜合金的tem图和hrtem图,(a)ods铜合金的tem图,(b)saed图,(c)a部分的高分辨率haadf图像,(d)ods铜合金的高分辨率haadf图像,(e)fft衍射花样(b区域)和(f)ods铜合金中b区域的ifft图像;
25.图5中的(a)、(b)、(c)分别是实施例1
‑
3的力学性能图和导热性能图,(a)为固结ods铜合金在不同温度下退火处理后的硬度,(b)为cu
‑
y合金、球磨cu
‑
y合金(maed cu
‑
y)和固结ods铜合金(600℃退火)在不同温度保温1h后淬火试样的硬度,(c)为cu
‑
y、maed cu
‑
y和固结ods铜合金在不同温度下的导热系数图。
具体实施方式
26.为了使本发明的目的、技术方案及优点更加清楚明白,以下结合附图及实施例,对本发明进行进一步详细说明。应当理解,此处所描述的具体实施例仅仅用以解释本发明,并不用于限定本发明。此外,下面所描述的本发明各个实施方式中所涉及到的技术特征只要彼此之间未构成冲突就可以相互组合。
27.请参阅图1,本发明提供的一种共格纳米氧化物弥散强化铜合金的制备方法,所述制备方法主要包括以下步骤:
28.步骤一,将采用雾化制粉方式制备得到的铜钇合金粉末与铝粉、硅粉、钛粉及锆粉中的至少一种通过机械合金化制备得到前驱体粉末。
29.具体地,所述前驱体粉末中铜钇合金粉末的质量百分比为91%,其余微合金元素(铝、硅、钛和锆中的至少一种)。当所述微合金元素采用铝时,所述前驱体粉末中铝的质量百分数为3%~9%;cu
‑
y合金粉中钇的含量为1wt%。其中,复杂氧化物如y
‑
ti
‑
o、y
‑
al
‑
o、y
‑
zr
‑
o等析出物与基体的晶格失配度较小、界面能更低,可以将氧化物的尺寸控制在10纳米以下。因此,复合氧化物弥散强化铜合金具备更优异的性能,更能满足实际需要。
30.通过铝固溶于铜,降低基体与复杂氧化物的晶格失配度来制备高性能ods铜合金的策略,制备了高数密度、高度分散、具有完全共格界面的纳米氧化物析出相(即析出物的晶格与周围基体几乎相同),提高了铜合金的力学性能、导热性能和高温稳定性。
31.其中,采用的不锈钢球的质量与铜钇合金粉末和微合金元素的质量之和的比值为15:1,使用含量为2wt%~5wt%的乙醇作为过程控制剂(pca),以避免机械合金化过程中的
冷焊。
32.步骤二,以所述前驱体粉末为原料,通过放电等离子烧结工艺进行固相烧结而得到圆柱形样品,并对烧结得到的所述圆柱形样品进行热处理,固相析出纳米氧化物颗粒,继而进行高温抗软化测试和导热性能测试。
33.具体地,固相烧结的温度为950℃,升温分为两个阶段:首先,将前驱体粉末加热至660℃,以50℃/min的加热速率,保温时间为10分钟;然后,将加热速率提高到100℃/min,温度保持在900℃,保温10min,同时将压力从30mpa提高到40mpa。此外,所制备的ods铜合金在烧结后需要进行退火处理,退火后采用炉冷降温至室温。
34.对ods铜合金进行线切割、打磨抛光之后进行组织结构、形貌、元素组成、高温抗软化和高温导热性能测试,结果如图2至图5所示,其中,高温抗软化和高温性能结果如表1及表2所示。
35.表1.cu
‑
y、机械合金化cu
‑
y、固结ods
‑
cu和退火态ods
‑
cu在不同热处理温度下的维氏硬度
[0036][0037]
表2.cu
‑
y、机械合金化cu
‑
y和热退火态ods
‑
cu合金在不同温度下的导热性能
[0038][0039][0040]
其中,ods铜合金进行了400℃、600℃、800℃和1000℃高温抗软化测试和200℃、400℃和600℃高温导热性能测试;所制备的ods铜合金,纳米氧化物具有极高数密度的纳米析出相(数密度约2.16
×
10
24
/m3,平均直径约4.8nm),且纳米氧化物与基体具有较低的晶格失配度(0.337%
±
0.002%);纳米y4al2o9弥散强化铜合金在600℃时的维氏硬度为227.33hv,导热系数为269.37w/(m
·
k)。
[0041]
本发明还提供了一种采用如上所述的共格纳米氧化物弥散强化铜合金的制备方法制备而成的共格纳米氧化物弥散强化铜合金。本发明还提供了一种如上所述的共格纳米
氧化物弥散强化铜合金在换热器中的应用。
[0042]
以下以几个实施例来对本发明进行进一步的详细说明。
[0043]
实施例1
[0044]
一种共格纳米氧化物弥散强化铜合金的制备方法包括以下步骤:
