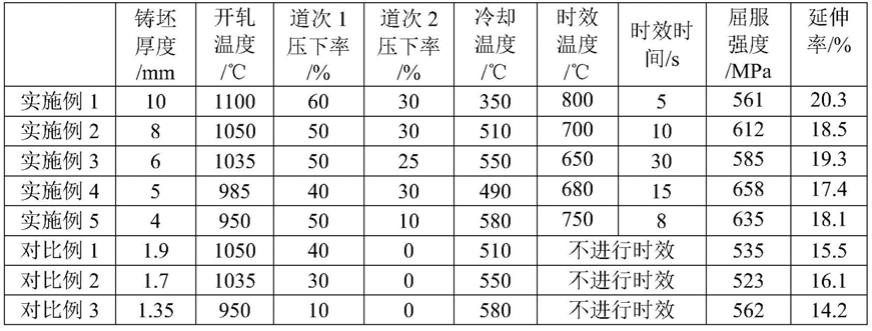
1.本发明属于薄规格微合金高强钢制造领域,具体涉及一种生产微合金高强钢的方法。
背景技术:2.微合金高强钢是一种量大面广的钢铁材料,广泛应用于汽车、集装箱、工程机械等领域。为实现薄规格微合金高强钢的生产,一般采用传统热连轧+冷轧的方式生产,存在制造流程长、工序复杂、制造成本高等问题。中国发明专利cn1962099a提出了一种基于薄板坯连铸连轧流程微合金高强钢的生产方法,通过薄板坯连铸机,浇铸出厚度≤60mm的连铸坯,再通过5-7道次热轧,实现了最薄厚度1.5mm薄规格微合金高强钢的生产。为进一步缩短制造流程,中国发明专利cn103305753b提出了一种薄带连铸低碳微合金钢带制造方法,采用双辊连铸机,浇铸出厚度为1-5mm的薄带,然后再通过一个道次的轧制,压下率为20-50%,实现0.5-3.0mm薄规格微合金高强钢的生产。中国发明专利cn103305759b也公开了一种薄带连铸700mpa级高强耐候钢制造方法,在低碳钢的基础上添加了nb、v、ti等微合金元素中的几种。采用薄带铸轧方式生产薄规格微合金高强钢,制造流程大幅度缩短,节能减排效果显著。
3.但是,已有生产实践表明,在薄带铸轧亚快速凝固工艺条件下,再加上轧制总变形量相对较小,绝大部分微合金化元素在钢中以过饱和的固溶形式存在,未能形成析出相,微合金元素的析出强化作用未能得到有效发挥,极大限制了其强化效果。为解决这一问题,中国发明专利cn103305754a提出一种时效硬化薄带连铸低碳微合金钢带的制造方法,利用双辊连铸机铸造厚度为1-5mm的铸带,其成分为c:0.01-0.25%,si:≤0.4%,mn:0.6-2.0%,p:≤0.015%,s:≤0.01%,n:≤0.012%,此外还包含nb、v、ti、mo中的至少一种,nb:0.005-0.1%,v:0.005-0.1%,ti:0.005-0.1%,mo:0.05-0.5%;经过薄带铸轧冷却后卷取,卷取温度550-700℃;之后再进行离线时效硬化处理,时效温度500-800℃,加热时间0.1-30分钟。通过时效处理,获得铌碳氮化物等纳米级析出物,提高产品的强度。但该方法采用离线时效处理的方式,需要将钢卷从室温重新加热至所需要的时效温度,使得制造过程变得复杂,同时增加了能耗和制造成本,降低了薄带铸轧流程“近终形、超短流程、低能耗、低成本”的优势。
技术实现要素:4.本发明解决的技术问题是提供一种生产微合金高强钢的方法,该方法能够解决传统热轧+冷轧流程或者薄板坯连铸连轧流程生产薄规格微合金高强钢制造流程长、工序复杂,以及现有薄带铸轧流程生产微合金高强钢无法完全发挥微合金元素的析出强化作用,需要进行离线时效处理等问题。
5.为实现上述目的,本发明第一方面提供如下技术方案:
6.一种生产微合金高强钢的方法,所述方法包括:
7.1)采用连铸机将钢水浇铸出一定厚度的超薄连铸坯;
8.2)将所述超薄连铸坯连续进行2个机架的热轧,实现铸态组织的调控,并轧至成品的厚度,得到钢带;
9.3)采用冷却装置对所述钢带进行控制冷却,根据产品性能要求获得所需要的微观组织后进入在线时效装置,加热至一定的时效温度;
10.4)使完成所述加热后的钢带进入卷取机进行高温卷取,卷取完后下线缓慢冷却,得到所述微合金高强钢。
11.作为本发明的一个实施例,所述超薄连铸坯的厚度为2-15mm,优选为4-10mm;
12.所述成品的厚度为0.9-4.5mm,优选为1.2-3.5mm。
13.作为本发明的一个实施例,所述热轧的道次压下率为10-60%,其中第一道次优选40-60%,第二道次优选10-40%。
14.作为本发明的一个实施例,所述控制冷却的冷却速率为10-300℃/s,冷却段的出口温度为300-600℃。
