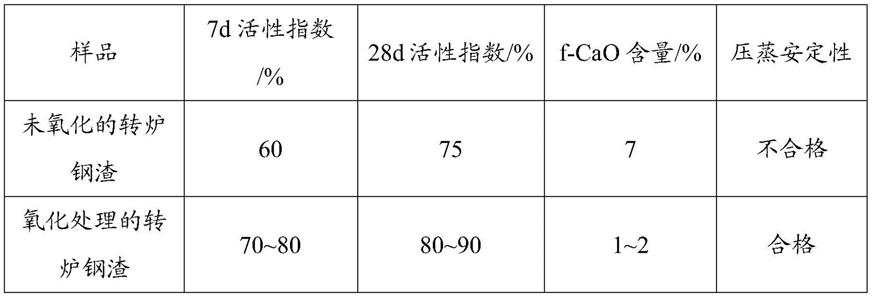
1.本发明属于冶金固废资源化利用技术领域,具体涉及一种钢渣改质方法及得到的改质钢渣。
背景技术:2.这里的陈述仅提供与本发明相关的背景技术,而不必然地构成现有技术。
3.我国目前的钢渣综合利用率不足30%,大量的钢渣被堆放或填埋,造成资源浪费和生态环境污染。主要原因为钢渣在生成和处理过程中,残留和生成一定量的f-cao和mgo,导致其具有体积膨胀性。同时由于钢渣的冷却制度,导致硅酸三钙(c3s)分解出硅酸二钙(c2s)和f-cao,因此钢渣的主要矿物组成为c2s和金属固溶体ro相(feo为主),其中用于c2s本身水化活性低,ro相不具备磁性,导致钢渣本身水化活性差,大量的fe元素被浪费。
4.钢渣的现有处理技术存在如下问题:(1)在熔融态钢渣中加入额外的调质剂,导致处理流程繁琐,存在无法均匀混合,调质反应不完全现象,因此导致钢渣性能不稳定;(2)无法实现酸性矿物与mgo的反应,钢渣中仍然存在影响体积安定的mgo;(3)钢渣中feo被浪费,没有得到有效的使用;(4)进行成分调质后的熔融态钢渣,只进行热闷或风淬处理(虽然可以在一定程度上消解钢渣中的f-cao的含量,但是无法彻底解决钢渣本身的安定性问题),没有进行矿物组成的保护,导致生成的硅酸盐相水化或分解的,容易导致钢渣水化活性的进一步降低,还容易产生二次f-cao的问题。
技术实现要素:5.针对现有技术存在的不足,本发明的目的是提供一种钢渣改质方法及得到的改质钢渣。
6.为了实现上述目的,本发明是通过如下的技术方案来实现:
7.第一方面,本发明提供一种钢渣改质方法,包括如下步骤:
8.向熔融钢渣表面通入富氧气体,激起液态钢渣以沸腾状态与富氧气体的接触,对其进行改质,使熔融钢渣中形成c3s和c2f组分,c3s固溶mgo;
9.采用大射流气体急冷造粒,并采用大流量气体对钢渣颗粒进行急冷,以保留钢渣中的c3s和c2f组分。
10.第二方面,本发明提供一种钢渣,由所述钢渣改质方法制备而成。
11.上述本发明的实施方式取得的有益效果如下:
12.在钢渣处在液态情况下,通入空气或富氧成分调整后的混合气,进行氧化状态下的自改质,将钢渣中的feo转变为fe2o3,钢渣中的sio2与cao优先结合形成c3s,同时c3s会固溶钢渣中的mgo;之后,残留的cao与fe2o3形成铁酸二钙(c2f);利用钢渣氧化自改质气源,采用大射流气体急冷造粒和大流量气体急冷技术,将改质后的液态钢渣快速急冷,快速跃迁c3s和c2f的分解温度1250~1350℃,保留了钢渣中水化活性高的c3s和c2f矿物组成,避免在钢渣处理过程中c3s和c2f的分解,实现解决钢渣中f-cao和mgo导致的体积膨胀性和水化活
性低的问题。
13.在钢渣处理过程中,钢渣已排入渣包内,不影响炼钢流程,同时不增加额外的调质剂,充分利用熔融态钢渣的显热与鼓入的含氧气体产生氧化自改质反应,且反应均匀,钢渣性能稳定。
14.在氧化自改质的过程中,可以实现生成的c3s固溶mgo反应,解决mgo产生的体积膨胀性的问题。
15.利用氧化特性,将feo转变为fe2o3,提高了钢渣消耗cao的极限值,fe2o3与钢渣中残留的cao反应生成c2f,有效的利用了钢渣中的fe元素,同时降低f-cao的含量,解决f-cao产生的体积膨胀性问题。无需额外的调质剂就可以消除钢渣中的f-cao和mgo产生的体积膨胀性问题。
16.使用大射流气体急冷造粒和大流量气体急冷的特殊技术,对氧化自改质钢渣的矿物组成进行保护,使c3s、c2f快速跃迁其分解温度,避免它们二次分解产生f-cao和mgo,同时c3s和c2f具有较高的水化活性,提升了钢渣的活性指数。
