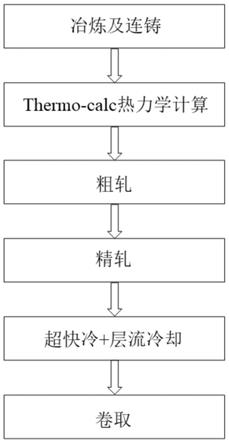
1.本发明属于热轧金属材料技术领域,具体涉及一种热轧高强结构钢的生产方法。
背景技术:2.热轧高强结构钢主要用于机械行业和工程建设行业,例如制造挖掘机、装载机、推土机,电力塔管,混凝土搅拌罐车,煤矿液压机架,伸吊臂,输电铁塔,电杆等产品工作部件和结构。
3.现有技术中热轧高强结构钢的生产方法均存在一些不足之处,具体如下:
4.公开号为cn112522616a的专利文献中公开了一种650mpa级热轧高强钢及其制备方法,其工艺特征是精轧后需要一次水冷、空冷、二次水冷,两次水冷+一次空冷造成生产工序繁琐,降低生产效率,不利于控制冷却速度。
5.公开号为cn111530942a的专利文献中公开了一种优质碳素结构钢的热轧工艺,其工艺特征是控制终轧温度为900~950℃,使终轧温度接近相变点,加速过冷奥氏体向珠光体+铁素体转变的速率,但是并没有具体给出相变点的温度得到方法。
6.公开号为cn110923549a的专利文献中公开了一种900mpa级热轧高强度起重机起重臂用结构钢及其生产方法,其在降c控低si的合金成分中,利用适量合金元素的添加改变钢种组织特性,通过多次试验总结,才开发出了钢种中添加nb、mo、ti、cr元素的钢种组,这无疑增加了研发成本和研发周期。
7.有鉴于此,有必要提供一种热轧高强结构钢的生产方法,能够避免重复性实验,显著降低生产成本。
技术实现要素:8.本发明的目的在于克服传统技术中存在的上述问题,提供一种热轧高强结构钢的生产方法,能够避免重复性实验,显著降低生产成本。
9.为实现上述技术目的,达到上述技术效果,本发明是通过以下技术方案实现:
10.一种热轧高强结构钢的生产方法,包括如下步骤:
11.1)冶炼及连铸:按设定化学成分冶炼铁水,经高炉铁水冶炼
→
kr铁水预处理
→
转炉冶炼
→
lf炉精炼
→
rh炉精炼
→
连铸
→
铸坯下线缓冷钢水连铸制成连铸坯;
12.2)热力学相图计算:利用热力学计算软件对钢的合金体系进行热力学相图计算,获得γ/α相变温度、共析转变温度;
13.3)粗轧:连铸坯冷装送入加热炉,加热后除磷送入粗连轧机架,控制粗轧温度为1100~1200℃;
14.4)精轧:控制精轧终轧温度为t1,且t1=(a
r1-60)~(a
r1-20)℃,其中a
r1
为γ/α相变温度,单位℃;共进行5~7道次精轧;
15.5)冷却:轧后采用超快冷+层流冷却模式将钢带快速冷却至卷取温度;
16.6)卷取:控制卷取温度为t2=(a
r3-150)~(a
r3-100)℃,其中a
r3
为共析转变温度,
单位℃;卷取后即可得到热轧高强结构钢。
17.进一步地,如上所述热轧高强结构钢的生产方法,步骤1)中,铁水其成分按质量百分比计含c:0.07%~0.11%,si:0.15%~0.30%,mn:1.75%~1.90%,p≤0.015%,s≤0.005%,al:0.015%~0.050%,nb:0.045%~0.060%,mo:0.15%~0.24%,ti:0.10%~0.14%,其余为fe和不可避免的杂质。
18.进一步地,如上所述热轧高强结构钢的生产方法,步骤2)中,热力学计算软件为thermo-calc软件,将钢成分输入thermo-calc程序中,利用准平衡模式计算得到高强结构钢的准平衡相图,并基于准平衡相图的辅助获得γ/α相变温度、共析转变温度。
19.进一步地,如上所述热轧高强结构钢的生产方法,步骤3)中,连铸坯采用三段式连续加热炉进行加热,加热炉的加热段炉温:1210~1270℃,均热段炉温:1200~1270℃,并保温220~320min;连铸坯厚度200~230mm。
20.进一步地,如上所述热轧高强结构钢的生产方法,步骤3)中,粗轧出口温度控制在1020~1060℃,粗轧后中间坯厚度>3倍钢卷成品厚度,粗轧后的中间坯厚度保证精轧压下率≥80%,之后经过保温罩送入精轧机组。
21.进一步地,如上所述热轧高强结构钢的生产方法,步骤4)中,精轧入口温度控制在970~1020℃,轧制速度4~8m/s,精轧后厚度6~9mm。
