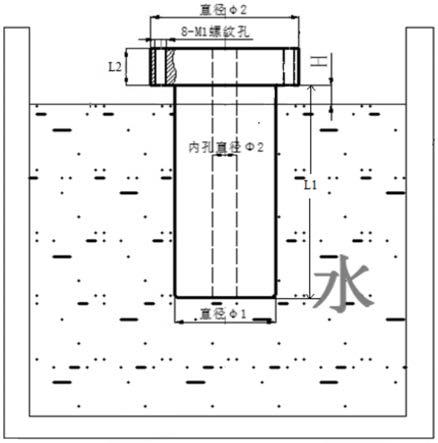
crwmn旋压芯模的双液淬火热处理方法
技术领域
1.本发明属于旋压芯模热处理方法技术领域,具体涉及crwmn旋压芯模的双液淬火热处理方法。
背景技术:2.旋压芯模是一种旋压加工生产中的关键工装,其使用过程中利用芯模端面的螺纹孔与旋压设备上的旋转主轴进行连接,在工作时旋压芯模受到旋压毛坯零件很大的挤压力,所以就要求旋压芯模工作部位必须具有很高的强度和表面耐磨性。常见的材质有9sicr、crwmn等,一般旋压芯模加工后都要进行热处理,使芯模硬度达到hrc58-62范围才能满足使用要求。在常规热处理过程中,为了提高芯模硬度而采用冷速较快的淬火介质,但同时会容易造成旋压芯模端头的螺纹孔部位开裂。所以在热处理过程中旋压芯模的硬度和开裂就成为最为突出的矛盾点。
技术实现要素:3.本发明的目的是提供crwmn旋压芯模的双液淬火热处理方法,能够在热处理过程中,既满足旋压芯模的硬度,又避免在旋压芯模端面螺纹孔处产生淬火裂纹。
4.为了达到上述目的,本发明所采用的技术方案是:crwmn旋压芯模的双液淬火热处理方法,具体按照以下步骤实施:
5.步骤1,将旋压芯模垂直吊挂在热处理炉中,封紧炉盖进行加热保温;
6.步骤2,打开炉盖,将所述步骤1中加热后的旋压芯模吊出并转移至水槽中,保证旋压芯模的上端部露出水面,进行冷却降温;
7.步骤3,将所述步骤2中冷却后的旋压芯模吊出转移至油槽中,整个模体完全没入油槽中进行二次冷却;
8.步骤4,二次冷却后的旋压芯模从油槽中吊出,然后置于回火炉中回火;
9.步骤5,回火完成后,取出冷却至室温即可。
10.本发明的技术方案,还具有以下特点:
11.步骤1中,热处理炉选用井式炉,井式炉的炉温均匀性为
±
5℃。
12.步骤1的具体过程为:封紧炉盖后,井式炉以80℃/h的速度加热至840℃,然后保温,保温时间根据旋压芯模的有效截面而定,保温36-54s/mm。
13.步骤2中旋压芯模露出水面的距离为40-50mm,冷却时间根据旋压芯模的有效截面而定,冷却0.8-1s/mm。
14.步骤3中,油槽中的淬火油为20#淬火机油,冷却时间根据旋压芯模的有效截面而定,冷却9-12s/mm。
15.步骤4具体过程为:旋压芯模从油槽中吊出后,水平置于箱式回火炉中,然后以60℃/h的温度升温至180℃并保温,保温时间由根据旋压芯模的有效截面而定,保温12-18min/mm。
16.回火炉的炉温均匀性为
±
5℃。
17.本发明的有益效果是:本发明的crwmn旋压芯模的双液淬火热处理方法,在对旋压芯模进行热处理淬火时,采用双液淬火(即水淬油冷)工艺,在井式炉垂直加热,然后吊出芯模进行淬火,在淬火时先在水槽中冷却,冷却时控制芯模的螺纹孔端不进入水中,避免开裂;随后将芯模迅速吊出水槽直接浸入油槽整体冷却。整个过程既达到在水中快速冷却提高芯模硬度的要求,又阻止螺纹孔位置不进入水中快冷,降低了螺纹孔位置的开裂风险,并在随后的油中冷却时,芯模整体得到较为缓慢的冷却速度,螺纹孔位置的脆性降低塑韧性提高,其与旋转主轴共同旋转工作时,安全性能较大提高。
附图说明
18.图1是本发明crwmn旋压芯模的双液淬火热处理方法中旋压芯模在水槽中的工作状态示意图;
19.图2是本发明crwmn旋压芯模的双液淬火热处理方法中旋压芯模在水槽中的工作状态示意图;
20.图3是本发明crwmn旋压芯模的双液淬火热处理方法中旋压芯模硬度检测的示意图。
具体实施方式
21.以下结合具体附图和具体实施方式对本发明进行详细说明。
22.本发明的crwmn旋压芯模的双液淬火热处理方法,具体按照以下步骤实施:
23.步骤1,将旋压芯模垂直吊挂在热处理炉中,封紧炉盖进行加热保温;热处理炉选用井式炉,井式炉的炉温均匀性为
±
5℃,具体过程为:封紧炉盖后,井式炉以80℃/h的速度加热至840℃,然后保温,保温时间根据旋压芯模的有效截面而定,保温36-54s/mm。
