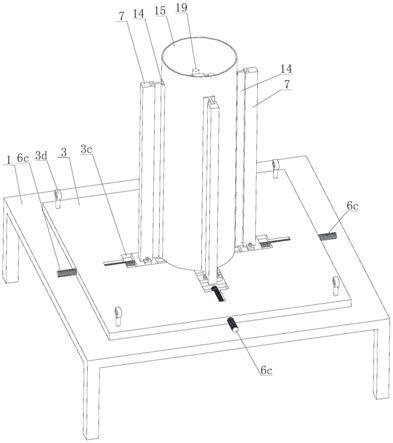
1.本发明涉及一种精密铸造方法,特别涉及一种薄壁回转体铝合金铸件的无箱浇注制造方法,属于精密铸造技术领域。
背景技术:2.砂型是铸造生产过程中用原砂、黏结剂及其他辅料做成的铸件型腔,传统的工艺要使用砂箱完成砂型的制作。被舂紧在上、下砂箱中的型砂与上、下砂箱一起,分别被称为上砂型和下砂型。将模样从砂型中取出后,留下的空腔称为型腔。
3.型芯俗称“泥芯”,铸造时用以形成铸件的内部结构,常由原砂和粘结剂配成的芯砂,在芯盒中手工或机器制成。芯盒通常用木材或金属制成,在浇铸前将型芯装置在砂型内,金属液浇入冷凝后,出砂时将它清除,在铸件中即可形成空腔。
4.回转体的铸件泥芯为圆柱体,由于模具分型方式有限,导致泥芯的圆柱度误差较大,缺乏有效的控制手段,影响成品铸件的内壁圆整度。传统的泥芯修型是通过尺寸样板、锉刀、卡尺进行修复,对于精度要求高的回转体的泥芯,在泥芯开模时,人工的力度和开模频率无法控制,加上模具本身的误差,泥芯的紧实度误差,都会导致泥芯本身圆柱度的误差,满足不了高精度的要求,一般泥芯涂刷都是人工涂刷、人工浸涂和人工喷涂,涂料的厚度层0.2-0.5mm不等,会加大泥芯的尺寸误差。
5.在型腔中浇注金属液,冷却后形成金属铸件,取得金属铸件前,必须将砂型清理掉。传统砂型清理分两种,一是人工清砂,二是机械震动清砂,前者需要利用行车吊起砂箱到指定的落砂点,然后合几人之力用锤子将砂型敲碎,费时费力,且容易对薄壁铸件造成损伤;根据砂型大小不等,用时也要几十分钟到几个小时不等,效率低,人工成本高。后者直接将砂箱调入震砂机内,开动机器,通过震动结合人工辅助进行清砂处理,虽效率高,但是投资成本高,需要购买设备,建立一条落砂生产线,对厂房的使用面积有一定的要求。对于小批量多品种的铸造规模就有所限制。
6.铸造铝合金热处理强化通常采用固溶处理及时效处理,传统上将要热处理的铸件一起堆放在框架内,铸件和铸件之间会因为堆放的数量或多或少和摆放不平稳等问题发生变形。为了生产用电的经济考虑,每个热处理的炉次都会满装;这样会导致铸件发生变形,尤其厚度为5mm以下的薄壁回转体铝合金铸件的变形风险更大,变形的方向无法预计。
7.当发生变形时,只能通过人工整形和实时测量来校正,因为固溶处理后,铸件表面的温度达到沸水温度,人工在整形和测量就要面对被烫伤的危险,而测量工具在较高温度下也会有所误差,影响整形的精准度。再者就是如果有条件,通过压机整形,就需要做不同直径的整形工装,这就加大了成本投入,工装和设备需要定期进行维护保养。
技术实现要素:8.本发明的目的在于,克服现有技术中存在的问题,提供一种薄壁回转体铝合金铸件的无箱浇注制造方法,可以大大减少模具的使用及工装的成本,简化制造工艺,使用简单
的工装对制造的全过程进行提升,提高产品质量。
