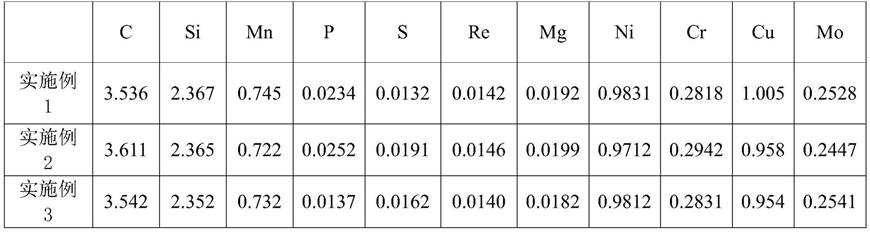
1.本发明属于铸造技术领域,主要涉及一种高强度蠕墨铸铁及其生产方法。
背景技术:2.蠕墨铸铁作为一种新型铸铁材料,兼有球墨铸铁和灰铸铁的优点。蠕墨铸铁具有良好的力学和物理综合性能,特别是热疲劳性能优良。蠕墨铸铁应用于汽车、船领域,尤其在发动机缸体、缸盖、排气管、制动盘、制动鼓、飞轮等等零部件取得了良好的应用效果。高强度蠕墨铸铁的要求较高的抗拉强度和疲劳强度,但目前现有技术中,高强度蠕墨铸铁的熔炼工艺不成熟、稳定性极差,同一批生产的蠕墨铸铁件,蠕化率达不到指标要求,直接导致抗拉强度偏差大,难以批量生产出符合要求的蠕墨铸铁。
技术实现要素:3.为了解决上述技术问题,本发明提供一种高强度蠕墨铸铁及其生产方法,提高批量生产的蠕墨铸铁的蠕化率的稳定性,在保证塑韧性的前提下提高蠕墨铸铁的强硬度。
4.为了达到上述目的,本发明技术方案如下:
5.一种高强度蠕墨铸铁,化学成分的质量百分比含量包括:
6.3.45%~3.70%的c,2.25%~2.45%的si,0.65%~0.75%的mn,<0.04%的p,0.010%~0.020%的s,0.01%~0.02%的re,0.010%~0.020%的mg,0.010%~0.020%的re,0.95%~1.05%的cu,0.95%~1.05%的ni,0.25%~0.35%的cr,0.2%~0.3%的mo,余量为fe和杂质元素。
7.上述高强度蠕墨铸铁的生产方法,包括以下步骤:
8.熔炼,称取55%~65%的生铁、15%~25%的蠕墨铸铁回炉料、15%~25%的废钢,加入电炉中,加热升温至全部加入料熔化;加入辅料并调整铁水化学成分;所述辅料包括增碳剂、硅铁、锰铁、铬铁、钼铁、铜和镍;
9.具体地,电炉中加入生铁是增加溶化后铁水的纯净度,电炉中加入蠕墨铸铁回炉料以节约生产成本。
10.蠕化孕育,铁水中加入镁蠕化剂、稀土蠕化剂和孕育剂,铁水与镁蠕化剂、稀土蠕化剂和孕育剂进行反应。
11.浇注,对孕育后的铁水进行拔渣、浇注,得到所述高强度蠕墨铸铁。
12.进一步地,所述蠕化步骤,镁蠕化剂和稀土蠕化剂均采用喂线方式加入。当铁水中s含量为0.010%~0.015%时,每吨铁水中所述镁蠕化剂的喂线量为6.9m~7.0m,每吨铁水中所述稀土蠕化剂的喂线量为4m~4.1m。当铁水中s含量为0.015%~0.018%时,每吨铁水中所述镁蠕化剂的喂线量为7.1m~7.3m,每吨铁水中所述稀土蠕化剂的喂线量为4m~4.1m。当铁水中s含量为0.018%~0.020%时,每吨铁水中所述镁蠕化剂的喂线量为7.9m~8.9m,每吨铁水中所述稀土蠕化剂的喂线量为4m~4.1m。
13.进一步地,所述镁蠕化剂的化学成分的质量百分含量包括:14.5%~15.5%的mg,
43%~46%的si,1.5%~2.5%的ca,≤1%的mgo,余量为fe和杂质元素。
14.进一步地,所述稀土蠕化剂的化学成分的质量百分含量包括:18%~22%的re,43%~46%的si,余量为fe和杂质元素。
15.进一步地,所述孕育步骤,孕育剂采用喂线方式加入;每吨铁水中所述孕育剂的喂线量为15m~15.1m。
16.进一步地,所述孕育剂的化学成分的质量百分含量包括:74%~76%的si,≤1%的al,余量为fe和杂质元素。
