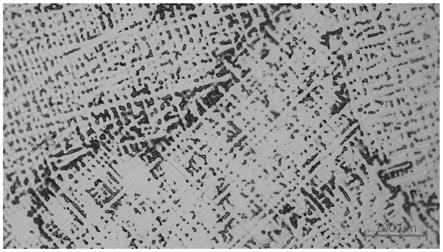
一种抗高温软化的cu-ni-sn系高强高弹铜合金及其制备方法
技术领域
1.本发明属于有色金属加工领域,涉及到抗高温软化的cu-ni-sn系高强高弹铜合金及其制备方法。
背景技术:2.随着信息产业和现代工业的快速发展,铜及铜合金应用范围日益广泛,需求量持续攀升,铜及铜合金材料已经成为国民经济和社会发展最重要的基础材料之一。高强度高弹铜合金材料作为目前先进的铜合金材料之一,是我国科技重大专项和各战略性新兴产业发展进步不可或缺的关键材料,广泛应用于新一代信息技术、节能与新能源汽车、先进轨道交通装备、航空航天装备、海洋工程等高新技术领域。
3.目前在我国的高强高弹铜合金市场,铍铜以其成型性好、弹性性能优异等特点仍然占据着较大的市场规模。但其制备过程易产生毒粉尘会对工人健康产生危害,且对环境会造成严重污染,另外,铍青铜在高于150℃环境下工作时稳定性差,抗应力松弛能力低,加上时效之后元件的变形度大,导致其生产工艺复杂、生产能耗高。随着国家常态化严苛的环保政策和能耗双控政策的落地,制备出安全无毒、工艺简单、性价比高且具有更高性能的高强高弹铜合金具有重要意义。铜镍锡系高强高弹铜合金性能与铍铜相当,且具有更优的抗热应力松弛性能,近年来,在耐磨轴承、轴瓦、轴套和大功率电子元件、精密插入式端子、光学仪器和传感器等的弹性元件具有广泛的应用。
4.cu-ni-sn系合金因sn元素含量较高,采用普通的感应熔炼浇铸的方法制备合金极易产生严重的枝晶偏析,后续需要高温长时间均匀化处理才能得以改善,不利于工业化生产和节能减耗的要求。此外,时效后期合金发生不连续沉淀反应,形成的胞状不连续沉淀组织会对严重恶化合金的性能,且随着温度的升高,不连续沉淀反应加剧,这就要求合金在具备高强高弹导电性能的同时,具备良好的抗高温软化能力。本发明采用微合金化处理和改进的制备工艺,可以调控cu-ni-sn系合金的微观组织和显微结构,达到改善合金性能,提高生产效率,降低生产成本的目的。
技术实现要素:5.本发明要解决的技术问题在于提供一种抗高温软化的cu-ni-sn系高强高弹铜合金及其制备方法,该制备方法能够有效改善合金的枝晶偏析,提高合金的抗高温软化性能、强度、弹性和耐磨性,且具有制备工艺简单,效率高,成本低等一些列优点。
6.为了实现本发明的目的,拟采用如下技术方案:
7.本发明一方面涉及一种抗高温软化的cu-ni-sn系高强高弹铜合金,所述合金的成分包括cu、ni、sn、al、zn、si或nb及不可避免杂质元素,其中,cu是合金基体,ni、sn、al、zn、si或nb是主合金元素,其含量:
8.ni含量:12-18wt%;
9.sn含量:4.5~8.5wt%;
10.al含量:0.5~2wt%;
11.zn含量:0.3~1.0wt%;
12.si含量:0.3~1.0wt%;
13.nb含量:0~1.0wt%。
14.此外,合金中还包含微量的co、p、fe、ag、cr、zr、ti、v等元素,其总含量不高于0.1wt%。
15.在本发明的一个优选实施方案中,所述的一种抗高温软化的cu-ni-sn系高强高弹铜合金,优化的成分如下:
16.ni含量:14.0-16.0wt%;
17.sn含量:4.5~6.5wt%;
18.al含量:1.0~1.8wt%;
19.zn含量:0.3~0.6wt%;
20.si含量:0.3~0.6wt%;
21.nb含量:0.3~0.6wt%。
22.此外,合金中还包含微量的co、p、fe、ag、cr、zr、ti、v等元素,其总含量不高于0.1wt%。
23.通过上述成分优化,本发明可以进一步提高合金的综合性能。
24.在本发明的一个优选实施方式中,所述种抗高温软化的cu-ni-sn系高强高弹铜合金,经上引连铸、多道次形变热处理,其强度达1200~1600mpa,弹性模量达135-150gpa,抗软化温度在580~650℃。