17.根据液态钢渣的显热和化学组成,以氧化、大射流气体急冷造粒和大流量气体急冷为技术手段,达成了解决钢渣因为f-cao和mgo产生的体积膨胀性的问题,同时形成以c3s和c2f水化活性高为主的矿物组成,解决了钢渣的胶凝性低的问题,对钢渣应用于建材行业,实现钢渣的高值化综合利用具有重大意义。
具体实施方式
18.应该指出,以下详细说明都是例示性的,旨在对本发明提供进一步的说明。除非另有指明,本发明使用的所有技术和科学术语具有与本发明所属技术领域的普通技术人员通常理解的相同含义。
19.第一方面,本发明提供一种钢渣改质方法,包括如下步骤:
20.向熔融钢渣表面通入富氧气体,激起液态钢渣以沸腾状态与富氧气体的接触,对其进行改质,使熔融钢渣中形成c3s和c2f组分,c3s固溶mgo;
21.采用大射流气体急冷造粒,并采用大流量气体对钢渣颗粒进行急冷,以保留钢渣中的c3s和c2f组分。
22.在一些实施例中,熔融钢渣的温度为1500~1600℃。
23.在一些实施例中,所述富氧气体中氧气含量为21%~30%,%为体积百分数,所述的富氧气体采用空气为主气源,通过引入转炉吹氧气源,通过调节控制流量阀门,调控富氧气体的氧气含量。
24.进一步的,所述富氧气体需经过空气干燥机进行脱水处理。
25.更进一步的,富氧气体脱水后的含水率为0.1%~1%。
26.在一些实施例中,熔融钢渣与富氧气体的接触时间为5~15min。
27.进一步的,向熔融钢渣中通入的富氧气体流量为10~30m3/t/min。
28.在一些实施例中,所述大射流气体急冷造粒的方法,具体为:
29.将液态钢渣倒入造粒室内,水平分布的喷嘴喷出富氧气体对液态钢渣进行吹制,使其快速冷却。
30.进一步的,大射流气体急冷造粒阶段,喷嘴的出口风速为550~800m/s,喷嘴的流
量消耗为吨渣800~1500m3/h。
31.液态钢渣经喷嘴处的气体快速冷却至表面结壳,无互相粘连,所需时间要求为0.1s~0.2s。
32.在一些实施例中,大流量气体对钢渣颗粒进行急冷阶段,冷却气温度为15~35℃。
33.进一步的,冷却器的流量为吨渣3000~5000m3/h。
34.进一步的,急冷阶段,在5s~10s内将钢渣冷却至350℃~400℃。
35.在一些实施例中,造粒和急冷阶段,钢渣与液态水隔离。钢渣不得与液态水接触,可以快速跃迁c3s和c2f的分解温度1250℃~1300℃,实现对c3s和c2f矿物组成的保护,避免二次其分解产生f-cao和mgo。
36.第二方面,本发明提供一种钢渣,由所述钢渣改质方法制备而成。
37.以表1中的钢渣的化学成分为举例,见下表,可知,未氧化的钢渣中的fe元素主要以feo的形式存在,而feo不能与cao反应。按照cao与sio2、al2o3和fe2o3酸性矿物反应,消耗cao的理论极限含量公式cao=2.8sio2+1.1al2o3+0.7fe2o3,计算得到钢渣中形成矿物消耗的cao极限值为34.29%,因此理论上钢渣中还有41.72%-34.29%=7.43%的cao残留,表明对于钢渣cao是富余的,而feo没有得到有效的利用。
38.将钢渣中的feo完全氧化转变为fe2o3后,重新计算钢渣中形成矿物消耗的cao极限值为49.5%,可知氧化生成的fe2o3完全可吸收钢渣中残留的cao。钢渣成分以及氧化后钢渣成分见表1,以下实施例均采用该种组成的钢渣。
39.表1
40.化学成分/%caosio2al2o3fe2o3feomgo未氧化转炉渣41.729.43.166.4219.569.67氧化转炉渣41.729.43.1628.15/9.67