17.进一步地,在所述熔炼步骤,加入辅料后调整铁水的化学成分至:3.65%~3.75%的c,1.90%~2.00%的si,0.65%~0.75%的mn,<0.05%的p,0.010%~0.020%的s,0.95%~1.05%的cu,0.95%~1.05%的ni,0.25%~0.35%的cr,0.2%~0.3%的mo,余量为fe和杂质元素。
18.进一步地,所述生铁为超高纯生铁,所述超高纯生铁的化学成分的质量百分含量包括:3.5%~4.0%的c,≤0.4%的si,≤0.1%的mn,≤0.010%的p,≤0.010%的s,≤0.010%的ti,余量为fe和杂质元素。
19.进一步地,在所述浇注步骤,浇注温度为1360℃~1380℃。
20.由上述技术方案可知,本发明的优点和积极效果在于:
21.本发明通过加大生铁和废钢的比例,控制铁水中的s含量和杂质元素含量,熔炼步骤中s含量能够稳定控制在0.010%~0.020%的范围内,蠕化步骤中铁水中同时加入镁蠕化剂和稀土蠕化剂,达到了稳定蠕墨铸铁蠕化率的效果,适用于批量生产。
22.本发明通过合金元素的加入以及合理的化学成分控制,充分发挥各元素之间的相互作用,稳定和细化基体组织中的珠光体并强化铁素体。本发明在保证蠕墨铸铁塑性的同时提高其强度,稳定地将附铸试块和本体的抗拉强度控制在450mpa以上,延伸率也达到4%以上,并且,铸件本体关键部位的蠕化率和珠光体的含量均达到75%以上。
具体实施方式
23.下面具体实施例对本发明作进一步说明,以使本领域技术人员可以更好的理解本发明并能予以实施,但所举实施例不作为对本发明的限定。按照本领域的普通技术知识和惯用手段,在不脱离本发明上述基本技术思想前提下,对本发明上述结构做出的其它多种形式的修改、替换或变更,均应落在本发明的保护范围。
24.实施例中的百分比、%、分数,如无特别说明指的是以质量计算。
25.本发明的实施例由于一个实施例对应不同批次的原料生产同一型号产品的结果,由于每批次间原料的细微不同,因此在实施例中的数值会存在轻微的浮动,但只要在所列举的范围能均能达到其效果。
26.本发明实施例公开一种高强度蠕墨铸铁,炉后化学成分的质量百分比含量包括:
27.3.45%~3.70%的c,2.25%~2.45%的si,0.65%~0.75%的mn,<0.04%的p,0.009%~0.020%的s,0.01%~0.02%的re,0.010%~0.020%的mg,0.010%~0.020%的re,0.95%~1.05%的cu,0.95%~1.05%的ni,0.25%~0.35%的cr,0.2%~0.3%的mo,余量为fe和杂质元素。
28.本发明实施例公开的高强度蠕墨铸铁,cu含量为0.95%~1.05%,cu元素能降低
