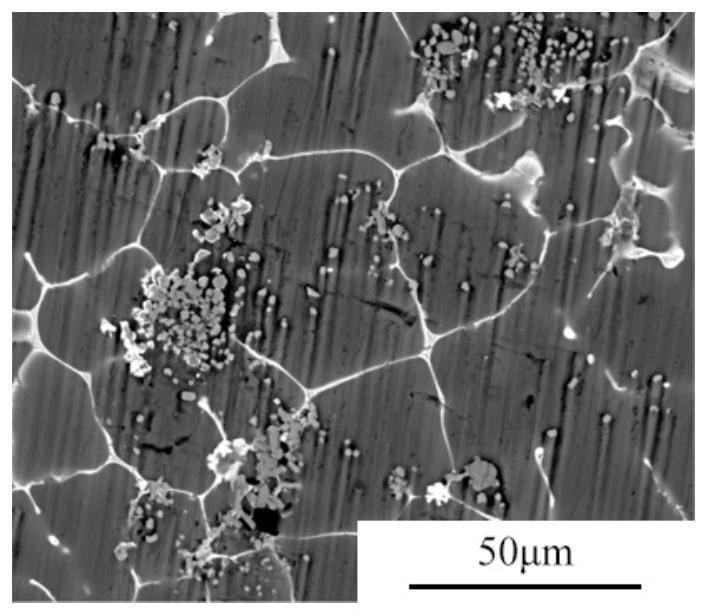
一种高延伸率、高模量tib2颗粒增强铝基复合材料及其制备方法
技术领域
1.本发明设计铝基复合材料制备与热挤压、锻造、轧制技术领域,尤其涉及一种高延伸率、高模量tib2颗粒增强超高强铝基复合材料制备及变形工艺。
背景技术:2.超高强铝合金是以al-zn-mg-cu系为主的可热处理强化铝合金,通常屈服强度在500mpa以上。超高强铝合金具有密度低、加工性能好及焊接性能优良的特点,在航空航天、车辆、建筑、桥梁、军工装备等方面广泛应用。从al-zn-mg-cu超高强铝合金问世开始,其研究主要经历了四大过程:
3.一是合金化路线。通过早期的提升zn含量,提高zn/mg比值,降低cu含量,到现在采用复合微合金化技术,添加稀土元素(sc、er、yb等)和过渡元素(ti、zr、hf等),结合两者的优势,形成与铝基体共格的具有l12结构的al3x相,以达到进一步强化合金的目的。
4.二是细晶处理技术。采用物理(电磁搅拌、超声振动、快速凝固等)或化学(变质处理、细化剂)等方式,通过使晶粒最大程度的细化而获得均值超细晶铸锭,从而提高合金铸锭的力学性能。
5.三是采用先进加工成型及变形工艺。通过改进传统的铸造冶金技术,如液芯磁流铸造技术、低频电磁半连续铸造等,或开发其他新的成型技术来提高合金的特殊性能或综合力学性能。对合金铸锭进行精确塑性变形(轧制、挤压、锻造),使合金在组织缺陷改善的同时产生加工硬化。
6.四是研究精确热处理技术。al-zn-mg-cu合金的热处理工艺沿着t6
→
t73
→
t76
→
t74
→
t77
→
rra的过程发展,通过不同的热处理工艺控制合金组织,使其表现不同特性或性能组合,并进一步进行优化改进或开发新的热处理工艺提高合金的综合性能。
7.尽管当前超高强铝合金的强度可达到使用要求,但其极限弹性模量为70gpa左右仍无法满足要求。通过添加增强体颗粒制备铝基复合材料可将弹性模量提升至72gpa以上,并同步提升强度。相较于其他增强体颗粒,tib2具有弹性模量高、线膨胀系数较低的优势,可以有效提升复合材料的强度、刚度。另外,tib2与铝基体具有良好的界面结合能力,tib2的(0001)面和α-al的(111)面错配度小于15%,从晶格匹配角度来看,tib2可作为形核中心,起到细晶强化的作用。与铝基体良好的润湿性使界面结合强度提高,这对提升复合材料性能极为重要。但是,现有颗粒增强复合材料的研究,可使强度、耐磨性大幅提升,但塑性急剧降低。由于增强体颗粒具有较大界面能,在传统铸造成型的凝固过程,增强体颗粒趋向于界面能减少的方向发展即发生颗粒团聚,降低比表面积以达到界面能最低的稳定状态,大幅降低了复合材料的塑性。国内外研究人员采用增材制造的方式以快速凝固的成型过程改善颗粒分布的问题以获得良好的强度及塑性,但制备大尺寸铸锭困难,无法制备大尺寸结构材料。
应变曲线。
具体实施方式
23.下面结合附图及实施例对本发明的技术方案做进一步的说明,但并不局限于此,凡是对本发明技术方案进行修改或者等同替换,而不脱离本发明技术方案精神和范围,均应涵盖在本发明的保护范围中。
24.实施例1,一种超高强铝合金挤压棒材及其制备方法,其特征在于,按如下步骤进行:
25.①
超高强铝合金的成分配比为:8%zn、1.6%mg、1.6%cu、0.1%zr、0.1%sc,6%tib2(可采用一种低成本al-ti-b细化剂及其制备方法,zl201310136359.7)余量为al。按设计的合金成分,以高纯铝锭,高纯镁,高纯锌,al-50%cu,al-4%zr,al-6%sc中间合金、tib2进行配料。将高纯铝锭在780℃进行熔化,按次序加入al-50%cu,al-4%zr,al-6%sc、中间合金和tib2,等待中间合金全部熔化后,对熔体进行匀速搅拌,之后在750℃下进行精炼,静置5min,除气、扒渣,然后依次加入高纯镁、高纯锌,待金属全部熔化,对熔体继续匀速搅拌,最后在730℃进行半连续铸造。拉坯速度为25mm/min,获得合金铸锭(ф280mm),其显微组织如图1所示。