9.为解决以上技术问题,本发明的一种薄壁回转体铝合金铸件的无箱浇注制造方法,依次包括如下步骤,s1、在工作台上安装无箱浇注用工装;s2、砂型造型:将产品模具和浇冒系统模具与造型砂结合,等造型砂固化后取出产品模具和浇冒系统模具,形成产品的外形和浇冒系统的空腔砂型;s3、制芯:将造型砂填入产品芯盒内,舂实后,拆分芯盒,得到泥芯;s4、合金液熔炼;s5、在工作台上处理泥芯上的披缝并上涂料;s6、将砂型与泥芯进行组合,确认砂型内壁与泥芯外壁之间的型腔间隙达到图纸尺寸要求;s7、在工作台上进行无箱浇注,将合金液注入型腔中,冷却成型后进行清砂,得到带浇冒系统的铸件;s8、去除铸件上的浇冒系统,打磨铸件的外观;s9、对铸件进行固溶热处理;s10、对铸件进行旋转挤压整形,使得铸件达到符合尺寸公差范围内的铸态;s11、将铸件放入时效炉进行时效处理。
10.作为本发明的改进,s1中所述无箱浇注用工装包括固定在工作台上的水平底板,水平底板的中心设有圆形的底板沉孔,所述底部沉孔的中心设有底板中心孔,所述底板沉孔的底壁上通过平面轴承支撑有平台旋转盖,所述工作台的底部中心安装有驱动平台旋转盖转动的调节电机;所述水平底板上设有对称位于平台旋转盖四周的滑块嵌槽,所述滑块嵌槽中分别嵌有滑块,各滑块的外侧分别连接有可转动的滑块调节螺杆,各滑块调节螺杆的螺纹段分别旋接在水平底板的螺孔中;各滑块顶部中心分别设有滑块沉槽,所述滑块沉槽的底壁设有滑块定位销。
11.作为本发明的进一步改进,s4中,将合金锭和中间合金熔化后、按比例将精炼剂、细化剂、覆盖剂加入熔化液中,搅拌除气直至化学成分合格。
12.作为本发明的进一步改进,s5包括如下子步骤:s5.1、将泥芯固定在平台旋转盖上且保持同轴;s5.2、在各滑块上分别固定调节竖杆,各调节竖杆的内侧分别设有沿竖向延伸的调节竖杆嵌槽,所述调节竖杆嵌槽的横截面呈燕尾状且向平台旋转盖的轴线方向开口;s5.3、在各调节竖杆嵌槽中分别插接沿竖向延伸的刮刀片,各刮刀片根部的燕尾榫与调节竖杆嵌槽相匹配;通过转动滑块调节螺杆使各刮刀片的作用面分别贴合在泥芯的圆周上;s5.4、驱动平台旋转盖以30-50rpm的转速旋转,直至没有虚砂掉落;然后通过气管向各刮刀片顶部靠近燕尾榫的顶部注入涂料,涂料先向下到达涂料腔的底部,然后从向上到达涂料腔的上部,从刮刀片作用面上部流出并涂抹在泥芯外壁。
13.作为本发明的进一步改进,s5.2中,各调节竖杆的下端分别嵌入相应的滑块沉槽中,且滑块定位销分别插入调节竖杆底部的定位孔中;各调节竖杆的底部两侧分别设有调节竖杆凸台,所述调节竖杆凸台通过调节竖杆固定螺钉固定在滑块的顶部。
14.作为本发明的进一步改进,s7包括如下子步骤:s7.1、在平台旋转盖的中心孔中旋接镶套,所述镶套的下部为皮带驱动端,所述皮带驱动端通过皮带与调节电机的输出端相连;s7.2、在镶套的内腔插接升液管,所述升液管的外周与所述镶套的内壁之间设有两道滚珠,所述升液管的顶部出口与砂型下端的浇口相对接;s7.3、在各调节竖杆嵌槽中分别插接砂型靠板,各砂型靠板的根部分别通过燕尾榫嵌于调节竖杆嵌槽中,通过转动滑块调节螺杆使各砂型靠板的内侧面分别与砂型外壁相切;s7.4、调节电机驱动平台旋转盖以30-50rpm转速旋转的同时,通过升液管将合金液注入型腔中,合金液冷却后形成铸件及浇冒系统;s7.5、拆除各调节竖杆,在各滑块上分别固定调节架,沿调节架的高度方向设有贯通的调节架竖槽,沿调节架竖槽的高度方向安装多个定位块,各定位块的两侧分别设有定位块凸榫,所述定位块凸榫分别嵌于调节架竖槽侧壁的水平嵌槽中;s7.6、在各定位块中心孔的内端口插入套筒,在套筒中心孔的内端口插接并固定切刀;s7.7、再次通过调节电机驱动平台旋转盖以40-60rpm转速旋转,同时人工摇动滑块调节螺杆使滑块向内渐进,各切刀将砂型切断后,进行手工清砂,并取出带浇冒系统的铸件。
