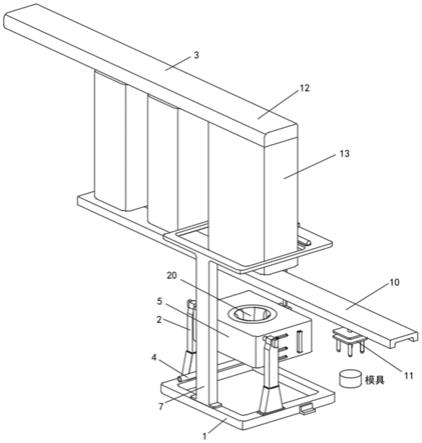
1.本发明属于合金轮毂制造技术领域,尤其是涉及一种铝合金轮毂液固增压铸造成形设备。
背景技术:2.在汽车工业中,合金轮毂是轮从它们的制造合金的铝或镁。合金是金属和其他元素的混合物。与纯金属相比,它们通常提供更高的强度,纯金属通常更柔软且更具延展性,铝或镁合金通常在相同强度下更轻,提供更好的导热性,并且通常具有比钢轮更好的外观。尽管钢是车轮生产中最常用的材料,是铁和碳的合金。
3.目前较为优良的锻造方法是采用倾斜式铸造,对比于传统的制造方式具有结构均匀,质量稳定,合格率高的优点,但传统的倾斜方式是采用液压杆拖动来实现所谓的倾斜,该方式具有两个显著的缺点,第一就是倾斜的角度控制不易,且角度也很难大范围调节,第二就是功能较为单一,只能进行倾斜作业和回位,无法进一步配合铸造作业的实施。
4.为此,我们提出一种铝合金轮毂液固增压铸造成形设备来解决上述问题。
技术实现要素:5.本发明的目的是针对上述问题,提供一种可以实现平顺倾斜和微振动两种模式的铝合金轮毂液固增压铸造成形设备。
6.为达到上述目的,本发明采用了下列技术方案:一种铝合金轮毂液固增压铸造成形设备,包括基本台架、支撑臂、冷气输入系统及浇筑输入系统,所述支撑臂设有多个并连接于基本台架上用作支撑,基本台架上设有操作台,所述操作台与支撑臂转动连接,所述支撑臂靠近基本台架的一端边缘处设置,且操作台与支撑臂的连接点也偏离操作台的中心点;所述基本台架上还连接有悬吊架,所述悬吊架上设置有悬吊机构用于上下移动,操作台的一端与悬吊机构相连接;所述操作台内设有夹持机构,其底部与浇筑输入系统相连接,操作台的上方横穿有铸造生产线,铸造生产线中循环活动有调运机构,所述夹持机构用于配合调运机构来对轮毂铸造模具进行分段夹持固定,所述冷气输入系统位于铸造生产线的上方。
7.在上述的铝合金轮毂液固增压铸造成形设备中,所述铸造生产线的上方设有主管道、多个副管道,所述主管道与冷气输入系统连接,用于冷气的输送,多个所述副管道连接在主管道上用于冷气分段输送,所多个所述副管道依次沿铸造生产线布设。
8.在上述的铝合金轮毂液固增压铸造成形设备中,所述主管道上设有多个备用的连接接口,连接接口在闲置时安装密封板密封。
9.在上述的铝合金轮毂液固增压铸造成形设备中,所述副管道中设有多个可主动转动的导流板,多个导流板可对向转动用于调节冷气流速。
10.在上述的铝合金轮毂液固增压铸造成形设备中,所述悬吊机构包括设置在悬吊架上的驱动电机、链条和固定轮、移动轮,所述驱动电机用于驱动链条转动,链条贯穿悬吊架
的面板与操作台的端面固定连接,所述链条通过固定轮接触,所述移动轮可在操作台的端面上移动,并可用于和固定轮对接,所述链条与支撑臂共同维持操作台的稳定和姿态。
11.在上述的铝合金轮毂液固增压铸造成形设备中,所述链条的端面镂空,其镂空的间隔呈圆柱状,通过圆柱状的镂空间隔配合固定轮和移动轮。
12.在上述的铝合金轮毂液固增压铸造成形设备中,所述固定轮、移动轮的端面均呈锯齿状,齿状结构与链条上的镂空格对应锲合,链条在固定轮的锯齿状结构上活动,所述移动轮可活动与固定轮对接,从而可对链条进行固定。
13.在上述的铝合金轮毂液固增压铸造成形设备中,所述夹持机构包括设于操作台上端面上的嵌孔,嵌孔用于放置轮毂铸造模具,嵌孔的底部与浇筑输入系统相连接,所述操作台内部有腔室,嵌孔中设有多个夹持板,所述腔室内活动连接有异形块,夹持板背部设有弹簧和导杆,导杆贯穿到腔室中与异形块相连接,所述异形块带动夹持板进行活动。