22.进一步地,如上所述热轧高强结构钢的生产方法,步骤5)中,轧后快速冷却的冷却速率为25~30℃/s。
23.进一步地,如上所述热轧高强结构钢的生产方法,步骤6)中,热轧高强结构钢的显微组织铁素体的体积分数为95%~100%,晶粒尺寸为10~15μm。
24.本发明的有益效果是:
25.1、本发明利用thermo-cale热力学计算软件对热轧高强结构钢的合金体系进行热力学相图计算,为成分优化和制定轧制工艺提供了可靠的关键点,避免了重复性实验,显著降低生产成本。
26.2、本发明设计的结构钢成分合理,通过控制热轧工艺来调控热轧板内部的组织状态,即采用终轧温度与相变温度相匹配,共析温度与卷取温度相匹配的方法,使内部存在晶粒度均匀细小的热轧高强钢,铁素体组织分数95%~100%,具有良好的力学性能。
27.3、与现有普通热轧高强结构钢卷取后晶粒尺寸大概为15~30μm相比,本发明热轧高强钢晶粒尺寸达到10~15μm,晶粒尺寸明显降低。
28.当然,实施本发明的任一产品并不一定需要同时达到以上的所有优点。
附图说明
29.为了更清楚地说明本发明实施例的技术方案,下面将对实施例描述所需要使用的附图作简单地介绍,显而易见地,下面描述中的附图仅仅是本发明的一些实施例,对于本领域普通技术人员来讲,在不付出创造性劳动的前提下,还可以根据这些附图获得其他的附图。
30.图1为本发明生产方法的流程框图;
31.图2为本发明实施例1中thermo-calc计算得到的平衡相图;
32.图3为本发明实施例1中热轧板的金相组织图;
33.图4为本发明对比例1中热轧板的金相组织图。
具体实施方式
34.下面将结合本发明实施例中的附图,对本发明实施例中的技术方案进行清楚、完整地描述,显然,所描述的实施例仅仅是本发明一部分实施例,而不是全部的实施例。基于本发明中的实施例,本领域普通技术人员在没有作出创造性劳动前提下所获得的所有其它实施例,都属于本发明保护的范围。
35.一种热轧高强结构钢的生产方法,包括如下步骤:
36.1)冶炼及连铸:按设定化学成分冶炼铁水,经高炉铁水冶炼
→
kr铁水预处理
→
转炉冶炼
→
lf炉精炼
→
rh炉精炼
→
连铸
→
铸坯下线缓冷钢水连铸制成连铸坯;其中,铁水其成分按质量百分比计含c:0.07%~0.11%,si:0.15%~0.30%,mn:1.75%~1.90%,p≤0.015%,s≤0.005%,al:0.015%~0.050%,nb:0.045%~0.060%,mo:0.15%~0.24%,ti:0.10%~0.14%,其余为fe和不可避免的杂质。
37.2)热力学相图计算:利用热力学计算软件对钢的合金体系进行热力学相图计算,获得γ/α相变温度、共析转变温度;热力学计算软件为thermo-calc软件,将钢成分输入thermo-calc程序中,利用准平衡模式计算得到高强结构钢的准平衡相图,并基于准平衡相图的辅助获得γ/α相变温度、共析转变温度。具体软件操作为:在thermo-calc软件界面选择tcfe9数据库,选择合计体系中的所有元素,并输入元素含量。在平衡计算器中选择性质图,执行作业树,对钢的合金体系进行热力学相图计算。
38.3)粗轧:连铸坯冷装送入加热炉,加热后除磷送入粗连轧机架,连铸坯采用三段式连续加热炉进行加热,加热炉的加热段炉温:1210~1270℃,均热段炉温:1200~1270℃,并保温220~320min;连铸坯厚度200~230mm。控制粗轧温度为1100~1200℃,具体:粗轧出口温度控制在1020~1060℃,粗轧后中间坯厚度>3倍钢卷成品厚度,粗轧后的中间坯厚度保证精轧压下率≥80%,之后经过保温罩送入精轧机组。
39.4)精轧:控制精轧终轧温度为t1,且t1=(a
r1-60)~(a
r1-20)℃,其中a
r1
为γ/α相变温度,单位℃;共进行5~7道次精轧;精轧入口温度控制在970~1020℃,轧制速度4~8m/s,精轧后厚度6~9mm。
40.5)冷却:轧后采用超快冷+层流冷却模式将钢带快速冷却至卷取温度,轧后快速冷却的冷却速率为25~30℃/s。