奥氏体转变温度,cu元素还能够扩大奥氏体转变区域,从而使c元素有充足的时间扩散,减小珠光体片间距,增加珠光体含量,得到稳定的细片状珠光体组织。本发明实施例公开的高强度蠕墨铸铁,ni含量为0.95%~1.05%,ni元素在铁液和固态铸铁中均能无线溶液,ni元素属于奥氏体元素,可使奥氏体转变温度降低;并且ni元素比cu元素的作用强,加入少量的ni就可使蠕墨铸铁中的铁素体受到抑制,使珠光体细化并增加珠光体含量,ni元素还可减少断裂敏感性。cr含量为0.25%~0.35%,在蠕墨铸铁中,cr元素有两个重要作用,缩小γ区和形成特殊的碳化物,cr元素与c元素的亲和力比cr元素与fe元素的亲和力要大得多,因而能形成很稳定的碳化物。在蠕墨铸铁中,加入少量的cr,会稳定珠光体中的碳化物,提高铸件的强度和硬度。mo含量为0.2%~0.3%,mo元素对石墨形态没有影响,蠕墨铸铁中加入mo可使共晶团细化;mo元素、cu元素和ni元素的共同作用,可形成贝氏体组织,提高蠕墨铸铁的强度和硬度。
29.本发明实施例公开的高强度蠕墨铸铁,cr元素、mo元素、cu元素和ni元素之间相互作用,使铸态蠕墨铸铁基体组织中的珠光体稳定控制,增加了珠光体的含量从而解决了铸态下珠光体数量的难题,并且有强化铁素体的作用。
30.以下具体实施例中按铁水炉前化学成分配比进行配料:
31.3.65%~3.75%的c,1.90%~2.00%的si,0.65%~0.75%的mn,<0.05%的p,0.010%~0.020%的s,0.95%~1.05%的cu,0.95%~1.05%的ni,0.25%~0.35%的cr,0.2%~0.3%的mo,余量为fe和杂质元素。
32.超高纯生铁的化学成分的质量百分含量包括:3.5%~4.0%的c,≤0.4%的si,≤0.1%的mn,≤0.010%的p,≤0.010%的s,≤0.010%的ti,余量为fe和杂质元素;要求超高纯生铁表面无锈蚀。
33.镁蠕化剂的化学成分的质量百分含量包括:14.5%~15.5%的mg,43%~46%的si,1.5%~2.5%的ca,≤1%的mgo,余量为fe和杂质元素。
34.稀土蠕化剂的化学成分的质量百分含量包括:18%~22%的re,43%~46%的si,余量为fe和杂质元素。
35.孕育剂的化学成分的质量百分含量包括:74%~76%的si,≤1%的al,余量为fe和杂质元素。
36.实施例1
37.一种高强度蠕墨铸铁的生产方法,包括以下步骤:
38.步骤一,称取原材料,主料:1962kg的超高纯生铁、652kg的蠕墨铸铁回炉料、674kg的废钢;辅料:29.5kg的增碳剂、58kg的硅铁、44kg的锰铁、14.6kg的铬铁、11.4kg的钼铁,24kg的电解铜,27kg的电解镍。
39.步骤二,废钢、回炉料、超高纯生铁依次快速连续加入电炉熔炼,辅料加入电炉中后熔炼到1450℃~1470℃,取样检测炉前化学成分,检测结果为:3.696%的c,1.969%的si,0.734%的mn,0.0236%的p,0.0148%的s,0.9837%的ni,0.2907%的cr,0.2598%的mo,1.006%的cu。
40.步骤三,升温至1480℃~1500℃出铁1.6t铁水到浇包内;
41.步骤四:浇包转运至喂线站,按s含量0.010%~0.015%,镁蠕化剂喂线11.1m,稀土蠕化剂喂线6.4m,孕育剂喂线24m。
42.步骤五,蠕化、孕育完成后,对铁水进行拔渣。
43.步骤六,浇包转运至浇注工位,对铁水测温,温度在1360℃~1380℃,浇注成型后即得到蠕墨铸铁。
44.实施例2:
45.一种高强度蠕墨铸铁的生产方法,包括以下步骤:
46.步骤一,称取原材料,主料:1953kg的生铁、644kg的蠕墨铸铁回炉料、692kg的废钢;辅料:29.7kg的增碳剂、57kg的硅铁、42kg的锰铁、14.9kg的铬铁、12.3kg的钼铁,23kg的电解铜,25kg的电解镍。
47.步骤二,废钢、回炉料、超高纯生铁依次快速连续加入电炉熔炼,辅料加入电炉中后熔炼到1450℃~1470℃,取样检测炉前化学成分,检测结果为:3.703%的c,1.942%的si,0.728%的mn,0.0244%的p,0.0186%的s,0.9723%的ni,0.3023%的cr,0.2723%的mo,0.963%的cu。
48.步骤三,升温至1480℃~1500℃出铁1.6t铁水到浇包内;
49.步骤四:浇包转运至喂线站,按s含量0.018%~0.020%,镁蠕化剂喂线13.3m,稀土蠕化剂喂线6.5m,孕育剂喂线24.1m。
50.步骤五,蠕化、孕育完成后,对铁水进行拔渣。
51.步骤六,浇包转运至浇注工位,对铁水测温,温度在1360℃~1380℃,浇注成型后即得到蠕墨铸铁。
52.实施例3:
53.一种高强度蠕墨铸铁的生产方法,包括以下步骤:
54.步骤一,称取原材料,主料:1820kg的超高纯生铁、653kg的蠕墨铸铁回炉料、723kg的废钢;辅料:28.4kg的增碳剂、58kg的硅铁、49kg的锰铁、13.2kg的铬铁、12.4kg的钼铁,25kg的电解铜,29kg的电解镍。
55.步骤二,废钢、回炉料、超高纯生铁依次快速连续加入电炉熔炼,辅料加入电炉中后熔炼到1450℃~1470℃,取样检测炉前化学成分,检测结果为:3.654%的c,1.953%的si,0.740%的mn,0.0232%的p,0.0157%的s,0.9942%的ni,0.2804%的cr,0.2694%的mo,0.994%的cu。
56.步骤三,升温至1480℃~1500℃出铁1.7t铁水到浇包内;
57.步骤四:浇包转运至喂线站,按s含量0.015%~0.018%,镁蠕化剂喂线12.2m,稀土蠕化剂喂线6.8m,孕育剂喂线25.5m。
58.步骤五,蠕化、孕育完成后,对铁水进行拔渣。
59.步骤六,浇包转运至浇注工位,对铁水测温,温度在1360℃~1380℃,浇注成型后即得到蠕墨铸铁。
60.对上述实施例1-3的蠕墨铸铁的炉后化学成分进行检测,结果如表1所示。
61.表1本发明实施例1-实施例3炉后化学成分检测结果(%)
[0062][0063]
对上述实施例1-3的蠕墨铸铁的力学性能和金相组织进行检测,结果如表2所示。
[0064]
表2本发明实施例1-实施例3力学性能、金相组织检测结果
[0065][0066]
在蠕化、孕育过程中,采用喂线法同步进行镁蠕化剂喂线蠕化、稀土蠕化剂喂线蠕化和孕育剂喂线孕育处理,以促进铁水对蠕化剂和孕育剂的吸收,提高蠕化元素和孕育元素的吸收率,降低蠕墨铸铁的生产成本;同时通过缩短铁水的处理时间,提高蠕墨铸铁的球化率的稳定性,从而提高蠕墨铸铁的力学性能。
[0067]
以上所述实施例仅表达了本发明的具体实施方式,其描述较为具体和详细,但并不能因此而理解为对发明专利范围的限制。应当指出的是,对于本领域的普通技术人员来说,在不脱离本发明构思的前提下,还可以做出若干变形和改进,这些都属于本发明的保护范围。因此,本发明专利的保护范围应以所附权利要求为准。