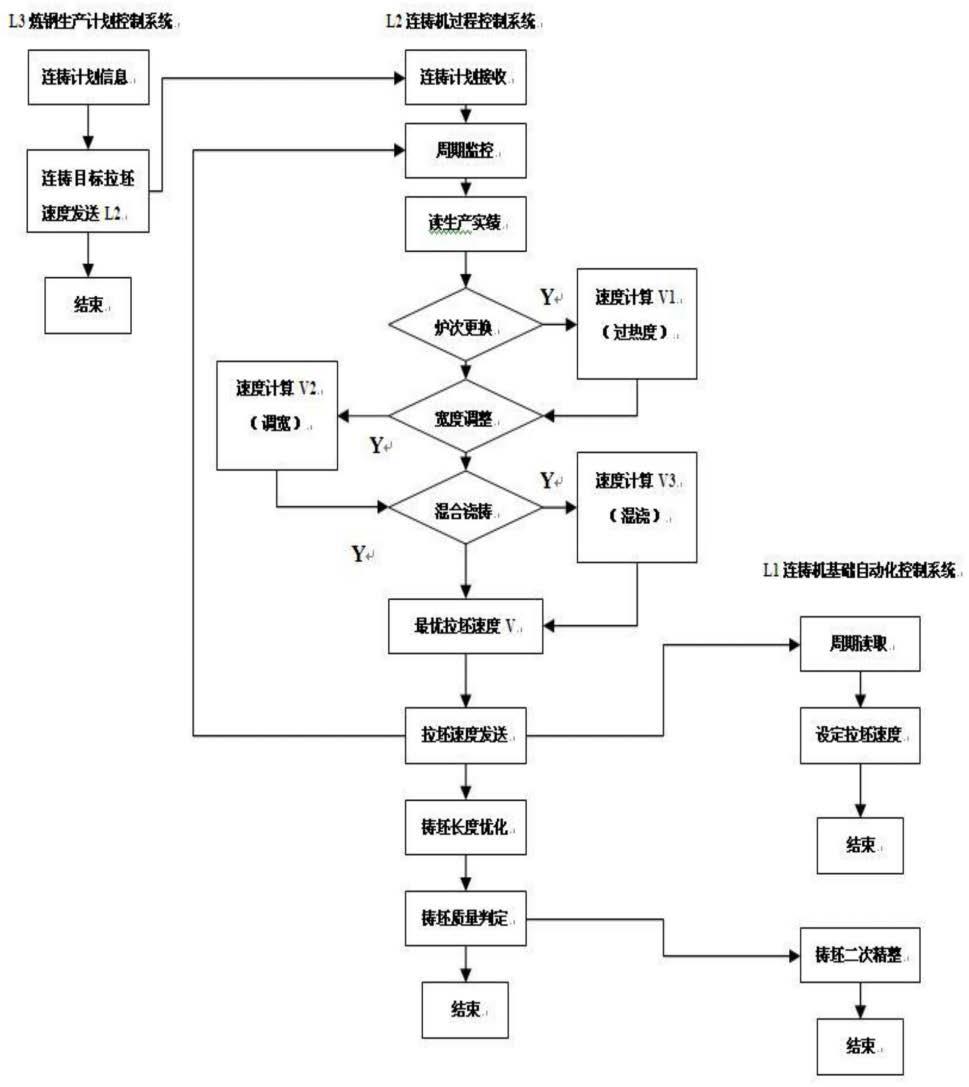
1.本发明涉及一种连铸机处理系统,具体涉及一种连铸机拉坯速度控制及二次处理方法,属于连铸机控制技术领域。
背景技术:2.连铸机生产过程中,由于钢水过热度、铸坯宽度调整、炉次更换、钢种混合浇铸、浸入式水口更换,水口堵塞等操作和异常情况,都需要对连铸机拉坯速度进行升降速控制。目前,现场的连铸机拉坯速度控制主要由操作人员根据工艺卡、炉次实绩以及现场生产状况进行人工干预手动调整,由于个人操作不同、理解不同,会导致拉坯速度手动控制中出现不稳定不及时,影响连铸生产节奏,造成结晶器内钢水液面的波动,影响连铸铸坯质量。
3.查新对比
4.经过查新,有一种连铸浇注的拉速控制方法(cn201810164343.x)、板坯连铸拉矫机实际拉速的优化方法(cn201310740520.1)、一种连铸铸坯速度检测装置及其检测方法(cn201010281751.7)、一种板坯连铸滞坯处理方法(cn201510635362.2)、一种板坯连铸漏钢预报控制方法(cn200710093907.7)等5个相关的发明专利。其中,一种连铸浇注的拉速控制方法(cn201810164343.x)、板坯连铸拉矫机实际拉速的优化方法(cn201310740520.1)、一种连铸铸坯速度检测装置及其检测方法(cn201010281751.7)三个发明专利是通过设备和方法计算,对实际拉坯速度和设定目标速度进行对比,通过预警、修正加速度,修正速度偏差,使得实际拉坯速度和设定目标拉速保持一致;一种板坯连铸滞坯处理方法(cn201510635362.2)是在连铸机发生滞坯异常事件后,在l1连铸基础自动化系统上,通过人工干预,手动调整流线二次冷却水量、不同的扇形段抬起、拉坯压力、拉坯速度等参数,对滞留在流道中的连铸铸坯的异常处理;一种板坯连铸漏钢预报控制方法(cn200710093907.7),对连铸拉坯速度的控制,仅为在连铸漏钢预报系统发出报警时,连铸拉坯速度直降至0.4m/min或铸机停止为止,不存在后续的连铸拉坯速度控制和异常处理。因此,迫切的需要一种新的方案解决上述技术问题。
技术实现要素:5.本发明正是针对现有技术中存在的问题,提供一种连铸机拉坯速度控制及二次处理系统,该技术方案通过接受l3炼钢生产计划控制系统下发的连铸拉坯速度目标值,结合连铸生产过程中的操作和异常事件,计算出最优的拉坯速度,发送给l1连铸基础自动化系统,对连铸机拉坯速度进行升降速控制,同时,将连铸机拉坯速度自动控制过程中异常事件发送给l2连铸机过程控制系统中的铸坯长度切割优化模块进行,铸坯长度优化,发送给连铸铸坯质量判定模块,对连铸铸坯进行质量判定,并将质量判定结果发送给l1连铸铸坯精整模块,对连铸铸坯进行二次处理。实现连铸机拉坯速度全过程自动控制,消除人为因素,提高铸坯的收得率和铸坯质量,提升连铸机自动控制水平。
6.为了实现上述目的,本发明的技术方案如下,一种连铸机拉坯速度控制及二次处
