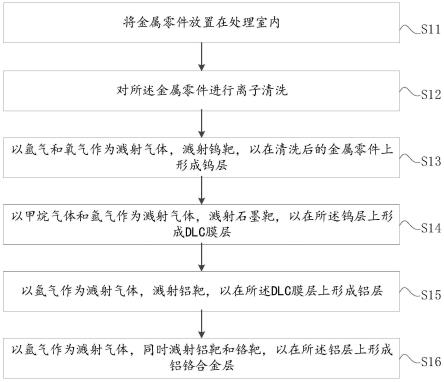
1.本发明涉及金属表面处理技术领域,特别是涉及一种金属零件的表面镀膜方法。
背景技术:2.机械制造领域中,由于金属零件的表面需要涂敷耐磨层,dlc(diamond-like carbon,类金刚石)层具有高硬度和高弹性模量,低摩擦因数,耐磨损以及高电阻率等特点,很适合于作为耐磨涂层。然而,dlc直接附着在金属表面时附着性较差,dlc层易剥落,特别是一些金属零件对于耐磨性要求较高,会导致金属零件在受到较大应力情况下容易出现dlc层剥落的情况。
技术实现要素:3.本发明实施例的目的是提供一种金属零件的表面镀膜方法,能够在金属零件表面形成耐磨损且附着力强的膜层。
4.为了解决上述技术问题,本发明实施例提供一种金属零件的表面镀膜方法,包括:
5.将金属零件放置在处理室内;
6.对所述金属零件进行离子清洗;
7.以氩气和氧气作为溅射气体,溅射钨靶,以在清洗后的金属零件上形成钨层;
8.以甲烷气体和氩气作为溅射气体,溅射石墨靶,以在所述钨层上形成dlc膜层;
9.以氩气作为溅射气体,溅射铝靶,以在所述dlc膜层上形成铝层;
10.以氩气作为溅射气体,同时溅射铝靶和铬靶,以在所述铝层上形成铝铬合金层。
11.作为上述方案的改进,在所述将金属零件放置在处理室内之前,还包括步骤:
12.清洗并干燥所述金属零件。
13.作为上述方案的改进,在所述对所述金属零件进行离子清洗之前,还包括步骤:
14.对所述处理室进行抽真空处理,使得所述处理室内的真空度达到4.5-5.5
×
10-3
pa。
15.作为上述方案的改进,所述对所述金属零件进行离子清洗,具体为:
16.向所述处理室内通入氩气,并开启射频离子源,以形成离子束对所述金属零件进行清洗;其中,所述射频离子源的工作电压为300v-350v,离子束流强为200-300ma,清洗时间为4-6min,温度为80-100℃。
17.作为上述方案的改进,在所述溅射钨靶的步骤中,氩气的流量为750-850sccm,氧气的流量为250-350sccm。
18.作为上述方案的改进,在所述溅射钨靶的步骤中,溅射电源为中频溅射电源,溅射压力为0.005-0.015pa,溅射功率为500-700w,温度为75-85℃,溅射时间为13-17min。
19.作为上述方案的改进,在所述溅射石墨靶的步骤中,环境压力为6-8pa,所述金属零件表面施加的负压为400-1000v,温度为80-90℃,溅射时间为95-105min。
20.作为上述方案的改进,在所述溅射铝靶的步骤中,溅射功率为9-10kw,离子轰击电
流为20-25a,溅射时间为70-90min。
21.作为上述方案的改进,在所述同时溅射铝靶和铬靶的步骤中,所述铝靶的溅射功率为9-10kw,所述铝靶的离子轰击电流为20-25a,所述铬靶的溅射功率为5-6.5kw,所述铬靶的离子轰击电流为12-15a,溅射时间为30-50min。
22.作为上述方案的改进,所述钨层的厚度为250-350nm,所述dlc膜层的厚度为750-850nm,所述铝层的厚度为150-250nm,所述铝铬合金层的厚度为100-200nm。
23.实施本发明实施例,具有如下有益效果:
24.本发明实施例提供一种金属零件的表面镀膜方法,通过对金属零件进行离子清洗,能够去除金属零件表面的杂质,以提高后续镀膜的附着力;通过在清洗后的金属零件上溅射形成钨层,能够以钨作为连接金属零件和dlc膜的中间介质,提高后续镀上的dlc膜在金属零件表面的附着力;通过在金属零件的钨层上依次溅射形成dlc膜层、铝层和铝铬合金层,能够在金属零件上形成掺杂铝铬合金的dlc复合膜,该dlc复合膜相较于一般的dlc膜具有更高的硬度,能够更好地防止金属零件磨损,从而延长金属零件的使用寿命。