15.作为本发明的进一步改进,s7.5中,各调节架的下端头分别嵌于相应的滑块沉槽中,且滑块定位销分别插入调节架底部的定位孔中;各调节架的底部两侧分别设有调节架凸台,所述调节架凸台通过调节架固定螺钉固定在滑块的顶部。
16.作为本发明的进一步改进,s8包括如下子步骤:s8.1、通过锯床锯除连在铸件上的浇冒系统;s8.2、通过车床车削铸件的外圆;s8.3、根据图纸对铸件进行尺寸测量和目视检查外观是否有铸造缺陷;s8.4、通过x射线和荧光检查铸件内部缺陷;s8.5、对x射线和荧光检查出的内部缺陷超标部位进行焊补;s8.6、通过车床车削铸件的焊补部位。
17.作为本发明的进一步改进,s9包括如下子步骤:s9.1、将铸件平稳放置在固溶底板上,固溶底板上端面的各弧形块均匀抵靠在铸件下端的外侧;s9.2、将各限位管的下端分别插入均布在固溶底板外周的底板插接沉孔中,各底板插接沉孔中分别设有径向限位块,各限位管的底部分别设有径向嵌槽卡在相应的径向限位块上;s9.3、在铸件上方放置圆形压盖,各限位管的上端从所述圆形压盖的导向孔中穿出,各限位管的侧壁与铸件外周相切贴合;s9.4、在两根固定长螺杆上各自旋接一颗上螺母并旋转到顶,将两根固定长螺杆对称插入圆形压盖上的压盖螺杆安装孔中,并穿过铸件内腔从底板螺杆安装孔中穿出;s9.5、在固定长螺杆的下端旋接下螺母并压在固溶底板的下端面,并保持两根固
定长螺杆顶部的起吊环高度一致,然后将上螺母向下旋并压在圆形压盖的上端面,使圆形压盖与固溶底板连接为整体且各限位管的上端保持浮动状态;s9.6、将钢丝绳穿过起吊环,将固溶工装整体吊起,并放入烘箱中升温及保温;s9.7、保温结束后,将固溶工装整体吊起并投入60-80℃的水池中快速冷却10分钟后取出。
18.作为本发明的进一步改进,s10包括如下子步骤:s10.1、拆除调节架上各定位块中的套筒与切刀;s10.2、将滚轮杆从后端插入定位块中心孔中,滚轮杆前端的叉头从定位块中心孔的前端伸出,在各滚轮杆叉头之间安装滚轮轴及滚轮;s10.3、将弹簧及限位杆依次从后端插入定位块中心孔中,弹簧的前端抵靠在滚轮杆凸台上,弹簧的后端抵靠在限位杆的内端面;s10.4、在各调节架外侧分别贴合且固定数显杆,数显杆上沿高度方向分别设有多个数显杆安装孔,各数显杆安装孔中分别旋接有感应螺座,各感应螺座面向调节架的一侧分别安装有感应片,各感应片分别抵靠在相应限位杆的外端头;s10.5、将预加工与铸件配套的托盘同轴固定在平台旋转盖上方;s10.6、将铸件下端嵌入托盘中,托盘的外缘设有向上竖起的环形竖边,沿环形竖边的圆周均匀旋接多颗径向螺钉将铸件的底部固定;s10.7、通过调整感应螺座使同一圆周上四个感应片与铸件轴线之间的距离相等;s10.8、通过调节电机驱动铸件旋转,各高度的四个滚轮对铸件进行旋转挤压整形,使得铸件的圆整度符合公差要求。