理系统,其特征在于,所述系统包括炼钢生产计划控制系统(l3)、连铸机过程控制系统(连铸l2),连铸机基础自动化系统以及连铸板坯精整控制系统,其中炼钢生产计划控制系统(l3)通过连铸机过程控制系统(连铸l2)连接连铸机基础自动化系统以及连铸板坯精整控制系统。其中炼钢生产计划控制系统根据炼钢生产全流程的生产状况,计算连铸生产计划的目标拉坯速度,并下发给连铸机过程控制系统(连铸l2);本发明涉及l3炼钢生产计划控制系统下发连铸生产目标拉坯速度,l2连铸机过程控制系统读取目标拉坯速度,结合连铸生产过程中炉次更换、中间包更换、铸坯宽度调整、钢种混合浇铸、浸入式水口更换等操作,以及钢水过热度、浸入式水口,连铸机停机等异常事件综合考虑,对连铸拉坯速度进行控制,同时,将有关连铸机拉坯速度变化过程中出现的异常事件,发送给l2连铸机过程控制中的连铸长度切割优化模块和连铸铸坯质量判定模块,进行连铸铸坯长度优化切割和铸坯质量判定,并将连铸铸坯质量判定结果发送给l1连铸机铸坯精整控制系统,对存在质量缺陷的连铸铸坯进行二次处理。
7.作为本发明的一种改进,所述连铸机过程控制系统包括连铸计划接收模块、连铸拉坯速度计算模块、铸坯切割长度优化模块以及铸坯质量判定模块,
8.其中连铸计划接收模块,用于接收连铸生产的目标拉坯速度;
9.连铸拉坯速度计算模块,根据连铸生产过程中的各种操作和异常事件,计算出最优的连铸机拉坯,并将计算结果发送给连铸机基础自动化系统(连铸l1),控制连铸机设备进行升、降速控制;铸坯切割长度优化模块,对于连铸机拉坯控制过程中出现的异常情况,对连铸铸坯切割长度进行优化,提高连铸铸坯收得率,并将计算结果发送给连铸铸坯质量判定模块;铸坯质量判定模块,对生产的连铸铸坯质量进行判定,并将结果发送给连铸铸坯精整控制系统(精整l1),连铸精整l1根据异常事件缺陷等级、异常事件对应铸坯长度,对缺陷区域精确定位,快速处理,减少对良坯的表面质量的影响,同时,减轻了连铸铸坯精整区域操作人员的劳动强度。
10.作为本发明的一种改进,该系统处理方法包括以下步骤:步骤1:连铸机目标拉坯速度下发,
11.炼钢生产计划控制系统(炼钢l3),根据炼钢生产状态,计算连铸机目标拉坯速度v
aim
,并下发给连铸过程控制系统(连铸l2),
12.步骤2:连铸机目标拉坯速度接收,
13.连铸机过程控制系统(连铸l2)接收来自炼钢生产计划控制系统(炼钢l3)的连铸机目标拉坯速度,
14.步骤3:周期读取连铸机生产实绩数据,根据生产实绩数据计算最优拉坯速度v:
15.1)是否有炉次更换:没有炉次更换,进入下一步;有炉次更换,根据下一炉次前工序出站温度,计算下一炉次钢水过热度tempsh,根据连铸工序的钢水温降速度,计算出第一个连铸浇铸时间tsh,根据连铸工序钢水通钢量和下一炉次钢水量,计算出第二个连铸浇铸时间tt,根据max[tsh,tt]计算出最小铸坯拉坯速度vmin,与当前实际拉坯速度vcurr比较,min[vmin,vcurr],得到本步骤的拉坯速度v1,进入一步;
[0016]
2)是否宽度调整:没有宽度调整,进入下一步;有宽度调整,计算出铸坯宽度调整值w,根据调宽设备油缸工作速度vequ,计算出宽度调整时间twid,再根据连铸宽度调整区间ladjust,计算出铸坯拉坯速度vwid,与当前实际拉坯速度vcurr比较,min[vwid,vcurr],
得到本步骤的拉坯速度v2,进入下一步;