14.在上述的铝合金轮毂液固增压铸造成形设备中,所述夹持板的上端面呈圆弧状,便于轮毂铸造模具进行在嵌孔中的调运。
15.在上述的铝合金轮毂液固增压铸造成形设备中,所述调运机构包括设置在铸造生产线上的第一液压杆,所述第一液压杆下端固定连接有连接板,连接板上连接有多根立柱,立柱上固定连接有气包膜,所述立柱上还设有压板用于挤压气包膜,所述气包膜为硬质密封布材质,所述气包膜内部填充有密封气体,所述压板上端固定连接有第二液压杆用于带动压板对气包膜进行活动挤压用于夹持轮毂铸造模具。
16.与现有的技术相比,本铝合金轮毂液固增压铸造成形设备的优点在于:
17.1、本发明通过设置的固定轮、移动轮和链条、支撑臂的配合,以达到利用链条和支撑臂对操作台形成的三点支撑结构,配合链条的长短改变来调节操作台的倾斜角度的效果,从而使得操作台与传统的液压驱动相比有更大的调节幅度,最大可以达到90度,同时利用固定轮、移动轮的相互配合,实现平顺倾斜和微振动两种模式,用于更好的配合进行铸造作业。
18.2、本发明通过设置的冷气输入系统和主管道、副管道的配合,以达到在传统水冷的基础上,记忆布开发出长效的气冷冷却的效果,从而摆脱了水冷所需要的长时间接触的弊端,从而更好的配合铸造生产线的高效运转,同时不影响传统的冷却效果。
附图说明
19.图1是本发明提供的一种铝合金轮毂液固增压铸造成形设备的外部结构示意图;
20.图2是图1的俯视结构示意图;
21.图3是图1的另一视角结构示意图;
22.图4是图1中操作台的结构示意图;
23.图5是图4的俯视结剖示意图;
24.图6是图5中夹持板的结构示意图;
25.图7是图3气包膜的初始状态示意图;
26.图8是图3气包膜的作业状态示意图;
27.图9是图3中b处的局部放大图;
28.图10是图1中主管道、副管道连接示意图;
29.图11是图1中固定轮、移动轮的连接示意图;
30.图12是图11中链条的结构示意图;
31.图13是图2中a处的局部放大图。
32.图中,1基本台架、2支撑臂、3冷气输入系统、4浇筑输入系统、5操作台、6压板、7悬吊架、8悬吊机构、9夹持机构、10铸造生产线、11调运机构、12主管道、13副管道、14密封板、15导流板、16驱动电机、17链条、18固定轮、19移动轮、20嵌孔、21夹持板、22异形块、23弹簧、24导杆、25第一液压杆、26连接板、27立柱、28气包膜。
具体实施方式
33.以下实施例仅处于说明性目的,而不是想要限制本发明的范围。
34.实施例
35.如图1-3所示,一种铝合金轮毂液固增压铸造成形设备,包括基本台架1、支撑臂2、冷气输入系统3及浇筑输入系统4,冷气输入系统3负责冷却作业,浇筑输入系统4负责进行浇筑模具作业,支撑臂2设有多个并连接于基本台架1上用作支撑,支撑臂2固定在基本台架1的底部的边缘处,竖直设置且用作支撑其余部件,支撑臂2采用干强度合金部件制成,且其可活动安装在基本台架1上的不同部位。
36.基本台架1上设有操作台5,具体的来说操作台5设置在基本台架1的上方,且距离要大于操作台5尺寸的最大长度,这样做的目的在于在操作台5进行角度偏转时其不受到地面距离的限制和影响,操作台5与支撑臂2转动连接,从而使得操作台5可与进行转动活动,其连接部件具体的采用活动连接轴的方式,支撑臂2靠近基本台架1的一端边缘处设置,且操作台5与支撑臂2的连接点也偏离操作台5的中心点,具体来说是位于操作台5的侧面后部的顶点处,这样做的好处是使得操作台5可以最大范围的进行翻转;