19.相对于现有技术,本发明取得了以下有益效果:1、使用同一个工作台供多道工序进行作业,大大降低了工装制作成本和制作周期;使用的模具少,工艺简化易于操作,且成品质量高。
20.2、通过调节电机驱动平台旋转盖及泥芯缓慢旋转,通过刮刀片对泥芯外周进行刮削,一边刮削,一边在泥芯外周刮涂涂料,通过四个刮刀片对泥芯进行精确定位且修整外圆周,减少其圆柱度误差,提高泥芯精度;且在对泥芯修型的同时同步进行刷涂料,省去后续的刷涂料工序。
21.3、浇注时,砂型靠板扶住砂型的外周,避免砂型发生倾斜;铸件冷却成型后,将砂型靠板更换成切刀工具即可将砂型清除,十分快捷方便,大大提高生产效率,且无需购置昂贵的设备。
22.4、固溶时,各限位管顺着薄壁回转体铝合金铸件的拔模锥度倾斜,且与薄壁回转体铝合金铸件的外壁相切,在升温、保温及冷却过程中,管束住铸件外周,使其保持圆整,减小变形量。且限位管与铸件外壁为线接触,不影响其均匀冷却。
23.5、整形时,通过调节电机驱动平台旋转盖、托盘及铸件缓慢旋转,托盘根据铸件的尺寸精密加工配套,刚固溶后时效前的铸件仍处于软状态,各高度均由外侧的四组滚轮对铸件进行精确定位且挤压外圆周,使铸件各个截面的圆柱度误差达到符合公差范围的状态,提高产品精度及质量,且锥度铸件及圆柱铸件均可整形。
附图说明
24.下面结合附图和具体实施方式对本发明作进一步详细的说明,附图仅提供参考与说明用,非用以限制本发明。
25.图1为本发明中泥芯旋转修型时的立体图;图2为图1的爆炸图;图3为图1的主剖视图;图4为图3中刮刀片的放大图;图5为本发明浇注时的立体图;图6为本发明浇注时去掉砂型及平台旋转盖后的爆炸图;图7为本发明浇注时的剖视图;图8为本发明中砂型及其下方结构的爆炸图;图9为本发明清砂时隐去砂型后的立体图;图10为图9的爆炸图;图11为本发明清砂时隐去砂型后的剖视图;图12为本发明中热处理固溶工装的立体图;图13为图12的爆炸图;图14为本发明中旋转挤压整形时的立体图;图15为图14的主剖视图;图16为图15中的局部放大图;图17为水平底板上省略托盘及部分数显杆后的爆炸图。
26.图中:1.工作台;2.调节电机;2a.皮带;3.水平底板;3a.底板沉孔;3b.底板中心孔;3c.滑块嵌槽;3d.底板调整螺钉;4.平面轴承;5.平台旋转盖;6.滑块;6a.滑块沉槽;6b.滑块定位销;6c.滑块调节螺杆;7.调节竖杆;7a.调节竖杆嵌槽;7b.调节竖杆凸台;7c.调节竖杆固定螺钉;8.刮刀片;8a.刮刀片燕尾榫;8b.涂料注入口;8c.涂料腔;8d.涂料流出口;9.泥芯;10.镶套;10a.皮带驱动端;11.升液管;12.滚珠;13.调节架;13a.调节架竖槽;13b.水平嵌槽;13c.调节架凸台;13d.调节架固定螺钉;14.砂型靠板;14a.靠板燕尾榫;15.砂型;15a浇口;16.定位块;16a.定位块凸榫;17.套筒;18.切刀;19.铸件;20.托盘;21.径向螺钉;22.滚轮杆;23.滚轮;24.弹簧;25.限位杆;26.数显杆;27.感应片;28.感应螺座;29.固溶底板;29a.固溶底板中心孔;29b.弧形块;29c.底板插接沉孔;29d.径向限位块;29e.底板螺杆安装孔;30.圆形压盖;30a.导向孔;30b.压盖螺杆安装孔;31.限位管;31a.径向嵌槽;32.固定长螺杆;32a.起吊环;33a.上螺母;33b.下螺母。