[0017]
3)是否混合浇铸:没有混合浇铸,进入下一步;有混合浇铸,根据混合浇铸允许长度lmix,换算成钢水量weight,再根据当前实际的钢水通钢量weighttr,计算出铸坯拉坯速度vmix,与当前实际拉坯速度vcurr比较,min[vmix,vcurr],得到本步骤的拉坯速度v3,进入下一步;
[0018]
4)结合连铸机过程控制系统(连铸l2)接收的连铸机目标拉坯,根据各种情况计算出的连铸机拉坯速度大于连铸机目标拉坯速度v
aim
,采用计算拉坯速度v1作为最优的连铸机拉坯速度v,既经济高效,又安全可靠;如果根据各种情况计算出的连铸机拉坯速度小于连铸机目标拉坯速度v
aim
,则采用目标拉坯速度v
aim
作为最优的连铸机拉坯速度v;
[0019]
步骤4:拉坯速度下发,
[0020]
将最优的连铸机拉坯速度v下发给连铸基础自动化系统(连铸l1),控制连铸设备进行升、降速控制;并将升、降过程中的拉坯速度变化异常数据发送给连铸铸坯切割长度优化模块(连铸l2);
[0021]
步骤5:连铸铸坯切割长度优化,
[0022]
连铸机在升、降过程中的拉坯速度变化异常数据,会对连铸铸坯质量产生影响,后工序会对该部分铸坯进行切除,因此,根据拉坯速度变化异常事件对应的浇铸长度,首先将距离邻近的异常事件考虑在同一区域,并对可能存在质量缺陷的该区域在进行连铸铸坯切割时,考虑在连铸铸坯的头部、尾部或两块连铸铸坯的结合部,尽可能避免出现在连铸铸坯的中间部分,从而避免连铸铸坯线下多次人工切割所造良坯的损失,提高连铸机生产的收得率,并减少质量缺陷连铸铸坯数量。
[0023]
步骤6:连铸铸坯质量判定,
[0024]
根据连铸铸坯的实绩数据,以及连铸机生产实绩数据,对生产出的连铸铸坯质量进行判定,并将连铸铸坯质量数据发送给连铸铸坯二次精整系统(精整l1),连铸精整l1根据异常事件缺陷等级、异常事件对应铸坯长度,对缺陷区域精确定位,快速处理,减少对良坯的表面质量的影响,同时,减轻了连铸铸坯精整区域操作人员的劳动强度。
[0025]
相对于现有技术,本发明具有如下优点,l3炼钢生产计划控制系统下发连铸生产目标拉坯速度,l2连铸机过程控制系统读取目标拉坯速度,结合连铸生产过程中炉次更换、中间包更换、铸坯宽度调整、钢种混合浇铸、浸入式水口更换等操作,以及钢水过热度、浸入式水口,连铸机停机等异常事件综合考虑,计算出最优连铸拉坯速度,下发连铸l1,对连铸拉坯速度进行控制,实现连铸拉坯速度全过程自动控制,提升连铸机自动控制水平,消除人为因素,提高连铸铸坯的收得率,同时,将有关连铸机拉坯速度变化过程中出现的异常事件数据,发送给l2连铸机过程控制中的连铸长度切割优化模块和连铸铸坯质量判定模块,进行连铸铸坯长度优化切割和铸坯质量判定,并将连铸铸坯质量判定结果发送给l1连铸机铸坯精整控制系统,对存在质量缺陷的连铸铸坯快速、准确的定位,进行连铸铸坯二次处理,减少连铸铸坯精整区域操作人员劳动强度的同时,避免质量缺陷连铸铸坯进入后工序生产。
附图说明
[0026]
图1为本发明系统流程图;
[0027]
图2为系统结构示意图。
具体实施方式:
[0028]
为了加深对本发明的理解,下面结合附图对本实施例做详细的说明。