41.6)卷取:控制卷取温度为t2=(a
r3-150)~(a
r3-100)℃,其中a
r3
为共析转变温度,单位℃;卷取后即可得到热轧高强结构钢。热轧高强结构钢的显微组织铁素体的体积分数为95%~100%,晶粒尺寸为10~15μm。
42.本发明的具体实施例如下:
43.实施例1
44.本实施例方法的流程如图1所示,具体为:
45.按设定化学成分冶炼钢水,其成分按质量百分比含c:0.08%,si:0.17%,mn:1.78%,p:0.010%,s:0.003%,al:0.023%,nb:0.049%,mo:0.23%,ti:0.14%,其余为fe和不可避免的杂质;将上述成分的钢水经连铸机制成连铸坯,厚度为210mm;
46.将高强结构钢成分输入thermo-calc程序中,利用准平衡模式计算得到γ/α相变
温度a
r1=
910℃、共析点温度a
r3
=669℃,计算得到的相图如图2所示
,
;
47.板坯加热,连铸坯冷装送入加热炉,铸坯加热过程中,加热段炉温:1210℃,均热段炉温:1200℃,并保温220min,连铸坯厚度210mm,加热后除磷送入粗连轧机架;
48.控制粗轧温度1150℃;粗轧出口温度控制在1030℃,粗轧后中间坯厚度33mm,之后经过保温罩送入精轧机组;
49.控制精轧终轧温度为t1,且t1=(a
r1-60)~(a
r1-20)℃=850~890℃,实际终轧温度870℃,7道次精轧,精轧完成后进行层流冷却+超快冷;精轧入口温度控制在1000℃,轧制速度7m/s,精轧后厚度7mm;
50.轧后采用前置超快冷+层流冷却模式将钢带快速冷却至t2=(ar
3-150)~(ar
3-100)℃==519~569℃进行卷取,实际卷取温度540℃,冷却速率为27℃/s。
51.热轧高强钢显微组织铁素体的体积分数为96%,热轧高强钢晶粒尺寸达到12μm。热轧高强钢的屈服强度=699mpa,抗拉强度=771mpa,延伸率=19%。
52.实施例2
53.本实施例方法同实施例1相比,不同点在于:
54.按设定化学成分冶炼钢水,其成分按质量百分比含c:0.07%,si:0.16%,mn:1.79%,p:0.012%,s:0.002%,al:0.024%,nb:0.048%,mo:0.24%,ti:0.14%,其余为fe和不可避免的杂质;
55.将高强结构钢成分输入thermo-calc程序中,利用准平衡模式计算得到γ/α相变温度a
r1=
915℃、共析点温度a
r3
=675℃;
56.控制精轧终轧温度为t1=(a
r1-60)~(a
r1-20)℃=855~895℃,实际终轧温度870℃,精轧后厚度8mm;
57.轧后采用前置超快冷+层流冷却模式将钢带快速冷却至t2=(a
r3-150)~(a
r3-100)℃=525~575℃进行卷取,实际卷取温度545℃,冷却速率要求25℃/s。
58.热轧高强钢显微组织铁素体的体积分数为97%,热轧高强钢晶粒尺寸达到12μm。热轧高强钢的屈服强度=701mpa,抗拉强度=761mpa,延伸率=20%。
59.实施例3
60.本实施例方法同实施例1相比,不同点在于:
61.按设定化学成分冶炼钢水,其成分按质量百分比含c:0.07%,si:0.16%,mn:1.79%,p:0.012%,s:0.002%,al:0.024%,nb:0.048%,mo:0.24%,ti:0.14%,其余为fe和不可避免的杂质;
62.将高强结构钢成分输入thermo-calc程序中,利用准平衡模式计算得到γ/α相变温度a
r1=
915℃、共析点温度a
r3
=675℃;
63.控制精轧终轧温度为t1=(a
r1-60)~(a
r1-20)℃=855~895℃,实际终轧温度870℃,精轧后厚度8mm;
64.轧后采用前置超快冷+层流冷却模式将钢带快速冷却至t2=(a
r3-150)~(a
r3-100)℃=525~575℃进行卷取,实际卷取温度545℃,冷却速率要求25℃/s。