[0045]
将雾化法制备的cu
‑
y粉末进行烧结。其中,采用真空气氛烧结(5pa~10pa),整个升温过程包括两个阶段:首先,将温度以50℃/min的速率升至650℃,并保温10min,压力维持在30mpa,使颗粒间的低升华温度杂质排出。然后,将温度以100℃/min的速率升至950℃,并保温10min,压力同步从30mpa均匀加载至40mpa,粉末颗粒发生软化、重排粉和液相烧结。最后,冷却阶段的降温速率为100℃/min以缓解随炉快冷带来的应力集中,压力同步均匀泄压。获得的圆柱形烧结试样,尺寸为直径30mm,厚度6mm。
[0046]
将制备的产品进行线切割成需要的尺寸,分成3组类型的尺寸,一组进行xrd和sem测试,结果如图2所示,一组在管式炉中进行400℃、600℃、800℃和1000℃条件下退火处理进行显微硬度测试,结果如图5所示。另一组在25℃、200℃、400℃、600℃进行导热性能测试,测试结果如图5所示。
[0047]
实施例2
[0048]
一种共格纳米氧化物弥散强化铜合金的制备方法包括以下步骤:
[0049]
步骤一,将cu
‑
y粉末的机械合金化在行星球磨机内进行。球磨机转速为350r/min,球磨时间为10h,不锈钢罐的容积为500ml,球磨介质选择不锈钢磨球,大小球的直径分别为10mm和6mm,并以1:3的比例进行级配,球料比为15:1;罐内抽真空并通氩气至0.05mpa;采用乙醇作为过程控制剂,以尽量降低球磨过程中的冷焊效应;球磨后,粉末在真空80℃下干燥10h,并在烧结前将其封装在真空密封袋中保存。
[0050]
步骤二,粉末烧结。采用真空气氛烧结(5pa~10pa),整个升温过程包括两个阶段:首先,将温度以50℃/min的速率升至650℃,并保温10min,压力维持在30mpa,使颗粒间的低升华温度杂质排出。然后,将温度以100℃/min的速率升至950℃,并保温10min,压力同步从30mpa均匀加载至40mpa,粉末颗粒发生软化、重排粉和液相烧结。最后,冷却阶段的降温速率为100℃/min以缓解随炉快冷带来的应力集中,压力同步均匀泄压。获得的圆柱形烧结试样,尺寸为直径30mm,厚度6mm。
[0051]
将制备的产品进行线切割成需要的尺寸,分成3组类型的尺寸,一组进行xrd和sem测试,结果如图2所示,一组在管式炉中进行400℃、600℃、800℃和1000℃条件下退火处理进行显微硬度测试,结果如图5所示。另一组在25℃、200℃、400℃、600℃进行导热性能测试,测试结果如图5所示。
[0052]
实施例3
[0053]
一种共格纳米氧化物弥散强化铜合金的制备方法包括以下步骤:
[0054]
步骤一,将cu
‑
y
‑
al粉末的机械合金化在行星球磨机内进行。球磨机转速为350r/min,球磨时间为10h,不锈钢罐的容积为500ml,球磨介质选择不锈钢磨球,大小球的直径分别为10mm和6mm,并以1:3的比例进行级配,球料比为15:1;罐内抽真空并通氩气至0.05mpa;采用乙醇作为过程控制剂,以尽量降低球磨过程中的冷焊效应;球磨后,粉末在真空80℃下干燥10h,并在烧结前将其封装在真空密封袋中保存。
[0055]
步骤二,粉末烧结。采用真空气氛烧结(5pa~10pa),整个升温过程包括两个阶段:
首先,将温度以50℃/min的速率升至650℃,并保温10min,压力维持在30mpa,使颗粒间的低升华温度杂质排出。然后,将温度以100℃/min的速率升至950℃,并保温10min,压力同步从30mpa均匀加载至40mpa,粉末颗粒发生软化、重排粉和液相烧结。最后,冷却阶段的降温速率为100℃/min以缓解随炉快冷带来的应力集中,压力同步均匀泄压。获得的圆柱形烧结试样,尺寸为直径30mm,厚度6mm。
[0056]
将制备的产品进行线切割成需要的尺寸,分成4组类型的尺寸,一组进行xrd和sem测试,结果如图2所示;一组进行sem和tem测试,结果如图2、图3和图4所示;一组在管式炉中进行400℃、600℃、800℃和1000℃条件下退火处理进行显微硬度测试,结果如图5所示。另一组分别在25℃、200℃、400℃、600℃进行导热性能测试,测试结果如图5所示。
[0057]
本领域的技术人员容易理解,以上所述仅为本发明的较佳实施例而已,并不用以限制本发明,凡在本发明的精神和原则之内所作的任何修改、等同替换和改进等,均应包含在本发明的保护范围之内。