[0029]
实施例1:参见图1,一种连铸机拉坯速度控制及二次处理系统,所述系统包括炼钢生产计划控制系统(l3)、连铸机过程控制系统(连铸l2),连铸机基础自动化系统以及连铸板坯精整控制系统,其中炼钢生产计划控制系统(l3)通过连铸机过程控制系统(连铸l2)连接连铸机基础自动化系统以及连铸板坯精整控制系统。其中炼钢生产计划控制系统根据炼钢生产全流程的生产状况,计算连铸生产计划的目标拉坯速度,并下发给连铸机过程控制系统(连铸l2),所述连铸机过程控制系统包括连铸计划接收模块、连铸拉坯速度计算模块、铸坯切割长度优化模块以及铸坯质量判定模块,其中连铸计划接收模块,用于接收连铸生产的目标拉坯速度;连铸拉坯速度计算模块,根据连铸生产过程中的各种操作和异常事件,计算出最优的连铸机拉坯,并将计算结果发送给连铸机基础自动化系统(连铸l1),控制连铸机设备进行升、降速控制;铸坯切割长度优化模块,对于连铸机拉坯控制过程中出现的异常情况,对连铸铸坯切割长度进行优化,提高连铸铸坯收得率,并将计算结果发送给连铸铸坯质量判定模块;铸坯质量判定模块,对生产的连铸铸坯质量进行判定,并将结果发送给连铸铸坯精整控制系统(精整l1),对连铸铸坯进行二次处理,减少连铸铸坯质量缺陷。
[0030]
该系统处理方法包括以下步骤:步骤1:连铸机目标拉坯速度下发,
[0031]
炼钢生产计划控制系统(炼钢l3),根据炼钢生产状态,计算连铸机目标拉坯速度v
aim
,并下发给连铸过程控制系统(连铸l2),
[0032]
步骤2:连铸机目标拉坯速度接收,
[0033]
连铸机过程控制系统(连铸l2)接收来自炼钢生产计划控制系统(炼钢l3)的连铸机目标拉坯速度,
[0034]
步骤3:周期读取连铸机生产实绩数据,根据生产实绩数据计算最优拉坯速度v:
[0035]
1)是否有炉次更换:没有炉次更换,进入下一步;有炉次更换,根据下一炉次前工序出站温度,计算下一炉次钢水过热度tempsh,根据连铸工序的钢水温降速度,计算出第一个连铸浇铸时间tsh,根据连铸工序钢水通钢量和下一炉次钢水量,计算出第二个连铸浇铸时间tt,根据max[tsh,tt]计算出最小铸坯拉坯速度vmin,与当前实际拉坯速度vcurr比较,min[vmin,vcurr],得到本步骤的拉坯速度v1,进入一步;
[0036]
2)是否宽度调整:没有宽度调整,进入下一步;有宽度调整,计算出铸坯宽度调整值w,根据调宽设备油缸工作速度vequ,计算出宽度调整时间twid,再根据连铸宽度调整区间ladjust,计算出铸坯拉坯速度vwid,与当前实际拉坯速度vcurr比较,min[vwid,vcurr],得到本步骤的拉坯速度v2,进入下一步;
[0037]
3)是否混合浇铸:没有混合浇铸,进入下一步;有混合浇铸,根据混合浇铸允许长度lmix,换算成钢水量weight,再根据当前实际的钢水通钢量weighttr,计算出铸坯拉坯速度vmix,与当前实际拉坯速度vcurr比较,min[vmix,vcurr],得到本步骤的拉坯速度v3,进入下一步;
[0038]
4)结合连铸机过程控制系统(连铸l2)接收的连铸机目标拉坯,根据各种情况计算出的连铸机拉坯速度大于连铸机目标拉坯速度v