25.本发明另一方面涉及抗高温软化的cu-ni-sn系高强高弹铜合金的制备工艺,所述工艺包括熔炼—上引连铸—均匀化及固溶处理—组合形变热处理的步骤,具体如下:
26.步骤一:向熔融的铜液中投入纯镍块,然后投入覆盖剂,所述熔炼炉中的熔炼温度控制在1200-1300℃,当纯镍块完全熔融后,保温5-8分钟,并充入惰性气体进行精炼,然后依次投入si、nb、al、sn、zn等合金元素,待其在铜水中混合均匀。
27.步骤二:将上述混合熔液降温至1120-1180℃,然后利用虹吸原理使得所述熔炼炉中的合金液进入上引连铸结晶器中,在上引连铸结晶器中通过冷却水系统进行冷却结晶,为了保证冷却效果,结晶器冷却水的压力为0.3-0.5mpa。
28.步骤三:上述合金铸坯先进行均匀化处理后迅速水冷,以达到固溶处理的效果,所述水淬的冷却水温度为20-35℃。均匀化及固溶处理的工序温度和时间根据sn含量进行选择,sn含量在4.5~5.5wt.%时,均匀化工艺为850℃-880℃保温2-6h;sn含量为5.5~6.5wt.%时,均匀化工艺为880℃-910℃保温4-8h;sn含量为6.5~8wt.%时,均匀化工艺为910℃-950℃保温6-12h;
29.步骤四:将步骤三均匀化及固溶处理后的样品进行形变和热处理,具体工艺为:一次冷变形(70%≤总变形量≤90%)—一次时效处理(400-450℃,3-8h)—二次冷变形(50%≤总变形量≤70%)—二次时效处理(300-400℃,1-5h)。
30.所述覆盖剂为优质木碳和石墨鳞片的混合体,其中优质木碳和石墨鳞片各占50%,覆盖剂的厚度为80-100mm。在铜液中加入ni,会增大氢在合金中的溶解度,从而导致制备的合金吸氢严重而恶化合金加工性能,采用优质木碳和石墨鳞片的混合体作为覆盖
剂,可以隔绝合金液与空气的接触,减少合金液的吸气。
31.所述充入的惰性精炼气体为氩气或者氮气,脱气精炼的时间为8-15min。为保证脱气精炼效果,在除气精炼前对气体进行脱水处理,确保充入的精炼气体氧含量小于0.03%,水分含量小于3.0g/l。
32.所述依次投入si、nb、al、sn、zn等合金元素中,zn元素以cu-zn中间合金的形式加入,以减少zn元素的挥发,si、nb、al、sn等金属元素可以以纯金属或中间合金的形式加入。
33.所述上引连铸前的熔体温度根据ni元素的含量确定,ni含量在12~15wt.%时,上引连铸前的熔体温度介于1120-1150℃之间,ni含量在15~18wt.%时,上引连铸前的熔体温度介于1150-1180℃之间,牵引过程中熔体的液面高度变化不超过
±
20mm,上引结晶器的冷却水进水温度≤30℃,出水温度≤50℃。
34.所述上引连铸采用的结晶器为高耐热低超声衰减的氮化硼材料,其特点是与合金主要成分均无化学反应,此外,为提高牵引效率,实际生产中可采用多头连续牵引的方式,且上引连铸过程中节矩为1-3mm,连续牵引速率不低于100cm/min。
35.所述上引连铸过程中,铸坯的尺寸需要根据sn元素含量进行选择,sn含量在4.5~5.5wt.%时,圆形铸杆直径不超过30mm;sn含量为5.5~6.5wt.%时,圆形铸杆直径不超过25mm;sn含量为6.5~8wt.%时,圆形铸杆直径最大不超过20mm,用以避免制备的合金铸坯发生反偏析。
36.所述第二次冷加工的总变形量≤第一次冷加工的总变形量,第二次冷加工的道次变形量≤第一次冷加工的道次变形量。
37.所述时效处理温度在300℃-450℃之间,时效时间在1-8h之间,且一次时效的温度要高于二次时效的温度,以确保合金获得优异的组织,保障合金获得高的抗软化温度。
38.本发明通过采用cu、ni、sn、al、zn、si或nb作为原材料,通过熔炼,上引连铸,均匀化和固溶处理,形变热处理等多种强化方式相结合的方法制备合金,显著提高了合金性能,使得合金的强度达1200~1600mpa,弹性模量达135-150gpa,抗软化温度在580~650℃,改善了现有cu-ni-sn系高强高弹铜合金抗高温软化能力不足的问题,满足现航天、航空以及微电子工业高性能导电弹性器件等发展的要求。