附图说明
25.图1是本发明提供的实施例中的一种金属零件的表面镀膜方法的流程图。
具体实施方式
26.下面将结合本发明实施例中的附图,对本发明实施例中的技术方案进行清楚、完整地描述,显然,所描述的实施例仅仅是本发明一部分实施例,而不是全部的实施例。基于本发明中的实施例,本领域普通技术人员在没有作出创造性劳动前提下所获得的所有其他实施例,都属于本发明保护的范围。
27.请参阅图1所示,其是本发明提供的实施例中的一种金属零件的表面镀膜方法的流程图,所述的金属零件的表面镀膜方法包括以下步骤:
28.s11、将金属零件放置在处理室内;
29.s12、对所述金属零件进行离子清洗;
30.s13、以氩气和氧气作为溅射气体,溅射钨靶,以在清洗后的金属零件上形成钨层;
31.s14、以甲烷气体和氩气作为溅射气体,溅射石墨靶,以在所述钨层上形成dlc膜层;
32.s15、以氩气作为溅射气体,溅射铝靶,以在所述dlc膜层上形成铝层;
33.s16、以氩气作为溅射气体,同时溅射铝靶和铬靶,以在所述铝层上形成铝铬合金层。
34.在本实施例中,通过对金属零件进行离子清洗,能够去除金属零件表面的杂质,以提高后续镀膜的附着力;通过在清洗后的金属零件上溅射形成钨层,能够以钨作为连接金属零件和dlc膜的中间介质,由于钨的材料较软,能够提高后续镀上的dlc膜在金属零件表面的附着力;通过在金属零件的钨层上依次溅射形成dlc膜层、铝层和铝铬合金层,能够在金属零件上形成掺杂铝铬合金的dlc复合膜,该dlc复合膜相较于一般的dlc膜具有更高的硬度,能够更好地防止金属零件磨损,从而延长金属零件的使用寿命。
35.作为其中一个可选的实施例,在所述将金属零件放置在处理室内之前,还包括步
骤:
36.s10、清洗并干燥所述金属零件。
37.在本实施例中,在金属零件的表面上镀膜之前,可以是先用超声波设备对金属零件的表面进行清洗并烘干,从而先去除金属零件表面的杂质,从而能够有效提高后续镀膜的附着力。
38.作为其中一个可选的实施例,在所述对所述金属零件进行离子清洗之前,还包括步骤:
39.s11'、对所述处理室进行抽真空处理,使得所述处理室内的真空度达到4.5-5.5
×
10-3
pa。
40.在本实施例中,在对所述金属零件进行离子清洗之前,先对所述处理室进进行抽真空处理,从而使得所述处理室内的真空度达到4.5-5.5
×
10-3
pa,这样能够有效提高后续离子清洗的效率。
41.在本实施例中,所述真空度可以为4.5
×
10-3
pa、4.75
×
10-3
pa、5.0
×
10-3
pa、5.25
×
10-3
pa、5.5
×
10-3
pa。当然,所述真空度不限于上述列举的具体数值,其可以根据实际需求进行设置,在此不做更多的赘述。
42.作为其中一个可选的实施例,所述步骤s12具体为:
43.向所述处理室内通入氩气,并开启射频离子源,以形成离子束对所述金属零件进行清洗;其中,所述射频离子源的工作电压为300v-350v,离子束流强为200-300ma,清洗时间为4-6min,温度为80-100℃。
44.本实施例通过上述方式对金属零件进行离子清洗,能够保证清洗效果。
45.在所述步骤s12中,所述射频离子源的工作电压可以为300v、310v、320v、330v、340v、350v;所述离子束的流强可以为200ma、225ma、250ma、275ma、300ma;所述清洗时间可以为4min、4.5min、5min、5.5min、6min;所述温度可以为80℃、85℃、90℃、95℃、100℃。当然,所述射频离子源的工作电压、所述离子束的流强、所述清洗时间和所述温度不限于上述列举的具体数值,其可以根据实际需求进行设置,在此不做更多的赘述。
