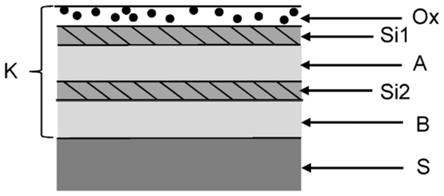
1.本发明涉及一种用于通过成形涂覆有防腐蚀涂层的扁钢产品来生产钢构件的方法。此外本发明还涉及由涂覆有防腐蚀涂层的钢制基板生产的钢构件。
2.当提到“扁钢产品”时,意思为钢带,钢薄板或者由此制成的扁坯或类似的产品。扁坯通常指钢板,其比制成该钢板的钢带或者钢薄板具有更加复杂的轮廓。
背景技术:3.在车身制造中使用对其机械特性以及加工行为要求较高的钢材。为了能够尽可能经济地进行加工,使用的钢材应首先适用于热成形并且能够很好地焊接和粘合。为了满足顾客提出的长时间的使用寿命的要求,在车辆制造中使用的车身零件应具有高的耐腐蚀性。耐腐蚀特性能够通过在钢制基板上涂覆耐腐蚀层来达到。
4.由此,本质上含锌的涂层能够显著改善车身零件的腐蚀行为。然而涂覆有锌基防腐蚀层的扁坯仅能通过间接热成形加工,而间接热成形是费用很高的处理。在间接热成形中首先将扁坯在室温下在工具中以高成形度进行成形然后才加热构件。将这些构件重新放入以小的成形度将其加工为最终形状的工具中,以修正先前处理的构件变形。与此相反,涂覆有铝基防腐蚀层的扁坯也适用于通过直接热成形进行的加工。在直接热成形中,首先将扁坯在熔炉中加热然后在工具中以高成形度进行热成形。用于形状修正的再次成形是不必要的,这总体上缩短了过程。
5.由wo 2008/053273 a1中已知一种用于生产设置有铝基防腐蚀层的钢构件的方法。其中,将待成形的,涂覆有铝或者铝合金的扁坯以4-12℃/s的速度加热,在880-940℃的温度下保持3至13分钟,然后转移到成形工具中并成形,再以至少30℃/s的速度降温。成形后该构件的涂层具有包含互扩散层,中间层,金属间层以及表面层的多层层结构。互扩散层由86-95%的fe,4-10%的al以及最多5%的si 组成。中间层由39-47%的fe,53-61%的al以及最多2%的si组成。金属间层由62-67%的fe,30-34%的al和2-6%的si组成。表面层由 39-47%的fe,53-61%的al和最多2%的si组成。该构件应具有好的可焊接性和防裂性。
技术实现要素:6.本发明的目的在于提供一种用于生产设置有防腐蚀层的钢构件的改进的方法。本发明的目的尤其在于,提供一种具有良好的可焊接性和良好的粘合特性的设置有防腐蚀层的钢构件。
7.有关方法的目的利用本发明给出的特征的方法解决。根据本发明的方法的有利的和优选的设计方案在本发明中给出。有关钢构件的目的通过具有本发明给出的特点的钢构件解决。根据本发明的钢构件的有利的和优选的设计方案在本发明中给出。
8.在用于生产设置有防腐蚀层的钢构件的根据本发明的方法中,首先准备设置有铝基防腐蚀层的扁钢制品。
9.通常用作扁钢产品钢制基板的钢材是全镇静钢,其具有下列组成:0.10-0.25重
量%的c,1.0-1.4重量%的mn,0.35-0.4重量%的 si,最大0.03重量%的p,最大0.01重量%的s,最大0.040重量%的al,最大0.15重量%的ti,最大0.1重量%的nb,最大0.005重量%的b,最大0.5重量%的cr,最大0.5重量%的mo,其中cr和mo 的含量总和最大为0.5重量%,其余为铁和不可避免的杂质。
10.当给出关于合金含量和组成时,如果没有其它明确说明,这些数据基于重量或者质量。
11.将铝基防腐蚀层借助于传统涂层方法,如热浸镀,涂覆到钢制基板上,该基板比如可以是钢薄板或者钢带。适用于此目的的熔池通常包括3-15重量%的硅(si),优选9-10重量%的si,最大3.5重量%的铁,剩下的为铝和不可避免的杂质。当在本技术中提到涂覆有防腐蚀层的扁钢产品或者钢构件时,由此意思是在至少一面上涂层的扁钢产品或者钢构件。
12.涂覆在扁钢产品上的铝基防腐蚀层通常包含3-15重量%的硅,优选7-12重量%的si,特别优选9-10重量%的si,以及最大3.5重量%的铁(fe),优选1-3.5重量%的fe,特别优选2-3.5重量%的fe,其余为铝和不可避免的杂质。涂覆在该扁钢产品上的防腐蚀层的厚度通常为每一面10-40μm,涂层重量通常为每一面30-100g/m2,优选每一面40-80g/m2。