24.步骤2,打开炉盖,将所述步骤1中加热后的旋压芯模吊出并转移至水槽中,保证旋压芯模的上端部露出水面,进行冷却降温;旋压芯模露出水面的距离为40-50mm,冷却时间根据旋压芯模的有效截面而定,冷却0.8-1s/mm。
25.步骤3,将所述步骤2中冷却后的旋压芯模吊出转移至油槽中,整个模体完全没入油槽中进行二次冷却;油槽中的淬火油为20#淬火机油,冷却时间根据旋压芯模的有效截面而定,冷却9-12s/mm。当旋压芯模端部的螺纹孔位置在油中冷却时已比较安全,不会再有开裂风险。
26.步骤4,二次冷却后的旋压芯模从油槽中吊出,此时旋压芯模温度达到150-200℃左右,然后置于回火炉中回火;具体过程为:旋压芯模从油槽中吊出后,水平置于箱式回火炉中,然后以60℃/h的温度升温至180℃并保温,保温时间由根据旋压芯模的有效截面而定,保温12-18min/mm,回火炉的炉温均匀性为
±
5℃。
27.步骤5,回火完成后,取出冷却至室温即可。
28.实施例1
29.本实施例所采用的材质为crwmn的旋压芯模,其产品尺寸为:直径φ2=320mm,直径φ1=200mm,总长度l1+l2=2560mm,直径φ2端面上有8个m12的螺纹孔。淬火硬度hrc58-62,材料成分如表1所示,
30.表1
31.csimncrw0.980.31.021.151.42
32.采用本发明的工艺进行操作,具体步骤如下:
33.(1)井式炉加热过程
34.将该件旋压芯模利用工装垂直吊挂在井式热处理炉进行加热,设定以80℃/h的速度加热至840℃,并在此温度下保温约3h;
35.(2)双液淬火过程
36.保温结束后,打开炉盖吊出旋压芯模,并快速转移至水槽,将芯模侵入水槽中,如图1所示,使旋压芯模上端φ320部位距离液面h约为40mm时停止下落,保持至旋压芯模的φ200部位在水中冷却约2min,同时φ320部位在空气中冷却,待2min后,可发现φ320部位的表面温度已约780-800℃,此时迅速将旋压芯模从水中吊出并移入油槽中,如图2保证芯模整体全部进入油中进行冷却,在油中冷却约25min后当芯模温度达到200℃左右时取出芯模;
37.(3)箱式炉回火过程
38.在油中冷却结束后,将旋压芯模直接水平放入箱式炉,以60℃/h的速度升温至180℃,并保温6h,保温结束后停炉,将芯模吊出箱式炉,空冷至室温即完成整个淬火过程。
39.(4)硬度检测
40.回火结束后对旋压芯模各处硬度进行检测如图3及下表2所示:
41.表2
42.检测点
①
检测点
②
检测点
③
检测点
④
检测点
⑤
hrc52hrc58.8hrc60.5hrc60.0hrc60.8
43.结果分析:硬度检测结果显示,旋压芯模的工作部位(直径φ1*l1)硬度均满足技术要求。其中检测点
②
的硬度略低于其余部位,是因为该位置是水冷过程中的h距离,此位置是通过水面向上的翻滚来冷却,所以冷却速度比直接在水中冷却的部位有所缓和,故淬火硬度略低于其他位置;其中检测点
①
位置硬度仅hrc52左右,是因为该位置未在水中进行冷却,而是先在空气中冷却了2min,随后转移至油槽中才进行了完全的冷却,整体的冷却条件均低于φ1*l1部位,故其淬火硬度较低,但是正是该处的缓慢冷却过程才大大避免了螺纹孔在淬火过程中的开裂,并且该处的硬度相对脆性减小,与旋转主轴的共同扭转过程中,使芯模的安全系数更高。
44.本发明crwmn旋压芯模的双液淬火热处理方法,在水冷时控制旋压芯模的螺纹孔位置不进入水中,考虑到芯模周围的水面沸腾翻滚现象的存在,故使液面与螺纹孔位置保持一定距离,水中的短时间冷却可显著提高芯模的淬火硬度,而后快速转移至油槽整体冷却。该过程既保证了旋压芯模工作部位的硬度,又大大降低了螺纹孔位置的淬火开裂风险,提高了旋压芯模的整体使用性能,并取得良好使用效果。