46.作为其中一个可选的实施例,为了保证镀膜质量,在所述溅射钨靶的步骤s13中,氩气的流量为750-850sccm,氧气的流量为250-350sccm。
47.在所述步骤s13中,所述氩气的流量可以为750sccm、775sccm、800sccm、825sccm、850sccm;所述氧气的流量可以为250sccm、275sccm、300sccm、325sccm、350sccm。当然,所述氩气的流量和所述氧气的流量不限于上述列举的具体数值,其可以根据实际需求进行设置,在此不做更多的赘述。
48.作为其中一个可选的实施例,为了保证镀膜质量,在所述溅射钨靶的步骤s13中,溅射电源为中频溅射电源,溅射压力为0.005-0.015pa,溅射功率为500-700w,温度为75-85℃,溅射时间为13-17min。
49.在所述步骤s13中,所述溅射压力可以为0.005pa、0.0075pa、0.010pa、0.0125pa、0.015pa;所述溅射功率可以为500w、550w、600w、650w、700w;所述温度可以为75℃、77.5℃、80℃、82.5℃、85℃;所述溅射时间可以为13min、14min、15min、16min、17min。当然,所述溅射压力、所述溅射功率、所述温度和所述溅射时间不限于上述列举的具体数值,其可以根据实际需求进行设置,在此不做更多的赘述。
50.作为其中一个可选的实施例,为了保证镀膜质量,在所述溅射石墨靶的步骤s14中,环境压力为6-8pa,所述金属零件表面施加的负压为400-1000v,温度为80-90℃,溅射时间为95-105min。
51.在所述步骤s14中,所述环境压力可以为6pa、6.5pa、7pa、7.5pa、8pa;所述金属零件表面施加的负压可以为400v、550v、700v、850v、1000v;所述温度可以为80℃、82.5℃、85℃、87.5℃、90℃;所述溅射时间可以为95min、97.5min、100min、102.5min、105min。当然,所述环境压力、所述金属零件表面施加的负压、所述温度和所述溅射时间不限于上述列举的具体数值,其可以根据实际需求进行设置,在此不做更多的赘述。
52.作为其中一个可选的实施例,为了保证镀膜质量,在所述溅射铝靶的步骤s15中,溅射功率为9-10kw,离子轰击电流为20-25a,溅射时间为70-90min。
53.在所述步骤s15中,所述溅射功率可以为9kw、9.25kw、9.5kw、9.75kw、10kw;所述离子轰击电流可以为20a、21.25a、22.5a、23.75a、25a;所述溅射时间可以为70min、75min、80min、85min、90min。当然,所述溅射功率、所述离子轰击电流和所述溅射时间不限于上述列举的具体数值,其可以根据实际需求进行设置,在此不做更多的赘述。
54.作为其中一个可选的实施例,为了保证镀膜质量,在所述同时溅射铝靶和铬靶的步骤s16中,所述铝靶的溅射功率为9-10kw,所述铝靶的离子轰击电流为20-25a,所述铬靶的溅射功率为5-6.5kw,所述铬靶的离子轰击电流为12-15a,溅射时间为30-50min。