39.本发明取得的有益成果为:
40.1)本发明通过上引连铸的方法,能够改善cu-ni-sn系合金铸态组织的偏析问题,同时该方法具有安全环保、高效节能的优点,符合我国环保政策和能耗双控政策的要求。具体来讲,通过控制sn元素含量、铸锭尺寸和上引连铸工艺,达到减小枝晶间距,消除合金的微观和宏观偏析,降低生产流程,简化生产工艺的目的。
41.2)通过合金化法调控cu-ni-sn系铜合金的显微组织和微观结构,抑制合金时效后期的不连续沉淀,显著提高cu-ni-sn系铜合金的强度和硬度,同时使得其抗高温软化能力大幅度提升。al、zn、si或nb元素的单独添加或复合添加,均可有效的抑制不连续沉淀的形核和长大。其中,si或nb元素的添加,可以与ni形成粗大的ni
31
si
11
相或ni3nb相,一方面占据不连续沉淀的形核位置,另一方面促进再结晶反应的发生,综合作用显著抑制不连续沉淀相的形成和长大,从而提高合金的耐高温时效能力和高温抗软化能力;al元素替代sn可保持合金原有的性能,降低sn的偏析;zn元素主要以固溶原子的方式存在于合金内部,对合金的力学性能和高温抗软化性能有较大的贡献。al、zn、si或nb元素的复合添加,一方面可改
善合金的显微组织和结构,另一方面可显著提高合金的性能,最终制备出抗高温软化性能优异的高强高弹cu-ni-sn系铜合金。
42.3)cu-ni-sn-al-zn-si、cu-ni-sn-al-zn-nb和cu-ni-sn-al-zn-si-nb合金具有较好的综合性能,抗拉强度、弹性模量、软化温度分别可达到1200~1600mpa、135-150gpa、580~650℃。
附图说明
43.图1为实施例1的铸态组织图。
44.图2为对比例1的铸态组织图。
45.从图1和图2可知,采用普通感应熔炼浇铸的方式制备的cu-ni-sn系铜合金铸态组织枝晶粗大,成分偏严重,采用上引连铸的方法制备的合金,可以显著减小铸态组织的枝晶间距,并使其分布的更加均匀。
具体实施方式
46.下面结合实施例对本发明作进一步描述:
47.实施例1:
48.步骤一、按照合金组分:15wt.%的ni,6wt.%的sn、1.4wt.%的al、0.5wt.%的zn、0.5wt.%的si,余量为纯铜。其中,ni、sn、al、zn、si的纯度为99.95wt.%。将配好的铜放入熔炼坩埚内,将ni、sn、al、市售cu-5zn中间合金和si元素分别放至加料托盘上;开始熔炼,当纯铜完全熔化后,投入纯镍块,并加入优质木碳和石墨鳞片的覆盖剂混合体,此时温度控制在1200~1300℃,当纯镍块完全熔融后,保温5-8分钟,充入氩气或者氮气对熔体进行搅拌除气;然后依次加入si、al、sn、和cu-zn中间合金,保温3~5min之后,将熔体温度降温至1150℃准备上引连铸。
49.步骤二、采用氮化硼材料作为结晶器材料,利用虹吸原理使得所述熔炼炉中的合金液进入上引连铸结晶器中,在上引连铸结晶器中通过冷却水系统进行冷却结晶,结晶器冷却水的压力为0.3-0.5mpa,上引结晶器的冷却水进水温度≤30℃,出水温度≤50℃,牵引过程中熔体的液面高度变化不超过
±
20mm,且上引连铸过程中节矩为3mm,连续牵引速率为120cm/min,最终牵引出的圆形铸杆直径为22mm。
50.步骤三、将上述合金铸杆在890℃均匀化处理7h,然后迅速水冷,获得过饱和固溶体合金。
51.步骤四、将步骤三的合金杆料进行形变和热处理,首先将合金杆料进行第一次冷加工处理,第一次冷加工的总变形量为80%,然后在400℃时效处理4h,再进行第二次冷加工处理,第二次冷加工的总变形量为60%,然后在350℃时效处理3h,其铸态组织如图1所示。
52.对比例1:
53.其他条件与实施例1相同,不同之处在于:合金成分为cu-15ni-8sn合金,而无其他元素的添加,且采用的是真空熔炼-浇铸的方式制备合金杆坯,其铸态组织如图2所示。
54.实施例2:
55.步骤一、按照合金组分:15wt.%的ni,6wt.%的sn、1.6wt.%的al、0.8wt.%的zn、
0.6wt.%的nb,余量为纯铜。其中,ni、sn、al、zn、nb的纯度为99.95wt.%。将配好的铜放入熔炼坩埚内,将ni、sn、al、cu-5zn中间合金和nb元素分别放至加料托盘上;开始熔炼,当纯铜完全熔化后,投入纯镍块,并加入优质木碳和石墨鳞片的覆盖剂混合体,此时温度控制在1200~1300℃,当纯镍块完全熔融后,保温5-8分钟,充入氮气或氩气对熔体进行搅拌除气;然后依次加入nb、al、sn、和cu-zn中间合金,保温3~5min之后,将熔体温度降温至1160℃准备上引连铸。
56.步骤二、采用氮化硼材料作为结晶器材料,利用虹吸原理使得所述熔炼炉中的合金液进入上引连铸结晶器中,在上引连铸结晶器中通过冷却水系统进行冷却结晶,结晶器冷却水的压力为0.3-0.5mpa,上引结晶器的冷却水进水温度≤30℃,出水温度≤50℃,牵引过程中熔体的液面高度变化不超过
±
20mm,且上引连铸过程中节矩为3mm,连续牵引速率为120cm/min,最终牵引出的圆形铸杆直径为22mm。
57.步骤三、将上述合金铸杆在900℃均匀化处理4h,然后迅速水冷,获得过饱和固溶态。
58.步骤四、将步骤三的合金杆料进行形变和热处理,首先将合金杆料进行第一次冷加工处理,第一次冷加工的总变形量为85%,然后在400℃时效处理3h,再进行第二次冷加工处理,第二次冷加工的总变形量为65%,然后在350℃时效处理4h。
59.其他条件与实施例3相同,不同之处在于:合金成分为cu-15ni-6sn合金,而无其他元素的添加。
60.实施例3:
61.步骤一、按照合金组分:15wt.%的ni,4.8wt.%的sn、1.2wt.%的al、0.5wt.%的zn、0.5wt.%的si,0.5wt.%的nb,余量为纯铜。其中,ni、sn、al、zn、si和nb的纯度为99.95wt.%。将配好的铜放入熔炼坩埚内,将ni、sn、al、cu-zn中间合金、si和nb元素分别放至加料托盘上;开始熔炼,当纯铜完全熔化后,投入纯镍块,并加入优质木碳和石墨鳞片的覆盖剂混合体,此时温度控制在1200~1300℃,当纯镍块完全熔融后,保温5-8分钟,充入氩气气体对熔体进行搅拌除气;然后依次加入nb、si、al、sn、和cu-10zn中间合金,保温3~5min之后,将熔体温度降温至1150℃准备上引连铸。
62.步骤二、采用氮化硼材料作为结晶器材料,利用虹吸原理使得所述熔炼炉中的合金液进入上引连铸结晶器中,在上引连铸结晶器中通过冷却水系统进行冷却结晶,结晶器冷却水的压力为0.3-0.5mpa,上引结晶器的冷却水进水温度≤30℃,出水温度≤50℃,牵引过程中熔体的液面高度变化不超过
±
20mm,且上引连铸过程中节矩为3mm,连续牵引速率为110cm/min,最终牵引出的圆形铸杆直径为26mm。
63.步骤三、将上述合金铸杆在870℃均匀化处理6h,然后迅速水冷,获得过饱和固溶态。
64.步骤四、将步骤三的合金杆料进行形变和热处理,首先将合金杆料进行第一次冷加工处理,第一次冷加工的总变形量为90%,然后在400℃时效处理5h,再进行第二次冷加工处理,第二次冷加工的总变形量为70%,然后在350℃时效处理4h。
65.对比例3:
66.其他条件与实施例3相同,不同之处在于:合金成分为cu-15ni-4.8sn合金,而无其他元素的添加。
67.表1实施例和对比例合金最终的力学性能、弹性模量和耐温性测试结果
[0068][0069]
通过上述研究可以发现,采用上引连铸和合金化的方法制备的cu-ni-sn系铜合金,可以显著减小枝晶间距,消除合金的微观和宏观偏析,降低生产流程,简化生产工艺,同时可以显著提高合金的抗拉强度、弹性模量和抗软化温度,特别适用于航天、航空以及微电子工业高性能导电弹性器件等的应用。
[0070]
以上描述了本发明优选实施方式,然其并非用以限定本发明。本领域技术人员对在此公开的实施方案可进行并不偏离本发明范畴和精神的改进和变化。