具体实施方式
27.在本发明的以下描述中,术语“上”、“下”、“前”、“后”、“左”、“右”、“内”、“外”等指示的方位或位置关系为基于附图所示的方位或位置关系,仅是为了便于描述本发明和简化描述,而不是指装置必须具有特定的方位。文中滑块中安装新部件即表明旧部件已经被拆除。
28.本发明的薄壁回转体铝合金铸件的无箱浇注制造方法,依次包括如下步骤:s1、在工作台1上安装无箱浇注用工装;
s2、砂型造型:将产品模具和浇冒系统模具与造型砂结合,等造型砂固化后取出产品模具和浇冒系统模具,形成产品的外形和浇冒系统的空腔砂型;s3、制芯:将造型砂填入产品芯盒内,舂实后,拆分芯盒,得到泥芯9;s4、合金液熔炼:将合金锭和中间合金熔化后、按比例将精炼剂、细化剂、覆盖剂加入熔化液中,搅拌除气直至化学成分合格;s5、在工作台1上处理泥芯9上的披缝并上涂料;s6、将砂型15与泥芯9进行组合,确认砂型内壁与泥芯外壁之间的型腔间隙达到图纸尺寸要求;s7、在工作台1上进行无箱浇注,将合金液注入型腔中,冷却成型后进行清砂,得到带浇冒系统的铸件19;s8、去除铸件19上的浇冒系统,打磨铸件19的外观;s9、对铸件19进行固溶热处理;s10、对铸件19进行旋转挤压整形,使得铸件19达到符合尺寸公差范围内的铸态;s11、将铸件19放入时效炉进行时效处理。
29.如图1至图4所示,s1中无箱浇注用工装包括固定在工作台1上方的正方形的水平底板3,水平底板3的四个角部分别旋接有底板调整螺钉3d,各底板调整螺钉3d的顶部分别设有圆环吊耳。水平底板3的中心设有圆形的底板沉孔3a,底部沉孔的中心设有底板中心孔3b,底板沉孔3a的底壁上通过平面轴承4支撑有平台旋转盖5,由于转速较慢,平面轴承4可以用嵌于环形凹槽中的钢珠代替;工作台1的底部中心安装有调节电机2,调节电机2的输出轴上端可以穿过底板中心孔3b与平台旋转盖5的底壁中心相连。
30.水平底板3上设有对称位于平台旋转盖5四周的滑块嵌槽3c,滑块嵌槽3c中分别嵌有滑块6,各滑块6的外侧分别连接有可转动的滑块调节螺杆6c,各滑块调节螺杆6c的螺纹段分别旋接在水平底板3的螺孔中。旋进或旋退滑块调节螺杆6c,滑块调节螺杆6c的内端头在滑块6的外侧转动且牵引滑块6在滑块嵌槽3c中滑动,以调节滑块6与平台旋转盖5轴线之间的距离。
31.各滑块6顶部中心分别设有滑块沉槽6a,滑块沉槽6a的底壁设有两根滑块定位销6b。
32.s5包括如下子步骤:s5.1、将泥芯9固定在平台旋转盖5上且保持同轴,可以在平台旋转盖5固定底盘,泥芯9固定于底盘中,底盘可以与泥芯9相匹配。组合砂型时更换更大的底盘,也可以直接使用与砂型15匹配的底盘,便于后道工序直接组合。