13.以传统方式由涂层的扁钢产品制造扁坯,对该扁坯进行热处理。为了进行热处理将厚度为d的涂层扁坯在炉长为l的熔炉中放置滞留时间t,该熔炉具有炉温t。其中滞留时间t为将扁坯放入熔炉和将扁坯从熔炉中取出之间度过的时间。这里扁坯厚度d的意思是扁坯的包含防腐蚀层在内的总厚度,也就是说钢制基板的厚度和防腐蚀层厚的总和。
14.研究显示,焊接特性和粘合特性都会受到扁坯厚度d,滞留时间 t,炉长l和炉温t的影响。因此根据本发明,根据等式(1),℃为单位的炉温t和mm为单位的扁坯厚度d的乘积与min为单位的扁坯在熔炉中的滞留时间t和m为单位的炉长l的乘积的比值最小为 0.0034℃/min以及最大0.021℃/min:
15.0.0034℃/min≤q≤0.021℃/min(1),
16.q=(t*d)/(t*l),其中
17.t=熔炉温度,单位℃,
18.d=扁坯厚度,单位mm,
19.t=扁坯在熔炉中的滞留时间,单位min,
20.l=熔炉长度,单位m。
21.根据等式(1)对于热处理作出的根据本发明的调整对于铁从钢制基板至防腐蚀层中的扩散并由此对于防腐蚀层的彻底合金化有着很大的意义。同时如此选择q,只要避免在热处理时的防腐蚀层的液化、在成形工具中成形时的液体组成部分、防腐蚀层在炉辊上的牢固粘附以及防腐蚀层在运输设备上和成形工具上的附着,就保证了过程可靠性。
22.当q小于0.0034℃/min时,防腐蚀层稀硅层a中会出现超过60重量%的过高铁含量,这对涂层的腐蚀保护行为有着负面影响。主要是在较小的q值时出现的在防腐蚀层表面的铁的聚集在很小的腐蚀性负载时就会造成红锈。此外还确定了,在小于0.0034℃/min 的q值时有明显的铁和锰原子从钢制基板扩散到防腐蚀层中,这促使了防腐蚀层表面上多孔氧化物层的形成。由此出现了锰和/或铁氧化物聚集的氧化物层,其厚度大于250nm并且非常多孔,这损害了导电性并由此损害了可焊接性。同时通过构件表面上的多孔氧化物层使
得漆的附着和胶粘剂的附着变差。后者能够在有负载的情况下导致提早的失效。
23.当q值大于0.021℃/min时,镀层的扁坯的表面在成形工具上烧结和粘附的风险提高,这导致了成形后的构件的表面性质的损坏,也导致了工具磨损的增强。此外当q值大于0.021℃/min时,能够在熔炉内部观察到炉辊上增多的铝的损坏,这可能导致在制成的构件中局部地达不到客户提出的关于镀层的最低厚度。
24.此外,当q值大于0.021℃/min时,不足以促进铁向层a中的扩散,由此层a中存在的铁的含量少于40重量%。由此已成形的构件的焊接特性变差,因为通过较小的铁含量导致层a的电阻升高。
25.在一个优选的实施方案中,如此设置炉温t,使得其不小于830 ℃并且不大于980℃。这里优选的炉温是最高910℃,因为利用这样的炉温能够生产出具有特别好的粘合特性的钢构件。
26.在另一个优选的实施方案中,扁坯在熔炉中的滞留时间t最小为1分钟最大为18分钟。通常将室温下的扁坯放入熔炉中,由此该滞留时间t能够既包括加热阶段也包括保持阶段。
27.830℃至980℃炉温t和/或1至18分钟的滞留时间t下的热处理已被证明特别适用于钢制基板的处理,该钢制基板具有0.10-0.25 重量%的c,1.0-1.4重量%的mn,0.35-0.4重量%的si,最大0.03 重量%的p,最大0.01重量%的s,最大0.040重量%的al,最大0.15 重量%的ti,最大0.1重量%的nb,最大0.005重量%的b,最大0.5 重量%的cr,最大0.5重量%的mo,其中cr和mo的含量总和最大为 0.5重量%,其余为铁和不可避免的杂质。
28.根据本发明的方法尤其适用于用于生产具有良好焊接特性和良好粘合特性的钢构件、厚度为0.60-3.5mm的扁钢产品。
29.已经证明,根据本发明的方法令人惊奇地特别适用于20-50m的炉长。在更短的熔炉中防腐蚀层与钢制基层脱离的风险加大。在炉长大于50m时会更多地出现炉辊的污染,这使得后续扁坯的表面性质变差。