15.作为本发明的一个实施例,所述在线时效装置的加热方式为电磁感应加热或辐射加热,优选电磁感应加热,加热速率50-300℃/s,所述时效温度为650-800℃,时效时间5-30s。
16.作为本发明的一个实施例,所述微合金高强钢的化学成分重量百分比为:c0.02-0.06%,si≤0.5%,mn 0.5-2.0%,p≤0.15%,s≤0.01%,n≤0.008%,以及nb、v、ti中至少一种,其中nb 0.01-0.1%,v 0.01-0.1%,ti 0.01-0.1%,余量为fe。
17.本发明提供的上述技术方案至少带来的有益效果:
18.(1)本发明采用连铸机浇铸出超薄连铸坯,仅需2个道次的热轧即可实现薄规格微合金高强钢的生产,与传统的热轧+冷轧流程相比,制造流程大幅度缩短;
19.(2)与现有薄带铸轧流程,本发明通过适当提高铸坯厚度,然后将原有的单道次轧制改为双道次轧制,通过增大轧制总变形量,解决了现有流程对铸态组织调控能力不足、奥氏体晶粒相对粗大的问题。同时,通过增加形变量,也提高了形变诱导微合金化元素析出的能力;
20.(3)本发明采用在线时效处理装置,配合高温卷取和钢卷下线缓慢冷却工艺,促使过饱和的微合金元素形成纳米级的析出物,从而充分发挥微合金化元素的析出强化作用,与传统的离线时效处理工艺相比,提高了生产的连续性和生产效率,同时充分利用带钢的余热,仅需少量补热即可达到时效处理的效果,降低了制造过程的能耗和成本。
附图说明
21.图1为本发明的生产微合金高强钢的方法的装置示意图。
22.附图标记说明如下:
23.1、钢包;2、中间包;3、连铸机;4、双机架四辊热轧机;5、冷却装置;6、在线时效处理装置;7、高速飞剪;8、卷取机。
具体实施方式
24.为使本发明的目的、技术方案和优点更加清楚,下面将对本发明实施方式作进一
步地详细描述。
25.以下实施例1-5、对比例1-3采用本发明的方法生产微合金高强钢,生产装置如图1所示。其中,钢包1中的钢水经中间包2,进入连铸机3,浇铸出超薄连铸坯,连铸机进入双机架四辊热轧机4进行两道次轧制,从轧机出来的带钢进入冷却装置5进行控制冷却,通过冷却温度的控制获得所需要的显微组织。带钢从冷却装置出来后直接进入在线时效处理装置6进行加热和保温,然后进入卷取机8进行高温卷取。当钢卷达到预定重量后,采用高速飞剪7对带钢进行分切。
26.实施例及对比例的化学成分如表1所示,主要工艺参数及性能如表2所示。由表中数据可知,实施例2与对比例1、实施例3与对比例2、实施例5与对比例3分别具有相同的钢水组成和工艺参数,而采用本发明的方案所制备的微合金高强钢比采用对比例方案所制备的微合金高强钢具有更高的屈服强度和延伸率。
27.表1钢水化学成分(wt.%)
[0028] csimnvnbtinsp实施例10.020.22.00.1//0.070.0030.05实施例20.030.31.8/0.1 0.0450.0020.12实施例30.040.41.6/ 0.10.0030.0040.08实施例40.050.51.40.010.050.010.060.0050.10实施例50.060.200.50.050.010.050.050.0020.06对比例10.030.31.8/0.1 0.0450.0020.12对比例20.040.41.6/ 0.10.0030.0040.08对比例30.060.200.50.050.010.050.050.0020.06
[0029]
表2主要工艺参数及性能
[0030][0031]
以上所述仅为本发明的较佳实施例,并不用以限制本发明,凡在本发明的精神和原则之内,所作的任何修改、等同替换、改进等,均应包含在本发明的保护范围之内。