37.基本台架1上还连接有悬吊架7,悬吊架7具体安装在基本台架1的后部,基本台架1为口字型,其底部与地面可以永久固定也可以半永久固定用于提高稳定性,在安装时基本台架1的前端为主要安装部位,是为了平衡其实际的重量,使其总体处于稳定的平衡状态,悬吊架7上设置有悬吊机构8用于上下移动操作台5,通过悬吊机构8的控制来,操作台5的一端与悬吊机构8相连接,连接方式可以是固定连接也可以是活动部件进行连接。
38.如图13所示,悬吊机构8包括设置在悬吊架7上的驱动电机16、链条17和固定轮18、移动轮19,具体的来说驱动电机16安装在一侧,随后通过固定的块体来架设转轴,在转轴上固定有卷棍,而驱动电机16启动就可以直接带动卷棍进行转动,驱动电机16用于驱动链条17转动,卷棍直接与链条17连接,所以卷棍直接控制链条17的收放,链条17贯穿悬吊架7的面板与操作台5的端面固定连接,链条17的贯穿部位形成一个缺口,缺口与链条17相匹配使其可以只有的进出活动,链条17通过固定轮18接触,固定轮18设置在缺口的一侧,用于链条17带动固定轮18滚动,从而使其可以平稳的下放和回收。
39.如图11-12所示,移动轮19可在操作台5的端面上移动,移动轮19则设置在缺口的另一侧,与固定轮18相对,悬吊架7上设有多个滑槽,固定轮18通过这些滑槽在悬吊架7上进行滑动,滑动的驱动力来自第三液压杆,第三液压杆固定在悬吊架7上,用于推动移动轮19进行前后移动与固定轮18对接,主要用途是与固定轮18进行配合对接,固定轮18、移动轮19的端面均呈锯齿状,也就是说固定轮18、移动轮19之间是可以相互卡紧的,移动轮19在移动
的过程中进行与固定轮18的啮合分离动作,链条17在固定轮18的锯齿状结构上活动,移动轮19可活动与固定轮18对接,从而可对链条17进行固定,链条17与支撑臂2共同维持操作台5的稳定和姿态,通过链条17来配合支撑臂2从而形成三支点,通过链条17控制的顶端支点来达到调节角度的问题,链条17的端面镂空,其镂空的间隔呈圆柱状从而使其表面保持圆润状,在配合固定轮18、移动轮19时可以较为顺畅,不会卡顿,通过圆柱状的镂空间隔配合固定轮18和移动轮19,齿状结构与链条17上的镂空格对应锲合;
40.链条17与固定轮18、移动轮19的配合还有可以第二种形式,即通过控制驱动电机16的转动方式和移动轮19与链条17之间的距离来达到一个震动模式的切换效果,在驱动电机16匀速转动下放或回收链条17时,移动轮19通过控制与链条17的接触面的深浅程度从而达到与链条17上镂空的间隔的接触力度的效果,从而使链条17在下放的过程中不断的进行轻微的震动,而此震动的好处在于,不仅配合倾斜式的铸造方法,同时也使其铸造模具内部更加的均匀散布,有效的提高了产品的合格率和质量,从而更好的生产合金轮毂。