41.熔融态钢渣氧化自改质方法,该方法是在转炉排渣阶段,钢渣为熔融液态,温度在1500~1600℃范围内,将液态钢渣倒入渣包内,然后将6根气管位置调整至距离液态钢渣上表面0.5m~1m处,通入空气或富氧成分调整后的混合气,使液态钢渣呈现沸腾状态,通入时间控制在5min~15min,通入的气流流量为吨渣每分钟10~30m3/(t
·
min),要求气源的o2含量在21%~30%,要求气源必须经过干燥机脱水处理,要求气源中的含水率在0.1%~1%。将钢渣中的feo氧化为fe2o3(反应式1),钢渣中的cao与sio2反应生成硅酸三钙,在硅酸三钙生成的同时,钢渣中的80%以上的mgo开始固溶进硅酸三钙的晶格内部(3cao
·
mgo
·
sio2)(反应式2);cao与fe2o3反应逐步开始反应生成铁酸二钙(2cao
·
fe2o3)(反应式3)。
42.2feo+1/2o2→
fe2o3ꢀꢀꢀ
(1)
43.3cao+sio2+mgo
→
3cao
·
mgo
·
sio2ꢀꢀꢀ
(2)
44.2cao+fe2o3→
2cao
·
fe2o3ꢀꢀꢀ
(3)
45.钢渣温度在1400℃~1450℃范围内时,将熔融液态的钢渣进行大射流气体急冷造粒技术处理,其所用气源要求与钢渣氧化自改质气源一致。对液态钢渣进行大射流气体急冷造粒的参数设置要求为:喷嘴的出口风速在550~800m/s,喷嘴的流量消耗为吨渣800~1500m3/h,液态钢渣经喷嘴处的气体快速冷却至表面结壳,无互相粘连,所需时间要求为0.1s~0.2s,经处理后钢渣平均粒度控制在1mm~1.5mm。
46.经大射流气体急冷造粒技术处理后的钢渣,温度控制在1000℃~1250℃,考虑钢
渣颗粒内部与外部存在梯度差,钢渣颗粒核心温度仍然存在高于1250℃~1300℃情况的存在,因此经造粒后的钢渣,仍需要急冷处理,即落入底部的大流量气冷篦冷机装置,在篦冷机底部通过风机送入大流量气冷,要求冷却气量的消耗为吨渣3000~5000m3/h,对钢渣颗粒进行进一步的快速冷却,大流量气冷篦冷机推动钢渣运动,在5s~10s内将钢渣冷却至350℃~400℃,整个液态钢渣处理过程中,钢渣不得与液态水接触,大流量气体急冷技术钢渣进行快速的急冷,可以快速跃迁硅酸三钙和铁酸二钙的分解温度1250℃~1300℃(反应式4、5),该快速冷却方法有助于硅酸三钙和铁酸二钙矿物的保护,避免二次分解产生f-cao和mgo。
47.3cao
·
mgo
·
sio2→
2cao
·
sio2+cao+mgo
ꢀꢀꢀ
(4)
48.2cao
·
fe2o3→
2cao+fe2o3ꢀꢀꢀ
(5)
49.将冷却至350℃~400℃的钢渣输送至堆场进一步冷却至室温,本方法产生的烟气可进行余热回收、烟气颗粒物净化经达标后,进行排放。
50.经矿物组成计算,使用熔融态钢渣氧化自改质及保护矿物组成方法,得到的钢渣的矿物组成约为45%的c3s,37%的c2f,剩余18%的ro相(主要是未反应的fe2o3、mno、al2o3等固溶体)。
51.经测试,使用熔融态钢渣氧化自改质及保护矿物组成方法得到的钢渣的活性指数如下表2,可知,使用该方法可以提高钢渣的水化活性,降低钢渣中f-cao和f-mgo的含量。
52.表2
[0053][0054]
下面结合具体实施例对本发明作进一步说明。
[0055]
实施例1
[0056]