aim
,采用计算拉坯速度v1作为最优的连铸
机拉坯速度v,既经济高效,又安全可靠;如果根据各种情况计算出的连铸机拉坯速度小于连铸机目标拉坯速度v
aim
,则采用目标拉坯速度v
aim
作为最优的连铸机拉坯速度v;
[0039]
步骤4:拉坯速度下发,
[0040]
将最优的连铸机拉坯速度v下发给连铸基础自动化系统(连铸l1),控制连铸设备进行升、降速控制;并将升、降过程中的拉坯速度变化异常数据发送给连铸铸坯切割长度优化模块(连铸l2);
[0041]
步骤5:连铸铸坯切割长度优化,
[0042]
连铸机在升、降过程中的拉坯速度变化异常数据,会对连铸铸坯质量产生影响,后工序会对该部分铸坯进行切除,因此,根据拉坯速度变化异常事件对应的浇铸长度,首先将距离邻近的异常事件考虑在同一区域,并对可能存在质量缺陷的该区域在进行连铸铸坯切割时,考虑在连铸铸坯的头部、尾部或两块连铸铸坯的结合部,尽可能避免出现在连铸铸坯的中间部分,从而避免连铸铸坯线下多次人工切割所造良坯的损失,提高连铸机生产的收得率,并减少质量缺陷连铸铸坯数量。
[0043]
步骤6:连铸铸坯质量判定,
[0044]
根据连铸铸坯的实绩数据,以及连铸机生产实绩数据,对生产出的连铸铸坯质量进行判定,并将连铸铸坯质量数据发送给连铸铸坯二次精整系统(精整l1),连铸精整l1根据异常事件缺陷等级、异常事件对应铸坯长度,对缺陷区域精确定位,快速处理,减少对良坯的表面质量的影响,同时,减轻了连铸铸坯精整区域操作人员的劳动强度。
[0045]
安装和工作过程:参照图1—图2,随着连铸生产工艺和生产要求的不断提高,对炼钢转炉和连铸之间的钢水生产匹配控制要求也在不断增加,连铸拉坯速度控制在连铸生产过程中的重要性显得更加重要。连铸机生产过程中,由于钢水过热度、铸坯宽度调整、炉次更换、钢种混合浇铸、浸入式水口更换,水口堵塞等操作和异常情况,都需要对连铸机拉坯速度进行升降速控制。目前,现场的连铸机拉坯速度控制主要由操作人员根据工艺卡、炉次实绩以及现场生产状况进行人工干预手动调整,由于个人操作不同、理解不同,会导致拉坯速度手动控制中出现不稳定不及时,影响连铸生产节奏,造成结晶器内钢水液面的波动,影响连铸铸坯质量。本发明提供了一种连铸机拉坯速度的控制及二次处理方法,l3炼钢生产计划控制系统下发连铸生产目标拉坯速度,l2连铸机过程控制系统读取目标拉坯速度,结合连铸生产过程中炉次更换、中间包更换、铸坯宽度调整、钢种混合浇铸、浸入式水口更换等操作,以及钢水过热度、浸入式水口,连铸机停机等异常事件综合考虑,对连铸拉坯速度进行控制,同时,将有关连铸机拉坯速度变化过程中出现的异常事件,发送给l2连铸机过程控制中的连铸长度切割优化模块和连铸铸坯质量判定模块,进行连铸铸坯长度优化切割和铸坯质量判定,并将连铸铸坯质量判定结果发送给l1连铸机铸坯精整控制系统,对存在质量缺陷的连铸铸坯进行二次处理。实现连铸机拉坯速度全过程自动控制,消除人为因素,提高铸坯的收得率和铸坯质量,提升连铸机自动控制水平。
[0046]
需要说明的是上述实施例,并非用来限定本发明的保护范围,在上述技术方案的基础上所作出的等同变换或替代均落入本发明权利要求所保护的范围。