30.热处理优选作为连续热处理在连续加热炉中进行。
31.在另一个优选的实施方案中,使得扁坯以至少1.5m/min,最高 25m/min的平均速度vp通过熔炉。vp是将扁坯从炉入口至炉出口运输的平均速度。该速度也被称作平均扁坯速度。
32.已经证明,1.5-25m/min的平均扁坯速度特别适用于根据本发明的方法在20-50m长的熔炉中的应用。
33.如果扁坯以至少1.5m/min的平均速度通过熔炉,那么防腐蚀层在炉辊上粘附的风险降低。此外,在使用更小的平均扁坯速度时,不希望的层形成出现的风险增大,因为防腐蚀层的核心温度提早变成了炉温,由此尤其是铁和锰由钢制基板到镀层的外层的扩散得以加强,这阻碍了根据本发明的防腐蚀层的形成。同时也会促使不希望出现的氧化物层在表面形成,这使得焊接特性变差。此外不希望出现的过多的铁扩散至防腐蚀层中,这增大了成品构件上红锈形成的可能性。
34.如果扁坯以大于25m/min的较快平均速度通过熔炉,油漆附着损伤的风险加大,因为过少的铁能够扩散至防腐蚀层的表面处并且在喷漆之前的磷化处理时没有对于良好的油漆附着来说必须的磷晶体形成。尤其是第一富硅层si1至少40重量%的铁含量无法可靠
地设置。此外过程可靠性会受损,因为在成型工具中的防腐蚀层可能具有黏稠的稠度。此外在熔炉中防腐蚀层增高的液相比例形成的风险增大,这促使了炉辊的污染。这里,增高的液相比例意思是防腐蚀层中大于或者等于2体积%的液相比例。对于设定用于利用模压淬火进行热成形的扁钢产品来说,能够根据钢制基板的组成,在超过25m/min的高的平均扁坯速度下不能够保证钢制基板的核心温度在其总厚度上加热到ac3转化温度以上的温度,这是完整的完全硬化的前提。
35.可以看到,当平均扁坯速度为2-17m/min时能够特别可靠地达到良好的焊接特性。这尤其适用于厚度d小于1.5mm的扁坯。对于厚度d至少为1.5mm的扁坯来说,特别有利的是2-8.4m/min的平均扁坯速度。
36.在另一个优选的实施方案中,穿过熔炉过程中平均扁坯速度vp 保持恒定,以减小防腐蚀层性质的波动。
37.热处理之后将扁坯从熔炉中取出然后放至成形工具中,在该成形工具中将扁坯成形为钢构件。
38.在一个优选的实施方案中,对扁坯在成形工具中进行热成形。为了避免较大的热损失,熔炉和成形工具之间的转运时间通常最多为 10秒。
39.选择性地能够将扁坯在成形工具中成形时以20-1000k/s的冷却速度,优选25-500k/s的冷却速度冷却,以比如将钢制基板淬火。
40.如此制造出的钢构件包括钢制基板以及至少在该钢制基板的一个面上包括防腐蚀层。可能的还有一些系统,在这些系统中其它的涂层涂覆在该防腐蚀层上。但在一个优选的实施方案中,该制成的钢构件由钢制基板和设置在该钢制基板的至少一个面上的防腐蚀层组成。
41.由工作步骤b)中的热处理所决定,防腐蚀层的组成发生改变。在热处理之后出现的钢构件的防腐蚀层通过扩散而积聚有尤其是铁原子。防腐蚀层中来自于钢制基板的锰原子的积聚同样是可能的。此外,钢制基板的防腐蚀层中的硅原子的分布以根据本发明的方式改变,由此在多个子层之间能够区分出不同的组成。
42.钢构件的防腐蚀层具有至少四个从表面向钢制基板方向上看彼此重叠放置的子层:
[0043]-第一富硅层si1,其在不可避免的杂质之外含有大于4至最多 8重量%的si,40-70重量%的fe,最多1重量%的mn和30-60重量%的铝,其中上述组成部分的总和为100重量%,该层位于第一稀硅层a之上,
[0044]-第一稀硅层a,其在不可避免的杂质之外含有大于1至4重量%的si,30-60重量%的fe,最多1重量%的mn和40-60重量%的铝,其中上述组成部分的总和为100重量%,该层位于第一富硅层si1和第二富硅层si2之间,
[0045]-第二富硅层si2,其在不可避免的杂质之外含有大于4至最多 8重量%的si,40-70重量%的fe,最多1重量%的mn和20-50重量%的铝,其中上述组成部分的总和为100重量%,该层位于第一稀硅层 a和第二稀硅层b之间,