65.热轧高强钢显微组织铁素体的体积分数为97%,热轧高强钢晶粒尺寸达到12μm。热轧高强钢的屈服强度=697mpa,抗拉强度=761mpa,延伸率=19%。
66.实施例4
67.本实施例方法同实施例1相比,不同点在于:按设定化学成分冶炼钢水,其成分按质量百分比含c:0.08%,si:0.14%,mn:1.73%,p:0.016%,s:0.001%,al:0.025%,nb:0.045%,mo:0.23%,ti:0.17%,其余为fe和不可避免的杂质;
68.将高强结构钢成分输入thermo-calc程序中,利用准平衡模式计算得到γ/α相变温度a
r1=
920℃、共析点温度a
r3
=670℃;
69.控制精轧终轧温度为t1=(a
r1-60)~(a
r1-20)℃=860~900℃,实际终轧温度887℃,精轧后厚度7mm;
70.轧后采用前置超快冷+层流冷却模式将钢带快速冷却至t2=(a
r3-150)~(a
r3-100)℃=520~570℃进行卷取,实际卷取温度555℃,冷却速率要求26℃/s。
71.热轧高强钢显微组织铁素体的体积分数为98%,热轧高强钢晶粒尺寸达到11μm。热轧高强钢的屈服强度=711mpa,抗拉强度=781mpa,延伸率=18%。
72.对比例1
73.本对比例方法同实施例2相比,不同点在于:
74.按设定化学成分冶炼钢水,其成分按质量百分比含c:0.07%,si:0.16%,mn:1.79%,p:0.012%,s:0.002%,al:0.024%,nb:0.048%,mo:0.24%,ti:0.14%,其余为fe和不可避免的杂质;
75.将高强结构钢成分输入thermo-calc程序中,利用准平衡模式计算得到γ/α相变温度a
r1=
905℃、共析点温度a
r3
=655℃;
76.精轧终轧温度t1=(a
r1-60)~(a
r1-20)℃=845~885℃,实际终轧温度910℃,精轧后厚度7mm;
77.轧后采用前置超快冷+层流冷却模式将钢带快速冷却至t2=(a
r3-150)~(a
r3-100)℃=505~555℃进行卷取,实际卷取温度535℃,冷却速率要求28℃/s。
78.热轧高强钢显微组织铁素体的体积分数为93%,热轧高强钢晶粒尺寸达到16μm。热轧高强钢的屈服强度=681mpa,抗拉强度=741mpa,延伸率=18%。
79.对比例2
80.本对比例方法同实施例2相比,不同点在于:
81.按设定化学成分冶炼钢水,其成分按质量百分比含c:0.07%,si:0.16%,mn:1.79%,p:0.012%,s:0.002%,al:0.024%,nb:0.048%,mo:0.24%,ti:0.14%,其余为fe和不可避免的杂质;
82.将高强结构钢成分输入thermo-calc程序中,利用准平衡模式计算得到γ/α相变温度a
r1=
908℃、共析点温度a
r3
=659℃;
83.精轧终轧温度t1=(a
r1-60)~(a
r1-20)℃=848~888℃,实际终轧温度830℃,精轧后厚度8mm;
84.轧后采用前置超快冷+层流冷却模式将钢带快速冷却至t2=(a
r3-150)~(a
r3-100)℃=509~559℃进行卷取,实际卷取温度539℃,冷却速率要求26℃/s。
85.热轧高强钢显微组织铁素体的体积分数为90%,热轧高强钢晶粒尺寸达到17μm。热轧高强钢的屈服强度=670mpa,抗拉强度=735mpa,延伸率=16%。
86.对比例3
87.本对比例方法同实施例3相比,不同点在于:
88.按设定化学成分冶炼钢水,其成分按质量百分比含c:0.06%,si:0.16%,mn:1.75%,p:0.010%,s:0.005%,al:0.020%,nb:0.050%,mo:0.25%,ti:0.17%,其余为fe和不可避免的杂质;
89.将高强结构钢成分输入thermo-calc程序中,利用准平衡模式计算得到γ/α相变温度a
r1=
940℃、共析点温度a
r3
=670℃;
90.控制精轧终轧温度为t1=(a
r1-60)~(a
r1-20)℃=880~920℃,实际终轧温度890℃,精轧后厚度7mm;