26.②
将铸锭切成ф280mm
×
500mm的圆柱体进行400℃/6h+465℃/30h的均匀化退火处。通过车床对均匀化铸锭去氧化皮至ф250mm,于420℃预热2h后进行锻造,变形量为50%,并风冷至室温。
27.③
将锻态材料于420℃保温2h沿正交方向进行正挤压,挤压比17.6:1,并风冷至室温,两步变形的组织如图2所示。经t6热处理后最终得到6wt.%/al-zn-mg-cu-zr-sc合金复合变形材料,进行力学性能测试,其抗拉强度达到731.55mpa,屈服强度为676.62mpa,延伸率为8.82%,弹性模量为73.17gpa。复合材料应力-应变曲线如图3所示。
28.实施例2,一种超高强铝合金挤压棒材及其制备方法,其特征在于,按如下步骤进行:
29.①
超高强铝合金的成分配比为:10%zn、1.6%mg、1.6%cu、0.1%zr、0.1%sc,8%tib2余量为al。按设计的合金成分,以高纯铝锭,高纯镁,高纯锌,al-50%cu,al-4%zr,al-6%sc中间合金、tib2进行配料。将高纯铝锭在780℃进行熔化,按次序加入al-50%cu,al-4%zr,al-6%sc中间合金、tib2,等待中间合金全部熔化后,对熔体进行匀速搅拌,之后在750℃下进行精炼,静置5min,除气、扒渣,然后依次加入高纯镁、高纯锌,待金属全部熔化,对熔体继续匀速搅拌,最后在730℃进行半连续铸造。拉坯速度为28mm/min,获得合金铸锭(ф280mm),其显微组织如图1所示。
30.②
将铸锭切成ф280mm
×
500mm的圆柱体进行400℃/6h+465℃/30h的均匀化退火处。通过车床对均匀化铸锭去氧化皮至ф250mm,于420℃预热2h后进行挤压,挤压比为17.6:1,并风冷至室温。
31.③
将一步挤压材料于420℃保温2h沿正交方向进行再次挤压,挤压比17.6:1,并风冷至室温。经t6热处理后最终得到6wt.%/al-zn-mg-cu-zr-sc合金复合变形材料,进行力学性能测试,其抗拉强度达到740.25mpa,屈服强度为691.53mpa,延伸率为9.12%,弹性模量为75.21gpa。
32.实施例3,一种超高强铝合金挤压棒材及其制备方法,其特征在于,按如下步骤进行:
33.①
超高强铝合金的成分配比为:11%zn、2.0%mg、1.7%cu、0.12%zr、0.12%sc,10%tib2余量为al。按设计的合金成分,以高纯铝锭,高纯镁,高纯锌,al-50%cu,al-4%zr,al-6%sc中间合金、tib2进行配料。将高纯铝锭在780℃进行熔化,按次序加入al-50%cu,al-4%zr,al-6%sc中间合金、tib2,等待中间合金全部熔化后,对熔体进行匀速搅拌,之后在750℃下进行精炼,静置5min,除气、扒渣,然后依次加入高纯镁、高纯锌,待金属全部熔化,对熔体继续匀速搅拌,最后在730℃进行半连续铸造。拉坯速度为30mm/min,获得合金铸锭(ф280mm)。
34.②
将铸锭切成ф280mm
×
500mm的圆柱体进行400℃/6h+465℃/30h的均匀化退火处。通过车床对均匀化铸锭去氧化皮至ф250mm,于420℃预热2h后进行挤压,挤压比为17.6:1,并风冷至室温。
35.③
将一步挤压材料于420℃保温2h沿正交方向切进行热轧,变形量为70%,并风冷至室温。经t6热处理后最终得到10wt.%/al-zn-mg-cu-zr-sc合金复合变形材料,进行力学性能测试,其抗拉强度达到720.06mpa,屈服强度为671.45mpa,延伸率为8.32%,弹性模量为76.81gpa。