33.s5.2、在各滑块6上分别固定调节竖杆7,各调节竖杆7的内侧分别设有沿竖向延伸的调节竖杆嵌槽7a,调节竖杆嵌槽7a的横截面呈燕尾状且向平台旋转盖5的轴线方向开口。
34.各调节竖杆7的底部两侧分别设有调节竖杆凸台7b,调节竖杆凸台7b通过调节竖杆固定螺钉7c固定在滑块6的顶部,滑块6嵌于水平底板3的滑块嵌槽3c中,各滑块6的两侧壁与滑块嵌槽3c构成滑动副。各滑块6的中部分别设有滑块沉槽6a,滑块沉槽6a的底壁设有两根定位销6b,调节竖杆7的下端头嵌于滑块沉槽6a中获得定位,两根定位销6b分别插入调节竖杆7底部的定位孔中获得双重定位。调节竖杆7的底部在滑块6上准确定位后,通过调节竖杆固定螺钉7c将调节竖杆凸台7b紧固在滑块6上,实现固定连接。
35.s5.3、在各调节竖杆嵌槽7a中分别插接沿竖向延伸的刮刀片8,各刮刀片8根部的刮刀片燕尾榫8a与调节竖杆嵌槽7a相匹配;通过转动滑块调节螺杆6c使各刮刀片8的作用面处于以泥芯轴线为圆心的同一个圆周上,且分别贴合在泥芯9的圆周上。
36.如图3、图4所示,安装时,只要将刮刀片燕尾榫8a从调节竖杆嵌槽7a的上端口向下插入即可,通过刮刀片燕尾榫8a与燕尾槽的配合,可以实现刮刀片8与调节竖杆7之间的精确配合且相互锁定,刮刀片燕尾榫8a工作时不会脱离燕尾槽;刮刀片8的上部设有沿竖向向下延伸的涂料腔8c,涂料腔8c的顶部封闭,刮刀片8的作用面上部设有涂料流出口8d,涂料流出口8d的内端头与涂料腔8c的上部相通;刮刀片8顶部靠近刮刀片燕尾榫8a的部位设有涂料注入口8b,涂料注入口8b的内端头向下延伸且与涂料腔8c的底部相连通。
37.s5.4、调节电机2的输出轴缓慢驱动平台旋转盖5以30-50rpm的转速旋转,平台旋转盖5带动泥芯9转动,平面轴承4承载平台旋转盖5的重量且使旋转十分轻便灵活;泥芯9转动的同时,四个相位上的刮刀片8分别在修整泥芯9的外周壁,直至没有虚砂掉落。然后将涂料通过气管注入涂料注入口8b,涂料先向下流动,从涂料腔8c的底部连通口进入涂料腔8c的下部,再沿涂料腔8c向上流动,最后从上部的涂料流出口8d流出,调节压力,让涂料贴着刮板片的作用面向下流动,在泥芯9旋转的同时,将涂料均匀刮涂在泥芯外壁,通过旋转作用刮涂整个泥芯圆周面。既保证了泥芯9的圆柱度,又减小刮刀片8与泥芯9之间的摩擦,省去了后续刷涂料的工序。
38.s7包括如下子步骤:s7.1、如图5至图8所示,调节电机2偏离平台旋转盖轴线安装,在平台旋转盖5的中心孔中旋接镶套10,镶套10的下部为皮带驱动端10a,皮带驱动端10a通过皮带2a与调节电机2的输出端相连。
39.s7.2、在镶套10的内腔插接升液管11,升液管11的外周与镶套10的内壁之间设有两道滚珠12,升液管11的顶部出口与砂型15下端的浇口15a相对接;可以在镶套10的内壁和升液管11的外壁分别加工出半圆形沟道,在升液管11上打孔,将数颗滚珠12塞入相应的沟道中后,再将孔眼封闭。
40.s7.3、在各调节竖杆嵌槽7a中分别插接砂型靠板14,各砂型靠板14的根部分别通过靠板燕尾榫14a嵌于调节竖杆嵌槽7a中,通过转动滑块调节螺杆6c使各砂型靠板14的内侧面分别与砂型15外壁相切,限制住砂型15的外周,避免其歪斜。