55.在所述步骤s16中,所述铝靶的溅射功率可以为9kw、9.25kw、9.5kw、9.75kw、10kw;所述铝靶的离子轰击电流可以为20a、21.25a、22.5a、23.75a、25a;所述铬靶的溅射功率可以为5kw、5.375kw、5.75kw、6.125kw、6.5kw;所述铬靶的离子轰击电流可以为12a、12.75a、13.5a、14.25a、15a;所述溅射时间可以为30min、35min、40min、45min、50min。当然,所述铝靶的溅射功率、所述铝靶的离子轰击电流、所述铬靶的溅射功率、所述铬靶的离子轰击电流和所述溅射时间不限于上述列举的具体数值,其可以根据实际需求进行设置,在此不做更多的赘述。
56.作为其中一个可选的实施例,为了使镀膜的硬度和附着力达到最佳,所述钨层的厚度为250-350nm,所述dlc膜层的厚度为750-850nm,所述铝层的厚度为150-250nm,所述铝铬合金层的厚度为100-200nm。
57.在本实施例中,所述钨层的厚度可以为250nm、275nm、300nm、325nm、350nm;所述dlc膜层的厚度可以为750nm、775nm、800nm、825nm、850nm;所述铝层的厚度可以为150nm、175nm、200nm、225nm、250nm;所述铝铬合金层的厚度可以为100nm、125nm、150nm、175nm、200nm。当然,所述钨层的厚度、所述dlc膜层的厚度、所述铝层的厚度和所述铝铬合金层的厚度不限于上述列举的具体数值,其可以根据实际需求进行设置,在此不做更多的赘述。
58.下面通过一个具体实施例来描述本方案的实施过程,包括:
59.步骤1:清洗金属零件并干燥,使表面没有尘埃和油渍;
60.步骤2:将金属零件放置在处理室内;
61.步骤3:对处理室进行抽真空处理,使得处理室内的真空度达到5.0
×
10-3
pa;
62.步骤4:将氩气充入处理室内中,打开转架,在气体稳定后,打开射频离子源,以形成离子束对金属零件进行清洗;其中,射频离子源的工作电压为325v,离子束流强为250ma,清洗时间为5min,温度为90℃;
63.步骤5:将氩气和氧气充入处理室内中,保持充气稳定,开启钨靶的中频溅射电源,以氩气和氧气作为溅射气体,溅射钨靶,以在清洗后的金属零件上形成钨层;其中,氩气的流量为800sccm,氧气的流量为300sccm,溅射压力为0.010pa,溅射功率为600w,温度为80℃,溅射时间为15min,钨层的厚度为300nm;
64.步骤6:通入甲烷气体,调节氩气环境压力0.1-0.5pa,关闭钨靶材溅射电源,只保留石墨靶作为碳源,将氩气环境压力调整到6-8pa,以甲烷气体和氩气作为溅射气体,溅射石墨靶,以在钨层上形成dlc膜层;其中,金属零件表面施加的负压为700v,温度为85℃,溅射时间为100min,dlc膜层的厚度为800nm;
65.步骤7:关闭石墨靶的电源,氩气流量保持不变,启动铝靶,以氩气作为溅射气体,溅射铝靶,以在dlc膜层上形成铝层;其中,溅射功率为9.5kw,离子轰击电流为22.5a,溅射时间为80min,铝层的厚度为200nm;
66.步骤8:镀铝完成后,启动铬靶,以氩气作为溅射气体,同时溅射铝靶和铬靶,以在铝层上形成铝铬合金层;其中,铝靶的溅射功率为9.5kw,铝靶的离子轰击电流为22.5a,铬靶的溅射功率为5.75kw,铬靶的离子轰击电流为13.5a,溅射时间为40min,铝铬合金层的厚度为150nm。
67.经测试,采用本实施例提供的金属零件的表面镀膜方法所得到的镀膜后的金属零件的更换周期由原来的3个月延长至6个月一次,由此可见,使用本实施例提供的金属零件的表面镀膜方法对金属零件进行镀膜,能够有效延长金属零件的使用寿命。
68.以上所述仅是本发明的优选实施方式,应当指出,对于本技术领域的普通技术人员来说,在不脱离本发明技术原理的前提下,还可以做出若干改进和替换,这些改进和替换也应视为本发明的保护范围。