91.轧后采用前置超快冷+层流冷却模式将钢带快速冷却,t2=(a
r3-150)~(a
r3-100)℃=520~570℃,实际按照卷取温度500℃进行卷取,冷却速率要求25℃/s。
92.热轧高强钢显微组织铁素体的体积分数为94%,热轧高强钢晶粒尺寸达到16μm。热轧高强钢的屈服强度=677mpa,抗拉强度=731mpa,延伸率=17%。
93.对比例4
94.本对比例方法同实施例3相比,不同点在于:
95.按设定化学成分冶炼钢水,其成分按质量百分比含c:0.06%,si:0.17%,mn:1.76%,p:0.014%,s:0.003%,al:0.025%,nb:0.050%,mo:0.23%,ti:0.15%,其余为fe和不可避免的杂质;
96.将高强结构钢成分输入thermo-calc程序中,利用准平衡模式计算得到γ/α相变温度a
r1=
946℃、共析点温度a
r3
=677℃;
97.控制精轧终轧温度为t1=(a
r1-60)~(a
r1-20)℃=886~926℃,实际终轧温度890℃,精轧后厚度7mm;
98.轧后采用前置超快冷+层流冷却模式将钢带快速冷却,t2=(a
r3-150)~(a
r3-100)℃=527~577℃,实际按照卷取温度500℃进行卷取,,冷却速率要求28℃/s。
99.热轧高强钢显微组织铁素体的体积分数为93%,热轧高强钢晶粒尺寸达到16μm。热轧高强钢的屈服强度=665mpa,抗拉强度=730mpa,延伸率=15%。
100.对比例5
101.本对比例方法同实施例3相比,不同点在于:
102.按设定化学成分冶炼钢水,其成分按质量百分比含c:0.06%,si:0.17%,mn:1.78%,p:0.011%,s:0.002%,al:0.023%,nb:0.049%,mo:0.23%,ti:0.17%,其余为fe和不可避免的杂质;
103.将高强结构钢成分输入thermo-calc程序中,利用准平衡模式计算得到γ/α相变温度a
r1=
919℃、共析点温度a
r3
=669℃;
104.控制精轧终轧温度为t1=(a
r1-60)~(a
r1-20)℃=859~899℃,实际终轧温度875℃,精轧后厚度7mm;
105.轧后采用前置超快冷+层流冷却模式将钢带快速冷却至t2=(a
r3-150)~(a
r3-100)℃=519~569℃进行卷取,实际卷取温度535℃,冷却速率要求20℃/s。
106.热轧高强钢显微组织铁素体的体积分数为96%,热轧高强钢晶粒尺寸达到17μm。热轧高强钢的屈服强度=660mpa,抗拉强度=738mpa,延伸率=17%。
107.通过上述实施例和对比例的比较可知,对比例1-2的终轧温度不在t1=(a
r1-60)~(a
r1-20)℃范围内,对比例3-4的卷取温度不在t2=(a
r3-150)~(a
r3-100)℃范围内,导致热
轧卷中热轧高强钢显微组织铁素体的体积分数不在95%~100%范围内,晶粒尺寸不在10~15μm范围内,最终得到的成品板性能劣化;上述对比例5的终轧温度在t1=(a
r1-60)~(a
r1-20)℃范围内,卷取温度在t2=(a
r3-150)~(a
r3-100)℃范围内,热轧卷中未再结晶组织体积分数也在95%~100%范围内,但由于冷却速度不在25~30℃/s范围内,最终得到的成品板性能也劣化。
108.本发明生产方法对热轧高强结构钢的合金体系进行热力学相图计算;来得到γ/α相变温度和共析转变温度,进而根据γ/α相变温度、共析转变温度来调控终轧温度和卷取温度使热轧板内部存在晶粒度均匀细小的热轧高强钢;同时采用前置超快冷+层流冷却模式将钢带快速冷却至卷取温度,提高生产效率。
109.以上公开的本发明优选实施例只是用于帮助阐述本发明。优选实施例并没有详尽叙述所有的细节,也不限制该发明仅为具体实施方式。显然,根据本说明书的内容,可作很多的修改和变化。本说明书选取并具体描述这些实施例,是为了更好地解释本发明的原理和实际应用,从而使所属技术领域技术人员能很好地理解和利用本发明。本发明仅受权利要求书及其全部范围和等效物的限制。