41.s7.4、升液管11保持不动,通过滚珠12支撑在升液管11外周的镶套10可以相对转动,调节电机2通过皮带2a驱动镶套10缓慢转动,镶套10带动平台旋转盖5及砂型15以30-50rpm转速旋转的同时,通过升液管11将合金液注入型腔中,按工艺规定的时间等待,合金液冷却后形成铸件19及浇冒系统。
42.s7.5、如图9至图11所示,拆除各调节竖杆7,在各滑块6上分别固定调节架13,沿调节架13的高度方向设有贯通的调节架竖槽13a,沿调节架竖槽13a的高度方向安装多个定位块16,各定位块16的两侧分别设有定位块凸榫16a,定位块凸榫16a分别嵌于调节架竖槽13a侧壁的水平嵌槽13b中。各调节架13的下端头分别嵌于相应的滑块沉槽6a中,且滑块定位销6b分别插入调节架13底部的定位孔中;各调节架13的底部两侧分别设有调节架凸台13c,调节架凸台13c通过调节架固定螺钉13d固定在滑块6的顶部。
43.s7.6、在各定位块中心孔的内端口插入套筒17,在套筒中心孔的内端口插接并固
定切刀18,切刀18抵靠在砂型15外壁。
44.s7.7、再次通过调节电机2驱动平台旋转盖5以40-60rpm转速旋转,同时人工摇动滑块调节螺杆6c使滑块6向内渐进,各切刀18将砂型15切成若干段后,进行手工清砂,并取出带浇冒系统的铸件19。
45.s8包括如下子步骤:s8.1、通过锯床锯除连在铸件19上的浇冒系统;s8.2、通过车床车削铸件19的外圆;s8.3、根据图纸对铸件19进行尺寸测量和目视检查外观是否有铸造缺陷;s8.4、通过x射线和荧光检查铸件内部缺陷;s8.5、对x射线和荧光检查出的内部缺陷超标部位进行焊补;s8.6、通过车床车削铸件的焊补部位。
46.s9包括如下子步骤:s9.1、如图12、图13所示,将铸件19平稳放置在固溶底板29上,固溶底板29的中心设有固溶底板中心孔29a,固溶底板29上端面的各弧形块29b均匀抵靠在铸件19下端的外侧,弧形块29b可以沿同一个圆周均匀设有四个,便于铸件19的下端嵌入,直接获得准确的定位。
47.s9.2、将各限位管31的下端分别插入均布在固溶底板29外周的底板插接沉孔29c中,各底板插接沉孔29c中分别设有径向限位块29d,各限位管31的底部分别设有径向嵌槽31a卡在相应的径向限位块29d上实现相互定位,并且限制限位管31转动。限位管31均匀排列,可以设有八根。
48.s9.3、在铸件19上方放置圆形压盖30,各限位管31的上端从圆形压盖30的导向孔30a中穿出,各限位管31的侧壁与铸件19外周相切贴合,对铸件19的外周进行均匀限位,可以适应铸件19的拔模锥度。使铸件19在固溶过程中保持圆整度,减小其变形量;各限位管31的轴向可以圆形压盖30的导向孔30a中自由伸缩。
49.s9.4、在两根固定长螺杆32上各自旋接一颗上螺母33a并旋转到顶,将两根固定长螺杆32对称插入圆形压盖30上的压盖螺杆安装孔30b中,并穿过铸件内腔从底板螺杆安装孔29e中穿出。