[0046]-第二稀硅层b,其在不可避免的杂质之外含有0.5至4重量%的si,40-97重量%的fe,0.5至1.5重量%的mn和2-40重量%的铝,其中上述组成部分的总和为100重量%,该层与钢制基板临接。
[0047]
当第二稀硅层b以μm为单位的厚度db与第一稀硅层a以μm 为单位的厚度da的比例x最小为0.4,最大为1.1时,能够得到钢构件优良的焊接特性:
[0048]
0.4≤x≤1.1
ꢀꢀꢀ
(2)
[0049]
其中x=db/da,其中
[0050]
db=稀硅层b以μm为单位的厚度以及
[0051]
da=稀硅层a以μm为单位的厚度。
[0052]
令人惊奇地确定了富硅层si1和si2的存在对根据本发明的钢构件的焊接特性尤其是粘合特性有正面影响。尤其在富硅层中的至少一个具有至少5重量%的si含量的防腐蚀层中显示出了特别好的粘合特性。
[0053]
子层a的fe含量为至少30重量%,优选至少40重量%,以保证防腐蚀层良好的可焊接性。
[0054]
子层b的al含量为至少2重量%,最大40重量%,以保证良好的粘合特性,尤其良好的粘合剂附着,以及良好的焊接特性。当子层 b的al含量限制在至少5重量%,最大20重量%时,这些能够非常可靠地达到。
[0055]
在另外一个特别优选的实施方案中,富硅层si1和si2分别具有比稀硅层a更高的铁含量。这对于成品构件的油漆附着有着正面影响,因为由此能够促进通常在喷漆过程前进行的磷化过程。
[0056]
在第一富硅层si1的上部能够有其它的防腐蚀层的子层。由此钢构件的防腐蚀层比如在其表面上具有薄的,富含硅氧化物和/或铝氧化物的层。该最外层也叫做氧化物层(ox)并且能够在镀层过程后以及热处理之前在工作步骤b)中出现,其厚度通常为约5nm。在于成形过程之前,也就是工作步骤b)中进行的热处理中,能够出现最外层中硅氧化物和铝氧化物的积聚。该氧化物层能够通过热处理增长到通常50至250nm的厚度。在生产方法的根据本发明的应用中,热处理之后在工作步骤b)中的氧化物层的厚度最大为250nm,优选最大150nm。在生产方法的不根据本发明的应用中,氧化物层增长到大于250nm的厚度并且除硅氧化物和铝氧化物之外更多地含有铁氧化物和锰氧化物,这导致了该层的更高的多孔性。更厚的氧化物层以及掺杂有铁氧化物和锰氧化物的氧化物层对于焊接特性和接合特性有负面影响。
[0057]
在一些情况下,尤其在880-920℃的炉温t下以及在扁坯在熔炉中3-8分钟的滞留时间中,能够在富硅层si1上部形成另一个稀硅层 c。该层在不可避免的杂质外还含有最大4重量%的si,30-60重量%的fe,最大1重量%的mn和30-60重量%的铝并且位于富硅层si1和最外层ox之间。
[0058]
层厚度能够间接地利用辉光放电光发射光谱分析法(gdoes)来确定。在gdoes中在层厚度上测量各个元素的重量百分比。为此,将样品进行切割并用正庚烷清洗。将如此准备过的样品放置在辉光放电光发射光谱分析仪中,并在层厚度上以10nm的解析度进行测量。利用该方法能够在防腐蚀层的总厚度上测量各个元素的重量百分比。通过稀硅层a和b与被其所包围的富硅层si1和si2相比不同的si含量能够确定稀硅层和富硅层之间的边界并由此确定稀硅层a和b的厚度。只要gdoes测量过程显示出si含量超过4重量%的测量点,稀硅层与富硅层的边界便能够确定。数值在4重量%的si以上的测量点归至富硅层,数值小于或者等于4重量%的si的测量点归至稀硅层。各个层之内的测量点的数值根据每层测出精确
数字并由此给出每层元素的重量比例。原则上层厚度也能够通过光学显微镜确定。为此,将横断面抛光并用3%的硝酸乙醇溶液进行酸蚀。在光学显微镜下明视场观察中富硅层出现,并且在1000倍放大时比稀硅层更暗。
[0059]
以gdoes测得的单独子层的典型厚度为:稀硅层a 3-16μm,稀硅层b 2-15μm,富硅层si1和si2分别为0.5-1.5μm以及选择性的稀硅层c为2-12μm。