一种熔融态钢渣氧化自改质方法,液态钢渣温度在1500℃,将液态钢渣倒入渣包内,通入氧气含量为21%的空气,通入时间控制在5min,通入的气体流量控制在10m3/t/min。钢渣降温至1400℃,对钢渣进行大射流气体急冷造粒和大流量气体急冷处理,液态钢渣经喷嘴处的气体快速冷却至表面结壳,无互相粘连,时间控制在0.2s,喷嘴风速控制在550m/s,喷嘴流量控制在800m3/h;钢渣落入底部的大流量气冷篦冷机装置,在10s内将钢渣冷却至400℃,冷却气量的消耗为吨渣3000m3/h,检测钢渣中的f-cao含量为1.8%,压蒸安定性合格,7天活性指数为72%,28天活性指数为83%,氧化自改质及保护矿物组成后的钢渣满足进一步使用的要求。
[0057]
实施例2
[0058]
一种熔融态钢渣氧化自改质及保护矿物组成方法,液态钢渣温度在1550℃,将液态钢渣倒入渣包内,通入氧气含量为25%的空气,通入时间控制在8min,通入的气体流量控
制在15m3/t/min。钢渣降温至1450℃,对钢渣进行大射流气体急冷造粒和大流量气体急冷处理,液态钢渣经喷嘴处的气体快速冷却至表面结壳,无互相粘连,时间控制在0.18s,喷嘴风速控制在650m/s,喷嘴流量控制在1000m3/h;钢渣落入底部的大流量气冷篦冷机装置,在8s内将钢渣冷却至380℃,冷却气量的消耗为吨渣4000m3/h,检测钢渣中的f-cao含量为1.6%,压蒸安定性合格,7天活性指数为75%,28天活性指数为85%,氧化自改质及保护矿物组成后的钢渣满足进一步使用的要求。
[0059]
实施例3
[0060]
一种熔融态钢渣氧化自改质及保护矿物组成方法,液态钢渣温度在1550℃,将液态钢渣倒入渣包内,通入氧气含量为27%的空气,通入时间控制在13min,通入的气体流量控制在25m3/t/min。钢渣降温至1450℃,对钢渣进行大射流气体急冷造粒和大流量气体急冷处理,液态钢渣经喷嘴处的气体快速冷却至表面结壳,无互相粘连,时间控制在0.15s,喷嘴风速控制在750m/s,喷嘴流量控制在1300m3/h;钢渣落入底部的大流量气冷篦冷机装置,在7s内将钢渣冷却至350℃,冷却气量的消耗为吨渣4500m3/h,检测钢渣中的f-cao含量为1.3%,压蒸安定性合格,7天活性指数为78%,28天活性指数为87%,氧化自改质及保护矿物组成后的钢渣满足进一步使用的要求。
[0061]
实施例4
[0062]
一种熔融态钢渣氧化自改质及保护矿物组成方法,液态钢渣温度在1600℃,将液态钢渣倒入渣包内,通入氧气含量为30%的空气(必须进行脱水处理,含水量在0.1%~1%),通入时间控制在15min,通入的气体流量控制在30m3/t/min。钢渣降温至1450℃,对钢渣进行大射流气体急冷造粒和大流量气体急冷处理,液态钢渣经喷嘴处的气体快速冷却至表面结壳,无互相粘连,时间控制在0.1s,喷嘴风速控制在800m/s,喷嘴流量控制在1500m3/h;钢渣落入底部的大流量气冷篦冷机装置,在5s内将钢渣冷却至350℃,冷却气量的消耗为吨渣5000m3/h,检测钢渣中的f-cao含量为1.0%,压蒸安定性合格,7天活性指数为80%,28天活性指数为90%,氧化自改质及保护矿物组成后的钢渣满足进一步使用的要求。
[0063]
从实施例1-4可以得出,本发明所采用的技术和方法可以很好的消除钢渣中的f-cao和mgo,压蒸安定性合格,活性指数提高。相比较氧化用气源的o2含量、自改质时间和大射流气体急冷造粒和大流量气体急冷技术的控制时间,较高的o2含量,氧化改质的时间,及快速的冷却时间,对钢渣改质的效果更好。
[0064]
以上所述仅为本发明的优选实施例而已,并不用于限制本发明,对于本领域的技术人员来说,本发明可以有各种更改和变化。凡在本发明的精神和原则之内,所作的任何修改、等同替换、改进等,均应包含在本发明的保护范围之内。