50.s9.5、在固定长螺杆32的下端旋接下螺母33b并压在固溶底板29的下端面,并保持两根固定长螺杆32顶部的起吊环32a高度一致,然后将上螺母33a向下旋并压在圆形压盖30的上端面,使圆形压盖30与固溶底板29连接为整体,便于起吊;各限位管31的上端保持浮动状态;s9.6、将钢丝绳穿过起吊环32a,将固溶工装整体吊起,并放入烘箱中升温及保温;由于热处理工装的锁紧力和材质对铝合金有着一定影响,因为铸件19热处理时,组织介质会发生转换,为了不影响组织介质的转换,经多次的实验验证,限位管31选用壁厚为32mm的0cr297ni9ti不锈钢管,在经过二次退火处理,得到接近适合铝合金铸件19的热处理硬度的钢管,这样就有效排除在固溶时阻碍组织介质的转化。
51.s9.7、保温结束后,将固溶工装整体吊起并投入60-80℃的水池中快速冷却10分钟后取出。由于限位管31与铸件19相切,只存在线接触,在铸件19浸入水中冷却时,与水接触不到的面积很小,不影响整体的快速且均匀冷却。冷却过程中,各限位管31仍限制住铸件19
的外壁,使其继续保持极高的圆整度。
52.s10包括如下子步骤:s10.1、拆除调节架13上各定位块16中的套筒17与切刀18。
53.s10.2、如图14至图17所示,将滚轮杆22从后端插入定位块中心孔中,滚轮杆22前端的叉头从定位块中心孔的前端伸出,在各滚轮杆叉头之间安装滚轮轴及滚轮23,滚轮23通过滚轮轴固定在滚轮杆叉头之间。
54.s10.3、将弹簧24及限位杆25依次从后端插入定位块中心孔中,弹簧24的前端抵靠在滚轮杆凸台上,弹簧24的后端抵靠在限位杆25的内端面。
55.s10.4、在各调节架13外侧分别贴合且固定数显杆26,数显杆26的上下两端通过螺钉与调节架13固定连接。数显杆26上沿高度方向分别设有多个数显杆安装孔,各数显杆安装孔中分别旋接有感应螺座28,各感应螺座28面向调节架13的一侧分别安装有感应片27,各感应片27分别抵靠在相应限位杆25的外端头。
56.s10.5、由于平台旋转盖5的尺寸不可更改,在加工不同外径的铸件19时,可以根据铸件19的外形尺寸精确加工配套的托盘20,托盘20底部通过八个螺栓孔与平台旋转盖5固定连接且实现精确同轴。
57.s10.6、将铸件19下端嵌入托盘20中,托盘20的外缘设有向上竖起的环形竖边,沿环形竖边的圆周均匀旋接多颗径向螺钉21将铸件19的底部固定。托盘20外缘的环形竖边精确卡在铸件19的下端外缘使铸件19与托盘20同心定位,如此可以确保平台旋转盖5旋转时,铸件19可以精确地实现同轴旋转。各径向螺钉21的内端头卡住铸件19的底部外周,避免整形时铸件19跟转。
58.s10.7、通过调整感应螺座28使同一圆周上四个感应片27与铸件19轴线之间的距离相等;s10.8、通过调节电机2驱动铸件19旋转,各高度的四个滚轮23对铸件19进行旋转挤压整形,使得铸件19的圆整度符合公差要求。
59.刚固溶后的铸件19仍处于软状态,旋转时铸件19的外周壁与各滚轮23接触,铸件19圆周的高点受到滚轮23的挤压,逐渐圆整,滚轮23的挤压力通过限位杆25传递给感应片27,各感应片27的压力在弹力测试仪的屏幕上显示。如果同一圆周上四个滚轮23的压力误差在设定公差范围内,说明该圆周的圆整度已经符合要求。