41.如图4-6所示,操作台5内设有夹持机构9,其底部与浇筑输入系统4相连接,浇筑输入系统4是一个外接的现有技术,其主要用途在于将需要铸造的原料送入模具中,本方案中图示并未示意二者是如何结合的,但由于是现有技术的直接应用,因此在此不再过多的赘述,夹持机构9包括设于操作台5上端面上的嵌孔20,嵌孔20就是用于放置模具的,而模具是通过铸造生产线10调运过来的,嵌孔20用于放置轮毂铸造模具,也就是说定型生产就是直接在嵌孔20内完成的,嵌孔20的底部与浇筑输入系统4相连接以便于在嵌孔20内直接进行铸造作业,操作台5内部有腔室用于匹合嵌孔20,嵌孔20中设有多个夹持板21,夹持板21可以活动,从而使其可以夹持固定内部的模具,夹持板21的上端面呈圆弧状,便于轮毂铸造模具进行在嵌孔20中的调运,具体来说是便于放入和取出,腔室内活动连接有异形块22,异形块22呈水滴状,一端平整一端凸出,凸出的一端就是用于推动夹持板21的,夹持板21背部设有弹簧23和导杆24,弹簧23的内部实际还有伸缩杆,安装在嵌孔20内,夹持板21的背部凹空用于放置上述部件,导杆24贯穿到腔室中与异形块22相连接,异形块22的转动源头在于设置在操作台5内部内部的电机,由于该部分也是属于常规技术,因此不在赘述,异形块22带动夹持板21进行活动,从而配合弹簧23使得夹持板21伸缩或复位。
42.如图7-10所示,操作台5的上方横穿有铸造生产线10,铸造生产线10就是一个单纯的货运生产线,内部部件可以自动运转移动,铸造生产线10中循环活动有调运机构11,夹持机构9用于配合调运机构11来对轮毂铸造模具进行分段夹持固定,调运机构11用于货运,而夹持机构9用于偏转固定,调运机构11包括设置在铸造生产线10上的第一液压杆25,第一液压杆25就是用于驱动调运伸缩的,将模具直接拿出或放入,第一液压杆25下端固定连接有连接板26,连接板26上连接有多根立柱27,立柱27设置有多根,不限制数量,立柱27上固定连接有气包膜28,立柱27上还设有压板6用于挤压气包膜28改变其内部的气体分布位置,气包膜28为硬质密封布材质,且气包膜28采用的是抗高温材质受热不易损毁,气包膜28内部填充有密封气体,通过密封气体的变化来带动气包膜28外部形态的变化,从而使得其改变外部形状,来对模具进行夹持作业,压板6上端固定连接有第二液压杆用于带动压板6对气包膜28进行活动挤压用于夹持轮毂铸造模具。
43.冷气输入系统3位于铸造生产线10的上方,铸造生产线10的上方设有主管道12、多个副管道13,主管道12用于输入和引流冷气,而副管道13则负责进行具体的冷却吹拂,副管
道13中设有多个可主动转动的导流板15,多个导流板15可对向转动用于调节冷气流速,从而使得在导流板15偏转后改变对下方模具的吹拂力度,主管道12与冷气输入系统3连接,用于冷气的输送,多个副管道13连接在主管道12上用于冷气分段输送,主管道12上设有多个备用的连接接口,连接接口在闲置时安装密封板14密封,所多个副管道13依次沿铸造生产线10布设,相比对传统的水冷来说,虽然单一的水冷效果好耗能少,但其也需要一定的时间来进行作业,就会导致作业时间偏长,明显不适宜本方案,因此采用的双结合的方式进行操作,先进行水冷作业(图中未示出),中途提升后进行主动的冷气冷却,这样既保证了冷却的速度,也不影响实际生产的效率。
44.尽管本文较多地使用了基本台架1、支撑臂2、冷气输入系统3、浇筑输入系统4、操作台5、压板6、悬吊架7、悬吊机构8、夹持机构9、铸造生产线10、调运机构11、主管道12、副管道13、密封板14、导流板15、驱动电机16、链条17、固定轮18、移动轮19、嵌孔20、夹持板21、异形块22、弹簧23、导杆24、第一液压杆25、连接板26、立柱27、气包膜28等术语,但并不排除使用其它术语的可能性。使用这些术语仅仅是为了更方便地描述和解释本发明的本质;把它们解释成任何一种附加的限制都是与本发明精神相违背的。