附图说明
[0060]
接下来借助于实施例和图示进一步说明本发明。
[0061]
图1示意性示出了根据本发明的防腐蚀层的第一实施形式的构成。
[0062]
图2示意性示出了根据本发明的防腐蚀层的第二实施形式的构成。
具体实施方式
[0063]
在该方法根据本发明的实施例中,位于经过热处理并成形为钢构件的扁钢产品上的防腐蚀层以及由此位于成形的钢构件上的防腐蚀层的一个典型构造示出在图1中。在根据本发明的防腐蚀层的第一个实施形式中,钢制基板s上有防腐蚀层k。该防腐蚀层k由5个子层组成:富含氧化物的层ox,该层作为最外层与周围气氛接触;第一富硅层si1,该层位于氧化物层ox和第一稀硅层a之间;第一稀硅层a,该层位于第一富硅层si1和第二富硅层si2之间;第二富硅层si2,该层位于层a和第二稀硅层b之间;以及第二稀硅层b,该层位于第二富硅层si2下面并且直接位于钢制基板s上。
[0064]
图2同样图示性示出了根据本发明的防腐蚀层构造,其中在氧化物层ox和第一富硅层si2之间额外形成有另一个稀硅层c。
[0065]
为了证明本发明的效果进行了10次试验。为此,使用两面热浸镀、具有表1中给出的组成的钢制薄板作为钢制基板并且使用两面热浸镀、具有表2中给出的组成的钢制薄板作为防腐蚀层。将该防腐蚀层借助于传统的方式通过热浸镀涂覆到钢制基板上。分别使用冷轧的钢带,该钢带在镀层之后制成钢制薄板。由该钢制薄板切割出扁坯,将该扁坯在表3中所示的条件下进行热处理。热处理之后分别将扁坯从热处理炉中取出,在成形工具中放置7s并以传统的方式成形为构件。
[0066]
成形后从构件中取样,借助辉光放电光发射光谱分析法确定这些样品防腐蚀层中的元素分布。表4中给出了防腐蚀层的层构造,子层a和b的厚度da和db以及由此得出的值x。防腐蚀层的总厚度在热处理之后为20至55um之间。样品1,2,4,5,9和10具有根据图1的层构造。在这些样品中,防腐蚀层分别由氧化物层ox,其下方首先是第一富硅层si1,然后是第一稀硅层a,然后是第二富硅层 si2,然后是第二稀硅层b。样品3,6,7和8具有根据图2的层构造。在这些样品中,防腐蚀层在氧化物层ox和第一富硅层si1之间还具有另一个稀硅层c。在热处理后出现的防腐蚀层的子层si1,si2, a,b以及对于样品3,6,7和8来说还有子层c的组成示出在表5 中。所有的样品中防腐蚀层的最外层都是氧化物层。这里,氧化物层的厚度为70至135nm之间。
[0067]
此外再从构件中取样用于检测焊接行为,取样用于检测粘合特性以及取样用于检测油漆附着。根据sep 1220-2,2011版本对焊接行为进行检查。至少为0.9ka的值对于焊接范围来说显示出良好的焊接行为。
[0068]
根据sep 1220-6在2016年8月的暂时性版本中检测粘合特性。使用陶氏化学公司的betamate 1485 s作为粘合剂。拉伸样品直至撕开。分析断面种类和使用的致断力来评估粘合行为。当拉伸剪切强度至少为30mpa并且断面基本在防腐蚀层表面中延伸时,得出良好的粘合行为。当断面的至少75%,尤其至少85%位于放置在表面上的氧化物层内部时,尤其能够得出良好的粘合行为。涂层的其它子层中或者粘合剂中不希望出现断面部分。
[0069]
根据din en iso 20567-1b+c确定涂层网格切割参数以检测油漆附着。这里允许的网格切割参数是值gt0,gt1和gt2。gt0和gt1 的网格切割指数是特别优良的油漆附着的标准。
[0070]
关于焊接行为,粘合行为和油漆附着的研究结果示出在表6中。从表6中可以看出,所有的样品具有有着至少为1ka的焊接范围的良好的焊接行为。所有粘合检测的样品基本在防腐蚀层的氧化物层中撕裂。由此所有的样品都显示出了很好的粘合行为,其氧化物层中的断裂面比例至少为75面积%并且拉伸剪切强度至少为30mpa。所有的样品的油漆附着同样良好。由此所有的样品都显示出了gt0至gt2的涂层网格切割参数。
[0071]
[0072]
[0073][0074]
表4
[0075]
[0076]